Разработка технологического процесса сборки и сварки опоры
![]()
|
1 2 17 % в общем ее объеме, связано с созданием более совершенного оборудования. Учитывая мировые тенденции расширения области применения прогрессивных ресурсосберегающих технологий можно предположить, что доля лазерной технологии в сварочном производстве в предстоящее десятилетие существенно увеличится и достигнет 6 – 8 % общего объема сварочных работ. |
Сортамент | Размер | в | T | 5 | | KCU |
- | Мм | МПа | МПа | % | % | кДж / м2 |
ГОСТ 19282-73 | 4 | 450 | 310 | 21 | | |
Таблица 2 - Химический состав в % стали 09Г2 по ГОСТ 19281 - 89
C | Si | Mn | Ni | S | P | Cr | N | Cu | As |
до 0.12 | 0.17 - 0.37 | 1.4 - 1.8 | до 0.3 | до 0.04 | до 0.035 | до 0.3 | до 0.008 | до 0.3 | до 0.08 |
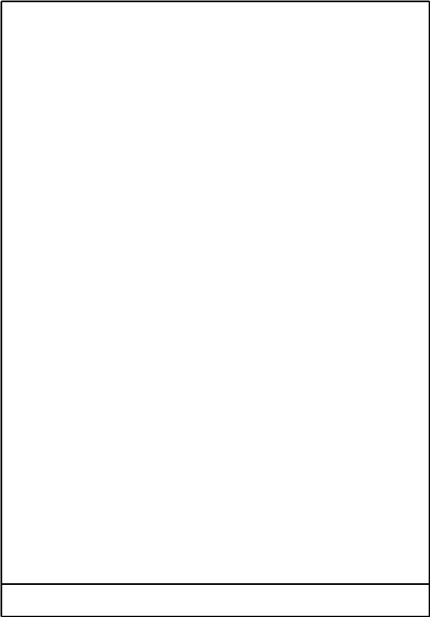
Свариваемость | без ограничений |
Флокеночувствительность | не чувствительна |
Склонность к отпускной хрупкости | не склонна |
Технические условия на сборку и сварку металлоконструкций
Настоящие технические условия распространяются на металлоконструкции и составляются на основании СНиП II-3 и СНиП II-23-81.
1.3.1 Требования к сварным конструкциям
1.3.1.1 Конструкции должны быть изготовлены в соответствии с требованиями настоящего стандарта, стандартов или технических условий на изделия конкретных видов, типов и марок по рабочей документации, утвержденной разработчиком и принятой к производству предприятием-изготовителем.
Рабочая документация на конструкции должна разрабатываться в соответствии с действующими в этой области строительными нормами и стандартами. Технология производства должна регламентироваться технологической документацией, утвержденной в установленном на предприятии-изготовителе порядке.
1.3.1.2 Конструкции должны удовлетворять установленным при проектировании требованиям по несущей способности (прочности и жесткости) и в случаях, предусмотренных стандартами или техническими условиями, выдерживать контрольные нагрузки при испытаниях нагружением.
В рабочих чертежах изделий должны быть установлены схемы загружения, контрольные разрушающие нагрузки, контрольные нагрузки по жесткости и контрольный прогиб.
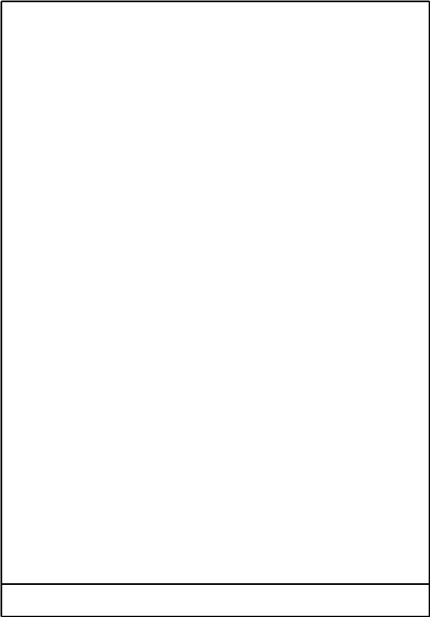
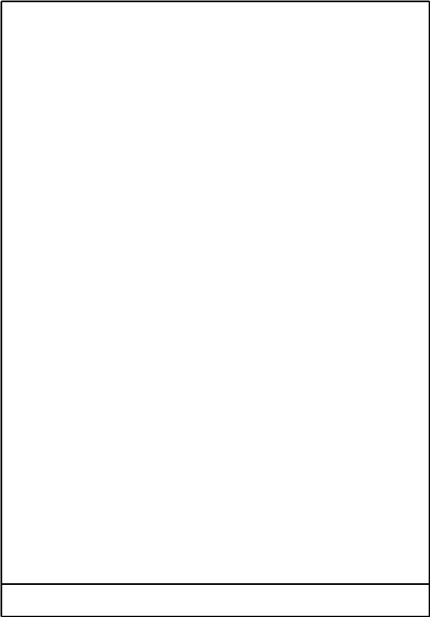
1.3.6.13 При вынужденном перерыве в работе сварку разрешается возобновлять после очистки концевого участка шва длиной 50 мм и кратера от шлака; этот участок и кратер следует полностью перекрыть швом.
