Навигация по странице:MATEMATИЧECKAЯ MOДEЛЬ AДEKBATHA2.2. Применяемое оборудование, контрольно- измерительные приборы и материалы2.3. Основы теории тепловых процессов сварочной дуги и массопереноса металла через дуговой промежуток, основные параметры электродуговой сваркиПроцесс массопереноса расплавленного металла через межэлектродный промежутокОсновные параметры электродуговой сваркиСкорость протекания процессов обезуглероживания зависят от температуры дугового промежутка и от характера массопереноса, который зависит от силы сварочного тока.2.4. Порядок проведения экспериментальных исследований 2.5. Построение математической моделиПорядок расчета математической модели на компьютереИСХОДНЫЕ ДАННЫЕ 120,000 135,000 150,000 180,000 200,000 5,700 5,500 5,6000 5,7000 5,900 6,100 6,200 6,300 6,100Решение матричного уравнения A*B=C A(J) -.356264E-03 .113120E+00 -.284005E+01 X(I) YM(I) YT(I)200.00 .556667E+01 .553346E+01Математическая модель адекватна
|
Лабораторная работа1. Лабораторная работа 1 Исследование стабильности горения сварочной дуги переменного тока
PACЧET ДИCПEPCИИ BOCПPOИЗBOДИMOCTИ ПOCTPOEHИE MATEMATИЧECKOЙ MOДEЛИ
A= .438466E+02 P= .0 B= .423472E-01
X(I) YM1(I) YT(I)
38.70 .848528E+01 .851528E+01
27.00 .118272E+02 .139757E+02
24.70 .176603E+02 .154055E+02
37.50 .926764E+01 .895918E+01 ПPOBEPKA AДEKBATHOCTИ MATEMATИЧECKOЙ MOДEЛИ
MATEMATИЧECKAЯ MOДEЛЬ AДEKBATHA
Рис.1.7. Листинг расчета математической модели на компьютере Математическая модель зависимости критического расстояния между электродами имеет вид: Lкр = 59,1819 exp( -0,0524249x)
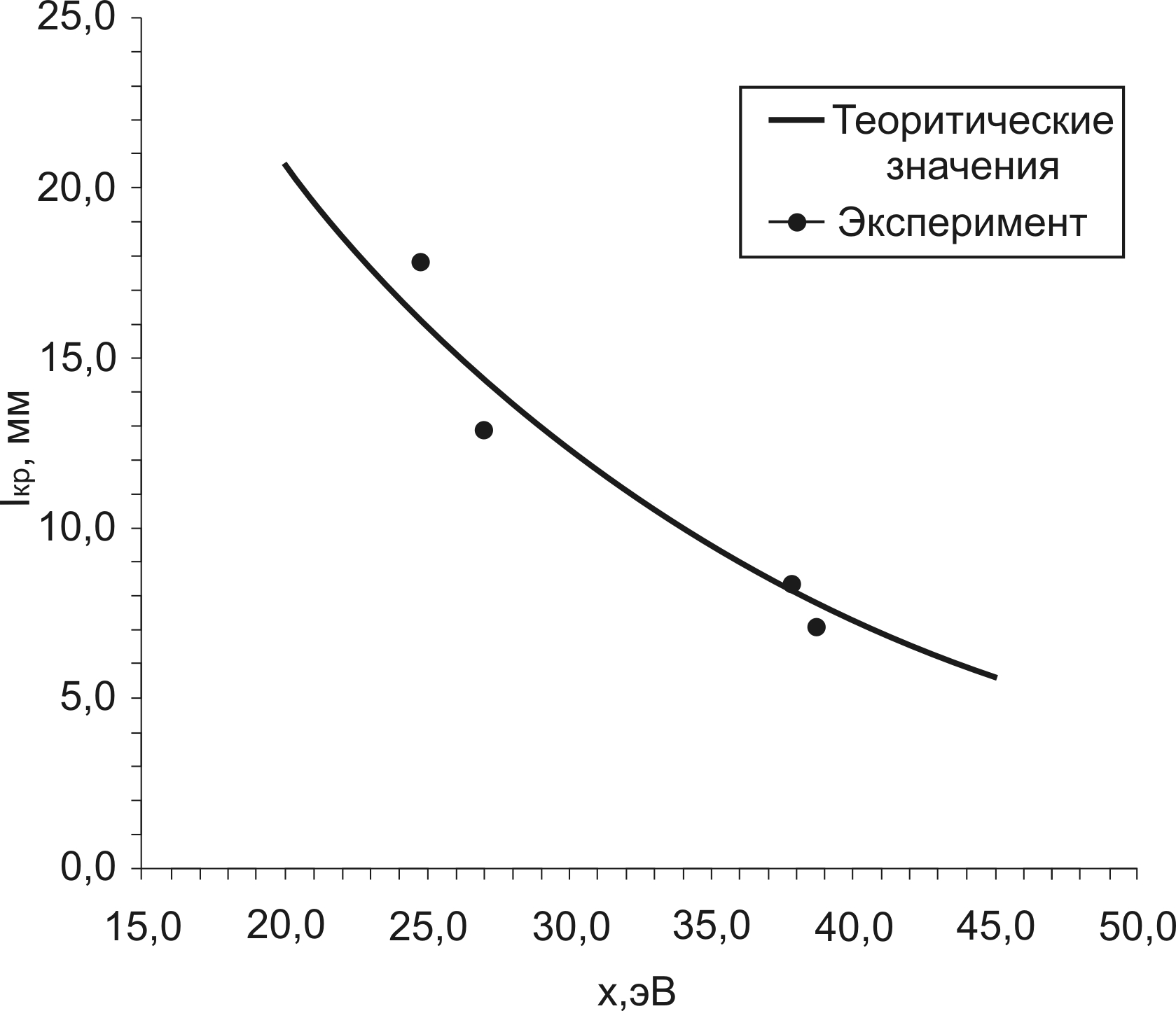
Рис.1.8. Зависимость критического расстояния lкр от приведенного потенциала ионизации х Лабораторная работа по сварке №2
Исследование влияния силы сварочного тока на значения коэффициентов наплавки и расплавления
2.1. Задачи работы, стоящие перед студентами
2.1.1. Закрепить теоретические знания, полученные на лекциях.
2.1.2. Получить навыки по постановке задачи и проведения иссле-дований.
