бтп. 20_03_01_БТПиО. Курсовая работа по дисциплине Безопасность технологических процессов и оборудования
![]()
|
|
Выполнил студент гр.Б18-621-1ЗУ | | Бокарева К. А. |
Принял К.т.н. доцент кафедры ТБ | | Али Е.Б. |
Рецензия:
Степень достижения поставленной цели работы: ___________________________________
_____________________________________________________________________________
Полнота разработки темы: ______________________________________________________
_____________________________________________________________________________
Уровень самостоятельности работы обучающегося: _________________________________
_____________________________________________________________________________
Недостатки работы: ____________________________________________________________
__________________________________________________________________________________________________________________________________________________________
Ижевск 2021
Аннотация
Курсовая работа на тему: «Безопасность технологических процессов и оборудования при изготовлении вала», выполнена студенткой группы Б18-621-1зу, Бокаревой К.А. В работе 48 страница, 7 рисунков, 10 таблицы и 2 диаграммы.
Содержание
Введение……………………………………………………………………….4
Характеристика производственного объекта………………………….…6
Общая характеристика производства……………………….…….….6
Характеристика изготавливаемой продукции……….……………….9
Описание технологического процесса ……………………………...11
Обеспечение безопасности технологического процесса…………….…20
Планировочное решение цеха………………………..………………20
Автоматизация производственных процессов…………………...…21
Обеспечение электробезопасности ………………………………….23
Оценка и улучшение условий труда ……………………………….……27
Характеристика основных вредных и опасных производственных факторов ………………………………………………………………27
Физические факторы………………………………..…….……28
Химические факторы…………………………………….…..…30
Биологические факторы…………………………………….….30
Психологические факторы……………………………………..31
Характеристика тяжести трудового процесса.………...……………32
Характеристика напряженности труда………...……………………33
Итоговая оценка условий труда по степени вредности и опасности……………………………………………………………...35
Травматизм и профессиональные заболевания……………………..36
Средства индивидуальной защиты…………………………………..36
Мероприятия по улучшению условий труда………………………..37
Пожарная безопасность…………………………………………………..40
Охрана окружающей среды………………………………………………42
Выбросы предприятия……………………………..…………………42
Характеристика сточных вод…………….………………………..…43
Предложения по защите окружающей среды.………………………44
Заключение …………………………………………………………………..45
Список используемой литературы….………………………………………46
Введение
Безопасность трудового процесса - это состояние его условий, когда исключено негативное воздействие на работающих опасных и вредных производственных факторов.
Сегодня, когда особенность производства - использование самых разнообразных технологических процессов, сложных по своей физико-химической основе, использование легковоспламеняющихся, высокотоксичных веществ, различного рода излучений, а также внедрение новейшего оборудования и материалов, которые часто мало изучены с точки зрения негативных последствий их применения, жизненно важным стоит вопрос о безопасности. И, несмотря на внедрение новых, более современных, а также безвредных для человека технологий, остается много отраслей, где травматизм являет собой существенную проблему. Таким образом, можно сказать, что степень производственного травматизма в Российской Федерации, в первую очередь, сегодня обусловливается технологическим уровнем всего производства.
Актуальность проблем безопасности труда определяется непрерывным ростом травматизма, количества производственных аварий, а также числа и тяжести профессиональных заболеваний, острых отравлений.
Цель курсовой работы: рассмотреть технологический процесс и оборудование на рабочем месте токаря-расточника, и проанализировать безопасность его трудовой деятельности.
Задачи:
Проанализировать технологический процесс изготовления вала.
Рассмотреть обеспечение безопасности технологического процесса в токарном цехе.
Рассмотреть основные вредные и опасные производственные факторы на рабочем месте токаря-расточника.
Разработать план мероприятий по улучшению условий труда токаря-расточника.
Изучить воздействие рассматриваемого предприятия на окружающую среду, с последующим предложением альтернативных воздействий на нее.
