|
устройство автомобилей. Устройство автомобилей
Федеральное агентство по образованию
Государственное образовательное учреждение высшего профессионального образования
Ульяновский государственный технический университет
Энергетический факультет
Кафедра «Основы проектирования механизмов и машин»
Устройство автомобилей.
Выполнил студент группы Эд-22
Насретдинов Р.Н.
Проверил:
Садриев Р. М.
Ульяновск, 2012г
Содержание.
Двигатель…………………………………………………………………….……..3
Поршневой двигатель внутреннего сгорания…………………………..…3
Карбюраторный двигатель………………………………………………8
Инжекторный двигатель……………………………………………..….9
Принцип работы………………………………………………..9
Достоинства двигателей, оборудованных системой впрыска с микропроцессорным управлением…………………………………...….10
Недостатки………………………………………………….…11
Трансмиссия……………………………………………………………………….11
Механические трансмиссии……………………………………………….11
Гидромеханические трансмиссии…………………………………….…..12
Электромеханические трансмиссии…………………………………...….13
Сцепление…………………………………………………………………..13
Коробка передач…………………………………………………………....15
Несущая система, подвеска, колеса……………………………………………..15
Несущая система……………………………………………….………….15
Подвеска…………………………………………………………………….22
Колеса………………………………………………………………….……24
Шины…………………………………………………………………….…26
Система управления………………………………………………………………29
Список литературы………………………………………………………………………40
Двигатель.
Автомобильный двигатель — это двигатель который преобразует энергию какого-либо рода в механическую работу, совершаемую при движении автомобиля.
Наиболее распространённым типом автомобильного двигателя является поршневой двигатель внутреннего сгорания. Этот двигатель может быть карбюраторным или инжекторным, питаться различным автомобильным топливом (бензин, дизельное топливо, сжиженный нефтяной или сжатый природный газ). Но кроме этого на автомобилях могут быть установлены двигатель Стирлинга или роторно-поршневой двигатель Ванкеля, двигатели использующие энергию предварительно раскрученного маховика, энергию находящегося под высоким давлением газа, паровые двигатели, электродвигатели.
На гибридных автомобилях силовая установка комбинированная.
Поршневой двигатель — двигатель внутреннего сгорания, в котором тепловая энергия расширяющихся газов, образовавшаяся в результате сгорания топлива в замкнутом объёме, преобразуется в механическую работу поступательного движения поршня за счёт расширения рабочего тела (газообразных продуктов сгорания топлива) в цилиндре, в который вставлен поршень.
Поступательное движение поршня преобразуется во вращение коленчатого вала кривошипно-шатунным механизмом.
Поршневой двигатель внутреннего сгорания.
Поршневой двигатель внутреннего сгорания сегодня является самым распространённым тепловым двигателем. Он используется для привода средств наземного, воздушного и водного транспорта, боевой, сельскохозяйственной и строительной техники, электрогенераторов, компрессоров, водяных насосов, помп, моторизованного инструмента (бензорезок (бензо-болгарок), газонокосилок, бензопил) и прочих машин, как мобильных, так и стационарных, и производится в мире ежегодно в количестве нескольких десятков миллионов изделий
Мощность поршневых двигателей внутреннего сгорания колеблется в пределах от нескольких ватт (двигатели авиа-, мото- и судомоделей) до 75 000 кВт (судовые двигатели).
В качестве топлива в поршневых двигателях внутреннего сгорания используются:
жидкости — бензин, дизельное топливо, спирты, биодизель;
газы — сжиженный газ, природный газ, водород, газообразные продукты крекинга нефти, биогаз;
монооксид углерода, вырабатываемый в газогенераторе, входящем в состав топливной системы двигателя, из твёрдого топлива (угля, торфа, древесины).
Полный цикл работы двигателя складывается из последовательности тактов — однонаправленных поступательных ходов поршня. Различают двухтактные и четырёхтактные двигатели.
Число цилиндров в разных поршневых двигателях колеблется от 1-го до 24-х. Объём цилиндра — это произведение площади поперечного сечения цилиндра на ход поршня. Суммарный объём всех цилиндров обычно называют объёмом двигателя. По способу смесеобразования делятся:
Двигатели с внешним смесеобразованием. Воспламенение воздушно-топливной смеси может выполняться электроискровым разрядом, вырабатываемым системой зажигания (например, автомобильный Бензиновый двигатель внутреннего сгорания). Двигатели с внешним смесеобразованием могут работать на газообразном топливе (природный газ, био и другие условно-бесплатные газы);
Двигатели с внутренним смесеобразованием (воспламенение от сжатия рабочего тела). Эти двигатели, в свою очередь, подразделяются на:
Дизельные, работающие на дизельном топливе или природном газе (с добавлением 5 % дизельного топлива для обеспечения воспламенения топливной смеси). В этих двигателях сжатию подвергается только воздух, а при достижении поршнем точки максимального сжатия в камеру сгорания впрыскиваеся топливо, которое воспламеняется при контакте с воздухом, нагретым при сжатии до температуры в несколько сотен градусов Цельсия.
Компрессионные двигатели. В них, в отличие от дизельных, топливо подается вместе с воздухом (как в бензиновых двигателях). Такие двигатели требуют особого состава топлива (обычно в его основе — диэтиловый эфир) и точной регулировки степени сжатия, так как от нее зависит момент воспламенения смеси. Компрессионные двигатели используются главным образом в авиа- и автомоделях;
Калильные двигатели. Схожи по принципу действия с компрессионными, но имеют калильную свечу, накал которой поддерживается за счёт сгорания топлива на предыдущем такте.Такие двигатели также требуют особого состава топлива (обычно в его основе — метанол, касторовое масло и нитрометан). Используются главным образом в авиа- и автомоделях;
Воспламенение от горячих частей двигателя (калоризаторные), обычно — днища поршня. Приводные двигатели прокатных станов (топливо-мартеновский газ).
