|
ТКМ шпоры. 1. Исходные материалы для металлургии руда, флюсы, огнеупоры, топливо пути повышения температуры горения металлургического топлива. Дайте определения и примеры химических формул
7.Кислородно-конверторный способ получения стали: исходные материалы, технология, технико-экономические показатели. Схема кислородного конвертера. Кислородно-конвертерный процесс - это выплавка стали из жидкого чугуна в конвертере с основной футеровкой и продувкой кислородом через водоохлаждаемую фурму.
Кислородный конвертер - это сосуд грушевидной формы из стального листа, футерованный основным кирпичом. Вместимость конвертера 130—350 т жидкого чугуна. В процессе работы конвертер может поворачиваться на цапфах вокруг горизонтальной оси на 360°С для завалки скрапа, заливки чугуна, слива стали и шлака.
Шихтовыми материалами кислородно-конвертерного процесса являются жидкий передельный чугун, стальной лом (не более 30 %), известь для наведения шлака, железная руда, а также боксит (А12О3), плавиковый шпат (CaF2), которые применяют для разжижения шлака.
Технология плавки. Перед плавкой конвертер наклоняют, через горловину с помощью завалочных машин загружают скрап (рис, 2.4, а), заливают чугун при температуре 1250—1400°С (рис. 2.4, б). После этого конвертер поворачивают в вертикальное рабочее положение (рис. 2.4, в), внутрь его вводят водоохлаждаемую фурму и через нее подают кислород под давлением 0,9-1,4 МПа. Одновременно с началом продувки в конвертер загружают известь, боксит, железную руду. Струи кислорода проникают в металл, вызывают его циркуляцию в конвертере и перемешивание со шлаком. Благодаря интенсивному окислению примесей чугуна при взаимодействии с кислородом в зоне под фурмой развивается температура до 2400°С.
В зоне контакта кислородной струи с чугуном в первую очередь окисляется железо, так как его концентрация во много раз выше, чем примесей. Образующийся оксид железа растворяется в шлаке и металле, обогащая металл кислородом. Кислород, растворенный в металле, окисляет кремний, марганец, углерод в металле, и содержание их понижается. При этом происходит разогрев ванны металла теплотой, выделяющейся при окислении примесей, поддержание его в жидком состоянии.
В кислородном конвертере благодаря присутствию шлаков с большим содержанием СаО и FeO, перемешиванию металла и шлака создаются условия для удаления из металла фосфора по реакции в начале продувки ванны кислородом, когда ее температура еще невысока. В чугунax перерабатываемых в конвертерах, не должно быть более 0,15 % Р. При повышенном (до 0,3 %) содержании фосфора для его удаления необходимо сливать шлак и наводить новый, что снижает производительность конвертера.
Удаление серы из металла в шлак протекает в течение всей плавки по реакциям (7) и (8). Однако высокое содержание в шлаке FeO (до 7-20 %) затрудняет удаление серы из металла. Поэтому для передела в сталь в кислородных конвертерах применяют чугун с содержанием до 0,07 % S.
Подачу кислорода заканчивают, когда содержание углерода в металле соответствует заданному. После этого конвертер поворачивают и выпускают сталь в ковш (рис. 2.4, г).
При выпуске стали из конвертера ее раскисляют в ковше осаждающим методом ферромарганцем, ферросилицием и алюминием; затем из конвертера сливают шлак (рис. 2.4, д).
В кислородных конвертерах выплавляют конструкционные стали с различным содержанием углерода, кипящие и спокойные.