Кратеры на концах швов должны быть тщательно заварены и зачищены.
1.3.6.14 Начало и конец стыкового шва, а также выполняемого автоматической сваркой углового шва в тавровом соединении, как правило, должны выводиться за пределы свариваемых деталей на выводные планки. Эти планки после сварки удаляются кислотной резкой, а места их установки зачищаются шлифмашинкой.
1.3.6.20 Швы сварных соединений и конструкции по окончании сварки должны быть очищены от шлака, брызг и натеков металла. Приваренные сборочные приспособления надлежит удалять без применения ударных воздействий и повреждения основного металла, а места их приварки зачищать до основного металла с удалением всех дефектов.
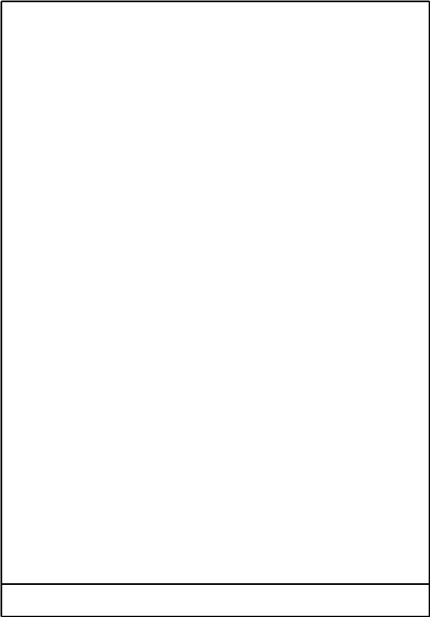
Контроль качества содержит две последовательно осуществляемые группы мероприятий: операционный контроль, приемочный контроль (входной контроль рассмотрен в разделе 1.3.6.24 Контроль за соблюдением требований к технологии и технике сварки должен осуществляться на соответствие требованиям технологических инструкций и технологических карт, разработанных на предприятии, в которых должна учитываться специфика используемого оборудования и контрольно-измерительных приборов.
1.3.6.25 Приемочный контроль качества швов сварных соединений осуществляется следующими основными методами, применяемыми в различном сочетании в зависимости от назначения конструкции, условий эксплуатации и степени ответственности: внешним осмотром и измерением, ультразвуком, радиографическим, капиллярным, пузырьковым, механическими испытаниями контрольных образцов и др.
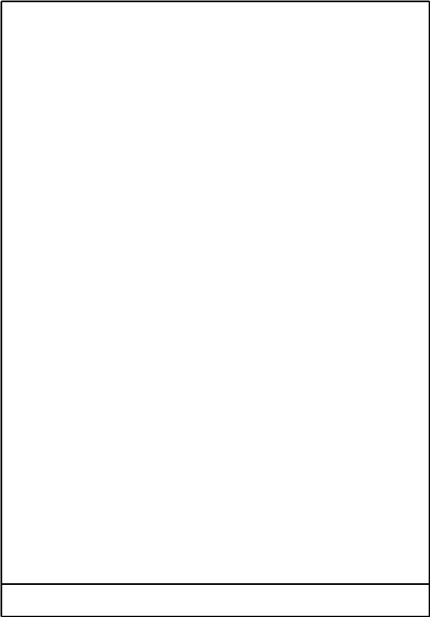
СПЕЦИАЛЬНАЯ ЧАСТЬ
Выбор и обоснование способа сварки
При выборе способа сварки необходимо учитывать следующие факторы:
1) материал и сортамент металла заготовок
2) химический состав материалов, определяющий его технологическую свариваемость
3) толщина металла
4) конструктивные особенности изделия с учетом его сложности, Массы, габаритных размеров, типов соединения.
5) производительность способа сварки
6) годовой объем выпуска и типа производства
Любое сварное соединение конструкции может выполняться множеством взаимозаменяемых способов сварки, каждый из которых обладает своими технологическими особенностями, техническими и экономическими показателями. Особенностью в работе технологического процесса является проработка нескольких вариантов технологического процесса с обязательным обоснованием выбранного решения структурно - логическая схема выбора способа сварки предусматривает многовариантный поиск проектных решений
С учетом вышеизложенных факторов для изготовления опоры выбран способ сварки в среде защитного газа, так как в настоящем проекте сварные швы имеют разную длину от нескольких миллиметров до нескольких сантиметров. Конфигурация швов позволяет успешно выполнять с применением механизированной полуавтоматической сварки плавящимся электродом в защитных газах в качестве защитных газов применяется евро смесь - 80%Ar+20%СО2 .