Двигатели с внутренним смесеобразованием имеют (как в теории, так и на практике) более высокий КПД и вращающий момент за счёт более высокой степени сжатия.
В рамках технической термодинамики работа поршневых двигателей внутреннего сгорания в зависимости от особенностей их циклограмм описывается термодинамическими циклами Отто, Дизеля, Тринклера, Аткинсона или Миллера.
Эффективный КПД поршневого ДВС не превышает 60%. Остальная тепловая энергия распределяется, в основном, между теплом выхлопных газов и нагревом конструкции двигателя. Поскольку последняя доля весьма существенна, поршневые ДВС нуждаются в системе интенсивного охлаждения. Различают системы охлаждения:
воздушные, отдающие избыточное тепло окружающему воздуху через ребристую внешнюю поверхность цилиндров; используются в двигателях сравнительно небольшой мощности (десятки л.с.), или в более мощных авиационных двигателях, работающих в быстром потоке воздуха;
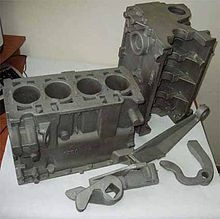
Рис.1. Блок цилиндров.
жидкостные, в которых охлаждающая жидкость (вода, масло или антифриз) прокачивается через рубашку охлаждения (каналы, созданные в стенках блока цилиндров), и затем поступает в радиатор охлаждения, в котором теплоноситель охлаждается потоком воздуха, созданным вентилятором. Иногда в жидкостных системах в качестве теплоносителя используется металлический натрий, расплавляемый теплом двигателя при его прогреве.
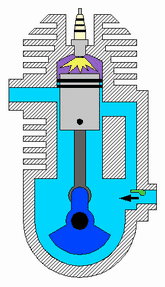
Рис.2. Зажигание смеси.
Основные параметры двигателя
С работой поршневого двигателя внутреннего сгорания связаны следующие параметры.
Верхняя мёртвая точка (в. м. т.) — крайнее верхнее положение поршня.
Нижняя мёртвая точка (н. м. т.) — крайнее нижнее положение поршня.
Радиус кривошипа — расстояние от оси коренной шейки коленчатого вала до оси его шатунной шейки
Ход поршня — расстояние между крайними положениями поршня, равное удвоенному радиусу кривошипа коленчатого вала. Каждому ходу поршня соответствует поворот коленчатого вала на угол 180° (пол-оборота).
Такт — часть рабочего цикла, происходящего при движении поршня из одного крайнего положения в другое.
Объём камеры сгорания — объём пространства над поршнем, когда он находится в верхней мертвой точке.
Рабочий объём цилиндра — объём, освобождаемый поршнем при перемещении его от верхней мертвой точки к нижней мертвой точке.
Полный объем цилиндра — объём пространства над поршнем при нахождении его в нижней мёртвой точке. Полный объём цилиндра равен сумме рабочего объёма цилиндра и объёма камеры сгорания.
Литраж двигателя для многоцилиндровых двигателей — это произведение рабочего объёма на число цилиндров.
Степень сжатия — отношение полного объёма цилиндра к объёму камеры сгорания.
1.2.1. Карбюраторный двигатель.
Карбюраторный двигатель - один из типов двигателя внутреннего сгорания с внешним смесеобразованием и автономным зажиганием.
В карбюраторном двигателе в цилиндры двигателя поступает готовая топливовоздушная смесь, приготавливаемая чаще всего в карбюраторе, давшем название типу двигателя, либо в газовоздушном смесителе, либо образующаяся при впрыске топлива, распыленного специальной форсункой, в поток всасывающегося воздуха - такие двигатели называются впрысковыми или инжекторными.
Независимо от способа смесеобразования и количества тактов в рабочем цикле карбюраторные двигатели имеют одинаковый принцип работы, а именно: сжатая в камере сгорания горючая смесь в определенный момент поджигается системой зажигания, чаще всего электроискровой. Может также использоваться зажигание смеси от калильной трубки, в настоящее время в основном в дешевых малогабаритных двигателях, например, на авиамоделях; плазменное, лазерное зажигание - в настоящее время в состоянии, скорее, экспериментальных разработок.
Карбюраторные двигатели по количеству тактов в рабочем цикле делятся на четырехтактные, или двигатели Отто, у которых рабочий цикл состоит из четырех тактов и включает четыре полуоборота коленвала, и двухтактные, рабочий цикл которых включает два полуоборота коленвала с одновременным протеканием разных тактов одновременно. Последние, благодаря относительной простоте конструкции, получили широкое распространение как двигатели для мотоциклов и разнообразных агрегатов, требующих простоты и дешевизны конструкции - бензопилах, мотокультиваторах, как пусковые двигатели для более мощных дизелей и т. д.
Карбюраторные двигатели разделяются на атмосферные, у которых впуск воздуха или горючей смеси осуществляется только за счет разрежения в цилиндре при всасывающем ходе поршня и двигатели с наддувом, у которых впуск воздуха или горючей смеси в цилиндр происходит под давлением, создаваемым специальным компрессором, с целью увеличения рабочего заряда в том же рабочем объеме и получения повышенной мощности двигателя.
Двухтактный карбюраторный двигатель 2СД-М1, работающий на смеси бензина и моторного масла (25:1). Карбюратор справа
В качестве топлива для карбюраторного двигателя в разное время применялись спирт, светильный газ, пропан-бутановая смесь, этиловый спирт, керосин, лигроин, бензин и их смеси. Наибольшее распространение получили бензиновые и газовые карбюраторные двигатели.
1.1.2. Инжекторный двигатель.
Система впрыска топлива (англ. Fuel Injection System) — система подачи топлива, устанавливаемая на современных бензиновых двигателях. Основное отличие от карбюраторной системы — подача топлива осуществляется путем непосредственного впрыска топлива с помощью форсунок во впускной коллектор или в цилиндр. Автомобили с данной системой питания часто называют инжекторными.
