|
Классификация основных процессов химической технологии
Конструкции теплообменных аппаратов. Основные параметры, определяемые в процессе технологического расчета. В зависимости от способа передачи тепла разл-ют 2 осн-ые группы теплооб-ов: 1) поверхностные, в кот-х передача тепла происх-т через пов-ть стенки; 2) смешения, в кот-х теплообмен происх-т непоср-но при соприк-ии теплонос-ля. Поверх-ые делятся на: а. Регенеративные, исп-ют значит-но реже, в основном для регенерации тепла отходящих газов. В них процесс переноса тепла от горячего теплонос-ля к холод-у раздел-ся на 2 периода и происх-т при попеременном нагревании и охлажд-и насадки. Регенеративные теплооб-ки обычно состоят из двух ап-ов цилиндр-ой формы, корпуса кот-х заполняются насадкой в виде свернутой в спираль метал-ой ленты, листового металла, кусков шамота, кирпича и др. материалов. Эта насадка попеременно нагревается при соприкосновении с горячим теплоносителем затем отдает свое тепло соприкасаясь с холодным теплоносителем.; б. Рекуперативные – кожухотрубчатые теплооб-и: жёсткие, полужёст-е, нежёст-е; вертикал-е, наклонные, элементные, литые. Поверхности теплообмена могут быть: шахматные, коридорные, спиральные, труба в трубе. Корпусные теплообменники с пластинчатой и спиральной поверхностью теплообмена. Поверхностные теплооб-ки. Вертикальный кожухотрубный теплообменник с жестким корпусом, одноходовой. С неподвижными трубными решетками 2 в которых закреплены трубы 3. К кожуху 1 крепится на прокладках и болтах крышка 4 и днище 5. Один из теплоносителей проходит по трубам, другой по межтрубным пространствам. Обычно нагреваемый теплонос-ль подается снизу, а охлажд-ый сверху вниз, противотоком. При сравнительно небольших расходах ж-ти ск-ть её движения в трубах таких теплообменников низка, соответственно низки коэф-ы теплоотдачи. Для увеличения ск-ти теплообмена применяют многоходовые теплообменники.
В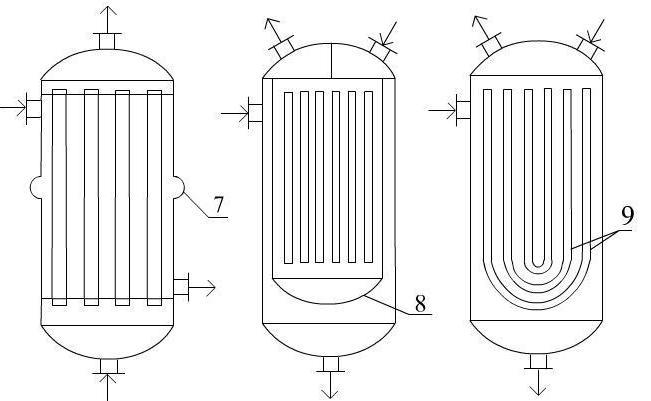 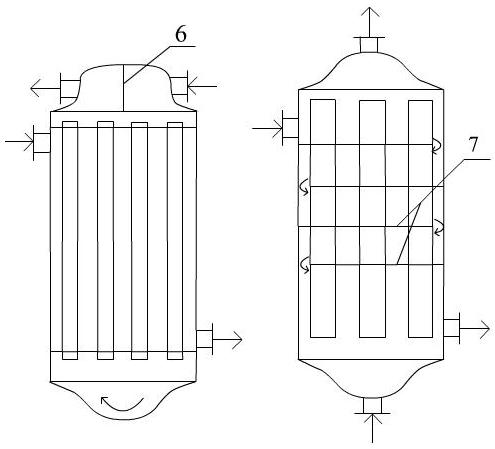 многоходовых теплообменниках по трубному пространству теплообменников с помощью поперечных перегородок 6 устанавливаемых в крышках теплообменниках трубный пучок раздел-ся на секции или ходы, по которым послед-но движ-ся теплонос-ль. При этом число труб в каждой секции примерно одинаково. В многоход-х теплообмен-ах при одном и том же расходе теплонос-я ск-ть его движ-я увелич-ся кратно числу ходов. Для увел-ия ск-ти движ-я в межтрубном пространстве в нем устан-ся ряд сегментных перегородок 7. В гориз-ых теплообменниках эти перегородки одновременно являются опорами для труб. Увеличение интенсивности теплообмена в многоходовых теплооб-ах сопровождается увеличением гидравлического сопротивления и усложнением конструкции. Это определяет выбор экономически целесообразной скорости зависящей от числа ходов теплооб-ка, который обычно не превышает 6. Многоходовые теплооб-ки работают по принципу смешанного тока следствием чего явл-ся некоторое снижение движущей силы теплопередачи по сравнению с чисто противоточным движением теплоносителя. Если разность темпе-р труб и кожуха достаточно велика, то трубы и кожух удлиняются существенно не одинаково. Это приводит к нарушению плотности соединения труб с решетками и соответственному недопустимому смешению теплоносителей. Поэтому при разности температур кожуха и труб более 50ºС или при значительной длине труб применяют теплообменники не жесткой конструкции допускающие некоторые перемещения труб относительно кожуха аппарата. В теплооб-ах с