Сверление. Записка. 1 Анализ способов обработки глубоких отверстий, конструкций инструментов для глубокого сверления, сил, действующих на сверло, факторов, оказывающих влияние на силы, моделей контакта при трении
![]()
|
|
С | Si | Мп | S | P | Cr | Ni | ||
не более | ||||||||
0,36…0,44 | 0,17…0,37 | 0,5…0,8 | 0,035 | 0,035 | 0,8…1,1 | <0,31 |
Мо | V | W | Fe | AL | Cu |
- | - | - | 97 | - | 0,3 |
Известны различные способы обработки отверстий. Это может быть обычное сверление, а еще лазерная, электроискровая, ультразвуковая и электрохимико-механическая обработки.
Лазерное излучение характеризуется огромной концентрацией энергии, обеспечивающей важную интенсификацию процессов обработки материалов [25]. При воздействии сфокусированного лазерного излучения на поверхность твердого тела вещество нагревается, плавится, отчасти улетучивается и ионизируется. В неоднородно нагретом веществе возникает сложное течение жидкости, паров, плазмы и находящегося вокруг газа. Перемещение вещества оказывает в свою очередь существенное влияние на распределение лазерного излучения, приводя к дополнительной фокусировке либо к дефокусировке [15, 68].
Высокая энергия светового потока способная расплавить и испарить всевозможные материалы, кратковременность протекания процесса, небольшие зоны оплавления и дееспособность луча проникать чрез разные прозрачные среды в места недоступные другим видам воздействия предоставляют возможность применить данный метод обработки для решения многих технологических задач. Самостоятельность процесса обработки заготовок световым лучом от механических параметров обрабатываемых материалов раскрывает широкую вероятность внедрения предоставленного способа при обработке деталей из металлических и не металлических материалов с высочайшими физико-механическими характеристиками (твердые сплавы, магнитные и жаропрочные материалы, специальные сплавы, закаленные стали, майолика, алмазы и т.д.). При применении лазера достигается большое отношение глубины к диаметру сверления. В работе [64] показано, что отношение глубины к среднему диаметру отверстия составляет около 11: 1, что значительно больше, чем при остальных методах обработки отверстий.
Однако всё это приемлемо для сверления отверстий малых диаметров, порядка 0,002…2 мм .
Электроискровая обработка базирована на электрической эрозии, то есть на разрушении поверхностных слоев материала наступающем в итоге электротермического действия импульсивных нестандартных электрических разрядов [68, 21]. При проскакивании искры в интервале меж катодом и анодом лектронная лавина с огромной скоростью обрушивается на анод, нагревая ту небольшую часть поверхности, на которую она обрушилась до оплавления и даже до испарения. Этот процесс происходит в виде небольшого взрыва: часть расплавленного металла, а время от времени и некоторое количество оставшихся в твердом состоянии частиц вещества энергично выбрасывается из пораженного эрозией участка. Электроискровый способ используется при обработке труднообрабатываемых токопроводящих материалов. Этим способом изготавливаются отверстия малых диаметров, узкие криволинейные пазы, глухие фасонные отверстия, фасонные внутренние полости в штампах и т.п. [62].
Суть ультразвуковой обработки заключается в том, что под воздействием ультразвуковых колебаний в жидкости возникают кавитационные явления, вследствие чего абразивные зерна, взвешенные суспензии, с большой скоростью и силой ударяются в обработанную поверхность и создают нужную работу (разрушение или упрочнение материалов) [68,60,87].
Использование данных видов обработки не приемлемо для обработки глубоких отверстий уже в следствии сложности изготовления станков для обработки таких диаметров и длин. Выпущенные до настоящего времени станки с выходящей мощностью генератора от 0,05 до 2,4 кВт разрешают обрабатывать отверстия диаметром приблизительно от 0,075 до 90 мм. Наибольший размер отверстия определяется мощностью станка, а наименьший размер - прочностью инструмента и чувствительностью механизма подачи. При этом наибольшая глубина обработки составляет примерно 2…5 диаметра инструмента [97].
Метод электрохимико-механической обработки может существовать только для чистовой обработки внутренних поверхностей деталей машин.
Таковым образом, более применимом методом обработки глубоких отверстий является глубокое сверление. Глубокое сверление является специфичной технологической операцией, обширно применяемой в современном производстве. Для проведения данной операции требуется создание специального инструмента, оснастки и оборудования.
Имеющиеся сверла для глубокого сверления на основании работ [13, 21, 75, 15] логично разделить на две группы: сверла для сплошного сверления и сверла для кольцевого сверления.
Сплошное глубокое сверление (рисунок 1а) различаются тем, что весь высверливаемый материал удаляется в виде стружки. Кольцевое глубокое сверление (рисунок 1б) – сверление, при котором в стружку превращается лишь часть высверливаемого материала, находящаяся в высверливаемой кольцевой полости, а остальная часть удаляется в виде оставляемого стержня диаметром dc.
При сплошном сверлении вблизи оси сверла возникают неблагоприятные условия резания, связанные с тем, что скорость резания снижается до нуля на оси сверла, а задний угол в процессе резания принимает отрицательное значение. У оси сверла по существу нет резания, а происходит лишь смятие материала, сопровождающееся возрастанием осевой составляющей силы резания и повышенным изнашиванием инструмента. Эти недостатки можно устранить понижением режущего лезвия вблизи оси (рисунок 2), что приводит к образованию так называемого «нулевого стержня». Разновидность этого сверления называют сплошным глубоким сверлением с нулевым стержнем.

