курсовая. I. технология сварки цветных металлов
![]()
|
II. КОНТРОЛЬ КАЧЕСТВА СВАРОЧНЫХ СОЕДИНЕНИЙ (ГОТОВЫХ ИЗДЕЛИЙ И КОНСТРУКЦИЙ) 2.1 Газовая сварка и резка металлов Для нее применяется сварочная горелка, работающая в большинстве случаев на ацетилене и кислороде. Не так давно для лабораторий выпущен небольшой генератор ацетилена с емкостью около 1 кг карбида, кроме того, в продаже имеются небольшие стальные баллоны с ацетиленом, обеспечивающие еще более чистое выполнение работ. Установка пригодна, между прочим, и для многих жестяных работ. Она не требует наличия каких-либо особых знаний или приготовлений, дешева в изготовлении и в эксплуатации. При сварке поступают следующим образом: после выбора соответствующей горелки, прежде всего, закрывают краны горелки. Вслед за этим открывают ацетиленовый кран на генераторе или на стальном баллоне, а затем - кислородный кран. После этого несколько приоткрывают ацетиленовый кран на горелке, зажигают вытекающий из него газ и поворачивают кислородный кран на горелке, открывая его до тех пор, пока у выхода горелки не возникает маленький острый конус пламени. Теперь горелка готова к работе. Свариваемую деталь сначала обрабатывают на некотором расстоянии вокруг места сварки, после чего легким прикосновением конуса пламени начинают расплавлять шов и, добавляя материал в виде сварочной проволоки, постепенно заполняют весь шов целиком. Чтобы приобрести некоторую уверенность в этих работах, начинающим следует попросить опытного сварщика показать им все операции сварки. Этим способом могут быть сварены почти все железосодержащие материалы. При сварке место соединения нагревают до расплавления высокотемпературным газовым пламенем. При нагреве газосварочным пламенем кромки свариваемых заготовок расплавляются, а зазор между ними заполняется присадочным металлом, который вводят в пламя горелки извне. Газовое пламя получают при сгорании горючего газа в атмосфере технически чистого кислорода. Кислородный баллон представляет собой стальной цилиндр со сферическим днищем и горловиной для крепления запорного вентиля. На нижнюю часть баллона насаживается башмак, позволяющий ставить баллон вертикально. На горловине имеется кольцо с резьбой для навертывания защитного колпака. Средняя жидкостная вместимость баллона 40 дм3. При давлении 15 МПа он вмещает |
Ст18ХГС | C, % | Mn, % | Cr, % | Ni, % | Si, % | P, % | S, % |
0,15-0,22 | 0,80-1,10 | 0,80-1,10 | 0,30 | 0,90-1,20 | 0,030 | 0,025 | |
Сталь 18ХГС низкоуглеродистая, среднелегированная, 2 группа свариваемости, легированных добавок3%.
Литые, кованые и штампованные заготовки обычно поступают на сварку в виде, не требующем дополнительных операций. По-другому обстоит дело с деталями из проката. После подбора металла по размерам и маркам стали необходимо выполнить следующие операции: правку, разметку, резку, обработку кромок, гибку и очистку под сварку.
Правка осуществляется созданием местной пластической деформации обычно в холодном состоянии. Наиболее частыми видами деформации листовой стали являются волнистость, местные выпучины и вогнутости, заломленные кромки, серповидность в плоскости листа.
Для правки листов и полос толщиной от 0,5 до 50мм широко используют многовалковые машины (число валков более 5).
Исправление достигается многократным изгибом при пропускании листов между верхним и нижним рядами валков, расположенных в шахматном порядке. Листы толщиной менее 0,5мм правят растяжением с помощью приспособлений на прессах или на специальных растяжных машинах. Мелко и средне сортовой, а также профильный прокат правят на роликовых машинах, работающих по схеме листоправильных.
В случаи необходимости создания более значительных деформаций правка и гибка должны производится в горячем состоянии.
Разметка. Разметка может быть индивидуальной (такая разметка трудоёмкая) и по наметочным шаблонам. Наметка более производительна, однако изготовление специальных наметочных шаблонов не всегда экономически целесообразно. Оптический метод по чертежу, проектируемому на размечаемую плоскость, позволяет вести разметку без шаблона.
