Нормирование точности и контроль деталей сборочной единицы
![]()
|
|
Наименования исходных данных | Значения исходных данных |
Контролируемая поверхность (вал или отверстие) | Отверстие, D=60 мм |
Исполнительный размер (D1,D2, D3 или d1, d2, d3) | ![]() |
Допуск на контролируемый размер, мкм | 30 |
Коэффициент технологической точности ![]() | 4 |
Тип производства | Серийное |
Задание. Для заданной поверхности детали по варианту требуется выбрать универсальные средства измерения для цехового и арбитражного контроля; определить параметры разбраковки при заданной относительной точности изготовления; решить вопрос о введении производственного допуска. Представить схемы вариантов приемочных границ.
Решение.
Для заданного диаметра по решению задания 1.1.3 назначена посадка


Так как процесс нестабильный (

Для допуска на изготовление (IT=30 мкм) по [1, табл. Г1] найдём допускаемую погрешность измерения δ=9 мкм.
Выберем возможные средства измерения, удовлетворяющие условию:

где


По таблице [1, табл. Г2] определим средства измерения, удовлетворяющие данному условию. Это:
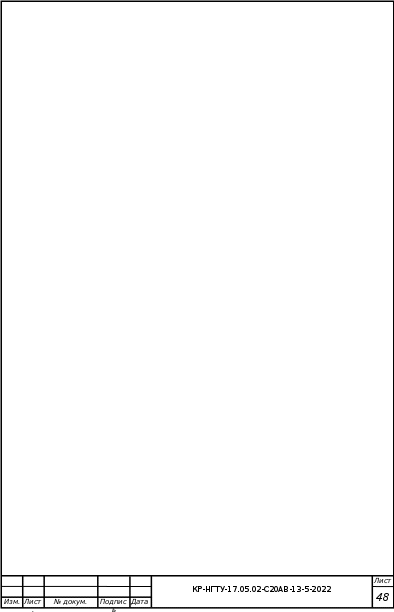

Методы измерения: контактный, относительный, косвенный.

Нутромер индикаторный, повышенной точности
(КМД-3 кл.

Методы измерения: контактный, относительный, косвенный.

Нутромер индикаторный, повышенной точности
(КМД-3 кл.

Методы измерения: контактный, относительный, косвенный.

Пневмопробки с отсчётным прибором

Методы измерения: бесконтактный, относительный, косвенный.

Пневмопробки с отсчётным прибором

Методы измерения: бесконтактный, относительный, косвенный.

Учитывая наличие средств измерений в лаборатории, их стоимость и удобство в эксплуатации, выбираем нутромер индикаторный НИ-100 (50-100) (ГОСТ 9244) КМД 3 кл.


Определим относительную точность метода измерения:
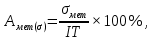
где

При доверительной вероятности P=0,95 случайная погрешность (соответствующая не исключённой инструментальной погрешности



Для нашего случая имеем:
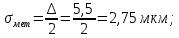

Принимаем
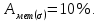
По графикам на рисунке [1, рис. Г1] при

m=0,3%;
n=2%;

Следовательно,

Рассчитаем предельно допустимые размеры, по которым производится оценка годности деталей:


Определим достоверность контроля по теории вероятностей:

где m и n– в сотых долях.

Среди годных деталей могут оказаться бракованные детали (не более 0,3%), у которых размеры выходят за границы поля допуска на величину до 1 мкм. Это риск заказчика. Риск изготовителя в этом случае будет не более 2%,
т. е. будут забракованы фактически годные детали.
Принимаем условие недопустимости риска заказчика, в этом случае увеличивается риск изготовителя.
Производим расчёт производственного допуска:

Предельно допустимые размеры с учётом производственного допуска:



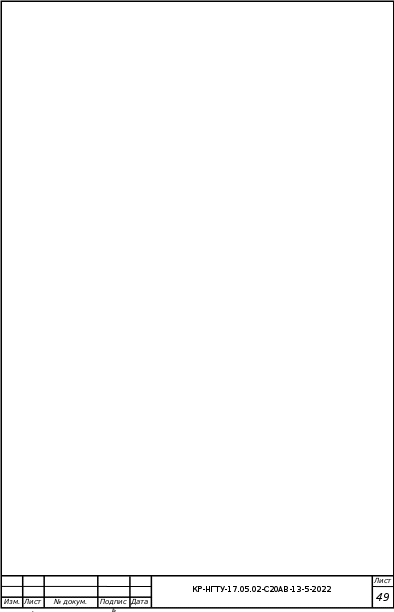
Определим допускаемую погрешность измерения при арбитражной перепроверке:

