|
Ведомый вал муфты. Конструкционные особенности детали
1.10 Подробная разработка операций с ЧПУ Операция: 015
Наименование операции: Токарная программная
Содержание: Установить деталь в трехкулачковый патрон. Крепить.
Станок: токарно-патронный 16К20Ф3С5
Приспособление: трехкулачковый патрон
Режущий инструмент: Резец проходной упорный Т15К6 φ=90
Краткая техническая характеристика станка приведена в таблице: Таблица 2.6 – Токарно-винторезный станок 16К20Ф3С5
-
Класс точности по ГОСТ 8-82
|
| Диаметр обрабатываемой детали, мм
| 400
| Диаметр детали над суппортом, мм
| 220
| Наибольшая длина обрабатываемой заготовки, мм
| 1000
| Габарит станка: Длина, Ширина, Высота, мм
| 3360х1710х1750
| Частота вращения шпинделя, об/мин
| 12.5/2000
| Мощность электродвигателя, кВт
| 10
|
Позиция 1. (Инструмент Т01)
Переход 1 Точить фаску 2х45
Переход 2 Точить диаметр Ø ,
Переход 3 Точить скругление с подрезкой торца, выдерживая размер 
Переход 4 Точить диаметр Ø ,
Переход 5 Точить скругление с подрезкой торца, выдерживая размер 
Переход 6 Точить фаску 1,5х45
Резец проходной упорный , Т15К6; Штангенциркуль ШЦ-2 150-0,05
Концентрат СОЖ «МОДУС-А»/ «MODUS-A»
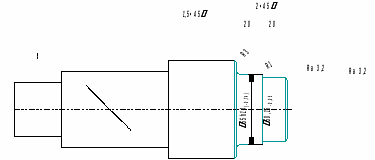
Рисунок 2.4 – Операционный эскиз к операции 015 Переход 2: Точить диаметр Ø , выдерживая размер 
Определяем припуск на операцию по формуле 2.14:
(2.14) где: D – диаметр заготовки;
d – диаметр детали;
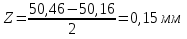 Определяем глубину резания:
t = 0,15 мм
Определяем число проходов по формуле 2.15:
(2.15)
 Определяем подачу:
S = 0,36 мм/об Нормативы режимов резания при работе на станках с ЧПУ (стр. 36)
Определяем скорость резания по формуле 2.16:
(2.16) где: – табличное значение допустимой скорости резания;
м/мин.
Нормативы режимов резания при работе на станках с ЧПУ (стр. 22)
– поправочный коэффициент в зависимости от механических свойств материала заготовки; для штамповки 
– поправочный коэффициент в зависимости от материала режущей части твердого сплава Т15К6;
. Определяем число оборотов шпинделя по формуле 2.17:
(2.17)
 Корректируем частоту вращения шпинделя по паспорту станка 16К20Ф3С5.
об/мин Определяем действительную скорость резания по формуле 2.18:
(2.18)

Переход 4: Точить диаметр Ø ,
Определяем припуск на операцию по формуле 2.19:
(2.19) где: D – диаметр заготовки, мм
d – диаметр детали, мм
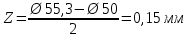 Определяем глубину резания:
t = 0,15 мм
Определяем число проходов по формуле 2.15:
 Определяем подачу:
S = 0,36 мм/об
Нормативы режимов резания при работе на станках с ЧПУ (стр. 36) Определяем скорость резания по формуле 2.16: где: – табличное значение допустимой скорости резания;
м/мин.
Нормативы режимов резания при работе на станках с ЧПУ (стр. 22)
– поправочный коэффициент в зависимости от механических свойств материала заготовки; для штамповки 
– поправочный коэффициент в зависимости от материала режущей части твердого сплава Т15К6;
 Определяем число оборотов шпинделя по формуле 2.20:
(2.20)
 Корректируем частоту вращения шпинделя по паспорту станка 16К20Ф3С5.
об/мин Определяем действительную скорость резания по формуле 2.21:
(2.21)
 Проверка по мощности привода шпинделя станка: Определяем мощность резания по формуле 2.22:
(2.22) где: – сила резания, Н
V – фактическая скорость резания, м/с
Силу резания при точении рассчитывают по следующей формуле 2.23:
(2.23)
где: – коэффициент, учитывающий свойства обрабатываемого материала, материал режущей части резца, а также условия обработки, по табл. 18П