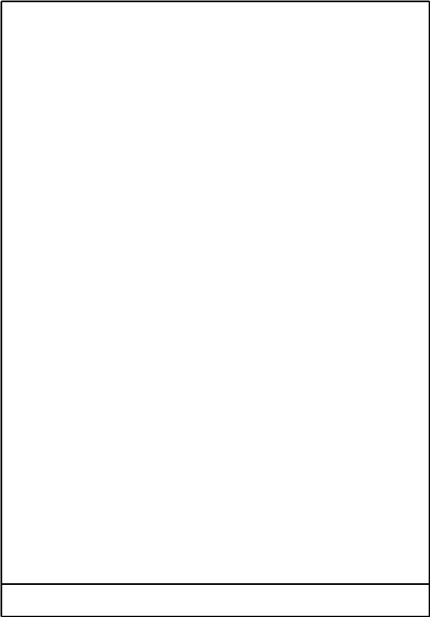
К особенностям дуговой сварки в защитных газах относится:
- небольшие деформации,
- высокая концентрация дуги,
- малая зона термического влияния,
- доступность наблюдения за процессом,
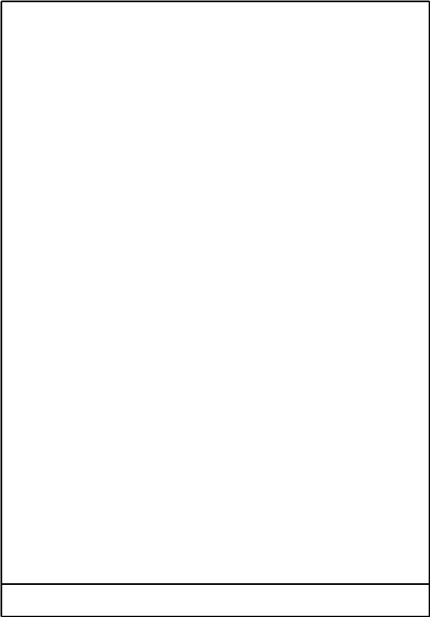
- простота механизации процесса,
- возможность сварки металла любой толщины,
- высокая защита расплавленного металла,
- отсутствие необходимости отчистки сварных швов от шлака,
- при полуавтоматической сварке возможность сварки швов любой протяженности и конфигурации.
Данный способ сварки является более экономичным, обеспечивает достаточно высокое качество швов. За счет уменьшения сил поверхностного натяжения расплавленного металла под действием кислорода стабилизируется процесс переноса металла, уменьшается разбрызгивание, улучшается внешний вид и формирование шва.
Одним из недостатков полуавтоматической сварки в среде углекислых газов является разбрызгивание электродного металла, что требует введение в технологический процесс дополнительной операции - зачистка металла от брызг после сварки.
Снизить разбрызгивание можно следующими способами:
1) использование для сварки проволоки малого диаметра,
2) использование в качестве защитного газа смеси из аргона и углекислого газа,
3) использовать в качестве источников дуги сварочные выпрямители с регулируемым углом наклона внешней его характеристики,
4) применение активизированной сварочной проволоки сплошного сечения.
Таким образом, с целью уменьшения разбрызгивания и для лучшего формирования шва принята сварка в смеси газов : 80% Ar и 20% CО2
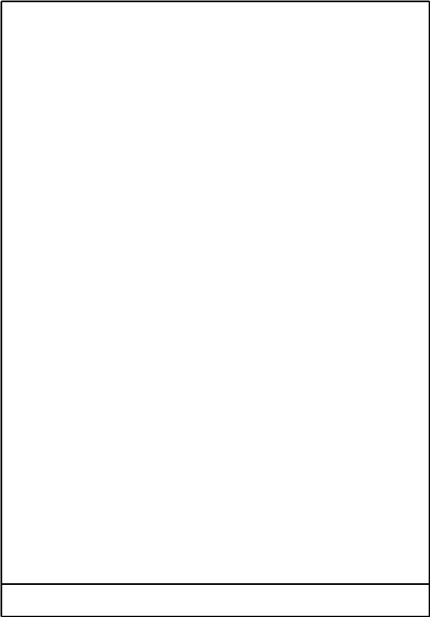
Сварочные материалы при сварке опоры принимаются исходя из способа сварки.
В данном случае для сварки изделия выбрана сварочная проволока диаметром 1,2 мм марки Св-08Г2С по ГОСТ 2246-70, так как она наиболее оптимально подходит к рассчитанным режимам сварки
Проволока сварочная диаметром 1,2 мм, марки Св-08Г2С, предназначенная для сварки с омеднённой поверхностью. Такая проволока, как и многие другие, должна поставляться или с омеднённой поверхностью, или с не омеднённой поверхностью, но с удалением следов мыльной смазки. При этом вид поверхности поставляемой проволоки устанавливается изготовителем, если в заказе не оговорена поставка проволоки с омеднённой поверхностью.
Проволока должна быть принята техническим контролем предприятия - изготовителя. Изготовитель должен гарантировать соответствие поставляемой проволоки требованиям ГОСТ 2246-70. В таблице ниже приведён химический состав проволоки Св-08Г2С.
