Конструирование мехатронных модулей главного движения металлоре. Задание на проектирование модуля станка
![]()
|
1 2 7.1. Определение исходных данныхИсходные данные определяются на основании предыдущего материала. Например: - тип проектируемого мехатронного станка – токарный с ЧПУ; - диапазон регулирования привода Rn = 250; - наибольшая частота вращения шпинделя nmax = 2500 об/мин; - регулирование частот вращения шпинделя - бесступенчатое; - номинальная и наибольшая частоты вращения электродвигате- ля nэном = 1000 об/мин, nэmax = 3500 об/мин; - компоновка модуля - с встроенным приводом. Разработка кинематической схемы модуля ведется с учетом рекомендаций [1, 7, 8, 9]. 7.2. Определение знаменателя ряда частот вращения и числа ступеней для переборной коробки Для отсутствия разрывов при регулировании частот вращения шпинделя необходимо обеспечить выполнение условия пк RэР (не менее, чем на 5 %), (1) где пк - знаменатель ряда частот вращения, обеспечиваемых пере- борной коробкой; RэР – диапазон регулирования частот вращения вала электродвигателя с постоянной мощностью. Вначале определяются диапазоны регулирования частот вращения шпинделя с постоянной мощностью RnР и с постоянным моментом RnT. Они находятся с учетом степенных зависимостей, рекомендуемых для конкретных типов проектируемых станков [7, 9] ![]() ![]() где Rn = ![]() ков, b = 3 для сверлильных и расточных станков. При этом |
Обобщенные показатели | Варианты | |
1 | 2 | |
кв | 3 | 4 |
кзк | 8 | 10 |
кпб | - | 2 |
км | 4 | 2 |
ккц | - | 2 |
кс | - | 2 |
B | 4b +2bм | 7b +bм |
max | 1,25 | 2 |
На следующем этапе расчета для выбранного варианта структурной формулы с помощью построенного графика частот вращения валов производится определение частных передаточных отношений [9]. Далее кинематический расчет привода продолжается по обычной методике (см. п. 6).
Проверка правильности кинематического расчета привода с бесступенчатым регулированием частот вращения шпинделя проводится на основании выполнения условия (1).
8. Определение расчетных нагрузок и проектные расчеты
деталей
8.1. Уточнение к.п.д. привода модуля
При проектировании модуля главного движения станка нормальной и повышенной точности к.п.д. механической части привода уточняется по формуле
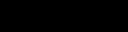
где рп - к.п.д. ременной передачи (для поликлиновой передачи –
0,98); зп - к.п.д. зубчатой передачи (для цилиндрической прямо-
зубой передачи - 0,99); п - к.п.д. подшипника (для подшипника
качения - 0,997); m, n, e – показатели степени, соответствующие
количеству передач и подшипников, участвующих в получении
расчетных частот вращения валов (см. п. 8.4).
При проектировании прецизионных станков классов В, А и С к.п.д. механической части привода определяется с учетом мощности холостого хода и динамических потерь.
8.2. Уточнение номинальной мощности приводного
электродвигателя
Расчетное значение номинальной мощности приводного электродвигателя уточняется по формуле

где Рэф – эффективная мощность резания, кВт.
Номинальная мощность электродвигателя принимается с округлением в большую сторону по справочным данным [8].
8.3. Определение мощности на валах привода модуля
Мощность на валах привода определяется по формуле
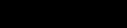
где

формуле (14), с учетом элементов, участвующих в передаче движения.
8.4. Определение расчетных значений частот вращения
валов и зубчатых колес
На графике частот вращения валов (рис. 5) выделяется двойными линиями расчетная цепь, которая показывает наиболее нагруженные варианты работы передач, участвующие в получении расчетной или более высокой частоты вращения шпинделя.
Для рассмотренного примера расчетные обороты валов: np = nэном ip; np = np i1; np = np (см. п. 7.3). Расчетными являются передачи iр, i1, i2 с указанными вариантами работы.
Далее находятся значения расчетных частот вращения шкивов и зубчатых колес. Например, для передачи i1 (рис. 5) расчетная частота вращения шестерни составляет 450 об/мин, колеса - 160 об/мин.