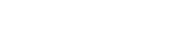
Рисунок 2 – Способы понижения режущего лезвия вблизи оси инструмента в целях образования «нулевого стержня»
Рисунок 1– Образование отверстия при сплошном и кольцевом сверлении




Области оптимального внедрения сплошного и кольцевого сверления чётко не разграничены. В отечественной практике сплошное сверление в настоящее время применяется при сверлении отверстий диаметром не более 90…100 мм. За рубежом (если судить по каталогам ВТА) сплошное сверление используется шире. Кольцевое сверление в отечественной практике удачно используется при сверлении отверстий Ø 60 и Ø 80 мм глубиной 6000 мм.
Инструменты для сплошного глубокого сверления различаются методом отвода стружки и расположением режущих лезвий относительно оси и по окружности, Тип направляющих элементов хотя и оказывает немаловажное воздействие на работу инструмента, но применительно к инструментам для сплошного сверления имеет подчиненное значение, так как выбирается с учетом расположения режущих частей.
Более обширное использование в настоящее время имеют трубчато-лопаточные (группа 1а) и лопаточные сверла (группа 2а). Используются и шнековые сверла (группа 1.6), какие разрешают сверлить глубокие отверстия с отношением 1: d0 по 10—15 на универсальных станках. Эти сверла не. относятся к инструментам глубокого сверления, так как при работе ими стружка отводится не потоком СОЖ, а с помощью винтовых канавок. Эжекторные сверла (группа За) в связи с организацией их централизованного производства имеют все шансы получить широкое применение. Сверла с. М образной заточкой (группа 26), имеющие режущую часть из быстрорежущей стали, в настоящее время в следствии маленькой производительности фактически не используются. Преимущества и недостатки каждой разновидности инструмента, приведенной в таблице, определяются совокупностью преимуществ и недостатков, связанных с. их отдельными отличительными признаками: методом отвода СОЖ, расположением режущих лезвий и распределением нагрузки между ними, типом направляющих частей, наличием определенности базирования, уравновешенности и т. д, (см. у л. I и 2). Ниже рассматривается конструкция, геометрия заточки и индивидуальности технологии сверления применяемыми в настоящее время инструментами.
В зависимости от метода отвода стружки распознают последующие разновидности глубокого сверления [65]:
- глубокое сверление с внутренним отводом стружки - при котором используют наружный подвод СОЖ и внутренний отвод стружки (рисунок 3),
- глубокое сверление с наружным отводом стружки - при котором используют внутренний подвод СОЖ и наружный отвод стружки (рисунок 4),
- эжекторное глубокое сверление - при котором применяется внутренний отвод стружки с использованием эжектора.