По таблице [1, табл. Г2] для арбитражной проверки выбираем горизонтальный оптиметр ИКГ (±0,1 по шкале); (0-300); КМД-3 класса.
Его технические характеристики: цена деления 0,001 мм, предельная инструментальная погрешность

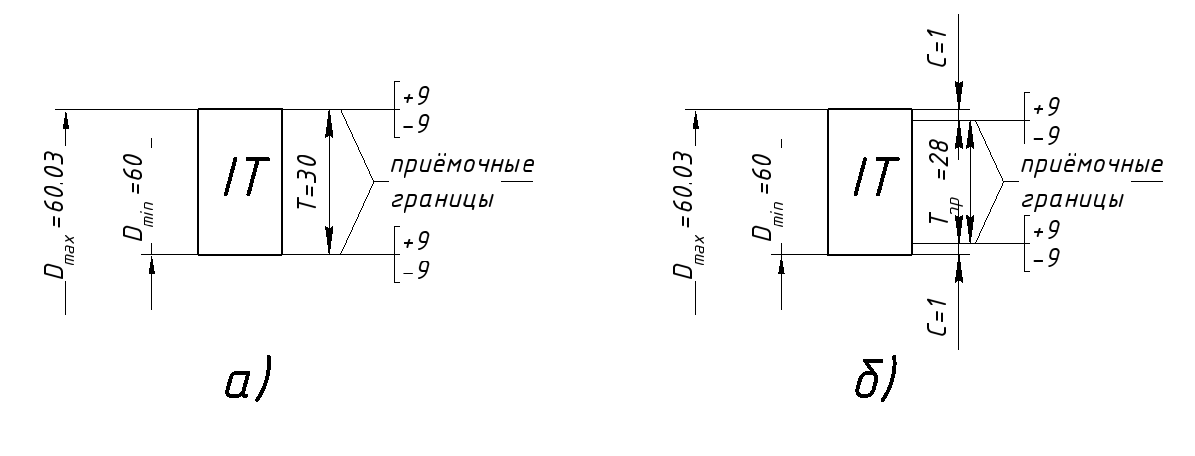
Приёмочные границы:
а – без производственного допуска; б – с производственным допуском.
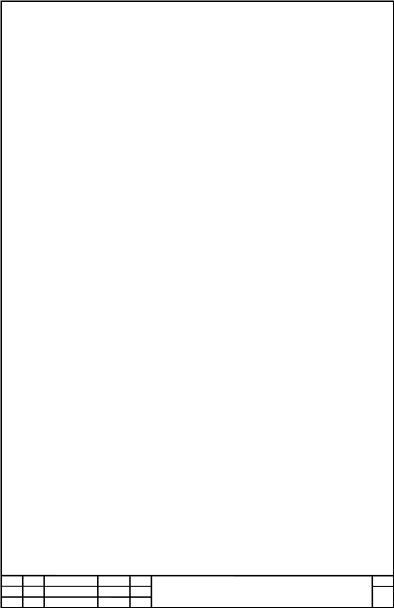
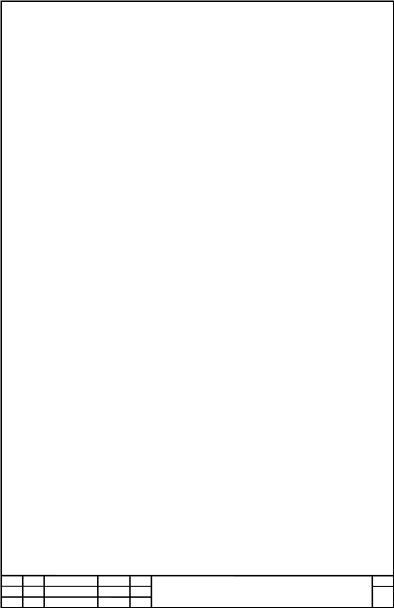
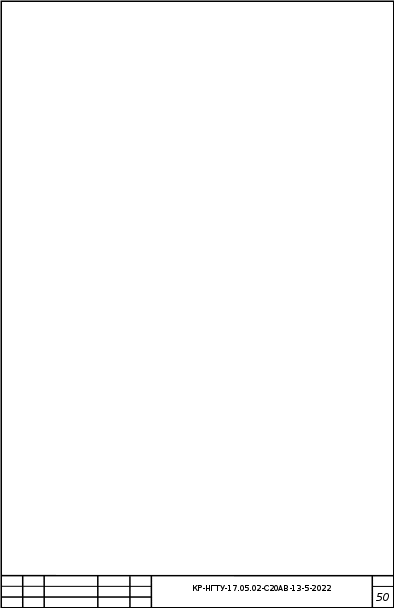
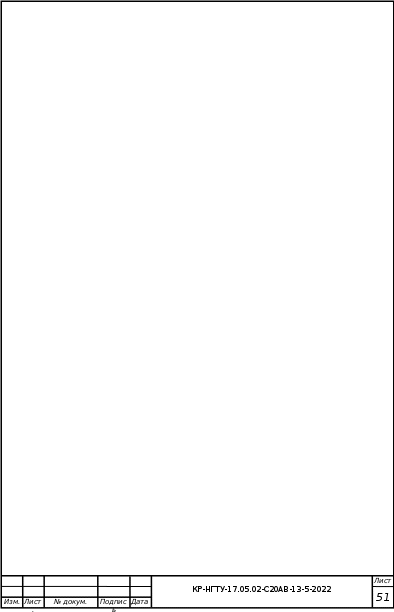
Основная
1. кайнова в. н. Метрология, стандартизация и сертификация: Практикум: Учебное пособие / Кайнова В. Н., Гребнева Т. Н. [и др.], под ред. В. Н. Кайновой; СПб.: Издательство «Лань», 2022. – 368 с.
2. Кайнова, В.Н. Нормирование точности изделий машиностроения: учеб. пособие / В.Н. Кайнова [и др.]; НГТУ. Н.Новгород, 2007.−207с.
3. Нормирование точности деталей машин: метод. указ./ сост.: Л.А. Болдин [и др.]; НГТУ. Н.Новгород, 1999.
4. Нормирование точности деталей машин: метод. указ./ сост.: В.Н. Кайнова, И.Н. Фролова [и др.]; НГТУ. Н. Новгород, 1996.
5. Проектирование гладких калибров для контроля валов и отверстий: метод. указ. / сост.: В.Н.Кайнова [и др.]; НГТУ. Н.Новгород, 2004.
6. Выбор универсальных средств измерения: метод. указ./ сост.: В.Н. Кайнова, [и др.]; НГТУ. Н. Новгород, 1996.
Дополнительная
7. Белкин И. М. Допуски и посадки /И. М. Белкин. − М.:Машиностроение, 1992.