1.1.2.1. Принцип работы.
В контроллер, при работе системы, поступает, со специальных датчиков, следующая информация:
о положении и частоте вращения коленчатого вала,
о массовом расходе воздуха двигателем,
о температуре охлаждающей жидкости,
о положении дроссельной заслонки,
о содержании кислорода в отработавших газах (в системе с обратной связью),
о наличии детонации в двигателе,
о напряжении в бортовой сети автомобиля,
о скорости автомобиля,
о положении распределительного вала (в системе с последовательным распределенным впрыском топлива),
о запросе на включение кондиционера (если он установлен на автомобиле)
На основе полученной информации контроллер управляет следующими системами и приборами:
топливоподачей (форсунками и электробензонасосом),
системой зажигания,
регулятором холостого хода,
адсорбером системы улавливания паров бензина (если эта система есть на автомобиле),
вентилятором системы охлаждения двигателя,
муфтой компрессора кондиционера (если он есть на автомобиле),
системой диагностики.
Изменение параметров электронного впрыска может происходить буквально «на лету», так как управление осуществляется программно, и может учитывать большое число программных функций и данных с датчиков. Также, современные системы электронного впрыска способны адаптировать программу работы под конкретный экземпляр мотора, под стиль вождения и многие другие характеристики и спецификации.
Ранее использовалась механическая система управления впрыском.
1.1.2.2. Достоинства двигателей, оборудованных системой впрыска с микропроцессорным управлением.
Преимущества, по сравнению с двигателями, оборудованными карбюраторной системой подачи топлива:
Некоторое уменьшение расхода топлива.
Упрощается запуск двигателя,
Приближенная к линейной характеристика крутящего момента (улучшаются динамические и мощностные характеристики двигателя).
Не требует кропотливой ручной регулировки системы впрыска, т.к. выполняет самостоятельную настройку на основе данных, передаваемых датчиками кислорода.
Поддерживает примерно стехиометрический состав рабочей смеси, что несколько уменьшает выброс несгоревших углеводородов и повышает экологичность (альфа 0.98-1.2).
1.1.2.3. Недостатки.
Основные недостатки двигателей с блоком управления по сравнению с карбюраторными:
Высокая стоимость узлов,
Низкая ремонтопригодность элементов,
Высокие требования к фракционному составу топлива,
Необходимость в специализированном персонале и оборудовании для диагностики, обслуживания и ремонта, высокая стоимость ремонта.
Зависимость от электропитания и критически важное требование к постоянному наличию напряжения питания.
Трансмиссия.
Трансми́ссия (силовая передача) — в машиностроении совокупность сборочных единиц и механизмов, соединяющих двигатель (мотор) с ведущими колёсами транспортного средства (автомобиля) или рабочим органом станка, а также системы, обеспечивающие работу трансмиссии. В общем случае трансмиссия предназначена для передачи крутящего момента от двигателя к колёсам (рабочему органу), изменения тяговых усилий, скоростей и направления движения. Трансмиссия входит в состав силового агрегата.
Механические трансмиссии.
Механические трансмиссии — (простые и планетарные) в коробках передач содержат лишь шестеренчатые и фрикционные устройства. Преимущества их состоят в высоком коэффициенте полезного действия (КПД), компактности и малой массе, надежности в работе, относительной простоте в производстве и эксплуатации. Недостатком механической трансмиссии является ступенчатость изменения передаточных чисел, снижающая использование мощности двигателя. Большое время на переключение передач рычагом усложняет управление машиной. Поэтому спортивные автомобили, снабженные механической трансмиссией, оборудуют электронными переключателями передач (подрулевыми лепестками, кнопками на руле и пр.) и коробками передач со сверхбыстрыми синхронизирующими сервомеханизмами.
Применение механических транисмиссий характерно для советского танкостроения (простые механические — Т-55, Т-62; планетарные с гидросервоуправлением — Т-64, Т-72, Т-80).
Гидромеханические трансмиссии.
Гидромеханические трансмиссии имеют гидромеханическую коробку передач, в состав которой входят гидродинамический преобразователь момента (гидротрансформатор, комплексная гидропередача) и механический редуктор. Преимущества этих трансмиссий состоят в автоматическом изменении крутящего момента в зависимости от внешних сопротивлений, возможности автоматизации переключения передач и облегчении управления, фильтрации крутильных колебаний и снижении пиковых нагрузок, действующих на агрегаты трансмиссии и двигатель, и в повышении вследствие этого надежности и долговечности поршневого двигателя и трансмиссии.
Основным недостатком этих трансмиссий является сравнительно низкий КПД из-за низкого КПД гидропередачи. При КПД гидропередачи не ниже 0,8 диапазон изменения момента не более трех, что вынуждает иметь механический редуктор на три-пять передач, считая передачу заднего хода. Необходимо иметь специальную систему охлаждения и подпитки гидроагрегата, что увеличивает габариты МТО. Без специальных автологов или фрикционов не обеспечиваются торможение двигателем и пуск его с буксира.
Гидромеханические трансмиссии получили широкое распространение в западном танкостроении — М1 «Абрамс» (США), «Леопард-2» (ФРГ). В трансмиссиях этих танков использованы не только гидродинамические передачи в основном приводе, но и гидростатические (гидрообъемные) передачи в дополнительном приводе для осуществления поворота.
Электромеханические трансмиссии
Электромеханическая трансмиссия состоит из электрического генератора, тягового электродвигателя (или нескольких), электрической системы управления, соединительных кабелей. Основным достоинством электромеханических трансмиссий, является обеспечение наиболее широкого диапазона автоматического изменения крутящего момента и силы тяги, а так же, отсутствие жёсткой кинематической связи между агрегатами электротрансмиссии, что позволяет создать различные компоновочные схемы.
