Переработка отходов. 9.6. Переработка отходов. 9 оценкА перспективы переработкИ отходов горнометаллургических производств
![]()
|
700 т золота). |
Наименование | руда, тыс.т | медь | молибден | Перспектива переработки | ||
% | тыс.т | % | тыс.т | |||
Забалансовые руды | 165797,3 | 0,27 | 450,0 | 0,0065 | 10,8 | Рекомендовано к переработке по заводской технологии |
Отвальные хвосты флотации | 164377,3 | 0,17 | 279,2 | 0,003 | 5,3 | Рекомендована технология КБВ |
Шлаки отражательной и кислородно-факельной плавки | 12380,0 | 0,7 | 86,7 | | | Рекомендовано флотационное обогащение |
Наименование | руда, тыс.т | свинец | цинк | медь | Перспективы переработки | |||
% | тыс.т | % | тыс.т | % | тыс.т | |||
Забалансовые руды | 40029,1 | 0,42 | 169,9 | 0,42 | 169,1 | | | Рекомендовано к переработке по заводской технологии |
Клинкер медный | 532,730 | 0,32 | 1,70 | 1,94 | 10,3 | 1,4 | 7,45 | Рекомендовано к дальнейшим исследованиям |
Свинцовый кек | 39,533 | 41,3 | 16,0 | 9,5 | 3,7 | 0,26 | 0,102 | Проводятся исследования |
Технология переработки бедного (0,2-0,3 г/т) золотосодержащего минерального сырья к настоящему времени полностью не разработана. В этом направлении ведутся целенаправленные исследования по совершенствованию технологических процессов рудосортировки и обогащению техногенных руд с целью извлечения золота с удовлетворительными показателями. Проводится паспортизация отвалов минерализованной массы, обогащение техногенных руд с применением различных методов сортировки, извлечение золота по технологии глубокой гравитации, кучного выщелачивания, биовыщелачивания золотосодержащих руд и других методов.
Исследованиями подтверждена целесообразность переработки забалансовых руд забойной крупности (1825 тыс. т) месторождения Аджибугут методом кучного выщелачивания (содержание 0,82 г/т, 1494 кг золота).
Таблица 9.37
Техногенная сырьевая база Навоийского ГМК по состоянию на 01.01.2009 г.
Месторождение | Запасы, тыс.т. | Содержание Au, г/т | Технология переработки |
Забалансовые руды | |||
Аджибугут - окисл.+смешан. | 1825,0 | 0,82 | проводится исследование по КВ золота |
Зармитан, скл. №1, 14 | 72,4 | 0,75 | рекомендована рудосортировка |
Итого | 1897,4 | | |
Отвалы добычи руд | |||
Мурунтау | 1973679,1 | 0,33 | рекомендована к рудосортировке и переработке гидрометаллургическим способом |
Кокпатас (уч. “Восточный”) | 60200 | 0,23 | технология отсутствуют |
Даугызтау | 12320,0 | 0,22 | технология отсутствует |
Аджибугут | 5740,0 | 0,22 | технология отсутствует |
Марджанбулак | 35000,0 | 0,35 | технология отсутствует |
Зармитан | 36540,0 | 0,30 | технология отсутствует |
Каракутан | 400,4 | 0,3 | технология отсутствует |
Итого: | 2123879,0 | | |
Промежуточные отходы | |||
Магнитная фракция ГМЗ-2 | 54,9 | 14,76 | сернокислотное выщелачивание магнитной фракции, получение сульфата железа, извлечение золота из кека сорбционным цианированием |
Итого: | 54,9 | 14,76 | |
Отвалы процесса сорбции и кучного выщелачивания | |||
ГМЗ-1 | | | используются для экранирования радиоактивных отходов производства урана |
ГМЗ-2, хвостохранилища | 716662,0 | 0,14 | технология отсутствует |
Отходы КВ золота, ЦКВЗ ЦРУ | 157000,0 | 0,6 | предложено обогащение бортовой и верхней части кучи методом глубокой гравитации |
ГМЗ-3, хвосто-хранилища | 51500,0 | 0,16 | технология отсутствует |
Марджанбулакская ЗИФ, хвостохранилища | 10000,0 | 0,8 | рекомендована сорбционная технология извлечения золота в смеси с рудой |
Итого: | 778162,0 | | |
На ГМЗ-2 в настоящее время накоплено около 20 тыс. т магнитной фракции с содержанием золота 10-20 г/т, которые содержат более 300 кг золота. Для ее переработки на ГМЗ-1 налажено производство железного купороса. При этом золотосодержащий кек возвращается в технологический процесс извлечения золота, а железный купорос используется для очистки воды г. Навои и утилизации цианидов. Объемы производств купороса ограничены спросом этой продукции.
Переработка более 10 млн. т хвостов Марджанбулакской ЗИФ с содержанием золота около 0,8 г/т по действующей технологии МЗИФ (совместно с исходной рудой или в отдельности) позволит продлить срок службы фабрики на 8-10 лет.