8. Марков Н. Н. Нормирование точности в машиностроении: – учеб. для машиностр. спец. вузов / Н. Н. Марков [и др.], под ред. Ю. М. Соломенцева. – 2-е изд., испр. и доп..− М.: Высш. шк., 2001.
9. Марков А. Л. Измерение зубчатых колес / А. Л. Марков. − Л.: Машиностроение, 1977.
10. Допуски и посадки: справочник в 2-х ч. / под ред. В. Д. Мягкова. − Л.: Машиностроение, 1983.
11. Дунаев П. Ф. Расчет допусков размеров / П. Ф. Дунаев, О. П. Леликов. − М.: Машиностроение, 1992.
12. Палей М. А. Допуски и посадки: справочник в 2-х ч./ М. А. Палей [и др.]. − Л.: Политехника, 1991.
13. Черменский О. Н. Подшипники качения: справочник-каталог/ О.Н. Черменский, Н. Н. Федотов. − М.: Машиностроение, 2003.
14. Радкевич Я. М. Метрология, стандартизация и сертификация: учеб для вузов / Я. М. Радкевич [и др.]. − М.: Высш. шк., 2004.
15. Варианты заданий курсовых работ по дисциплине «Метрология, стандартизация и сертификация» Ч.2: метод. указ./ сост.: В. Н. Кайнова [и др.]; НГТУ. Н.Новгород, 2006.
16. Кайнова В. Н., Гребнева Т. Н. Метрология, стандартизация и сертификация: комплекс учебно-методических материалов: Ч1/ В. Н. Кайнова, Т. Н. Гребнева; НГТУ, Н.Новгород,2006.
Нормативная документация
1. ГОСТ 2.307-2011 ЕСКД. Нанесение размеров и предельных отклонений.
2. ГОСТ 2.308-2011 ЕСКД. Указание на чертежах допусков формы и распо-ложения поверхностей.
3. ГОСТ 2.309-73 ЕСКД. Обозначение шероховатости поверхности.
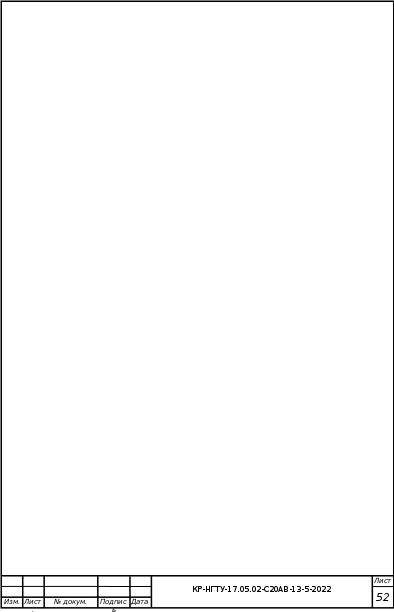
5. ГОСТ 2.409-74 ЕСКД. Правила выполнения чертежей зубчатых (шлицевых) соединений.
