Содержание. Содержание 3 1 Описание конструкции и работы привода механизма 5
![]()
|
|
№ вала | Р, кВт | n, мин-1 | Т, Нм | ω, с-1 |
1 | 7,5 | 500 | 143,25 | 52,33 |
2 | 7,2 | 357,14 | 192,53 | 37,38 |
3 Расчет зубчатой передачи редуктора
Исходные данные:
- мощность на колесе Р2=7,2 кВт,
- крутящий момент на ведущем валу Т1=143,25 Нм,
- крутящий момент на ведомом валу Т2=192,53 Нм,
- частоты вращения валов n1=500 мин-1, n2=357,14 мин-1,
- передаточное число u=1,4,
3.1 Выбор материала зубчатых колес
С целью понижения габаритов передачи, получения высокой изгибной и контактной выносливости зубьев выбираем для шестерни и колеса материал сталь 40Х. Механические характеристики сердцевины – σВ=850МПа, σТ=550МПа [3, табл.8.8]. Термообработка шестерни – закалка ТВЧ до твердости 50 HRC, термообработка колеса – закалка ТВЧ до твердости 46 HRC.
3.2 Определение эквивалентного числа циклов перемены напряжений
Срок службы передачи:


Эквивалентное число циклов перемены напряжений при расчете на контактную прочность:

где с=1 – число колес, находящихся в зацеплении с рассчитываемым,

- для шестерни:

-для колеса:

3.3 Определение допускаемых контактных напряжений
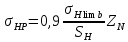
Предел контактной выносливости:



SH=1,2 – коэффициент безопасности [3, табл. 8.9].
Коэффициент долговечности:

Базовое число циклов NHO:


m– показатель степени.
Т.к.


Тогда:
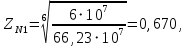
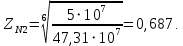
Таким образом, допускаемые контактные напряжения для шестерни и колеса:


Расчетные допускаемые контактные напряжения:

3.4 Определение допускаемых изгибных напряжений
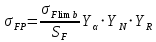
Предел изгибной выносливости


SF=1,75 – коэффициент безопасности [3].
Коэффициент долговечности:

q=9 – показатель степени при твердости шестерни и колеса больше 350НВ,

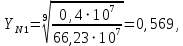
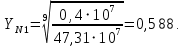
Принимаем YN=1.

Для нереверсивной нагрузки



Таким образом, допускаемые изгибные напряжения для шестерни и колеса:


3.5 Расчет геометрических параметров передачи
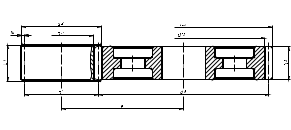
Рисунок 3.1 – Геометрические параметры цилиндрической передачи
Межосевое расстояние:
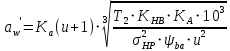
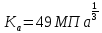




Принимается коэффициент ширины колеса относительно диаметра

Тогда коэффициент ширины колеса относительно межосевого расстояния:
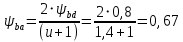
Принимается


Принимается

Ширина зубчатого венца колеса:


Ширина венца шестерни:

Принимается предварительно

Модуль зацепления:

Принимаем согласно ГОСТ 9563-60

Суммарное число зубьев передачи:
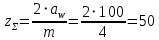
Число зубьев:
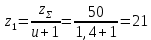

Фактическое передаточное число:
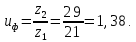
Погрешность передаточного числа:

Делительные диаметры:



Уточняется межосевое расстояние:

Диаметры вершин:



Диаметры впадин:



Коэффициент торцевого перекрытия:

Окружная скорость колес:

Принимается 9-я степень точности [1].
3.6 Силы в зацеплении
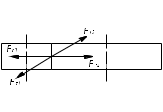
Рисунок 3.2 – Силы в зубчатом зацеплении
Окружная сила

Радиальная сила

3.7 Проверочный расчет на выносливость по контактным напряжениям
Контактная выносливость устанавливается сопоставлением действующих в полюсе зацепления расчетного и допускаемого контактных напряжений:

