Практика. практика. Отчет по практике
![]()
|
|
Филиал РГУ нефти и газа (НИУ) имени И.М. Губкина в г. Оренбурге | |
Отделение | химической технологии переработки нефти, газа и экологии |
Оценка: | | Рейтинг: | | ||
Руководитель практики: | |||||
| | доцент Курякова Т.А. | |||
(подпись) | | (фамилия, имя, отчество) | |||
| | | |||
| |||||
(дата) | |||||
| | |
ОТЧЕТ ПО ПРАКТИКЕ
Наименование практики: | Каталитический крекинг |
| |
|
Место прохождения практики: | Филиал ГРУ нефти и газа (НИУ) |
имени Губкина в г. Оренбурге | |
| |
(отделение, структурное подразделение; наименовании организации) |
| | ВЫПОЛНИЛ: | ОХТ-15-01 |
| | Студент группы | |
| | | (номер группы) |
| | Федоренко С.В. | |
| | (фамилия, имя, отчество) | |
| | | |
| | (подпись) | |
| | | |
| | (дата) |
| Оренбург, 2018 | |
Введение
Кре́кинг (англ. cracking, расщепление) — высокотемпературная переработка нефти и её фракций с целью получения, как правило, продуктов меньшей молекулярной массы — моторных топлив, смазочных масел и т. п., а также сырья для химической и нефтехимической промышленности.
Различают три основных вида крекинга:
Термический -осуществляемый под действием высокой температуры и давления; Термический крекинг проводят, напр., при 450-550 °С, давлении 4-6 МПа.
Каталитический крекинг -каталитический, происходящий при одновременном воздействии высокой температуры, давления и катализатора. осуществляют, напр., при 450-500 °С, давлении до 0,4 МПа, в присутствии катализаторов - алюмосиликатов.
Гидрокрекинг-переработка высокипящих нефтяных фракций,мазута, акуумного газойля для получения бензина, дизельного и реактивного топлива, смазочных масел,сырья для каталитического крекинга. Проводят под действием водорода при температуре 330-450 °С и давлением 5-30 МПа в присутствии никель-молибденовых катализаторов. [1]
1. Значение и назначение процесса
Процесс каталитического крекинга является одним из наиболее распространенных крупнотоннажных процессов углубленной переработки нефти и в значительной мере определяет технико-экономические показатели современных и перспективных НПЗ топливного профиля.
Основное целевое назначение каталитического крекинга – производство с максимально высоким выходом ( до 50% и более) высокооктанового бензина и ценных сжиженных газов – сырья для последующих производств высокооктановых компонентов бензинов изомерного строения: алкилата и метил-трет-бутилового эфира, а также сырья для нефтехимических производств. Получающийся в процессе легкий газойль используется обычно как компонент дизельного топлива, а тяжелый газойль с высоким содержанием полициклических ароматических углеводородов – как сырье для производства технического углерода или высококачественного электродного кокса (например, игольчатого).
Процессы каталитического крекинга получили наибольшее развитие в США, где удельный вес их в 1999г. составил 34,2% от первичной переработки нефти, причем на некоторых НПЗ этот показатель достигает свыше 50%. Доля этого процесса на НПЗ других развитых капиталистических стран составляет 10-15%.[5]
Еще в 1919-1920-х гг. академиком Н.Д.Зелинским была предложена идея по осуществлению низкотемпературного каталитического крекинга (200°С) нефтяного сырья на хлориде алюминия. На основе этих работ была создана и испытана опытная установка по получению бензина. Однако в силу существенных недостатков хлорида алюминия как катализатора (сильная коррозия аппаратуры, большой расход катализатора вследствие образования комплексных соединений с углеводородами, периодичность процесса и др.) эта идея не нашла промышленного внедрения. Первая промышленная установка по каталитическому крекингу керосино-газойлевых фракций, которая была пущена в США в 1936г., представляла собой периодически регенерируемый процесс со стационарным слоем катализатора из природной глины. В 1940г. [3] Природная глина была заменена на более активный синтетический гранулированный алюмосиликатный катализатор (установки Гудри). В 1942г. Промышленный процесс каталитического крекинга переводят на непрерывную схему с применением шарикового катализатора, циркулирующего между реактором и регенератором. В последующие годы возникли и нашли широкое промышленное внедрение более совершенные установки каталитического крекинга с кипящим слоем микросферического катализатора.[2]
Решающее значение для дальнейшего усовершенствования и интенсификации установок каталитического крекинга сыграли разработка в 1962г. и промышленное внедрение цеолитсодержащих алюмосиликатных катализаторов. Более высокие активность, селективность и термостабильность которых позволили существенно увеличить выход бензина, а также разработать и внедрить (1971г.) высокоинтенсивные технологии каталитического крекинга с прямоточным реактором – с восходящим потоком микросферического катализатора в так называемом лифт – реакторе.