Резка металла и обработка кромок. Механическую резку производят на ножницах, на отрезных станках и штампах на прессах. Для резки используют ножницы листовые с наклонным ножом, высечные, дисковые, комбинированные, пресс-ножницы, сортовые для резки уголка, швеллеров и двутавров, ручные пневматические и электрические. Отрезные станки применяют для резки труб, фасонного и сортового материала. Детали сварных конструкций вырезают на отрезных стаканах с дисковыми и ленточными пилами, трубоотрезных стаканах, на станках с абразивными кругами, в некоторых случаях гладким диском за счёт сил трения.
Термическая разделительная резка менее производительна, чем резка на ножницах, но более универсальна и применяется для получения свариваемых заготовок разных толщин как прямолинейного, так и криволинейного профиля.
Термическая разделительная резка основана на способности металла сгорать в струе технически чистого кислорода и удалении продуктов сгорания из полости реза. В зависимости от источника теплоты, применяемого для резки, различают газовую резку, основанную на использовании теплоты газового пламени; дуговую резку расплавлением с использованием теплоты электрической дуги, обычно горящей между разрезаемым металлом и электродом; плазменно-дуговую резку (резку сжатой дугой) — особый вид дуговой резки, основанный на вытеснении металла из полости реза направленным потоком плазмы.
Металл из полости реза в процессе термической резки удаляется:
термическим способом за счёт расплавления и вытекания металла из полости реза;
химическим способом за счёт окисления металла, его превращения в окислы и шлаки, которые также удаляются из полости реза;
механическим способом за счёт механического действия струи газа, способствующей выталкиванию жидких и размягчённых продуктов из полости реза.
Термическая резка разделяется на ручную, механизированную и автоматическую. Ручная и механизированная резка выполняются по разметке, автоматическая — с помощью копирных устройств, по масштабному чертежу и на машинах с программным управлением.
Кромки подготавливают термическими и механическими способами. Кромки с односторонним или двусторонним скосом можно получить, используя одновременно два или три резака, располагаемых под соответствующими углами.
Гибка Листовые элементы толщиной 0,5-50мм для получения цилиндрических и конических поверхностей гнут на листогибочных вальцах с валками длинной до 13м.
Очистка поверхности металла под сварку. Очистку применяют для удаления с поверхности металла средств консервации, загрязнений, смазочно-охлаждающих жидкостей, ржавчины, окалины, заусенцев, грата и шлака.
При сварке с неочищенной поверхностью возникают различные дефекты шва: поры и трещины, а также ухудшается формирование шва. Для очистки проката, деталей и сварных узлов используют механические и химические методы. К механическим методам относятся дробеструйная и дробемётная обработка, зачистка металлическими щётками, иглофрезами, шлифовальными кругами и лентами.
Химическими методами очистки обезжиривают и травят поверхности свариваемых деталей.
Для предохранения металла от коррозии кроме очистки обычно пассивируют или грунтуют поверхности, что позволяет сваривать металл без удаления защитного покрытия.
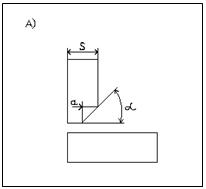
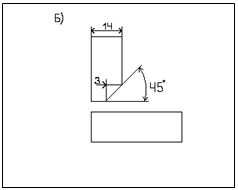
Рис. 2 Геометрические (А) и конструктивные (Б) размеры кромок. a — угол скоса кромки;
S – толщина металла;
а – притупление;
Стыки конструкций по мере сборки закрепляют прихватками – короткими сварными швами для фиксации взаимного расположения подлежащих сварке деталей.
Прихватки размещают в местах расположения сварных швов, за исключением мест их пересечения. Длина прихваток для сталей с пределом текучести до 390 МПа должна быть не менее 50мм и расстояние между ними – не более 500м; для сталей с пределом текучести до 390 МПа прихватки должны быть длиной 100мм и расстоянием между ними – не более 400мм.
Моя конструкция не нуждается в досварочной термообработке, потому что она слишком большая по диаметру и по толщине металла.