линзовым компенсатором 7 темпер-ые деформации компенсируются осевым сжатием или растяжением компенсатора. Теплооб-ки с плавающей головкой 8 применяются при значительных относительных перемещений труб и кожуха. В нем одна из трубных решеток не соединена с кожухом и может свободно перемещаться вдоль оси при температурных удлинениях. В теплооб-ке с U образными трубами 9 сами трубы выполняют функцию компенсирующих устройств. При этом упрощается и облегчается конструкция аппарата имеющего лишь одну неподвижную трубную решетку. Однако в этом аппарате усложняется монтаж труб, затрудняется очистка их внутренних стенок. Нежесткий корпус – это корпус с сальниковым компенсатором. Примечание: Теплообменники с сальниковым компенсатором используется, как правило, при небольших давлениях межтрубного теплоносителя.
Двухтрубные теплообменники или теплообменники типа “Труба в трубе”. Эти ап-ты состоят из нескольких последовательно соединенных элементов образованных концентрически расположенных трубами. Один теплоноситель движется по внутренним трубам 1, другой по кольцевому зазору между внутренними и наружными трубами 2. Внутренние трубы соединяются с помощью калачей 3, а наружные с помощью п атрубков 4. Так как сечение внутренних труб и кольцевого зазора невелики, то в этих теплообменниках достигается значительная скорость движения теплоносителей. Это приводит к увеличению коэффициентов теплопередачи и тепловых нагрузок, замедлению отложения накипи и загрязнений на стенках труб. Однако двухтрубные теплообменники более громоздки чем кожухотрубчатые и требуют большего расхода металла на единицу поверхности теплообмена. Их применяют для процессов со сравнительно небольшими тепловыми нагрузками и соответственно малыми поверхностями теплообмена.
З меевиковые теплообменники. Спиральный пучек. В змеевиковых теплообменниках основным элементом явл-ся змеевик, т.е. труба согнутая по определенному профилю. Змеевики погружаются в жидкость находящаяся в корпусе аппаратов. Из-за большого сечения корпуса скорость движения жидкости мала, что приводит к снижению коэффициента теплоотдачи от наружной стенки змеевика к жидкости или наоборот. Скорость движения жидкости повышают путем установки в корпусе аппарата стакана. В этом случае жидкость движется по кольцевому зазору между стенками аппарата и стакана с повышенной скоростью.
Т еплооб-ки с плоской поверхностью теплопередачи. К такому виду относятся пластинчатые и спиральные теплообменники. В пластинчатых теплообменниках поверхностью теплообмена являются гофрированные параллельные пластины с помощью которых создается система узких каналов шириной 5-6 мм с волнистыми стенками. Так как скорость движения жидкости в таких каналах значительна от 1-3 м/с, то коэффициенты теплопередачи в пластинчатых теплообменниках достигает больших значений 3000-4000 Вт/м2·К при сравнительно не высоких гидравлических сопротивлений. Пластинчатые теплообменники просты в изготовлении, их легко разбирать и ремонтировать. Однако серьезную проблему представляет герметизация пластин. По этой же причине их применение при высоких давлениях затруднительно. В спиральных теплообменниках поверхность теплообмена образуется двумя длинными металлическими листами свернутыми по спирали. Эти аппараты компактны, позволяют создавать высокие скорости движения теплоносителей при небольших гидравлических сопротивлений. Однако, они сложны в изготовлении, не могут работать при высоких давлениях более 1 мПа, т.к. герметизация их вызывает трудность.
