боранбаев отчет (2). Утверждаю И. о зам. Председателя Правления по академической работе
![]()
|
|
| Введение | 3 |
1 | Особенности процесса резания композитов | 4 |
2 | Материалы и методы | 9 |
3 | Виды обработок | 12 |
3.1 | Лезвийная обработка МКМ | 12 |
3.2 | Ультразвуковые способы формообразования | 13 |
3.3 | Обработка с применением лазерных технологий | 16 |
3.4 | Гидроабразивная резка | 18 |
| Заключение | 19 |
| Список использованной литературы | 20 |
Введение
Казахстанское машиностроение является важнейшей отраслью, обеспечивающей в экономике страны как переход к новым технологическим укладам, так и развитие уже распространенного четвертого уклада. Однако, выполнить данную роль машиностроение сможет при условии быстрой модернизации и технического перевооружения своего производственного аппарата, который на сегодняшний день серьезно изношен и мало конкурентоспособен.
Вследствие стремительного развития материаловедения использование композиционных материалов стало повсеместным. Появление новых композиционных материалов с уникальным сочетанием свойств, которые превосходят свойства классических материалов, требует в машиностроении разработки и внедрения новых технологических методов их обработки, характеризующихся повышенной точностью и производительностью. Развитие механической обработки направлено на получение высокоточных изделий с минимальными затратами и автоматизацию оборудования.
Композитный материа́л (КМ), компози́т — многокомпонентный материал, изготовленный из двух или более компонентов с существенно различными физическими или химическими свойствами, которые, в сочетании, приводят к появлению нового материала с характеристиками, отличными от характеристик отдельных компонентов и не являющимися простой их суперпозицией. При этом отдельные компоненты остаются таковыми в структуре композитов, отличая их от смесей и твёрдых растворов. В составе композита принято выделять матрицы и наполнители. Варьируя состав матрицы и наполнителя, их соотношение, ориентацию наполнителя, получают широкий спектр материалов с требуемым набором свойств. Многие композиты превосходят традиционные материалы и сплавы по своим механическим свойствам и в то же время они легче. Использование композитов обычно позволяет уменьшить массу конструкции при сохранении или улучшении её механических характеристик.
Благодаря своим высоким механическим показателям в сочетании с низкой плотностью, КМ находят все более широкое применение в авиастроении, космической технике, морских сооружениях, трубопроводах, электронике, автомобилестроении и многих других областях.
.
1 Особенности процесса резания композитов
Особенностью композитов является, как отмечалось выше, совмещение технологического процесса получения материала с технологическим процессом изготовления готового изделия. Прогрессивные методы, такие как намотка, прессование, литье, экструзия и т.д., позволяют получать изделия из композитов относительно высокой точности и качества поверхности. Однако весьма существенный объем механической обработки всегда остается. Поскольку речь идет только о высокопрочных материалах, полученных, главным образом, намоткой и прессованием, то необходимые операции механической обработки рассмотрим применительно к изделиям, характерным именно для этих методов формования. Это, в первую очередь, различные по размерам оболочки, плиты и изделия относительно простой формы. Для получения окончательной формы и размеров готовых изделий необходимо применять почти все существующие виды механической обработки [1].
Механическая обработка необходима для достижения требуемой точности и качества поверхности, получения сложных конфигураций изделия. Это вполне оправдано, особенно при сравнительно небольших объемах производства идентичных изделий, когда разработка и изготовление сложных форм оказываются экономически невыгодными. Она необходима для разрезки изделий до требуемых размеров, а также для получения образцов, с помощью которых определяются физико-механические характеристики готовых изделий, например, оболочек из композитов.
При изготовлении изделий из композитов применяют следующие виды механической обработки: точение (наружное и подрезка торца), сверление и развертывание, фрезерование, разрезка, шлифование и нарезание резьбы.
Точение применяется для обработки сопрягаемых поверхностей оболочек, конических участков, для проточки шеек под нарезание резьбы, а также для подрезания торцов заготовок и необходимых канавок, например, при установке уплотняющих элементов. Точение применяют и для сложного ступенчатого профиля оболочки. Кроме того, с помощью токарной обработки можно получить отдельные детали относительно небольших размеров из различных единичных заготовок.