Контактное напряжение в полюсе зацепления при

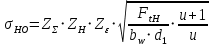
Коэффициент нагрузки


где



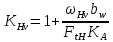
где

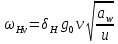
где



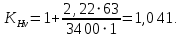










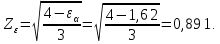


3.8 Проверочный расчет на выносливость по напряжениям изгиба
Проверка изгибной прочности для прямозубых цилиндрических колес производится по формуле:
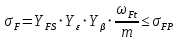
Определяем менее прочное зубчатое колесо.
Число зубьев биэквивалентного колеса:


Тогда коэффициент, учитывающий форму зубьев [3, рис. 8.20],


Находим отношения:
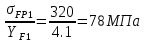
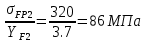
Так как





Удельная расчетная окружная сила
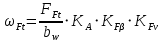
Коэффициент, учитывающий распределение нагрузки между зубьями


Коэффициент, учитывающий динамическую нагрузку, возникающую в зацеплении

Удельная окружная динамическая сила
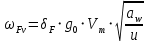



Удельная расчетная окружная сила в зоне ее наибольшей концентрации:

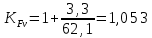
Таким образом, удельная расчетная окружная сила

Тогда расчетные контактные напряжения

Проверочный расчет на изгибную прочность выполняется, т.к.

4 Выбор конструкции и определение параметров цилиндрического колеса
Исходные данные: Модуль зубчатой передачи m=4 мм, ширина венца зубчатого колеса b2=63 мм, диаметр ведущего вала d1=30 мм.
Шестерня выполняется за одно целое с валом, ее размеры определены выше:



Колесо кованое:



Диаметр ступицы

Длина ступицы

Принимаем

Толщина обода

Принимаем

Толщина диска

Диаметр отверстия в диске:

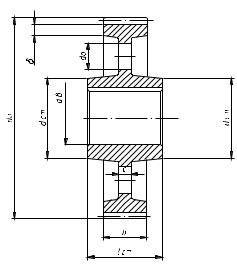
Рисунок 4.1 – Зубчатое колесо
5 Конструирование корпуса редуктора. Конструирование валов и подшипниковых узлов
Корпус редуктора выполняется литым из чугуна марки СЧ 15 ГОСТ 1412.
Для удобства сборки корпус выполняется разборным. Плоскость разъема проходит через ось выходного вала, что позволяет использовать глухие крышки для подшипников. Плоскость разъема для удобства обработки располагается параллельно плоскости основания.
Для соединения корпуса и крышки редуктора по всему контуру плоскости разъема выполняются фланцы. Фланцы объединены с приливами для подшипников.
Для предотвращения взаимного смещения корпусных деталей при растачивании отверстий под подшипники и обеспечения точного расположения их при повторных сборках, крышка фиксируется относительно корпуса двумя коническими штифтами.
Толщина стенок корпуса и крышки.

Толщина поясов корпуса и крышки.


нижнего пояса

Диаметры болтов:
– фундаментных

Принимается болты М16,
– крепящих крышку корпуса у подшипников

Принимается болты М12.
– соединяющих крышку с корпусом

Принимается болты М8.
Диаметр штифта

При проектном расчете валов определяется диаметр выходного конца вала или диаметр под шестерней для промежуточных валов. Расчет ведется на чистое кручение по пониженным допускаемым напряжениям:

где Т – крутящий момент на валу, Н∙мм;

Для определения диаметра выходных концов валов принимаем

Диаметр выходного конца быстроходного вала:
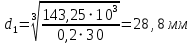
Принимаем

Диаметр вала под подшипники

Принимаем

Диаметр вала под манжету

Принимаем

Диаметр выходного конца тихоходного вала:
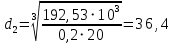
Принимаем

