ЭндРЮ АРо. Курсовой проект по дисциплине Технология и оборудование сварки плавлением
![]()
|
|
| С,% | Si,% | Mn,% | Cr,% | S,% | P,% |
Не более | ||||||
Сталь35 | 0,32-0,40 | 0,17-0,37 | 0,5-0,8 | 0,25 | 0,04 | 0,035 |
| σв , Н/мм2 | σт Н/мм2 | δ5, % | KCU Дж/см2 | Ψ, % |
Сталь 35 | Не менее | ||||
530 | 315 | 20 | 69 | 45 |
Таблица 2- Механические свойства стали 35
Основным легирующим элементом, определяющим механические свойства углеродистых сталей, является углерод. С повышением углерода увеличивается прочность и снижается пластичность. Чувствительность к перегреву и закаливаемости повышается, что снижает свариваемость. Марганец, кремний, сера, фосфор, кислород, водород и азот попадают в металл в процессе производства. Из них активными раскислителями являются марганец и кремний. Сера образует низкотемпературную эвтектику по границам зерен, что приводит к горячим трещинам при сварке. Фосфор, растворяясь в феррите, резко снижает пластичность стали и повышает хладноломкость. Содержание серы и фосфора в сталях для сварных изделий не должно превышать 0,035—0,040%. Кислород, образуя оксидные включения, охрупчивает сталь. Азот, образуя нитриды, также способствует охрупчиванию стали. Азот и кислород при сварке способствуют образованию пористости. Содержание их не должно превышать предела растворимости в данной стали. Водород при высоком содержании вызывает образование внутренних надрывов. При охлаждении стали ниже 2000С водород выделяется из твердого раствора и создает внутренние напряжения, приводящие к появлению трещин. Содержание газов в металлах снижается при выплавке и разливке в вакууме. Для конструкционных среднеуглеродистых сталей характерной особенностью является образование закалочных структур в шве и зоне термического влияния, создающих опасность хрупкого разрушения. Поэтому, для получения надежных сварных соединений, при изготовлении изделий из сталей этой группы необходимо выбирать марку стали не только исходя из показателей прочности основного металла, но и с учетом возможности получения необходимых стабильных механических свойств сварных соединений в условиях производства данного конкретного изделия и полной реализации этих свойств при работе конструкций. Содержание углерода более 0,30% способствует склонности сталей к перегреву и закалке, образованию горячих и холодных трещин в сварном соединений и пор в металле шва. Для предупреждения этих явлений необходимы усложняющие технологический процесс операции подогрева при сварке и термообработки после сварки. Образование холодных трещин при сварке закаливающихся сталей уменьшается:
при выборе способа и технологии сварки, обеспечивающих отсутствие грубодендритной закалочной структуры литого металла шва, минимальном перегреве зоны термического влияния и минимальных дополнительных растягивающих напряжениях при остывании шва за счет реакций связей;
при сварке с применением подогрева, уменьшающего вероятность образования закалочных структур;
при снижении содержания водорода в сварном соединении;
при отпуске после сварки.
Склонность к горячим трещинам сварных швов углеродистых конструкционных сталей определяется следующими факторами:
химическим составом металла шва, от которого зависит межкристаллитная прочность и пластичность в опасном
температурном интервале хрупкости (ТИХ);
величиной и скоростью нарастания растягивающих напряжений и соответственно деформаций в ТИХ;
величиной первичных кристаллитов;
формой сварочной ванны (шва), от которой зависит направление роста столбчатых кристаллитов, характер их срастания и расположение осей кристаллитов (или межкристаллитных участков) относительно направления растягивающих напряжений.
Качественные конструкционные стали, содержащие минимальное количество серы и фосфора (менее 0,035—0,025%), малочувствительны к горячим трещинам. Однако с повышением содержания углерода выше 0,25% чувствительность к горячим трещинам заметно возрастает. При этом, чем ниже содержание легирующих элементов, препятствующих образованию кристаллизационных трещин, которыми являются марганец, кислород, титан, хром и ванадий, тем выше склонность к трещинообразованию при одном и том же содержании углерода. В швах среднеуглеродистых сталей склонность к горячим трещинам резко падает при легировании марганцем до 1,8—2,5%.
4.1 Сведения о свариваемости
Свариваемость конструкционных углеродистых сталей можно определить как способность стали переносить тепловой режим при том или ином сварочном процессе без образования в соединении участков металла с пониженными пластическими свойствами, способствующими возникновению трещин при сварке конструкций или разрушению сварных соединений во время эксплуатации. Распад аустенита при охлаждении в условиях сварочного термического цикла начинается при более низких температурах и в некоторых случаях полностью не заканчивается даже при остывании до 20оС; при этом в структуре металла наряду с мартенситом остается нестабильный остаточный аустенит (в зависимости от уровня легирования). О свариваемости применительно к ее чувствительности к закаливаемости ориентировочно судят по коэффициенту эквивалентности по углероду для различных легирующих элементов:

, где С%, Mn%, Cr%, V%, Mo%, Ni%, Cu%, P% процентное содержание углерода, марганца, хрома, ванадия, молибдена, никеля, меди и фосфора соответственно. Стали с эквивалентом по углероду более 0,45 склонны к образованию трещин при сварке. Подсчет эквивалента углерода для стали 35 по верхнему и нижнему пределу