Сверление - одна из наиболее распространенных операций механической обработки композитов. В плитах и пластинах - это сверление различных отверстий под крепежные элементы и для других эксплуатационных целей, в оболочках - это, главным образом, сверление большого количества сквозных и глухих отверстий для штифто-болтового соединения оболочки с другими элементами конструкции. При необходимости получения отверстий более высокой точности, а главным образом, более высокого качества их поверхности, иногда применяется операция развертывания.
Фрезерование применяют для прорезки пазов, вырезки окон, лючков, для получения различного рода канавок и уступов, причем при обработке материалов типа стекло-, органо-, боро- и углепластиков -фрезерование концевыми, дисковыми и шпоночными фрезами и значительно реже - торцовыми и цилиндрическими.
Разрезка является также весьма распространенным видом механической обработки композитов. Она необходима как при получении требуемых размеров изделий, так и при изготовлении образцов для определения физико-механических характеристик композитов. При разрезке основным требованием является требование к качеству реза -шероховатости поверхности и минимальной его ширине.
Шлифование при обработке композитов применяют как отделочную операцию, главной целью которой является обеспечение качества поверхности. Отсюда требования, предъявляемые к этой операции, - это обеспечение требуемого параметра шероховатости поверхности. Основные виды шлифования - наружное круглое шлифование и плоское шлифование периферией круга.
Нарезание резьбы. В изделиях из композитов нарезают крепежные резьбы - метрические и специального профиля. Нарезание метрической резьбы, особенно внутренней, производят метчиками. Резьбу специального профиля, как правило, прямоугольного, нарезают абразивными или алмазными кругами и очень редко резцом.
Обработка резанием композитов обладает рядом специфических особенностей, определяемых, главным образом, особенностью их структуры и свойств. В то же время процессу резания композитов сопутствуют те же явления, что и при резании металлов, т.е. наблюдаются стружкообразование, силовые и тепловые явления, интенсивное изнашивание режущего инструмента. Каждое из перечисленных явлений в той или иной мере отличается от аналогичных явлений при резании металлов.
Процесс резания композитов имеет ряд особенностей:
1. Анизотропия свойств материалов. Если металлы, имеющие кристаллическое строение, с определенным допущением можно считать изотропными, то композиты, наполнителем в которых являются волокнистые материалы различного состава, обладают анизотропией свойств. Это определяет различие процесса резания, в частности стружкообразования, при обработке вдоль и поперек армирующих волокон. Существенным образом схема армирования будет влиять и на качество получаемой поверхности, поэтому при разработке технологической операции механической обработки следует учитывать и направление обработки относительно направления армирования.
2. Относительная сложность получения высокого качества поверхности. Вследствие невысоких прочностных характеристик полимерных композиционных материалов (особенно при повышенных температурах), а также из-за их слоистой структуры и в ряде случаев низкой адгезионной связи наполнителя со связующим их обработку следует производить острозаточенным инструментом. При больших затуплениях инструмента из-за низкой адгезии связующего с армирующим волокном при увеличении сил резания образуются трещины между волокном и связующим, происходят выкрашивания связующего с обрабатываемой поверхности изделия, особенно в местах входа и выхода инструмента, что, естественно, сказывается на качестве обработки. Слоистая структура приводит к тому, что при повышенных износах инструмента происходит расслоение материала. Кроме того, при перерезании армирующих волокон, особенно при перекрестном армировании, наблюдается разлохмачивание перерезанных волокон, что ухудшает качество обработанной поверхности и заставляет иногда применять дополнительную отделочную операцию, например, зачистку шкуркой.
3. Высокая твердость наполнителя. Например, у материалов на основе волокон бора микротвердость наполнителя составляет 40-43 ГПа, что превосходит твердость таких инструментальных материалов, как быстрорежущие стали и твердые сплавы, и соизмерима с микротвердостью сверхтвердых материалов - натуральных алмазов (98,1 ГПа), синтетических алмазов АС6 (89 ГПа) и Эльбора-Р (84 ГПа). Поэтому для обработки таких материалов могут быть применены только сверхтвердые материалы (СТМ), причем и в этом случае проблема обработки не снимается, ибо соотношение микротвердостей инструментального и обрабатываемого материалов составляет всего 2,5, тогда как для эффективного осуществления процессов резания соотношение микротвердостей должно составлять 4-6.
