инженерка. Отчёт по итогам практики уп. 05 Выполнение работ по профессии электросварщик ручной сварки в рамках специальности 22. 02. 06 Сварочное производство при освоении профессиональных модулей пм.
![]()
|
|
Марка | С | Si | Mn | Cr | Ni | N | Cu | Прочие элементы | |
S | P | ||||||||
Сталь Ст3 | 0,14 | 0,15–0,3 | 0,4–0,65 | До 0,3 | 0,5-0,8 | До 0,008 | До 0,3 | До 0,05 | До 0,04 |
Таблица 2 – Механические свойства используемой стали
Марка | Тип термообработки | σ0,2, Н/мм2 | σв, Н/мм2 | δ, % | КСU, Дж/см2 |
Сталь Ст3 | Листовой прокат, горячекатаный | 400 | 540 | 21 | 50 |
Расшифровка
C | 0,14 - 0,22 |
Si | 0,15 - 0,3 |
Mn | 0,4 - 0,65 |
Ni | до 0,3 |
S | до 0,05 |
P | до 0,04 |
Cr | до 0,3 |
N | до 0,008 |
Cu | до 0,3 |
As | до 0,08 |
Fe | 97 |
4.2. Характеристика сварочных материалов.
4.2.1 Сварочная проволока Св08Г2С.
Сварочные проволока «Св08Г2С» Чаще всего проволока СВ08Г2С применяется при проведении работ на сварочных автоматах и полуавтоматахв промышленных условиях. Применяя ее, можно проводить ручную сварку различных изделий из стали. Применяя этот расходный материал, можно получить сварное соединение высокого качества. Шов получается ровным и чистым.
Для сварки сталей углеродистых, низколегированных, относящихся к группе 1 с классом прочности до К54. Использование данной проволоки снижает риск «залипания» электрода и уменьшает интенсивность разбрызгивания металла. Обеспечивается возможность работы с различными видами сварочного оборудования.
4.2.2 Электроды.
УОНИ 13/55
Данный тип обладает большими преимуществами, которые востребованы в строительных условиях. Ведь здесь могут возникать достаточно большие нагрузки, а так как шов всегда является самым слабым местом, то надежность соединения должна быть максимально высокой. Эта марка используется для сварки изделий из углеродистой и низкоуглеродистой стали. Сварочные электроды УОНИ-13 55 обладают достаточно высокими показателями по вышеприведенным пунктам. Область применения здесь очень широка, так как электроды УОНИ-13 55 характеристики имеют удобные практически для всех отраслей. Их можно встретить и в домашних условиях, и на строительных объектах. Лучше всего они подходят для соединения стальных металлоконструкций, так как состав наплавленного металла максимально схож с обыкновенной сталью. Соединение обладает длительным сроком эксплуатации, что подходит для строительной сферы. С помощью ремонтируют различные изделия, заваривают герметичные емкости, резервуары и трубы. Процесс проходит качественно и просто, что только повышает восстребованность.
Тип соединения: - ручной дуговой сваркой, постоянным током обратной полярности. Покрытие (обмазка) – основное. Диаметры электродов от 2 до 5 мм. Преимущества: получение прочного сварного шва, увеличение наплавки на 10%.
ОК – 46
Сварочные электроды ОК – 46 предназначены для сварки низколегированных и низкоуглеродистых сортов стали с пределом текучести до 380 МПа.
Сварку данными электродами производят во всех пространственных положениях, переменным и постоянным током любой полярности. Электроды ОК – 46 можно смело назвать универсальными.
Изготавливают диаметром 6 2, 2.5, 3, 4, 5.
