Представить свойства литейных оловянных бронз. Описать влияние легирующих элементов 3
![]()
|
|
Марка бронз | Химический состав (Сu- основа; примеси 0,04— 0,07), % | в Мн/м2 | . % | НВ, Мн/мг | Назначение | |
Sn | прочие | |||||
Бр.ОФ6,5-0,15 | 6—7 | 0,1—0,25Р | 350—450 | 60—70 | 700—900 | Ленты, полосы, прутки, проволока для пружин, подшипниковые детали |
Бр.ОФ4-0,25 | 3,5—4,0 | 0,2—0,3 Р | 340 | 52 | 550—700 | Трубки, применяемые в аппарато- строении и для контрольно - измерительных приборов |
Бр.ОЦ4-3 | 3,5—4,0 | 2,7—3,3 Zn | 350 | 40 | 600 | Ленты, полосы, прутки, проволока для пружин и аппаратуры в химической промышленности |
Бр.ОЦС4-4-2,5 | 3—5 | 3—5 Zn 1,5—3,5 Pb | 300—350 | 35—45 | 600 | Ленты и полосы для прокладок во втулках и подшипниках |
Таблица 2 - Химический состав, механические свойства и назначение литейных оловянных бронз
Марка бронз | Химический состав (Сu- основа; примеси 0,04— 0,07), % | в Мн/м2 | . % | НВ, Мн/мг | Назначение | ||
Sn | Zn | Pb | |||||
Бр.ОЦСН3-7-5-1 | 2,5—4,0 | 6,0—9,5 | 3,0—6,0 (0,5- 2,0 Ni) | 180—210 | 8—5 | 600 | Арматура, работающая в морской и пресной воде, маслах и других слабокоррозионных средах, а также в парах под давлением до 25 кгс/см2, антифрикционные детали |
Бр.ОЦСЗ-12-5 | 2.0—3,5 | 8,0-15 | 3,0—6,0 | 180—210 | 8—5 | 600 | Арматура, работающая в пресной воде и парах под давлением до 25 кгс/с2, антифрикционные детали |
Бр.011С5-5-6 | 4,0—6,0 | 4,0—6,0 | 4,0—6,0 | 150—180 | 6—4 | 600 | антифрикционные детали |
Бр.ОЦС4-4-17 | 3,5—5,0 | 2,0—6,0 | 14,0—20,0 | 150 | 5 | 600 | |
Вр.ОЦСЗ, 5-7-5 | 3,0—4,5 | 6,0—9,5 | 3,0—6,0 | 150—180 | 6—4 | 600 ) | |
На рис. 1 показано изменение механических свойств оловянистых бронз в зависимости от содержания Sn. Так, при 5% Sn падает пластичность, а при 25% Sn уменьшается прочность, т. е. при максимальной хрупкости бронз вследствие преобладания -фазы. Добавкой 5—10% Zn обеспечивается экономичность бронз (в таких количествах Zn эффективно растворяется в Сu и не влияет на структуру бронз).
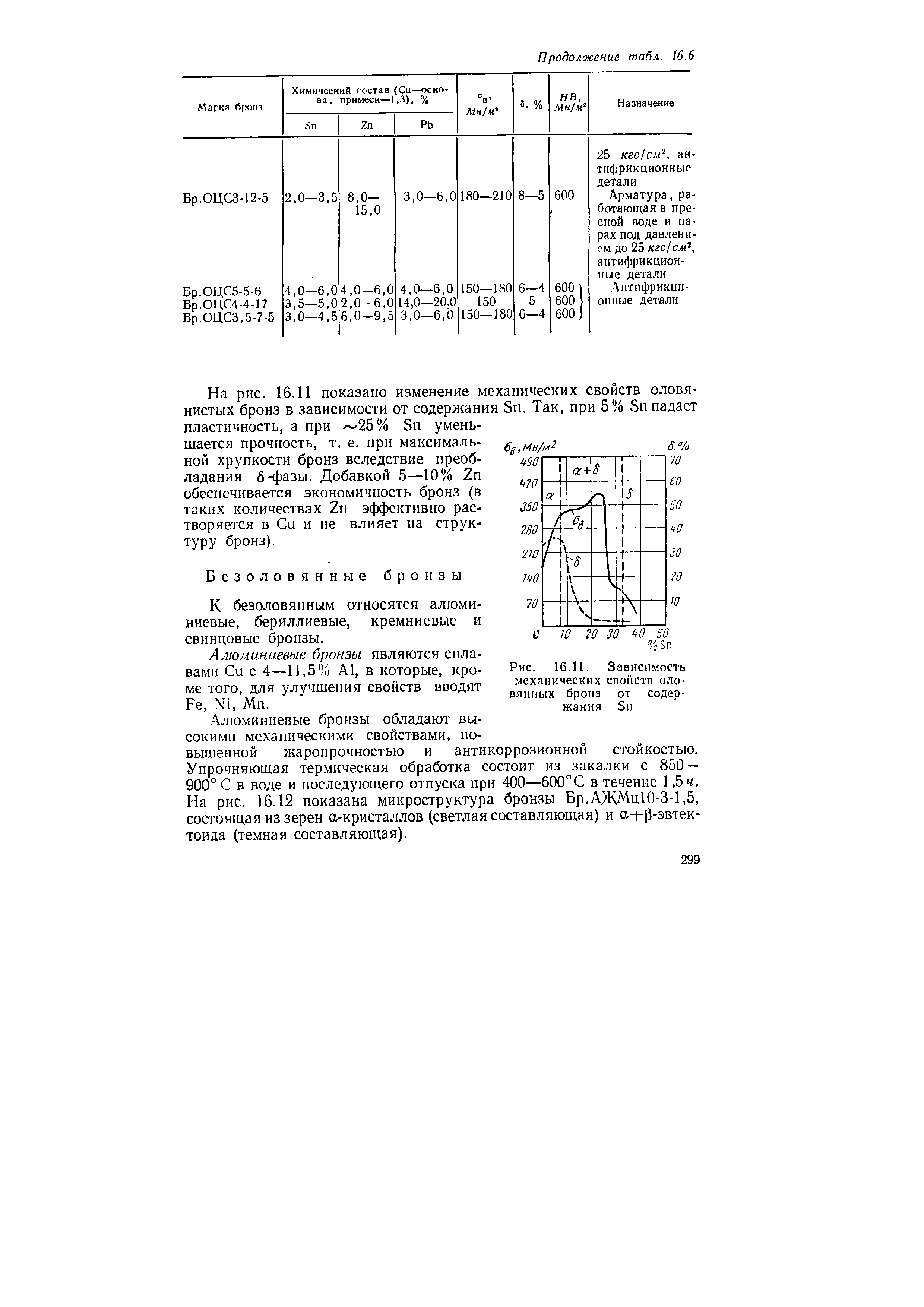
Рисунок 1- Зависимость механических свойств оловянных бронз от содержания Sn
Описать термодинамику процесса кристаллизации металлов
При фиксированных значениях внешнего давления P и абсолютной температуры T энергетическое состояние любой физикохимической системы1 характеризуют свободной энергией Гиббса: G = H — TS, где Н и S — энтальпия и энтропия системы соответственно. Энтальпия характеризует полную энергию (теплосодержание) системы и определяется суммой U + PV , где U и V — внутренняя энергия и объем системы. Произведение T х S характеризует так называемую связанную энергию, необходимую для существования системы. Таким образом, по физическому смыслу свободная энергия Гиббса — это тепло, которое в данных условиях (T, P = const) может быть выделено из системы и превращено в работу. Если система предоставлена самой себе (т.е. находится в неизменных внешних условиях), в ней могут протекать только те процессы и превращения, которые приводят эту систему в более устойчивое состояние с меньшим запасом свободной энергии.
