|
ТКМ шпоры. 1. Исходные материалы для металлургии руда, флюсы, огнеупоры, топливо пути повышения температуры горения металлургического топлива. Дайте определения и примеры химических формул
15п Типовая формовочная смесь содержит: , ' - 90% кварцевого песка:
- 5-10% глины;
- - до 5% компонентов, улучшающих свойства смесей;
- 3-6% воды сверх 100Х сухой смеси.
Кварцевый песок SiO2 - огнеупорная основа смеси. Он состоит из зерен размером 0.06-р.8 мм.
Глина является связующим материалом песчаных смесей. Свои связующие свойства глина проявляет только в присутствии воды.
К добавкам. позволяющим регулировать свойства смеси, относятся: молотый уголь, мазут, асбестовая крошка, опилки, битум и ряд других материалов.
Типовая стержневая смесь содержит:
- 94-98% кварцевого песка;
- 2-6% связующих материалов на основе синтетических смол и других добавок.
Литниковая система-это система каналов, через которые расплавленный металл подводят в полость формы. Л.с должна обеспечивать заполнение литейной формы с необходимой скоростью, задержания шлака и др. неметаллических включений, выход паров и газов из полости формы, непрерывную подачу расплавленного металла к затвердевающей отливке.
К недостаткам способа относятся низкая точность размеров отливок и большая шероховатость поверхности, что приводит к увеличению объема механической обработки. Для процесса характерна оптимальная трудоемкость получения
| 16 Литьё в оболочковые формы,способ получения фасонных отливок из металлических сплавов в формах, состоящих из смеси песчаных зёрен (обычно кварцевых) и синтетического порошка (термореактивная смола 4-7%).Смесь насыпают на металлическую модель, нагретую до 300°С, выдерживают в течение нескольких десятков сек до образования тонкого упрочнённого слоя, избыток смеси удаляют. Термореактивная смола в пограничном слое переходит в жидкое состояние, склеивает песчинки с образованием песчано-смоляной оболочки толщиной 5-20 мм. Бункер возвращают в исходное положение, модельная плита снимается и нагревается в печи при t 300-350 в течение 1-2 мин, термореактивная смола переходит в твердое состояние. Аналогично изготавливают вторую полуформу. . Готовые оболочковые формы склеивают, предварительно установив в них литейные стержни.
Заливка форм производится в вертикальном или горизонтальном положении.Выбивку отливок проводят на специальных выбивных или вибрационных установках.
Литье в оболочки обеспечивает высокую герметическую точность, точность отпечатка не нарушается(оболочка снимается без расталкивания). Снижается припуск на обработку в 2 раза, снижена шероховатость. Высокая прочность позволяется изготавливать тонкостенные формы, что снижает расход формовочной смеси. Процесс легко автоматизируется .Повышенная производительность труда . Минус- ограничение по массе (50-60 кг).
Изготавливают отливки для автомобилей, тракторов, с\х машин из чугуна, уг сталей, цвет сплавов
17 Ещё один способ литья металлов — по выплавляемой модели — применяется в случаях изготовления деталей высокой точности (например лопатки турбин и т. п.) Получают путем заливки расплавленного ме в формы, изготовленные по выплавляемым моделям многократным погружением в керамическую суспензию с последующими обсыпкой и отверждением.
Разовые выплавляемы модели изгот в пресс-формах, сост из 2 и более легкоплавких комп (парафин, стеарин, жирных кислот). На модельный блок наносят суспензию и производят обсыпку, так наносят от 6 до 10 слоёв. Сушка каждого слоя занимает не менее получаса.Из сформировавшейся оболочки выплавляют модельный состав: в воде, в модельном составе, выжиганием, паром высокого давления. После сушки и вытопки блок прокаливают при температуре примерно 1000 для удаления из оболочковой формы веществ способных к газообразованию. После чего оболочки поступают на заливку. Перед заливкой блоки нагревают в печах до 1000. Нагретый блок устанавливают в печь и разогретый металл заливают в оболочку. Залитый блок охлаждают в термостате или на воздухе. Когда блок полностью охладится его отправляют на выбивку. Ударами молота по литниковой чаше производится отбивка керамики, далее отрезка .Таким образом получаем отливку.
+ Высокая точность , Малая шероховатость .
- Сложность процесса , Высокая себестоимость
В силу большого расхода металла и дороговизны процесса применяют только для ответственных деталей.
Схемы на стр 149(?там нет ничего)
| 18 Литьё металлов в кокиль — более качественный способ. Изготавливается кокиль — разборная форма (чаще всего металлическая), в которую производится литьё. После застывания и охлаждения, кокиль раскрывается и из него извлекается изделие. Затем кокиль можно повторно использовать для отливки такой же детали.
