Курсовая Газосепаратор с промывочной секцией. Введение Общие сведения по району
![]()
|
120 г/м3. |
Компоненты | Молекулярная масса, кг/моль | % мольные |
N2 | 28 | 0,68 |
СО2 | 44 | 0,3 |
СН4 | 16 | 89,64 |
С2Н6 | 30 | 4,54 |
С3Н8 | 44 | 1,99 |
i-С4Н10 | 58 | 0,48 |
n-С4Н10 | 58 | 0,47 |
С5+ | 115 | 1,9 |
В качестве ингибитора гидратообразования принят метанол (ГОСТ 2222-78).
Физико-химическая характеристика :
Химическая формула - СНзОН
Молекулярный вес - 32,04
Плотность при 20°С - 0,79
Температура кипения, °С - 64,7
Температура замерзания, °С - минус 97,1
Температура плавления, °С - минус 93,9
Пластовый газ с давлением до 11 МПа и температурой 15-30°С от кустов скважин поступает на узлы входа шлейфов. Схема узлов входа шлейфов обеспечивает продувку шлейфов на ГФУ и вывод на режим, снижение давления газа до требуемого на входе в УКПГ, защиту от превышения давления.
С узлов входа шлейфов сырой пластовый газ по 2 коллекторам с давлением до 10,0 МПа и температурой 15-25°С поступает в сепараторы С-1 пункта сепарации I очереди.
Пункт сепарации пластового газа предназначен для отделения газа от конденсата, пластовой или метанольной воды и механических примесей.
Сырой пластовый газ от ППА по коллекторам с давлением до 10,0 МПа и температурой 15-25°С поступает в сепараторы С-1/1-3, в которых происходит отделение от газа конденсата, пластовой воды и механических примесей.
Из сепараторов С-1 сырой газ, частично освобожденный от конденсата, пластовой воды и механических примесей, поступает на установку подготовки газа и извлечения конденсата в абсорберы А-1/1-3.
Конденсат с пластовой водой из сепараторов С-1/1-3 поступает на установку подготовки газа и извлечения конденсата в разделители Р-1/1-4.
В продувочном сепараторе С-2 дегазируются поступившие из пробкоуловителя конденсат, пластовая вода, которые из сепаратора С-2 поступают в трубопровод подачи конденсата из сепараторов С-1/1-3 в разделители Р-1/1-4.
Газ из сепаратора С-2 поступает в трубопровод подачи сырого газа из сепараторов С-1/1-3 в абсорберы А-1/1-3.
Для сокращения потерь метанола схемой предусматривается подача части водометанольного раствора (ВМР), отбираемого с "полуглухой" тарелки абсорбера А-1/1-3, в разделители Р-2 для разбавления водометанольной фазы, что снижает растворимость метанола в углеводородном конденсате. В низкотемпературных абсорберах А-2/1-3, состоящих из кубовой, абсорбционной и сепарационной секций производится извлечение углеводородов абсорбентом — охлажденным конденсатом, подаваемым из разделителей Р-1/1-4.
Для охлаждения газа применяются воздушные холодильники ВХ-1/1-8, турбодетандерные агрегаты БТД-1/1-6, работающие по схеме "компрессор-турбина". Для рекуперации холода газовых и конденсатных потоков используются кожухотрубчатые теплообменники Т-1/1-3 (газ-газ), Т-2/1-6 (газ-конденсат) и Т-3/1-6 (конденсат-конденсат). Теплообменники Т-1/1-3 обвязаны параллельно по трубному и межтрубному пространству. Теплообменники Т-2/1-6 и Т-3/1-6 смонтированы попарно в 3-й группы теплообменников. Теплообменники Т-2/1-6 и Т-3/1-6 по межтрубному пространству обвязаны последовательно - параллельно.
Для предотвращения гидратообразования производится подача метанола через панели ИНГ-2 и систему трубопроводов индивидуальной подачи в следующие точки :
- на вход газа в турбины турбодетандерных агрегатов БТД-1/1-6;
- на вход газа в воздушные холодильники ВХ-1/1-8;
- на вход газа в трубное пространство теплообменников Т-1/1-3;
- на вход газа в трубное пространство теплообменников Т-2/1-6;
- на вход конденсата в трубное пространство теплообменников Т-3/1-6.
В низкотемпературных сепараторах С-3/1-3 отделяется конденсат и ВМР, выделившиеся при охлаждении газа в воздушных холодильниках ВХ-1/1-8 и теплообменниках Т-1/1-3.