В кислородных конвертерах трудно выплавлять стали, содержащие легкоокисляющиеся легирующие элементы, поэтому в них выплавляют низколегированные (до 2-3 % легирующих элементов) стали. Легирующие элементы вводят в ковш, расплавив их в электропечи, или твердые ферросплавы вводят в ковш перед выпуском в пего стали. Плавка в конвертерах вместимостью 130-300 т заканчивается через 25-50 мин. Кислородно-конвертерный процесс более производительный, чем плавка стали в мартеновских печах.
| 7п
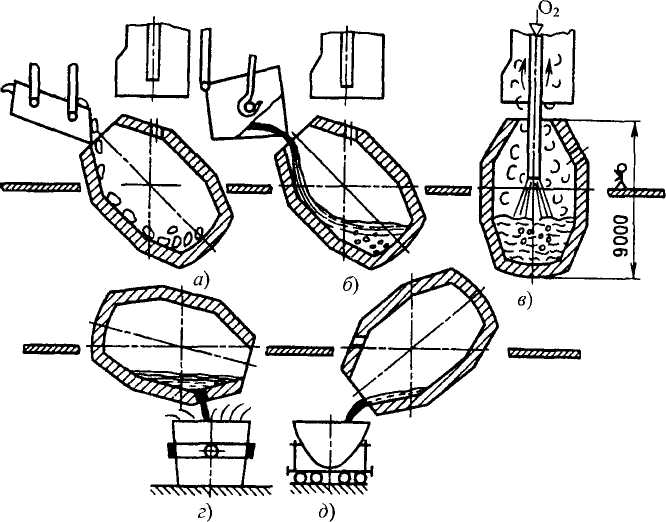
| 8
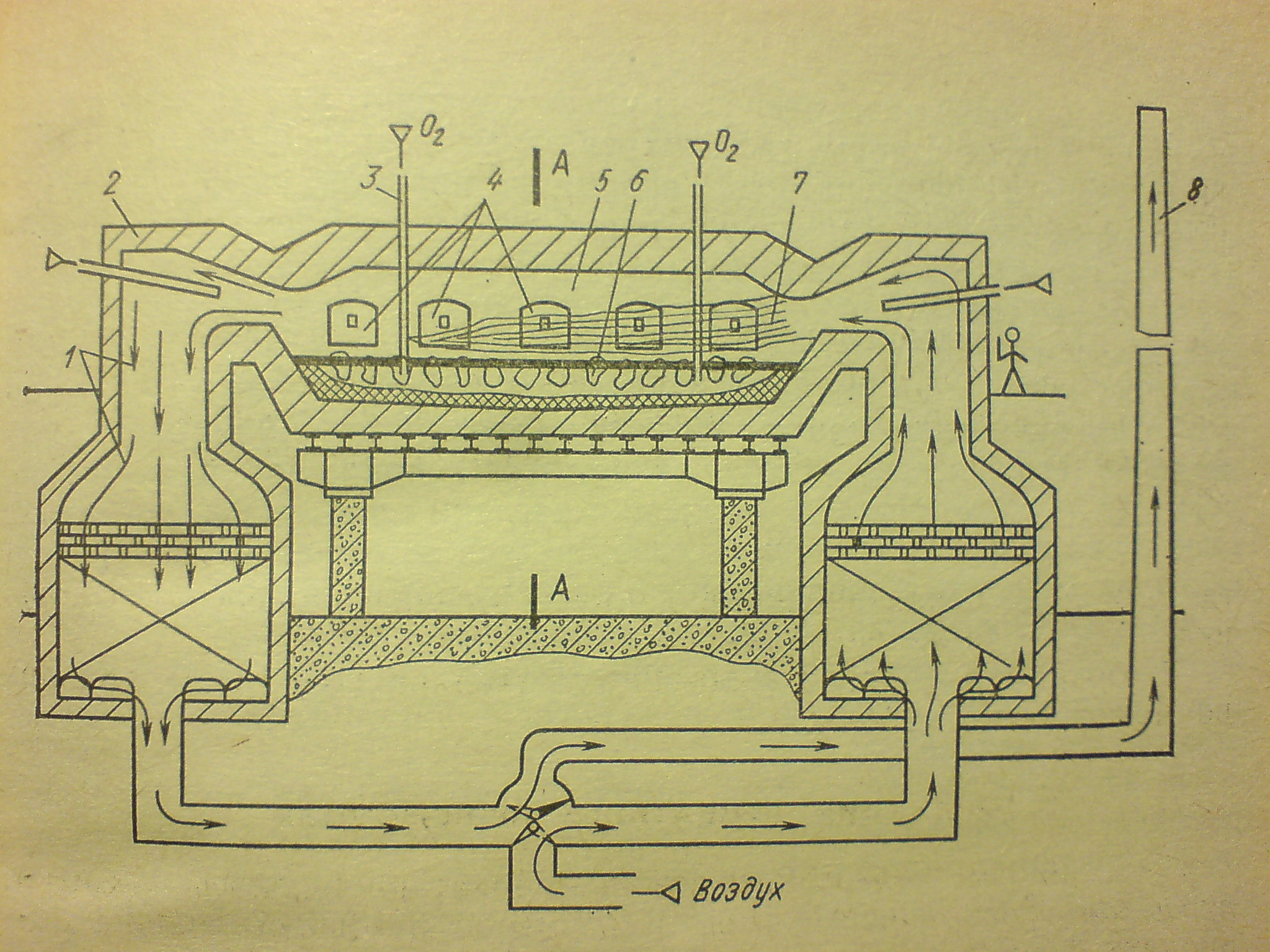
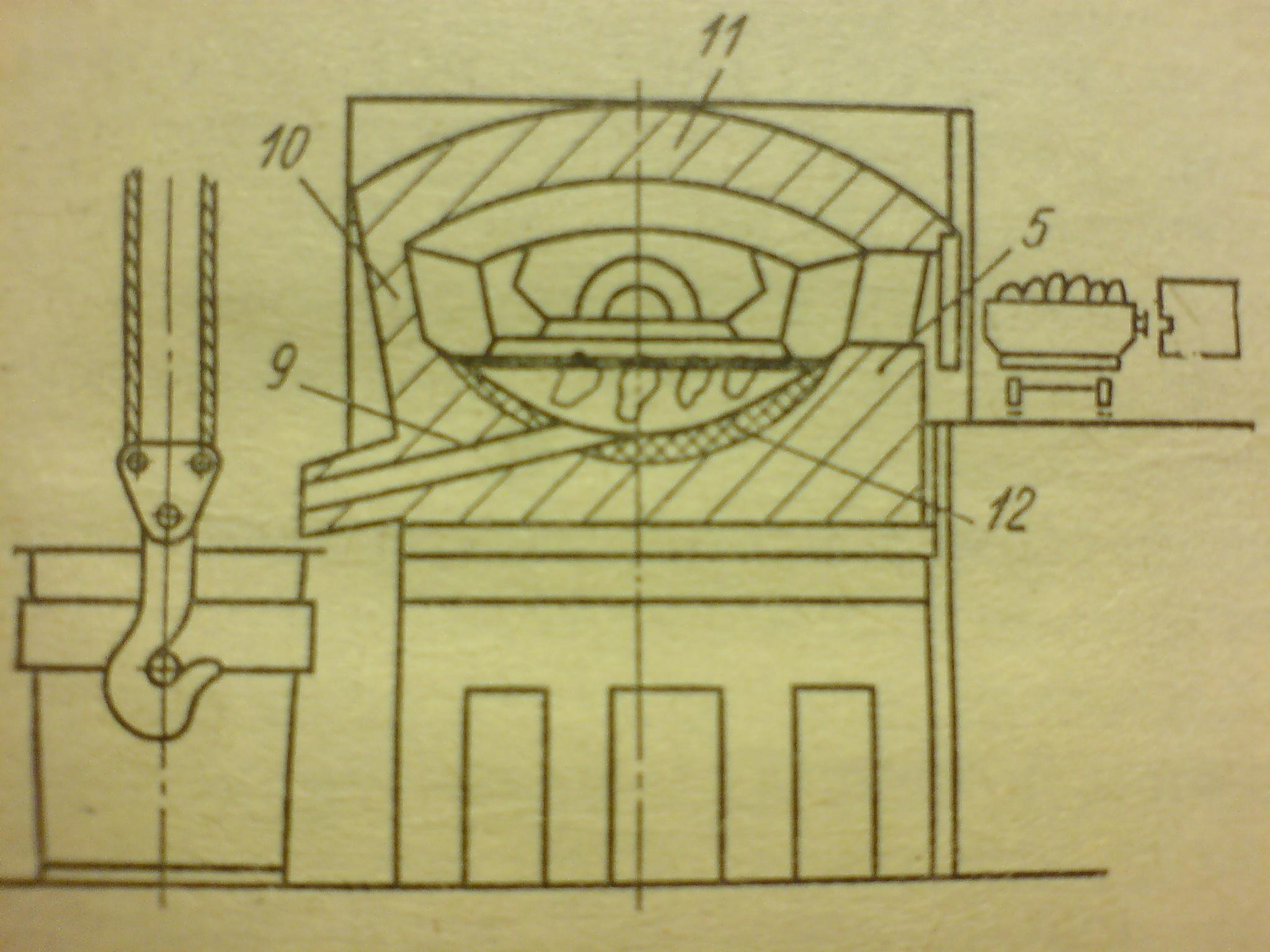
| 8п Устройство и работа мартеновской печи. Мартеновская печь - пламенная отражательная регенеративная печь. Она имеет рабочее плавильное пространство, ограниченное снизу подиной 12, сверху сводом 11, а с боков передней 5 и задней 10 стенками. Подина имеет форму ванны с откосами по направлению к стенкам печи. Футеровка печи может быть основной и кислой. Если в процессе плавки стали в шлаке преобладают основные окислы, процесс называют основным мартеновским процессом, а если кислые — кислым. Основную мартеновскую печь футеруют магнезитовым кирпичом, на который набивают магнезитовый порошок. Кислую мартеновскую печь футеруют динасовым кирпичом, а