2.1.3. Ознакомиться с лабораторным оборудованием и контрольно-измерительными устройствами.
2.1.4. Провести исследования экспериментальные исследования влияния силы сварочного тока на значения коэффициентов наплавки и расплавления
2.1.5. Построить математическую модель и обработать результаты экспериментальных исследований на персональных компьютерах. 2.2. Применяемое оборудование, контрольно- измерительные приборы и материалы При проведении лабораторной работы в распоряжении студентов:
сварочный трансформатор, электрододержатель, электронные весы, штангенциркуль, металлические пластинки. 2.3. Основы теории тепловых процессов сварочной дуги и массопереноса металла через дуговой промежуток, основные параметры электродуговой сварки Сварочная дуга является мощным концентрированным источником тепловой энергии. Электрическая энергия, потребляемая сварочной дугой, преобразуется в тепловую энергию, которая локально вводится в место соединения заготовок.
Полная тепловая энергия, выделяемая при горении электрической сварочной дуги, может быть рассчитана по формуле:
Qп = I∙U∙t, Дж (2.1 )
где I – сила сварочного тока (А); U – напряжение сварочной дуги (В); t – время сварки (с).
Однако не вся тепловая энергия, выделяющаяся при горении сварочной дуги, расходуется на нагрев и расплавление основного металла и электрода; часть тепловой энергии рассеивается в окружающей среде и расходуется на плавление покрытия электрода.
Эффективной тепловой энергией (Qэфф) называется полезно используемая при сварке теплота, которая рассчитывается по формуле:
Qэфф = I∙U∙t, Дж (2.2)
где I – сила сварочного тока, А; U – напряжение сварочной дуги ,В; t – время сварки, с.
Полная тепловая мощность рассчитывается по формуле:
Qп = I∙U, Вт (2.3)
где I – сила сварочного тока (А); U – напряжение сварочной дуги (В).
Эффективная тепловая мощность рассчитывается по формуле:
Qэфф = η∙I∙U, Вт ,Дж/с (2.4)
где η – коэффициент полезного использования тепловой энергии сварочной дуги; I – сила сварочного тока (А); U - напряжение сварочной дуги, В.