В разделителях Р-1/1-4 разделяются конденсат и метанольная вода, выделившейся в сепараторах С-1/1-3 и сепарационной секции абсорберов А-1/1-3.
Сырой газ, с давлением до 10,0 МПа и температурой 15-25°С, из пункта сепарации пластового газа по коллектору через входные пневмокраны Г-201/1-3 поступает в абсорберы А-1/1-3, в которых последовательно проходят секции :
сепарационную, где происходит отделение газа от конденсата и пластовой воды, которые через клапан-регулятор уровня поз.КРУ-2, дроссельную шайбу поступают в разделители Р-1/1-4;
отдувочную, где происходит отдувка газом метанола из ВМР с концентрацией 80-85% масс., подаваемого на верхнюю тарелку секции насосами И-10/3-13 из емкости Е-4 установки регенерации метанола;
фильтрующую, где капельный ВМР, выносимый потоком газа, коагулируется на сетке фильтра, стекает в коллектор насыщенного ВМР и поступает в разделители Р-3/1-2.
С полуглухой тарелки отдувочной секции, ВМР с концентрацией метанола 40-65% масс., поступает в разделители насыщенного ВМР Р-3/1-2 установки регенерации метанола и далее в разделители II ступени Р-2.
Газ из абсорберов А-1/1-3 поступает по коллектору на компрессоры турбодетандерных агрегатов БТДА-1/1-6.
Газ после компрессоров БТДА-1/1-6 поступает в воздушные холодильники ВХ-1/1-8, где охлаждается до температуры 4-18°С.
В холодный период года при давлении газа на входе в С-1 >8,7 МПа достижение температуры НТА минус 29-30°С возможно без применения турбодетандерных агрегатов БТДА-1/1-6 за счет дроссель-эффекта, получаемого на клапане-регуляторе давления КРД-2, при этом газ проходит по байпасам компрессора и турбины БТДА.
Недостатком технологической схемы является то, что входные и выходные коллекторы АВО газа изготовлены из нехладостойкой стали. Для предотвращения разрушения коллекторов при температурах ниже минус 20°С предусмотрен электрообогрев коллекторов, осуществляемый греющим кабелем типа КМЖ, который обеспечивает плюсовую температуру стенок коллекторов и патрубков при температуре окружающего воздуха до минус 54°С.
Из воздушных холодильников ВХ-1/1-8 газ поступает в трубное пространство обвязанных параллельно теплообменников Т-1/1-3 (газ-газ) и Т-2/1-6 (газ-конденсат), при этом количество газа, поступающего в Т-2/1-6 регулируется клапаном-регулятором поз.КРТ-2 по температуре конденсата, направляемого в выветриватель В-2 (в насосную конденсата).
В теплообменниках газ охлаждается поступающими в межтрубное пространство потоками :
газа в Т-1 /1 -3 - из абсорберов А-2/1 -3 с температурой минус 25-30°С;
конденсата в Т-2/1-6 — из теплообменников Т-3 или разделителей Р-2 с температурой минус 15-11°С.
Из теплообменников Т-1/1-3 и Т-2/1-6 охлажденный газ под давлением 8,5-10,5 МПа, с температурой 4-+15°С поступает в низкотемпературные сепараторы С-3/1-3, где от газа отделяется жидкая фаза, которая поступает в трубопровод подачи конденсата в выветриватель В-2.
Из сепараторов С-3/1-3 большая часть газа (80%) направляется в турбины ТДА-1/1-6, где за счет расширения до давления 5,5-6,4 МПа, охлаждается до температуры минус 23-28°С, и далее - в абсорберы извлечения тяжелых углеводородов А-2/1-3.
Остальной газ (20%) поступает в качестве активного в эжекторы ЭГ-1/1-3. Пассивным являются газы выветривания из разделителей Р-2, выветривателя В-2 и емкостей Е-101.
В зимний период при работе I очереди по дроссельной схеме, а II - с включением ТДА, количество активного газа не регламентируется и поэтому эжекторы I очереди могут принять также газы выветривания из разделителей Р-2р II очереди, обеспечивая более устойчивый режим работы ТДА II очереди.