В частности, самопроизвольный переход системы из состояния A в состояние B возможен лишь в том случае, когда G = GB - Ga < 0 . В конечном итоге система должна достигнуть наиболее устойчивого состояния с минимальной энергией Гиббса. Такое состояние системы называют равновесным.
Переход металла из жидкого состояния в кристаллическое (при охлаждении) называют кристаллизацией, обратный переход (при нагреве) - плавлением. Объемный эффект этих превращений составляет 2-6 %. Иначе говоря, объем металла при плавлении или кристаллизации почти не меняется.
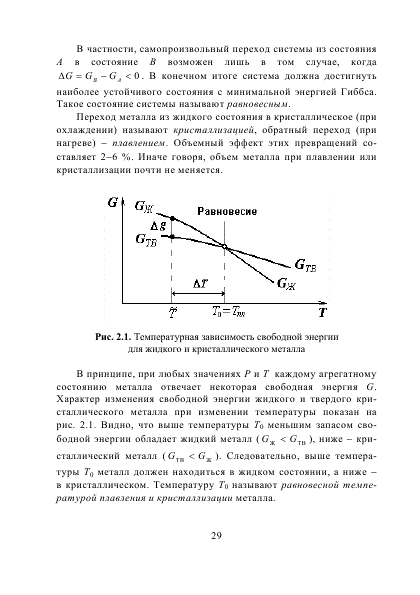
Рисунок 2 - Температурная зависимость свободной энергии для жидкого и кристаллического металла
В принципе, при любых значениях P и T каждому агрегатному состоянию металла отвечает некоторая свободная энергия G. Характер изменения свободной энергии жидкого и твердого кристаллического металла при изменении температуры показан на рис. 2. Видно, что выше температуры Т0 меньшим запасом свободной энергии обладает жидкий металл (Gx < Gтв), ниже - кристаллический металл (Gтв < Gx). Следовательно, выше температуры T0 металл должен находиться в жидком состоянии, а ниже - в кристаллическом. Температуру Т0 называют равновесной температурой плавления и кристаллизации металла.
Равенство энергий GTB = Gж при T = T0 (см. рис. 2) означает, что жидкое состояние металла термодинамически равноправно его кристаллическому состоянию. При температуре Т0 расплав металла и металлические кристаллы будут находиться в термодинамическом равновесии. Это означает, что они могут сосуществовать одновременно и притом бесконечно долго, не превращаясь друг в друга. Следовательно, при температуре Т0 процесс кристаллизации (как и процесс плавления) происходить, строго говоря, не может.
Для начала кристаллизации необходимо охладить жидкий металл (расплав) до некоторой температуры Т, которая меньше равновесной температуры Т0. Только в этом случае в системе возникает энергетический стимул превращения (см. рис. 2.1), который определяется разностью свободных энергий металла, находящегося в менее устойчивом (жидком) и более устойчивом (кристаллическом) состояниях: g(Т) = Gж (Т) - СТВ (Т). Иначе говоря, кристаллизация начнется лишь при некотором переохлаждении расплава ниже равновесной температуры Т0. Разность Т = Т0 - Т между равновесной и фактической температурами кристаллизации называют степенью переохлаждения расплава.