Величина зависит от способа сварки, материала электрода, состава покрытия и других факторов. При сварке открытой дугой электродами с толстым покрытием =0,70…0,75, при автоматической сварке под слоем флюса =0,85…0,90.
Электроды или сварочная проволока при различных способах дуговой сварки плавлением нагреваются от двух источников тепловой энергии: эффективной тепловой энергии сварочной дуги и тепловой энергии, которая выделяется при протекании тока по вылету электрода. Тепло, выделяемое на вылете электрода, рассчитывается по закону Джоуля–Ленца, которое рассчитывается по формуле 14
, (2.5)
где - удельное сопротивление металла, Омм; lвыл – длина вылета не более 0,42…0,43 м; F – площадь сечения сварочной проволоки, м2.
При соблюдении оптимальных режимов сварки сварочная прово-
лока по длине вылета нагревается до 870 К (600C). Такая температура способствует ускорению процесса плавления электрода. При большей плотности сварочного тока электрод нагревается более 900 К, при этом ухудшается формирование шва и увеличивается разбрызгивание металла, обмазка отслаивается от поверхности электрода. Поэтому при ручной дуговой сварке величину тока ограничивают.
Температура в столбе электрической дуги по разным источникам колеблется от 5000 К - 7000 К, температура на катоде - 3000 К, на аноде - 3300 К. При таких температурах скорости химических реакций и реакций диссоциации различных газов, веществ велики.
Высокие температуры в реакционной зоне обуславливают высокие скорости протекания химических реакций; температурная зависимость констант скоростей химических реакций определяется законом Аррениуса
K(T) = Ko exp ( - Ea/RT), (2.6)
где Ko - предэкспоненциальный множитель или множитель Аррениуса; Ea – энергия активации химических реакций, Дж/моль; R – газовая постоянная, R=8.314 Дж/(мольК); T – температура в реакционной зоне горения электрической дуги.
В реакционной зоне сварочной дуги имеют место диссоциация газов и веществ покрытий электродов.
Температура в дуговом промежутке равна Т= 5000 …7000 К, на электродных пятнах соответственно - 3000…3500 К. При этих температурах двухатомные газы полностью диссоциированы. На рис.1 приведена температурная зависимость степени диссоциации.
При температурах Т 6000 - 7000 К кислород и водород практически полностью диссоциированы, степень диссоциации азота намного меньше. Атомарные кислород, водород, азот активно взаимодействуют в химических реакциях и активно растворяются в металле. В состав покрытий и флюсов входит плавиковый шпат CaF2, который диссоциирует по реакции
CaF2 = CaF + F.
При температуре Т= 3000 С степень диссоциации = 0,92. F - атомарный фтор ухудшает стабильность горения дуги вследствие высокого сродства к электрону, но связывает водород, образуя фтористый водород, который не растворяется в металле, тем самым играет очень важную роль в металлургических процессах, протекающих в электрической дуге.
Основным источником водорода в дуговом промежутке является влага, которая может содержаться в электродных материалах.
2Н2О = 2Н2 + О2
В состав покрытий и флюсов входят карбонаты, например, мел, мраморная крошка, которые диссоциируют по реакциям
CaCO3 = CaO + CO2
В дуговом промежутке происходит также диссоциация углекислого газа по реакции
2СО2 = 2CO + O2
При температурах Т 6000 - 7000 К кислород и водород практически полностью диссоциированы, степень диссоциации азота намного меньше.
О2=2О; Н2 =2Н; N2=2N
Атомарные кислород, водород, азот активно взаимодействуют в химических реакциях и активно растворяются в металле.
Газовая среда дугового промежутка может существенно влиять на поверхностное натяжение и соответственно поверхностную энергию жидкого металла и тем самым влиять на массоперенос жидкого металла через межэлектродный промежуток.
Процесс массопереноса расплавленного металла через межэлектродный промежуток
Процесс массопереноса жидкого металла через межэлектродный промежуток существенно влияет на качество сварных соединений.
Использование скоростной киносъемки (5800 кад/с) позволило установить, что жидкий металл переносится через межэлектродный промежуток в сварочную ванну в виде капель. Причем сила сварочного тока оказывает существенное влияние на характер массопереноса.