4. Низкая теплопроводность композитов. Низкая теплопроводность композитов существенно влияет на соотношение составляющих общего теплового баланса. Так, теплопроводность композитов составляет 0,14-0,50 Вт/(мК), что в несколько сот раз меньше, чем у металлов. Это обусловливает слабый отвод теплоты со стружкой и в обрабатываемое изделие, поэтому при обработке композитов основная доля теплоты отводится через режущий инструмент. Так, расход теплоты при обработке полимерных композиционных материалов распределяется следующим образом: в инструмент - 90%, в стружку - 5%, в обрабатываемую деталь - 5%. В то же время при обработке металлов порой до 90% теплоты уносится стружкой и только 10% поглощается деталью и инструментом. Такое перераспределение расходной части теплового баланса накладывает определенные условия на применяемый режущий инструмент, который должен интенсивно отводить выделяющуюся в зоне резания теплоту.
5. Абразивное воздействие наполнителя. Из всех видов пластмасс наибольшие трудности вызывает обработка композитов, так как наполнителем в них являются стеклянные, борные или угольные волокна, обладающие высокой твердостью и абразивной способностью. Наличие в зоне резания твердых составляющих приводит к абразивному износу инструмента, который при обработке некоторых композитов, например, боропластиков, имеет преобладающее значение. Следовательно, обработка резанием композитов определяется во многом свойствами наполнителя.
6. Деструкция полимерного связующего при резании. Характерной особенностью пластмасс, и композитов в частности, является наличие в материале полимерного связующего. При воздействии в процессе резания механических нагрузок и выделяющейся в зоне резания теплоты происходит неизбежная деструкция связующего. Деструкция происходит за счет действия больших локальных напряжений и высокой температуры, превышающей теплостойкость полимера, и заключается в том, что происходит массовый разрыв химических связей у молекулярных цепей полимера, образуется большое количество свободных макрорадикалов, обладающих избыточной энергией. В результате этого образуется вязко-текучий в микрообъемах полимер, являющийся поверхностно-активным веществом (ПАВ). Мигрируя по поверхности механически напряженного режущего клина инструмента и по дефектам его поверхности, деструктированный полимер ПАВ снижает поверхностную энергию металла (эффект Ребиндера), что облегчает отрыв от его поверхности отдельных микро- и макрочастиц. В результате этого возникает механо-химический адсорбционный износ инструмента, который характерен только для обработки полимерных материалов.
7. Высокие упругие свойства композитов. Композиты обладают высокими упругими свойствами, что определяет особенности процесса резания. Из-за высоких упругих характеристик обрабатываемого материала происходит упругое восстановление слоя обрабатываемого материала, лежащего над поверхностью резания. Это приводит к увеличенным площадкам контакта, и, как следствие этого, к повышенным значениям сил резания. Учет этих сил при обработке композитов необходим из-за интенсивных контактных явлений на задних поверхностях инструмента (его износ происходит главным образом по задней поверхности и путем округления режущей кромки). Упругое восстановление обработанной поверхности следует учитывать и при оценке точности обработки. Силы резания при обработке композитов в 10-20 раз ниже, чем при аналогичной обработке металлов, а упругие характеристики выше, поэтому точность их обработки в меньшей мере определяется упругими деформациями системы станок - приспособление - инструмент.
8. Технологический критерий износа. Характерным при обработке композитов является технологический критерий износа инструмента. Поскольку из-за слоистой структуры материалов, а иногда из-за низкой адгезии наполнителя и связующего при обработке композитов образуются характерные дефекты поверхности, такие как сколы, расслоения, разлохмачивание, прижоги, то при определении допустимого износа преобладает технологический фактор - отсутствие этих дефектов и определенный уровень шероховатости поверхности, которая существенно зависит от степени износа инструмента. Поэтому допустимый износ инструмента при обработке композитов всегда ниже, чем при аналогичной обработке металлов и оценивается по технологическим факторам, определяющим качество поверхности.
9. Специфика процесса стружкообразования. При обработке композитов иначе, чем у металлов, происходит процесс стружкообразования, что объясняется, в первую очередь разницей их структур. Анизотропия свойств композитов определяет иные процессы стружкообразования и при резании в разных (по отношению к направлению армирования) направлениях. Высокие упругие свойства материала определяют процесс разрушения материала, который носит хрупкий характер. Получение в ряде случаев мелкодисперсной стружки ставит вопросы ее удаления и защиты от ее воздействия на обслуживающий персонал.