Таблица 4 - Химический состав проволоки Св-08Г2С по ГОСТ 2246-70
C | Si | Mn | Cr | Ni | S | P |
0,05 - 0,11 | 0,7 - 0,95 | 1,8 - 2,1 | 0,2 | 0,25 | 0,025 | 0,03 |
Так же наиболее оптимально подходит к рассчитанным режимам сварки евросмесь - 80%Ar+20%СО2 - Смесь газовая ТУ 2114-001-87144354-2012 Ar/20% CO2/80% Свидетельство НАКС № АЦСМ-12-01610
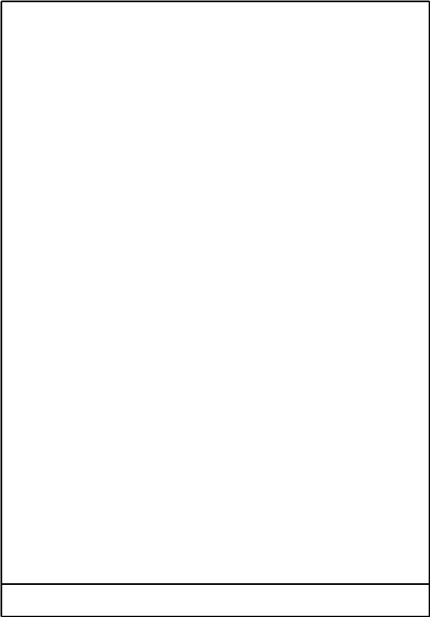
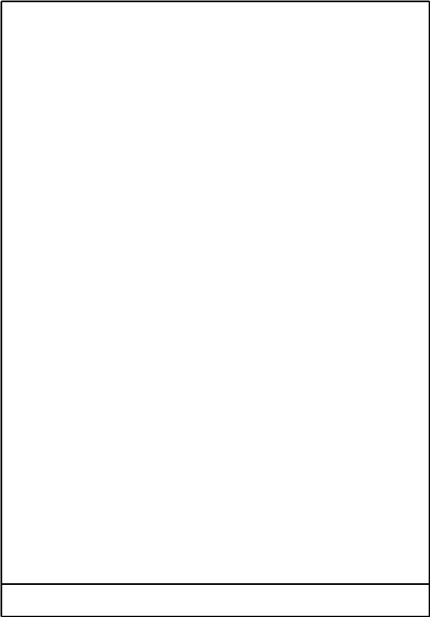
Показатели | Сорт в % | |
Высший | Первый | |
Объемная доля аргона | 99,99 | 99,987 |
Объемная доля кислорода | 0,0007 | 0,002 |
Объемная доля азота | 0,005 | 0,07 |
Водяные пары | 0,007 | 0,07 |
Углекислый газ | 0,0005 | 0,007 |
Таблица 6 - Химический состав СО2 по ГОСТ 8050-85
Показатели | Сорт в % | |
Высший | Первый | |
Объемная доля CO2 | 99,8 | 99,5 |
Объемная масса примесей | 0,7 | |
Массовая концентрация водяных паров | < 0,037 | 0,037 |
Аргон газообразный сорт высший (99,993%);CO2 — двуокись углерода газообразная сорт высший (99,8%).Поставляется: в стальных баллонах под давлением 150 кгс/см2; в моноблоках БМКБ — под давлением 200 кгс/см2.
Баллоны окрашены в черный цвет и имеют белую надпись «смесь Ar-CO2».
Область применения этой смеси :
- полуавтоматическая сварка и наплавка обычных конструкционных сталей;
- полуавтоматическая сварка нержавеющих сталей с порошковой проволокой;
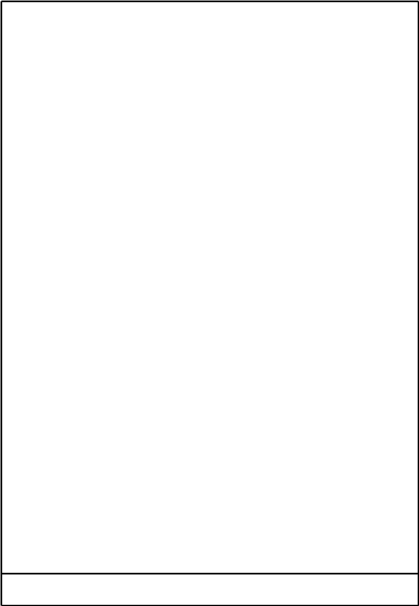
Опора сваривается с применением полуавтоматической сварки в среде углекислого газа и аргона, где основными параметрами являются:
1) диаметр электрода, мм.
2) величина сварочного тока, А
3) напряжение на дуге, В
4) скорость сварки, м/ч
5) расход защитного газа, л/мин
7) вылет электрода, мм
Режим сварки для таврового соединения Т1 ГОСТ 14771 - 76
Таблица 7 - Режимы прихваток
ГОСТ 14771-76 | Количество слоев | Катет | Iсв, А | Uг, А | Vсв | Vп.п. | Вылет электрода | Расход защитного газа |
прихватки | 1 | 3 | 110-120 | 20-22 | 22 | 210 | 16-18 | 12-14 |
Согласно ГОСТ 14771 - 76 рассчитываются режимы сварки для таврового соединения Т1 с толщиной металла 10 мм и катетом 6 мм
- диаметр сварочной проволоки - dэ = 1,2 мм.