подину набивают из кварцевого песка. Свод мартеновской печи делают из динасового кирпича или магнезитохромитового кирпича. В передней стенке печи имеются загрузочные окна 4 для подачи шихты и флюса, а в задней — отверстие 9 для выпуска готовой стали.
В нашей стране работают мартеновские печи вместимостью 200— 900 т жидкой стали. Характеристикой рабочего пространства является площадь пода печи, которую условно подсчитывают на уровне порогов загрузочных окон. Например, для печи вместимостью 900 т площадь пода составляет 115 м2. Головки печи 2 служат для смешения топлива (мазута или газа) с воздухом и подачи этой смеси в плавильное пространство.
Для подогрева воздуха и газа (при работе на низкокалорийном газе печь имеет два регенератора 1. Регенератор—это камера, в которой размещена насадка — огнеупорный кирпич, выложенный в клетку. Отходящие из печи газы имеют температуру 1500-1600°C. Попадая в регенераторы, газы нагревают насадку до 1250-1280°С. Через один из регенераторов, например, правый подают воздух, который, проходя через насадку, нагревается до температуры 1100-1200 °С и поступает в головку печи, где смешивается с топливом на выходе из головки образуется факел 7, направленный на шихту 6. Отходящие газы проходят через противоположную головку (левую) очистные устройства (шлаковики), служащие для отделения от газа частиц шлака и пыли, и направляются во второй (левый) регенератор нагревая его насадку. Охлажденные газы покидают печь через дымовую трубу 8. После охлаждения насадки правого регенератора переключают клапаны и поток газов в печи изменяет направление: через нагретые левый регенератор и головку в печь поступает воздух, а правый нагревается теплотой отходящих газов.
Факел имеет температуру 1750—1800°С и нагревает рабочее пространство печи и шихту. Факел способствует окислению примесей шихты при плавке.
В зависимости от состава шихты, используемой при плавке, различают разновидности мартеновского процесса: 1) скрап-процесс, при котором шихта состоит из стального лома (скрапа) и 25— 45 % чушкового передельного чугуна; процесс применяют на заводах, где нет доменных печей, но расположенных в промышленных центрах, где много металлолома; 2) скрап-рудный процесс, при котором шихта состоит из жидкого чугуна (55—75 %), скрапа и железной руды; процесс применяют на металлургических заводах, имеющих доменные печи. Наибольшее количество стали производят скрап-рудным процессом в мартеновских печах с основной футеровкой, что позволяет переделывать в сталь различные шихтовые материалы.