Теплооб-ки смешения являются высокоэффективными ап-ми, т.к. в них отсутствует термическое сопротивление стенки и теплообмен происходит при непосредственном соприкосновении теплоносителей. Такие аппараты применяют в тех случаях, когда допустимо смешение теплоносителей или оно определяется технологическими условиями. Наиболее часто смесительные теплооб-ки применяют для конденсации водяного пара, нагревание и охлаждение воды и воздуха. По принципу устройства теплообменники смешения подразделяются: 1. барбатажные. 2. полочные. 3. посадочные. 4. полые. На рисунке изображен полочный противоточный барометрический конденсатор смешения предназначенный для создания вакуума в аппаратах с паровой средой в частности выпарных установках. Пар вводят в корпус 1 конденсатора с сегментными перфорированными полками 2. На верхнюю полку подается вода, далее каскадно перетекает вниз по полкам имеющим небольшие борта. При контакте с водой пар конденсируется вследствие чего в конденсаторе и в аппарате создается разряжение. Образовавшаяся смесь конденсата и воды самотеком сливается в барометрическую трубу 3 высотой около 10 метров, затем в емкость 4 и далее в канализацию. Барометрическая труба и емкость образуют гидрозатвор, который препятствует проникновению наружного воздуха в аппарат. Не конденсирующийся воздух находившийся в паре и охлаждающей воде пропускают через ловушку 5 и откачивают вакуум-насосом. Насадочные смесительные теплообменники представляют собой цилиндр заполненный различными по конфигурации телами, так называемой насадкой, которая служит для развития поверхности контакта. Т.к. эти аппараты применяют для конденсации паров или охлаждения газа какой-либо жидкостью (обычно водой), то эту жидкость через распределительное устройство подают на насадку. Под действием силы тяжести жидкость растекается по насадке увеличивая поверхность контакта с поднимающимися снизу паром или газом. В полых аппаратах цилиндрической формы устанавливают разнообразные разбрызгиватели для увеличения поверхности контакта между водой, паром, газом. Контакт между фазами здесь происходит на поверхности капель.
12.Выпаривание. Основные способы и их характеристика
В ыпариванием наз-ся процесс концентрации раст-ов тв-х нелетучих вещ-в путем удаления ж-го летучего растворителя в виде паров. Сущность выпар-ия закл-ся в переводе раст-ля в парообразное состояние и отводе полученного пара от оставшегося концентрированного ра-ра. Выпар-е обычно проводится при кипении, т.е. когда давление пара над раствором равно давлению в рабочем объеме ап-та. Теплоту для выпар-ия можно подводить любыми теплоносителями применимыми при нагревании. Однако в большинстве случаев в качестве теплонос-ля для выпар-ия испол-ся глухой водяной пар, который наз-ся греющим или первичным. Пар, образовавшийся при выпар-ии кипящего раствора, наз-ся вторичным. В технологии используются следующие способы выпаривания: 1. простое выпаривание, проводимое как периодически, так и непрерывно. 2. многократное выпаривание, осуществляемое только непрерывно. 3. выпаривание с применением теплового насоса. Два последних способа имеют преобладающее значение, т.к. обеспечивают значительную экономию тепла. Процессы выпаривания проводят как под давлением, так и под вакуумом в зависимости от свойств выпарных растворов и параметров греющего пара. Простое выпаривание. Этот процесс осущ-ся на установках небольшой производительности включ-их один выпарной ап-ат. Ап-ат состоит из нагреваемой камеры и сепаратора. Камера и сепаратор могут быть объединены в одном ап-те или камера может быть вынесена и соединена с сепаратором трубами. Многократное выпаривание. Сущность процесса многократного выпар-я состоит в том, что он проводится в нескольких соединенных последовательно ап-ах, давление в которых поддерживают так, чтобы вторичный пар предыдущего ап-та может быть использован как греющий в следующем ап-те. При этом давление пара в каждом предыдущем ап-те должно быть больше его давления в последующем. Это достигается созданием избыточного давления в 1 ап-те или вакуума в последнем или и тем и другим одновременно. Многократное выпар-ие позволяет сократить расход тепла на проведение процесса приблизительно пропорционально числу корпусов, т.е. числу послед-но соединенных ап-ов. Эта экономия достигается за счет увеличения поверхности теплообмена. Установки для многократного выпар-я всегда имеют несколько корпусов и называются многокорпусными. Многокорпусные выпарные установки могут быть прямоточными, противоточными и комбинированными. В прямоточных установках греющий пар и выпариваемый раствор перемещаются из корпуса в корпус в одном направлении. В противоточных – в противоположных направлениях. А в комбинир-ых установках осуществляются различные варианты ввода и перемещения раствора. Преимуществом прямоточных установок является возможность перемещения раствора из корпуса в корпус без применения насосов работающих на горячих потоках. Поэтому они получили большее распространение хотя средний коэффициент теплопередачи выше в противоточных установках. Выпаривание с применением теплового насоса. Этот способ основан на возможности использования вторичного пара для испарения растворителя в том же ап-те, если темп-ра вторичного пара будет повышена до температуры греющего пара. Повысить темп-ру вторичного пара можно путем его сжатия компрессором или паровым инжектором. Расход пара на выпаривание с тепловым насосом значительно меньше, чем при простом выпаривании. Однако наряду с этим необходимо расходовать механическую энергию на работу компрессора. Выпарные установки с тепловым насосом применяют для выпаривания растворов с малой температурной депрессией и в условиях, когда необходимо обеспечить минимальный расход греющего пара.