Степень переохлаждения жидкого металла АТ не является постоянной величиной. Она зависит, в частности, от скорости, с которой охлаждают расплав. Поэтому кристаллизация одного и того же металла может протекать при разных температурах Т. В отличие от процесса формирования и роста кристаллов (кристаллизации) плавление - это процесс разрушения кристаллической решетки, который не требует времени на перераспределение атомов. Поэтому, независимо от скорости нагрева, металлический кристалл начинает плавиться сразу, как только его температура превысит температуру Т0. Иначе говоря, возможная степень перегрева при плавлении чистого металла пренебрежимо мала. Поэтому важнейшая физическая характеристика металла - температура плавления Тпл фактически равна температуре Т0 (см. рис. 2).
Процесс затвердевания (точнее, кристаллизации) металла можно изобразить в координатах «температура-время». На рис. 2 показаны термические кривые охлаждения, которые соответствуют разным скоростям отвода тепла от затвердевающей жидкости.
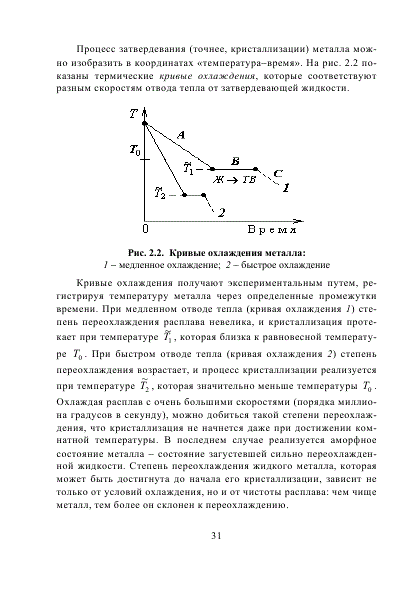
Рисунок 2 - Кривые охлаждения металла:
1 - медленное охлаждение; 2 - быстрое охлаждение
Объяснить, почему в поршневых алюминиевых сплавах содержание кремния достигает 22 процентов. Описать особенности структуры и свойств поршневых алюминиевых сплавов
Применение алюминиевых сплавов для изготовления поршней дало возможность снизить вес двигателя и удельный расход топлива на единицу мощности.
История применения жаропрочных сплавов алюминия ведет свое начало от появления в 1907-1908 гг. первых литых поршней для гоночных автомобилей из сплавов алюминия с цинком.
Современные алюминиевые сплавы, как правило, технологичны, имеют относительно высокую прочность и пластичность. В таблице 4 приведен химический состав, а в таблице 3 физико-механические свойства некоторых поршневых сплавов при нормальной и повышенной температуре.
Как видно из таблицы 3, поршневые сплавы отличаются довольно сложным химическим составом, потому что для повышения жаропрочности их обычно легируют медью, марганцем, никелем, хромом, кобальтом и другими элементами. Поэтому целесообразно рассмотреть влияние легирующих элементов на структуру и свойства поршневых сплавов.
В настоящее время поршни отечественных автомобильных и тракторных двигателей в большинстве своем изготавливают из алюминиевых сплавов типа АЛ 25 и АЛ 26. Эти сплавы относятся к эвтектическому типу - в равновесии находятся твердый раствор кремния в алюминии и твердый раствор алюминия в кремнии.
Таблица 3 - Химический состав некоторых алюминиевых поршневых сплавов
|
Таблица 4 - Физико-механические свойства некоторых поршневых сплавов
Свойства | Марка сплава | ||
АК 4 | АЛ 25 | АЛ 26 KS 288 | |
Предел прочности, МПа | 293 | 230-280 | 200-250 |
Твердость НВ, кГс/мм2 | 293 | 95-125 | 100-110 |
Длительная прочность, МПа | 573 (100 Ч.) | 47,5 | 50 |
Отностельное удлинение 85, % | 293 | 0.3-1,0 | 0,2-0,6 |
Удельный вес у, кг/м3 | 293 | 2650 | 2720 |
Относительная износостойкость | 293 | 1,15 | 1,0 |
Коэф. линейного расш. а, 1/КхЮ'6 | 293 | 23-24 | 20-25 |
Как уже упоминалось, для того, чтобы повысить прочностные свойства поршневых сплавов и сделать их восприимчивыми к упрочняющей термообработке, используют дополнительное легирование медью и магнием. Изменение содержания меди в пределах 0,5-4,5% мало отражается на прочности сплава при комнатной температуре, но повышение содержания меди способствует повышению длительной прочности при температуре 570 К [1].
Согласно изотермическим разрезам тройной диаграммы состояния А1 - Сu - Мg с повышением температуры область -твердого раствора сильно расширяется и сплавы при низких температурах, будучи трехфазными (разрез при 20°С), становятся при температуре 500°С гомогенными твердыми растворами. Фазы СuAl2 и S при этом переходят в твердый раствор. Железосодержащие фазы и марганцовистая фаза остаются нерастворенными.
Этим пользуются для придания слиткам однородной (гомогенной) структуры перед горячей прокаткой. Гомогенизация слитков дюралюминия заключается в длительном нагреве при температуре 480-490° С после незначительной предварительной деформации (на 8-10%) с последующим охлаждением на воздухе.
При комнатной температуре структура сплавов состоит из кристаллов твердого раствора и избыточной фазы Mg2Al3. В этих сплавах прочностные характеристики повышаются с повышением содержания магния за счет увеличения количества избыточной фазы. Сплавы Аl-Mg, как и сплавы Al-Mn, часто применяются в нагартованном состоянии, когда с помощью пластической деформации обеспечивается их заметное упрочнение. Однако, пластические характеристики при этом резко снижаются, что ограничивает применение нагартованных сплавов.