Плавка стали скрап-рудным процессом в основной мартеновской печи. В печь с помощью завалочной машины загружают железную руду, и известняки после их прогрева подают скрап. По окончании прогрева скрапа в печь заливают жидкий чугун, который взаимодействует с железной рудой и скрапом. В и период плавления за счет оксидов руды и скрапа интенсивно окисляются примеси чугуна: кремний, фосфор по реакции (6), марганец и частично углерод. Оксиды SiO2, Р2О5, МnО, а также СаО и извести образуют шлак с высоким содержанием FeO и МnО (железистый шлак).
Кислый мартеновский процесс. Этим способом выплавляют качественные стали.
Основные технико-экономические показатели производства стали в мартеновских печах следующие: производительность печи, определяемая съемом стали с 1м2 площади пода в сутки (т/м2 в сутки) и расход топлива на 1 т выплавляемой стали (кг/т). Средний съем стали с 1м2 площади пода в сутки составляет 10 т/м, а расход условного топлива — до 80 кг/т.
| 8пп 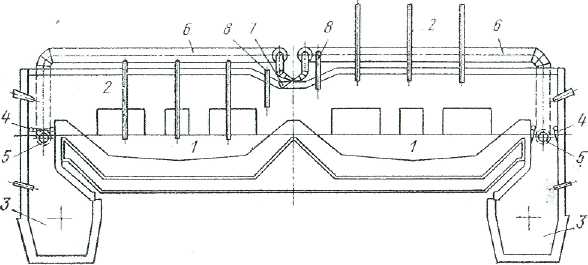
1 – ванны печи; 2 – фурмы; 3 – шлаковики; 4 – водоохлаждаемая заслонка; 5 – амбразура для отбора воздуха из вертикального канала; 6 – футерованный воздухопровод; 7 – амбразура в своде печи; 8 – эжектор использования СО и частичного улавливания пыли в самом рабочем пространстве создана двух ванная сталеплавильная печь (рис. 123).
Рабочее пространство такой печи разделено переводом на две ванны. Обе ванны имеют общий .свод, так что продукты сгорания, образующиеся в одной ванне, проходят вторую часть рабочего пространства. 1.1 Устройство работы двухванной печи Печь работает следующим образом: в одной ванне (горячей) происходит плавление и доводка с интенсивной продувкой металла кислородом, а во второй ванне (холодной) в то же время идет завалка и прогрев твердой шихты. Газы из горячей части печи направляются в холодную и состоят до 35% из оксида углерода. В холодной части печи СО догорает до СО2 и за счет выделяющегося тепла происходит нагрев твердой шихты. Недостающее для процесса нагрева тепло восполняется подачей природного газа через горелки, установленные в своде печи. Сгорание природного газа и догорание СО совершаются за счет дополнительного кислорода.
Когда готовую сталь из первой ванны выпускают, во вторую ванну заливают жидкий чугун. После заливки чугуна тут же начинают продувку ванны кислородом. Заканчивается продувка за 5–7 мин до выпуска. С выпуском металла из первой ванны цикл плавки заканчивается и начинается новый. В то же время с помощью перекидных шиберов изменяется направление движения газов. Теперь бывшая холодная ванна становится горячей. Первую ванну заправляют и производят завалку шихты, и цикл повторяется.
Двух ванная печь должна работать таким образом, чтобы было равенство холодного и горячего периодов, протекающих одновременно в разных ваннах. В холодный период входит выпуск, заправка, завалка, прогрев, заливка чугуна; в горячий период – плавление и доводка. Например, для печи с садкой каждой ванны 250 т общая продолжительность плавки составляет 4 ч, каждый период длится по 2 ч. Металл выпускается также через каждые 2 ч. Раскисление стали, производят в ковше.
| 8ппп Металл продувают кислородом в каждой ванне через две–три кислородные фурмы с интенсивностью 20–25м3/ч" на 1 т металла. Каждая часть печи оборудована сводовыми кислородными фурмами и газокислородными горелками. Горелки необходимы для сушки и разогрева печи после ремонтов, а также для подачи дополнительного топлива.