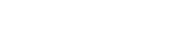
Рисунок 3–Схема сверления при наружном подводе СОЖ и внутреннем отводом стружки
Рисунок 4–Схема глубокого сверления с внутренним подводом СОЖ и наружным отводом стружки

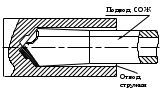
Основные виды инструментов для сплошного сверления:

Рисунок 5–Инструмент с наружным отводом стружки

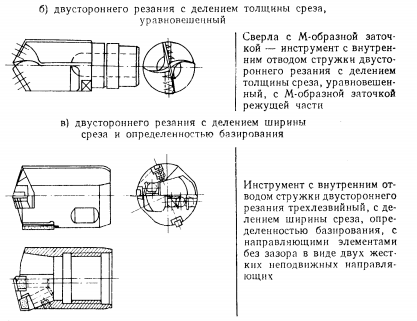

Рисунок 6–Инструменты с внутренним отводом стружки.
В зависимости от кинематической схемы сверления различают три разновидности сверления:
1) заготовка 1 вращается с частотой

2) заготовка 1 вращается с частотой

3) заготовка 1 неподвижна, а инструменту 2 одновременно сообщается вращение с частотой и поступательное движение подачи (рисунок 7 в)
Рассматривая данные схемы, наиболее предпочтительной является 1-я схема (рис. 7 а). Так как при сверлении по 2-й схеме (рисунок 7 б) вращающийся инструмент является источником дополнительных погрешностей (в частности, создаются более благоприятные условия для образования огранки). При сверлении по 3-й схеме (рисунок 6 в) возникают большие уводы оси отверстия, чем при сверлении по первым двум схемам. Однако при сверлении по второй схеме можно достигнуть наибольшей производительности производительности процесса.


