|
Курс лекций ТПвМ. Курс лекций по дисциплине Технологические процессы в машиностроении
Лекция 7. Технология обработки металлов давлением. Физико-механические основы обработки металлов давлением.
Технология обработки давлением. Общие сведения
Обработкой давлением называются процессы получения заготовок или деталей машин силовым воздействием инструмента на исходную заготовку из исходного материала.
Пластическое деформирование при обработке давлением, состоящее в преобразовании заготовки простой формы в деталь более сложной формы того же объема, относится к малоотходной технологии.
Обработкой давлением получают не только заданную форму и размеры, но и обеспечивают требуемое качество металла, надежность работы изделия.
Высокая производительность обработки давлением, низкая себестоимость и высокое качество продукции привели к широкому применению этих процессов.
Классификация процессов обработки давлением
Пластическое деформирование в обработке металлов давлением осуществляется при различных схемах напряженного и деформированного состояний, при этом исходная заготовка может быть объемным телом, прутком, листом.
По назначению процессы обработки металлов давлением группируют следующим образом:
– для получения изделий постоянного поперечного сечения по длине (прутков, проволоки, лент, листов), применяемых в строительных конструкциях или в качестве заготовок для последующего изготовления деталей – прокатка, волочение, прессование;
– для получения деталей или заготовок, имеющих формы и размеры, приближенные к размерам и формам готовых деталей, требующих механической обработки для придания им окончательных размеров и заданного качества поверхности – ковка, штамповка.
Основными схемами деформирования объемной заготовки являются:
– сжатие между плоскостями инструмента – ковка;
– ротационное обжатие вращающимися валками – прокатка;
– затекание металла в полость инструмента – штамповка;
– выдавливание металла из полости инструмента – прессование;
– вытягивание металла из полости инструмента – волочение.
Характер пластической деформации зависит от соотношения процессов упрочнения и разупрочнения. Губкиным С. И. предложено различать виды деформации и, соответственно, виды обработки давлением.
Горячая деформация – деформация, после которой металл не получает упрочнения. Рекристаллизация успевает пройти полностью, новые равноосные зерна полностью заменяют деформированные зерна, искажения кристаллической решетки отсутствуют. Деформация имеет место при температурах выше температуры начала рекристаллизации.
Неполная горячая деформация характеризуется незавершенностью процесса рекристаллизации, которая не успевает закончиться, так как скорость ее недостаточна по сравнению со скоростью деформации. Часть зерен остается деформированными и металл упрочняется. Возникают значительные остаточные напряжения, которые могут привести к разрушению. Такая деформация наиболее вероятна при температуре, незначительно превышающей температуру начала рекристаллизации. Ее следует избегать при обработке давлением.
При неполной холодной деформации рекристаллизация не происходит, но протекают процессы возврата. Температура деформации несколько выше температуры возврата, а скорость деформации меньше скорости возврата. Остаточные напряжения в значительной мере снимаются, интенсивность упрочнения снижается.
При холодной деформации разупрочняющие процессы не происходят. Температура холодной деформации ниже температуры начала возврата.
Холодная и горячая деформации не связаны с деформацией с нагревом или без нагрева, а зависят только от протекания процессов упрочнения и разупрочнения. Поэтому, например, деформация свинца, олова, кадмия и некоторых других металлов при комнатной температуре является с этой точки зрения горячей деформацией.
Технологические свойства
При выборе металла или сплава для изготовления изделия различными способами обработки давлением учитывается способность материала к данному методу обработки.
Ковкость – свойство металла изменять свою форму под действием ударов или давления, не разрушаясь.
Степень ковкости зависит от многих параметров. Наиболее существенным из них является пластичность, характеризующая способность материала деформироваться без разрушения. Чем выше пластичность материала, тем большую степень суммарного обжатия он выдерживает.
В условиях обработки металлов давлением на пластичность влияют многие факторы: состав и структура деформируемого металла, характер напряженного состояния при деформации, неравномерность деформации, скорость деформации, температура деформации и др. Изменяя те или иные факторы, можно изменять пластичность.