- сила сварочного тока Iсв = 200 А
- коэффициент наплавления

Определяется площадь наплавленного металла:


Скорость сварки определяется по формуле:
Vсв =

Vсв =
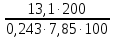
Определяется скорость подачи проволоки:
Vп.п =

Vп.п =
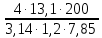
Масса, кг | 85 |
Размеры, мм | 610х360х820 |
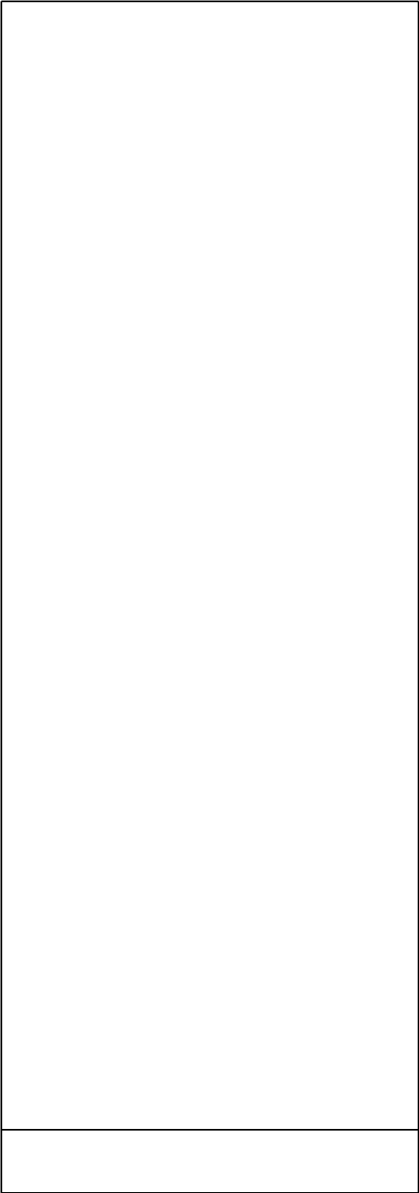
Технологическая карта сборки и сварки опоры
№ Операц. | Наименование и содержание операции | Оборудование, приспособления, инструменты |
1. | Подготовительная Ознакомиться с чертежем и техпроцессом на сборку и сварку опоры. Подготовить рабрчее место, чтобы оно соответствовало габаритным размерам изделия. | Чертеж, техпроцесс на сварку опоры |
2 | Перемещение Подать детали на рабочее место, соблюдая схемы строповок. | Мостовой кран г/п 5тс |
3. | Слесарная 1 Укомплектовать узел деталями согласно спецификации чертежа. Детали должны быть замаркированы и приняты ОТК. | |
4. | Сверлильная 1 Разметить и просверлить 4отв. диаметром 28,5мм в плите (поз.5) по чертежу. | 2Н170 |
5. | Слесарная 2 Разметить плиту (поз.5) под установку листа (поз.7) | Рулетка ГОСТ 7502-80 Чертилка ИН-036 |
![]() | Слесарная 3 Зачистить свариваемые кромки и прилегающие зоны металла шириной 10-15мм на листе (поз.7) и в местах его установки на листе (поз.5) до чистого металла. | Шлиф.маш ГОСТ 12634-87 Шлиф.кругПП14А50, Очки защ. 02-76У |
9. | Слесарная 5 Зачистить свариваемые кромки и прилегающие зоны металла шириной 10-15мм на листах (поз.3,4,6,) и в местах его установки до чистого металла. | Шлиф.маш ГОСТ 12634-87 Шлиф.кругПП14А50, Очки защ. 02-76У |
10. | Сборка 2 Установить лист (поз.3,4,6) на плиту (поз. 5) по разметке согласно чертежу по угольнику. Прихватить полуавтомат. эл.сваркой. Св-08Г2С; диам. 1,2мм;L=10-15мм, длина - 200-250мм. Зачистить прихватки. Осмотреть. Прихватки не должны иметь дефектов: пор, наплывов, подрезов и др. | Молоток ГОСТ 2310-87, Угольник Зубило ГОСТ7211-82, Эл.держатель 14651-87, Щиток ГОСТ 12.4.035-87, |
11. | Сварка 1 Заварить собранный узел полуавтомат. эл.сваркой. Св-08Г2С; диам. -1,2мм;L=10-15мм, длина -200-250мм. Оббить шлак, осмотреть. При сварке кантовать краном. Выполнить схемы строповок. | Эл.держатель 14651-87, Щиток ГОСТ 12.4.035-87, Мостовой кран г/п 5тс Lincoln Electric Invertec CV/CC 500 |
![]() | Слесарная 6 Зачистить брызги после сварки, а также сварные швы и околошовные зоны на ширину не менее 20мм по обе стороны сварного шва до чистого металла. | Шлиф.маш ГОСТ 12634-87 Шлиф.кругПП14А50, Очки защитные 02-76У |
13. | Сборка 3 Установить лапку (поз.2), совместив отверстия на лапке и листе (поз.6). Поставить болты (поз.8), шайбы (поз.9) , навернуть гайки (поз.10). | Гаечн. ключ ГОСТ 2839-80 |
14 | Сварка 2 Заварить собранный узел полуавтомат. эл.сваркой. Св-08Г2С; диам. -1,2мм; Оббить шлак, осмотреть. При сварке изделие кантовать краном. Выполнить схемы строповок. | Эл.держатель ГОСТ14651-87, Щиток ГОСТ 12.4.035-87, Lincoln Electric Invertec CV/CC 500 Мостовой кран г/п 5тс |