6. ГОСТ 25346-2013 ОНВ. Характеристики изделий геометрические. Система допусков на линейные размеры. Основные положения, допуски, отклонения и посадки.
7. ГОСТ 25347-82 ОНВ. Характеристики изделий геометрические. Система допусков на линейные размеры. Ряды допусков, предельные отклонения отверстий и валов.
8. ГОСТ 24642-81 ОНВ. Допуски формы и расположения поверхностей.
Основные термины и определения.
9. ГОСТ 24643-81 ОНВ. Допуски формы и расположения. Числовые значения.
10. ГОСТ 520-2011 Подшипники качения. Общие технические условия.
11. ГОСТ 3189-89 Подшипники шариковые и роликовые. Система условных обозначений.
12. ГОСТ 3325-85 Подшипники качения. Поля допусков и технические
требования к посадочным поверхностям валов и корпусов. Посадки.
13. ГОСТ 8724-2002 ОНВ. Резьба метрическая. Диаметры и шаги.
14. ГОСТ 9150-2002 ОНВ. Резьба метрическая. Профиль.
15. ГОСТ 16093-2004 ОНВ. Резьба метрическая. Допуски. Посадки с зазором.
16. ГОСТ 24705-2004 ОНВ. Резьба метрическая. Основные размеры.
17. ГОСТ 1139-80 ОНВ. Соединения шлицевые прямобочные. Размеры и
допуски.
18. ГОСТ 23360-78 ОНВ. Соединения шпоночные с призматическими шпонками. Размеры шпонок и сечений пазов. Допуски и посадки.
19. ГОСТ 8.051-81 ГСИ. Погрешности, допускаемые при измерении линейных размеров до 500 мм.
20. ГОСТ 8.549-86 ГСИ. Погрешности, допускаемые при измерении линейных размеров до 500 мм с неуказанными допусками.
21. РД 50-98-86 Выбор универсальных средств измерений линейных размеров до 500 мм.
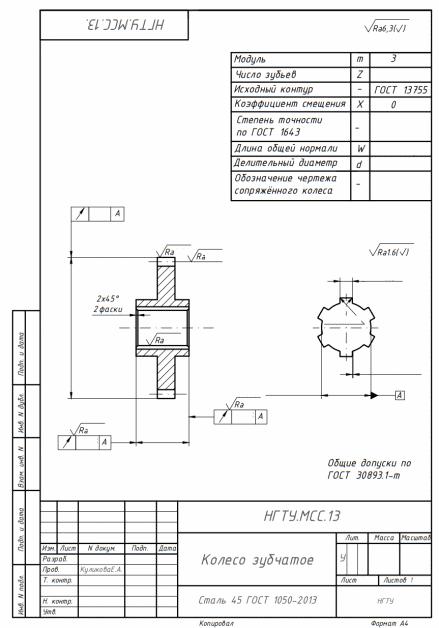