Диаметр вала под подшипники

Принимаем

Диаметр вала под колесо

Принимаем

Диаметр вала под манжету

Принимаем

На входной и выходной валы редуктора устанавливаем шариковые радиальные подшипники. Основные размеры и характеристики представлены в таблице 5.1.
Таблица 5.1 – Характеристики подшипников
Условное обозначение подшипника | d | D | B | Грузоподъемность, кН | |||
Размеры, мм | С | С0 | |||||
207 | 35 | 72 | 17 | 35,1 | 17,8 | ||
210 | 50 | 90 | 20 | 43,2 | 27 |
6 Подбор и проверочный расчет подшипников
6.1 Расчет подшипников ведущего вала
Из конструктивных соображений выбирается подшипник 207.
Подшипник | d, мм | D, мм | C, Н |
207 | 35 | 72 | 35100 |
6.2 Расчет подшипников ведомого вала
Из конструктивных соображений выбирается подшипник 210.
Подшипник | d, мм | D, мм | C, Н |
210 | 50 | 90 | 43200 |
7 Расчет соединений «вал-ступица» с подбором посадок
7.1 Методика расчета
Исходные данные: Крутящий момент на ведущем валу Т1=143,25 Нм, крутящий момент на ведомом валу Т2=193,53 Нм.
Для закрепления на валах зубчатого колеса, шкива и муфты применены призматические шпонки, выполненные по ГОСТ 23360 (рисунок 8.1).
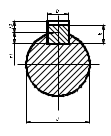
Рисунок 7.1 – Шпоночное соединение
Так как высота и ширина призматических шпонок выбираются по стандартам, расчет сводится к проверке размеров по допускаемым напряжениям при принятой длине [2]:
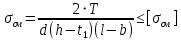
где T - крутящий момент на валу,

d - диаметр вала, мм;
h - высота шпонки, мм;
t1 - заглубление шпонки в валу, мм;
l – полная длина шпонки, мм;
b- ширина шпонки, мм.
7.2 Шпонка под колесом
Для заданного диаметра вала (



Длина шпонки

Принимаем




Принимается шпонка 161056 ГОСТ 23360.
7.3 Шпонка под муфтой
Для заданного диаметра вала (



Длина шпонки

Принимаем




Принимается шпонка 12856 ГОСТ 23360.
7.4 Подбор посадок
Назначаем посадки основных деталей редуктора:
– зубчатого колеса на вал Н7/p6 [5];
– муфты и шкива на валы редуктора H7/k6 [5];
– фланцев в корпус H7/d9 [5];
– шпонки в вал P9/h9 [5];
– шпонки в ступицу P9/h9 [5].
Шейки валов под подшипники выполняем с отклонением вала k6 [5], отклонения отверстий в корпусе под наружные кольца подшипников Н7 [5].
Отклонения вала в месте соприкосновения с манжетой по h8 [5].
8 Выбор и проверочный расчет муфты
Исходные данные: Крутящий момент на ведомом валу Т2=193,53 Нм, диаметр вала под муфтой d2=40 мм.
Зубчатые муфты (рисунок 8.1) применяются для соединения валов, нагруженных большими крутящими моментами при различной комбинации радиальных, угловых и осевых смещений.
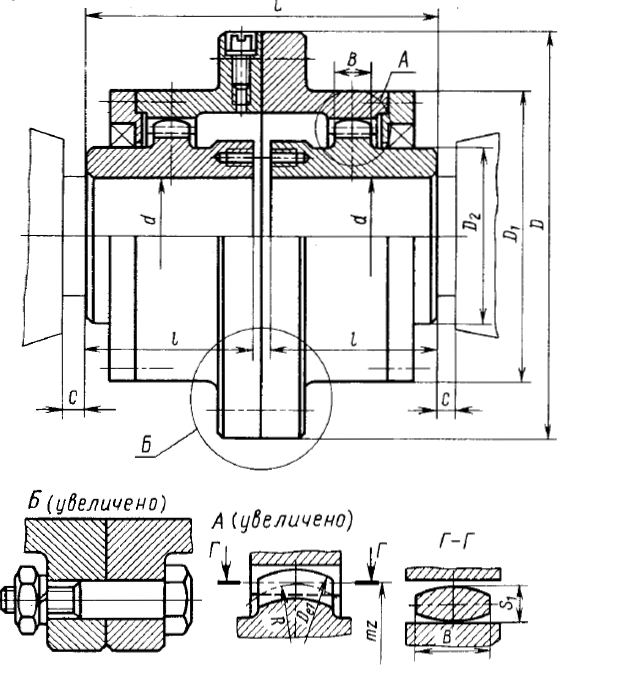
Рисунок 8.1 – Зубчатая компенсирующая муфта
Зубчатая муфта выбирается по ГОСТ 5006 по крутящему моменту на выходном валу редуктора