Сэ = 0,4705÷0,6005
Из расчета эквивалента углерода следует, что данная сталь склонна к образованию трещин при сварке, и требует предварительного и сопутствующего подогрева при сварке. В стали 35 содержание углерода превышает 0,30%, а это означает, что при быстром охлаждении металла в зоне термического влияния образуется твердая мартенситная или трооститная структура, значительно более хрупкая, чем основной металл, что создает опасность хрупкого разрушения как в процессе изготовления изделий (холодные трещины), так и при эксплуатации. С увеличением углерода также повышается опасность образования пористости сварных швах. Для предупреждения трещин при сварке следует применять предварительный подогрев, а после сварки – высокотемпературный отпуск для восстановления пластичности сварного соединения и снятия внутренних напряжений. Отпуск сварных конструкций снимает остаточные сварочные напряжения, улучшает структуру и свойства металла шва, снижает твердость закаленных зон сварного соединения и устраняет опасность образования холодных трещин со временем. Перерыв между началом сварки и термической обработкой устанавливают различный (от 30 мин до нескольких часов) в зависимости от марки стали и склонности ее сварных соединений к замедленному разрушению. Для предупреждения пористости следует использовать специальные электроды. Для повышения прочности изделий из стали 35 после сварке иногда подвергают упрочняющей термической обработке.
4.2 Подготовка под сварку
Качество сварных соединений в значительной степени определяется подготовкой поверхности свариваемых кромок и электродной проволоки. Перед сваркой тщательно удаляют жировую смазку, которой покрывают полуфабрикаты при консервации. Поверхность металла на ширине 10-15 мм от кромки обезжиривают ацетоном, авиационным бензином, уайт-спиритом или другими растворителями. Для щеток рекомендуется использовать проволоку из нержавеющей стали диаметром не более 0,15 мм. Зачистка кромок шабером и металлической щеткой предпочтительнее, так как не создает опасности загрязнения шва абразивом. Шабрение рекомендуется выполнять непосредственно перед сваркой. При разработке технологических процессов сварки среднеуглеродистых конструкционных сталей – сталь 35, для обеспечения надежных с заданными эксплуатационными характеристиками изделий необходимо предусматривать некоторые положения:
Правку, вальцовку, штамповку и другие операции формообразования свариваемых заготовок выполнять в отожженном состоянии.
2. Подготовку свариваемых кромок выполнять на металлорежущих станках (строгание, фрезерование, точение, резку на ножницах тонких листов), что обеспечивает необходимую точность сборки и отсутствие изменения структуры металла в месте реза. Газовую резку при подготовке кромок можно применять как
исключение в условиях монтажа крупногабаритных сооружений для сталей с прочностью до 1000МПа.
3. Поверхность металла в зоне сварки очищать от окалины, ржавчины и других загрязнений, а также от влаги. Перечисленные загрязнения создают условия для образования пористости, окисных включений, а в некоторых случаях и трещин в металле шва (за счет насыщения металла водородом). Зачистку производить на участке шириной не менее 10—15 мм как сверху, так и снизу свариваемых кромок, а также торца, если последний имеет окисленную поверхность. Зачистку производят, как правило, вручную щетками, или на пескоструйных и дробеструйных аппаратах.
4. В случае сварки деталей, упрочненных термической обработкой, особенно крупногабаритных, подготовку кромок под сварку (подрезку торца, выполнение разделки кромок) и их зачистку следует выполнять после термической обработки для обеспечения необходимых точности сборки свариваемых деталей и параметров шероховатости поверхности.
5. При сборке деталей под сварку обеспечивать надежное закрепление деталей относительно друг друга. При этом смещение кромок должно быть минимальным и не превышать 10—15% толщины свариваемых кромок. Зазоры между кромками должны быть минимальными и постоянными по величине за исключением специальных случаев сварки в щелевой зазор. Сварочные приспособления должны обеспечивать фиксирование свариваемых деталей, предупреждая изменение зазора и смещение кромок в процессе сварки .
6. При необходимости прихваток для фиксирования деталей в месте сварки их размеры и расположение должны обеспечивать необходимую прочность и возможность полной переварки при укладке основных швов. Прихватки выполняют с особой тщательностью, их металл не должен иметь пор и трещин. Кратеры прихваток должны быть заварены. Перед наложением основного шва прихватки необходимо тщательно зачищать. Перечисленные мероприятия не предотвращают полностью закалки металла в околошовной зоне, и для получения высоких пластичных и вязких свойств сварного соединения необходимо применять последующую термическую обработку—отпуск или закалку с отпуском, особенно при наличии соединений больших толщин. На среднеуглеродистых сталях удовлетворительное соединение можно получить всеми видами сварки, за исключением газовой. После сварки необходим отпуск при 650 °С; изделия сложной конфигурации и с толщиной стенок более 15 мм сваривают с предварительным подогревом до 200 °С. Сварку производят по возможности без перерывов. Ветер и сквозняк, а также низкая температура при сварке не допускаются. При возрастании тока увеличивается нагрев стали в зоне шва и замедляется, ее охлаждение. В результате этого сталь закаливается слабее. Однако повышенными режимами следует пользоваться с осторожностью, так как может возникнуть опасность значительного перегрева в околошовной зоне и образование горячих кристаллизационных трещин в шве из-за появления грубой дендритной структуры. Неровности шва, резкие переходы от шва к основному металлу, грубые проплавы и т. п. могут служить очагами появления трещин или приводить к хрупким разрушениям при нагружении изделия. Для улучшения формы перехода от шва к основному металлу, например, при сварке трубчатых конструкций с угловыми швами, применяют наложение дополнительных сглаживающих валиков газовой или аргонодуговой сваркой (сварка с усом). С этой же целью осуществляют и механическую обработку швов:
а) предварительную до сварки с целью снятия остаточных напряжений после гибки, штамповки и т. п. путем отжига или придания деталям перед сваркой соответствующих механических свойств с помощью закалки и отпуска;
б) промежуточную для устранения повышенной твердости шва и зоны закалки (с целью выполнения последующей правки) путем отпуска при 650—6800С и для предупреждения образования холодных трещин путем местного или общего отпуска при 200—600 0С;
в) окончательную для придания сварному изделию требуемых высоких механических свойств и улучшения структуры сварного соединения.
В случае повышенной склонности к образованию холодных трещин металла отдельных партий рекомендуется подогрев деталей (или кромок) перед сваркой до 200- 250 °С. Отпуск с помощью ТВЧ должен производиться не позднее чем через 15 мин после окончания сварки.
5 Сущность и схема сварки в СО2