Различают три формы переноса жидкого металла через дуговой промежуток: крупнокапельный (при небольших значениях силы сварочного тока j < 50 A/мм2); мелкокапельный массоперенос (при плотностях силы сварочного тока 50 A/мм2 < j <100 A/мм2); струйный массоперенос жидкого металла - очень мелкие капли (при плотностях силу сварочного тока 100 A/мм2 < j).
Итак, с увеличением силы сварочного тока размеры капель уменьшаются. На размеры капель жидкого металла при заданной силе сварочного тока могут также влиять марка сварочной проволоки и химический состав газов в межэлектродном промежутке, так как они влияют на поверхностную энергию жидкого металла, которая определяет, в конечном счете, размеры капель жидкого металла.
Отрыв капель жидкого металла и перенос их через межэлектрод-ный промежуток в варочную ванну происходит под действием следующих сил: силы тяжести, силу поверхностного натяжения, электромагнитных сил Лоренца, силы давления газов и паров металла. Основные параметры электродуговой сварки При электродуговой сварке формирование сварного шва определяется процессами расплавления плавящегося электрода или присадочного стержня, переносом расплавленного металла через дуговой промежуток, а также наплавки его на основной металл.
Важным параметром дуговой сварки является производитель-ность сварки, которая определяет необходимое время для выполнения сварочных работ.
По определению производительностью сварки (G) называется масса наплавленного металла в единицу времени, которая определя-
ется выражением , г/ч, где Gн – масса наплавленного металла, г; t - время сварки, ч.
Производительность дуговой сварки зависит силы сварочного тока, которую можно определить выражением:
GH=KH I, г/ч, (2.7)
где KH- коэффициент наплавки, г/(Ач), I – силы сварочного тока, А.
Коэффициентом наплавки KH называется масса наплавленного металла, приходящаяся на силу тока в 1А в единицу времени, г/( Ач).
Коэффициент наплавки рассчитывается по формуле
, г/(Ач), (2.8)
где Gн –масса наплавленного металла, г; I- сила сварочного тока, А; t - время сварки, с.
Величина коэффициента наплавки зависит от силы сварочного тока, марки электрода от способа сварки. При ручной дуговой сварке KH=7…10 г/Ач.
Производительность сварки определяется скоростью расплавле-ния плавящегося электрода или присадочного стержня, скоростью потерь жидкого металла, при переносе его межэлектродный промежуток.
Массы расплавленного и наплавленного металла, а также масса потерь жидкого металла в процессе переноса его через межэлектродный промежуток определяется законом сохранения вещества Gр = Gн + Gп , (2.9)
где Gр, Gн, Gп – соответственно массы расплавленного, наплавленного металла, а также масса потерь жидкого металла в процессе его переноса через дуговой промежуток.
Другим важным параметром электродуговой сварки является коэффициент расплавления Кр.
Коэффициентом расплавления Кр называется масса расплавлен-ного металла, приходящаяся на силу тока 1А в единицу времени, г/(А ч).
Коэффициент расплавления рассчитывается по формуле
, г/( Ач), (2.10)
где Gр - масса расплавленного металла, г; I- сила сварочного тока, А; t - время сварки, с.
Оценки, проведенные одним из авторов данной работы, показали, что с увеличением силы сварочного тока имеет незначительное уве-личение коэффициента расплавления, которым можно пренебречь.
Другим очень важным параметром электродуговой сварки является коэффициент потерь, который определяется выражением
100, % (2.11)
где Gл - масса потерь жидкого металла на разбрызгивание в процессе переноса его через дуговой промежуток; Gр - масса расплавленного металла.
Используя выражение (18), можно получить выражение для расчета Кп, используя экспериментально найденные значения коэффициентов расплавления Кр и наплавки Кн
% . (2.12)
На величину потерь жидкого металла при переносе его через междуговой промежуток оказывают следующие факторы: число заряженных частиц и их кинетическая энергия, бомбардирующих ванну жидкого металла (металла заготовок); электромагнитные силы Лоренца, действующих на заряженные капли жидкого металла при переносе их через дуговой промежуток; скорость процессов обезуглероживания (при изготовлении стальных сварных конструкций). Влияние вышеперечисленных факторов определяется силой сварочного тока.