2.Сырье для каталитического крекинга
В качестве сырья в процессе каталитического крекинга в течение многих десятилетий традиционно использовали вакуумный дистиллят (газойль) широкого фракционного состава (350-500°С). [2]В ряде случаев в сырье крекинга вовлекаются газойлевые фракции термодеструктивных процессов, гидрокрекинга, рафинаты процессов деасфальтизации мазутов и гудронов, полупродукты масляного производства и др. В последние годы в мировой нефтепереработке наблюдается тенденция к непрерывному утяжелению сырья.
На современных зарубежных установках перешли к переработке глубоковакуумных газойлей с температурной конца кипения 540-620°С. На специально запроектированных установках каталитическому крекингу подвергают остаточное сырье: мазуты и даже гудроны или их смеси с дистиллятным сырьем без или после предварительного облагораживания гидроочиткой, деасфальтизацией или деметаллизацией. [4]
Всю совокупность показателей, характеризующих качество сырья, по степени влияния на процесс каталитического крекинга условно можно подразделить на слудующие три группы:
Показатели, влияющие на выход (т.е. на материальный баланс) и качество продуктов крекинга: фракционный и групповой химический состав и содержание гетероорганических соединений;
Показатели, влияющие на обратимую дезактивацию катализатора, такие как плотность, коксуемость и содержание сернокислотных смол;
Показатели, влияющие на необратимую дезактивацию катализатора: содержание металлов, прежде всего ванадия и никеля. [7]
По фракционному составу к сырью процесса предъявляются следующие требования: практически полное отсутствие бензино-лигроиновых фракций, поскольку в условиях крекинга они претерпевают незначительные превращения, к тому же нерационально загружают реакционный аппарат и отрицательно влияют на октановое число бензина; ограниченное (до 10 %) содержание фракций, выкипающих до 350° С; ограниченная температура конца кипения (500-620 °С), что обусловливается концентрированием в высококипящих фракциях коксогенных компонентов сырья (смол и асфальтенов) и гетероорганических соединений и металлов. [3]
Групповой химический состав сырья более значительно влияет на выход и качество продуктов крекинга. В большинстве вакуумных газойлей, направляемых на каталитический крекинг, в зависимости от типа исходной нефти содержание в них групповых компонентов колеблется в довольно широких пределах; парафиновых 15-35% нафтеновых 20-40 % и ароматических 15-60 %.
Наилучшим для каталитического крекинга по выходу целевых продуктов (бензина и сжиженных газов) является сырье с преобладанием парафиновых и нафтеновых углеводородов. Полициклические ароматические углеводороды и смолы сырья в условиях крекинга дают мало бензина и много тяжелых фракций и кокса. Сернистые и кислородные соединения однотипного по химическому составу сырья не оказывают существенного влияния на материальный баланс каталитического крекинга, но ухудшают качество продуктов. [6] Однако следует указать, что с увеличением содержания гетероорганических соединений в сырье, как правило, одновременно повышается содержание в нем полициклических углеводородов и смол.
К компонентам, обратимо дезактивирующим катализаторы крекинга, относят полициклические ароматические углеводороды, смолы, асфальтены и азотистые соединения сырья. Об обратимой дезактивирующей способности сырья можно судить: косвенно по плотности, а количественно — по коксуемости, определяемой по Конрадсону. [9] Как правило, чем выше коксуемость сырья, тем больше выход кокса на катализаторе.