Механизм выделения β-фазы в зависимости от продолжительности старения недостаточно выяснен. Допускается следующая последовательность процесса старения: «зоны», обогащенные магнием, неравновесная β' — равновесная β.
Существование зон подтверждается лишь измерением электросопротивления сплавов. Строение фаз β' и β, выделяющихся в форме мелких пластин, отличается большой сложностью.
Помимо времени гомогенизации, на образование выделений оказывают влияние условия закалки. При закалке в холодную воду β-фаза при последующем старении выделяется по границам зерен в непрерывной форме. Закалка в кипящую воду или горячее масло дает после старения выделения β-фазы по границам зерен в форме разобщенных включений. Остаточная дендритная ликвация и обеднение вакансиями зон, прилегающих к границам зерна, оказывают важное влияние на условия и характер выделений β-фазы. Вакансии ускоряют процесс выделения β-фазы, так как ее образование сопровождается увеличением объема.

Рисунок 3 – Метастабильная диаграмма Al-Mg
Основываясь на метастабильной диаграмме сплавов системы Al-Mg (рис. 4), предложена схема последовательности образования β-фазы при старении сплавов с 10% Mg. По границам зерен процессы выделения и последовательного превращения идут на одну стадию быстрее, так как возможность образования зародышей здесь большая.
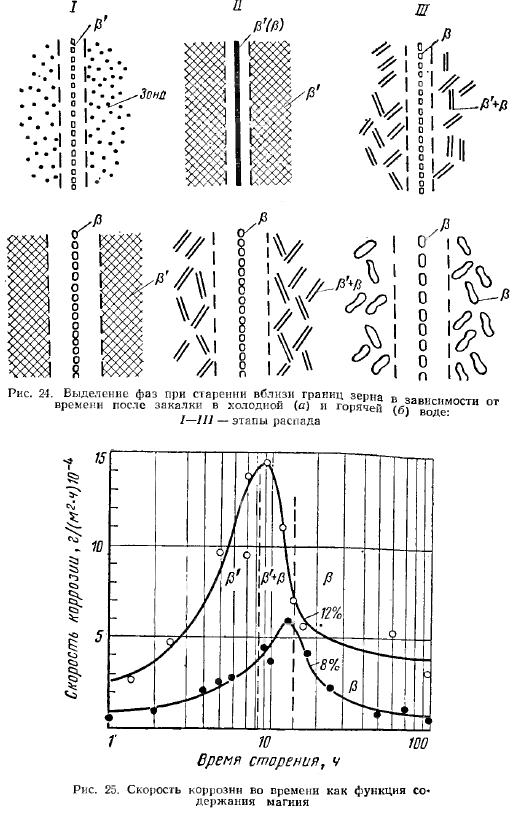
Рисунок 4 – Выделение фаз при старении вблизи границ зёрен в зависимости от времени после закалки в холодной (а) и горячей (б) воде: I-III – этапы распада
Свободные от выделений области по границам зерен являются слабым местом отливок, и поэтому разрушение идет по границам зерна, особенно во второй стадии, при закалке в холодную воду, когда β-фаза образует непрерывные цепочки. Прочностные свойства отливок понижаются. Коррозионная же стойкость сильнее всего ухудшается во время превращения β'→β. Можно считать, что коррозионная стойкость сплавов зависит от характера выделений β-фазы. Это согласуется с тем, что сплавы, закаленные в холодной воде, имеют пониженную коррозионную стойкость.
Начертить диаграмму состояния железо-цементит. Обозначить фазовые области и линии диаграммы состояния. Нарисовать и описать кривую охлаждения стали 08. Представить структурные превращения при медленном охлаждении стали. Нарисовать структуру при комнатной температуре. Определить количество перлита при комнатной температуре
Компонентами железоуглеродистых сплавов можно считать железо и карбид железа.
Железо — металл сравнительно мягкий, пластичный. Прочность железа составляет 250 МПа, твердость НВ 60...80, пластичность = 45 %. Существующее при комнатной температуре α-железо растворяет до 0,005 % С. Твердый раствор углерода в α-железе называют ферритом (Ф). По своим свойствам феррит практически не отличается от технически чистого железа.
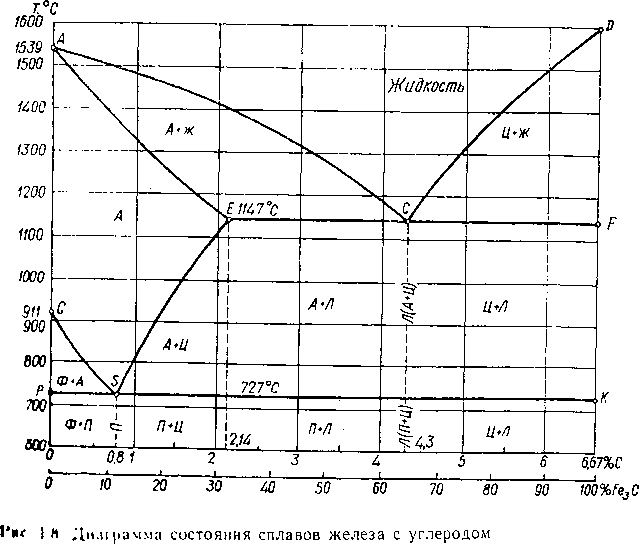
Рисунок 5 – Диаграмма железо-углерод
Карбид железа Fe3C, наоборот, очень тверд (НВ 800), но хрупок. Его называют цементитом (Ц). С увеличением содержания углерода образуется больше цементита, поэтому сплав становится тверже и хрупче.