1. Характеристика производственного объекта
1.1 Общая характеристика производства
АО «Ижевский механический завод» - многопрофильное промышленное предприятие в России, выпускающее гражданское и служебное оружие, электроинструмент, упаковочное оборудование, нефтегазовое оборудование, медицинскую технику, точное стальное литье, а также машиностроение, приборостроение, металлургия, микроэлектроника. Он был основан 20 июля 1942 года.
Потенциальные опасности в токарном цехе:
вероятность контакта с вращающимися (шпиндели сверлильных станков, патроны токарных станков) и перемещающимися (суппорты токарных станков) элементами оборудования при замерах, установке и снятии детали;
возможность контакта с отлетающими осколками инструмента в виду его поломки или выкрашивания;
возможность контакта с отлетающей стружкой во время работы с заготовкой;
наличие опасной зоны - перемещающимися по проходам электрокары, поднимаемые-опускаемые и перемещаемые кран-балкой грузы;
риск появления электрического напряжения на металлических нетоковедущих частях оборудования и приспособлений из-за повреждения изоляции токоведущих элементов;
загазованность воздуха рабочей зоны парами смазочно-охлаждающими жидкостями в результате ее разбрызгивания и испарения в процессе работы оборудования;
возможность повышения уровня производственного шума в виду одновременной работы всех установленных на участке единиц технологического оборудования.
Для общей характеристики объекта необходимо также рассмотреть непосредственно сам материал, из которого производится деталь, а именно сталь марок 45.
Сталь марки 45- конструкционная углеродистая качественная со содержанием от 0,42 до 0,5% углерода, магний более 0,1% и кремний более 0,1%.
Валы, в основном, изготовляют из конструкционных и легированных сталей, к которым предъявляются требования высокой прочности, хорошей обрабатываемости, малой чувствительности к концентрации напряжений, а также повышенной износостойкости. В технических требованиях на изготовление валов, прежде всего, указывается твердость материала или необходимость соответствующей термической обработки. Эти специальные свойства стали придают добавки определенного количества других металлов-хрома, молибдена, никеля, вольфрама и др. Данные добавки называются легирующими, а сами стали, соответственно, легированными сталями[4].
Поэтому сталь 45 - конструкционная легированная. Если значение твердости не превышает НВ 200...230, то заготовки подвергают нормализации, отжигу или термически не обрабатывают. Для увеличения износостойкости валов повышают твердость их рабочих поверхностей. Часто это достигается поверхностной закалкой токами высокой частоты, обеспечивающей твердость HRС 48...55.
Поверхности валов из малоуглеродистых марок стали подвергают цементации на глубину 0,7...1,5 мм с последующей закалкой и отпуском. Представлена таблица 1, в ней рассмотрен основной состав стали 45
Таблица 1- Основной состав стали 45
Показатель | Величина |
Удельный вес | 7826 кг/м3 |
Температура ковки, оС | начала 1250, конца 700 |
Термообработка | Закалка 880 оС, масло, Отпуск 220 Со, воды |
Твердость материала | HB 10 -1 = 170 Мпа |
Представленная диаграмма, в ней рассмотрено химический состав стали 45
Диаграмма 1-химический состав стали 45
C | 0,42 - 0,5 | ![]() |
Si | 0,17 - 0,37 | |
Mn | 0,5 - 0,8 | |
Ni | до 0,25 | |
S | до 0,04 | |
P | до 0,035 | |
Cr | до 0,25 | |
Cu | до 0,25 | |
As | до 0,08 | |
Fe | 97 |
1.2 Характеристика изготавливаемой продукции
Вал — это деталь механизма, выполненная из металла, имеющая сечение определенной формы и передающая крутящий момент на другие элементы, вызывая их вращение.
Для изготовления валов используются заготовки с большим припуском, которые зажимаются в патроне и поджимаются задним центром. При черновой обработке необходимо максимально снять припуск, используя наибольшую глубину резания, определяемую мощностью станка. Оставшиеся припуски для окончательной обработки высчитываются исходя из конфигурации и размеров детали, методов последующей обработки.
