|
Реферат по материаловедению. Термическая, термохимическая и термомеханическая обработка стали
Министерство образования и науки Российской Федерации Федеральное государственное автономное образовательное учреждение высшего образования «Уральский федеральный университет имени первого Президента России Б. Н. Ельцина» (УрФУ)
Институт фундаментального образования
Кафедра турбин и двигателей 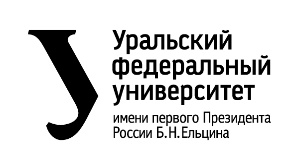
Реферат
по материаловедению
по теме: Термическая, термохимическая и термомеханическая обработка стали
Студент: Делягин Д. О.
Группа: ЭН – 360016
Преподаватель: Новиков В. А.
Екатеринбург
2018
СОДЕРЖАНИЕ
Основные теории термической обработки стали………………….…….3
Превращения при нагреве………………………………….….……..3
Превращения при охлаждении……………………………..………..6
Перлитное превращение…………………………………..………….8
Промежуточное превращение……………………………………....12
Мартенситное превращение………………………………...………14
Превращение в закаленных сталях при отпуске……..……………19
Технологии термической обработки стали……………………………..21
Отжиг I - ого рода……………………………………………………21
Отжиг II – ого рода…………………………………………………..24
Закалка стали…………………………………………………………29
Обработка холодом…………………………………………………..31
Отпуск стали………………………………………………………….33
Поверхностная закалка стали………………………………………..35
Химико-термическая обработка стали………………………..…..……..37
Цементация стали…………………………………………………….37
Азотирование стали…………………………………………………..42
Цианирование стали………………………………………………….45
Диффузионная металлизация………………………………………..46
Термомеханическая обработка стали……………………………………47
Высокотемпературная механическая обработка стали………….48
Низкотемпературная механическая обработка стали……………48
Литература…………………………………………………………………50
1. Основные теории термической обработки стали
1.1 Превращения при нагреве
Превращения в стали при нагревании связаны с достижением сплавами критических температур, при которых происходят фазовые превращения.
В системе железоуглеродистых сплавов приняты следующие обозначения критических температур: температура линии РSК обозначается А1 (727 °С), температура линии МО — А2 (768 °С), температура линии GOS — А3 (727...911 °С), температура линии ЕS — Ат (727... 1147 °С). Чтобы отличить критическую температуру, полученную при охлаждении, от критической температуры, полученной при нагревании, перед цифровым индексом при охлаждении ставят букву r (Аr1 Аr2), а при нагревании — с (Ас1, Ас2).
Превращение перлита в аустенит в полном соответствии с диаграммой Fе — Fе3С может завершиться при температуре 727 °С (АС1) при медленном нагревании. Скорость превращения перлита в аустенит находится в прямой зависимости от содержания в стали углерода.
При температуре 768 °С (точка Кюри —Ас2) стали теряют свои магнитные свойства.
Окончание процесса превращения характеризуется образованием аустенита и исчезновением перлита.
При нагревании сталей с содержанием углерода менее 0,8 %, т. е. доэвтектоидных, с исходной структурой, состоящей из феррита и перлита, происходят следующие структурные превращения. При температуре 727 °С происходит превращение перлита в аустенит. При этом сохраняется двухфазная структура — из аустенита и феррита. При дальнейшем нагревании происходит превращение феррита в аустенит, которое заканчивается при достижении критической температуры Ас3, т.е. на линии GOS.
У заэвтектоидных сталей при нагреве выше температуры Ас1 происходит растворение цеменита в аустените (в соответствии с линией SЕ), которое заканчивается при критической температуре Аст, т. е. на линии SЕ.
Для более полного понимания процессов структурных преобразований рассмотрим диаграмму изотермического превращения перлита в аустенит при нагревании (рис. 6.1).