Обычно на установках каталитического крекинга преимущественно перерабатывают типовое сырье (вакуумный газойль 350-500° С) с коксуемостью не более 0.3-0.5 % мас. Если регенератор имеет запас мощности по массе сжигаемого кокса, то может быть использовано сырье с коксуемостью до 2-3 % мас. На специальных установках, предназначенных для крекинга остаточного сырья и имеющих системы отвода тепла из регенератора, допускается коксуемость сырья до 5% мас.
Обратимыми ядами для алюмосиликатных катализаторов являются азотистые основания: они прочно адсорбируются на кислотных активных центрах и блокируют их. При одинаковых основных свойствах большее дезактивирующее воздействие на катализатор оказывают азотистые соединения большей молекулярной массы. После выжига кокса активность отравленного азотистыми основаниями катализатора полностью восстанавливается. Цеолитсодержащие катализаторы, благодаря молекулярно-ситовым свойствам, отравляются азотом в значительно меньшей степени, чем аморфные алюмосиликатные. [2]
Металлоорганические соединения, содержащиеся преимущественно в высококипящих и особенно остаточных фракциях нефти, относят к необратимо дезактивирующим компонентам сырья крекинга. Блокируя активные центры катализатора, они отрицательно влияют не только на его активность, но и на селективность. Так, по мере увеличения содержания никеля и ванадия, являющихся, как известно, дегидрирующими металлами, интенсивно возрастает в продуктах крекинга выход водорода и сухих газов, а выход бензина существенно снижается.
На установках каталитического крекинга, на которых не предусмотрены специальные приемы но улавливанию или пассивации отравляющего действия металлов, содержание их в сырье нормируется не более 2 г/т. Для переработки сырья с коксуемостью более 10 % масс. и содержащем металлов 10- 30 г/г и более требуется обязательная его предварительная подготовка. [5]
3. Облагораживание сырья каталитического крекинга
С целью снижения содержания металлов и коксогенных компонентов в сырье до такой степени, чтобы его последующая каталитическая переработка была бы более экономична, т.е. при умеренных габаритах регенератора и без чрезмерного расхода дорогостоящего катализатора, осуществляется его подготовка.
Из процессов облагораживания сырья каталитического крекинга в настоящее время широко применяется каталитическая гидроочистка преимущественно вакуумных газойлей и более тяжелого сырья с ограниченным содержанием металлов.
К сырью гидрогенизационных процессов, по сравнению с каталитическим крекингом, не предъявляется столь жестких ограничений по коксуемости, поскольку скорости коксообразования в этих процессах несопоставимы. Однако по содержанию металлов к сырью обоих процессов предъявляются практически одинаковые ограничения, поскольку металлы сырья одинаково необратимо дезактивируют как металлические центры, так и кислотные центры катализаторов. [7]
Необходимо отметить следующие достоинства комбинированной каталитической переработки с предварительной гидроочисткой сырья крекинга:
существенно снижается содержание сернистых и азотистых соединений во всех жидких продуктах каталитического крекинга и содержание оксидов серы в газах регенерации, в результате отпадает необходимость в их облагораживании и снижаются выбросы вредных газов в атмосферу
полициклические ароматические углеводороды и смолы сырья при гидроочистке подвергаются частичному гидрокрекингу с образованием алкилароматических углеводородов с меньшим числом колец, в результате снижается коксообразование в процессе каталитического крекинга; ·
существенно снижается содержание металлов в гидроочищенном сырье, что снижает расход катализаторов крекинга;
при каталитическом крекинге гидроочищенного сырья увеличивается выход целевых (более высокого качества) продуктов и снижается выход газойлей и кокса. [3]
К недостаткам комбинированной переработки следует отнести увеличение капитальных и эксплуатационных затрат и возможность переработки сырья с ограниченным содержанием металлов.