8.5. Определение расчетных значений крутящих моментов
Расчетные значения крутящих моментов деталей привода определяются по формуле
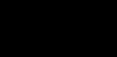
где Рip – расчетное значение мощности на валу, определяется анало-
гично Рi (16) при условии передачи расчетных частот вращения.
9. Предварительная разработка конструкции модуля
Определение требований к проектируемому модулю. В общем случае необходимо учитывать обеспечение:
- рациональных нагрузок элементов привода;
- наименьших радиальных и осевых габаритов;
- удобной сборки и регулировки;
- технологичности конструкции (за счет стандартизации, нормализации, унификации и упрощения конструкции нестандартных дета-
лей);
- возможности компенсации температурных деформаций валов и шпинделя,
- наименьшей себестоимости изготовления модуля.
При конструировании следует учитывать известные методики поиска технических решений и опыт проектирования аналогичных устройств [1, 2, 3, 14, 15, 17 и др.].
Вначале рекомендуется выполнить предварительную разработку конструкции модуля. К этапам этой работы относятся (рис. 9):
- проектные расчеты валов, зубчатых передач и определение их геометрических размеров); разработка компоновки развертки валов c учетом наименьших радиальных габаритов привода, условием проектирования является обеспечение наименьших радиальных зазоров 1 между вращающимися валами и деталями соседних групп передач; при этом возможна коррекция сумм зубьев групп передач, чисел зубьев и размеров зубчатых колес;
- корректировка компоновки развертки валов для достижения наименьших или рациональных радиальных и осевых габаритов привода; при необходимости производится изменение чисел зубьев колес с учетом обеспечения расчетных значений передаточных отношений;
- cоставление эскизов валов c указанием диаметров их поверхностей и корректировка компоновки развертки валов с учетом обеспечения удобной сборки привода и технологичности изготовления его деталей;
- выбор варианта компоновки развертки валов модуля; данный этап осуществляется с учетом комплексной оценки предыдущих вариантов, в качестве которой могут быть использованы обобщенные показатели вариантов и сравнительная себестоимость изготовления модуля; при выполнении этого этапа по указанию консультанта может проводиться поиск варианта с улучшенными динамическими характеристиками (см. п. 11);
- предварительная разработка подробной конструкции развертки валов; этот этап рекомендуется выполнять с использованием подсистем САПР «Шпиндельный узел» [12, 16].
При выполнении этапов 1 4 (рис. 9) рекомендуется проектирование производить в уменьшенном масштабе, а для этапа 5 – в масштабе 1:1.
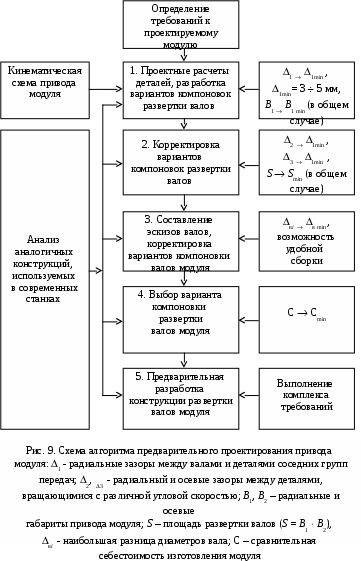
На чертеже конструкции должны быть указаны размеры и посадки для основных сопряжений деталей, расстояния с допусками между осями валов, а также осевые габариты модуля.