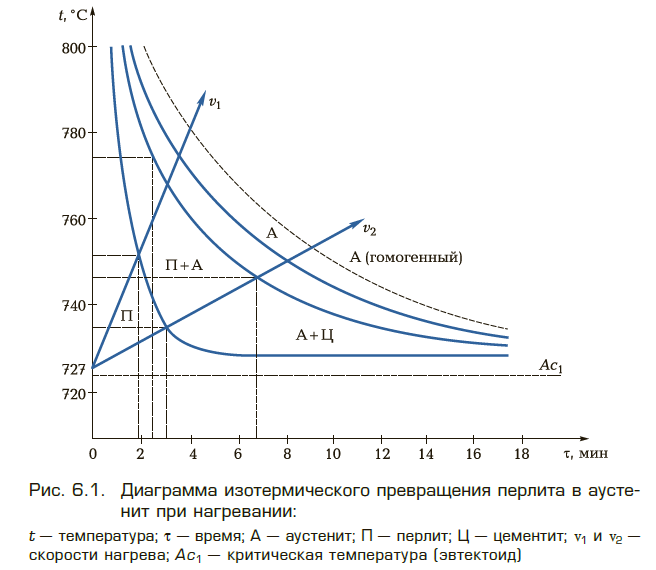
Так как перлит — это смесь цементита и феррита в соотношении примерно 1:6, то при нагревании на границе раздела феррита и цементита образуются зерна аустенита. При последующем нагревании происходят растворение цементита в аустените и дальнейший рост зерен аустенита. С ростом зерен аустенита происходит постепенное увеличение массовой доли углерода в аустените. Скорость нагрева также влияет на превращение перлита в аустенит. На диаграмме лучами v1, и v2 графически изображены различные скорости нагрева. Чем меньше скорость нагрева, тем при более низких температурах происходит весь процесс фазовых превращений.
Важной характеристикой стали является склонность к росту зерна аустенита при нагревании. При росте зерна при незначительном перегреве выше критической точки сталь считается наследственно крупнозернистой. Если же зерно начинает расти при большем перегреве — наследственно мелкозернистой. На рост зерна большое влияние оказывают различные примеси, попадающие в сталь в процессе плавки. Склонность к росту аустенитного зерна является плавочной характеристикой.
Зернистость влияет на механические свойства сталей. Мелкозернистая сталь обладает значительно большей ударной вязкостью, чем крупнозернистая, поэтому при термической обработке сталей этот фактор следует учитывать.
Действительная величина зерна — это размер зерна при обычных температурных условиях после определенного типа термообработки. Для определения величины зерна принята стандартная шкала. В ГОСТ 5639—82’ представлена шкала для оценки величины зерна по десятибалльной системе (рис. 6.2).
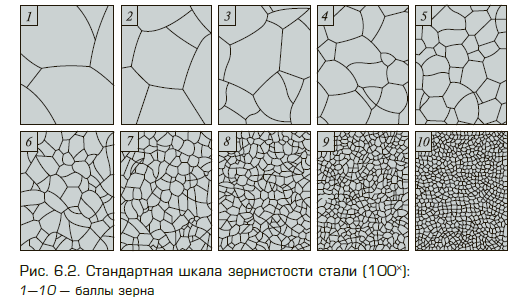
Величину зерна определяют при стократном увеличении методом сравнения со стандартной шкалой. Для определения зернистости сталь должна быть нагрета до температуры 930 °С. Если при этой температуре номер зерна 1—4, то это сталь наследственно крупнозернистая. Стали, у которых номер зерна 5 — 8 и более, — наследственно мелкозернистые. Легирующие элементы (ванадий, вольфрам, молибден, титан и др.) способствуют образованию наследственно мелкозернистой макроструктуры. Такая сталь при высоких температурах хорошо поддается любому виду обработки деформированием (прокатка, ковка, штамповка и др.). Укрупнения зерна и снижения механических свойств при этом не происходит. Как правило, большинство легированных сталей, а также спокойные стали — наследственно мелкозернистые. Все кипящие стали — наследственно крупнозернистые, имеют низкую ударную вязкость и высокую хладноломкость. 1.2 Превращения при охлаждении
При охлаждении сталей с аустенитной структурой могут происходить различные превращения, зависящие от скорости охлаждения. Рассмотрим диаграмму изотермического превращения аустенита в перлит (рис. 6.3).
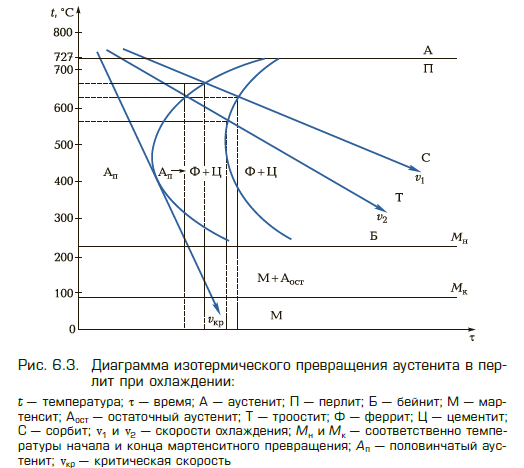
Кривые превращения аустенита имеют С-образную характеристику и показывают, что скорость превращений неодинакова. Максимальная скорость превращения соответствует охлаждению ниже Ас1, (727˚С) на 170˚С. Кривые начала и конца превращений смещены вправо и соответствуют наибольшей устойчивости.