Смесь газов с давлением 5,5—6,4 МПа направляется в общий коллектор входа в абсорберы А-2/1-3.
Остаток потока газа после С-3/1-3, не используемый в эжекторах, дросселируется, проходя клапаны-регуляторы КРД-2 и также поступает в абсорберы А-2/1-3.
Генпроектировщиком Ямбурга - институтом «Южниигипрогаз» проведение процесса низкотемпературной абсорбции разрешено при температуре не ниже минус 30°С.
В абсорберах извлечения тяжелых углеводородов А-2/1-3 газ последовательно проходит секции:
- абсорбционную, в которую поступает на нижнюю тарелку. В абсорбционной секции происходит извлечение (абсорбция) из газа углеводородов С3+ охлажденным конденсатом из разделителей Р-1/1-4, подаваемым на орошение на верхнюю тарелку;
- сепарационную, где происходит отделение газа от капельного конденсата, выносимого потоком газа.
При неработающих БТДА-1/1-6 газ из сепараторов С-3/1-3 поступает в качестве активного газа в эжекторы ЭГ-1/1-3, смонтированные параллельно, эжектируя газы выветривания из выветривателя В-2 и разделителей Р-2/1-3. Производительность эжекторов определяется применением соответствующих вставок-сопел. Из эжекторов ЭГ-1/1-3 смесь газов поступает в трубопровод подачи газа в абсорберы А-2/1-3, после клапана-регулятора давления КРД-2.
Схемой предусмотрена подача активного газа на эжекторы ЭГ-1/1-3 после абсорберов А-1/1-3 при возникновении избытка холода в зимний период.
Из абсорберов А-2/1-3 осушенный газ под давлением до 6,0 МПа с температурой минус 25-30°С поступает в межтрубное пространство теплообменника Т-1/1-3.
Из межтрубного пространства теплообменников Т-1/1-3 газ с температурой минус 2-5°С поступает на узел хозрасчетного замера, состоящий из трех параллельных ниток с замерными диафрагмами.
Из замерного узла товарный газ по коллектору Ду 1000 направляется в межпромысловый коллектор.
В разделителях Р-1/1-4 происходит разделение конденсата от пластовой воды и метанола и дегазация жидкой фазы. Газ из разделителей Р-1/1-4 поступает в кубовую секцию абсорберов А-2/1-3.
Водометанольный раствор из разделителей Р-1/1-4 через клапан-отсекатель поз. КРУ-4 поступает на установку регенерации метанола.
Конденсат из разделителей Р-1/1-4 через клапан-регулятор уровня КРУ-5 направляется в трубное пространство теплообменников Т-3/1-6, где охлаждается до температуры минус 22-25°С конденсатом, поступающим в межтрубное пространство из кубовой части абсорберов А-2/1-3, и направляется на орошение верхней тарелки абсорбционной секции абсорберов А-2/1-3.
В абсорберах А-2/1-3 конденсат с полуглухих тарелок абсорбционной и сепарационной секций поступает в кубовую секцию. Из кубовой секции абсорберов А-2/1,3 конденсат подается в межтрубное пространство теплообменников Т-3/1-6 (конденсат-конденсат), а затем Т-2/1-6 (газ-конденсат), где газом, подаваемым в трубное пространство, регулируется температура конденсата, поступающего из Т-2 в выветриватель В-2.
Особенностью обвязки вывода конденсата из кубовой секции абсорбера А-2/2 является то, что клапан-регулятор уровня КРУ-6 установлен на трубопроводе после теплообменников Т-2/1-6, Т-3/1-6.
После теплообменников Т-2/1-6, Т-3/1-6конденсат с температурой 2-7°С поступает в выветриватель В-2. Для снижения потерь метанола с углеводородным конденсатом после монтажа дополнительных трубопроводов конденсат после теплообменников Т-3 подается на разгазирование в выветриватель В-2, разделители Р -2 и емкости Е-101, а затем насосами Н-20 возвращается на нагрев в теплообменники Т-2 и далее – на хозрасчетный замер и в магистральный конденсатопровод.
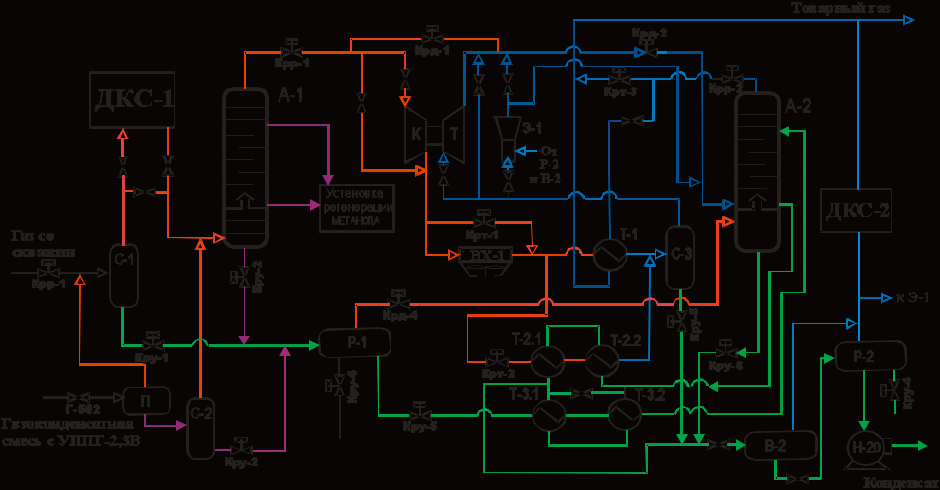
Рисунок 4.3 – Принципиальная схема технологической линии УКПГ-1В Ямбургского месторождения
5. Принцип работы аппарата очистки газа и его конструкция