Недостатком, препятствующим широкому распространению электрических трансмиссий, являются относительно большие габариты, масса и стоимость (особенно если используются электрические машины постоянного тока), сниженный КПД (по сравнению с чисто механической). Однако, с развитием электротехнической промышленности, массовым распространением асинхронного, синхронного, вентильного, индукторного и др. видов электрического привода, открываются новые возможности для электромеханических трансмиссий.
Такие трансмиссии применяются в тепловозах, карьерных самосвалах, некоторых морских судах, тракторах, самоходных механизмах, военной технике (в свое время, на танках ЭКВ (СССР) и немецких военных машинах «Фердинанд» и «Мышонок»), автобусах (которые с таким видом трансмиссии, правильнее называются теплоэлектробус (например ЗиС-154)).
Сцепление.
Сцепле́ние — механизм передачи вращения, который может быть плавно включён и выключен (выжат), обеспечивающий безрывковое трогание автомобиля с места и бесшумное переключение передач.
Обычно термин «сцепление» относится к компоненту трансмиссии транспортного средства с двигателем, предназначенному для подключения или отключения соединения двигателя с коробкой передач. Изобретение сцепления приписывают Карлу Бенцу.
Существует много различных типов сцепления, но большинство основано на одном или нескольких фрикционных дисках, плотно сжатых друг с другом или с маховиком пружинами. Фрикционный материал очень похож на используемый в тормозных колодках и раньше почти всегда содержал асбест, в последнее время используются безасбестовые материалы. Плавность включения и выключения передачи обеспечивается проскальзыванием постоянно вращающегося ведущего диска, присоединенного к валу двигателя, относительно ведомого диска, соединенного через шлиц с коробкой передач.
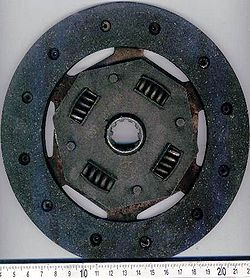
Усилие от педали сцепления передается на механизм путем гидравлического привода или троса. Выжимание педали сцепления разжимает диски сцепления, в итоге оставляя между ними свободное пространство, а отпускание педали приводит к плотному сжатию ведущего и ведомого дисков. Почти все стандартные типы сцепления содержат пружины демпфера крутильных колебаний (видны на снимке), служащие для выравнивания небольших постоянных колебаний момента, неизбежно возникающих при передаче его шестернями коробки передач.
Коробка передач.
Коро́бка переда́ч (коробка перемены передач, коробка переключения передач, коробка скоростей, КП, КПП, англ. Gear box) — агрегат (как правило — шестерёнчатый) различных промышленных механизмов (например, станков) и трансмиссий механических транспортных средств.
КП транспортных средств предназначена для изменения частоты и крутящего момента в более широких пределах, чем это может обеспечить двигатель транспортного средства. Как правило, это относится к двигателям внутреннего сгорания (ДВС), которые имеют недостаточную приспособляемость. Транспортные средства с паровыми или электрическими (трамвай, троллейбус) двигателями, имеющими высокую приспособляемость и обеспечивающими изменение частоты вращения и крутящего момента в более широких пределах, чем ДВС, обычно выполняются без КП. Также КП предназначена для обеспечения движения транспортного средства задним ходом и длительного отключения двигателя от движителя при пуске двигателя и работе его на стоянках.
В металлорежущих и других станках КП применяют, в первую очередь, для обеспечения оптимальных режимов резания — частот вращения (скоростей перемещения) режущего инструмента или обрабатываемой детали (например, частота вращения шпинделя токарного или сверлильного станка).
Несущая система, подвеска, колеса.
Несущая система.
Кузов легкового автомобиля - основная часть автомобиля, предназначенная для безопасного и комфортабельного размещения людей, багажа и грузов, а также крепления к нему необходимых узлов и агрегатов автомобиля, таких как: двигатель, трансмиссия, ходовая часть, топливные баки и прочие вспомогательные системы и оборудование. Основная функция кузова - обеспечение максимально возможной безопасности в случае столкновения, опрокидывания, падения с высоты и в прочих аварийных ситуациях, и защита пассажиров от воздействия внешних факторов (ветер, дождь, снег, холод и т.д.). По конструкции кузова бывают трёхобъёмные, двухобъёмные и однообъёмные.
Трёхобёмный кузов.
Трёхобъёмными являются автомобильные кузова, разделённые на три изолированных друг от друга отсека: двигательный отсек, пассажирский салон и багажный отсек
.
Рис.3. Трёхобъёмный кузов.
Трёхобъёмный кузов считается самым безопасным и комфортабельным в силу того, что при фронтальном столкновении или ударе сзади энергию удара в первую очередь принимают на себя и поглощают либо двигательный отсек, либо багажный, а не пассажирский салон. В тоже время такая конструкция кузова позволяет обеспечить максимальный комфорт для пассажиров благодаря тому, что пассажирский салон изолирован от двигательного и багажного отсеков, в которые поступают шумы от работы двигателя, неровностей дороги и ударов по колёсам, передаваемые внутрь кузова через элементы крепления подвесок и двигателя автомобиля, запахи от перевозимого багажа и принадлежностей (запасное колесо, домкрат и т.п.). К недостаткам конструкции можно отнести увеличенную общую длину автомобиля, что влечёт за собой некоторые трудности при маневрировании и парковке в местах большого скопления транспортных средств.
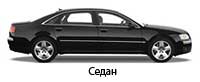
Рис.4. Седан.
Седан - Четырёхдверный или двухдверный кузов с двумя рядами полноценных сидений и жёсткой крышей, рассчитанный на комфортабельное размещение 4-5 человек. По одной из версий, это слово произошло от названия французского города Седан, в котором было развито производство дорожных карет в XIX веке. По другой версии - английский вариант названия паланкина.