Покрытие: рутил - целлюлозное;
Стержень электрода: стальная сварочная проволока Св08 (Св08А)
5. Описание основного и технологического оборудования
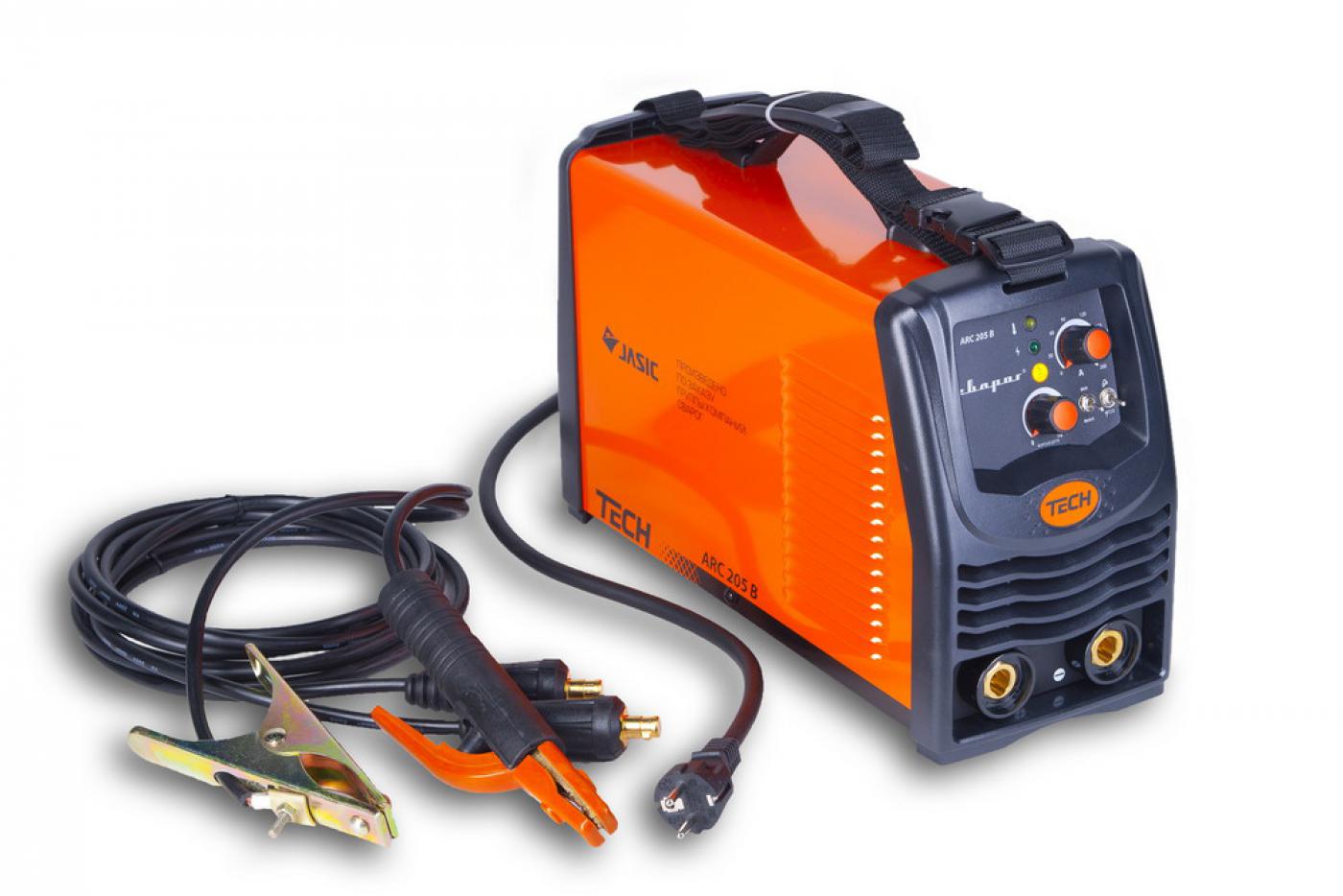
Сварог TECH ARC 205 B (Z203)-инверторный сварочный аппарат. Диапазон сварочного тока от 10 до 200 ампер.
Аппарат предназначен для ручной дуговой сварки (MMA) и наплавки покрытым штучным электродом, а так-же ручной дуговой сварке (TIG) и наплавки неплавящимся электродом в среде инертных газов и газовых смесей. Важным отличием аппарата является VRD – функция снижения напряжения холостого хода.
Особенности этого сварочного инвертора – это высокий КПД, универсальность, мобильность, наличие режима снижения холостого хода, стабильность горения и саморегулирования мощности дуги.
Электроды MMA: диаметром от 1,5 до 5,0 мм.
Электроды TIG: диаметром от 1,0 до 3,0 мм.
Вес: 8кг.
Габаритные размеры: 410х160х260 мм.