10. Низкая теплостойкость композитов. Существенной особенностью композитов является их низкая теплостойкость. В зависимости от типа связующего теплостойкость этих материалов составляет 160-300°С. При температурах выше указанных происходит выгорание связующего, на поверхности обработанной детали появляются прижоги. Поэтому уровень температур в зоне резания должен быть значительно меньше, чем при обработке металлов. Это усугубляется еще и тем, что в большинстве случаев не допускается применение смазочно-охлаждающих жидкостей (СОЖ). Как известно, композиты обладают таким свойством, как влагопоглощение, поэтому применение СОЖ во многих случаях влечет за собой введение дополнительной операции – сушки изделия. Следовательно, чаще всего приходится предусматривать механическую обработку изделий из композитов без применения СОЖ.
11. Выделение мелких частиц материала при резании. Обработка резанием композитов сопровождается выделением мельчайших частиц наполнителя, смешанного со связующим, выделением летучих, порой токсичных веществ, поэтому требования техники безопасности и производственной санитарии также будут носить специфический характер.
Перечисленные особенности обработки резанием композитов показывают, что простой перенос закономерностей процесса резания металлов на эти материалы недопустим.
2 Материалы и методы
Благодаря своим высоким механическим показателям в сочетании с низкой плотностью, КМ находят все более широкое применение в авиастроении, космической технике, морских сооружениях, трубопроводах, электронике, автомобилестроении и многих других областях[2-4].
Как правило, одна из фаз в КМ – непрерывная (матрица), которая может быть полимером, металлом или керамикой. Другая фаза является дисперсной (частицы) или непрерывной (волокна) и может состоять из стекла, графита, бора, арамидов и других различных оксидов, карбидов и нитридов. Матричная фаза обычно более пластичная и менее твердая, тогда как дисперсная фаза обычно тверже матрицы.
Основной вид механической обработки КМ – лезвийная обработка, в которой воздействие на материал происходит вращающимся режущим инструментом (точение, фрезерование, сверление, шлифование). Применяются также гидроабразивные, ультразвуковые и лазерные методы обработки.
Зарубежный опыт и отечественная практика показали, что обрабатываемость КМ по ряду критериев идентична, несмотря на различия по их составу и свойствам. Рационально разделять обрабатываемость КМ по атрибутам, что будет способствовать в дальнейшем определению оптимальных режимов обработки.
При лезвийной обработке многих КМ не допускается использование смазочно-охлаждающей жидкости (СОЖ) из-за риска набухания и расслоения материала, ввиду активизации процесса водопоглощения. В случае необходимости охлаждения заготовки без использования СОЖ, назначают охлаждение сжатым воздухом.
Особенности механической обработки КМ [1] представлены в табл. 1.
Таблица 1 – Обрабатываемость композиционных материалов (КМ) резанием
Атрибут структуры КМ | Влияние на свойства КМ | Влияние на обрабатываемость КМ |
Свойства матрицы | Твердость, прочность, жесткость, теплопроводность, вязкость | Обеспечение лучшей обрабатываемости при наличии оптимальной прочности матрицы |
Особенности укладки и ориентации волокон в матрице | Анизотропия свойств | Различие процесса резания вдоль и поперек армирующих волокон, возрастающая вероятность расслоения во время обработки при высокой анизотропии |
Тип армирующего волокна | Прочность, жесткость | С повышением прочности материала абразивное действие волокон и силы резания увеличивается |
Диаметр армирующего волокна | Увеличение диаметра волокна снижает прочность материала | Обрабатываемость ухудшается |
Длина волокна | – | При использовании коротких волокон материал более склонен к расслоению и вытягиванию волокон, что ухудшает обрабатываемость |
Механическая обработка металлических композиционных материалов (МКМ) и полимерных композиционных материалов (ПКМ) отличается применением как традиционных лезвийных и абразивных методов механической обработки (точение, фрезерование, шлифование и др.), так и новых методов (лазерное сверление, гидроабразивная резка и др.), а также комбинированных методов обработки. Для керамических композиционных материалов (ККМ) и углерод-углеродных композиционных материалов (УУКМ) применяют преимущественно ультразвуковую обработку.
Преимущества и недостатки методов механической обработки КМ[1] приведены в табл. 2.