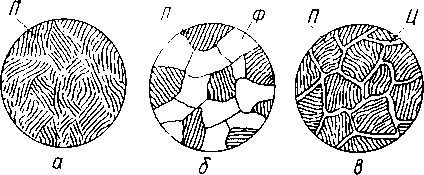
Рисунок 6 - Схемы микроструктур углеродистых сталей
Диаграмма состояния Fe—Fe3C. Линией ликвидус на диаграмме является линия ACD, солидус — AECF. Линии GC, SE и PSK отражают превращения в сплавах после затвердевания.
Точка Е, соответствующая концентрации 2,14 % С, делит железоуглеродистые сплавы по структуре на две группы. Слева от этой точки расположены сплавы, которые затвердевают с образованием твердого раствора углерода в -железе, называемого аустенитом (Л). Эти сплавы достаточно пластичны, способны обрабатываться давлением, их называют сталями.
Сплавы, расположенные правее точки Е, с содержанием углерода свыше 2,14 %, затвердевают с образованием эвтектики, уменьшающей пластичность, но улучшающей литейные их свойства. Эти сплавы называются чугунами.
Структура сталей. Аустенит в стали с 0,8 % С при охлаждении до 727 °С (точка S, рис. 5) распадается на дисперсную смесь, состоящую из феррита и цементита (рис. 6,а). Смесь, образующуюся при распаде твердого раствора, называют эвтектоидом. Точку S, а также сталь со структурой эвтектоида называют соответственно эвтектоидными. Эвтектоид в железоуглеродистых сплавах получил название перлита (П).
Стали, расположенные левее точки S, называют доэвтектоидними и правее—заэвтектоидными.
В доэвтектоидных сталях превращения при охлаждении начинаются на линии GS выделением феррита. Поэтому концентрация углерода в аустените повышается и при 727 °С (линия PSK) достигает эвтектоидной — 0,8 %. В этих условиях аустенит превращается в перлит. Таким образом, в доэвтектоидной стали после завершения всех превращений образуется структура, состоящая из феррита и перлита (рис. 6).
Превращения в заэвтектоидной стали начинаются на линии SE, отражающей предельную растворимость углерода в аустените. При температурах ниже линии SE из аустенита выделяется цементит. При этом аустенит обедняется углеродом и, достигнув эвтектоидной концентрации (727 °С), превращается в перлит. В результате превращений в заэвтектоидной стали формируется структура, состоящая из перлита и цементита (рис. 6,в).
Структура чугунов. В правой части диаграммы точка С является эвтектической. Эвтектика в чугуне после затвердевания состоит из аустенита и цементита, ее называют ледебуритом (Л). При 727 °С аустенит превращается в перлит, поэтому при нормальной температуре ледебурит состоит из перлита и цементита. Соответственно доэвтектические чугуны состоят после затвердевания из (аустенита и ледебурита, а заэвтектические — из ледебурита и цементита. Ниже 727 °С аустенит в них также превращается в перлит.
Таким образом, структура чугунов, отражаемых диаграммой состояния «железо — цементит», состоит из двух фаз — феррита и цементита, т. е. углерод в них находится в связанном состоянии; в виде цементита. Такие чугуны имеют в изломе белый оттенок и называются белыми. В связи с большим количеством цементита они отличаются высокой твердостью, затрудняющей обработку резанием. Их применяют преимущественно для передела в сталь.
В применяемых на практике чугунах часть углерода находится; свободном состоянии — в виде графита. Такие чугуны по серому оттенку в изломе получили название серых.
Диаграмма «железо — цементит» отражает состояние и структуру основных конструкционных материалов — сталей, поэтому имеет нe только большое научное значение, но и находит практическое применение. Она позволяет устанавливать температуры плавления и заливки сталей, интервал оптимальных температур нагрева сталей для обработки давлением, режимы термической обработки.