Сепаратор с промывочной секций (рисунок 5.1) предназначен для выделения основной массы жидкости из газового потока.
Сепаратор представляет собой вертикальный цилиндрический аппарат внутренним диаметром 1800 мм с узлом предварительной очистки газа (у штуцера входа) и тремя секциями:
- входной с сепарационными элементами типа ГП 353;
- выходной сепарационной с элементами типа ГПР 667;
- секции промывки, состоящей из 2-х массообменных тарелок с центробежными элементами типа ГПР 340.
Газ входит в среднюю часть сепаратора и ударяется в отбойное ребро. При этом резко изменяется направление и скорость газового потока.
За счет изменения скорости газа происходит частичное выделение взвешенных в нем капель жидкости, которые стекают вниз по поверхности ребер. Для более полного выделения капель жидкости из газового потока служит жалюзийная насадка. Проходя через жалюзи насадки, газовый поток неоднократно изменяет свое направление, что приводит к выделению капель жидкости. Стекая по насадке, капли укрупняются, образуют пленку и смачивают насадку. Затем жидкость попадает в сливные трубки, по которым стекает в сливные карманы, служащие гидрозатворами.
Из сливных карманов жидкость направляется в кубовую часть сепаратора с подогревом, где происходит выделение некоторого количества газа из отделившейся в сепараторе жидкости. Уровень жидкости в первичном сепараторе поддерживается с помощью регулятора непрерывного действия, также предусмотрена сигнализация максимум и минимум уровней, давление контролируется техническим манометром. Для интенсификации процесса отделения капель жидкости от газа на входе в сепаратор установлено завихрительное устройство.
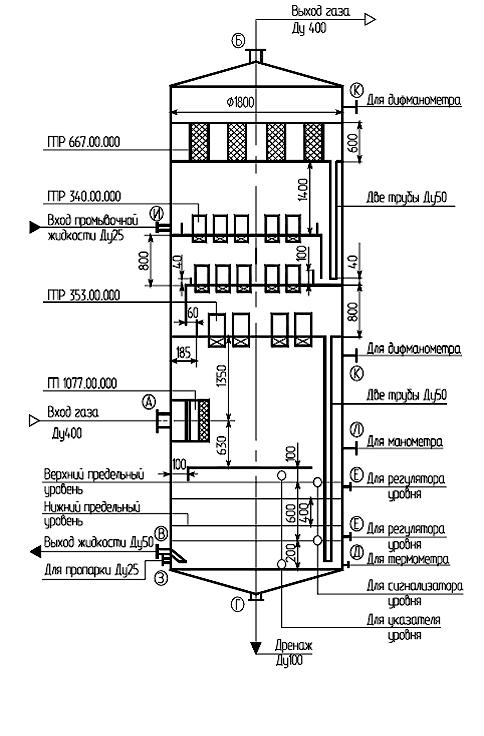
Рисунок 5.1– Эскиз сепаратора С-201 с промывочной секцией (ГП 1181.04.000-01)
На выходе из завихрителя поток газа приобретает вращательное движение, капельки жидкости, имеющие большую, чем частички газа массу, отбрасываются к периферии потока, укрупняются и под действием силы тяжести оседают вниз. Жидкость собирается в нижней части аппарата. Уровень жидкости в промежуточном сепараторе поддерживается автоматически регулятором непрерывного действия, фиксируются минимальная и максимальная величины уровней и сигнализируются на дисплее. Температура сепараторе измеряется термометром сопротивления, давление – техническим манометром.
6. Технологический расчет сепаратора с промывочной секцией С-201 ( ГП 1181.04.01.000 РР2)
Задачей технологического расчета является определение геометри-ческих размеров аппарата и его гидравлического сопротивления.
Таблица 6.1 Исходные данные для расчета
Наименование показателя, обозначение, единица измерения | Значение |
Производительность по газу Qг, м3/ч при условии: P=0,1013 МПа; t=0°C | 416670 |
Давление рабочее Рр, МПа | от 7,5 до 3,0 |
Давление расчетное Ррасч, МПа | 8,25 |
Температура рабочая T, K: | 293 |
Производительность по промывочной жидкости Qж, м3/ч | 10 |
Начальное содержание жидкости в газе, г/см3 (см3/см3): | |
-воды, lв | 1,06 |
-конденсата, lк | 0,007 |
-метанола, lм | 0,3 |
Плотность газа ρ0, кг/м3 | 0.7259 |
Плотность пластовой воды ρв, кг/м3 | 1010 |
Наименование промывочной жидкости | конденсационная вода |
Плотность промывочной жидкости ρж, кг/м3 | 1000 |
Поверхностное натяжение промывочной жидкости при P=0,1013 МПа ![]() | 74,9⸱10-3 |
Поверхностное натяжение конденсата в рабочих условиях ![]() | 13⸱10-3 |
Допустимое гидравлическое сопротивление [ ![]() | 0,03 |
Массовая концентрация мехпримесей на входе, мг/м3 | 10 |
6.1 Расчет входной сепарационной секции (элементы по ГПР 353.00.000)
Объемная производительность по газу в рабочих условиях определяется по формуле