Таблица 2 – Сравнительные характеристики методов механической обработки композиционных материалов (КМ)
Вид обработки | Достоинства | Недостатки |
Механическая (лезвийная) | Высокая точность обработки, низкая шероховатость обработанных поверхностей | Низкая стойкость режущего инструмента приводит к расслоению материала, вырыванию волокон, повышению температуры в зоне резания, вследствие этого возникает термическая деструкция матрицы КМ |
Гидроабразивная | Высокая производительность, возможность резки материала большой толщины, отсутствие термической деструкции матрицы КМ | Высокая шероховатость обработанных поверхностей, высокая вероятность насыщения материала водой |
Лазерная | Высокая точность обработки, отсутствие габаритных ограничений для деталей или заготовок | Термическая деструкция матрицы КМ с незначительным оплавлением краев в зоне резания, выделение дыма и пыли |
Ультразвуковая | Высокая точность обработки, низкая шероховатость обработанных поверхностей, отсутствие или минимальное расслоение материала | Низкие производительность и стойкость режущего инструмента |
3 Виды обработок
3.1 Лезвийная обработка МКМ
Для обеспечения заданной конфигурации изделий из МКМ лезвийная обработка включает операции точения, сверления, фрезерования и пр., в частности обработку на токарных и фрезерных станках, или в многофункциональных обрабатывающих центрах.
Токарную обработку МКМ используют для обработки тел вращения. При обработке длинномерных заготовок на универсальных токарно-винторезных станках (1К62, 16К20 и др.) используют люнеты, чтобы уменьшить прогибы обрабатываемого материала.
При обработке МКМ главной проблемой является обеспечение качества поверхностного слоя изделий, так как он играет ключевую роль в показателях эксплуатационных характеристик материала. При лезвийной обработке изменяется состояние слоя, происходит перерезание армирующих волокон, что приводит к снижению прочности до 20% [5]. Это связано с анизотропией свойств КМ, наличием у них слоистой структуры, высоких прочностных характеристик, низкой теплопроводности и высокой твердости наполнителя. Поэтому первоначально решают проблему выбора режущего инструмента.
Опытным путем выявлено, что при резании МКМ основной износ режущего инструмента, вызванный упругим восстановлением обрабатываемого материала после прохождения режущего клина, приходится на его заднюю поверхность (рис. 1). Износ по передней поверхности режущего инструмента не столь значителен и вызван высокой температурой в зоне резания, трением отделяющейся стружки и абразивным износом разрушаемого материала заготовки.
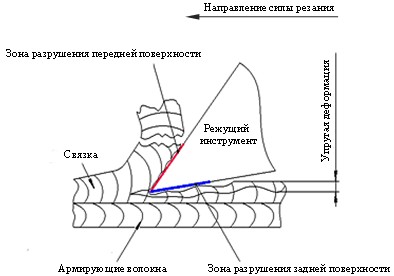
Рисунок 1 – Схема износа поверхностей режущего инструмента при лезвийной обработке металлического композиционного материала
В обработке МКМ [6-7] исследователи отметили превосходство режущего инструмента с покрытием из поликристаллического алмаза (PCD) и с профильной впайкой вставок из PCD над инструментом с покрытием из оксида алюминия или карбида титана (Al2O3/TiC) вследствие его более высокой твердости и теплопроводности, которая помогает эффективно выводить тепло из зоны резания. Инструмент с покрытием из поликристаллического кубического нитрида бора (PCBN) и PCD признан в обработке МКМ лучшим , чем твердосплавный инструмент без покрытия, содержащий в основном карбиды вольфрама (WC). В работе [8] отмечено, что вставки с CVD (химическое осаждение из паровой фазы) и PCD-покрытием при обработке МКМ значительно снижают износ инструмента. Вставки из PCBN, которые обладают исключительной твердостью в горячем состоянии и характеризуются хорошей прочностью и термостойкостью, используются при очень высоких скоростях резания и являются наилучшими по производительности в лезвийной обработке Al–SiC материалов.
3.2 Ультразвуковые способы формообразования
Во время ультразвуковой обработки материал удаляется режущим инструментом, которому передаются колебания. Такая обработка позволяет получать изделия сложной формы из твердых и хрупких труднообрабатываемых материалов, в том числе и КМ. Различают два метода ультразвуковой обработки.
Размерная ультразвуковая обработка – это процесс формообразования, при котором съем материала производится за счет режущего инструмента, колеблющегося с высокой частотой и низкой амплитудой в среде суспензии абразивного порошка (рис. 2) [9]. Инструмент перемещается вертикально или ортогонально к поверхности детали при амплитудах от 0,05 до 0,125 мм. Мелкие абразивные зерна смешивают с водой для образования суспензии, которая распределяется по части режущей поверхности и кончику инструмента. Типичные размеры зерен основной фракции абразивного материала варьируются от 1000 до 100 мкм (зернистость – от №10 до 80 по ГОСТ 52381–2005), где меньшие зерна (большее количество зерен) обеспечивают более гладкую поверхность. В результате процесса копируется форма режущего инструмента в изделии.