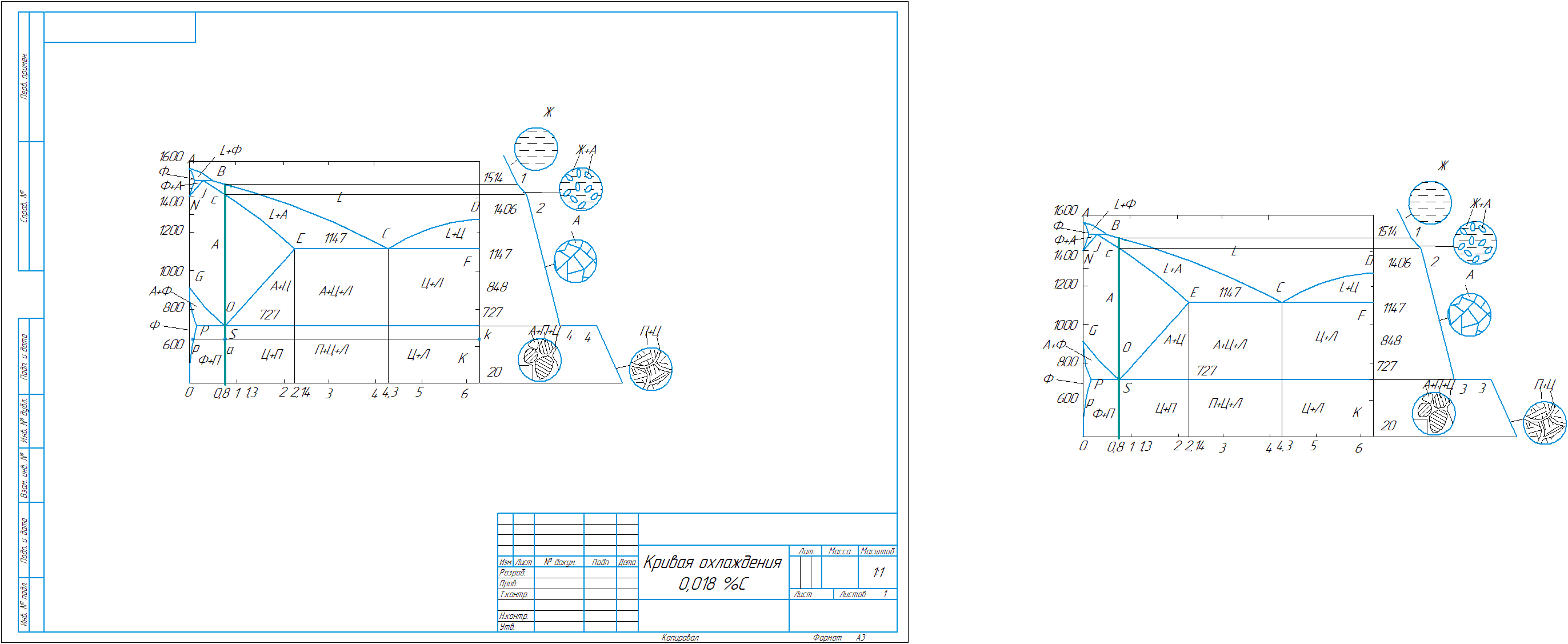
Рисунок 7 – Кривая охлаждения сплава 0,8 %С
1–2 – первичная кристаллизация, образование аустенитной структуры, Ж+А
2–3 – охлаждение твердого сплава (превращений нет), А
образуются зоны с высоким содержание углерода, которые превращаются в Ц.
3–3' – эвтектоидное превращение А в П;
При температуре 727 °С( точка S) во всем объеме аустенита начинается эвтектоидное превращение, которое подчиняется общим законам кристаллизации и происходит путем образования центров кристаллизации феррита и цементита с последующим ростом кристаллов этих фаз. A (Ф + Ц ii)
В связи с тем, что углерод в аустените распределен неравномерно (наличие флуктуаций) появление центров кристаллизации существенно облегчается. При этом ведущей фазой при превращении является цементит, зародыши которого возникают по границам зерен аустенита. Зародыши зерен цементита растут в форме тонких пластин, направленных вглубь зерен аустенита. Для роста пластинки цементита необходимо, чтобы к ней диффундировал углерод из соседних участков. В результате аустенит, расположенный около пластинки обедняется углеродом, перестраивается решетка (Fe Fe), и в результате этого создаются условия для образования феррита.
3' – конец превращения; t = 727° C =const .
Ниже 3' – остывание сплава, идет процесс третичной кристаллизации, ЦIII из феррита (теоретически). Структура – перлит.

Назвать формы графита в чугунах. Объяснить связь формы графита со свойствами чугунов. Привести структуры чугунов с разной формой графита. Обозначить фазы и структурные составляющие
Чугуны отличаются от сталей более высоким содержанием углерода, по технологическим свойствам - лучшими литейными свойствами, малой способностью к пластическим деформациям, экономически чугун дешевле стали.
Белый чугун - в нем весь углерод находится в связанном состоянии в виде Fe3C (белый доэвтектический, белый эвтектический, белый заэвтектический). Белым чугун называют по виду излома - кристаллический, блестящий.
Серый чугун, в котором значительная часть углерода находится в свободном состоянии в виде графита (пластинчатый). Пластинчатая форма (готовые трещины) ухудшает механические свойства при растяжении. Разработаны методы плавки, при которой изменяется форма графитовых включений (в виде червячков) - вермикулярный графит. Механические свойства вермикулярного графита выше, чем у серого чугуна.
Высокопрочный чугун, в котором весь углерод находится в виде сферических (глобулярных) частиц. Шаровидный графит. Механические свойства высокие. Ковкий чугун получают отжигом отливок из белого чугуна. В нем графит находится в виде хлопьев (углерод отжига).
Белые чугуны - так они называются по виду излома, в котором видны только кристаллы металлических фаз (светлые, блестящие).
В доэвтектических сплавах при первичной кристаллизации выделяется избыточный аустенит, на эвтектической линии остаток жидкости образует ледебурит. На линии PSK (727 °С) из аустенита образуется перилит.
В заэвтектических сплавах вначале образуется цементит первичный (Ц1), дальше при охлаждении образуется ледебурит, на линии PSK аустенит ледебурита превращается в перлит.
Во всех этих чугунах есть ледебуритная эвтектика (рис. 8), содержится много цементита, придающего чугунам высокую твердость и хрупкость. Чугуны применяются как износоустойчивые изделия, готовятся только литьем.