Определение и расчёт параметров режима сварки конструкции начнём с диаметра электрода; диаметр электрода будет равен в первом слое d э1 =4 мм, а во втором слое dэ2 =5 мм; первым накладывается корневой слой, а вторым – кольцевой. Идём дальше и определяем силу сварочного тока по формуле:
I=k×d;


I1=40×4=160 А;
I2=40×5=200 А;
далее находим марку электрода: УОНИИ — 13/45, далее находим род и полярность тока: -I(-) постоянный ток обратной полярности.
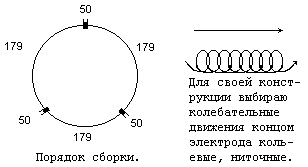
Для моей конструкции используется марка электрода УОНИИ — 13/45.
Условное обозначение электрода:
Э42-УОНИИ-13/45-5,0-УД-2
Е-432 (5) — Б 1 0
Э — электрод,
42 — временное сопротивление sв=42кг·с/мм,
Э42 — тип электрода,
УОНИИ — 13/45-марка электрода по ГОСТу,
5 – dэ = 5мм,
У — для сварки углеродистых сталей,
Д — толстое по пластичности обычный,
Е — состав электродного покрытия,
432(5) — условное табличное обозначение химического состава электродного (наплавленного) металла,
Б — основное покрытие,
1 — положение сварки (для сварки в любом пространственном положении),
0 — -I(-) постоянный ток обратной полярности.
Классификация электродов: Электроды, применяемые для сварки и наплавки, классифицируются по назначению (для сварки стали, чугуна, цветных металлов и для наплавочных работ) технологическим особенностям (для сварки в различных пространственных положениях, сварки с глубоким проплавлением и ванной сварки), виду и толщине покрытия, химическому составу стержня и покрытия, характеру шлака, механическим свойствам металла шва и способу нанесения покрытия (опресовкой или окунанием).
Основными требованиями для всех типов электродов являются: обеспечение стабильного горения дуги и хорошего формирования шва; получение металла сварного шва заданного химического состава; спокойное и равномерное расплавление электродного стержня и покрытия; минимальное разбрызгивание электродного металла и высокая производительность сварки; лёгкая отделимость шлака и достаточная прочность покрытий; сохранение физико-химических и технологических свойств электродов в течении определённого промежутка времени; минимальная токсичность при изготовлении и при сварке.
По назначению металлические электроды для РДС сталей и наплавки поверхностных слоёв с особыми свойствами, изготовляемые способом опресовки, подразделяются (ГОСТ 9466-75):
для сварки углеродистых и низкоуглеродистых сталей с временным сопротивлением разрыву до 60 кгс/мм2 (600 МПа), с условным обозначением У;
для сварки легированных сталей с временным сопротивлением разрыву свыше 60кгс/мм2 (600 МПа) — Л; для сварки легированных теплоустойчивых сталей — Т;
для сварки высоколегированных сталей с особыми свойствами — В;
для наплавки поверхностных слоёв с особыми свойствами — Н.
По толщине покрытия электроды подразделяются на электроды с тонким, средним, толстым и особо толстым покрытиями.
По виду покрытия электроды подразделяются: с кислым покрытием А, с основным покрытием — Ц, с рутиловым покрытием — Р, с покрытием смешанного вида — с двойным обозначением, с прочими видами покрытий — П.
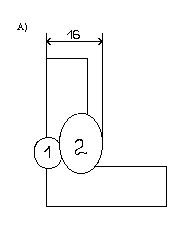
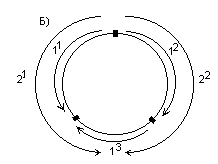
Рис.3. А) Заполнение шва по сечению, Б) Заполнение шва по длине.
Расчёт сварных швов на прочность:
При расчёте сварных швов на прочность нужно учитывать, что стыковые швы работают на сжатие и растяжение, а угловые на срез.
Прочность углового шва на 30% меньше прочности стыкового.
Расчёт на прочность ведётся по формуле: для углового шва:
Nр = 0,7×Rсв×K×Lшв;
Rcв = 18×10 7 Н/м2;
К = 16×10 -3 м;
L шв = p×d = 3.14×219 = 688 мм;
Решение:
L шв = 0,688+0,688 = 1,376 м;
N р = 0,7×18×107 ×16×10-3 ×1,376 = 2,8×106 Н.