Чем больше сила сварочного тока, тем соответственно больше число заряженных частиц, бомбардирующих ванну жидкого металла, тем больше вероятность потерь жидкого металла разбрызгиванием.
При этом газовая среда дугового промежутка будет оказывать существенное влияние на поверхностную энергию жидкого металла и
соответственно влиять на образование брызг жидкого металла при бомбардировке сварочной ванны заряженными частицами.
При массопереносе жидкого металла через межэлектродный промежуток капли жидкого металла адсорбируют заряженные частицы, на которые действуют электромагнитные силы Лоренца Fл, которые оказывают влияние на величину потерь его при изготовлении сварных конструкций.
Величина сил Лоренца рассчитывается по формуле
, (2.13)
где q – заряд капли жидкого металла; с – скорость света, V – скорость перемещения капель жидкого металла через дуговой промежуток к сварочной ванне под действием сил электрического поля; В – индук- ция магнитного поля. Под действием сил Лоренца заряженные капли металла отклоняются из зоны сварки. Магнитная индукция пропорцио-на силе сварочного тока. Таким образом, с увеличением силу свароч-ного тока потери жидкого метала на разбрызгивание возрастает.
Схема, поясняющая действие сил Лоренца на каплю жидкого металла приведена на рис.2.1.
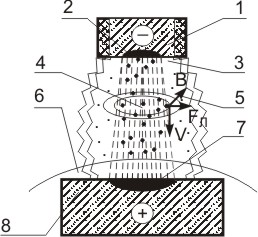 Рис.2.1. Схема, поясняющая действие сил Лоренца на каплю жид-
кого металла при её переносе через дуговой промежуток
Другим фактором, влияющим на потери жидкого металла при сварке стальных конструкций, является скорость процесса обезугле-
роживания. Капля жидкого металла в дуговом промежутке контактирует с двухатомными газами, в частности с кислородом, кото- рый растворяется в ней. В капле стальной сварочной проволоке содержится углерод, который взаимодействует с атомарным кислородом газовой фазы с образованием окиси углерода. Причем оксид углерода не растворяется в жидком металле. Эта химическая реакция изменяет химический состав газовой фазы дугового промежутка. Помимо этого, атомарный кислород газовой фазы активно растворяется в капле жидкого металла и с поверхности её диффундирует внутрь последней. Растворенные кислород [O] и углерод [C] внутри капли жидкого металла взаимодействуют по реакции [O] + [C] = СО, в результате которой образуется оксид углерода, который не растворяется в ней. В результате этой реакции внутри капли жидкого металла образуется газовый пузырь, газовое давление которого растет по мере протекания химической реакции. При достижения критического давления, когда РсоVг >Eпов произойдет разрыв капли жидкого металла на отдельные её части, где Рсо - давление оксида углерода внутри газового пузыря; Vг -критический объем газового пузыря оксида углерода; Епов -поверхностная энергия капли жидкого металла. Таким образом, с увеличением скорости протекания химической реакции обезугле-роживания внутри капли жидкого металла ([C] + [O] =CO) потери металла на разбрызгивание увеличиваются.
Скорость протекания процессов обезуглероживания зависят от температуры дугового промежутка и от характера массопереноса, который зависит от силы сварочного тока.
С увеличением силы сварочного тока размеры переносимых капель жидкого металла через межэлектродный промежуток уменьшаются, и соответственно поверхность контакта газовой фазы дугового промежутка с каплями жидкого металла увеличиваются; соответственно скорость протекания химической реакции обуглероживания [C] + [O] = CO возрастает, и соответственно возрастают потери металла на разбрызгивание.
Таким образом, анализ влияния вышеперечисленных факторов на потери металла показал, что с увеличением силы сварочного тока потери металла на разбрызгивание при изготовлении сварных конст-
рукций увеличиваются.