15. | Сборка 4 Зачистить свариваемые кромки и прилегающие зоны металла шириной 10-15мм на листах (поз.7) и лист (поз. 1)в местах его установки до чистого металла. | Шлиф.маш ГОСТ 12634-87 Шлиф.кругПП14А50, Очки защ. 02-76У |
16. | Сварка 3 Заварить собранный узел полуавтомат. эл.сваркой. Св-08Г2С; диам. -1,2мм;L=10-15мм, длина -200-250мм. Оббить шлак, осмотреть. | Эл.держатель 14651-87, Щиток ГОСТ 12.4.035-87, Мостовой кран г/п 5тс Lincoln Electric Invertec CV/CC 500 |
17. | Слесарная 7 Зачистить брызги после сварки, а также сварные швы и околошовные зоны на ширину 20мм по обе стороны сварного шва до чистого металла. | Шлиф.маш ГОСТ 12634-87 Шлиф.кругПП14А50, Очки защ. 02-76У |
18. | | |
![]() | Контроль Проверить правильность сборки опоры из деталей (поз.1,2,3,4,5,6,7,) и подготовку под сварку согласно чертежа. Проверить качество сварки внешним осмотром, ультразвуковым измерением. Проверить подготовку сварочных материалов в соответствии с инструкцией. Проверить зазор между листами (поз. 1 и 7) Проверить правильность нанесения маркировки. | Рулетка ГОСТ 7502-80, Угольник ШС-2, Катетомер. Щуп ГОСТ 882-85 Маркеры |
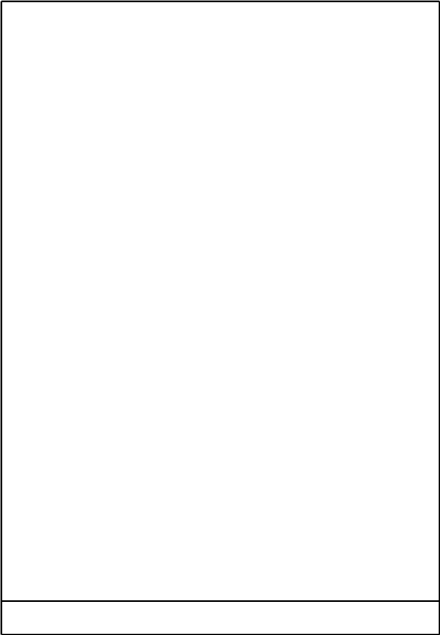
Выбор методов контроля качества сварки
ГОСТ 18353-79 "Контроль неразрушающий. Классификация видов и методов"
Дефекты сварных швов и причины их возникновения
Отсутствие дефектов соединений при сварке металлов плавлением - единственная гарантия надежности сварных соединений. Дефекты сварных швов уменьшают прочность и эксплуатационную надежность сварных соединений и могут привести к разрушению всей конструкции. Дефекты сварных соединений подразделяются на шесть групп:
трещины;
полости, поры, свищи, усадочные раковины, кратеры;
твердые включения;
несплавления и непровары;
нарушения формы шва (подрезы, усадочные канавки, превышения выпуклости, превышения проплава, наплавы, смещения, натеки, прожоги);
прочие дефекты.
Причинами возникновения дефектов сварных швов являются нарушения технологического процесса при подготовке, сборке, сварке, термообработке соединяемых узлов, а также небрежностью и низкой квалификацией сварщика.
Классификация дефектов приведена в межгосударственном стандарте ГОСТ 30242-97 «Дефекты соединений при сварке металлов плавлением. Классификация, обозначения и определения».
При сварке опоры были выбраны следующие методы контроля:

1.Визуальный контроль:
Визуальный контроль качества или ВИК контроль является первичным методом неразрушающей диагностики. Внешний осмотр изделия может проводиться как при помощи простейших измерительных инструментов, так и с использованием специальных оптических систем предназначенных для осуществления контроль качества сварных швов и основного металла, соединений и наплавок, в процессе проведения подготовительных и сварочных работ, и в случае выявления дефектов.