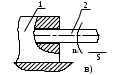
Рисунок 7 – Схемы сверления при вращении: а) заготовки,
б) заготовки и инструмента, в) инструмента
В зависимости от характера подачи также различают некоторые виды сверления. Глубокое сверление обычно производится с равномерной подачей сверла, при которой толщина срезаемого слоя остается неизменной. При сверлении отверстий малых диаметров в труднообрабатываемых вязких материалах образуется тонкая сливная стружка, которую трудно отводить из отверстия. В данных случаях используют способы дробления стружки по длине за счет применения переменной по величине подачи, при которой толщина срезаемого слоя также будет переменной. Разработка вибрационного сверления гарантирует кинематическое дробление стружки.
Вибрационное сверление – глубокое сверление, при котором на обычное осевое движение подачи накладывается дополнительное осциллирующее движение. Дробление стружки успешно осуществляется за счет прерывистого резания, получаемого при колебаниях обрабатываемой детали вдоль оси, которые создаются с помощью вибратора. Путем изменения кинематики вибратора регулируется величина элементов стружки, образующейся при резании. Начиная с диаметра 8 мм, необходимо применять не вибрационное сверление, а сверление с внутренним отводом стружки и равномерной подачей, так как это не требует применения вибратора, а отвод стружки обеспечивается надежно [35].
Исходя из схемы сверления различают одностороннее и двустороннее сверление [35]. Сверление сквозных отверстий часто производится с одной стороны на проход. Только при длине отверстия 9000-10000 мм используют двустороннее сверление.
Классификация свёрл происходит по различным конструктивным элементам. Самыми действенными из них являются конструкции резцов и направляющих свёрл и конструкции элементов присоединения свёрл к стеблям.
У малых свёрл режущие кромки и направляющие напайные, твёрдосплавные. Это так называемые сверлильные головки БТА, отличающиеся тем, что при малых диаметрах сверления твердосплавные режущие и направляющие пластины напаиваются непосредственно на трубчатый стебель. А при больших диаметрах на головки, навинчиваемые на стебель [46].
1.2 Анализ условий работы инструмента при сверлении отверстий малого диаметра
Инструмент для сверления отверстий малого диаметра обладает малой жесткостью на изгиб и кручение. В этой связи, даже при сверлении инструментом с внутренним отводом стружки, обладающим большей жесткостью, чем инструмент с наружным отводом стружки, нужно работать с малыми подачами. Так, при сверлении глубоких отверстий диаметром 0-30 мм в заготовках из легированных и конструкционных сталей с отношением l/d0 > 100 рабочие подачи не превышают 0,05—0,06 мм/об. В работе малыми подачами образуется сливная стружка, которая не поддается дроблению по длине, а срезание стружки происходит в неблагоприятных условиях, так как толщина среза равна или меньше радиуса скругления режущего лезвия. В разработке процесса сверления отверстий малого диаметра необходимо учитывать особенности отвода стружки и сложность ее отвода.
Необходимо более подробно рассмотреть две особенности: резкое уменьшение жесткости сверла и повышения скорости СОЖ в зоне резания с уменьшением диаметра сверления.
Для надежного отвода сливной стружки нужно иметь значительные скорости СОЖ. Чтобы не было больших потерь давления при подводе СОЖ, необходимо увеличивать площадь проходного сечения подводного канала, т, е. во внутреннем отводе стружки уменьшать наружный диаметр стебля Д. С другой стороны, что бы отвести сливную стружку по сравнению с дробленой приходится брать большую площадь проходных сечений отводных каналов за счет увеличения внутреннего диаметра стебля dc в. Это приводит к снижению жесткости и устойчивости к вибрациям стебля, вследствие чего допустимая по вибрациям подача снижается, а также уменьшается производительность.
Как показывают исследования, с уменьшением диаметра сверления
максимально допустимый наружный диаметр стебля резко уменьшается (рисунок 8), следовательно, резко снижается жесткость инструмента с уменьшением диаметра сверления. Расчет максимально допустимого наружного диаметра стебля сложный процесс. Для практических расчетов при сверлении отверстий глубиной lld0 100 .
Исследования но выявлению степени влияния длины стебля /0 (глубины сверления) на предельно допустимую по вибрациям подачу (5пред) показали (рисунок 8.1), что с увеличением длины стебля естественно падает его жесткость и уменьшается допустимая подача, однако, начиная с некоторого отношения ljd0 дальнейшего снижения допустимой подачи не происходит, что, видимо, объясняется возникновением дополнительных точек опоры стебля при его изгибе в отверстии. Возникновение такой опоры неоднократно наблюдалось в ходе исследований.
Как показывают исследования, что скорость СОЖ. где Wтребующаяся для надежного отвода сливной стружки, резко возрастает с уменьшением диаметра сверления (рисунок 8). Это можно объяснить ухудшением условий для отвода стружки с уменьшением диаметра сверления, вследствие чего требуется большая скорость СОЖ для надежного отвода стружки. Принимая во внимание огромное влияние скорости СОЖ в зоне резания на температуру стружкообразования, удельные силы резания и изменение их значений вдоль режущей кромки, рассмотрим подробно эти вопросы.
Образование сливной стружки при сверлении отверстий малого диаметра нужно учитывать и при расчете стружко-сборников, имея в виду, что коэффициент заполнения сливной стружкой в десятки раз меньше, нежели дробленой.
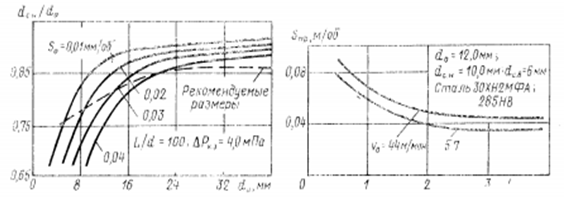
Рисунок 8–Изменение максимально допустимого наружного диаметра стебля в зависимости от диаметра сверления
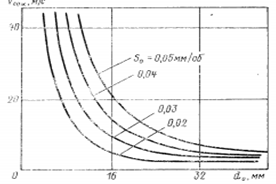
Рисунок 8–Зависимость скорости потока СОЖ, необходимой для отвода стружки, от диаметра сверления (F# р = 0,28<*2)
Силы, действующие на инструмент.
При сплошном сверлении наиболее широко применяются сверла одностороннего резания с наружным и внутренним отводом стружки (группы 1а и 2а). Сверление же отверстий малого диаметра происходит в основном только этими инструментами.
Инструменты имеют одну режущею часть 3, смещенное в одну сторону от оси, и два жестких неподвижных направляющих 1 и 2. Такое расположение лезвия в сочетании с тем, что оно является единственным в инструменте, и порождает ряд его свойств. В этих инструментах просто и надежно обеспечивается определенность базирования. Только из-за отсутствия других лезвий равнодействующая R составляющих сил резания Р и Рг,