Априорный анализ влияния силы сварочного тока на коэффициенты наплавки и расплавления (рис.2.2) показал, что с увеличением силы сварочного тока значение коэффициента наплавки уменьшаются (кривая 1), а также в некоторых случаях при сварке короткой дугой и при небольших значениях силы сварочного тока зависимость коэффициента наплавки от силы сварочного тока имеет вид (кривая 2). Небольшое увеличение коэффициента наплавки с увеличением тока, которое может иметь место при сварке короткой дугой и малых значениях силы сварочного тока, связано с коротким замыканием крупными каплями жидкого металла межэлектродного промежутка и соответственно с взрывным испарением жидкого металла
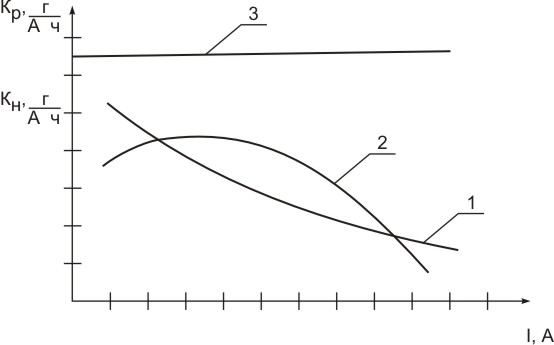
Рис.2.2. Влияние вилы сварочного тока на значение коэффициентов наплавки и расплавления Оценки, проведенные одним из авторов данной работы, показали, что имеет место незначительное увеличение коэффициента расплавления с увеличением силы сварочного тока (кривая 3), которым можно пренебречь. 2.4. Порядок проведения экспериментальных исследований
Исследовать влияние силы сварочного тока на величину коэф-
фициентов наплавки Кн и расплавления Кр для электродов с толстым (или средним покрытием) в диапазоне от 100…200 А.
Провести исследования влияния силы тока на значения коэффициента наплавки и расплавления при 5 различных её значениях в указанном диапазоне.
Перед проведением опытов пластинки взвесить на электрических весах, измерить диаметр и длину электрода. Установить электрод в электродержатель. Во время наплавки электродного металла на стальную пластинку фиксируют силу тока и время непрерывного горения дуги в секундах. После наплавки валика металла на пластинку очистить её металлической щеткой от шлаковой корки и вторично взвесить, а также измерить оставшуюся длину электрода после наплавки металла на пластинку.
На каждом токе провести три параллельных опыта. Результаты экспериментальных исследований записывают в таблицу 2.1.
Таблица 2.1.
Условия проведения экспериментов и результаты исследований
I,
А
| Gдн, г
| Gпн, г
| Gн,
Г
| Lд,
Мм
| Lп,
мм
| Gр,
Г
| Кн,
г/(Ач)
| Кр,
г/(Ач)
| Кп,
%
| 1
| 2
| 3
| 4
| 5
| 6
| 7
| 8
| 9
| 10
| I1
|
|
|
|
|
|
|
|
|
| I1
|
|
|
|
|
|
|
|
|
| I1
|
|
|
|
|
|
|
|
|
| I2
|
|
|
|
|
|
|
|
|
| I2
|
|
|
|
|
|
|
|
|
| I2
|
|
|
|
|
|
|
|
|
| I3
|
|
|
|
|
|
|
|
|
| I3
|
|
|
|
|
|
|
|
|
| I3
|
|
|
|
|
|
|
|
|
| I4
|
|
|
|
|
|
|
|
|
| I4
|
|
|
|
|
|
|
|
|
| I4
|
|
|
|
|
|
|
|
|
| I5
|
|
|
|
|
|
|
|
|
| I5
|
|
|
|
|
|
|
|
|
| I5
|
|
|
|
|
|
|
|
|
|
По результатам опытов рассчитывают производительность сварки G, коэффициенты наплавки Кн, расплавления Кр и потерь Кп по формулам
; 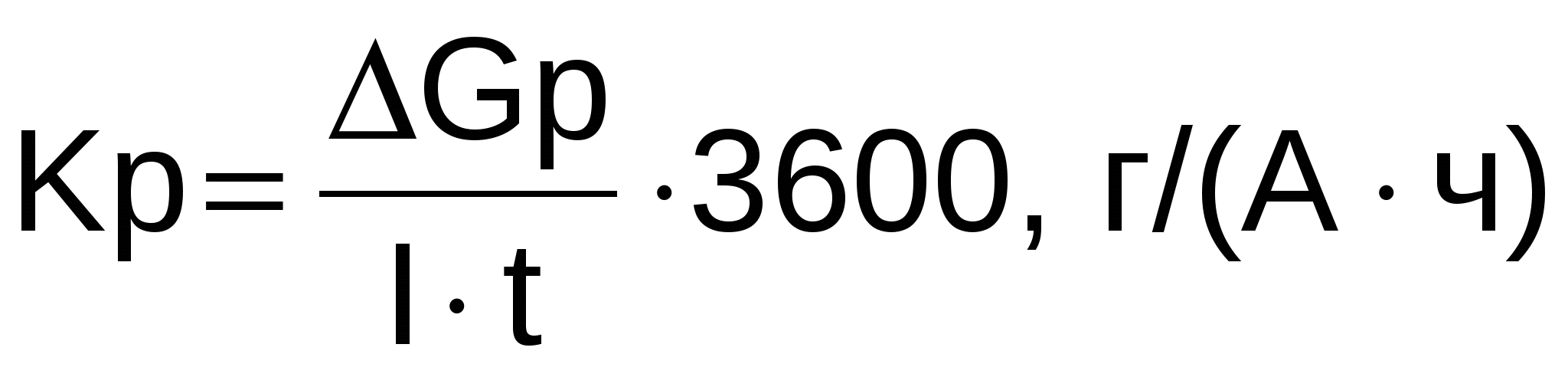
; G = Kн I, г/ч