Литьё в кокиль, кокильное литьё, способ получения фасонных отливок в металлических формах — кокилях. В отличие от других способов литья в металлические формы (литьё под давлением, центробежное литьё и др.), при литье в кокиль заполнение формы жидким сплавом и его затвердевание происходят без какого-либо внешнего воздействия на жидкий металл, а лишь под действием силы тяжести. Основные операции и процессы: очистка кокиля от старой облицовки, прогрев его до 200—300°С, покрытие рабочей полости новым слоем облицовки, простановка стержней, закрывание частей кокиля, заливка металла, охлаждение и удаление полученной отливки. Процесс кристаллизации сплава при литье в кокиль ускоряется, что способствует получению отливок с плотным и мелкозернистым строением, а следовательно, с хорошей герметичностью и высокими физико-механическими свойствами. Однако отливки из чугуна из-за образующихся на поверхности карбидов требуют последующего отжига. При многократном использовании кокиль коробится и размеры отливок в направлениях, перпендикулярных плоскости разъёма, увеличиваются.
Разновидность кокильного литья – литье в облицованные кокили. Состоит в том, что модельную плиту с моделью нагревают электрическими или газовыми нагревателями до t 200 . На плиту устанавливают нагретый кокиль. В зазор м\ду кокилем и моделью из пескодувной головки через сопла вдуваются формовочная смесь с термореактивным связующим. Оболочка толщиной 3-5 мм формируется и упрочняется за счет теплоты кокиля и модели. После отверждения оболочки на кокиле модель извлекают. Аналогично изготавливают и вторую половину.
Все операции процесса механизированы и автоматизированы.
+ Сокращается расход формовочной и стержневой смесей. , более высокие плотности ме и мех. Свойства, чем у отливок полученных в песчаные формы. Имеют высокую геом точность размеров и малую шероховатость. Высокая производительность.
- Высокая трудоемкость, ограниченная стойкость, трудность изготовления сложных конфигураций
19 Литье под давлением получают отливки в ме формах, при этом заливку ме в форму и формирование отливки осуществляют под давлением. Изготавливают отливки на машинах литья под давлением с холодной или горячей камерой прессования. При получении отливок на литейных машинах с холодной камерой прессования необходимое количество сплава заливается в камеру прессования вручную или заливочным дозирующим устройством. Сплав из камеры прессования под давлением прессующего поршня через литниковые каналы поступает в оформляющую полость плотно закрытой формы, излишек сплава остаётся в камере прессования в виде пресс-остатка и удаляется. После затвердевания сплава форму открывают, снимают подвижные стержни и отливка выталкивателями удаляется из формы.
+ Массовое и крупносерийное производство, высокая точность размеров и малая шероховатость. Резко сокращается мех обработка, высокая производительность
-Высокая стоимость пресс-форм и оборудования, ограниченность габаритных размеров и массы отливок. Наличие воздушной пористости в массивных частях.
20 Сплав заливают во вращающиеся формы, формирование отливки соущ под действием центробежных сил. Технология центробежного литья обеспечивает целый ряд преимуществ, зачастую недостижимых при других способах, к примеру:Высокая износостойкость. Высокая плотность металла. Отсутствие раковин. В продукции центробежного литья отсутствуют неметаллические включения и шлак.
Центробежным литьем отливки изготавливают в металлических, песчаных, оболочковых и по выплавляемым моделям на центробежных машинах. Изложницы изготовляют из чугуна.
Получение внутренних полостей трубных заготовок без применения стержней ; большая экономия сплава за счет отсутствия литниковой системы; возможность получения двухслойной заготовки.
| 21
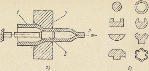
Пресование
При прессовании металл выдавливается из замкнутой полости через отверстие, соответствующее сечению прессуемого профиля Этим процессом изготовляют не только сплошные профили, но и полые.
Исходной заготовкой при прессовании служит слиток или прокат.
При прессовании металл подвергается всестороннему неравномерному сжатию и поэтому имеет весьма высокую пластичность.
Прессованием можно получать профили сложных форм, которые не могут быть получены другими видами обработки металлов давлением (в частности прокаткой). Точность прессованных профилей выше, чем прокатанных.
К недостаткам прессования следует отнести большие отходы металла: весь металл не может быть выдавлен из контейнера и в нем остается так называемый пресс-остаток, который после окончания прессования отрезается от полученного профиля.
ВОЛОЧЕНИЕ
При волочении заготовку протягивают через постепенно сужающееся отверстие в инструменте, называемом волокой. Волочение, как правило, осуществляют в холодном состоянии. Исходными заготовками служат прокатанные или прессованные прутки и трубы из стали, цветных металлов и их сплавов.