Рисунок 9 – Силы действующие на инструмент
1.3 Анализ факторов, влияющих на силы при глубоком сверлении
В процессе резания на силы при глубоком сверлении оказывают влияние многие факторы.
Влияние длины и обратной конусности направляющих.
Результаты опытов с различными длинами направляющих [54] показали, что изменение их длины не влияет на силы при глубоком сверлении. Это наглядно показывает А.И. Соловьев, приводя данные по осевой силе и крутящему моменту при различных длинах направляющих. Отсутствие влияния длины направляющих на силы он объясняет следующим обстоятельством. От длины направляющих не зависят силы трения, поскольку последние определяются только нормальной нагрузкой, а не площадью контакта. Нормальная же нагрузка при этом не изменяется, поскольку остаются постоянными силы резания. Уменьшение длины направляющих до 5 мм не приводит к снижению сил при глубоком сверлении. Напротив, даже в силу их меньшей стойкости и интенсивного износа после сверления нескольких заготовок наблюдается заметное увеличение сил, что не имеет место для свёрл с направляющими длиной 25 мм. На основании сказанного по рекомендациям [104] нецелесообразно уменьшать длину направляющих меньше 0,5d. Учитывая это, можно говорить о влиянии износа на направляющих на силы при глубоком сверлении. С увеличением величины износа должно наблюдаться и увеличение сил. Результаты опытов со свёрлами, имеющими различную величину обратной конусности на направляющих, показали, что этот параметр также не влияет на силовые характеристики процесса глубокого сверления. Отсутствие влияния обратной конусности на силы также объясняется неизменностью сил трения на направляющих сверла. Обратную конусность на направляющих, по-видимому, можно было бы вообще не предусматривать. Однако во избежание случайного образования прямой конусности, по-видимому, целесообразно оговаривать чертежом минимальные значения обратной конусности.
Влияние диаметрального расположения направляющих и формы заточки их торцов.
Экспериментальные исследования, проведенные в работе, сверл с различным расположением направляющих по диаметру относительно калибрующей кромки показали, что занижение диаметра по направляющим не влияет на силы при глубоком сверлении. Диаметр по направляющим был меньше на
0,14 мм. Полученные результаты закономерны, поскольку с уменьшением диаметра не изменились практически ни силы резания на режущих кромках, ни силы трения на направляющих. Наблюдаемое в некоторых случаях увеличение сил связано с другими явлениями и в первую очередь со срезанием стружки направляющими сверла [104]. Действительно, как показывает производственный опыт, направляющие могут выполнять функции режущих кромок и срезать стружку, если торцы их не закруглены. Неокругленные торцы направляющих срезают стружку достаточно большой ширины (до 2 мм). В случае, когда торцы направляющих были тщательно прошлифованы по сфере, они не срезали стружку. Срезание стружки не закругленными торцами направляющих наблюдалось на всех режимах резания, как и в работе.
Срезание стружки направляющими приводит к резкому увеличению как осевой силы, так и крутящего момента. Силы при этом увеличиваются почти на 70 % по сравнению со сверлением без врезания направляющих. Наличие процесса врезания направляющих в поверхность отверстия приводит не только к резкому росту сил, но и ухудшению точности и качества просверленных отверстий. Поэтому рекомендации некоторых исследователей о заточке торца направляющих без закругления следует считать неприемлемыми. То же самое можно сказать и в отношении рекомендаций ряда исследователей об уменьшении диаметра по направляющим элементам относительно диаметра на калибрующей фаске. Уменьшение сил при этом не происходит, но зато точность обработки ухудшается.
Влияние диаметра «нулевого стержня».
С увеличением диаметра стержня осевая сила и крутящий момент, как видно из работы, возрастают, причем в большей степени осевая сила. Повышение осевой силы и крутящего момента связано с тем, что увеличиваются сила резания по всей длине режущей кромки и сила трения на направляющих вследствие роста силы резания на внутреннем участке режущей кромки сверла.
Влияние износа на режущей кромке сверла.
Как показали результаты опытов, значения осевой силы и крутящего момента по мере углубления сверла изменялись незначительно, не наблюдалось и значительной разницы между силами в начале и в конце сверления. Для иллюстрации сказанного на рисунке 10а показаны зависимости сил от глубины сверления при сверлении одной заготовки. Не отмечалось также увеличения сил после сверления 6 деталей (рисунок 10б). Величина фаски и износа по задней грани при этом не превышала 0,2 мм. Это дает основание предполагать, что износ режущей кромки сверла в указанном пределе не влияет на силы при глубоком сверлении. Так как от сил резания зависит нагрузка на направляющие сверла, то при данном износе режущей кромки не имело место и увеличение сил трения на направляющих. Этим и объясняется отсутствие заметного роста сил при глубоком сверлении. На основании проведенных в работе опытов по влиянию износа на силы резания можно утверждать, что наблюдаемые колебания сил по длине сверления связаны только с процессом схватывания на направляющих сверла, а не износом режущей кромки. Износ на направляющих сверла, когда длина их была равна 5 мм, а не износ по режущей кромке приводит к увеличению сил с ростом количества просверливаемых заготовок (рисунок 10). На это также не обращалось внимания. Увеличение сил по длине отверстия или после сверления нескольких заготовок связывали только с влиянием износа на режущих кромках сверла. Так М.А. Царенко [20] отмечает, что с увеличением суммарной глубины обработанных отверстий происходит затупление инструмента и при величине фаски износа по задней грани, равной 0,4 мм крутящий момент возрастает в 1,4 раза. При этом совершенно не упоминается, что увеличение момента может быть вызвано износом направляющих. Такое ошибочное представление о причинах изменения сил приводит к тому, что при сверлении переточку производят только по режущей кромке и не уделяют внимания состоянию направляющих сверла.