Состав и структура металла. Пластичность находится в прямой зависимости от химического состава материала. С повышением содержания углерода в стали пластичность падает. Большое влияние оказывают элементы, входящие в состав сплава как примеси. Олово, сурьма, свинец, сера не растворяются в металле и, располагаясь по границам зерен, ослабляют связи между ними. Температура плавления этих элементов низкая, при нагреве под горячую деформацию они плавятся, что приводит к потере пластичности.
Пластичность зависит от структурного состояния металла, особенно при горячей деформации. Неоднородность микроструктуры снижает пластичность. Однофазные сплавы, при прочих равных условиях, всегда пластичнее, чем двухфазные. Фазы имеют неодинаковые механические свойства, и деформация получается неравномерной. Мелкозернистые металлы пластичнее крупнозернистых. Металл слитков менее пластичен, чем металл прокатанной или кованой заготовки, так как литая структура имеет резкую неоднородность зерен, включения и другие дефекты.
Характер напряженного состояния. Один и тот же материал проявляет различную пластичность при изменении схемы напряженного состояния. Еще в 1912 году немецкий ученый Карман осаживал образцы из мрамора и песчаника, помещенные в толстостенный цилиндр, в который нагнетался глицерин под давлением до 170 МН/м2. Деформация происходила при схеме всестороннего сжатия. В результате остаточная деформация образцов составила 9 %, в дальнейшем удалось достигнуть деформации в 78 %. Схема всестороннего сжатия является наиболее благоприятной для проявления пластических свойств, так как при этом затрудняется межзеренная деформация и вся деформация протекает за счет внутризеренной. Появление в схеме растягивающих напряжений снижает пластичность. Самая низкая пластичность наблюдается при схеме всестороннего растяжения.
Неравномерность деформации. Чем больше неравномерность деформации, тем ниже пластичность. Неравномерность деформации вызывает появление дополнительных напряжений. Растягивающие напряжения всегда снижают пластичность и способствуют хрупкому разрушению. Кроме того, неравномерность напряженного состояния понижает механическую прочность материала, так как напряжения от внешней нагрузки суммируется с остаточными растягивающими напряжениями, то разрушение наступает при меньшей нагрузке.
Скорость деформации. С повышением скорости деформации в условиях горячей деформации пластичность снижается. Имеющаяся неравномерность деформации вызывает дополнительные напряжения, которые снимаются только в том случае, если скорость разупрочняющих процессов не меньше скорости деформации.
Влияние температуры. Качественная зависимость пластичности от температуры представлена на рис. 13.
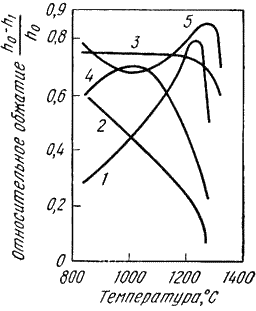
Рис. 13. Влияние температуры на пластичность сталей
Влияние температуры неоднозначно. Малоуглеродистые и среднеуглеродистые стали, с повышением температуры, становятся более пластичными (1). Высоколегированные стали имеют большую пластичность в холодном состоянии (2). Для шарикоподшипниковых сталей пластичность практически не зависит от температуры (3) . Отдельные сплавы могут иметь интервал повышенной пластичности (4). Техническое железо в интервале 800…1000 0С характеризуется понижением пластических свойств (5). При температурах, близких к температуре плавления пластичность резко снижается из-за возможного перегрева и пережога.
Влияние обработки металлов давлением на структуру и свойства металлов, и эксплуатационные характеристики деталей
Лекция 8. Нагрев металлов перед обработкой давлением. Прокатка.