К некаталитическим процессам подготовки сырья к каталитическому крекингу (а также гидрокрекингу) не предъявляются таковые ограничения по содержанию металлов, что позволяет значительно расширить ресурсы сырья за счет вовлечения остаточных видов сырья. Но они характеризуются повышенными капитальными и эксплуатационными затратами, из-за чего сдерживается их широкое применение в современной нефтепереработке.
Из внедренных в промышленном масштабе в нефтепереработке методов некаталитической подготовки остаточных видов сырья следует отметить процессы сольвентной и термоадсорбционной деасфальтизации и деметаллизации.
Сольвентная деасфальтизация с использованием в качестве растворителей пропана, бутана, пентана или легкого бензина основана на технологии подобной пропановой деасфальтизации гудронов, применяемой в производстве смазочных масел. В этих процессах наряду с деасфальтизацией и обессмоливанием достигаются одновременно деметаллизация, а также частичное обессеривание и деазотирование тяжелых нефтяных остатков (ТНО), что существенно облегчает последующую их каталитическую переработку. [4]
В случае применения некаталитических процессов облагораживания ТНО возможна трехступенчатая переработка остаточного сырья по схеме: деасфальтизация гудрона (сольвентная или термоадсорбционная) → гидрообессеривание смеси деасфальтизата и вакуумного газойля → каталитический крекинг гидрогенизата.
Целевым назначением процесса 3D (дискриминационной деструктивной дистилляции) является подготовка нефтяных остатков (тяжелых нефтей, мазутов, гудронов, битуминозных нефтей) для последующей каталитической переработки путем жесткого термоадсорбционного крекинга в реакционной системе с ультракоротким временем контакта (доли секунды) циркулирующего адсорбента (контакта) с нагретым диспергированным сырьем. В отличие от АРТ в процессе 3D вместо лифт-реактора используется реактор нового поколения, в котором осуществляется исключительно малое время контакта сырья с адсорбентом на коротком горизонтальном участке трубы на входе в сепаратор циклонного типа. Эксплуатационные испытания демонстрационной установки показали, что выход и качество продуктов 3D выше, чем у процесса АРТ. [8]
Процесс АКО (адсорбционно-контактная очистка) разрабатывался во ВНИИНП в 1980-1990-х гг. и испытан в широком масштабе, предназначен для глубокой очистки нефтяных остатков от нежелательных примесей; по аппаратурному оформлению реакционной системы (лифт-реакторного типа) аналогичен процессу АРТ. В качестве адсорбента используется природный мелкозернистый каолин . Типичный режим процесса: массовая скорость подачи сырья - 20; время контактирования — 0,5 с; температура в реакторе — 520 °С. [8]
В результате очистки мазута происходит удаление тяжелых металлов на 95-98 %, серы - на 35-45 %, азота — на 50-60 %, а коксуемость снижается на 75-80 % мас. Процесс АКО характеризуется низкими выходами газа и бензина (5-6 и 6-8 % мас. соответственно ) и высокими выходами газойлевой фракции (порядка 80 %мас.). Выход кокса составляет 125 % от коксуемости сырья по Кондрадсону. Тяжелый газойль и широкая газойлевая фракция являются качественным сырьем каталитического крекинга после предварительной гидроочистки. Применяемый в процессе адсорбент позволяет полностью исключить выбросы оксидов серы с газами регенерации. [8]
4. Катализаторы крекинга
Катализаторы современных крупнотоннажных процессов каталитического крекинга, осуществляемых при высоких температурах (500-800 °С) в режиме интенсивного массо- и теплообмена в аппаратах с движущимся или псевдоожиженным слоем катализатора, должных обладать не только высокими активностью, селективностью и термостабильностью, но и удовлетворять повышенным требованиям к ним по регенерационным, механическим и некоторым другим эксплуатационным свойствам. Промышленные катализаторы крекинга представляют собой в этой связи сложные многокомпонентные системы, состоящие из: 1) матрицы (носителя); 2) активного компонента — цеолита; 3) вспомогательных активных и неактивных добавок. [7]
Матрица катализаторов крекинга выполняет функции как носителя — поверхности, на которой затем диспергируют основной активный компонент — неолит и вспомогательные добавки, так и слабого кислотного катализатора предварительного (первичного) крекирования высокомолекулярного исходного нефтяного сырья. В качестве материала матрицы современных катализаторов крекинга преимущественно применяют синтетический аморфный алюмосиликат с высокой удельной поверхностью и оптимальной поровой структурой, обеспечивающей доступ для крупных молекул крекируемого сырья.