2.5. Построение математической модели Зависимость коэффициента наплавки Кн от силы тока I описывается математической моделью
Кн = А2 I2 + A1I2 + A0 (2.14)
где А2 , А1,А0 - коэффициенты математической модели.
Для построения математической модели (2.14) используется метод наименьших квадратов с обязательной проверкой однородности дисперсий по критерию Кочрена и проверкой однородности математической экспериментальным данным. Порядок расчета математической модели на компьютере
Порядок расчета математической модели на компьютере
Исходные данные записываются в текстовый файл dan2.txt в бесформатном виде в следующем порядке: 2 3 5 90.09 0.790 2.0 120.0 135.0 150.0 170.0 200.0 7.0 7.1 7.0 7.8 7.7 7.9 8.0 8.0 8.1 6.4 6.3 6.2 5.5 5.4 5.3, где 2 - порядок степенной функции; 3 - число параллельных опытов; 5 - число экспериментальных точек; 90.09 - критерий Фишера; 0.790 - критерий Кочрена, 2 - число степеней свободы дисперсии неадекватности; 120.0, 135.0, 150.0, 170.0, 200.0 - силы сварочного тока; 7.0, 7.1, 7.0 – экспериментально найденные коэффициенты наплавки, соответствующие силе тока I = 120 А; 7.8, 7.7, 7.9 - коэффициенты наплавки, соответствующие силе тока I = 135 А; далее соответственно вводятся значения коэффициентов наплавки для токов 150 А, 170 А, 200 А.
После ввода исходных данных в файл dan2.txt необходимо их сохранить. Для расчета математической модели необходимо установить курсор на исполняемый файл a1.exe и нажать на клавишу Enter; после этого производится расчет математической модели.
Результаты расчета математической модели записываются в текстовый файл rez.txt. Для просмотра и печати результатов расчета математической модели необходимо открыть файл rez.txt .
На рис.1.21. приведен пример листинга расчета математической модели зависимости коэффициентов наплавки от силы сварочного тока,
ИСХОДНЫЕ ДАННЫЕ
120,000 135,000 150,000 180,000 200,000 5,700 5,500
5,6000 5,7000 5,900 6,100 6,200 6,300 6,100
5,9000 5,7000 5,900 5,500 5,600 5,400
Расчет дисперсии воспроизводимости
Лабораторная работа 2
Кафедра технологии материалов
Решение матричного уравнения A*B=C
A(J)
-.356264E-03
.113120E+00
-.284005E+01 X(I) YM(I) YT(I)
120.00 .560000E+01 .560419E+01
135.00 .590000E+01 .593829E+01
150.00 .620000E+01 .597866E+01
180.00 .590000E+01 .597866E+01
200.00 .556667E+01 .553346E+01
Проверка адекватности математической модели
Математическая модель адекватна Рис.2.1. Листинг расчета математической модели зависимости коэффициента наплавки от силы сварочного тока
Kр Kн
Рис. 2.2. Зависимость коэффициентов наплавки Кн и расплавления от силы сварочного тока I
н
легкоионизирующим элементом (компонентом) называется такой элемент, который имеет маленький потенциал ионизации
100> |
|
|