– общий поправочный коэффициент, численно равный произведению ряда коэффициентов, каждый из которых отражает влияние определенного фактора на силу резания, определяется по формуле 2.24:
(2.24) где: – поправочный коэффициент учитывающий качество обрабатываемого материала, определяется по таблице 19П:

– поправочный коэффициент, учитывающий угол в плане - 30°
– поправочный коэффициент, учитывающий угол в плане.
– поправочный коэффициент, учитывающий наклона главного лезвия.
– поправочный коэффициент учитывающий радиус при вершине резца
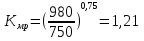
Показатели x, y, n – принимаем по таблице 18П: Тангенциальная сила резания:
; ; ; 
; ; ;


Радиальная сила резания:
; ; ; 
; ; ;


Осевая сила резания:
; ; ; 
; ; ;

 Рассчитываем мощность резания по формуле 2.25:
(2.25)

Мощность, затрачиваемая на резание , кВт, должна быть меньше или равна допустимой мощности на шпинделе , определяемой по мощности привода:
≤ = , где: – мощность электродвигателя токарного станка, кВт (см. паспортные данные станков в приложениях);
η – КПД станка (в паспорте станка).
= 11 кВт
ŋ – К.П.Д коробки скоростей станка – 0,75
= 

 Переход 5 подрезать торец
Определяем глубину резания в зависимости от припуска на обработку:

Для подрезания уступов принимаем подачу в 2 раза меньше, чем подача для наружного точения при тех же условиях 2.26:
(2.26) где: – табличное значение подачи для наружного продольного точения
– 1,3 мм/об
– поправочный коэффициент для угла , 
– поправочный коэффициент для штамповки
 Определяем скорость резания по формуле 2.16: где: – табличное значение допустимой скорости резания;
м/мин.
Нормативы режимов резания при работе на станках с ЧПУ (стр. 22)
– поправочный коэффициент в зависимости от механических свойств материала заготовки; для штамповки 
– поправочный коэффициент в зависимости от материала режущей части твердого сплава Т15К6;
 Определяем число оборотов шпинделя по формуле 2.20:
 Корректируем частоту вращения шпинделя по паспорту станка 16К20Ф3С5.
об/мин Определяем действительную скорость резания по формуле 2.21:
 Рассчитываем основное (машинное) время на операцию по формуле 2.27:
(2.27) где: – путь рабочего хода точения фаски 2х45 . 
– путь рабочего хода точения Ø .
– путь рабочего хода точения скругления , 
– путь рабочего хода подрезания уступа на Ø , 
– путь рабочего хода точения Ø ,
– путь рабочего хода точения скругления , 
– путь рабочего хода подрезания уступа на Ø , 
– путь рабочего хода точения фаски 1х45 .  Минутная подача для каждого перехода определяется по формуле 2.28:
(2.28)









 Определяем штучное время, затрачиваемое на данную операцию, определяем по формуле 2.29:
(2.29) где: – вспомогательное время, мин;
время на установку и снятие деталей – 0,52, мин.
время на измерения детали – 0,72, мин.
 Определяем оперативное время по формуле 2.30:
(2.30)
 Время на обслуживание рабочего места определяем по формуле 2.31:
(2.31)
 Время перерывов в работе определяем по формуле 2.32:
(2.32)
 Штучное время определяется по формуле 2.33:
(2.32)
 Подготовительно-заключительное время: 
Штучно калькуляционное время определяем по формуле 2.33:
(2.33) где: N – партия запуска; шт.
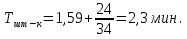
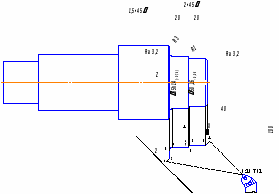
Рисунок 2.4 – циклограмма работы инструмента Таблица 2.7 Разработка рукописи УП в абсолютной системе Н22-1М.
-
Участок траектории
| Содержание кадра
| 1
| 2
|
| N001 G27 T101 S137 M104 LF
| Продолжение таблицы 2.5
-
1
| 2
| 0 – 1
| N002 G10 X+004216 Z-000200 F70000 LF
| 1 – 2
| N003 X+005016 Z+000200 F10360 LF
| 2 – 3
| N004 Z+001900 F10360 LF
| 3 – 4
| N005 G26 G03 I+00768 К+0 X+05216 Z+02000 F10360 LF