Аморфные алюмосиликаты являлись основными промышленными катализаторами крекинга до разработки цеолитсодержащих катализаторов. Синтезируются они при взаимодействии растворов, содержащих оксиды алюминия и кремния, например жидкого стекла и сернокислого алюминия . Химический состав аморфного алюмосиликата может быть выражен формулой , где х — число молей на 1 моль . Обычно в промышленных аморфных алюмосиликатах содержание оксида алюминия находится в пределах 6-30% мас. [7]
Аморфные алюмосиликаты обладают ионообменными свойствами, а для придания каталитической активности обрабатывают их раствором сернокислого алюминия для замещения катионов на . Высушенные и прокаленные аморфные алюмосиликаты проявляют протонную и апротонную кислотности. При этом по мере повышения температуры прокаливания происходит превращение протонных кислотных центров в апротонные. [9]
Активным компонентом катализаторов крекинга является цеолит, который позволяет осуществлять вторичные каталитические превращения углеводородов сырья с образованием конечных целевых продуктов. Цеолиты (от греческого слова цео — кипящий, литос — камень) представляют собой алюмосиликаты с трехмерной кристаллической структурой.
Недостатком всех цеолитов является их не очень высокая механическая прочность в чистом виде, и поэтому они в качестве промышленного катализатора не используются. Обычно их вводят в диспергированном виде в матрицу катализаторов в количестве 10-20% мас. [7]
Вспомогательные добавки улучшают или придают некоторые специфические физико-химические и механические свойства цеолитсодержащих алюмосиликатных катализаторов (ЦСК) крекинга. ЦСК без вспомогательных добавок не могут полностью удовлетворять всему комплексу требований, предъявляемых к современным промышленным катализаторам крекинга. Так, матрица и активный компонент – цеолит, входящий в состав ЦСК, обладают только кислотной активностью, в то время как для организации интенсивной регенерации закоксованного катализатора требуется наличие металлических центров, катализирующих реакции окислительно-восстановительного типа. Современные и перспективные процессы каталитического крекинга требуют улучшения и оптимизации дополнительно таких свойств ЦСК, как износостойкость, механическая прочность, текучесть, стойкость к отравляющему воздействию металлов сырья и т.д., а также тех свойств, которые обеспечивают экологическую чистоту газовых выбросов в атмосферу. [9]
5. Аппаратурное оформление
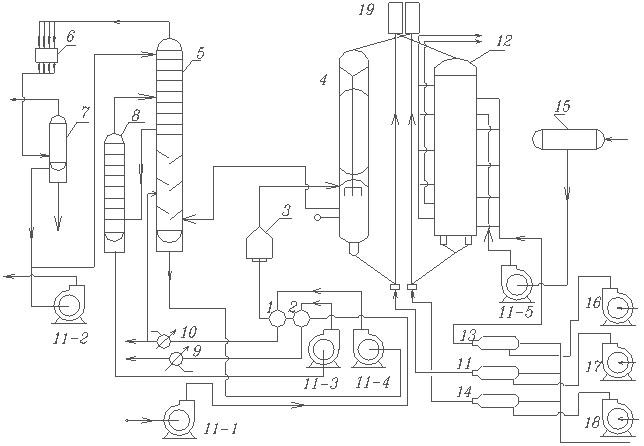
Вакуумный газойль насосом Н – 1 прокачивается через теплообменники легкого 1 и тяжелого 2 газойля и поступает в трубчатую печь 3, где нагреваясь до температуры 460 – 4800С, поступает в реакционную зону реактора 4. В реакторе контактируя с катализатором, поступающим из бункера реактора с температурой 5200С, пары сырья крекируются. Из нижней части реактора через сепарирующее устройство пары продуктов реакции вместе с перегретым водяным паром, подаваемым на отпарку катализатора с температурой 4600С, отводятся в