При волочении сплошного и полого профилей площадь поперечного сечения заготовки уменьшается, а следовательно, длина (из условия постоянства объема при пластической деформации) увеличивается. Количественно деформацию, так же как и при прокатке, можно характеризовать отношением полученной длины к исходной, т. е. вытяжкой (мю).'Вследствие того что к заготовке при волочении приложено тянущее усилие, в отверстии волоки (очаге деформации) и после выхода из нее металл испытывает растягивающие напряжения. Поэтому величина деформации за один проход ограничена, и вытяжка (мю) = 1,25-1,45.
Волочением обрабатывают различные сорта стали и цветные металлы: медь и ее сплавы, алюминий и его сплавы и др. Сортамент изделий, изготовляемых волочением, очень разнообразен: проволока диаметром 0,002—5 мм и фасонные профили, призматические и фасонные направляющие;сегментные, призматические и фасонные шпонки; шлицевые валики; опорные призмы и ножи и т. д.). Волочением калибруют стальные
трубы диаметрами от капиллярных до 200 мм, стальные прутки диаметром 3—150 мм.
ПРОКАТНОЕ ПРОИЗВОДСТВО I. СУЩНОСТЬ ПРОЦЕССА
Прокатке подвергают до 90 % всей выплавляемой стали и большую часть цветных металлов. При прокатке металл пластически деформируется вращающимися валками. Взаимное расположение валков и заготовки, форма и число валков могут быть различными. Выделяют три основных вида прокатки; продольную, попе-•речную и поперечно-винтовую.
При продольной прокатке заготовка деформируется между двумя валками, вращающимися в разные стороны, и перемешается перпендикулярно к осям валков.
При поперечной прокатке валки вращаясь в одном направлении, придают вращение заготовкеи деформируют ее.При поперечно-винтовой прокатке валки расположены под углом и сообщают заготовке при деформировании вращательное н поступательное движения.
| 22 В зависимости от температурно-скоростных условий деформирования различают холодную и горячую деформацию.
Холодная деформация характеризуется изменением формы зерен, которые вытягиваются в направлении наиболее интенсивного течения металла. При холодной деформации формоизменение сопровождается изменением механических и физико-химических свойств металла. Это явление называют упрочнением (наклепом). Изменение механических свойств состоит в том, что при холодной пластической деформации по мере ее увеличения возрастают характеристики прочности, в то время как характеристики пластичности снижаются. Изменения, внесенные холодной деформацией в структуру и свойства металла, не необратимы. Они могут быть устранены, например, с помощью термической обработки (отжигом). Явление зарождения и роста новых равноосных зерен взамен деформированных, вытянутых, происходящее при определенных температурах, называется рекристаллизацией. При температурах ниже температуры начала рекристаллизации, наблюдается явление, называемое возвратом. При возврате (отдыхе) форма и размеры деформированных, вытянутых зерен не изменяются, но частично снимаются остаточные напряжения. Эти напряжения возникают из-за неоднородного нагрева или охлаждения (при литье и обработке давлением), неоднородности распределения деформаций при пластическом деформировании и т. д. Остаточные напряжения создают системы взаимно уравновешивающихся сил и находятся в заготовке, не нагруженной внешними силами. Снятие остаточных напряжений при возврате почти не изменяет механических свойств металла, но влияет на некоторые его физико-химические свойства. Формоизменение заготовки при температуре выше температуры рекристаллизации сопровождается одновременным протеканием упрочнения и рекристаллизации.