Современные двухванные печи работают на техническом кислороде без вентиляторного воздуха, поэтому регенераторы отсутствуют. Холодная ванна печи частично выполняет роль регенераторов, аккумулируя тепло газов, покидающих горячую часть печи с температурой 1700°С, и частично улавливает плавильную пыль, тем самым выполняет роль шлаковиков. Тем не менее количество пыли в продуктах сгорания, покидающих печь, составляет большую величину (20–40 т/м} Пыль состоит на 85–90 % из окислов железа.
Дымовые газы, покидающие рабочее пространство печи с температурой около 1500 °С, поступают по вертикальному каналу в шлаковик, в котором охлаждаются водой до температуры 900–1000 °С, а затем направляются в боров. В борове за счет подсоса холодного воздуха происходит дальнейшее понижение их температуры до 700 °С
9 Плавка стали в электропечах: сущность процесса, исходные материалы, преимущества, область использования. Схема электропечи для выплавки стали.
Плавильные электропечи имеют преимущества по сравнению с другими плавильными агрегатами, так как в них можно получать высокую температуру металла, создавать окислительную, восстановительную, нейтральную атмосферу и вакуум, что позволяет выплавлять сталь любого состава, раскислять металл с образованием минимального количества неметаллических включений — продуктов раскисления. Поэтому электропечи используют для выплавки конструкционных, высоколегированных, инструментальных, специальных сталей и сплавов.
Плавильные электропечи бывают дуговыми и индукционными.
Дуговая плавильная электропечь (рис. 2.5) питается трехфазным переменным током и имеет три цилиндрических электрода 9 из графтизированной массы. Электрический ток от трансформатора кабелями 7 подводится к электрододержателям 8, а через них — к электродам 9 и ванне металла. Между электродами и металлической шихтой 3 возникает электрическая дуга, электроэнергия прекращается в теплоту, которая передается металлу и шлаку излучением. Рабочее напряжение 160......600 В, сила тока 1-10 кА. Во время работы печи длина дуги регулируемся автоматически путем перемещения электродов. Стальной кожух 4 печи футерован огнеупорным кирпичом 7, основным (магнезитовый, магнезитохромитовый) или кислым (динасовый). Подину 12 печи набивают огнеупорной массой. Плавильное пространство ограничено стенками 5, подиной 12 и сводом 6 из огнеупорного кирпича. Для управления ходом плавки имеются рабочее окно 10 и летка для выпуска готовой стали по желобу 2 в ковш.
Печь загружают при снятом своде. Механизмом 11 печь может наклоняться в сторону загрузочного окна и летки. Вместимость этих печей 0,5-400 т. В металлургических цехах используют электропечи с основной футеровкой, а в литейных с кислой.
В основной дуговой печи можно осуществить плавку двух видов: на шихте из легированных отходов (методом переплава) и на углеродистой шихте (с окислением примесей).
Плавку на шихте из легированных отходов ведут без окисления примесей. Шихта для такой плавки должна иметь меньше, чем в выплавляемой стали, марганца и кремния и низкое содержание фосфора. По сути это переплав. Однако в процессе плавки примеси (алюминии, титан, кремний марганец, хром) окисляются. Кроме этого, шихта может содержать оксиды. После расплавления шихты из металла удаляют серу, наводя основной шлак, при необходимости науглероживают и доводят металл до заданного химического состава. Затем проводят диффузионное раскисление, подавая на шлак мелкораздробленны и ферросилиций, алюминий, молотый кокс. Так выплавляют легированные стали из отходов машиностроительных заводов,
При выплавке легированных сталей в дуговых печах в сталь вводят легирующие элементы в виде ферросплавов. Порядок ввода определяется сродством легирующих элементов к кислороду. В дуговых печах выплавляют высококачественные углеродистые стали — конструкционные, инструментальные, жаропрочные и жаростойкие.
| |
|
|