При нагреве металла с повышением температуры уменьшается его временное сопротивление, а относительное удлинение увеличивается. Таким образом, при деформации стали, нагретой, например, до 1200°С, можно достичь большего формоизменения при меньшем приложенном усилии, чем при деформировании ненагретой стали. Все металлы и сплавы имеют тенденцию к увеличению пластичности и уменьшению сопротивления деформированию при повышении температуры в случае выполнения ряда требований, предъявляемых к процессу нагрева. Так, каждый металл должен быть нагрет до вполне определенной максимальной температуры. Если нагреть, например, сталь до температуры, близкой к температуре плавления, наступает пережог, выражающийся в появлении хрупкой пленки между зернами металла вследствие окисления их границ. При этом происходит полная потеря пластичности. Пережог исправить нельзя, пережженный металл может быть отправлен только на переплавку.
Ниже температуры пережога находится зона перегрева. Явление перегрева заключается в резком росте размеров зерен. Вследствие того, что крупнозернистой первичной кристаллизации (аустенит), как правило, соответствует крупнозернистая вторичная кристаллизация (феррит + перлит или перлит + цементит), механические свойства изделия, полученного обработкой давлением из перегретой заготовки, оказываются низкими. Брак по перегреву в большинстве случаев можно исправить отжигом. Однако для некоторых сталей (например, хромоникелевых) исправление перегретого металла сопряжено со значительными трудностями, и простой отжиг оказывается недостаточным.
Максимальную температуру нагрева, т. е. температуру начала горячей обработки давлением, следует назначать такой, чтобы не было пережога и перегрева. В процессе обработки нагретый металл обычно остывает, соприкасаясь с более холодным инструментом и окружающей средой. Заканчивать горячую обработку давлением следует также при вполне определенной температуре, ниже которой пластичность вследствие упрочнения (рекристаллизация не успевает произойти) падает и в изделии возможно образование трещин. Но при высоких температурах заканчивать деформирование нецелесообразно (особенно для сплавов, не имеющих фазовых превращений). В этом случае после деформирования зерна успевают вырасти и получается крупнозернистая структура, характеризующаяся низкими механическими свойствами.
Каждый металл и сплав имеет свой строго определенный температурный интервал горячей обработки давлением. Например, алюминиевый сплав АК4 470—350 °С; медный сплав БрАЖМц 900—750 °С; титановый сплав ВТ8 1100—900 °С. Для углеродистых сталей температурный интервал нагрева можно определить по диаграмме состояния (см. разд. 1) в зависимости от содержания углерода. Например, для стали 45 температурный интервал 1200—750 °С, а для стали У10 1100—850 °С.
Заготовка должна быть равномерно нагрета по всему объему до требуемой температуры. Разность температур по сечению заготовки приводит к тому, что вследствие теплового расширения между более нагретыми поверхностными слоями металла и менее нагретыми внутренними слоями возникают напряжения. Последние тем больше, чем больше разность температур по сечению заготовки, и может возрасти настолько, что в центральной зоне с растягивающими напряжениями при низкой пластичности металла образуются трещины. Разность температур по сечению увеличивается с повышением скорости нагрева, поэтому существует допустимая скорость нагрева. Наибольшее время требуется для нагрева крупных заготовок из высоколегированных сталей из-за их низкой теплопроводности. Например, время нагрева слитка массой 40 т. из легированной стали составляет более 24 ч.
Однако с увеличением времени нагрева увеличивается окисление поверхности металла, так как при высоких температурах металл активнее химически взаимодействует с кислородом воздуха. В результате на поверхности, например, стальной заготовки образуется окалина—слой, состоящий из оксидов железа: Fe2O3, Fe3O4, FeO. Кроме потерь металла с окалиной, последняя, вдавливаясь в поверхность заготовки при деформировании, вызывает необходимость увеличения припусков на механическую обработку. Окалина увеличивает износ деформирующего инструмента, так как ее твердость значительно больше твердости горячего металла.
При высоких температурах на поверхности стальной заготовки интенсивно окисляется не только железо, но и углерод: происходит так называемое обезуглероживание. Толщина обезуглероженного слоя в отдельных случаях достигает 1,5—2 мм.
Для уменьшения окисления заготовки нагревают в нейтральной или восстановительной атмосфере.
Повышение эффективности нагревательных устройств. Понятие о механизации и автоматизации нагревательных устройств.