где





Коэффициент сверхсжимаемости газа в рабочих условиях Zp определяется (используя псевдоприведенные давления π и температуру τ ) по графикам[1, c. 387] или по уравнению, справедливому для тощих газов:
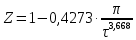
или по уравнению

Плотность газа в рабочих условиях (ρр), кг/м3, определяется по формуле
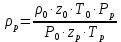
где ρ0 – плотность в нормальных условиях, кг/м3;
Определяем критическую скорость газа (

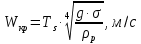
где Ts=f(p) – коэффициент структурных изменений газожидкостного потока; Ts=8,5;
g – ускорение свободного падения, м2/с;
σ – поверхностное натяжение конденсата в рабочих условиях, н/м, σ=13⸱10-3 н/м;
ρр – плотность газа в рабочих условиях.
Расчетная площадь прямоточно-центробежных элементов определяется из выражения

Определяем расчетное количество прямоточно-центробежных элементов np:

где fc – площадь прямоточно-центробежного элемента

где dc – элемента, м, dc=0,1 м.
Расчетный диаметр сепаратора определяется по формуле

где ε – коэффициент использования живого сечения полотна тарелки, ε=0,36.
6.2 Расчет секции промывки ( элемента по ГПР 340.00.000)
Определяем допустимую скорость в контактно-сепарационном элементе

где Фmax – фактор скорости газа в контактно-сепарационном элементе, Фmax =24,3.
Расчетное число контактно-сепарационных элементов n k-c определяется из выражения
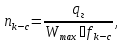
где fk-s – площадь одного элемента

где dk-c – диаметр элемента, м. dk-c=0,06 м.
Рабочая площадь контактно-сепарационной тарелки Fраб равна

где fраб – рабочая площадь, занимаемая одним элементом:

где dэл.н – диаметр элемента наружный, м;
dэд.н = 0,062 м;
сэл – расстояние между элементами по наружному диаметру, м;
сэл = 0,038 м.
Площадь сечения перелива
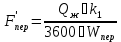
где Qж – производительность по промывочной жидкости, м3/ч;
k1 – коэффициент запаса на площадь переливных перегородок;
k1 = 1,05;
Wпер=0,1 м/с – допустимая скорость в переливе.
Площадь свободного сечения аппарата без учета площади опорных балок и опорных колец Fk″ равна
Fk″=Fраб + 2F′пер, м2. (6.16)
Диаметр аппарата D” определяется из выражения
D″=1,13

Количество опорных балок nб определяется из выражения
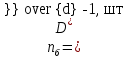
Определяем площадь опорных балок Fоп.б

где b – ширина полотна тарелки, требуемая под опорную балку, м.
b=0,06 м
Площадь сечения аппарата с учетом площади опорных балок F’k определяется из выражения