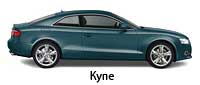
Рис.5. Купе.
Купе - Двухдверный кузов с жёсткой, заниженной в задней части кузова крышей, имеющий один или два ряда сидений. Второй ряд сидений, как правило, носит чисто номинальный характер. На нём можно перевозить ручную кладь: сумочку, ноутбук, собаку наконец, но только не людей. Предназначен для размещения двух человек и имеет укороченную базу. В переводе с французского coupé означает сократить, укоротить.
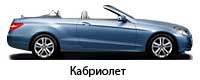
Рис.6. Кабриолет.
Кабриолет - Кузов седан или купе с двумя рядами сидений, со съёмной или складывающейся крышей. Очень эффектный, привлекающий к себе внимание, но не практичный кузов. В своё время выпуск кабриолетов был приостановлен в связи с несоответствием конструкции требованиям безопасности. Комментарии, как говорится, излишни. Предположительно происходит от итальянского сарriоlа, сарrа - "коза".
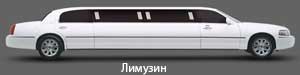
Рис.7. Лимузин.
Лимузин - Седан с удлинённой базой и жёсткой крышей, имеющий более двух рядов сидений. Переднее водительское сиденье отделено от остального салона жесткой перегородкой со стеклом. Может иметь более четырёх дверей и отличается высочайшим уровнем комфорта для пассажиров. Назван по имени области Лимузен во Франции.
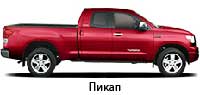
Рис. 8. Пикап.
Пикап — Легковой автомобиль, имеющий открытый или легко открывающийся багажный отсек, расположенный позади пассажирского салона. Иными словами - грузовой вариант легкового автомобиля. Pick-up - в переводе с английского поднимать, отрывать.
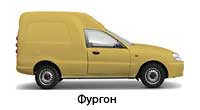
Рис.9. Фургон.
Фургон - Фактически - это пикап с закрытым грузовым отсеком. Могут быть как трёхобъёмными, так и двухобъёмными. Происходит от французского слова fourgon - повозка закрытого типа для перевозки поклажи.
Двухобъёмный кузов
Двухобъёмными кузовами являются все автомобильные кузова конструктивно разделённые на два изолированные друг от друга отсека
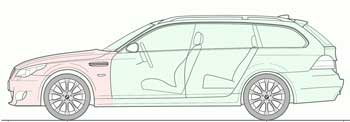
Рис. 10. Двухобъёмный кузов.
двигательный и грузопассажирский. Как правило, такие автомобили имеют нечётное количество дверей благодаря наличию открывающейся задней двери. Грузовой и пассажирский отсеки объединены в один общий отсек со всеми вытекающими последствиями. С одной стороны такая компоновка позволяет легко увеличить при необходимости объём багажного отсека, с другой стороны - приводит к неизбежному снижению уровня комфорта и безопасности, так как шумы от задней подвески и посторонние запахи от багажа неизбежно будут поступать непосредственно в салон автомобиля, а предметы перевозимые в качестве груза или багажа представляют реальную угрозу для пассажиров в случае возникновения аварийных ситуаций, поскольку имеют возможность свободно перемещаться внутри салона во время столкновения или опрокидывания автомобиля.
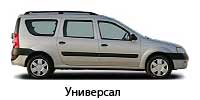
Рис.11. Универсал.
Универсал - Кузов автомобиля с жёсткой крышей, у которого крышка багажника расположена почти вертикально и представляет собой дополнительную заднюю дверь. По общей длине не отличается от седана. В некоторых случаях оборудован дополнительным третьим рядом облегченных, легко демонтируемых сидений. Второй ряд сидений складывающийся, что позволяет использовать часть пассажирского салона для перевозки багажа и грузов. Очень широкое применение этот тип кузова нашёл при производстве внедорожников. В переводе с латыни универсал (universalis) означает общий.
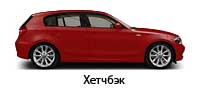
Рис.12. Хетчбэк.
Хетчбэк - Кузов с такими же свойствами как универсал, но с укороченным багажным отсеком и, как следствие, коротким задним свесом, что делает машину более компактной и удобной для использования в стеснённых городских условиях. Название кузова происходит от английского hatchback (hatch — люк, back — сзади).
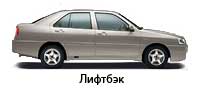
Рис.13. Лифтбэк.
Лифтбэк - Хетчбэк, который внешне похож на седан, однако крышка багажника открывается вместе с задним стеклом, обеспечивая доступ, как в багажный отсек, так и в пассажирский салон. Характерная особенность лифтбэка - отсутствие металлической перегородки, придающей кузову дополнительную прочность и изолирующей пассажирский салон от багажного отделения, как в настоящем седане. В переводе с английского lift - поднимать, back — задняя часть.
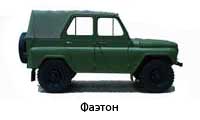
Рис.14. Фаэтон.
Фаэтон - Кузов с мягкой крышей и съёмными дверными стёклами. Очень специфический и довольно редко встречающийся тип кузова. Классический пример фаэтона - УАЗ 469.
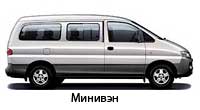
Рис.15. Минивэн.
Минивен - Кузов универсал увеличенного объёма, предназначенный для перевозки пассажиров и грузов. Изначально разрабатывался именно для перевозки пассажиров, и лишь впоследствии на его базе появились грузовые варианты минивэнов-фургонов. Включает в себя подклассы: микровэны, компактвэны, мультивэны. Может быть как двухобъёмным, так и однообъёмным. Происходит от англиского mini - маленький и van - фургон.
Однобъёмный кузов.