При соотношении диаметра вала к его длине более чем 1:15 применяются подвижные и неподвижные люнеты. Эти поддерживающие устройства принимают на себя реакцию сил резания, не допуская деформаций заготовки. Этим повышается жесткость режущей системы и уменьшается вероятность возникновения нежелательных вибраций.
Чистовая обработка валов проводится в центрах, при этом конец вала закрепляется в поводковом патроне или используется хомутик. При обработке единичных изделий одна сторона вала проходится за одну установку с использованием всех необходимых инструментов. Крупные партии изделий изготавливаются на различных станках с использованием минимального набора инструментов. Чистовая обработка проводится на высокоточном оборудовании. При этом обработка начинается с наибольшего диаметра, последовательно переходя на следующий меньший размер.
Ось, отличается от вала тем, что служит только для их опоры. Если оси подразделяются на подвижные и статические, то валы всегда вращающиеся. Геометрическая форма оси, может быть только прямой.
Вал составляют следующие участки:
Опорный.
Промежуточный.
Концевой.
Вал имеет центровые отверстия, позволяющие устанавливать его в центрах на большинстве операций, кроме сверлильной и фрезерной операций, что обеспечивает необходимую точность размеров обрабатываемых поверхностей и их взаимное расположение. Это обеспечивает принцип постоянства баз в технологическом процессе.
К нетехнологическим элементам могут быть отнесены закрытые шпоночные пазы и глухое отверстие с резьбой FM16 в торце детали.
Деталь имеет удобные базовые поверхности, что позволяет на всех операциях использовать стандартные приспособления, представлено на рисунке 1.
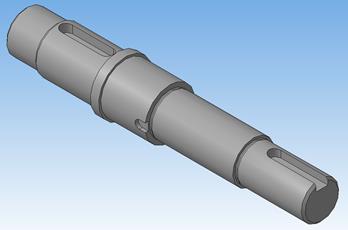
Рисунок 1- схема вала
Технические требования при изготовлении вала:
точность сопрягаемых цилиндрических поверхностей по 6—8-му квалитетам с параметрами шероховатости поверхности соответственно Ra= 1,25 ... 0,63 мкм и Ra — 2,5 ... 1,25 мкм;
допуск цилиндричности и круглости шеек под подшипники примерно 0,25—0,5 допуска на диаметральный размер;
допуск радиального биения шеек под зубчатые колеса относительно шеек под подшипники примерно 0,25—0,5 допуска на диаметральный размер;
допуск радиального биения шеек под зубчатые колеса относительно шеек под подшипники 0,01—0,03 мм;
допуск соосности шеек под подшипники 0,01—0,02 мм;
допуск симметричности боковых сторон шпоночных канавок и зубьев шлицевых поверхностей относительно общей оси подшипниковых шеек 0,03— 0,05 мм.
1.3 Описание технологического процесса
Технологическим процессом называют часть производственного процесса, содержащую действия по изменению и последующему определению состояния предмета производства. В результате выполнения технологических процессов изменяются физико-химические свойства материалов, размеры и относительное положение элементов деталей, геометрическая форма, качество поверхности, внешний вид объекта производства и т.д. Технологический процесс состоит из технологических и вспомогательных операций.
Технологический процесс изготовления валов
К валам относят детали, образованные наружными и внутренними поверхностями вращения, имеющими одну общую прямолинейную ось при отношении длины цилиндрической части к наибольшему наружному диаметру более двух представлено на рисунке 2.
а) ![]() | б) ![]() | в) ![]() |
г) ![]() | д) ![]() | е) ![]() |
Рисунок 2-Типичные ступенчатые валы
а – ступенчатый вал без шлицев и зубчатого венца; б – шлицевой вал; в – вал-шестерня без шлицев; г – вал-шестерня со шлицами; д – вал-шестерня коническая со шлицами; е – полый ступенчатый вал
Конструктивное разнообразие валов вызывается различным сочетанием цилиндрических, конических, а также зубчатых (шлицевых), резьбовых поверхностей. Валы могут иметь шпоночные пазы, лыски, осевые и радиальные отверстия.