Cхема сварки в СО2
1-деталь
2-дуга
3-защитный газ СО2
4-плавящаяся электродная проволока 08Г2С
5-сопло
6-сварочная ванна
Для получения при дуговой сварке в СО2 качественных соединений на сталях необходимы защита зоны сварки и расплавленной ванны от вредного воздействия воздуха, а также легирование и металлургическая обработка металла шва. При сварке в СО2 и его смесях защита зоны сварки осуществляется потоком СО2 или его смеси, подаваемым с помощью горелки у месту сварки. Источником нагрева при сварке в СО2 служит электрическая дуга, горящая между электродной проволокой, подаваемой в зону сварки, и изделием. Дуга, расплавляет кромки деталей и электродную проволоку, переходящую в виде капель на деталь, при этом образуется общая металлическая ванна. По мере перемещения дуги ванна затвердевает, образуя сварной шов, соединяющий кромки деталей. При сварке в СО2 используют электродную проволоку сплошного сечения, трубчатую, заполненную внутри легирующими и шлакообразующими веществами, называемую порошковой. При сварке в СО2 проволоками Св-08ГС и Св-08Г2С в основном используют процесс с частыми принудительными короткими замыканиями, которые получают при сварке в СО2 проволоками ø0,5-1,4мм путем программирования сварочного тока, обеспечивающего изменение скорости плавления электрода и давления дуги. Весь процесс можно разделить на ряд подобных повторяющихся циклов. Теплота,выделяемая дугой, интенсивно расплавляет электродную проволоку и деталь. При этом длина дуги быстро увеличивается.По мере уменьшения сварочного тока скорость расплавления проволоки и давление дуги уменьшаются. В результате капля электродного металла и ванночка приближаются друг к другу и замыкают разрядный промежуток. Дуга гаснет, напряжение резко уменьшается, а сила тока в цепи возрастает. С увеличением тока растет электродинамическая сила и приводит к ускорению перехода капли в ванну и образованию шейки между электродом и каплей. Утоненная шейка перегревается проходящим током и перегорает со взрывом. Напряжение резко возрастает, и зажигается дуга. После этого все явления повторяются.
6 Расчёт режимов сварки
Выбор режимов сварки изделия “Топливный бак” может осуществляться двумя путями:
Подбор режимов по специальной литературе;
Расчет режимов.
В данном дипломном проекте выбран расчет режимов.
В основу выбора диаметра электродной проволоки положены те же принципы, что и при выборе диаметра электрода при ручной дуговой сварке:
Для листа толщиной 2 мм выбираем диаметр электродной проволоки dэ=1,0 мм.
Расчет сварочного тока, А при сварке проволокой сплошного сечения производится по формуле:

где, j – плотность тока в электродной сварочной проволоке, А/мм2 (при сварке в среде СО2 j=110 – 130 А/мм2);
dэ – диаметр электродной проволоки, мм.

Механизированные и автоматизированные способы сварки позволяют применять большие плотности тока по сравнению с ручной дуговой сваркой. Это объясняется меньшей длиной вылета электрода.
Напряжение дуги и расхода углекислого газа выбирается в зависимости от сварочного тока. Напряжение дуги 20 В. Расход углекислого газа 10 л/мин.
Из специализированных литературных источников:
Сила сварочного тока 90-110 А;
Напряжение дуги 18-25 В;
Расход аргона 5-7 л/мин.
При сварочном токе 90 – 110 А длина дуги должна быт в пределах 1,2 ÷ 3,0 мм. Вылет электродной проволоки составляет 8 ÷14 мм (уменьшается с повышением сварочного тока).
Скорость подачи электродной проволоки , м/мин.
Рассчитывается по формуле:
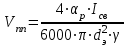
где, αр – коэффициент расплавления проволоки, г/А∙ч;
γ – плотность металла электродной проволоки, г/см3.