Однообъёмные автомобильные кузова отличаются отсутствием деления на отсеки. Имеют общий грузопассажирский салон, причём капот двигателя, если имеется, открывается внутрь салона.
Рис.16. Однобъёмный кузов.
Такая конструкция позволяет максимально эффективно использовать полезный объём кузова, как в целях перевозки грузов, так и для перевозки пассажиров. Кузовами такого типа оснащаются автобусы, микроавтобусы (УАЗ 452 - "Буханка") и минивэны (Mitsubishi L300, Toyota Previa) , а также некоторые сити-кары или той-кары (например, Smart).
Подвеска.
Подвеска автомобиля, или система подрессоривания — совокупность деталей, узлов и механизмов, играющих роль соединительного звена между кузовом автомобиля и дорогой. Входит в состав шасси.
Подвеска выполняет следующие функции:
Физически соединяет колёса или неразрезные мосты с несущей системой автомобиля — кузовом или рамой;
Передаёт на несущую систему силы и моменты, возникающие при взаимодействии колёс с дорогой;
Обеспечивает требуемый характер перемещения колёс относительно кузова или рамы, а также необходимую плавность хода.
Основными элементами подвески являются:
Упругие элементы, которые воспринимают и передают нормальные (направленные по вертикали) силы реакции дороги, возникающие при наезде колеса на её неровности;
Направляющие элементы, которые задают характер перемещения колёс и их связи между собой и с несущей системой, а также передают продольные и боковые силы и их моменты.
Амортизаторы, которые служат для гашения колебаний несущей системы, возникающих вследствие действия дороги.
В реальных подвесках зачастую один элемент выполняет сразу несколько функций. Например, многолистовая рессора в классической рессорной подвеске заднего моста воспринимает одновременно как нормальную реакцию дороги (то есть, является упругим элементом), так и боковые и продольные силы (то есть, является и направляющим элементом), а также за счёт межлистового трения выступает в качестве несовершенного фрикционного амортизатора.
Однако в подвесках современных автомобилей, как правило, каждую из этих функций выполняют отдельные конструктивные элементы, достаточно жёстко задающие характер перемещения колёс относительно несущей системы и дороги, что обеспечивает заданные параметры устойчивости и управляемости.
Современные автомобильные подвески становятся сложными конструкциями, сочетающими механические, гидравлические, пневматические и электрические элементы, зачастую имеют электронные системы управления, что позволяет достичь сочетания высоких параметров комфортабельности, управляемости и безопасности.
Колеса.
Автомобильное колесо за последние 100 лет претерпело немало изменений, от деревянных колёс до композитов и сверхпрочных сплавов.
Спицевое колесо.
В настоящее время его носителями являются только велосипеды и некоторые мотоциклы. Достоинства спицевых колёс в их высокой энергоёмкости[неизвестный термин], к недостаткам можно отнести высокую трудоёмкость в производстве колёс и невысокую точность геометрии колеса. Также спицевые колёса можно встретить на выставочных автомобилях или ретро-карах.
Классическое стальное колесо
Является наиболее распространёнными и дешёвым типом колёс в мире, выполняется как правило из листовой стали, довольно прочно, зарекомендовало себя во всех видах транспорта.
Колёса из лёгких сплавов
Колёса из лёгких сплавов можно поделить на три категории (по технологии производства): литые, кованые и комбинированные (сборные).
Основные преимущества легкосплавных колёс перед стальными это:
геометрическая точность,
меньший вес (как правило),
улучшенное отведение тепла от тормозных систем,
разнообразие дизайна колёс.
Например — если стальное колесо типоразмерности 5Jx13 весит 5,5 кг, то легкосплавное литое — около 4,8-5 кг, а кованое — около 4,2-4,5 кг (взвешивание колёс ВАЗ-21099 произведено в испытательной лаборатории компании K&K в 1999 г.). Технически уменьшение веса колеса означает снижение массы неподрессоренных частей и сил инерции. Благодаря этому оно легче «отрабатывает» неровность поверхности дорожного полотна, что даёт более чёткую и меньшую нагрузку на подвеску автомобиля, что в свою очередь улучшает контакт автомобиля с дорогой и его управляемость. Снижение инерционности, соответственно, увеличивает ресурс самого транспортного средства, повышает тормозную и разгонную динамику и как следствие снижает расход топлива.
Литые колёса
Литые изготавливаются методом отливки в форму. Используются как правило алюминиевые, магниевые и очень редко титановые сплавы. После отливки в ряде случаев происходит термообработка отливок (для улучшения механических свойств колеса). Свой конечный вид колесо получает после механической обработки и покраски. По стоимости — это самый окупающийся вид производства легкосплавных колёс.
Кованые колёса
Кованые колёса изготавливаются методом очень энергоёмкой горячей штамповки. Поковка проходит обязательную термообработку(процесс старения и закалку). Конечный вид колесо получает после механической обработки и покраски. По стоимости это один из самых дорогих видов производства легкосплавных колёс (поковка может весить 25 кг — выход одного колеса 5 кг плюс большие энерго- и трудозатраты).
Комбинированные колёса
Тип колёс, который состоит как правило из двух и более частей. Каждая из которых может быть выполнена по разным технологиям (пример: спицы — алюминиевый сплав, литьё. Обод — титановый прокат, вальцовка.). Спицевое колесо тоже относится к данному типу.
Композитные колёса
В настоящее время композитные колёса стоят на некоторых велосипедах и спорткарах. Широкое распространение этого типа ограничено их высокой стоимостью.
Шины.
Автомобильная шина (покрышка, баллон или резина) — один из наиболее важных элементов колеса, представляющий собой упругую резино-металло-тканевую оболочку, установленную на обод колеса. Шина обеспечивает контакт транспортного средства с дорожным полотном, предназначена для поглощения незначительных колебаний, вызываемых несовершенством дорожного покрытия, компенсации погрешности траекторий колёс, реализации и восприятия сил, возникающих в пятне контакта.