Принимается муфта 1000-40-1 ГОСТ 5006.
Диаметр отверстия в муфте для установки вала d=40 мм.
Проверка муфты производится по напряжениям смятия рабочих поверхностей зубьев [2].
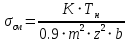
где К=1,3 - коэффициент режима работы для неравномерно нагруженных механизмов [2];





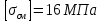
9 Выбор способа смазки и смазочных материалов передач и подшипников
Смазывание зубчатого зацепления производится маслом, заливаемым внутрь корпуса до уровня, обеспечивающего погружение колеса примерно на 25…30 мм. Смазывание подшипников осуществляется жидким маслом путем разбрызгивания. Объем масла определяем из расчета 0,25 дм3 масла на 1 кВт передаваемой мощности:


Для смазывания принимается масло индустриальное И-70А ГОСТ 20799.
Для контроля уровня смазки предусмотрена установка маслоуказателя.
Высота масла Hм=(0,2…0,3)da2=(0,2…0,3)x124=24,8…37,2 мм.
Принимаем конструктивно Hм=36 мм.
Смазка подшипников осуществляется пластичными маслами марки ЦИАТИМ-221 ГОСТ 9494. Для предотвращения вымывания пластичной смазки подшипниковые камеры закрываются мазеудерживающими кольцами.
Заключение
В курсовой работе был спроектирован редуктор к горизонтальному ленточному транспортеру.
Были рассчитаны элементы и детали редуктора. На листах формата А1 и А3 выполнены чертежи привода, редуктора, тихоходного вала и зубчатого колеса.
Список использованных источников
Кузьмин, А.В. Курсовое проектирование деталей машин, часть 1 / А.В.Кузьмин, Н.Н.Макейчик, В.Ф. Калачёв. – Мн.: Высшая школа, 1982. – 412 с.
Кузьмин, А.В. Курсовое проектирование деталей машин, часть 2 / А.В.Кузьмин, Н.Н.Макейчик, В.Ф. Калачёв. – Мн.: Высшая школа, 1982. – 430 с.
Иванов, М.Н. Детали машин / М.Н.Иванов. – М.: Высшая школа, 1991. – 480 с.
Кузьмин, А.В. Расчёты деталей машин / А.В. Кузьмин, И.М. Чернин, Б.С. Козинцов. - Мн.: Высшая школа, 1986. – 386 с.
Курмаз, Л.В. Детали машин, проектирование / Л.В. Курмаз, А.Т. Скойбеда. – Мн.: УП «Технопринт», 2001. – 310 с.
Дунаев, П.Ф. Детали машин. Курсовое проектирование: Учебное пособие для машиностроительных специальностей техникумов / Дунаев П.Ф. Леликов О.П. – М.: Высшая школа, 1984. – 295 с.
Подскребко, М.Д. Задания и методические указания к курсовому проекту по деталям машин/ М.Д. Подскребко - Мн.: Ротапринт БАТУ, 1993. – 116 с.
Агейчик, В.А. Детали машин и основы конструирования. Часть 1: методическое пособие по выполнению курсового проекта / В.А. Агейчик и др. – Мн.: БГАТУ, Кафедра сопротивления материалов и деталей машин, 2007. – 197 с.
Дунаев, П.Ф. Конструирование узлов и деталей машин / П.Ф. Дунаев – М.: Высшая школа, 1978. – 315 с.
Чернавский, С.А. Курсовое проектирование деталей машин / С.А. Чернавский, К.Н. Боков, И.М. Чернин и др. – М.: Машиностроение, 1988. – 345 с.