Левая кривая на диаграмме соответствует границе начала превращений, правая кривая показывает конец превращения аустенита. Превращение аустенита в перлит носит диффузионный характер.
Скорость диффузии зависит от степени переохлаждения или от скорости охлаждения. Продукты перлитного превращения имеют пластинчатое строение, определены как перлит, сорбит и троостит и различаются степенью дисперсности. Но если перлит— это равновесная структура, то сорбит и троостит— неравновесные структуры, в них содержание углерода больше или меньше 0,8%. Существует еще промежуточное (бейнитное) превращение в области температур 500...350˚С. При большей степени переохлаждения (до 230 ˚С) аустенит находится в неустойчивом состоянии, диффузионные процессы отсутствуют, образуется перенасыщенный углеродом твердый раствор.
Мартенситное превращение в стали имеет три особенности. Во- первых, мартенситное превращение имеет бездиффузионный характер. Во-вторых, кристаллы мартенсита ориентированы. Третья особенность заключается в том, что мартенситное превращение происходит при непрерывном охлаждении в интервале определенных температур для каждой стали. Температуру начала мартенситного превращения называют мартенситной точкой и обозначают Мн, а температуру окончания обозначают Мк. Положение точек Мн и Мк на диаграмме зависит от количества углерода в стали и присутствия легирующих элементов. Как правило, большое содержание углерода и наличие легирующих элементов понижают положение точек.
Наложим на диаграмму графики скоростей охлаждения и изобразим схему влияния скорости охлаждения на температуру превращений аустенита. Из диаграмм видим, что чем больше скорость охлаждения, тем дисперснее получаемая структура. При небольшой скорости v1, образуется перлит, при большей скорости v2 — сорбит и еще большей vкр — троостит. При скорости охлаждения, большей, чем vкр, часть аустенита превращается в мартенсит. Минимальная скорость охлаждения, при которой весь аустенит переохлаждается до точки Мн и превращается в мартенсит, называется критической скоростью закалки. Этот процесс превращения в мартенсит имеет большое практическое значение и положен в основу термической обработки.
Перлитное превращение в стали применяют в процессе отжига; мартенситное — при закалке; промежуточное — при изотермической закачке.
Механические свойства стали со структурами перлита, сорбита и троостита зависят от степени понижения температуры распада и дисперсности ферритно-цементитной структуры. При этом твердость, пределы прочности, текучести и выносливости возрастают.
Структура мартенсита имеет более высокую твердость и прочность, а также зависит от содержания углерода в стали. Отрицательным фактором мартенситной структуры является повышенная хрупкость. Как уже говорилось, легирующие элементы влияют на положение точек Мн и Мк и соответственно влияют на практическую скорость закачки, обычно в сторону уменьшения.
1.3 Перлитное превращение
Перлитное превращение переохлажденного аустенита протекает при температурах Ar1 - 500˚C (см. рис. 112). В процессе превращения происходит полиморфное γ → α - превращение и диффузионное перераспределение углерода в аустените, что приводит к образованию ферритно-цементитной структуры:
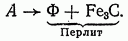
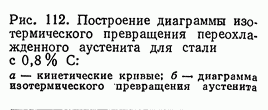
Аустенит, практически однородный по концентрации углерода, распадается с образованием феррита (почти чистое железо) и цементита, содержащего 6,67 % C, т. е. состоит из фаз, имеющих различную концентрацию углерода (рис. 113). Ведущей, в первую очередь возникающей фазой при этом является карбид (цементит). Его зародыши, как правило, образуются на границах зерен аустенита.
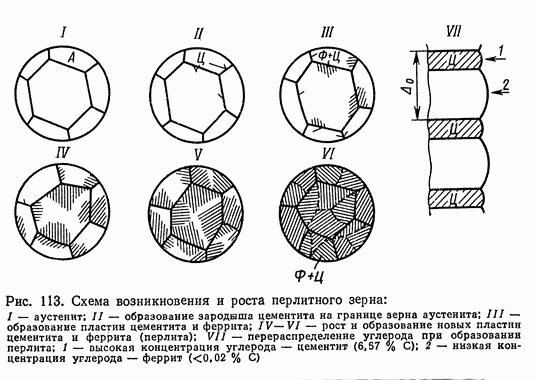
В результате роста частиц этого карбида прилегающий к нему объем аустенита обедняется углеродом, снижает свою устойчивость и испытывает полиморфное γ → α - превращение. При этом кристаллики феррита зарождаются на границе с цементитом, который облегчает этот процесс.