Основными материалами для производства шин являются резина, которая изготавливается из натуральных и синтетических каучуков, и корд. Кордовая ткань может быть изготовлена из металлических нитей (металлокорд), полимерных и текстильных нитей.
Шина состоит из: каркаса, слоёв брекера, протектора, борта и боковой части.
Структура шины: 1 — протектор; 2 — плечевая часть; 3 — каркас; 4 — боковая часть(крыло шины); 5 — брекер и подушечный слой; 6 — дополнительная вставка в плечевой зоне(зелен.цв.); 7 — бортовое кольцо; 8 — бортовая часть
Измерение высоты протектора.
Текстильный и полимерный корд применяются в легковых и легкогрузовых шинах. Металлокорд — в грузовых. В зависимости от ориентации нитей корда в каркасе различают шины:
радиальные
диагональные
В радиальных шинах нити корда расположены вдоль радиуса колеса(как на схеме, позиция № 3). В диагональных шинах нити корда расположены под углом к радиусу колеса, нити соседних слоёв перекрещиваются.
Радиальные шины конструктивно более жёсткие, вследствие чего обладают большим ресурсом, обладают стабильностью формы пятна контакта, создают меньшее сопротивление качению, обеспечивают меньший расход топлива. Из-за возможности варьировать количество слоёв каркаса (в отличие от обязательно чётного количества в диагональных) и возможности снижения слойности, снижается общий вес шины, толщина каркаса. Это снижает разогрев шины при качении — увеличивается срок службы. Брекер и протектор так же легче высвобождают тепло — возможно увеличение толщины протектора и глубины его рисунка для улучшения проходимости по бездорожью. В связи с этим, в настоящее время, радиальные шины для легковых автомобилей практически полностью вытеснили диагональные.
Брекер находится между каркасом и протектором. Предназначен для защиты каркаса от ударов, придания жёсткости шине в области пятна контакта шины с дорогой и для защиты шины и ездовой камеры от сквозных механических повреждений. Изготавливается из толстого слоя резины (в лёгких шинах) или скрещённых слоёв полимерного корда и (или) металлокорда.
Протектор необходим для обеспечения приемлемого коэффициента сцепления шин с дорогой, а также для предохранения каркаса от повреждений. Протектор обладает определённым рисунком, который, в зависимости от назначения шины различается. Шины высокой проходимости имеют более глубокий рисунок протектора и грунтозацепы на его боковых сторонах. Рисунок и конструкция протектора дорожной шины определяется требованиями к отведению воды и грязи из канавок протектора и стремлением снизить шум при качении. Но, всё же, главная задача протектора шины — обеспечить надёжный контакт колеса с дорогой в неблагоприятных условиях, таких как дождь, грязь, снег и т. д., путём их удаления из пятна контакта по точно спроектированным канавкам и желобкам рисунка. Но эффективно удалять воду из пятна контакта протектор в силах лишь до определённой скорости, выше которой жидкость физически не сможет полностью удаляться из пятна контакта, и автомобиль теряет сцепление с дорожным покрытием, а следовательно и управление. Этот эффект носит название аквапланирование. Существует широко распространённое заблуждение, что на сухих дорогах протектор снижает коэффициент сцепления из-за меньшей площади пятна контакта по сравнению с шиной без протектора (slick tyre). Это неверно, так как в отсутствие адгезии сила трения не зависит от площади соприкасаемых поверхностей. На гоночных автомобилях в сухую погоду используются шины с гладким протектором либо вообще без него для того, чтобы снизить давление на колесо, уменьшив его износ, тем самым позволив применять в изготовлении шин более пористые мягкие материалы, обладающие бóльшим сцеплением с дорогой. Во многих странах существуют законы, регулирующие минимальную высоту протектора на дорожных транспортных средствах, и многие дорожные шины имеют встроенные индикаторы износа.
Борт позволяет покрышке герметично садиться на обод колеса. Для этого он имеет бортовые кольца и изнутри покрыт слоем вязкой воздухонепроницаемой (для бескамерных шин) резины.
Боковая часть предохраняет шину от боковых повреждений.
Шипы противоскольжения. В целях повышения безопасности движения автомобиля в условиях гололёда и обледенелого снега применяют металлические шипы противоскольжения. Езда на шипованных шинах имеет заметные особенности. На ходу автомобиль делается заметно более шумным, ухудшается его топливная экономичность. В снежно-грязевой каше или в глубоком рыхлом снегу эффективность шипов невелика, а на твёрдом сухом или влажном асфальте шипованные шины даже проигрывают «обычным»: из-за снижения площади пятна контакта шины с дорогой, тормозной путь автомобиля увеличивается на 5-10 %. Хотя 70-процентное сокращение тормозного пути на льду — их несомненное преимущество.
Бескамерные шины (tubeless) наиболее распространены благодаря своей надёжности, меньшей массе и удобству эксплуатации (так, например, прокол в бескамерной шине не причинит больших неудобств по дороге до автосервиса).
Система управления.
Рулевое управление предназначено для обеспечения движения автомобиля в заданном водителем направлении.
Рулевое управление современного автомобиля имеет следующее устройство:
рулевое колесо с рулевой колонкой;
рулевой механизм;
рулевой привод.
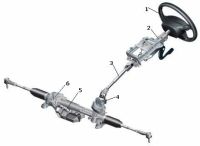
Рис.17. Схема рулевого управления
Рулевое колесо воспринимает от водителя усилия, необходимые для изменения направления движения, и передает их через рулевую колонку рулевому механизму. Диаметр рулевого колеса легковых автомобилей находится в пределе 380 - 425 мм, грузовых автомобилей – 440 – 550 мм. Рулевое колесо спортивных автомобилей имеет меньший диаметр.