0
| 1
| 2
| 4 – 5
| N006 G27 G01 X+05500 F10360 LF
| 5 – 6
| N007 Z+003700 F10360 LF
| 6 – 7
| N008 G26 G03 I+01200 К+0 X+05216 Z+02000 F10360 LF

0
| 7 – 8
| N008 G27 X+007330 F10360 LF
| 8 – 9
| N008 X+008130 Z+004350 F10360 LF
| 9 – 10
| N009 X+020000 Z-004000 F70000 LF
|
| M102 LF
|
Для последующих переходов режимы резания сводим в таблицу: Таблица 2.8– Значения режимов резания, назначенные табличным способом
№ операции
| Содержание перехода
| Z, мм
| L, мм
| t, мм
| i
| S
мм/об
| V
м/мин
| n
об/мин
|
,
мин
| 015 Токарная программная
| Переход 1
| 2
| 5,66
| 2
| 1
| 0,4
| 153
| 1000
| 0,014
| Переход 3
| 1
| 1
| 1
| 1
| 0,4
| 153
| 1000
| 0,003
| Переход 6
| 1,5
| 4,95
| 1,5
| 1
| 0,4
| 153
| 1000
| 0,012
| 1.11Подробная разработка универсальной операции Операция: 030
Наименование операции: Зубофрезерная
Содержание: Установить заготовку в трехкулачковый патрон. Крепить.
Фрезеровать зубья (пов. 24)
Приспособление: трехкулачковый патрон
Оборудования: Зубофрезерный 53А10
Технологические базы: 1,22,20
Обрабатываемая поверхность: 24
Характеристика станка приведена в таблице 2.7:
Таблица 2.9 – краткая техническая характеристика станка 53А10
-
Наибольший диаметр нарезаемых колес, мм
| 500
| Наибольший угол наклона зубьев нарезаемых колес, град.
| ±60
| Наибольший вертикальный ход фрезы, мм
| 360
| Наибольший диаметр фрезы, установленной в суппорте, мм
| 180
| Осевое перемещение фрезы, мм
| 200
| Подача, мм/об.:
вертикальная 0,75-7,5 радиальная 0,2-2,25 осевая 0,13-2,6
|
| Класс точности
| П
| Наибольший диаметр обрабатываемой детали, мм
| 500
| Наибольший модуль обрабатываемых зубчатых колес
| 10
| Длина зуба нарезаемого колеса, мм
| 350
| Min частота вращения шпинделя об/м:
| 40
| Max частота вращения шпинделя, об/м:
| 405
| Мощность, кВт:
| 12,5
| Размеры (Д_Ш_В), мм:
| 2670х1810х2250
| Масса станка с выносным оборудованием, кг
| 9850
|
Выбираем червячную фрезу:
Класс точности – С
Число заходов – 1
Наружный диаметр 
Число зубьев – 18
Назначаем режим резания
Рассчитываем глубину резания: За один проход по формуле 2.34:
(2.34) где: m – модуль нарезаемого колеса

Выбираем подачу: Назначаем подачу на один оборот, нарезаемого зубчатого колеса. Определяем классификационную группу, к которой относится зубофрезерный станок. Станок – 53А10 Определяем подачу:
мм/об. Определяем поправочные коэффициенты на подачу по формуле 2.35:
(2.35) где: – коэффициент, зависящий от обрабатываемого материала – 1
– коэффициент, зависящий от угла наклона зуба – 1

Назначаем период стойкости фрезы:

Определяем скорость главного движения резания
Определяем допустимое число осевых перемещений фрезы за время ее работы между двумя повторными заточками. Принимаем 5 перемещений. Учитываем поправочные коэффициенты на скорость резания по формуле 2.36:
(2.36) где: 
Рассчитываем частоту вращения фрезы по формуле 2.37:
(2.37)
 Корректируем частоту вращения шпинделя по станку:

Уточняем скорость резания по принятому значению по формуле 2.38:
(2.38)

Определяем мощность резания по формуле 2.39:
(2.39) где: – табличное значение мощности резания – 
– поправочный коэффициент в зависимости от механической характеристики стали – 
– поправочный коэффициент в зависимости от количества проходов – 
– поправочный коэффициент в зависимости от угла наклона зубьев – 
кВт. Проверяем достаточность мощности привода станка

, следовательно, обработка возможна.
Рассчитываем основное время по формуле 2.40:
(2.40) где: – врезание и перебег фрезы, мм, определяется по формуле 2.41:
(2.41)
, мм

b – ширина зубчатого венца колеса, мм.
z – число зубьев нарезаемого колеса
– частота вращения, мин
– подача на мм/об.
К – число заходов червячной фрезы
 Рассчитываем норму штучного времени по формуле 2.42:
(2.42)
– вспомогательное время;
– основное время; 
– время на обслуживание рабочего места находится по формуле 2.43:
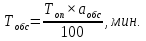

– оперативное время, находим по формуле 2.44:
(2.44)

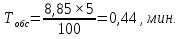
– время на отдых и личные надобности находится по формуле 2.45:
(2.45) где: 

 Определяем подготовительно заключительное время по формуле 2.46:
(2.46) где: n – партия запуска; 
- подготовительно заключительное время включает в себя:
Время на наладку станка, инструмента приспособлений – 30 мин
На пробную обработку деталей – 4,5 мин.
На дополнительные приемы 5 мин.
На получения инструмента и приспособлений до начала и сдачу их после окончания обработки – 7 мин.


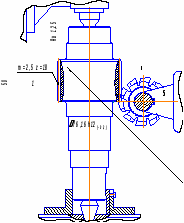
Рисунок 2.5 – эскиз зубофрезерной операции
Таблица 2.10 – таблица режимов резания назначенных табличным методом №
|
| t
| S
| V
| K
| To
| 1
| 2
| 3
| 4
| 5
| 6
| 7
| 005
| Фрезерно-центровальная
Подрезать торец 2,23
Центровать отв. 1,22
|
2
2,5
|
0,6
0,25
|
40
22,4
|
0,011
0,00056
|
0,473
0,033
| 010
| Токарная черновая
Установ 1
Точить пов. 14
Подрезать торец 16
Точить пов. 18
Точить пов. 20
|
1,85
2
1,5
2
|
0,4
0,5
0,4
0,4
|
105
70
105
105
|
0,000075
0,0000224
0,000075
0,000075
|
0,32
0,010
0,32
0,32
|
| Установ 2
Подрезать торец 12
Точить пов. 10
Точить пов. 8
Точить пов. 6
Точить пов. 4
|
2
1,5
2
2
2
|
0,5
0,4
0,5
0,5
0,5
|
70
105
105
105
105
|
0,000011
0,000075
0,000075
0,000075
0,000075
|
0,010
0,32
0,15
0,07
0,114
| 020
| Круглошлифовальная Установ 1
Шлифовать пов. 4
Шлифовать пов. 8 Установ 2
Шлифовать пов. 20
|
0,1
0,1
0,1
|
0,05
0,05
0,05
|
30
30
30
|
0,00012
0,000184
000184
|
0,192
0,744
0,744
| 025
| Шпоночно-фрезерная
Фрезеровать пов. 25
| 0,1
| 1
| 44
| 0,00666
| 0,93
|
Таблица 2.11 – нормирование операции табличным методом
№ операции
|

|

|

|

|

|

|

| 005
| 0,46
| 4,9
| 5,36
| 0,29
| 11,01
| 22
| 12
| 010
| 1,62
| 0,93
| 2,55
| 0,13
| 5,23
| 7
| 5,44
| 020
| 1,68
| 1
| 2,68
| 0,134
| 5,494
| 8
| 5,73
| 025
| 0,93
| 0,48
| 1,41
| 0,07
| 2,81
| 14
| 3,22
| 040
| 4,76
| 6,5
| 11,26
| 0,9
| 12,16
| 29
| 13,1
| |
|
|