Последующий рост ферритных пластинок ведет к обогащению окружающего аустенита углеродом, что затрудняет дальнейшее развитие γ → α - превращения. В обогащенном таким образом углеродом аустените зарождаются новые и растут ранее возникшие пластинки цементита. Вследствие этих процессов образования и роста частиц карбидов вновь создаются условия для возникновения новых и роста имеющихся кристалликов (пластинок) феррита. В результате происходит колониальный (совместный) рост кристалликов феррита и цементита, образующих перлитную колонию (рис. 113).
Продукты перлитного превращения имеют пластинчатое строение. Пластинчатые структуры эвтектоидного типа часто определяют как перлит, сорбит и троостит или соответственно грубо-, средне- и тонкодифференцированный перлит. Чем больше переохлаждение, тем тоньше получается ферритно-цементитная структура, т. е. меньше межпластинчатое расстояние ∆0 (рис. 113), равное усредненной сумме толщин двух пластинок феррита и цементита, и выше твердость:

Перлит, сорбит и троостит, образующиеся при диффузионном распаде переохлажденного аустенита, являются ферритно-цементитными структурами, имеющими пластинчатое строение и различающимися лишь степенью дисперсности (рис. 114).
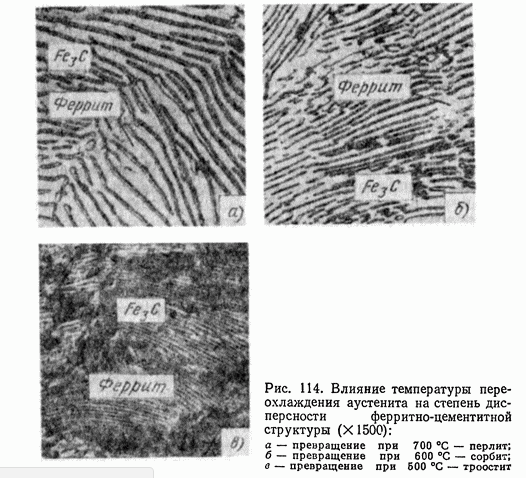
Однако в отличие от перлита (эвтектоида) сорбит и троостит, называемые квазиэвтектоидными, не являются равновесными структурами в сталях, не соответствующих эвтектоидному составу (содержат углерода больше или меньше 0,8 %).
Механические свойства стали со структурами перлита, сорбита и троостита.Твердость и прочность стали с указанными структурами прямо пропорциональна площади поверхности раздела между ферритом и цементитом, поэтому с увеличением степени дисперсности ферритно-цементитной структуры, т. е. с понижением температуры ее распада, твердость, пределы прочности, текучести и выносливости возрастают (рис. 115).
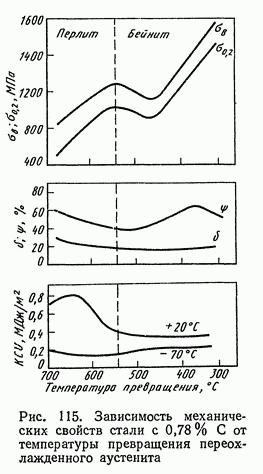
Относительное удлинение и относительное сужение наивысшие у сорбита. При переходе к трооститу (более низкой температуре превращения) вязкость (KCU) уменьшается.
Изотермическое превращение аустенита в доэвтектоидных и заэвтектоидных сталях.В этих сталях (рис. 116) в отличие от эвтектоидной стали в верхнем интервале температур сначала выделяются избыточные фазы — феррит (в доэвтектоидной стали) или избыточный цементит (в заэвтектоидной стали).
Начало выделения избыточного феррита (цементита) на диаграмме изотермического распада отмечается дополнительной кривой (рис. 116, б и в). Количество выделяющегося избыточного феррита (или цементита) уменьшается с понижением температуры, и при некоторой степени переохлаждения распад начинается непосредственно с образования зародышей эвтектоида или, точнее, квазиэвтектоида, т. е. структуры эвтектоидного типа, но отличающейся иным составом, чем перлит (эвтектоид).