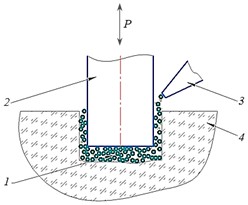
Рисунок 2 – Принцип размерной ультразвуковой обработки: 1 – суспензия абразивного порошка; 2 – режущий инструмент; 3 – подача суспензии; 4 – обрабатываемый материал (изделие)
При втором методе колебания накладываются непосредственно на вращающийся режущий инструмент. Значительных успехов в этом направлении добилась фирма-производитель обрабатывающего оборудования DMG MORI (Германия), представившая в 2013 г. линейку обрабатывающих центров ULTRASONIC, которые позволяют изготавливать детали сложной формы из труднообрабатываемых КМ, керамики, стекла и корунда. [10] Принцип работы обрабатывающих центров с технологией ULTRASONIC изображен на (рис. 3). Путем наложения ультразвуковых колебаний на осевое вращение режущего инструмента достигается сокращение силы резания до 40% в отличие от общераспространенных методов лезвийной механической обработки. Технология резания ULTRASONIC также позволяет повысить скорость и величину подачи, продлить срок службы режущего инструмента и обеспечить шероховатость Ra до 0,1 мкм.
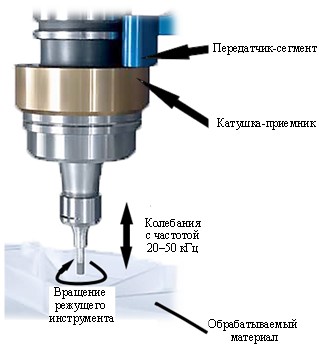
Рисунок 3 – Принцип технологии ультразвуковой обработки ULTRASONIC
При передаче ультразвуковых колебаний режущему инструменту происходит воздействие на взаимодействие вращающегося режущего инструмента и обрабатываемого материала:
– циклически меняются модуль и направление вектора действительной скорости резания;
– циклически меняются кинематические углы инструмента, в результате изменяются условия формирования поверхностного слоя детали, что приводит к улучшению его (слоя) качества (снижаются растягивающие остаточные напряжения);
– меняются условия трения на рабочих гранях и устраняется наклеп материала на инструмент;
– повышается динамическая устойчивость технологической системы «станок–приспособление–инструмент–деталь»;
– улучшаются условия доступности и проникновения смазочно-охлаждающей жидкости в зону резания;
– сокращаются силы и мощность, затрачиваемые на механическую обработку.
Точность и качество обработанной поверхности являются приоритетными факторами для конечной продукции, особенно это касается процесса получения отверстий. Наличие заусенцев негативно сказывается на процессе сборки изделия, поэтому существует практически единственный способ уменьшить или предотвратить образование заусенцев при обработке материалов – это применение ультразвуковых вибраций при операции сверления.
Дополнение металлорежущего оборудования ультразвуковыми устройствами, применение специализированного алмазного режущего инструмента и внедрение соответствующих технологических процессов открывают новые возможности в формообразовании КМ.
3.3 Обработка с применением лазерных технологий
Лазерная обработка позволяет реализовать широкий спектр технологических процессов и видов механической обработки. Наиболее распространены операции по раскрою листового материала по сложному контору, гравировке, наплавке, сварке (LBW), закалке, сверлению (одноимпульсное, ударное трепанирование (вырезание отверстий), сверление лазерным спиральным сверлом) и др. [11]
Раскрой листового материала является заготовительной операцией, подразумевающей размещение заготовок на листе. Лазерный раскрой считается прогрессивным методом раскроя и применяется при серийном производстве изделий практически из всех материалов, в том числе МКМ и ПКМ. Луч лазера, управляемый специализированным программным комплексом станка, обеспечивает концентрацию энергии, достаточную для прорезания листового материала любой толщины и состава.
Лазерная гравировка отличается тем, что изображение или текст наносится на какое-либо изделие с помощью сфокусированного лазерного луча и имеет некоторую глубину (рельеф).
В процессе лазерной наплавки материал наносится при помощи лазерного луча, используемого для создания ванны расплава, куда подается материал. В качестве присадки используют порошок или проволоку. Наплавку производят или непрерывным лазером, характеризующимся большей производительностью, или импульсным лазером, отличающимся большой пиковой мощностью.