Валы классифицируются по различным признакам.
По форме наружных поверхностей:
бесступенчатые;
ступенчатые;
с фасонными частями (конусами, шлицами, фланцами, зубчатыми венцами, кулачками, рейками и т.п.)
По форме внутренних поверхностей:
сплошные;
полые.
По соотношению размеров:
жесткие;
нежесткие.
Жесткими считаются валы, у которых отношение длины к диаметру (l/d) не превышает 10 – 12см. Валы с большим соотношением называют нежесткими.
Основные технологические задачи при обработке валов следующие:
выдержать: точность и шероховатость поверхностей (5 – 7 квалитет; шероховатость Ra=0,03…2,5 мкм); прямолинейность общей оси; концентричность поверхностей вращения; соосность резьб с наружными поверхностями или точными внутренними цилиндрическими отверстиями;
получить глубокие центральные отверстия, соосные наружной поверхности в пустотелых валах (допускаемые отклонения ± 0,02) с радиальным биением шеек и торцовым биением торцов 0,02 – 0,03;
выполнить шпоночные канавки и шлицы, параллельные оси вала (допускаемое отклонение 0,03 на длине 100мм).
Точность размеров валов являются, как правило, его опорные шейки, поверхности под детали, передающие крутящий момент. Обычно они выполняются по 6 – 7-му квалитетам.
Точность формы - наиболее точно регламентируется форма в продольном и поперечном сечениях у опорных шеек под подшипники качения. Отклонения от круглости и профиля в продольном сечении не должны превышать 0,25...0,5 допуска на диаметр в зависимости от типа и класса точности подшипника.
Точность взаимного расположения поверхностей. Для большинства валов главным является обеспечение соосности рабочих поверхностей, а также перпендикулярности рабочих торцов базовым поверхностям. Как правило, эти величины выбираются по V–VII степеням точности.
Качество поверхностного слоя. Шероховатость базовых поверхностей обычно составляет Rа = 3,2...0,4 мкм, рабочих торцов Rа = 3,2...1,6 мкм, остальных неответственных поверхностей Rа = 12,5...6,3 мкм. Валы могут быть сырыми и термообработанными. Твердость поверхностных слоев, способ термообработки могут быть весьма разнообразными в зависимости от конструктивного назначения валов. Если значение твердости не превышает НВ 200...230, то заготовки подвергают нормализации, отжигу или термически не обрабатывают. Для увеличения износостойкости валов повышают твердость их рабочих поверхностей. Часто это достигается поверхностной закалкой токами высокой частоты, обеспечивающей твердость НRС 48...55. Поверхности валов из малоуглеродистых марок стали подвергают цементации на глубину 0,7...1,5 мм с последующей закалкой и отпуском. Таким способом можно достичь твердости НRС 55...60.
Основные технологические базы - преимущественно центровые отверстия, центровые фаски для пустотелых валов.
Наиболее распространённым методом обработки цилиндрических наружных поверхностей является точение резцом (резцами).
Для точения цилиндрических поверхностей и поверхностей, прилегающих к ним и ограничивающих их длину (торцы, уступы, канавки, радиусы и т.д.), применяют проходные, подрезные (прямые и отогнутые), отрезные, канавочные и другие резцы с напайными пластинами из быстрорежущей стали или твёрдых сплавов и композиционных материалов.
При токарной обработке различают:
черновое точение (или обдирочное) – с точностью обработки IТ13... IТ12 с шероховатостью поверхности до Rа = 6,3 мкм;
получистовое точение – IТ12... IТ11 и шероховатость до Rа = = 1,6 мкм;
чистовое точение – IТ10... IТ8 и шероховатость до Rа = 0,4 мкм.