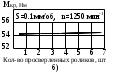
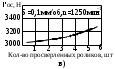
Рисунок 16–Изменение сил в зависимости от: а) глубины сверления одной
заготовки, б) количества просверленных заготовок
1.4 Анализ теоретических исследований моделей контакта при трении
Установлено, что вследствие волнистости и шероховатости поверхностей касание двух твердых тел всегда дискретно, то есть происходит в отдельных точках. В точках касания развиваются высокие удельные давления, приводящие к взаимному внедрению поверхностей на разную глубину [55, 62]. В зависимости от глубины внедрения характер нарушения фрикционных связей принято классифицировать как упругое оттеснение, пластическое оттеснение, микрорезание. Если известно распределение неровностей по высоте и величине сближения, то можно определить, какое число неровностей на какую глубину проникает. Диаметр единичного пятна касания поверхностей мало изменяется от нагрузки, поэтому кривая распределения неровностей по высоте может одновременно служить и для оценки величины площади касания. Величина фактической площади касания определяет силу трения, так как сила трения равна произведению удельной силы трения на фактическую площадь касания.
Износ с точностью до множителя l/n (где n- число циклов повторных воздействий на единичную фрикционную связь, приводящее к разрушению материала) также зависит от фактической площади касания. Поэтому вопрос об определении сближения и фактической площади касания является весьма важным для анализа процессов трения и износа. Впервые задача о сближении двух идеально гладких тел, имеющих криволинейные очертания, была рассмотрена Герцем [62]. Герц установил, что размеры и форма зоны контакта зависят от упругой деформации тел. Для двух сфер радиусами R1 и R2 центрально сжатых вместе силой


где

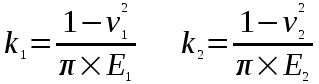
где V1, V2 - коэффициенты Пуассона,

В формуле 1.1 учитывается только нагрузка Р0 . Хотя известно, что чем больше сближение тел, тем сильнее их взаимодействие на молекулярном уровне, т.к. появляется составляющая адгезионного сцепления.
Сближение двух сферS под действием силы Ро описывается формулой

К полученным формулам (1.16, 1.17) Герц пришел через деформирование объемов. По утверждению И.Д. Крагельского, поверхность соприкасается с деформируемым материалом (рисунок 11) по поверхности 1, в то время как при построении кривой опорной поверхности учитывается только сечение 2.


Рисунок12–Контакт двух тел с разной твердостью поверхностей
Рисунок 11–Схема контакта идеально гладких тел

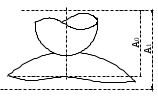
Модель Герца работает при различных диаметрах, коэффициентах Пуансона, модулях упругости и материалах сближаемых сфер. Но если контактируют два тела с различной твердостью, то контактная поверхность не окажется линейной, то есть одно тело углубится в другое (рисунок 12) и А0 будет неопределенной величиной.
Дальнейший вклад в изучение взаимодействия тел внесли Робертсон и Канделл. При небольших нагрузках ими были определены силы сцепления поверхностей, когда последние были сухими и смазанными. Эти дополнительные силы увеличивали область контакта и были особенно заметны при стремлении нагрузкиР0 к нулю, а контактная поверхность между сферами оказывается значительно больше, чем следует из формулы Герца. На рисунке 13 а штриховыми линиями показаны контактирующие сферы радиусов R1, R2, радиус контакта, рассчитанный по Герцу для нагрузки Р0 , равен а0. В действительности контакт имеет радиус а1, а сфера приобретает форму, показанную сплошными линиями. В результате адгезионного сцепления нагрузка Р1 > P0.