10. Уточнение конструкции модуля
Уточнение конструкции развертки валов модуля проводится в последовательности (рис. 10):
- на основании предварительно разработанной конструкции модуля составляется схема свертки валов; при этом учитываются компоновки станка и разрабатываемого модуля, направление и величина силы резания, расположение двигателя и механизмов управления; для обеспечения плотной свертки валов должны выдерживаться радиальные зазоры между деталями соседних групп передач, близкими к наименьшим допускаемым значениям; на схеме свертки валов указываются направления вращения валов и действующие силы при условии передачи расчетных крутящих моментов;
- составляются расчетные схемы валов с указанием сил, действующих в горизонтальной и вертикальной плоскостях, эти схемы сопровождаются эпюрами крутящих и изгибающих моментов;
- проверочные расчеты деталей привода [16, 18, 19, 20 и др.]; для валов проводятся расчеты на выносливость, при этом определяются коэффициенты запаса прочности по нормальным и касательным напряжениям, определяются общие коэффициенты запаса прочности, которые сравниваются с наименьшими допускаемыми значениями, также выполняются проверочные расчеты шлицев и шпонок;
для шпиндельного узла проводится расчет на жесткость [1, 16 и др.], при этом деформации шпинделя сравниваются с допускаемыми значениями; на основе этого расчета может проводиться оптимизация размеров шпиндельного узла;
для зубчатых колес находятся изгибные и контактные напряжения, производится их сравнение с допускаемыми напряжениями, уточнение материала колес и их ширины; при выполнении расчетов передач с поликлиновыми ремнями определяются начальное напряжение и натяжение ремня, сила, действующая на вал (или стакан, связанный с корпусом модуля); эта сила сравнивается с допускаемым значением по условию обеспечения работоспособности модуля;
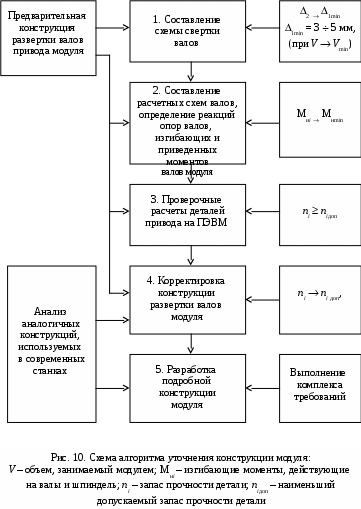
для передачи с зубчатым ремнем определяется действующее в ремне напряжение сдвига, проводится расчет по выполнению условия сохранения зацепления в передаче, при этом определяется предельно допустимая окружная сила, также определяется сила предварительного натяжения ремня, действующая на вал (или стакан); значения напряжения и сил сравниваются с допускаемыми значениями;
при выполнении расчетов подшипников определяется их динамическая грузоподъемность с учетом долговечности (не менее 12000 часов), которая сравнивается с нормативными значениями для выбранных типоразмеров подшипников;
при курсовом проектировании допускается расчеты проводить только для одного наиболее нагруженного вала и связанных с ним деталей;
- корректировка конструкции развертки валов модуля производится с учетом обеспечения рациональных значений запасов прочности деталей, при этом уточняются применяемые материалы, размеры деталей и их конструкция, типы и размеры подшипников; существенное превышение запасов прочности в сравнении с допускаемыми значениями должно быть обосновано;
- разработка подробной конструкции модуля; при этом показываются необходимые сечения и виды с проработкой элементов управления и базирования (по указанию консультанта);
- cоставление спецификации; эта работа проводится для выполняемой конструкторской разработки, при этом необходимо учитывать требования стандартов [35, 37].
11. Анализ динамических показателей работы привода
Данный этап выполняется по заданию консультанта в целях улучшения показателей динамики привода модуля. При этом составляется динамическая модель привода в виде системы с сосредоточенными массами, соединенными между собой упругими и демпфирующими связями. Для анализа показателей модуля рекомендуется использовать методику имитационного моделирования [22], которая предусматривает определение физического взаимодействия звеньев модели, построение графа связей, структурной модели и определение общей передаточной функции модели.
Для анализа передаточных функций частей модели и общей передаточной функции целесообразно применение программы визуального моделирования Simulink, входящей в состав пакета MATLAB. Эта программа позволяет осуществлять в автоматическом режиме построение графиков, характеризующих переходные процессы модели и ее отдельных частей. При этом появляется возможность сравнения отдельных вариантов компоновки привода по динамическим показателям.
На рис. 11 показана обобщенная модель привода модуля главного движения в виде двухмассовой системы (анализу могут подвергаться и другие модели привода).