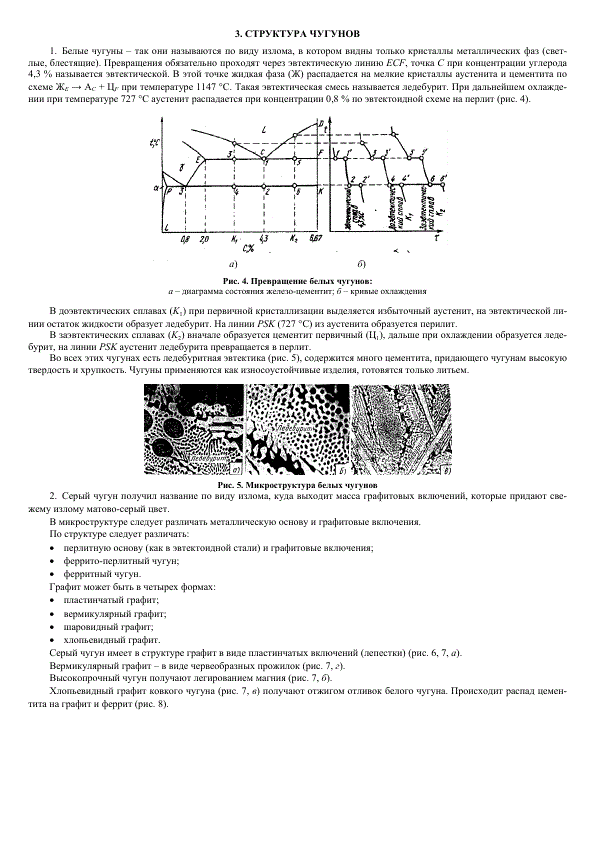
Рисунок 8 - Микроструктура белых чугунов
Серый чугун получил название по виду излома, куда выходит масса графитовых включений, которые придают свежему излому матово-серый цвет.
В микроструктуре следует различать металлическую основу и графитовые включения. По структуре следует различать:
перлитную основу (как в эвтектоидной стали) и графитовые включения;
феррито-перлитный чугун;
ферритный чугун.
Графит может быть в четырех формах:
пластинчатый графит;
вермикулярный графит;
шаровидный графит;
хлопьевидный графит.
Серый чугун имеет в структуре графит в виде пластинчатых включений (лепестки) (рис. 9, а). Вермикулярный графит - в виде червеобразных прожилок (рис. 9, г). Высокопрочный чугун получают легированием магния (рис. 9, б).
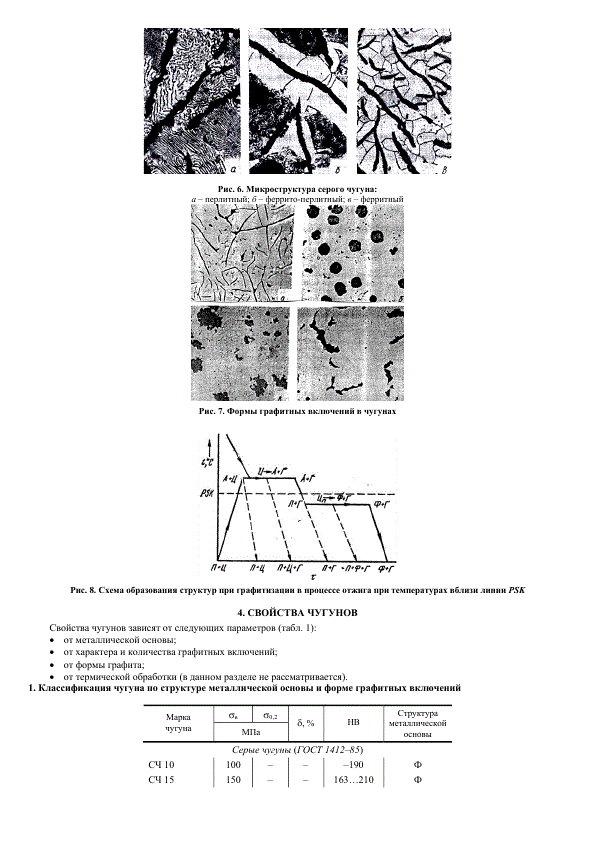
Рисунок 9 – Микроструктура серого чугуна:
а – перлитный; б – феррито-перлитный; в - ферритный
Хлопьевидный графит ковкого чугуна (рис. 7, в) получают отжигом отливок белого чугуна. Происходит распад цементита на графит и феррит (рис. 10).
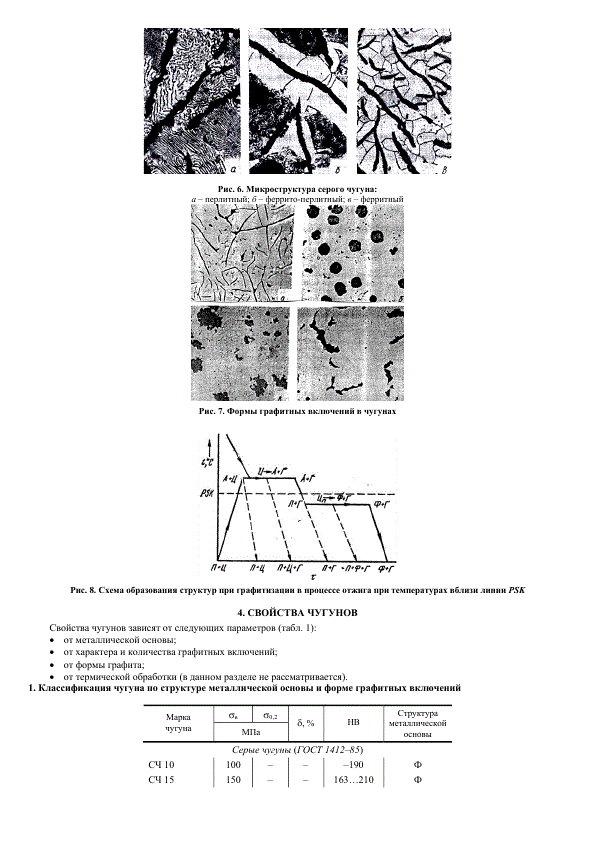
Рисунок 10 - Формы графитных включений в чугунах
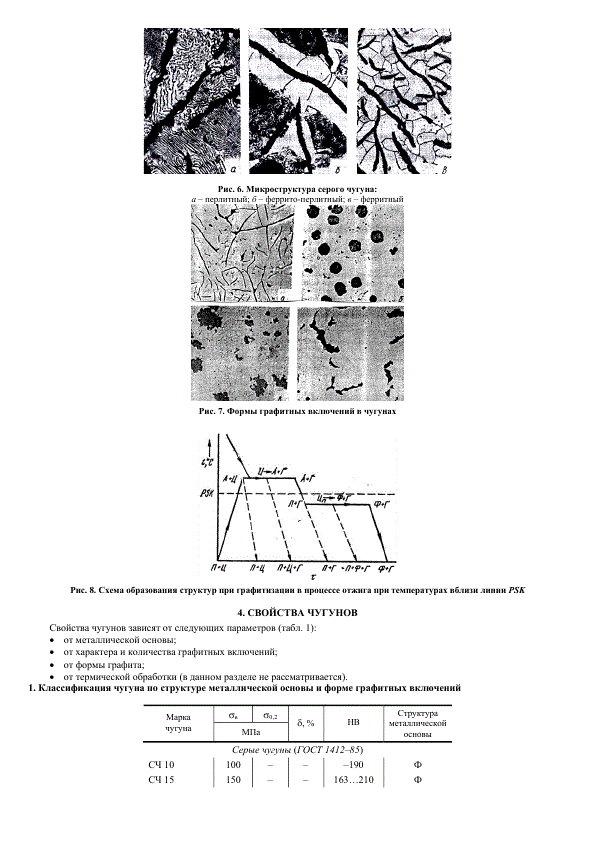
Рисунок 11- Схема образования структур при графитизации в процессе отжига при температурах вблизи линии PSK
6. Объясните маркировку и применение следующих материалов: Д16; КЧ33-8; А20; Ст3сп; ЛА77-2; 50; АК9пч; БрСЗ0; МЛ6
Д16 - Алюминиевый деформируемый сплав )дюралюминий №16).
Использование в промышленности: для силовых элементов конструкций самолетов, кузовов автомобилей, труб и т.д.; для детелей, работающих при температурах до -230 С.
КЧ33-8 - чугун ковкий с хлопьевидным графитом, предел прочности при растяжении 330 МПа, относительное удлинение 8%.
Использование в промышленности: детали, работающие при средних статических и динамических нагрузках. |
А20 - сталь конструкционная повышенной обрабатываемости (атоматная), содержание углерода 0,2%.
Использование в промышленности: мелкие детали машин и приборов, малонагруженные детали сложной конфигурации, к которым предъявляются требования высокой точности размеров и качества поверхности, после цементации и цианирования — малонагруженные детали, к которым предъявляются требования износостойкости и повышенного качества поверхности. |