13.Массообменные процессы. Движущая сила.
Т ехнолог-ие проц-ы, скор-ть протекания кот-ых опр-ся скор-ю переноса вещ-ва из одной фазы в другую наз-ся массооб-ми проц-ми. Производные установки в хим-ой пром-ти в больш-ве случаев созд-ся по след-ей схеме: исх-ое сырьё поступает в реактор, где лишь частично превр-ся в прод-ы реакции. Выходящаяиз реактора смесь напр-ся в массообменную разделит-ую аппаратуру, в которой производиться разделение смесей на прод-ы реакции и непрореагир-ее сырьё. последнее возвращ-ся в реактор, а продукт на переработку. Между реакт-м и раздел-ым ап-ом сущ-ет технолог-ая связь: чем меньше нагрузка на реактор, т.е. чем меньше превращение исходного сырья в прод-ы реакции, тем больше нагрузка на разделит-ый ап-ат и наоборот. Работа идет нормально, когда оптимальное сочетание. В раздел-ом агрегате могут провод-ся след-ие массообменные проц-ы: абсорбция – избират-ое погл-ие газов или паров жидким поглотителем, абсорбентом. здесь Г→Ж; ректификация – проц-с раздел-я смеси на компон-ы путём противоточного взаимод-ия потоков пара и жид-и. переход Ж↔Г; экстракция – извлеч-е компон-а из одной ж-ти другой, несмеш-ся с первой, Ж→Ж; экстрагирование – проц-с перехода тв-ой фазы в ж-ую Т→Ж; кристаллизация – выделение вещ-ва в виде тв-ых крист-ов из раст-ов или распл-ов, Ж→Т; адсорбция – избир-ое погл-ие комп-ов г-ых смесей или ж-их раст-ов поверх-ю тв-го порист-го поглатителя, Г→Т, Ж→Т; сушка – удал-ие летучего растворителя из тв-ых матер-ов путём его испар-ия, Т→Г или пар; мембранное раздел-е – раздел-ие, находящихся в растворе вещ-в, основанное на способности полупрониц-ых мембран: пропускать одни в-ва и задерж-ть другие, переход вещ-ва из исх-ой Ж или Г фазы в выделен-ю Ж-ю или Г-ю фазу, Г→Г, Ж→Ж; ионообменный проц-с – извл-ие вещ-а из раст-ра, основ-ое на способности ионообменных смол: обменивать свои подвиж-е ионы на ионы извлекаемого вещ-ва, Ж→Т. Во всех перечисленных проц-х осущ-ся переход вещ-ва из одной фазы в другую в направлении достиж-ия равнов-я наз-ся массопередачей. Ур-ие массопер-и: М = К·F·Δ, где М-кол-о в-ва, переход-е из одной фазы в др-ю в ед-цу врем-и; К-коэф-т массопер-и [м/с]; F-поверх-ть соприкос-я фаз; Δ-движ-ая сила проц. массопер-и. Средняя движущая сила массообменных проц-ов. Движ-ей силой этих проц-ов явл-сяразность хим-х потенц-ов. Разность между рабочими и равновес-ми конц-ми и есть движ-ая сила массооб-х проц-в. Т.к. движ-ая сила различна по всей длине ап-та, то в осн-ое ур-ие массопер-и входит величина сред-ей движ-ей силы. При её опр-ии возможны 2 случая: 1) линейная зависимость между равновес-и конц-ми, т.е. линия равн-ия явл-ся прямой. В этом случае ср-яя движ-ая сила опр-я по ур-ю: ΔСР = (Δ1–Δ2)/ ln(Δ1/Δ2), где Δ1 и Δ2 – движ-ие силы на концах ап-та; 2) не линейная завис-ть между равновес-и конц-ми: ΔYср = (YН–YВ)/ ∫ [dY/(Y–Y*)]; ΔХср = (ХН – ХВ) / ∫ [dХ/(Х*–Х)], интеграл в знаменателях этих ур-ий наз-ся числом ед-ц переноса. ∫ [dY/(Y–Y*)] = nY = (YН–YВ)/ΔYср; ∫ [dХ/(Х*-Х)] = nх = (ХН–ХВ)/ΔХср. Согласно этим выр-ям число единиц переноса характ-т изменение рабочей концентрации фазы, приходящейся на единицу движущей силы. Одну ед-цу переноса можно рассм-ть