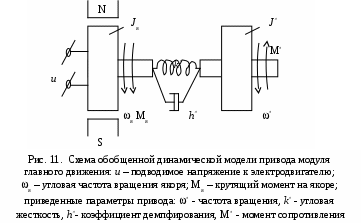
Приведенный момент инерции
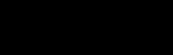
где Ij – момент инерции вращающейся детали или части привода [8, 23, 24];

Приведенный момент сопротивления
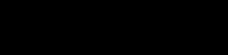
где Мс – момент резания; Mтрj– приведенный момент трения для j–го элемента,
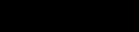
Эквивалентная податливость Пэкв с учетом приведенной жесткости k*


или


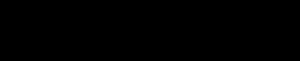
где kjпр –приведенная жесткость j–го элемента, поэтому
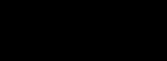
С учетом этого приведенная жесткость
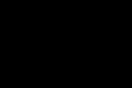
Приведенный коэффициент демпфирования
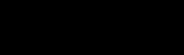
где hj – коэффициент демпфирования упругого элемента (части привода).
Для вариантов компоновки привода модуля с различным расположением масс на валах и распределением моментов инерции вращающихся частей определяются показатели переходного процесса, что позволяет определить наиболее рациональный вариант компоновки валов на этапе предварительного проектирования.
После корректировки конструкции модуля, проведенной с учетом проверочных расчетов, проводится уточнение показателей переходного процесса. Также может предусматриваться построение амплитудно-фазово-частотной характеристики и определение виброустойчивости привода [24].
12. Оформление пояснительной записки и графической
части курсового проекта
Пояснительная записка включает титульный лист, задание на
курсовой проект, материалы по определению технических характеристик модуля и выбору его компоновки, разработке структуры и кинематической схемы, результаты проектных и проверочных расчетов деталей модуля, результаты моделирования и оптимизационных расчетов, список использованной литературы.
Графическая часть курсового проекта содержит:
- таблицы с результатами анализа методов формообразования поверхностей заданной детали и определения функциональных подсистем, блок-схему и структуру модуля (1лист ф. А1);
- общий вид модуля в виде развертки валов (1 лист ф. А1).
Графическую часть рекомендуется выполнять с помощью программ Auto CAD, или КОМПАС. Разработка конструкции модуля должна сопровождаться использованием современных методов поиска технических решений и патентных исследований. Обязательным условием выполнения курсового проекта является соблюдение требований стандартов.
При курсовом проектировании рекомендуется использовать указанную литературу, а также подсистемы автоматизированного проектирования и пакеты прикладных программ.
Список литературы
1. Станочное оборудование автоматизированного производства. /Под редакцией В.В. Бушуева. - М.: Издательство "Станкин". Т. 1, 1993 – 582 с., Т. 2, 1994 – 656 с.
2. Бушуев В.В. Основы конструирования. Москва. Издательство «Станкин», 1995 – 520 с.
3. Кутин А.А. Создание конкурентноспособных станков. - М.: Изд-во «Станкин», 1996. - 202 с.
4. Аверьянов О.И. Модульный принцип построения станков с ЧПУ. М.: Машиностроение, 1987. –232 с.
5. Кудояров Р.Г. Точность деталей машин при алмазном хонинговании. /Под ред. В.Ц. Зориктуева. – М.: Изд-во МАИ, 2002. – 170 с.
6. Кудояров Р.Г. Функционально-структурное построение мехатронных станочных модулей. Учебное пособие. – Уфа.: УГАТУ, 2000.- 60 с.
7. Куликов С.И., Дурко Е.М. Металлорежущие станки и станочные системы. Свердловск: Изд-во Уральского университета, 1988. – 272 с.
8. Методическое руководство к проектированию приводов станков с ЧПУ (материалы к курсовому и дипломному проектированию). /Дурко Е.М., Галеев С.М. Уфа: УАИ,1980. – 54 с.
9. Методические указания к практическим занятиям по курсу "Промышленное оборудование автоматизированного производства". /Куликов С.И., Кудояров Р.Г., Дурко Е.М., Совин В.П. Уфа: УГАТУ, Уфа, 1989. – 42 с.
10. Методические указания к лабораторным работам «Металлорежущие станки с ЧПУ» по курсу «Оборудование машиностроительного производства» для специальности 071800 /Кудояров Р.Г., Евсеев Ю.М., Муратов Б.С. – Уфа: УГАТУ, 2000. –52 с.
11. Металлорежущие станки и автоматы. Учебник для машиностроительных втузов. /Под ред. А.С. Проникова М.: Машиностроение, 1981. – 479 с.