Дефекты сварных соединений. Согласно ГОСТ 23055 — 78* для соединений, выполненных сваркой плавлением, возможно образование шести видов дефектов.
пористость шва: сферическая, канальная, цепь пор, группа пор, линейная (протяжённая).
шлаковые и металлические включения: разделяются на шлак компактный, шлак линейный, металлические включения, поверхностные включения.
несплавления: по кромкам и между слоями многослойного шва.
дефекты формы шва: чрезмерный провар корня (прожог, протёк), неровности (наплывы, вмятины и пр.), подрезы, несовпадения кромок и т.п.
Все эти дефекты ухудшают механические свойства сварных соединений и, следовательно, работоспособность конструкций. Часть из них, такие, как наружная пористость и наружные включения, прожоги, неплотность шва, подрезы, вмятины, недостаточные размеры швов и усилений, должна быть исправлена немедленно при обнаружении силами сварщика, допустившего дефект.
Наиболее опасны и недопустимы трещины всех видов, при обнаружении которых сварного соединения бракуется или же подлежит исправлению. Исправление возможно при наличии единичных трещин, а сварное соединение с множественными трещинами исправлению не подлежит. Для ликвидации единичной трещины предварительно засверливают металл на расстоянии примерно 30 — 50 мм от её концов, после чего делают разделку трещины, затем подогревают участку металла на её концах до температуры 100 — 150°С и одновременно заваривают подготовленную трещину.
Для моей конструкции используется: Ультразвуковая дефектоскопия (УЗД) основана на использовании ультразвуковых колебаний (УЗК), которые представляют собой колебания упругой Среды со сверхвысокими частотами (более 20 кГц), не воспринимаемыми человеческим ухом. Ультразвуковые волны могут проникать в металл на большую глубину и отражаться от неметаллических включений и других дефектов. Для контроля применяют колебания частотой 0,5 — 10 Мгц. Введение этих колебаний осуществляют пьезоэлементами (пьезопреобразователями), которые состоят из пьезопластин толщиной, равной половине длины волны, излучаемой УЗК. Пьезоэлектрические материалы обладают способностью преобразовывать действие электрического поля в механические деформации и наоборот — действие механических деформаций в электрические заряды. Пластины изготавливают из пьезоэлектрической керамики или кварца и наклеивают на призмы из оргстекла, полистирола, капрона и других материалов, которые поглощают ультразвук и обеспечивают высокое затухание колебаний, что позволяет получать короткие зондирующие импульсы. Для приложения и съёма электрического поля на противоположных поверхностях пластины нанесени серебряные электроды. Пьезопреобразователь обладает свойством излучать УЗК в металл через контактирующую смазку (глицерин, солидол и т.п.) синхронно с приложенным высокочастотным током и воспринимать отражённые от дефектных мест обратные УЗК, преобразуя их в электрические импульсы, фиксируемые электронно — лучевой трубкой. Чаще всего применяют наклонный преобразователь, работающий по совмещённой схеме и служащий одновременно излучателем и приёмником УЗК. Применяются также раздельно совмещённый преобразователь, в котором одна пьезопластина служит излучателем УЗК, а другая приёмником. Примерная технология контроля приведена на рис. 4. Контроль, как правило, проводят с одной стороны соединения (для толщины до 50 мм), но с обеих сторон шва, как показано на рисунке. В настоящее время УЗК применяют всё более широко для проверки качества стыковых и угловых швов и даже стыков арматурной стали. Иногда для большей надёжности сомнительные места просвечивают.
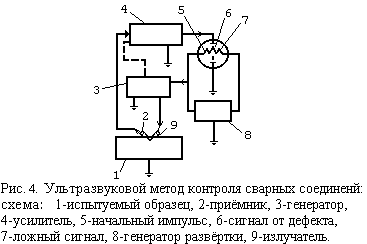
Сварочный пост — это рабочее место сварщика.
Пост ручной дуговой сварки (РДС)
Стационарный сварочный пост комплектуется:
1. Система вентиляции,
2. освещение,
3. заземление,
5. сварочные кабели — прямой и обратный,
6. электрододержатель,
7. стол и стул сварщика,
8. стакан для электродов,
9. ёмкость для металлоотходов и огарков,
10. инструменты: (металлическая щётка, щётка смётка, напильник, молотки, линейка, угольник, чертилка, шаблон мел, ножовка, ножницы, зубило, молоток для шлака, клеймо).