Определяем диаметр аппарата с учетом площади опорных балок

Центральный угол сегментного перелива α1’ определяется по формуле
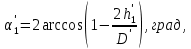
где h′1 –величина стрелки сегментного перелива, м.
h′1=0,1 м
Площадь сегментного перелива F’ определяется по формуле
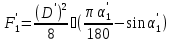
Определяем величину стрелки приемного кармана h’2
h′2=h′1 + 0,06 (6.24)
Центральный угол сегмента приемного кармана α′2 определяется по формуле
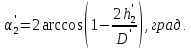
Площадь сегмента кармана F’2 определяется по формуле
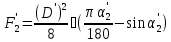
Расчетная площадь сечения аппарата Fp равна
Fp=Fраб+Fоп.б+F′1+F′2, м2. (6.27)
Определяем расчетный диаметр аппарата Dp

На основании анализа расчета входной сепарационной секции (Dp) и секции промывки (Dp) проверяют, подходит ли стандартный диаметр аппарата (D=1,8 м). Если Dp
- на входной сепарационной тарелке установлены элементы по ГПР 353.00.000 в количестве 12 шт.;
- на тарелке в секции промывки установлены элементы по ГПР 340.00.000 в количестве 190 шт.;
- на входной сепарационной тарелке установлены овально-цилиндрические барабаны по ГПР 657.00.000 в количестве 15 шт.
6.3 Расчет выходной сепарационной секции (овально-цилиндрические барабаны по ГПР 657.00.000)
Критическая скорость газа в барабанах Wкр определяется по формуле

где Се – коэффициент, характеризующий начальное содержание жидкости:
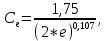
где е – унос жидкости из секции промывки, см3/м3:
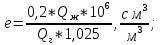
Cε = f(ε) – коэффициент использования живого сечения, Cε = 0,93

где Fd – площадь сечения аппарата, м²:

σж – поверхностное натяжение жидкости в рабочих условиях, (мН/м)
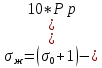
где σ0 – поверхностное натяжение жидкости в нормальных условиях, мН/м
Суммарную площадь верхних овальных оснований барабанов ΣFв.ос определяем из выражения

где

nб=15 шт;

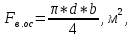
где d – ширина овального основания, м; d = 0.21 м;
b – длина овального основания, м; b = 0,44 м.
Ts=f(n), где

Необходимая рабочая поверхность барабанов Fн определяется из выражения следующего вида

Фактическая рабочая поверхность барабанов, определяемая по средней линии с учетом толщины сетки, определяется из выражения

где




Необходимое условие

6.4 Расчет переливного устройства секции промывки
Центральный угол сегментного перелива
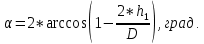
Действительная площадь перелива Fпер определяется по формуле
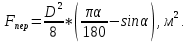

Действительная величина стрелки приемного кармана


Длина хорды сегментного перелива
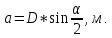
6.5 Расчет гидравлического сопротивления контактных тарелок
Перепад давления на тарелке

(6.45)
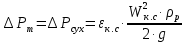

(6.46)
Действительная скорость газа в элементе

где Fк.с – площадь контактно-сепарационных элементов, м2

(6.47)

где fк.с – площадь контактно-сепарационного элемента, м2;
nк.с – количество контактно-сепарационных элементов, шт.

(6.48)
Нагрузка по жидкости на единицу длины слива определяются из следующего выражения

(6.49)



(6.50)
Подбор жидкости над сливной планкой


(6.51)
Высота слоя светлой жидкости на тарелке

где hп – высота сливной планки, мм,
hп =40 мм.

(6.52)
Объемный расход жидкости, проходящей через один элемент:


(6.53)
Условие нормальной работы тарелки

6.6 Проверка расстояния между контактными тарелками

(6.54)
Высота слоя светлой жидкости в переливе hж определяется по формуле

где hз.п – высота запорной планки, мм;
hз.п =100мм.

(6.55)

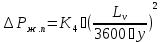
где y – наиболее узкое сечение в переливе, м;
y= 0, 04 м;
K4=250 м.

(6.56)
ρж′ – плотность жидкости по отношению к плотности, мм.вод. ст.,


(6.57)
Высота вспененной жидкости в переливе
Hп=


(6.58)
где ρп’ – плотность вспененной жидкости по отношению к плотности исходной жидкости;


(6.59)
Условие нормальной работы перелива
Hп