Горячей деформацией называют деформацию, характеризующуюся таким соотношением скоростей деформирования и рекристаллизации, при котором рекристаллизация успевает произойти во всем объеме заготовки и микроструктура после обработки давлением оказывается равноосной, без следов упрочнения. Чтобы обеспечить условия протекания горячей деформации, приходится с увеличением ее скорости повышать температуру нагрева заготовки (для увеличения скорости рекристаллизации). При горячей деформации сопротивление деформированию примерно в 10 раз меньше, чем при холодной деформации, а отсутствие упрочнения приводит к тому, что сопротивление деформированию (предел текучести) незначительно изменяется в процессе обработки давлением. Этим обстоятельством объясняется в основном то, что горячую обработку применяют для изготовления крупных деталей, так как при этом требуются меньшие усилия деформирования (менее мощное оборудование). При горячей деформации пластичность металла выше, чем при холодной деформации. Поэтому горячую деформацию целесообразно применять при обработке труднодеформируемых, малопластичных металлов и сплавов, а также заготовок из литого металла (слитков). В то же время при горячей деформации окисление заготовки более интенсивно (на поверхности образуется слой окалины), что ухудшает качество поверхности и точность получаемых размеров. Холодная деформация без нагрева заготовки позволяет получать большую точность размеров и лучшее качество поверхности по сравнению с обработкой давлением при достаточно высоких температурах. Отметим, что обработка давлением без специального нагрева заготовки позволяет сократить продолжительность технологического цикла, облегчает использование средств механизации и автоматизации и повышает производительность труда. Влияние холодной деформации на свойства металла можно использовать для получения наилучших эксплуатационных свойств деталей, а управление изменением свойств в требуемом направлении и на желаемую величину может быть достигнуто выбором рационального сочетания холодной и горячей деформации, а также числа и режимов термических обработок в процессе изготовления детали
24 Метал течет туда,где меньше сопротивление....при давлении весь метал перетекает туда, куда проще, потеря составляет лишь 0.2 процента... Подобие....сначала испытывают маленькую деталь, затем на ее основе большую
| 25 ТЕРМИЧЕСКИЙ РЕЖИМ
При нагреве металла с повышением температуры уменьшается его временное сопротивление, а относительное удлинение увеличивается. Таким образом, при деформировании стали, нагретой, например, до температуры 1200 °С, можно достичь большего форме-
изменения при меньшем приложенном усилии, чем при деформировании ненагретой стали. Все металлы и сплавы имеют тенденцию к увеличению пластичности и уменьшению сопротивления деформированию при повышении температуры в случае выполнения ряда требований, предъявляемых к процессу нагрева. Так, каждый металл должен быть нагрет до вполне определенной максимальной температуры. Если нагреть, например, сталь до температуры, близкой к температуре плавления, наступает пережог, выражающийся в появлении хрупкой пленки между зернами металла вследствие окисления их границ. При этом происходит полная потеря пластичности.Ниже температуры пережога находится зона перегрева. Явление перегрева заключается в резком росте размеров зерен. Вследствие того, что крупнозернистой первичной кристаллизации (аусте-иит), как правило, соответствует крупнозернистая вторичная кристаллизация (феррит + перлит или перлит + цементит), механические свойства изделия, полученного обработкой давлением из перегретой заготовки, оказываются низкими.
Максимальную температуру нагрева, т. е. температуру начала горячей обработки давлением, следует назначать такой, чтобы не было пережога и перегрева. В процессе обработки нагретый металл обычно остывает, соприкасаясь с более холодным инструментом и окружающей средой. Заканчивать горячую обработку давлением следует также при вполне определенной температуре, ниже которой пластичность вследствие упрочнения (рекристаллизация не успевает произойти) падает и в изделии возможно образование трещин.
Заготовка должна быть равномерно нагрета по всему объему до требуемой температуры. Разность температур по сечению заготовки приводит к тому, что вследствие теплового расширения между более нагретыми поверхностными слоями металла и менее нагретыми внутренними слоями возникают напряжения.Разность температур по сечеиию увеличивается с повышением скорости нагрева, поэтому существует допустимая скорость нагрега. Наибольшее время требуется для нагрева крупных заготовок из «Высоколегированных сталей из-за их низкой теплопроводности. [ Например, время нагрева слитка массой 40 т из легированной стали составляет более 24 ч.
Однако с увеличением времени нагрева увеличивается окисление • поверхности металла, так как при высоких температурах металл > активнее химически взаимодействует с кислородом воздуха. В ре-Вультате на поверхности, например, стальной заготовки образуется I окалина—слой, состоящий из оксидов железа: Ре^О^, Рел04, РеО. 1 При высоких температурах на поверхности стальной заготовки интенсивно окисляется не только железо, но и углерод: происходит Так называемое обезуглероживание. Толщина обезуглероженного слоя в отдельных случаях достигает 1,5—2 мм. I Для уменьшения окисления заготовки нагревают в нейтральной или восстановительной атмосфере.
2. НАГРЕВАТЕЛЬНЫЕ УСТРОЙСТВА
Устройства, в которых нагревают металл перед обработкой давлением, можно подразделить на нагревательные печи и электронагревательные устройства. В печах теплота к заготовке передается главным образом конвекцией и излучением из окружающего пространства нагревательной камеры, выложенной огнеупорным материалом. Теплоту получают в основном сжиганием газообразного, реже жидкого, топлива (мазута).
• По конструктивным признакам печи разделяют на ряд разновидностей. Например, одним из наиболее распространенных типов являются камерные печи
В электронагревательных устройствах теплота выделяется в самой заготовке либо при пропускании через нее тока большой силы — в контактных устройствах, либо при возбуждении в ней вихревых токов — в индукционных устройствах.Преимущества электронагрева: высокая скорость, значительно превышающая скорость нагрева в печах; почти полное отсутствие окалины; удобство автоматизации, улучшение условий труда. Однако применяют электронагревательные устройства только при необходимости нагрева достаточно большого количества одинаковых заготовок диаметром до 75 мм в контактных и до 200 мм в индукционных устройствах.
| |
|
|