11. сборочно-сварочные приспособления,
12. спецодежда,
13. маска (щиток),
14. медицинская аптечка,
15. средства пожаротушения.
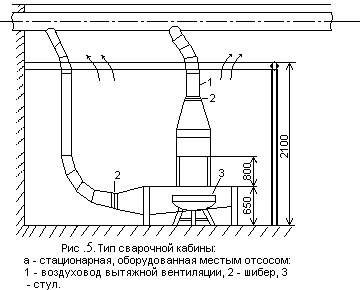
Трёхфазная мостовая схема выпрямления (рис 6, а) наиболее распространена в выпрямителях с падающей и жёсткой характеристиками. Схему применяют для работы в комплекте с наиболее простой конструкцией трёхфазных трансформаторов. На рис. 6, б показаны синусоиды каждой фазы, а рис 6, в — выпрямленный ток, который приобретает форму, показанную на рисунке.
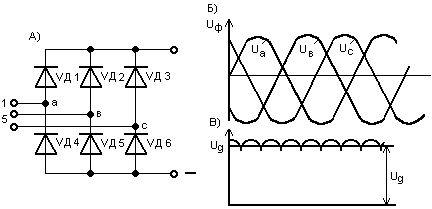
Сварочными выпрямителями называют электрические аппараты, преобразующие переменный ток трёхфазной сети в постоянный при помощи полупроводниковых приборов. Полупроводниковыми называют кристаллические вещества (например, легированные кристаллы кремния, германия и т.п), которые используют для изготовления полупроводниковых электрических приборов — диодов, тиристоров и транзисторов. Диод обладает свойством односторонней проводимости положительного тока (анода) и задержки отрицательного тока (катода).
Аналогично диоду работает тиристор, который имеет управляющий электрод УЭ, через который подаётся электрический сигнал тиристору для открывания и пропуска тока. Его называют управляемым диодом. Свойство этих приборов пропускать ток в одном направлении и закрывать проход тока в другом аналогично свойству вентилей открывать и закрывать прохождение воды или газа, поэтому их называют полупроводниковыми вентилями. Третий прибор — транзистор обладает свойством усиления тока, напряжения и мощности.
Сварочные выпрямители имеют значительные преимущества по сравнению со сварочными преобразователями. Они повышают стабильность дуги и уменьшают разбрызгивание при сварке. КПД выпрямителей значительно выше, а потери холостого хода ниже, чем у преобразователей. Пределы регулирования сварочного тока и напряжения расширены, увеличена возможность автоматизации сварочного процесса. Выпрямители имеют меньшую массу и габариты, что упрощает их размещение на строительной площадке и в цехах. Наибольшее количество выпрямителей выпускается с питанием от трёхфазной сети с применением трёхфазных и шестифазных схем выпрямления.
Пульсация его становится шестифазной с частотой 300 Гц. Выпрямленный ток имеет жёсткую внешнюю характеристику. При увеличении индуктивного сопротивления характеристика получается падающей. Техническое обслуживание и эксплуатацию выпрямителей следует производить только после тщательного изучения паспортов, входящих в комплект их поставки, в которых содержатся сведения об устройстве выпрямителей, порядке работы, правилах безопасности, правилах проверки (измерения) характеристик и т.п.
Перед началом эксплуатации выпрямитель должен быть очищен от пыли и проверен в соответствии с паспортной инструкцией. Затем необходимо заземлить корпус выпрямителя и зажим вторичной цепи, идущей к изделию, и после устранения всех неисправностей можно включить выпрямитель в сеть и проверить работу вентилятора. Установку, подключения к сети и регулировку выпрямителя может выполнять только квалифицированный электромонтажник, имеющий группу по электробезопасности не ниже третьей. Работа по сварке может быть поручена только электросварщику, прошедшему обучение по работе с выпрямителем и имеющему удостоверение на право производства работ, а также группу по электробезопасности не ниже второй.