Сварка материалов пучком лазера – LBW (Laser Beam Welding) – получила большое распространение в области автомобилестроения как автоматизированный процесс при работе с объемными конструкциями. Лазерный пучок в качестве концентрированного источника тепла образует узкие и глубокие сварные швы при высокой скорости сварки [21]. С помощью разностороннего LBW-процесса удается сваривать углеродистые, никелевые и коррозионностойкие стали, алюминий и титан. Однако из-за высокой скорости охлаждения при сварке высокоуглеродистых сталей возникает проблема появления трещин. Сварной шов имеет высокое качество, аналогичное получаемому при электронно-лучевой сварке (EBW). Скорость сварки пропорциональна мощности излучения лазера, но также зависит от типа и толщины обрабатываемого материала.
Некоторые из преимуществ LBW по сравнению с EBW заключаются в
следующем:
– лазерный луч передается через воздух, при этом не требуется условий вакуума;
– процесс легко автоматизируется с помощью робототехнического оборудования;
– при LBW отсутствует рентгеновское излучение;
– LBW – сварка более высокого качества.
Производная от LBW-процесса – гибридная лазерная сварка совмещает преимущества лазерной сварки с методом дуговой сварки. Это сочетание позволяет добиться большей точности перемещения лазера, так как сварка в защитном газе позволяет расплавить металл до заполнения стыка шва, а за счет использования лазера увеличивается скорость сварки сверх той скорости, которая обычно возможна при дуговой сварке в защитных газах (GMAW). Качество сварки при гибридной лазерной сварке, как правило, выше, чем при LBW-процессе.
Сверление отверстий с помощью лазерных технологий является методом с самым большим количеством операций. Такое сверление широко применяют для получения отверстий не только в материалах с высокой твердостью, но и при обработке особо хрупких материалов. Если сверление отверстий цельными сверлами диаметром <250 мкм является труднореализуемой практической задачей, то лазерное сверление позволяет получать отверстия диаметром, соизмеримым с длиной волны излучения, с достаточно высокой точностью позиционирования.
С помощью лазера также осуществляют метод прямого лазерного спекания (DMLS), который относится к сфере аддитивных технологий и позволяет в короткий срок получить детали и образцы любой формы из порошков высококачественной и инструментальной сталей, алюминия и титана. Метод DMLS имеет колоссальный потенциал для применения в промышленности благодаря реализуемости широкого круга задач при производстве.
При применении лазерных методов не происходит прямого механического воздействия на обрабатываемый материал, благодаря чему деформации сведены к минимуму, а точность максимальна. В процессе резания мощный световой поток фокусируется на определенном участке, вызывая плавление или испарение обрабатываемого материала.
Поскольку КМ характеризуются сочетанием нескольких материалов, выбор правильной длины волны лазера является ключевым параметром. Если матрица и армирующий компонент КМ органические, то они поглотят всю энергию лазерного луча (CO2). Если установить достаточно высокую мощность лазера, можно рассчитывать, что луч пройдет через весь обрабатываемый материал, оставляя ровные и чистые края.
Лазерная обработка является перспективным методом обработки как традиционных материалов, так и КМ. При этом решается широкий спектр задач, возникающих при механической обработке.
3.4 Гидроабразивная резка
Под гидроабразивной резкой подразумевают такой вид механической обработки, при котором удаление обрабатываемого материала происходит посредством воздействия на него струи воды, смешанной с твердым абразивным материалом, под высоким давлением и с высокой скоростью. [12] Такая механическая обработка позволяет получать высокое качество реза (шероховатость кромки Ra=1,6 мкм) в зависимости от обрабатываемого материала. В качестве абразива принято применять гранатовый песок, однако также используют карбид кремния или электрокорунд, повышающие скорость резания в 2–4 раза, но увеличивающие стоимость операции резки.
Гидроабразивная резка показывает высокую эффективность при обработке таких труднообрабатываемых материалов, как высокопрочные стали, керамика, титановые сплавы, а также при резке многослойных, сотовых и других КМ.
Заключения
В заключении хотелось бы сказать что современный технический уровень подготовки режущего инструмента для обработки КМ не до конца изучен, что задает направления для исследования новых материалов, повышающих стойкость режущего инструмента, а также разработки и внедрения конструкторско-технологических решений для рационализации процессов формообразования изделий из КМ.
