Расчёт. Министерство высшего образования науки рф федеральное государственное бюджетное образовательное учреждение высшего образования
![]()
|
Министерство высшего образования науки РФФедеральное государственное бюджетное образовательное учреждениевысшего образования«Магнитогорский государственный технический университетим. Г.И. Носова»Кафедра металлургии и химических технологийРасчеты Углевосстановительного процесса получения силикомарганца марки МнС22 Разработал: Студент группы ММБ-19-1 Шинкарук Б.Б. Проверил: Профессор кафедры металлургии и химических технологий Бигеев В.А. Магнитогорск2022 Исходные данные для расчета Расчет шихты приведен для выплавки силикомарганца марки МнС22. Расчет производится на 100 кг рудной части шихты (агломерата). Химический состав силикомарганца, %:
Состав коксика, %: зола – 10,3; сера – 1,6; летучие вещества – 1,7; углерод – 85,2. В электродной массе содержится С = 77 %. Таблица 1 Химический состав шихтовых материалов
Таблица 2 Распределение элементов между продуктами плавки
Определение содержания элементов в сплаве по балансовым уравнениям Уравнение в общем виде на 100 кг агломерата% Qр · <Э> · ηЭ = [Э]· QMe, где Qр – количество руды/агломерата (100 кг); <Э> – доля элемента в сырье (руде, агломерате); ηЭ – степень перехода элемента в сплав; [Э] – доля элемента в металле; QMe – количество силикомарганца. Балансовое уравнение по марганцу: 100 · 0,38 · 0,8 = 0,653 · QMe, где 100 – количество агломерата; 0,32 – доля марганца в агломерате; 0,8 – степень перехода марганца в металл; 0,653 – доля марганца в металле; QMe – количество силикомарганца, QMe = 35,2 кг. Балансовое уравнение по фосфору при QMe = 35,2 кг: 100 · 0,0473 · 0,7 = 0,033 · QMe, 100 · 0,0473 · 0,7 = 0,033, где 0,000473 – доля фосфора в агломерате; 0,7 – степень перехода фосфора в металл. В 35,2 кг металла находится 0,033 кг фосфора, содержание фосфора в силикомарганце 0,07 %, то есть ниже допустимой нормы (0,6 %). Расчет количества необходимого углерода на восстановление марганца Mn3O4 + C = 3MnO + CO Количества необходимого углерода на восстановление марганца ![]() Всего шихтовыми материалами вносится MnO ![]() По реакции MnO+C=Mn+CO Требуется углерода: ![]() Всего требуется углерода на восстановление марганца ![]() ![]() Количество марганца, переходящего в металл: ![]() Количество марганца, переходящего в шлак: ![]() Расчет количества углерода на восстановление кремния Вносится кремнезема агломератом ![]() где 0,232 – доля кремнезема в агломерате. Количество кремния в силикомарганце (23,7 %) ![]() Для получения сплава требуется кремнезем ![]() где 0,53 – доля перехода кремния в сплав; 60 и 28 – молярная масса SiO2 и Si соответственно. Необходимо дополнительно внести кремнезема ![]() или в пересчете на кварцит: 10,52*( ![]() где 0,97 − доля кремнезема в кварците. На восстановление кремнезема потребуется углерода по реакции SiO2 + 2C = Si + 2CO ![]() где 0,07 − доля кремния, теряемого с колошниковыми газами. Переходит в шлак кремнезема 33,72* 0,4 = 13,49 кг где 0,4 − доля кремнезема, переходящего в шлак. Расчет количества углерода на восстановление железа Количество углерода на восстановление Fe2O3 по реакции Fe2O3 + С = 2FeO + CO ![]() где 0,113 – доля Fe2O3 в агломерате; 12 и 160 – молярная масса углерода и Fe2O3 соответственно. Всего вносится FeO агломератом ![]() Потребуется углерода на восстановление FeO по реакции FeO + С = Fe + CO ![]() где 0,95 – доля железа, переходящего в металл; 12 и 72 – молярная масса углерода и FeO соответственно. Количество железа, переходящего в сплав: ![]() В шлак переходит FeO 5,88 * 0,05 = 0,294 кг где 0,05 – доля FeO, переходящего в шлак При выплавке силикомарганца на 1 т сплава расходуется около 1,2 кг железа из арматуры, следовательно, на 35,2 кг сплава расходуется 0,05 кг арматуры. Всего переходит железа в силикомарганец 4,54 + 0,05 = 4,59 кг. Всего необходимо углерода на восстановление железа |
SiO + 2С = Si + 2СO | 1,0116 кг |
Fe2O3 + 3C = 2Fе + 3CO | 0,506 кг |
P2O5 + 5С = 2P + 5CO | 0,0001 кг |
MnO + С = Mn + СО | 0,0003 кг |
SO3 + 3C = S + 3CO | 0,0026 кг |
Всего | 1,511 кг |


85,2 − 1,511 = 83,688 кг,
где 85,2 – содержание углерода в коксе.
Расход сухого коксика с учетом в нем активного углерод
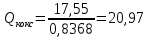
Количество золы, вносимой коксиком:
20,97 * 0,103 = 2,16 кг
При расчете количества и состава шлака не учитывались поступления компонентов из электродной массы в связи с малым их количеством (0,03–0,1 %)
Таблица 3