В настоящее время имеются отходы цеха кучного выщелачивания золота (ЦКВЗ) (бывший СП «Зарафшан-Ньюмонт») в количестве 157 млн. т со средним содержанием 0,6 г/т (94,2 т золота). Проблему извлечения золота предлагается решить в два этапа: на первом этапе поверхностные и боковые части кучи с неполным выщелачиванием золота обогащают методом глубокой гравитации, а на втором этапе - сортировка оставшейся части отходов для последующей переработки по заводской технологии.
Д
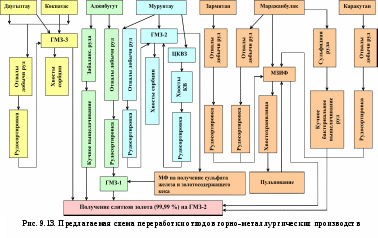
В хвостохранилищах ГМЗ-2 и ГМЗ-3 находится 768,2 млн. т отработанной руды с содержанием около 0,2 г/т (108,5 т золота). В перспективе она так же может оказаться техногенным сырьем для получения продукции.
Таким образом, в настоящее время заскладированные забалансовые руды, вскрышные породы (минерализированные массы), промежуточные отходы процесса рудоподготовки и гидрометаллургии, отвальные хвосты процесса кучного выщелачивания, флотации и сорбции, шлаков процесса пирометаллургии можно рассматривать как техногенные месторождения. Оценка экономической эффективности разработанных технологий переработки отходов горно-металлургических производств приведена в табл. 9.38
Результаты разработанной технологии переработки отходов горно - металлургических производств представлены на рис. 9.14.
Таблица 9.38
Оценка экономической эффективности разработанных технологий
переработки отходов горно-металлургических производств
Источник образования ресурсов и постановка задач | Пути и приемы решения задач | Достигнутый результат |
Отходы переработки медно-молибденовых руд: 1.1. отвальные хвосты флотации 1.2. шлаки отражательной и кислородно-факельной плавки Получение товарной руды из отходов производства | Вовлечение в переработку отходов горно - металлургических производств биокислением хвостов флотации с последующим выщелачиванием меди, золота и серебра | 1.1. Рекомендована технология КБВ 1.2. Рекомендовано флотационное обогащение Расширение сырьевой базы на 176,8 млн.т и увеличение выпуска меди на 365,9 тыс.т Получено из отходов производства Cu 11206 т/ год, Au – 350 кг/год Экономический эффект составляет 46,9 млн.$/год |
Отходы переработки свинцово-цинковых руд: 2.1. клинкер медный 2.2. свинцовый кек Получение товарной руды из отходов производства | Вовлечение в переработку отходов горно - металлургических производств флотационным обогащением шлаков | Расширение сырьевой базы на 572,3 тыс.т и увеличение выпуска свинца на 17,7 тыс.т, цинка на 19,8 тыс.т, меди на 7,6 тыс.т |
Отходы переработки золотосодержащих руд: 3.1. отвалы добычи руд карьера Мурунтау 3.2. магнитная фракция ГМЗ-2 3.3. отходы кучного выщелачивания золота 3.4. хвостохранилище МЗИУ Получение товарной руды из отходов производства | 3.Вовлечение в переработку отходов горного производства 3.1. Рудосортировка и переработка гидрометаллургическим способом 3.2. Сернокислотное выщелачивание, получение сульфата железа, извлечение золота из кека сорбционным цианированием 3.3. Предложено обогащение бортовой и верхней части кучи методом глубокой гравитации 3.4. Рекомендована сорбционная технология извлечения золота в смеси с рудой | - Увеличение и поддержание на заданном уровне выпуска золота. - Расширение сырьевой базы золота на 1,0 млн.т. |
Решение научно-технической проблемы обоснования и разработки технологии переработки отходов горно-металлургических производств расширяет сырьевую базу и продлевает срок эффективной работы: АГМК - МОФ и цинкового завода на 50 лет; НГМК - ГМЗ-2 на 28лет, МЗИУ на 10 лет. |
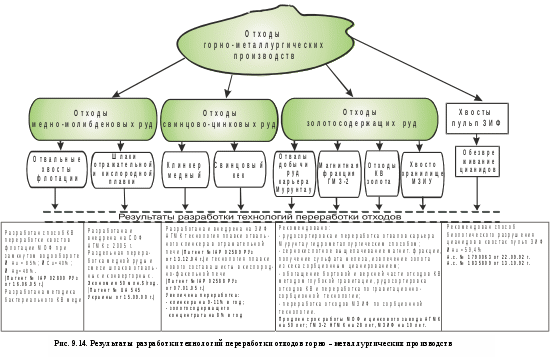
Создание производств для комплексной переработки техногенных месторождений позволит решить ряд проблем городов и районов с монопроизводством: уменьшить нагрузку на местные рынки труда, увеличить объемы средств, поступающих в местные бюджеты, снизить экологическое загрязнение окружающей среды, вернуть в оборот земли, находящиеся в настоящий момент под отвалами и хвостохранилищами, получить ценную продукцию, востребованную на рынке.
Разработка техногенных месторождений позволит перейти к рациональному природопользованию с обеспечением взаимосвязей разных экологических и социально-экономических факторов, для снижения негативного влияния последствий деятельности горных предприятий на окружающую среду с учетом социально-экономических интересов региона.