Значение αр рассчитывается по формуле:


Скорость сварки , м/мин.
Рассчитывается по формуле:
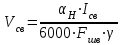
где, αн – коэффициент наплавки, г/А∙ч, он рассчитывается по формуле:
αн=αр∙(1 - ψ), (1.6)
где, ψ – коэффициент потерь металла на угар и разбрызгивание.
При сварке в среде СО2 ψ= 0,1 – 0,15;
Fшв – площадь поперечного сечения шва при однопроходной сварке (или одного слоя валика при многослойном шве), см2
γ – плотность металла электрода, г/см3.
αн=10,6∙(1 – 1,5)=12,2 г/А∙ч

Масса наплавленного металла, г.
При сварке рассчитывается по следующей формуле:

где, l - длина шва, см.

Время горения дуги, ч (основное время) определяется по формуле:
31


Полное время сварки, приближено определяется по формуле:

где, kп – коэффициент использования сварочного поста, (kп =0,6÷0,57).

Расход электродной проволоки, г рассчитывается по формуле:
Gпр=Gп∙(1+ψ), (1.10)
где, Gн – масса наплавленного металла, г;
ψ – коэффициент потерь, (ψ=0,1 – 0,15).
Gпр=178,8∙(1+0,15)=205,6г
7 Выбор сварочных материалов
Поскольку углекислый газ не является абсолютно нейтральным газом, то с целью уменьшения окислительного действия свободного кислорода применяют электродную проволоку с повышенным содержанием раскисляющих присадок (марганца - Г, кремния - С) типа Св-08ГС-0 или Св-08Г2С-0. Таким образом, достигают равнопрочности сварного шва и основного металла. Омеднение сварочной проволоки (индекс 0) гарантирует ее сохранность от коррозионного повреждения при хранении, обеспечивает надежный электрический контакт в токоподающем механизме аппарата, дает надежную дугу. При этом получается беспористый шов с хорошими механическими свойствами. Диаметр проволоки 0,8 мм выбран как оптимальный для сварки основных толщин металлов и нагрузок на сварочные полуавтоматы. Для сварки в защитных газах используется сварочная проволока. Сварочная проволока выбирается в соответствии с необходимыми требованиями к сварочному шву. Для сварки стали 35 была подобрана сварочная проволока ø1,0 мм и марки 08Г2С по ГОСТ 2246-70, ее состав приведен в таблице 2.
Таблица 3- Химический состав сварочной проволоки 08Г2С по ГОСТ 2246-70
| C, % | Si, % | Mn, % | Cr, % | Ni, % | S, % | P, % | |
| Не более | |||||||
08Г2С | 0,05-0,11 | 0,70-0,95 | 1,80-2,10 | 0,20 | 0,25 | 0,025 | 0,030 |
8 Конструкторская часть
8.1. Расчет и конструирование узла сборочно-сварочного приспособления
Сборочно-сварочными приспособлениями называются дополнительные технологические устройства к оборудованию, используемые для выполнения операций сборки под сварку, сварки, термической резки, пайки, наплавки, устранение или уменьшение деформации напряжений, а так же контроля. Сборочно-сварочные приспособления бывают ручными, механизированными и автоматизированными. По приводу приспособления делятся на пневматические, гидравлические, ручные, электромеханические и др.
Сборочно-сварочные приспособления классифицируются по нескольким признакам:
- по выполняемым операциям технологического процесса в сварочном производстве - приспособления для разметки, термической резки, сборки под сварку, сварки и для контроля;
- по виду обработки и метода сварки - приспособления для электродуговой сварки, электрошлаковой сварки, контактной сварки, наплавки, пайки и др.;
- по степени специализации- приспособления специальные, универсальные, переналаживаемые, специализированные;
- по уровню механизации и автоматизации - приспособления ручные, механизированные, полуавтоматические и автоматические;
- по виду установки- приспособления стационарные, передвижные, переносные;
- по необходимости и возможности поворота - поворотные и неповоротные;
- по источникам энергии привода вращения, перемещения, зажатия детали-приспособления пневматические, гидравлические, электромеханические и др.
Применение сборочно-сварочных приспособлений позволяет уменьшить трудоемкость работы, повысить производительность труда, сократить длительность производительного цикла, улучшить условия труда, повысить качество продукции, расширить технологические возможности сварочного оборудования, способствует повышению комплексной механизации и автоматизации производства.
К конструкциям сборочно-сварочных приспособлений предъявляется целый ряд требований:
- удобство в эксплуатации;
- обеспечение заданной последовательности сборки и наложения швов в соответствии с разработанным технологическим процессом;
- обеспечение заданного качества сварного изделия;
- обеспечение сборки всей конструкции с одной установки, наименьшего числа поворотов при сборке и прихватке, свободного съема собранного изделия;
- технологичность детали и узлов приспособления, а также применения приспособления в целом;
- использование механизмов для загрузки, подачи и установки деталей, снятия, выталкивания и выброски собранного изделия.