Сведения, приведенные в научно-технической литературе, позволяют сделать вывод, что систематизированные данные о процессах формообразования изделий из КМ отсутствуют. Выполнение требований к геометрической форме и качеству поверхности изделий возможно, в частности, с помощью режимов резания, основанных на режимах обработки традиционных материалов. Все существующие эмпирические зависимости не учитывают анизотропные свойства существующих КМ.
Наиболее перспективными направлениями в области формообразования изделий из КМ являются методы лазерной обработки, совмещенные с аддитивными технологиями.
Автоматизация процессов обработки и комбинирование методов резания оказывают существенное влияние на процесс изготовления изделий в промышленности, позволяя получить качественный продукт в короткий срок и при низких затратах.
Список использованных источников
1. Раскутин А.Е., Хрульков А.В., Гирш Р.И. Технологические особенности механообработки композиционных материалов при изготовлении деталей конструкций (обзор) // Труды ВИАМ: электрон. науч.-технич. журн. 2016. №9. Ст. 12. URL: http://viam-works.ru (дата обращения: 10.09.2018). DOI: 10.18577/2307-6046-2016-0-9-12-12.
2. Оспенникова О.Г. Итоги реализации стратегических направлений по созданию нового поколения жаропрочных литейных и деформируемых сплавов и сталей за 2012–2016 гг. // Авиационные материалы и технологии. 2017. №S. С. 17–23. DOI: 10.18577/2071-9140-2017-0-S-17-23.
3. Антипов В.В. Перспективы развития алюминиевых, магниевых и титановых сплавов для изделий авиационно-космической техники // Авиационные материалы и технологии. 2017. №S. С. 186–194. DOI: 10.18577/2071-9140-2017-0-S-186-194.
4. Гращенков Д.В. Стратегия развития неметаллических материалов, металлических композиционных материалов и теплозащиты // Авиационные материалы и технологии. 2017. №S. С. 264–271. DOI: 10.18577/2071-9140-2017-0-S-264-271.
5. Карташов А.Б. Механическая обработка композитов [Электронный ресурс].URL: www.bmstu.ru/ps/kartashov/fileman/download/ПКМ2017/ПКМ_ВКМ_11.pdf (дата обращения: 10.09.2018).
6. Ravi Sekhar T.P. Singh Mechanisms in turning of metal matrix composites: a review // Journal of Materials Research and Technology. 2015. No. 4 (2). P. 197–207. URL: http://www.jmrt.com.br (дата обращения: 10.09.2018). DOI: 10.1016/j.jmrt.2014.10.013.
7. El-Gallab M., Sklad M. Machining of Al/SiC particulate metal-matrix composites: Part I: Tool performance // Journal of Materials Processing Technology. 1998. No. 83. P. 151–158. URL: https://www.sciencedirect.com/science/article/pii/S0924013698000545 (дата обращения: 21.09.2018). DOI: 10.1016/S0924-0136(98)00054-5.
8. Weinert K., Biermann D. Turning of fiber and particle reinforced aluminium // Proceedings of the International Conference on Machining Of Advanced Materials. 1993. P. 437–453.
9. Моргунов Ю.А., Опальницкий А.И., Перепечкин А.А. Современное состояние и перспективы применения в машиностроении ультразвуковой размерной обработки изделий // Известия МГТУ «МАМИ». 2012. №2 (14). Т. 2. С. 140–144.
10. Yan Chen, Yuhong Liang, Jiuhua Xu, Andong Hu. Ultrasonic vibration assisted grinding of CFRP composites: Effect of fiber orientation and vibration velocity on grinding forces and surface quality // International Journal of Lightweight Materials and Manufacture. September. 2018. P. 189–196. URL: https://www.sciencedirect.com/science/article/pii/S2588840418300386 (дата обращения: 08.10.2018). DOI: 10.1016/j.ijlmm.2018.08.003.
11. Астапчик С.А., Голубев В.С., Маслаков А.Г. Лазерные технологии в машиностроении и металлообработке. Минск: Белорусская наука. 2008. C. 232–242.
12. Грищенко Т.А., Мелюхов Н.И., Любушкин В.О. Применение гидроабразивной резки при обработке деталей из полимерных композиционных материалов // Вестник инженерной школы ДВФУ. 2017. №2 (31). С. 49–55. URL: https://www.dvfu.ru/vestnikis/archive-editions/2-31/6/ (дата обращения: 10.09.2018). DOI: 10.5281/zenodo.808901.
250>