Он основан на получении первичной информации об объекте при визуальном наблюдении или с помощью оптических приборов.Визуальный контроль, как правило, производится невооруженным глазом или с использованием увеличительных луп 2х до 7х. В сомнительных случаях и при техдиагностировании допускается увеличение до 20х. Визуальный контроль выполняется до проведения других методов контроля.
Только после того, как был проведен ВИК и устранены недопустимые дефекты, сварные соединения могут быть подвергнуты контролю любыми другими методами, например, рентгеновскому или ультразвуковому контролю.
Всё это позволяет использовать визуальный контроль качества, как высокоэффективный инструмент для выявления и предупреждения дефектов на разных стадиях
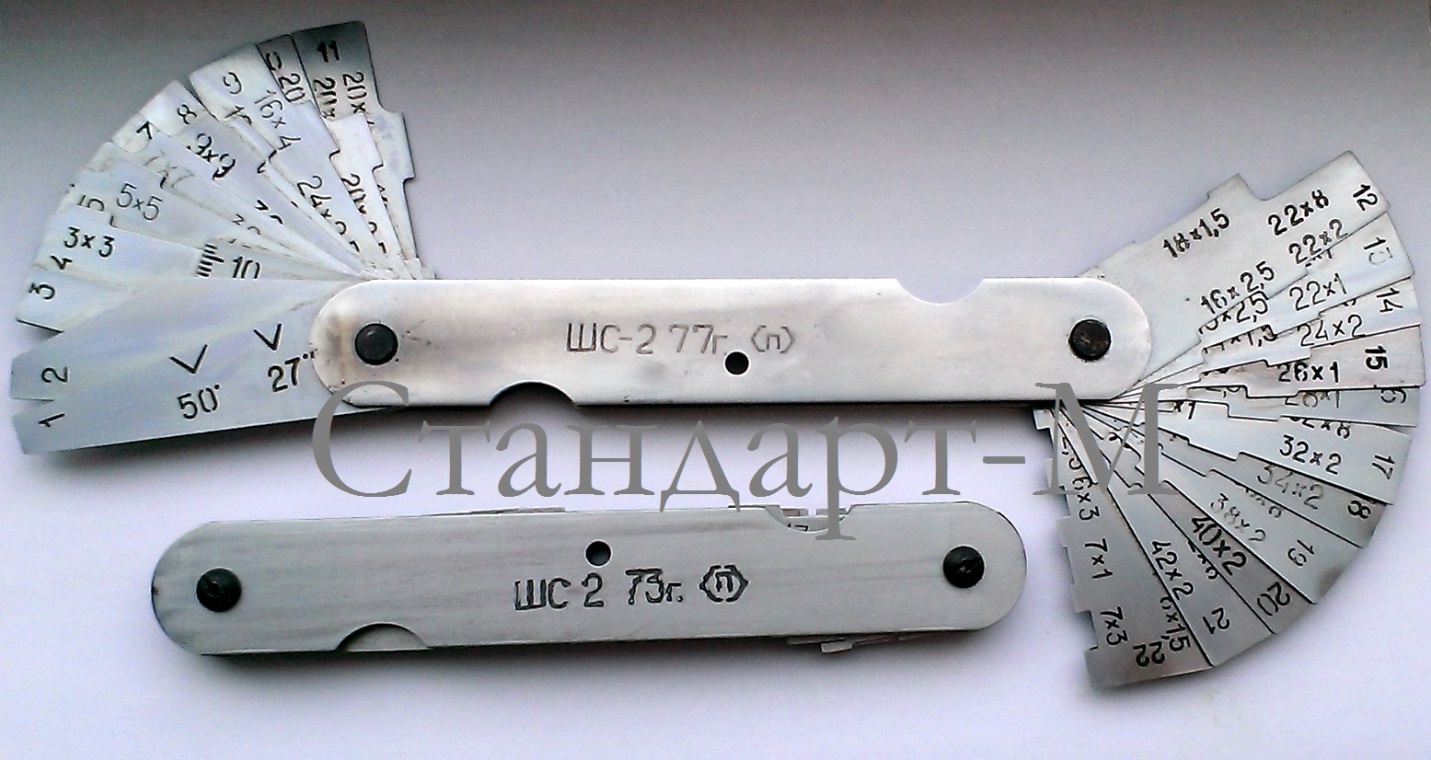
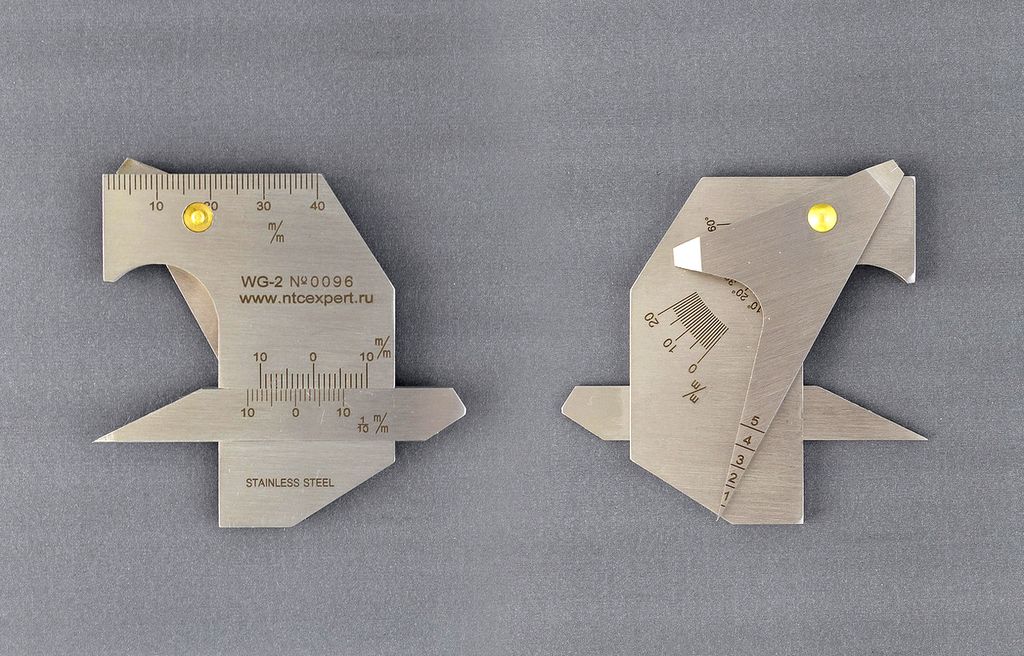
Ультразвуковой контроль:
Суть ультразвукового метода заключается в излучении в изделие и специального оборудования – ультразвукового дефектоскопа и пьезоэлектропреобразователя (-ей) и дальнейшем анализе полученных данных с целью определения наличия дефектов, а также их эквивалентного размера, формы (объемный/плоскостной), вида (точечный/протяженный), глубины залегания и пр.