Элемент | Поступило, кг | Всего | ||
из шихты | из золы коксика | кг | % | |
Mn | 29,97 | 0,01 | 29,99 | 68,21 |
Si | 8,34 | 0,22 | 8,56 | 19,48 |
Fe | 4,59 | 0,33 | 4,92 | 11,2 |
P | 0,13 | 0,0045 | 0,13 | 0,3 |
C | 0,35 | − | 0,35 | 0,8 |
S | 0,000064 | 0,00043 | 0,00043 | 0,00098 |
Всего | 43,39 | 0,56 | 43,96 | 100,00 |

Количество и состав шлака силикомарганца
Оксид | Поступило, кг | Всего | ||
из шихты | из золы коксика | кг | % | |
Mn | 5,15 | 0,00 | 5,15 | 16,85 |
SiO2 | 11,2 | 0,36 | 11,56 | 37,79 |
FeO | 0,39 | 0,02 | 0,41 | 1,35 |
P2O5 | 0,02 | 0,00 | 0,02 | 0,06 |
Al2O3 | 3,80 | 0,57 | 4,37 | 14,29 |
CaO | 6,40 | 0,12 | 6,52 | 21,32 |
MgO | 2,50 | − | 2,50 | 8,17 |
S | 0,04 | 0,01 | 0,05 | 0,17 |
Прочие | 6,0 | 0,00 | 0,00 | 0,00 |
Всего | 35,50 | 1,08 | 30,58 | 100,0 |
Вносится серы компонентами шихты
Вносится серы агломератом:
100 ∙ 0,001 ∙ 0,4 = 0,04 кг .
Вносится серы коксиком:
20,97 ∙ 0,016 = 0,33 кг,
где 0,016 − доля серы в коксике. Вносится серы золой коксика
2,16 ∙ 0,0104 = 0,022 кг,
Всего вносится серы:
0,04 + 0,335 + 0,022 = 0,39 кг.
Потери компонентов с колошниковой пылью и печными газами
Потери с колошниковой пылью:
Марганца:

кремния:

фосфора:
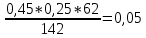
Всего: 3,64 кг
Потери с элетропечными газами:
сера в виде:

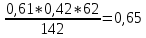
летучие кокса: 20,97 * 0,017 = 0,35 кг
Потери в виде

100 * 0,0055 = 0,55 кг
Количество и состав газовой фазы
Количество окиси углерода, образующейся при восстановлении элементов шихты:


кг

41,69 + 0,81 =42,51 кг
Состав газовой фазы

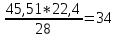

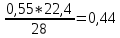

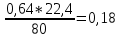
Таблица 7
Состав и количество колошникового газа | ||||
Составляющие | Кг | Объем, нм3 | Объем, % | Масса, % |
СО | 42,51 | 34,01 | 94,04 | 96,36 |
СО2 | 0,55 | 0,44 | 1,22 | 1,25 |
SO3 | 0,65 | 0,18 | 0,50 | 1,47 |
H2 | 0,06 | 0,77 | 2,12 | 0,14 |
Летучие | 0,35 | 0,77 | 2,12 | 0,79 |
Всего | 44,12 | 36,16 | 100,00 | 100,00 |
Состав и количество образующегося газа колошникового газа
Таблица 8
Баланс по железу
Приход | Расход | ||||
Поступило | кг | % | Получено | кг | % |
Марганцевый агломерат | 6,15 | 88,36 | Металл | 6,13 | 95,33 |
Кварцит | 0,39 | 5,6 | Шлак | 0,30 | 4,67 |
Электродная арматура | 0,05 | 0,72 | | | |
Зола кокса | 0,37 | 5,32 | | | |
Всего | 6,96 | 100,00 | Всего | 6,43 | 100,00 |
Таблица 9
Баланс по фосфору
Приход | Расход | ||||
Поступило | кг | % | Получено | кг | % |
Марганцевый агломерат Зола коксика | 3 0,0006 | 99,98 0,02 | Металл Шлак Улет | 0,1404 0,007 0,0532 | 69,99 3,5 26,52 |
Всего | 3,0006 | 100 | Всего | 0,2006 | 100 |
Таблица 10
Баланс по углероду
Приход | Расход | ||||
Поступило | кг | % | Получено | кг | % |
Коксик Электродная масса | 16,84 0,75 | 95,64 4,35 | На науглероживание Окисление до СО (q' + q" ) c c | 0,63 17,02 | 3,57 96,43 |
Всего | 17,23 | 100 | Всего | 17,65 | 100 |
На основании сводного материального баланса определяется расход шихтовых материалов на натуральную и базовую (сумма кремния и марганца − 62 %) тонну силикомарганца
Таблица 12
Расход шихтовых материалов на 1 т силикомарганца
Материал | Расход на 1 т, кг | |
натуральную | базовую | |
Марганцевый агломерат | 2458,8 | 2429,2 |
Кварцит | 27,8 | 27,5 |
Коксик | 504,5 | 498,4 |
Электродная масса | 17,5 | 17,3 |
Расчет количества продуктов плавки на одну натуральную тонну силикомарганца
Металл:
Шлак:
Колошниковый газ:
Улет элементов:
35,2 ∙ 24,588 = 865,5 кг.
35,50 ∙ 24,588 = 872,87 кг.
38,33 ∙ 24,588 = 942,7 кг.
3,5 ∙ 24,588 = 86,1 кг,
где 24,588 – коэффициент пересчета на одну натуральную т. МнС18LP

PAGE 7