Рулевая колонка обеспечивает соединение рулевого колеса с рулевым механизмом. Рулевая колонка представлена рулевым валом, имеющем несколько шарнирных соединений. На современных автомобилях предусмотрено иеханическое или электрическое регулирование положения рулевой колонки. регулировка может производиться по вертикали, по длине или в обоих направлениях. В целях защиты от угона осуществляется механическая или электрическая блокировка рулевой колонки.
Рулевой механизм предназначен для увеличения, приложенного к рулевому колесу усилия, и передачи его рулевому приводу. В качестве рулевого механизма используются различные типы редукторов. Наибольшее распространение на легковых автомобилях получили реечные рулевые механизмы.
Реечный рулевой механизм включает шестерню, установленную на валу рулевого колеса и связанную с зубчатой рейкой. При вращении рулевого колеса рейка перемещается в одну или другую сторону и через рулевые тяги поворачивает колеса. Реечный рулевой механизм располагается, как правило, в подрамнике подвески автомобиля.
Рулевой привод предназначен для передачи усилия, необходимого для поворота, от рулевого механизма к колесам. Он обеспечивает оптимальное соотношение углов поворота управляемых колес, а также препятствует их повороту при работе подвески.
Наибольшее распространение получил механический рулевой привод, состоящий из рулевых тяг и рулевых шарниров. Рулевой шарнир выполняется шаровым. Шаровый шарнир состоит из корпуса, вкладышей, шарового пальца и защитного чехла. Для удобства эксплуатации шаровый шарнир выполнен в виде съемного наконечника рулевой тяги. По своей сути рулевая тяга с шаровой опорой выступает дополнительным рычагом подвески.
Для уменьшения усилий, необходимых для поворота рулевого колеса, в рулевом приводе применяется усилитель рулевого управления. Применение усилителя обеспечивает точность и быстродействие рулевого управления, а также снижает общую физическую нагрузку на водителя.
В зависимости от типа привода различают следующие виды усилителей рулевого управления:
гидравлический;
электрический;
пневматический.
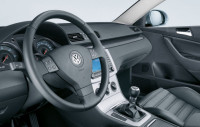
Рис.18. Современное рулевое колесо.
Большинство современных автомобилей имеют гидравлический усилитель рулевого управления (другое название – гидроусилитель руля). Разновидностью гидроусилителя является электрогидравлический усилитель рулевого управления.
Гидроусилителем рулевого управления (обиходное название – гидроусилитель руля) называется конструктивный элемент рулевого управления автомобиля, в котором дополнительное усилие при повороте рулевого колеса создается с помощью гидравлического привода. Гидроусилитель руля является самым распространенным видом усилителя рулевого управления.
Простейший гидроусилитель руля имеет привод гидронасоса от коленчатого вала двигателя. У такого усилителя производительность прямо пропорциональна частоте вращения колнечатого вала двигателя, что противоречит реальным потребностям рулевого управления (при максимальной скорости движения требуется минимальный коэффициент усиления, и наоборот).
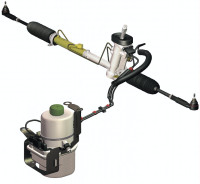
Рис.19. Электрогидравлический усилитель руля
Наиболее совершенным с точки зрения потребительских свойств и конструкции является электрогидравлический усилитель руля. Преимуществами электрогидравлического усилителя являются компактность, возможность функционирования на неработающем двигателе, экономичность за счет включения в нужный момент. В конструкции данного гидроусилителя предусмотрена возможность электронного регулирования коэффициента усиления. Поэтому, наряду с комфортностью управления усилитель может обеспечить легкость маневрирования на малых скоростях, что недоступно обычному гидроусилителю.
Электрогидравлический усилитель рулевого управления имеет следующее устройство:
насосный агрегат;
гидравлический узел управления;
система управления.
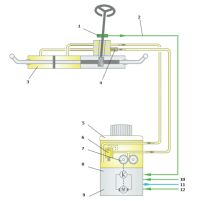
Рис.20. Схема электрогидравлического усилителя руля .
Насосный агрегат представляет собой объединенный блок, включающий гидравлический насос, электродвигатель насоса и бачок для рабочей жидкости. На насосный агрегат устанавливается электронный блок управления.
Гидравлический насос может быть лопастного или шестеренного типа. Наиболее простым и надежным является шестеренный насос.
Гидравлический узел управления является исполнительным механизмом усилителя руля. Он включает:
торсион с поворотным золотником и распределительной гильзой;
силовой цилиндр с поршнем.
Гидравлический узел управления объединен с рулевым механизмом. Шток поршня силового цилиндра является продолжением рейки рулевого механизма.
Система управления обеспечивает работу гидроусилителя. На современных автомобилях используется электронная система управления, которая обеспечивает регулирование коэффициента усиления в зависимости от скорости поворота рулевого колеса и скорости движения автомобиля. Усилитель с такими характеристиками называется адаптивным усилителем рулевого управления.
На автомобилях концерна Volkswagen и BMW электронная система управления гидравлическим усилителем руля имеет торговое название Servotronic.
Система Servotronic включает:
входные датчики;
электронный блок управления;
исполнительное устройство.
Входными датчиками системы являются датчик усилителя руля (датчик угла поворота рулевого колеса – на автомобилях, оборудованных ESP), датчик спидометра. Помимо датчиков, система использует информацию о частоте вращения коленчатого вала двигателя, поступающую от системы управления двигателем.
Электронный блок управления гидроусилителем руля принимает и обрабатывает сигналы датчиков и в соответствии с установленной программой воздействует на исполнительное устройство.
В разных модификациях системы Servotronic используются следующие исполнительные устройства:
электродвигатель насоса;
электромагнитный клапан в гидросистеме.
В первом случае изменение производительности гидроусилителя осуществляется за счет изменения скорости вращения электродвигателя. Во-втором, за счет изменения проходного сечения гидросистемы (открытие-закрытие клапана).
|
|
|