Приспособление должно быть ремонтоспособным, безопасным в эксплуатации, иметь достаточно высокий срок службы, для этого следует предусмотреть возможность замены быстро изнашиваемых деталей и восстановления требуемой точности приспособления. Базирование называют определение положения деталей в изделии относительно друг друга или изделия относительно приспособления, рабочего инструмента, технологичности сварочного оборудования. Установочной базой следует считать каждую поверхность детали, которой она соприкасается с установочными поверхностями приспособления. Любое твердое тело имеет 6 степеней свободы: перемещение в направлении трех координатных осей x y z и вращения относительно этих же осей wx, wy, wz. Для базирования любой детали требуется выполнять правило 6 точек: чтобы предать детали в полнее определенное положение в приспособлении, необходимо и достаточно иметь 6 точек опоры, лишающих деталь всех 6 степеней свободы. Силой замыкания с помощью прижимов предусматривают для предупреждения смещения деталей в результате температурного расширения металла от случайных нагрузок и от собственной массы. При установки деталь не допустимо использовать более 6 опорных точек. Лишние опорные точки препятствуют правильной установки детали, при закреплении ее, положение нарушается. Поверхность детали с тремя опорными точками называются главной базирующей; боковая поверхность - направляющей; торцевая поверхность с одной точкой - упорной. В качестве главной базирующей поверхности желательно выбирать, имеющую наибольшие габаритные размеры, а в качестве направляющей- поверхности наибольшей протяженности. Выполняем базирование детали исходя из выше указанных требований к приспособлениям. В сборочно-сварочном приспособлении чаще всего применяется прижимы с механическим, пневматическим, гидравлическим, магнитным или электромеханическим приводом.
По степени механизации зажимы делят на:
- ручные - работающие от мускульной силы рабочего;
- механизированные – работающие от силового привода, управляемого вручную;
- автоматизированные – осуществляющие зажим и закрепление деталей и узлов без участия рабочего.
Различные конструкции зажимов имеют разное время срабатывания и закрепления (открепления) деталей. Закрепляемые детали должны находиться в равновесии под действием всех сил фиксаций, а также сил, возникающих в процессе сварки, и реакции опор. Изготовление качественных сварных швов зависит от целого ряда факторов технологической системы. Одной из основных причин появления брака могут быть неквалифицировано выбранные и спроектированные силовые узлы сварочных приспособлений.
Основные требования, предъявляемые к силовым узлам:
1. Силовые узлы в процессе зажима не должны нарушать положения детали, заданное ей при базировании.
2. Силовые узлы должны полностью исключить возможность перемещения обрабатываемой детали под действием сил резания.
Выбрав способ установки детали и разместив установочные элементы в приспособлении, определяем величину, место расположения и направление сил для зажима обрабатывавемой детали. Выбрав конструкцию зажимных устройств, подбираем конструкцию привода для их перемещения при зажиме и разжиме детали в приспособлении. Величину сил зажима и их направление определяют в зависимости от сил резания и их моментов, действующих на обрабатываемую деталь. Для данной детали применяется поршневой пневмомезанизм. При зажиме детали перемещаются два поршня.
Преимущества данного механизма:
- незначительно вспомогательное время, необходимое для фиксации и освобождения детали;
- не требуется больших физических усилий рабочими:
- постоянство сил зажима;
Для технологичной и быстрой работы вводим в приспособление электропривод для поворота приспособления на угол 90 град..
Основным назначением силового привода в приспособлении является создание исходной силы тяги W, необходимой для прижима ,бака силой Q. Кроме того, силовые приводы используют для механизации и автоматизации приёмов загрузки и выгрузки заготовок, поворота приспособления, включения и выключения робота и др. Силовой агрегат привода представляет собой преобразователь какого-либо вида энергии в механическую, необходимую для работы зажимных механизмов. В связи с этим приводы классифицируют по виду преобразуемой энергии. В данном приспособлении используются два пневмопривода. Пневмопривод широко используется в приспособлениях благодаря его быстродействию, простоте конструкции, лёгкости управления, надёжности и стабильности в работе. Вместе с тем пневмопривод имеет недостатки: неплавное перемещение штока, большие габариты силовых агрегатов, шум при выпуске отработанного воздуха. Исходной энергией в пневмоприводах является энергия сжатого воздуха. В данном приспособлении силовым узлом служит поршневой пневмоцилиндр. Сжатый воздух из системы попадает через штуцер 3 (рисунок 2) внутрь цилиндра и давит на шток 2. Шток под давлением воздуха перемещается и давит на зажимные элементы приспособления. Рабочий ход поршня в цилиндре 80 мм. Данный цилиндр двустороннего действия, то есть для разжима заготовки воздух подаётся в штуцер 4 и поршень перемещается обратно. Для жёсткого и безвибрационного закрепления бака учитывая, усилие, возникающее при сварке в приспособлении, усилие на каждом штоке должно быть не менее 582Н, исходя из этого находим диаметр поршня:
W=р*п*D2/4*η1* η2
р-давление сжатого воздуха в сети (6Н/см2),
D-диаметр поршня,
η1-КПД поршня цилиндра (0,8),
η2-КПД одного зажимного элемента (0,75),

Из стандартного ряда подбираем диаметр поршня 276 мм.