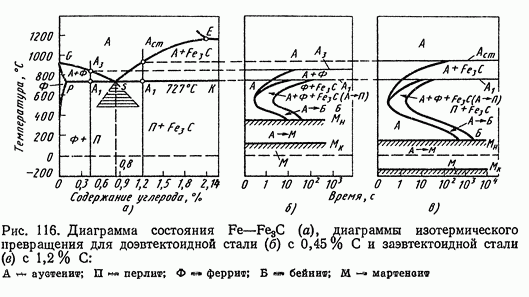
Так как с понижением температуры количество выделяющегося избыточного феррита (цементита) уменьшается, то квазиэвтектоид сорбит и троостит в доэвтектоидных сталях содержит углерода <0,8%, а в заэвтектоидных сталях > 0,8%.
Увеличение содержания углерода в аустените доэвтектоидной концентрации несколько повышает его устойчивость (кривые изотермической диаграммы сдвигаются вправо; см. рис. 116).
1.4 Промежуточное (бейнитное) превращение
Природа бейнита. Бейнитное (промежуточное) превращение протекает в температурной области между перлитным и мартенситным превращениями (см. рис. 112). В результате промежуточного превращения образуется бейнит, представляющий собой структуру, состоящую из α - твердого раствора, претерпевшего мартенситное превращение и несколько пересыщенного углеродом, и частиц карбидов. Различают структуру верхнего и нижнего бейнита. Верхний бейнит, образующийся обычно в области температур ⁓ 500-350 ˚С, имеет «перистый» вид (типа резаной соломы). Частицы карбидов выделяются не в виде пластинок, как в перлите, а в виде изолированных узких частиц (рис. 122, а). Нижний бейнит образуется обычно при температурах от 350˚С до точки Мн и имеет игольчатое (пластинчатое) строение (рис. 122, б). Карбидные частицы в нижнем бейните располагаются в пластинках α - фазы (рис. 122, в).
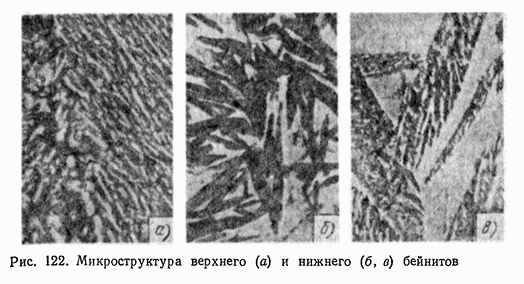
Механизм промежуточного превращения. Бейнитное (промежуточное) превращение переохлажденного аустенита сочетает в себе элементы перлитного и мартенеитного превращений: диффузионное перераспределение углерода в аустените между продуктами его распада и мартенситное бездиффузионное превращение.
Бейнитное превращение протекает при температурах, когда самодиффузия железа и диффузия легирующих элементов практически невозможны, а диффузия углерода еще достаточно высока. Это и предопределяет особенности бейнитного превращения. В начале этого превращения происходит диффузионное перераспределение углерода в аустените, что приводит к образованию в нем объемов, обогащенных и обедненных углеродом. Участки аустенита с низким содержанием углерода, у которых точка Мн лежит в области температур промежуточного превращения, претерпевают γ → α -превращение по мартенситному механизму. В объемах аустенита, обогащенных углеродом, если их пересыщение высокое, в процессе изотермической выдержки могут выделяться частицы карбидов, что, естественно, приведет к обеднению этих участков аустенита углеродом и к протеканию в них превращения по мартенситному механизму. Мартенситный механизм образования а-фазы обусловливает ее мартенситную структуру и появление характерного рельефа на поверхности микрошлифов, особенно заметного при образовании нижнего бейнита.
Образующаяся при бейнитном превращении α - фаза (мартенсит) пересыщена углеродом и при том тем сильнее, чем ниже температура превращения. В связи с этим сразу после γ → α - превращения, если диффузионная подвижность при данной температуре достаточная, из пересыщенного а-раствора могут выделяться частицы карбидов. Механизм образования верхнего и нижнего бейнита в принципе одинаков. Различие состоит в том, что в области образования верхнего бейнита вначале происходит более значительная дифференциация по концентрации углерода в кристаллах аустенита, что вызывает более сильное обогащение объемов аустенита углеродом и, следовательно, образование более обедненной углеродом α - фазы, поэтому выделение карбидов происходит главным образом из аустенита.
При образовании нижнего бейнита, наоборот, обогащение аустенита углеродом обычно сравнительно невелико, а пересыщение α - фазы более значительно, поэтому карбиды выделяются главным образом в кристаллах α - фазы (см. рис. 122, в).