Параметры выявленных дефектов определяются с помощью ультразвуковых дефектоскопов. Так например, п о времени распространения ультразвука в изделии (если известна скорость ультразвука скорость распространения ультразвуковых волн в различных материалах) в данном металле) определяют расстояние до дефекта, а по амплитуде отраженного импульса – его относительный размер.
Для проведения ультразвукового контроля в зависимости от конкретных условий (марки материала, его толщины, геометрических особенностей поверхностей контроля, минимально выявляемых размеров дефектов и др.) имеется достаточно широкий ассортимент средств контроля.
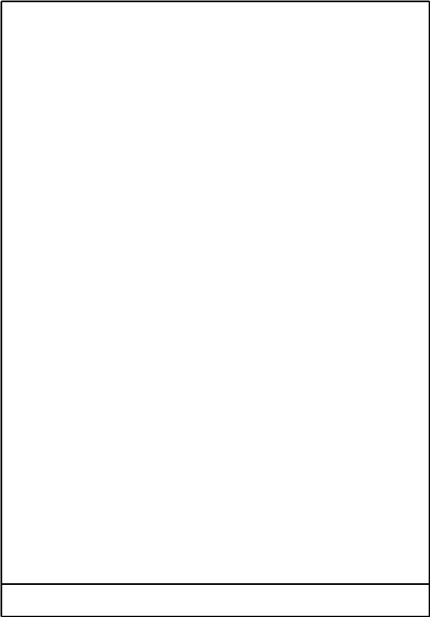
Ультразвук низких частот применяют при: работе с объектами большой толщины ( ультразвуковой контроль отливок, поковок, сварных соединений выполненных электрошлаковой сваркой); контроле металлов, имеющих крупнозернистую структуру (чугун, медь, аустенитные стали) и большое затухание – “плохо проводят ультразвук”.
- возможность проведения ультразвукового контроля (в отдельных случаях) на действующем объекте, т.е. на время проведения УЗК не требуется выведения контролируемой детали/объекта из эксплуатации.
- при проведении УЗК исследуемый объект не повреждается.
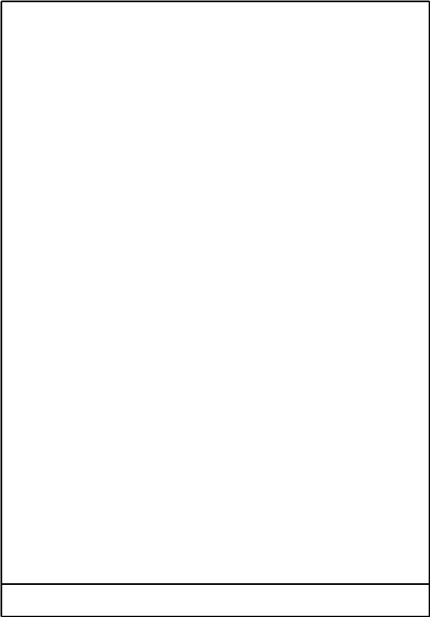
3.ОХРАНА ТРУДА И ТЕХНИКА БЕЗОПАСНОСТИ
Техника безопасности при выполнении сварочных работ
1 2