При черновом обтачивании, как и при любой черновой обработке снимают до 70% припуска. При этом назначаются максимально возможные глубина резания и подача.
На черновых операциях повышение производительности обработки добиваются увеличением глубины резания (уменьшением числа рабочих ходов), а также подачи.
На чистовых операциях подача ограничивается заданной шероховатостью поверхности, поэтому сокращение основного времени возможно за счёт увеличения скорости резания. На универсальных токарно-карусельных станках обрабатывают заготовки деталей типа тел вращения разнообразной формы диаметром до 10 000 мм.
К методам чистовой обработки относятся: тонкое точение и различные методы шлифования. Они, как правило, позволяют обеспечить требуемые точность размеров, формы, взаимного расположения и, в большинстве случаев, качество поверхностного слоя.
Тонкое точение применяется, главным образом, для отделки деталей из цветных металлов и сплавов (бронза, латунь, алюминиевые сплавы и другие) и отчасти для деталей из чугуна и закалённых сталей (НRС 45...60). Объясняется это тем, что шлифование цветных металлов и сплавов значительно труднее, чем стали и чугуна, вследствие быстрого засаливания кругов. Кроме того, имеются некоторые детали, шлифование которых не допускается из-за возможного шаржирования поверхности.
Тонкое точение обеспечивает получение наружных цилиндрических поверхностей вращения правильной геометрической формы с точным пространственным расположением осей и является высокопроизводительным методом. При тонком точении используются алмазные резцы или резцы, оснащённые твёрдым сплавом. Тонкое точение характеризуется незначительной глубиной резания (t = 0,05...0,2 мм), малыми подачами (S = 0,02...0,2 мм/об) и высокими скоростями резания (V = 120….1000 м/мин). Точность размеров IТ5...IТ6; Ra = 0,8...0,4 мкм.
Подготовка поверхности под тонкое точение сводится к чистовой обработке с точностью IТ8...IТ9. Весь припуск снимается за один рабочий ход. Применяются станки особо высокой точности, жёсткости и виброустойчивости. На этих станках не следует выполнять другие операции.
Основные операции при обработке гладких и ступенчатых валов – это центрование, обточка на токарных станках, шлифование посадочных поверхностей, доводка поверхностей.
Основные схемы базирования. Основными конструкторскими базами большинства валов являются поверхности опорных шеек. Однако использовать их в качестве технологических баз для обработки наружных поверхностей на всех операциях затруднительно. Для условия сохранения единства и постоянства баз за технологические базы принимают поверхности центровых отверстий (ГОСТ 14034–74).
Передача крутящего момента при установке вала в центрах осуществляется с помощью поводкового патрона (ГОСТ 2571–71) или хомутика (ГОСТ 2578–70).
Основные операции механической обработки:
Заготовительная. Для заготовок из проката: рубка прутка на прессе или резка прутка на фрезерно-отрезном или другом станке. Для заготовок, получаемых методом пластического деформирования, штамповать или ковать заготовку.
Правильная (применяется для проката). Правка заготовки на прессе или другом оборудовании. В массовом производстве может производиться до отрезки заготовки. В этом случае правится весь пруток на правильно-калибровочном станке.
Термическая. Улучшение, нормализация.
Подготовка технологических баз. Операцию обработки торцов и сверление центровых отверстий в зависимости от типа производства производят:
в единичном производстве подрезку торцов и центрование на универсальных токарных станках последовательно за два установа с установкой заготовки по наружному диаметру в патроне;
в серийном производстве подрезку торцов выполняют раздельно от центрования на продольно-фрезерных или горизонтально-фрезерных станках, а центрование – на одностороннем или двустороннем центровальном станке. Применяются фрезерно-центровальные полуавтоматы последовательного действия с установкой заготовки по наружному диаметру в призмы и базированием в осевом направлении по упору;
в массовом производстве применяют фрезерно-центровальные станки барабанного типа, которые одновременно фрезеруют и центруют две заготовки без съема их со станка.