12. Методические указания по автоматизированному проектированию шпиндельных узлов станков (к курсовому и дипломному проектированию). /Куликов С.И., Акмаев О.К., Киселева Л.Н. Уфа: УАИ, 1986. - 33 c.
13. Модзелевский А.А., Соловьев А.В., Лонг В.А. Многооперационные станки. М.: Машиностроение, 1981. – 215 с.
14. Многоцелевые станки с ЧПУ. Учебное пособие /Кудояров Р.Г., Зориктуев В.Ц., Евсеев Ю.М., Жаринов В.Н., Михайловский А.И. Уфа: УГАТУ, 1995. – 98 с.
15. Основы общей методики конструирования. Учебное пособие. /Акмаев О.К. Уфа: УГАТУ, 1993. – 110 с.
16. Пакеты прикладных программ к подсистемам САПР металлорежущих станков. ЭНИМС, СТАНКИН. М. 1985 – 2002.
17. Приводы металлорежущих станков. Процедура и технологические основы проектирования. Учебное пособие. /Ризванов Ф.Ф. Уфа: УГАТУ, 1994. – 122 с.
18. Расчет и проектирование деталей машин. Учебное пособие для втузов. /Жуков К.П., Кузнецова А.К., Масленникова С.И. и др. под ред. Г.Б. Столбина и К.П. Жукова. М.: Высшая школа, 1978. – 247 с.
19. Свирщевский Ш.И., Макайчик Н.Н. Расчет и конструирование коробок скоростей и подач. Минск: Высшая школа, 1976. - 590 c.
20. Справочник конструктора - машиностроителя. В 3-ех томах./Анурьев В.И. Под ред. И.Н. Жестковой. 8-ое изд. М.: Машиностроение. 2001. Т1 - 920 с. Т2 - 912 с.
21. Справочник технолога-машиностроителя. В 2-х томах. /Под ред. А.М. Дальского, А.Г. Косиловой, Р.К. Мещерякова. 5-е изд. М.: Машиностроение. Т.1 – 2001.- 912 с., Т.2 – 2001. – 994 с.
22. Имитационное моделирование узлов металлорежущих станков на ЭВМ. Учебное пособие. /Чикуров Н.Г., Куликов С.И. –Уфа: УАИ, 1988, 101 с.
23. Михайлов О.П. Автоматизированный электропривод станков и промышленных роботов. Учебник для вузов. – М: Машиностроение. 1990 – 304 с.
24. Орликов М.Л. Динамика станков. 2-е изд. – К.: Выща шк. 1989. – 272 с.
25. ГОСТ 8032-84. Предпочтительные числа и ряды предпочтительных чисел.
26. ГОСТ 2.701-84. Правила выполнения кинематических схем.
27. ГОСТ 2.770-68. Обозначения условные графические в схемах. Элементы кинематики.
28. ГОСТ 18097-88Е. Станки токарные и токарно- винторезные. Основные размеры.
29. ГОСТ 1227-79. Станки вертикально-сверлильные. Основные размеры.
30. ГОСТ 1165-81. Станки фрезерные консольные. Основные размеры.
31. ГОСТ 9405-73. Станки шлифовально-притирочные, хонинговальные).
32. ГОСТ 12593-93. Концы шпинделей фланцевые под поворотную шайбу и фланцы зажимных устройств.
33. ГОСТ 12595-85. Станки металлорежущие. Концы шпинделей фланцевого типа А.
34. ГОСТ 2701-72. Концы шпинделей сверлильных и расточных станков.
35. ГОСТ 2.105-95. Общие требования к текстовым документам.
36. ГОСТ 2.109-73. Основные требования к чертежам.
37. Стандарт предприятия. Графические и текстовые конструкторские документы. СТП УГАТУ 002 – 98. Уфа: УГАТУ. 1998. – 81 с.
Приложение А
Типовое задание 1
УГАТУ
Кафедра АТС
ЗАДАНИЕ
к курсовому проекту по дисциплине
«Конструирование мехатронных модулей»
студенту гр.________ ___________________
Выполнить разработку элементов эскизного и технического проекта станочного модуля станка с компьютерным управлением.