ректификационную колонну 5 под отбойную тарелку. С верха ректификационной колонны жирный газ, пары бензина и водяной пар с температурой 1300С поступают в конденсатор – холодильник 6. Жирный газ, бензин и вода из холодильника 6 с температурой 400С поступают в газосепаратор 7, где происходит разделение жирного газа, бензина и воды. Из газосепаратора жирный газ поступает на разделение. Нестабильный бензин частично подается на орошение колонны 5, остальная часть откачивается на стабилизацию. [4]
С тарелки 16 колонны 5 через отпарную колонну 8 насосом Н-3 легкий газойль откачивается в резервуар товарного парка. Тяжелый газойль с низа колонны 5 частично поступает на орошение низа колонны, а остальная часть откачивается в товарный парк. Отработанный катализатор воздухом, нагретым в топках под давлением 11, транспортируется в регенератор 12, где происходит выжиг кокса за счет подачи вентилятором воздуха, нагретого в топке под давлением. Регенерированный катализатор с температурой 580 – 6000С горячим воздухом транспортируется в бункер реактора, откуда поступает в реакционную зону реактора. Тепло, выделяемое при выжиге кокса с катализатора, снимается водой, подаваемой в охлаждающие змеевики регенератора насосом Н-5. [4]
Реактор.
Реактор представляет собой вертикальный цилиндрический аппарат высотой от 15 до 20 м и диаметром от 3 до 5м в зависимости от мощности установки. Назначение реактора – проведение процесса крекинга нефтяного сырья. В реакторе имеется семь зон, в каждой из которых проводится определенная операция. В первой, или верхней, зоне имеется устройство для распределения поступающего сюда регенерированного катализатора по поперечному сечению аппарата. Горячие пары сырья поступают из змеевиков печи во вторую зону реактора, в пространство между указанными переточными трубами. Это пространство ограничено сверху днищем, а снизу – слоем катализатора. Пары и катализатор проходят рабочую зону сверху вниз прямотоком. В этой зоне протекает процесс каталитического крекинга. Внутрренних устройств третья зона не имеет, за исключением выступающих карманов термопар для замера температуры реакции. Ниже расположена четвертая зона, служащая для отделения паров продуктов реакции от катализатора. Разделительное устройство состоит из нескольких рядов колпачков, равномерно расположенных по высоте большого числа вертикальных труб. Последние имеют под каждым колпачком отверстия для отвода крекинг – продуктов в пятую зону. Катализатор проходит по переточным трубам в шестую зону, где он продувается перегретым водяным паром с целью удаления содержащихся в нем углеводородных паров. В седьмой зоне расположено выравнивающее устройство, которое служит для равномерного опускания слоя катализатора по всему поперечному сечению реактора. Этой части аппарата придается важное значение, так как в случае различной скорости движения отдельных порций катализатора будет происходить неравномерное отложение кокса на катализаторе. [9]
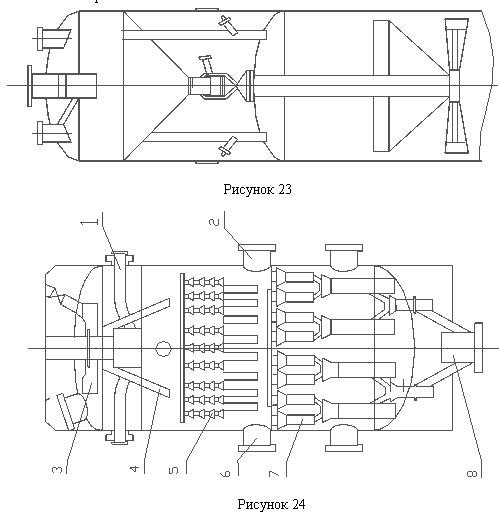
Регенератор.