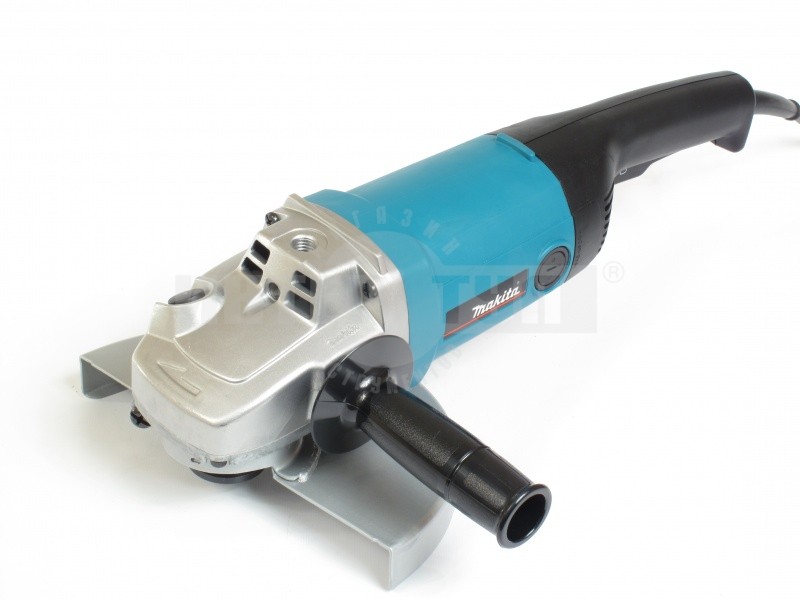
УШМ Угловая шлифовальная машина Makita 9069. Надёжна и идеальна для отрезных, зачистных, шлифовальных работ.
Технические характеристики:
Чистота холостого хода, об/мин - 6600
Габаритная длинна - 458мм
Мощность, Вт - 2000
Диаметр отрезного круга - 230мм
Диаметр шлифкруга с вдавленной центральной частью - 230 мм
Диаметр чашечной проволочной щётки – 110мм
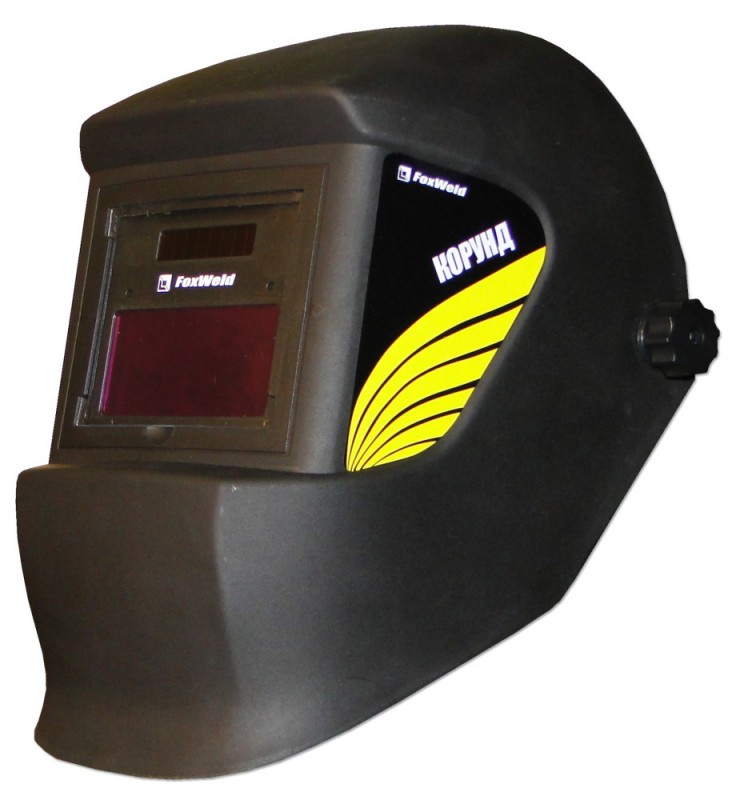
Сварочная маска – средство индивидуальной защиты, используемое при выполнении определённых видов сварки, для защиты глаз, лица и шеи от ожогов, ультрафиолетового излучения, искр, инфракрасного света и высоких температур. Чаще всего используется во время электродуговой сварки, сварки неплавящимся электродом и полуавтоматической сварки в защитных газах. Основная часть масок имеет смотровое окошко со светофильтром, через который сварщик видит процесс сварки.
6. Дефекты, причины их возникновения и методы контроля качества.
6.1 Причины возникновения дефектов швов сварных соединений.
Причинами возникновения дефектов сварных швов являются нарушения технологического процесса при подготовке, сборке, сварке, термообработке соединяемых узлов, а также небрежностью и низкой квалификацией сварщика.
Дефекты сварных соединений подразделяются на шесть групп:
трещины;
полости, поры, свищи, усадочные раковины, кратеры;
твердые включения;
несплавления и непровары;
нарушения формы шва (подрезы, усадочные канавки, превышения выпуклости, превышения проплава, наплавы, смещения, натеки, прожоги);
прочие дефекты.
6.2 Виды и методы контроля качества швов сварных соединений.
Под контролем качества сварки подразумеваются проверка условий и порядок выполнения сварочных работ, а также определение качества выполненных сварных соединений в соответствии с техническими требованиями.