Исходные данные:
сведения об обрабатываемых деталях
____________________________________________________________________
сведения о выполняемых операциях
____________________________________________________________________
проектирование модуля ____________________________________________________________________
дополнительные условия
____________________________________________________________________
Содержание и этапы курсового проектирования:
1) определение технологического назначения станка, анализ схем обработки и методов формообразования поверхностей деталей - 10%;
2) определение функциональных подсистем проектируемого модуля и разработка кинематической структуры - 5%;
3) определение основных технических характеристик модуля - 5%;
4) составление компоновки станка и модуля - 5%;
5) разработка кинематической схемы модуля - 10%;
6) расчет и проектирование модуля с применением ЭВМ - 20%;
7) оформление расчетно-графической части
- сведения о функциональных подсистемах, блок схема и структура
модуля (1л. ф.А1) - 10%,
- общий вид модуля (развертка валов) (1 л. ф. А1) - 25%;
8) cоставление пояснительной записки (30 40 л. ф. А4) - 10%.
В пояснительной записке привести схемы обработки поверхностей, эскизы компоновок проектируемого модуля и станка, структурную схему модуля станка, расчетные схемы, сведения о выполненных расчетах и обоснование принятых решений.
Консультант________________________
Дата выдачи задания Срок выполнения
Приложение Б
Типовое задание 2
УГАТУ
Кафедра АТС
ЗАДАНИЕ
к курсовому проекту по дисциплине
«Конструирование мехатронных модулей»
студенту гр.________ ___________________
Выполнить разработку элементов эскизного и технического проекта модуля главного движения токарного станка с компьютерным управлением.
Исходные данные (учесть подчеркнутое):
наибольший диаметр обрабатываемой детали 250, 320, 400, 530 мм;
переходы обработки - токарные, сверлильные, резьбонарезные;
обрабатываемые материалы – конструкционные стали HB 150, 160 – 260,
260 – 320;
наибольшая глубина резания (при токарной обработке) 1, 2, 3, 4 мм;
регулирование частот вращения шпинделя – ступенчатое, бесступенчатое;
компоновка привода – встроенная, разделенная;
дополнительные условия ________________________________________________________________
Содержание и этапы курсового проектирования:
1) определение технологического назначения станка, анализ схем обработки и методов формообразования поверхностей деталей - 10%;
2) определение функциональных подсистем проектируемого модуля и разработка кинематической структуры - 5%;
3) определение основных технических характеристик модуля - 5%;
4) составление компоновки станка и модуля - 5%;
5) разработка кинематической схемы модуля - 10%;
6) расчет и проектирование модуля с применением ЭВМ - 20%;
7) оформление расчетно-графической части
- сведения о функциональных подсистемах, блок схема и структура
модуля (1л. ф.А1) - 10%,
- общий вид модуля (развертка валов) (1 л. ф. А1) - 25%;
8) cоставление пояснительной записки (30 40 л. ф. А4) - 10%.
В пояснительной записке привести схемы обработки поверхностей, эскизы компоновок проектируемого модуля и станка, структурную схему модуля станка, расчетные схемы, сведения о выполненных расчетах и обоснование принятых решений.
Консультант________________________
Дата выдачи задания Срок выполнения
Составители: КУДОЯРОВ Ринат Габдулхакович,
ДУРКО Евгений Маркович
КОНСТРУИРОВАНИЕ МЕХАТРОННЫХ МОДУЛЕЙ
ГЛАВНОГО ДВИЖЕНИЯ МЕТАЛЛОРЕЖУЩИХ СТАНКОВ
МЕТОДИЧЕСКИЕ УКАЗАНИЯ
к курсовому проектированию по дисциплине
«Конструирование мехатронных модулей»
Подписано к печати 30.06.2004. Формат 60х84 1/16.
Бумага офсетная. Печать плоская. Гарнитура Таймс New Roman Cyr. Усл. печ. 2,2. Усл. кр. - отт. 2,2. Уч. - изд. л. 2,1.
Тираж 100 экз. Заказ №
Уфимский государственный авиационный технический университет.
Центр оперативной полиграфии УГАТУ
450000, Уфа, центр, ул. К. Маркса, 12

1 2