Регенератор представляет собой вертикальный аппарат квадратного или круглого сечения. Основное назначение аппарата – непрерывный выжиг кокса, отложившегося в реакторе на катализаторе. Во избежание перегрева стального корпуса аппарат имеет внутреннюю футеровку, выполняемую из огнеупорного кирпича. Общая высота регенератора 20 – 30 м. В верхней его части имеется распределительное устройство, состоящее из бункера с патрубками (“паук”). В нижней части регенератора имеется выравнивающее устройство для создания равномерного движения катализатора по всему поперечному сечению аппарата. Кроме того, в регенераторе имеется девять секций, служащих для выжига кокса и охлаждения катализатора. В шести нижних секциях после выжига части кокса и нагрева катализатора производится охлаждение последнего путем передачи через змеевики определенного количества избыточного тепла воде, проходящей внутри трубок змеевиков. [9]
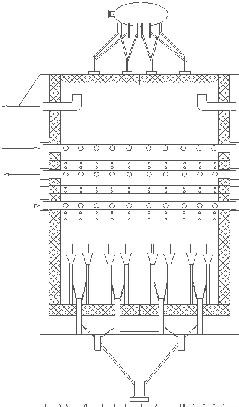
В каждую секцию регенератора из двух вертикальных воздуховодов поступает горячий воздух, который вводится в центральные коллекторы, имеющие по 28 зубчатых коробов каждый. Из каждой секции регенератора по гладким коробам отводятся дымовые газы. Количество охлаждающих змеевиков в аппарате (выполненных из цельносварных труб диаметром 60 мм из стали 1Х18Н9), число рядов, количество труб уточняется на месте в зависимости от качества сырья и предполагаемой коксовой нагрузки.
Длительность регенерации от 60 до 80 мин. Рабочие условия в регенераторе температура от 480 до 7000С, давление 800 мм вод. ст.
Cистема пневмотранспорта.
Подъем отработанного и регенерированного катализатора производится смесью воздуха и дымовых газов. Способ передвижения сыпучих материалов в виде взвеси в газовоздушном потоке носит название пневмотранспорта. Размеры и конструкция системы пневмотранспорта имеют решающее значение на величину кратности циркуляции катализатора.
Система пневмотранспорта включает: 1) воздуховоды; 2) загрузочные устройства – дозеры; 3) стволы пневмоподъемников; 4) сепараторы с циклонами; 5) бункер – подогреватель; 6) катализаторопроводы; 7) устройство для удаления катализаторной мелочи; 8) топки под давлением для нагрева воздуха; 9) воздуходувки.
Смесь дымовых газов и воздуха поступает по воздуховодам большого диаметра (0, 5-1 м), изготовленным из углеродистой стали, к месту потребления. Равномерное регулирование подачи катализатора в реактор и регенератор достигается загрузочными устройствами – дозерами (рис. 26), расположенными внизу стволов пневмоподъемников. Каждый дозер состоит из верхней, средней и нижней частей, переходного конуса 1 и чугунной отливки – трубки 2 переменного сечения. Для регулирования количества подаваемого катализатора в верхней части дозера установлена регулирующая обечайка 3, управление которой осуществляется посредством наружной системы рычагов. Для равномерной подачи воздуха в ствол в средней части дозера имеется выравниватель 4 потока воздуха, состоящий из двух концентрически расположенных цилиндров и конусной наставки 5 на внутренний цилиндр. Катализатор поступает в дозер через штуцеры, расположенные в верхней части аппарата. Вводимый под днище верхней части воздух, пройдя выравниватель 4 потока, подхватывает ссыпающийся через кольцевой зазор катализатор и подает его по стволу пневмоподъемника в верхний бункер. [8]
Циклонный сепаратор.
Сепаратор с циклоном размещен над стволом соответствующего пневмоподъемника и предназначен для отделения газа от катализатора, изменения направления движения катализатора и создания устойчивого уровня катализатора над реактором и регенератором.