Выпрямитель необходимо предохранять от атмосферных осадков, сырости, пыли и грязи. Установка его на строительной площадке допускается только в специальном передвижном машинном помещении. В цехе он должен быть установлен в специально отведённом месте и отгорожен от посторонних лиц, а также от возможных ударов при передвижении конструкций. При эксплуатации необходимо очищать выпрямитель раз в три месяца от пыли и грязи, продувая сжатым воздухом, и заполнять тугоплавкой смазкой трущиеся поверхности, а также проверять исправность контактов, вентилятора, тепловой защиты и других деталей.
В процессе работы могут возникнуть следующие неисправности, характерные для всех выпрямителей:
выпрямитель не даёт напряжения, причинами этого могут быть неисправность ветрового реле, неправильная работа вентилятора (засасывание воздуха не со стороны жалюзи), выход из строя одного или нескольких вентилей выпрямительного блока;
электродвигатель вентилятора не работает. Причиной этому может быть обрыв цепи питания или выход из строя предохранителя сети.
Трёхфазная мостовая схема выпрямления применена для однопостовых выпрямителей с падающей характеристикой ВД — 306 на токи 200, 315 и 400 А. Они изготавливаются с механическим трансформаторным регулированием и благодаря простоте конструкции, надёжности и лёгкости обслуживания широко применяются на стройках. Изменение диапазонов в этих выпрямителях обеспечивается переключением первичных, а также вторичных обмоток трансформаторов с “треугольника” на “звезду”. Плавное регулирование в пределах диапазона осуществляется путём перемещения катушек вторичной обмотки ходовым винтом. Выпрямительный мост состоит из шести кремниевых вентилей В200. Вентиляция для охлаждения вентилей — воздушная, принудительная. Нормальная работа вентиляции контролируется ветровым реле. Выпрямитель ВД-306 имеет защиту при аварийных ситуациях путём отключения аппарата от сети. Структурная схема и внешние характеристики выпрямителей типа ВД даны на рис. 7.
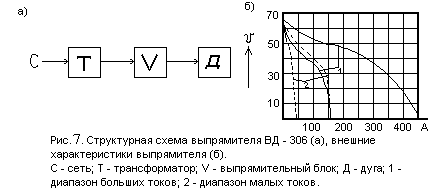
Инструменты и принадлежности электросварщика.
К инструментам и принадлежностям электросварщика относятся электрододержатель, щиток или маска, специальный молоток с зубилом, стальная щётка, металлические клейма для маркировки сварных швов и ящик или сумка для хранения и переноски электродов и инструмента.
Электрододержатель — один из основных инструментов электросварщика, от которого во многом зависят производительность и безопасные условия труда. Электрододержатель должен удовлетворять следующим требованиям: быть лёгким (не более 0,5 кг) и удобным в обращении; иметь надёжную изоляцию; не нагреваться при работе и обеспечивать наиболее полное расплавление электрода; обеспечивать быстрое и надёжное закрепление электрода в удобном для сварки положении; его зажимное устройство должно действовать без больших усилий как при закрепление электрода, так и при его смене; присоединение сварочного провода к стержню держателя должно быть прочным и обеспечивать надёжный контакт. Для ручной дуговой сварки существует несколько типов электрододержателей. В некоторых из них для безопасной работы сварщика предусмотрено либо ручное, либо автоматическое отключение тока в момент прекращения процесса сварки. Один из таких электрододержателей показан на рисунке 8.
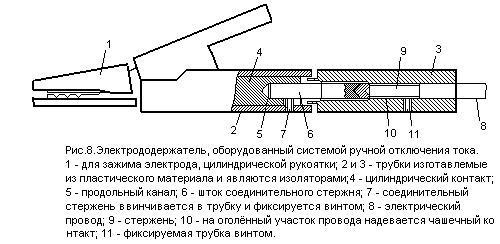
При ввинчивании стержня 9 в трубку до соприкосновения его с контактом, электрическая цепь от провода до цилиндрического контакта 4 замыкается. При одном-двух поворотах цилиндрической рукоятки стержень 6 вывинчивается из трубки 3 и образует зазор между ним и контактом 10, в результате чего электрическая цепь размыкается.