Рассматриваемое промежуточное превращение как и мартенситное чаще не идет до конца. Нераспавшийся при изотермической выдержке аустенит при последующем охлаждении может в той или иной степени претерпевать мартенситное превращение или сохраняться (остаточный аустенит).
Механические свойства стали с бейнитной структурой. Образование верхнего бейнита (распад при 550-450 °С) снижает пластичность стали по сравнению с получаемой для продуктов распада аустенита в перлитной области (см. рис. 115). Твердость и прочность при этом не изменяются или несколько снижаются.
Пониженная пластичность верхнего бейнита связана с выделением сравнительно грубых карбидов по границам ферритных зерен.
В результате распада аустенита в нижней области промежуточного превращения (см. рис. 115) наблюдается некоторое повышение прочности, твердости и пластичности.
Нижний бейнит по сравнению с продуктами распада аустенита в перлитной области (сорбит, троостит) имеет более высокую твердость и прочность при сохранении высокой пластичности.
Высокие прочностные свойства нижнего бейнита объясняются наличием внедренных атомов углерода и большой плотностью дислокаций в мартенситной α-фазе, а также образованием включений дисперсных карбидов, расположенных в кристаллах этой фазы.
1.5 Мартенситное превращение
Природа мартенсита. Мартенсит является упорядоченным пересыщенным твердым раствором внедрения углерода в α - железе. Если в равновесном состоянии растворимость углерода в α - железе при 20˚С не превышает 0,002% то его содержание в мартенсите может быть таким же, как в исходном аустените, т. е. может достигнуть 2,14%
Атомы углерода занимают октаэдрические поры вдоль оси [0.01] в решетке α - железа (мартенсита) и сильно ее искажают. Мартенсит имеет тетрагональную решетку (рис. 117, а), в которой один период «с» больше другого — «а». При увеличении содержания углерода высота тетрагональной призмы «с» увеличивается, а размеры ее основания уменьшаются (рис. 117, б).
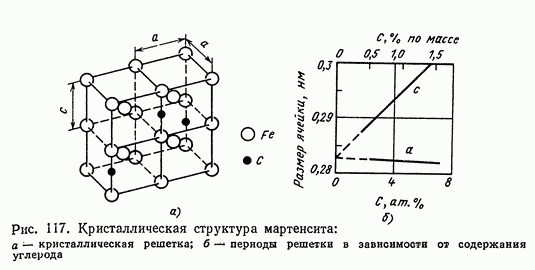
Следовательно, чем больше в мартенсите углерода, тем больше отношение с/а, т. е. больше тетрагональность решетки. Отношение с/а = 1 + 0,046С, где С — концентрация углерода в аустените, % по массе.
Механизм мартенситного превращения. Мартенситное превращение происходит только в том случае, если быстрым охлаждением аустенит переохлажден до низких температур, при которых диффузионные процессы становятся невозможными. Превращение носит бездиффузионный характер, т. е. оно не сопровождается диффузионным перераспределением атомов углерода и железа в решетке аустенита.
Мартенситное превращение осуществляется путем сдвига и не сопровождается изменением состава твердого раствора.
Сдвиговый механизм превращения отличается закономерным кооперативным направленным смещением атомов в процессе перестройки решетки. Отдельные атомы смещаются относительно друг друга на расстояния, не превышающие межатомные, сохраняя взаимное соседство, однако величина абсолютного смещения растет пропорционально удалению от межфазной границы. Это приводит к макроскопическому сдвигу, внешним проявлением которого является микрорельеф на поверхности металлического шлифа (рис. 118, а). В процессе превращения кристаллы мартенсита сопряжены с аустенитом по определенным кристаллографическим плоскостям и межфазная граница не образуется.
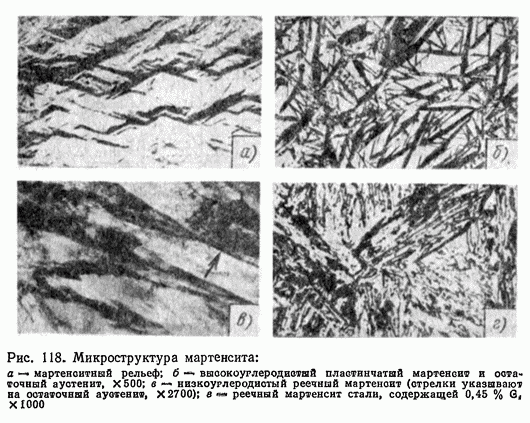
Пока на границе мартенсита и аустенита существует сопряженность решеток (когерентность), скорость образования и роста кристаллов мартенсита очень велика (⁓103 м/с).