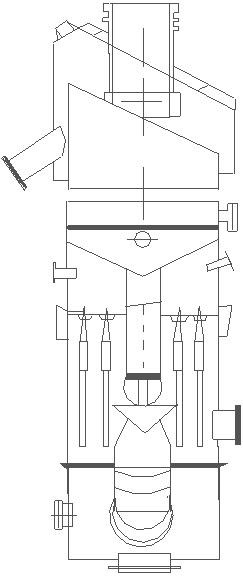
Катализатор, поступающий из пневмоподъемника 3 в нижнюю часть аппарата, за счет резкого снижения скорости отделяется от дымовых газов и пыли и по наклонной трубке 4 ссыпается из сепаратора в бункер. Пыль собирается в приемнике 5, а дымовые газы отводятся в атмосферу по патрубку 2. Мультициклоны 1, расположенные вверху каждого сепаратора, служат для отделения катализаторной мелочи и пыли от дымовых газов. [9]
Заключение
Путем каталитического крекинга получают:
Углеводородные газы каталитического крекинга содержат не менее 75—80 % смеси пропан-пропиленов, бутан-бутиленов и пентан-амиленов. Содержание изомерных соединений достигает 25—40 %, Это делает газы каталитического крекинга ценным сырьем для нефтехимических процессов.
Бензин имеет плотность 0,72—0,77, октановое число по исследовательскому методу от 87 до 91. По химическому составу бензин каталитического крекинга отличается от прямогонных бензинов и бензинов термических процессов. В нем содержится 8—15 % непредельных углеводородов и 20—30 % аренов. Непредельные углеводороды и арены не менее чем на две трети состоят из углеводородов изомерного строения.
Лёгкий газойль (фракция 195—350°С) имеет плотность 0,89-0,94 и состоит на 40—80 % из аренов. Цетановое число, колеблется от 45 до 24. Легкий газойль с высоким цетановым числом используется как компонент дизельного топлива, с низким цетановым числом — как разбавитель мазута. И бензин, и легкий газойль, полученные из сернистого сырья, нуждаются в очистке серы.
Тяжелый газойль (фракции выше 350 °С)—остаточный жидкий продукт каталитического крекинга — используется как компонент топочного мазута или в качестве сырья установок коксования. Содержание серы в нем выше, чем в исходном сырье.
Библиографический список
Гусейнова А. Д. Достижения в развитии процесса каталитического крекинга в Азербайджане / А. Д. Гусейнова, Х. Ю. Исмаилова, Э. А. Касумзаде // Химия и технология топлив и масел. - 2011. - № 1. - С. 13-15 .
Глаголева О.Ф. «Технология переработки нефти Часть1 Первичная переработка нефти» - 2002. - 325 с. .
Патент ФРГ N 3410731, кл. B 01 D 53/34, 1985.
Патент ФРГ N 3444469, кл. C 01 L 10/00, 1986.
С.М. Ткачев, С.И. Хорошко, А.Ф. Корж, С.В. Покровская, А.А. Ермак Каталитический крекинг миллисеконд (MSCC), Новополоцк, 2002. - 161 с. .
Капустин В.М., Гуреев А.А. Технология переработки нефти. В 2 ч. Часть вторая. Деструктивные процессы. - М.: КолосС, 2007. - 334 с. .
Бондаренко Б.И., Никулин Д.Д., Суханов В.П. Каталитический крекинг. М.: Государственное научно-техническое издательство нефтяной и горно-топливной литературы, 1956. - 209 с. .
Патент ФРГ N 3409014, кл. C 01 L 10/00, 1985.
Патент ФРГ N 3325570, кл. C 01 L 10/00, 1985.
Хаджиев С.Н. Крекинг нефтяных фракций на цеолитсодержащих катализаторах. - М.: Химия, 1982. - 280 с. .
Ахметов С.А. Технология глубокой переработки нефти и газа: Учебное пособие для вузов. Уфа: Гилем, 2002. - 672 с. .
Войцеховский Б.В., Корма А. Каталитический крекинг. Катализаторы, химия, кинетика. Пер. с англ./ Под ред. Н.С. Печуро. - М.: Химия, 1990.-152 с. .
Мухленов И.П., Добкина Е.И., Дерюжкина В.И., Сороко В.Е., под ред. проф. Мухленова И.П. Технология катализаторов, 3-е изд., перераб. - Л.: Химия, 1989 - 272 с.,