Рисунок 2 - Пневмоцилиндр
1- корпус цилиндра, 2- шток, 3,4- штуцеры;
8.2 Описание работы автоматизированной линии сборки и сварки топливных баков
Автоматизированная линия производства топливных баков автомобиля ЗИЛ-4331 имеет два параллельных участка (рисунок 3). Первый участок загружается верхними половинками бака, а второй является основным, который продвигает заготовки по всему технологическому процессу. Сварочное оборудование расположено между двумя этими участками. Для переноса заготовок с первого участка на второй, а также для переноса заготовок на сварочные операции и обратно со сварочных операций на поточную линию используются два портальных манипулятора типа МРЛ-901П. Также линия обеспечена автоматической системой контроля, с помощью датчиков движение линии на одну позицию осуществляется только после полной установки заготовки манипулятором на приспособление-спутник после сварочной операции.
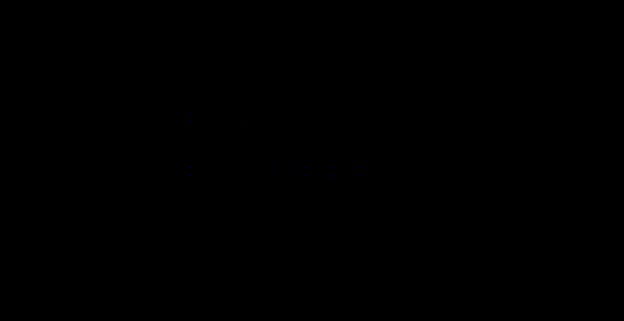
Рисунок 3 - Компоновка автоматизированной линии.
Важнейшим эксплуатационным требованиям для сварных изделий замкнутых объемов (баки, цистерны, резервуары, газопроводы и т.д.) являются герметичными. В данном дипломном проекте разрабатывается изготовление Топливного бака, который также должен быть герметичным. Герметичность – это способность сварного изделия сохранять в рабочих условиях начальное количество содержащихся в изделии вещества. Контроль герметичности сварных изделий основан на проникании пробных веществ (газов и жидкостей) через сквозные дефекты (течи) и их регистрации с помощью различных приборов, например, течеискателей, и