В процессе роста мартенситного кристалла вследствие разности удельных объемов аустенита и мартенсита увеличиваются упругие напряжения в области когерентного сопряжения, что в конечном счете приводит к пластической деформации и образованию межфазной границы с неупорядоченным расположением атомов. Сопряженность решеток нарушается и по достижении растущим кристаллом границы зерна (субграницы) или других дефектов кристалла. При нарушении когерентности решеток дальнейший упорядоченный переход атомов из аустенита в мартенсит становится невозможным, и рост кристалла мартенсита прекращается.
Диффузионный переход атомов из кристаллов аустенита в мартенсит при низких температурах невозможен. Дальнейшее превращение протекает в результате образования новых кристаллов мартенсита.
Кинетика мартенситного превращения. Мартенситное превращение в общем случае не удается подавить быстрым охлаждением, как это может быть при диффузионных превращениях. При переохлаждении до температуры, соответствующей точке Мн, аустенит начинает превращаться в мартенсит. Следовательно, температура, отвечающая точке Мн, соответствует началу мартенситного превращения.
Чтобы мартенситное превращение развивалось, необходимо непрерывно охлаждать сталь ниже температуры Мн. Если охлаждение прекратить, то мартенситное превращение практически также остановится. Эта особенность мартенситного превращения резко отличает его от диффузионного перлитного, которое полностью протекает в изотермических условиях при температуре ниже точки А1. Зависимость количества образовавшегося мартенсита от температуры, до которой охлажден образец, может быть выражена так называемой мартенситной кривой (рис. 119).
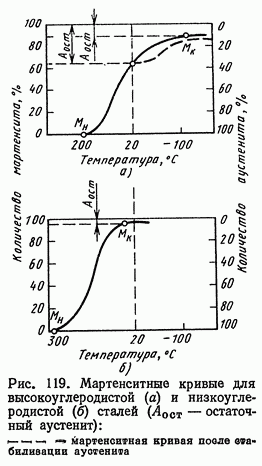
Чем ниже температура, тем больше образуется мартенсита. Количество мартенсита при этом возрастает в результате образования все новых и новых кристаллов, а не вследствие роста уже возникших кристаллов, имеющих некогерентную границу. По достижении определенной для каждой стали температуры превращение аустенита в мартенсит прекращается. Эту температуру окончания мартенситного превращения обозначают Мк. Положение точек Мк и Мн не зависит от скорости охлаждения и обусловлено химическим составом аустенита. Чем больше в аустените углерода, тем ниже температура точек Мк и Мн. Все легирующие элементы, растворенные в аустените, за исключением кобальта и алюминия, понижают точки Мк и Мн.
Мартенситное превращение очень чувствительно к напряжениям, а деформация аустенита может вызывать превращение даже при температурах выше Мн (мартенсит деформации).
Кристаллы мартенсита в зависимости от состава стали, а следовательно, и от температуры своего образования могут иметь различные морфологию и субструктуру. Различают два типа мартенсита - пластинчатый и реечный (рис. 121). Пластинчатый мартенсит образуется в высокоуглеродистых сталях, характеризующихся низкой температурой мартенситной точки (см. рис. 119, 120). В этом случае кристаллы мартенсита состоят в средней своей части из большого числа микродвойников, образующих среднюю зону повышенной травимости, называемую нередко мидрибом (рис. 121).
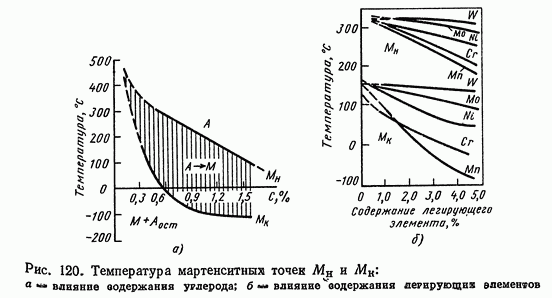
На рис. 118, б приведена микроструктура такого мартенсита. Его кристаллы представляют собой широкие пластины. В плоскости шлифа они имеют вид игл.
Наиболее часто (конструкционные углеродистые и легированные стали) кристаллы мартенсита имеют форму тонких реек (реечный мартенсит), вытянутых в одном направлении (см. рис. 118, в, 121). Чаще образуется и наблюдается пакет из реек (см. рис. 121). Такой высокотемпературный мартенсит называют массивным, в отличие от игольчатого (см. рис. 118).