Щитки и маски (рис.9) применяются для предохранения глаз и кожи лица сварщика от вредного влияния ультрафиолетовых лучей и брызг расплавленного металла. Их изготовляют из лёгкого токонепроводящего материала (фибра, спецфанера).
Масса щитка или маски не должна превышать 0,6 кг. За процессом сварки наблюдают через специальные стёкла. Тёмные стёкла — светофильтры марки Э-1 применяют при величине тока до 70А, Э-2 – при величине тока до 200А, Э-3 — при величине тока 400А и Э-4 — при величине тока больше 400А. Для предохранения от брызг металла светофильтры марки ТС-3 закрывают прозрачным стеклом. Для работы в монтажных условиях лучше применять каску-маску, которая также надёжно защищает голову и удобна в эксплуатации как в летнее, так и зимнее время.
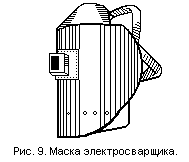
Сварочные провода. Ток от силовой сети подводится к сварочным аппаратам по проводам марки КРПТ. От сварочных аппаратов к рабочим местам сварочный ток поступает по гибкому проводу марки ПРГ, АПР, или ПРГД с резиновой изоляцией. К электрододержателю должен быть подключен гибкий медный провод марки ПРГД длиной не менее 3 м.
В таблице 2 приведены данные по выбору сечения гибких сварочных проводов.
Таблица -2
Сечение сварочного провода
Допускаемая величина, А | Сечение проводов, мм² | Допускаемая величина тока, А | Сечение проводов мм² | ||
одинарного | двойного | одинарного | двойного | ||
300 | 50 | 2*16 | 1000 | - | 2*70 |
Длина проводов от сварочных аппаратов к рабочему месту не должна быть более 30– 40м, так как при большей длине проводов напряжение в них значительно упадёт, что приведёт к уменьшению напряжения дуги. Для соединения сварочных проводов применяют специальные муфты (рис.10).
Сечение сварочного кабеля, присоединяющего источник питания к электрододержателю, подбирают в зависимости от наибольшей величины сварочного тока: при токе до 240А — 25 мм 2; до 300А — 35 мм2 , до 400А — 50 мм2 , до 500А — 70 мм2 . Гибкий (медный) кабель используют на напряжение до 220 В. В случае использования негибкого кабеля конец его, подсоединяемый к электрододержателю, длиной не менее 1,5-3м должен быть обязательно гибким. Общая длина сварочного кабеля должна быть не более 30-40м, так как при более длинном кабеле ухудшается процесс сварки из-за падения напряжения в сварочной цепи.
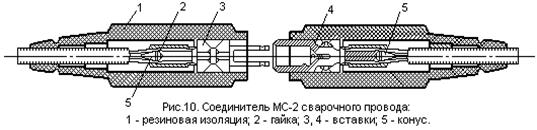
Для подсоединения сварочного кабеля к источнику питания используют специальный концевой соединитель заводского изготовления или приваренную к кабелю клемму. Сращивание коротких кусков кабеля осуществляют соединителями заводского изготовления (рис.10) МС-2, предназначенными для соединения кабелей сечением 35, 50 и 70 мм 2. Соединитель МС-2 состоит из двух частей, которые соединяются вставками и закрепляются поворотом одной из частей. Разъединение совершается аналогично закреплению поворотом в обратную сторону. Перед соединением к каждой половине соединителя прикрепляется сварочный кабель путём заклинивания жил его оголённой части между корпусом гайки, вставками и конусом. Соединитель покрыт резиновой изоляцией. Существуют другие типы соединителей, имеющих конструктивные особенности, принципиально не отличающиеся от МС-2.
Вспомогательный инструмент — в процессе работы сварщик пользуется инструментами для зачистки кромок от ржавчины и других загрязнений, а также для вырубки дефектов и зачистки швов от шлака. Для этого применяют металлическую проволочную щётку, зубило, молоток, комбинированное зубило с рукояткой, имеющее один заострённый конец, а другой конец в виде обычного зубила. Такая форма зубила удобна для очистки от шлака отдельных слоёв многослойного шва. Иногда применяют комбинированное зубило-щётку, но оно менее удобно, так как не имеет заострённого конца. У сварщика должно быть личное клеймо для клеймения выполненных швов.