Рисунок 13–Контактирование сферических поверхностей
Распределение напряжений в зоне контакта показано на рисунок 13б. Кривые - С, А отображают напряжение сжатия для сил Р0 и Р1, а кривая В – действительное распределение напряжений. В области между кривыми А и В действуют растягивающие напряжения теоретически уходящие в минус бесконечность (практически определяющиеся силами сцепления сфер).
Ни Герц, ни Робертсон с Канделлом не указывают ограничения действия моделей, а из графика видно, что при нагрузке, которая дает пятно контакта, то есть диаметр самих шариков, сближение растет медленнее, чем диаметр пятна контакта. Рост диаметра пятна контакта с ростом нагрузки должен ускоряться, а сближение замедляется (за счет постоянства объема) (рисунок 14). При их расчетах не учитывался переход от упругого взаимодействия к пластическому.
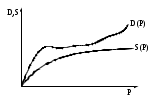
Рисунок 14–Зависимость диаметра пятна контакта D(P)
и величины сближения от нагрузки P
Упругое контактирование шероховатой поверхности моделированной в виде набора сфер с гладкой плоскостью.
Существует довольно много теоретических разработок по этому вопросу, но работа И. В. Крагельского [62] является основополагающей. Шероховатая поверхность в его работе моделируется в виде набора сферических выступов радиуса r, расположенных с постоянной плотностью (рисунок 15), закон распределения которых по высоте задается степенной функцией (1.3). При этом число выступов предполагается столь большим, что функция будет непрерывной.

где




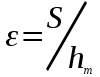
где S– сближение равное деформации наиболее высокого выступа,

И.В. Крагельский [62] установил, что уравнение (1.3) при надлежащем выборе параметров С и

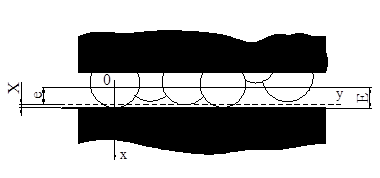
Рисунок 15–Схема контакта шероховатой поверхности с гладкой плоскостью
Сближение отдельного единичного выступа


где: Е – модуль упругости материала;r- радиус сферы;



где

Полная нагрузка, приложенная к поверхности, будет равна

т.е.




В формуле присутствуют те же величины, что и у Герца (нагрузка, модуль упругости, радиус сферы и коэффициент Пуассона). Затем Крагельский представляет нагрузку, как функцию от hmax константами С и


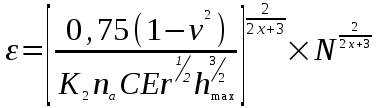
и

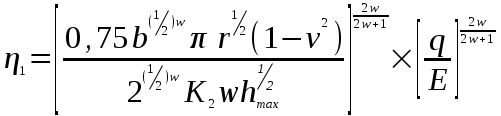
Из формулы (1.7) видно, что фактическая площадь контакта прямо пропорциональна радиусу выступов r, удельной нагрузке qи обратно пропорциональна модулю упругости Е, максимальной высоте неровностей и параметрам, характеризующим геометрию поверхностей

Зависимость величины относительной площади касания от контурного удельного давления


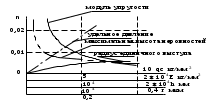
Рисунок 16–Влияние отдельных параметров на относительную площадь касания
Выводы
1. Анализ известных работ показывает, что вопросы повышения интенсивности обработки глубоких отверстий ранее рассматривались без учета специфики операции.
2. Ряд вопросов построения режимов, конструкции инструмента и оснастки ранее не рассматривался.
1.5 Цели и задачи исследования
Проведенный литературный обзор позволяет сформулировать цель работы: Разработка и исследование методов повышения износостойкости сверл малого диаметра.
Для достижения указанной цели необходимо поставить следующие задачи исследования, подлежащие решению в данной работе:
1. Установить закономерность влияния топологии направляющих поверхностей сверла на фактическую площадь контакта, маслоемкость стыка с обрабатываемым отверстием и износостойкость сверлильных головок.
2. Предложить методику проектирования направляющих поверхностей сверла и обрабатываемого отверстия при глубоком сверлении с определением фактической площади контакта, учитывающую режимы резания и направление неровностей направляющих поверхностей.
3. Установить зависимости для оценки фактической площади контакта применительно к взаимодействию направляющих сверла и обрабатываемого отверстия при глубоком сверлении с учетом режимов резания и направлений неровностей направляющих поверхностей.
4. Экспериментально подтвердить правомерность полученных зависимостей для повышения износостойкости инструмента для глубокого сверления.