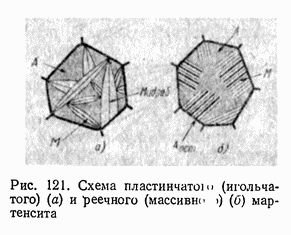
Тонкая структура реечного мартенсита сложна и представляет собой запутанные дислокации высокой плотности (⁓1012 см-2) при отсутствии двойниковых кристаллов. В легированных сталях нередко внутри мартенситных пакетов между кристаллами мартенсита сохраняются прослойки остаточного аустенита (см. рис. 118, в и г и 121, б).
Размеры кристаллов любой морфологии мартенсита определяются величиной исходного зерна аустенита. Они тем крупнее, чем больше зерно аустенита. Первая пластина мартенсита имеет протяженность, соответствующую поперечному размеру зерна аустенита. Кристаллы, образующиеся при более низких температурах, стеснены в своем развитии и имеют меньшие размеры (см. рис. 121).
1.6 Превращение в закаленных сталях при отпуске
Отпуск заключается в нагреве закаленной стали, структура которой состоит из тетрагонального мартенсита и остаточного аустенита, до температур ниже Ас1, выдержке при этой температуре и последующем охлаждении. Так как мартенсит представляет собой перенасыщенный твердый раствор углерода в Feα то структура закаленной стали является нестабильной и при отпуске протекают процессы, приводящие к равновесному состоянию стали, что, очевидно, будет достигаться выделением углерода из мартенсита и остаточного аустенита.
Дилатометрические исследования процессов, протекающих при отпуске закаленной углеродистой стали выявляют три температурных интервала изменения длины образцов: уменьшение при 150 °С, увеличение при 150-300 °С и снова уменьшение длины при 300-400 °С (рис. 218). С дилатометрическими данными коррелируют результаты измерения электросопротивления, магнитной индукции и других свойств. Соответствующие превращения при отпуске называются первым, вторым и третьим. Так как исходной является структура, состоящая из мартенсита и аустенита, а удельный объем мартенсита выше, чем у аустенита, то при превращении мартенсита объем будет уменьшаться (сжатие образца), а при превращении аустенита — увеличиваться (расширение образца). Таким образом первое и третье превращения связаны с изменениями состояния мартенсита, а второе — с изменением состояния аустенита.
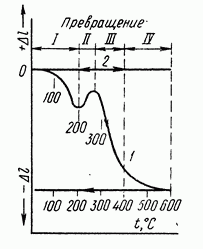 
Большую роль в выяснении сущности процессов, протекающих при отпуске, играют рентгеноструктурные исследования. Было установлено, что первое превращение связано с распадом мартенсита, второе с распадом остаточного аустенита и третье с дораспадом мартенсита и карбидообразованием (рис. 219). Дальнейшие исследования, проведенные с привлечением самых разнообразных методов исследования показали, что деление процессов, протекающих при отпуске на три стадии довольно условно; кроме того, в температурные интервалы значительные поправки могут вносить легирующие элементы.
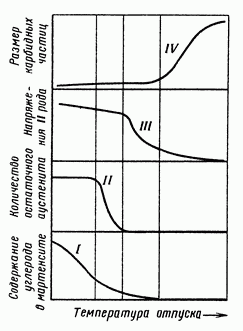 
Игольчатый характер строения мартенсита сохраняется до высоких температур и только при продолжительном отпуске при 650 °С вместо игольчатой мартенситной структуры наблюдаются равновесные мелкие ферритные зерна. Дальнейшее повышение температуры приводит к процессам возврата (преимущественно уменьшению плотности дислокаций) в феррите и рекристаллизации ферритных зерен.
Сталь, отпущенная при 350 - 500 °С, имеет структуру троостита (рис. 220, а), а при 500 - 600 °С — структуру сорбита (рис. 220, б). Эти структуры представляющие собой смесь цементита и феррита, различаются по твердости и степени дисперсности цементитных частиц.
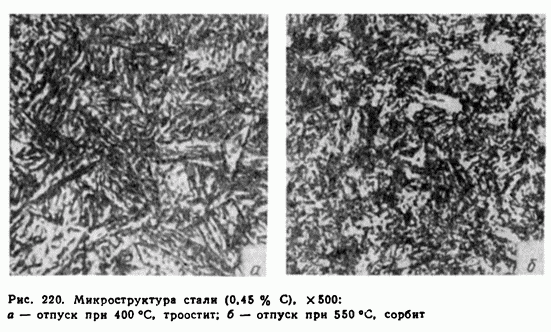
|
|
|