Ст3сп - сталь конструкционная углеродистая обыкновенного качества №3, спокойная.
Использование в промышленности: несущие элементы сварных и несварных конструкций и деталей, работающих при положительных температурах.
ЛА77-2 - Латунь, обрабатываемая давлением. Содержание меди 77%, алюминия 2%, остальное- цинк.
Использование в промышленности: для изделий средней прочности, хорошей коррозионной стойкости.
50 - сталь конструкционная углеродистая качественная, содержание углерода 0,5%.
Использование в промышленности: зубчатые колеса, прокатные валки, штоки, тяжелонагруженные валы, оси, бандажи, малонагруженные пружины и рессоры, лемехи, пальцы звеньев гусениц, муфты сцепления коробок передач, корпуса форсунок и другие детали, работающие на трение. |
АК9пч - Алюминиевый литейный сплав №9 в чушках.
Использование в промышленности: для изготовления фасонных отливок.
БрСЗ0 – бронза оловянистая литейная. Содержание свинца 30%, остальное-медь.
Применяется для подшипников скольжения.
МЛ6 - магниевый литейный сплав №6.
Использование в промышленности: для изготовления высоко и средненагруженных деталей; предельная рабочая температура: 150 °C
ЛИТЕРАТУРА
Новиков И.И., Строганов Г.Б., Новиков А.И. Металловедение, термообработка и рентгенография: Учебник для вузов. – М.: МИСиС, 1994. – 480 с.
Биронт, В. С. Материаловедение. Конструкционные материалы: учеб. пособие / В. С. Биронт; ГАЦМиЗ. – Красноярск, 2002. – 156 с.
Биронт В. С. Материаловедение. Основы физического металловедения : учеб. пособие / В. С. Биронт; ГАЦМиЗ. – Красноярск, 2003. – 144 с.
Методы физического металловедения: Практикум /Сост.: Л.С. Цурган, Е.В. Краснова, Т.А. Орелкина, В.И. Аникина, Г.А. Меркулова; Под ред. В.С. Биронта; ГАЦМиЗ - Красноярск, 2001.-132с.
Материаловедение. Формирование структуры в сплавах двухкомпонентных систем : учеб. пособие / В. С. Биронт, Т. А. Орелкина, В. Ю. Гурская, В. И. Аникина; ГАЦМиЗ. – Красноярск, 2006. – 96 с.
Практическое металловедение цветных металлов и сплавов: учеб.пособие/ Орелкина Т.А., Дроздова Т.Н., Надолько А.С.-Красноярск: Сиб.федер.ун-т,2013.-124с
1 Физико-химической называют систему, в которой возможно перераспределение энергии и вещества.