как участок ап-та, для кот-го измен-е конц-ии одной из фаз = сред-й движ-ей силе на этом уч-ке. Число ед-ц переноса опр-ют методом графич-го интегр-ия. Задаваясь рядом знач-й между YН и YВ опр-ют вел-у 1/(Y–Y*). Опр-ют площадь, огранич-ю получ-ой кривой и соответ-ми абсциссами и находят велич-у интегр-а с учётом масштабов m1 и m2 выраж-х числом ед-ц в 1 см постр-ия. nY = ∫ [dY/(Y–Y*)] = f·m1·m2. Число ед-ц переноса широко исп-ся для расч-а высоты массообмен-х ап0ов. Обозн-м высоту ап-та через Н, площадь попер-го сеч-я через S и удел-ю пов-ть контакта фаз в ед-це объёма ап-та чсерез f, тогда площ-дь пов-ти массопер-чи = произв-ю этих величин F=HSf, поставл-я это знач-е в осн-ое ур-ие массопер-и имеем: М=КYHSfΔYср. Согласно ур-ю матер-го баланса М=G(YН–YВ). Отсюда, высота ап-та: H=[G/(KYSf)]·[(YН–YВ)/ΔYср]= [G/KYSf]·nY, где G/KYSf – высота ед-цы переноса = hY. H=hY·nY.
14.Абсорбция. Области применения и аппаратурное оформление
Абс-ей наз-ют поглощ-е газов или паров из г-ых или паровых смесей ж-им поглот-ем – абсорбентом. При физ-ой абс-ии поглощ-ый газ, абсорбтив, не взаим-ет с хим-им поглот-ем, если же абсорбтив образует с абсорб-ом хим-ую связь, то это хемосорбция. В технике часто встречается сочетание обоих видов абс-ии. Обратная абс-ия, т.е. выдел-е поглощ-го газа из поглот-го раст-ра – это десорбция, являющаяся результ-ом обратимости физ-ой абс-ции. Отработ-ые после хемосорбции абсорб-ты обычно регенерируют хим-ми методами или нагреванием. Сочетание абс-ии и десорб-и позволяет многократно прим-ть поглотитель и выделять поглощённый газ в чистом виде. Часто десорб-ю проводить не обязательно, т.к. полученный в результ-е абс-ии раст-р явл-ся конеч-м прод-ом, пригодным для дальнейшего исп-ия. В пром-ти абс-ию прим-ют для решения след-их осн-х задач: 1) для получения готовой продукции (н-р, абс-ия SO3 в производ-е серной к-ты, абс-ия HCl с получением хлороводородной к-ты, абс-ия оксидов азота водой в производ-ве азотной к-ты и т.д.), при этом абс-ию проводят без десорбции; 2) для выделения ценных компонентов из газ-х смесей (н-р, абс-ия бензола из коксового газа; абс-ия ацетилена из газов крекинга или пиролиза природ-го газа и тд), при этом абс-ию проводят в сочетании с десорбцией; 3) для очистки газ-х выбросов от вредных примесей (н-р, очистка топочных г-ов от SO2, оч-ка от фтористых соед-ий газов, выделяющихся при производ-ве минерал-х удобр-й и т.д.). Очистку г-ов от вредных примесей абс-ей исп-ют также применительно к технолог-им г-ам, когда присутствие прим-ей недопустимо для дальнейшей переработки газа (н-р, очистка коксового и нефтяного газов от Н2S, оч-ка азотоводородной смеси для синтеза аммиака от СО2 и СО и т.д.). В этих случаях извлекаемые из газ-х смесей компоненты обычно исп-ют, поэтому их выделяют десорбцией; 4) для осушки газов, когда в абсорбционных проц-ах (абс-ия, дес-ия) участвуют две фазы – ж-ая и г-ая – и происходит переход в-ва из газ-ой фазы в жид-ю (при абс-ии) или наоборот, из ж-ой фазы в газ-ю (при десорбции), причём инертный газ и поглотитель являются только носителями компонента соответственно в г-ой и ж-ой фазах и в этом смысле в массопереносе не участвуют.
|
|
|