В сварочном производстве применяют следующие виды контроля: входной (предупредительный), текущий (пооперационный) и приемочный (выходной) готовых изделий и узлов.
Цель входного контроля – уменьшить вероятность возникновениябрака при выполнении сварочных работ (контроль документации, качества исходных и сварочных материалов, квалификации сварщиков и т. д.).
Текущий контроль осуществляется в процессе сборочно-сварочных работ.
Приемочный, или выходной контроль, осуществляется для выявления наружных и внутренних дефектов сварки.
Различают разрушающие и неразрушающие методы контроля качества сварных соединений.
6.2.1 Разрушающие методы контроля качества сварных соединений.
Разрушающие испытания проводят на образцах-свидетелях, моделях и реже на самих изделиях для получения информации, прямо характеризующей прочность, качество или надежность соединений. К их числу относятся: механические испытания, металлографические исследования, химический анализ и специальные испытания. Эти методы применяют главным образом при разработке технологии изготовления металлических конструкций или для выборочного контроля готовой продукции.
6.2.2 Неразрушающие методы контроля качества сварных соединений.
При неразрушающих испытаниях оценивают те или иные физические свойства, косвенно характеризующие прочность или надежность сварного соединения. Неразрушающие методы (ими проверяется более 80 % сварных соединений) применяют, как правило, после изготовления изделия для обнаружения в нем дефектов. К неразрушающим методам контроля качества сварных соединений относятся: внешний осмотр, радиационный, ультразвуковой и магнитный контроль, контроль на непроницаемость и ряд других методов, имеющих ограниченное применение.
6.2.3 Магнитографический контроль.
Основан на обнаружении полей рассеивания, образующихся в местах расположения дефектов при намагничивании контролируемых сварных соединений (рис. 3). Поля рассеивания фиксируются на эластичной магнитной ленте, плотно прижатой к поверхности шва. Запись производят на дефектоскопе. Магнитографический контроль можно применять только для проверки сварных соединений металлов и сплавов небольшой толщины, обладающих ферромагнитными свойствами. Выявляют поверхностные и подповерхностные макротрещины, непровары, поры и шлаковые включения глубиной 2...7 % на металле толщиной 4...12 мм. Менее четко обнаруживаются поры округлой формы, широкие непровары (2,5...3 мм), поперечные трещины, направление которых совпадает с направлением магнитного потока.
6.2.4 Ультразвуковой контроль.
Основан на способности ультразвуковых колебаний (механические колебания частотой 16...25 МГц) отражаться от поверхности, разделяющей среды с разными акустическими свойствами. Для получения ультразвуковых колебаний используют свойство титаната бария, кристаллов кварца и некоторых других веществ преобразовывать электрические колебания в механические и наоборот (обратный и прямой пьезоэффекты).Ультразвуковой контроль имеет определенные преимущества перед радиационными методами: высокую чувствительность (площадь обнаруживаемого дефекта 0,2...2,5 мм² при толщине металла до 10 мм и 2...15 мм² при больших толщинах), возможность контроля при одностороннем доступе к шву, высокую производительность, возможность определения точных координат залегания дефекта, мобильность аппаратуры.
6.3. Способы устранения дефектов .
В случае со стальными конструкциями испорченную поверхность срезают (плазменно-дуговая сварка), тщательно зачищают место неудачного соединения, а затем повторяют попытку. Если имеются незначительные внешние дефекты сварных швов (неравномерность соединения, неглубокие оспины), то их можно попросту зашлифовать. Если речь идет об изделиях из легированной стали, которые должны пройти обязательную термическую обработку, то исправление дефектов сварных швов должно производиться толькопосле отпуска в температурном диапазоне от 450 до 650 °С.Если имеется прожог, то устранение дефектов сварных швов провести довольно просто: сперва поверхность как следует зачищается, а затем ее повторно проваривают. Приблизительно так же поступают и с кратерами.Проще всего исправлять наплывы и механическую неравномерность шва. В таком случае место соединения просто зачищают. Об исправлениях подрезов мы уже говорили выше, но еще раз заметим – с такими дефектами деталь более целесообразно сразу выбраковать, так как ее эксплуатация может быть опасна.
Заключение.
В процессе практики, я успешно применил полученные знания на практике. Научился выполнять процесс сварки в нижнем, под наклонном в 450, вертикальном, горизонтальном и потолочном положении. А также изучил процесс сваривания материала из высокоуглеродистых и низкоуглеродистых сталей. В период практики по получению первичных профессиональных навыков изучил вопросы подлежащие изучению.
Все выполненные упражнения и сварочные работы занесены в дневник. Дневник прилагается к отчету, для проверки руководителем практики от колледжа и предприятия.