других средств регистрации индикаторных веществ. Под газом понимают физическое тело, молекулы которого модно представить как упругие материальные частицы и силы межмолекулярного воздействия, между которыми отсутствуют, а объем, занимаемый собственно молекулами, мал по сравнению с объемом, свободным от молекул. Под жидкостью понимают физическое тело, обладающее текучестью, крайне мало изменяющее свою плотность при изменении давления, в силу чего не имеющее постоянной формы и принимающее форму, в которую ее помещают. Методы и способы контроля герметичности сварных соединений с точки зрения эффективности их использования позволяют проводить как качественную, так и количественную оценку утечки, в данном случае жидкости. Течь – это канал или пористый участок изделия или его элементов, нарушающих их герметичность. Как правило, малые характерные размеры течей исключают возможность их визуального наблюдения или обнаружения всеми другими методами дефектоскопии, кроме методов проникающих веществ. Контроль герметичности сварных соединений проводят в тех случаях, когда изделия предназначены для работы под давлением газов или жидкостей. Существующие в настоящее время методы контроля герметичности, определяющие утечку пробного вещества через различные несплошности, можно условно подразделить на газовые, жидкостные, газожидкостные и технологические. Для контроля герметичности изделия Топливный бак выбираем пузырьковый метод испытаний. Этот метод основан на регистрации локальных утечек по появлению пузырьков газа. Применяют три варианта пузырькового метода: пневматический, пневмогидравлический , вакуумный. В дипломном проекте будет использоваться пневмогидравлический метод. Его применяют для замкнутых сосудов небольших объемов. Контрольный газ (воздух, азот) подают под избыточным давлением в сосуд с последующим погружением его в индикаторную жидкость (обычно в воду), где наблюдают за образованием пузырьков.
Выводы
В данной курсовой работе рассмотрены вопросы, посвящённые модернизации технологии и разработки нового автоматического оборудования для сварки горловины топливного бака автомобиля ЗИЛ 4331. Произведено сравнение способов сварки горловины топливного бака: ручная дуговая сварка в СО2, сварка в инертных газах, полуавтоматическая дуговая сварка в среде СО2.
Приведена оценка свариваемости стали 35 и выбран оптимальный режим свариваемости.
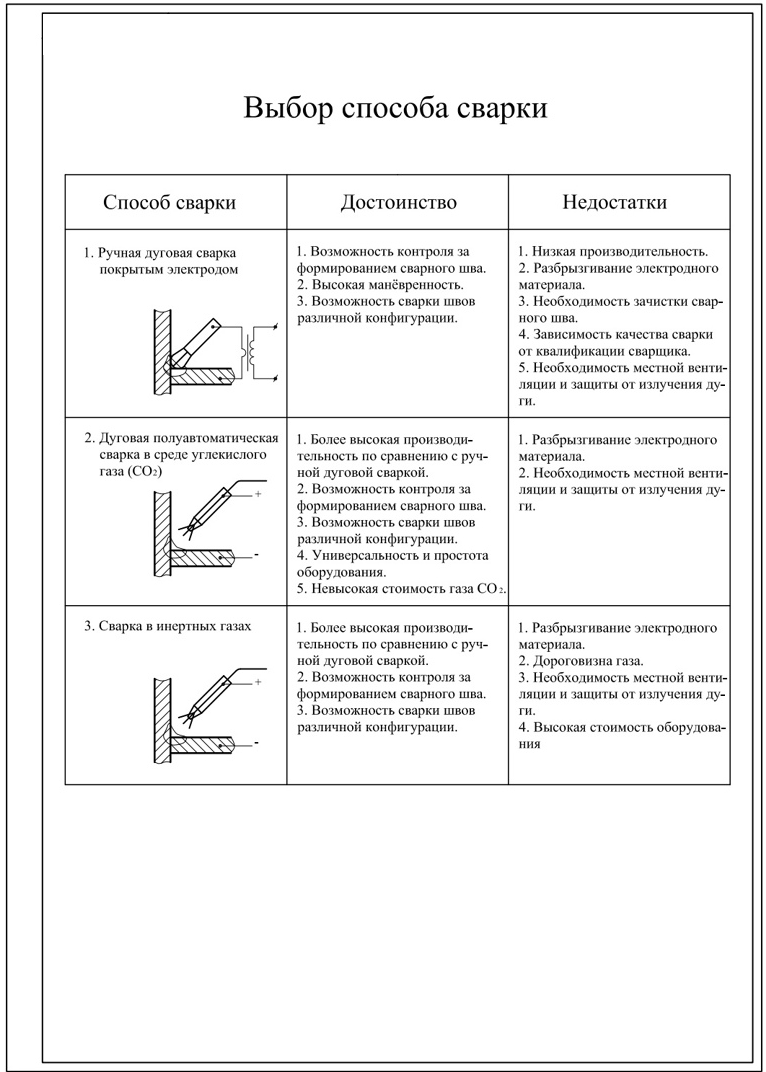
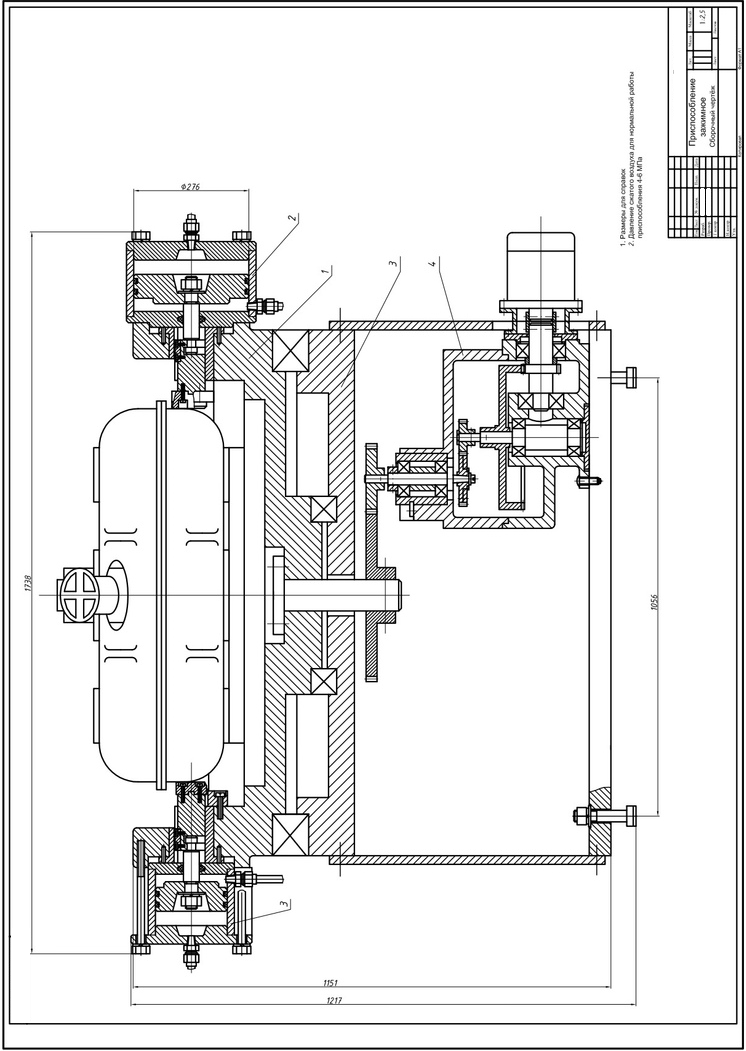
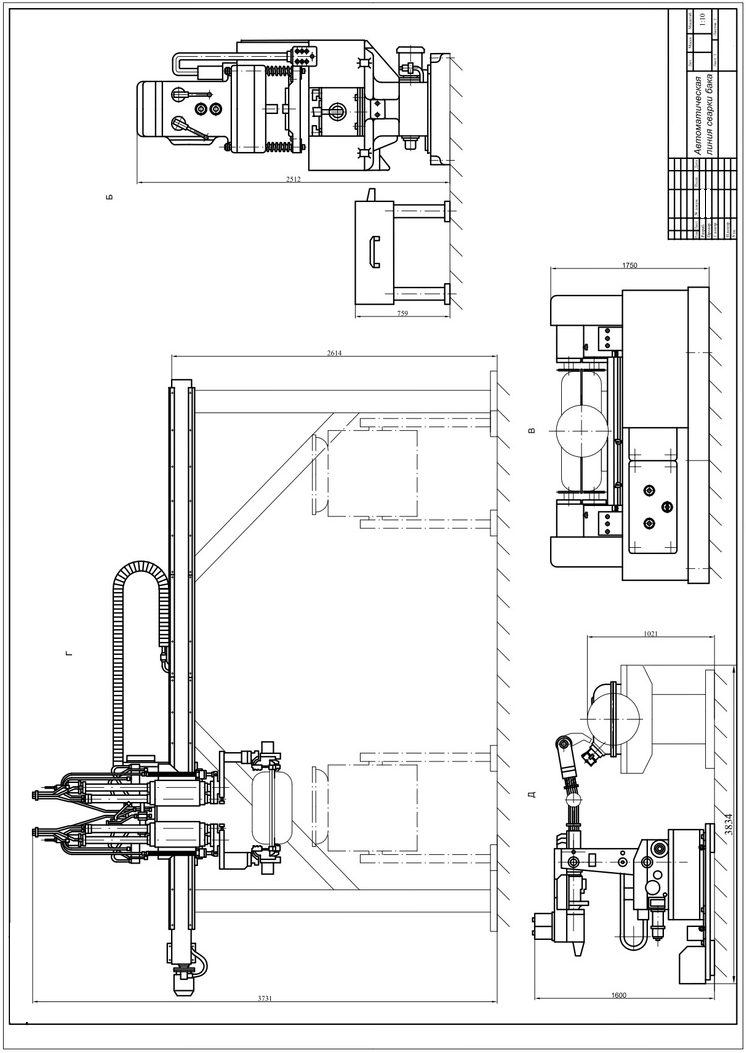
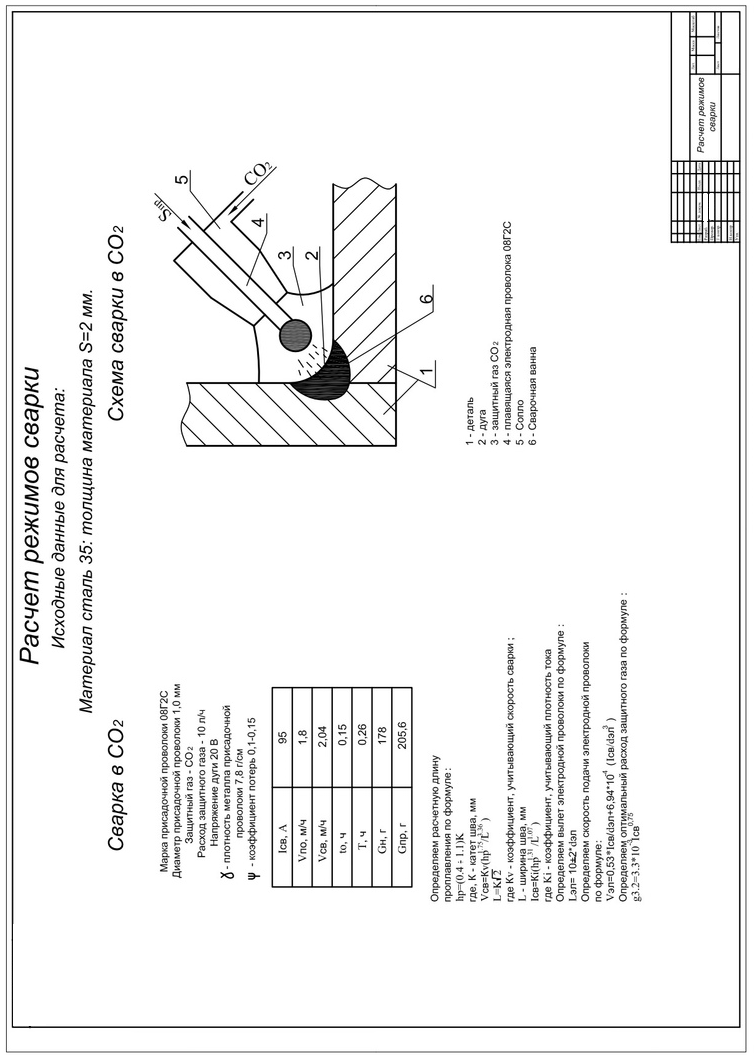

Список используемой литературы
1. Думов С.И. – «Технология электрической сварки плавлением » - М : Машиностроение, 1987г.
2. Куркин А.С «Сварочные конструкции» - М: Машиностроение, 1991г.
3. Китаев А.М «Сварочная книга сварщика » - М: Машиностроение, 1985г.
4. Рыморов К.С «Механизация и автоматизация сварочного производства» - М: Машиностроение, 1990г.
5. Потапьевский А.Г. Сварка в углекислом газе.- М.: Машиностроение, 1984г.
6. “Дуговая сварка в защитном газе”-ГОСТ 14771-76
7. Сварка и свариваемые материалы: В 3-х т. Т. II. Технология и оборудование. Справ. Изд. /Под ред. В.М. Ямпольского. -М.: Изд-во МГТУ имени Н.Э. Баумана,1998г.