Прокат и его производство
Прокатка – это способ обработки пластическим деформированием – наиболее распространённый. Прокатке подвергают до 90 % всей выплавляемой стали и большую часть цветных металлов. Способ зародился в XVIII веке и, претерпев значительное развитие, достиг высокого совершенства.
Сущность процесса: заготовка обжимается (сдавливается), проходя в зазор между вращающимися валками, при этом, она уменьшается в сво¨м поперечном сечении и увеличивается в длину. Форма поперечного сечения называется профилем.
Способы прокатки
Когда требуется высокая прочность и пластичность, применяют заготовки из сортового или специального проката. В процессе прокатки литые заготовки подвергают многократному обжатию в валках прокатных станов, в результате чего повышается плотность материала за сч¨т залечивания литейных дефектов, пористости, микротрещин. Это придает заготовкам из проката высокую прочность и герметичность при небольшой их толщине.
Существуют три основных способа прокатки, имеющих определенное отличие по характеру выполнения деформации: продольная, поперечная, поперечно – винтовая (рис. 14).
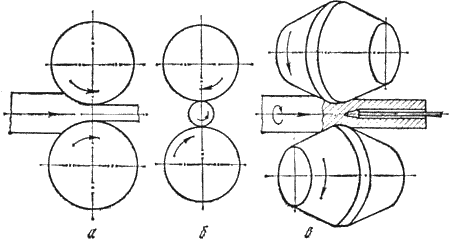
Рис. 14. Схемы основных видов прокатки:
а – продольная; б – поперечная; в – поперечно – винтовая
При продольной прокатке деформация осуществляется между вращающимися в разные стороны валками (рис. 14 а). Заготовка втягивается в зазор между валками за счет сил трения. Этим способом изготавливается около 90 % проката: весь листовой и профильный прокат.
Поперечная прокатка (рис. 14.б). Оси прокатных валков и обрабатываемого тела параллельны или пересекаются под небольшим углом. Оба валка вращаются в одном направлении, а заготовка круглого сечения – в противоположном.
В процессе поперечной прокатки обрабатываемое тело удерживается в валках с помощью специального приспособления. Обжатие заготовки по диаметру и придание ей требуемой формы сечения обеспечивается профилировкой валков и изменением расстояния между ними. Данным способом производят специальные периодические профили, изделия представляющие тела вращения – шары, оси, шестерни.
Поперечно – винтовая прокатка (рис. 14.в). Валки, вращающиеся в одну сторону, установлены под углом друг другу. Прокатываемый металл получает ещ¨ и поступательное движение. В результате сложения этих движений каждая точка заготовки движется по винтовой линии. Применяется для получения пустотелых трубных заготовок.
Технико–экономические показатели производства отдельных видов проката.
Лекция 9. Прессование и волочение
Прессование
Прессование – вид обработки давлением, при котором металл выдавливается из замкнутой полости через отверстие в матрице, соответствующее сечению прессуемого профиля.
Это современный способ получения различных профильных заготовок: прутков диаметром 3…250 мм, труб диаметром 20…400 мм с толщиной стенки 1,5…15 мм, профилей сложного сечения сплошных и полых с площадью поперечного сечения до 500 см2.
Впервые метод был научно обоснован академиком Курнаковым Н. С. в 1813 году и применялся главным образом для получения прутков и труб из оловянисто-свинцовых сплавов. В настоящее время в качестве исходной заготовки используют слитки или прокат из углеродистых и легированных сталей, а также из цветных металлов и сплавов на их основе (медь, алюминий, магний, титан, цинк, никель, цирконий, уран, торий).
Технологический процесс прессования включает операции:
подготовка заготовки к прессованию (разрезка, предварительное обтачивание на станке, так как качество поверхности заготовки оказывает влияние на качество и точность профиля); нагрев заготовки с последующей очисткой от окалины; укладка заготовки в контейнер; непосредственно процесс прессования; отделка изделия (отделение пресс-остатка, разрезка).
Прессование производится на гидравлических прессах с вертикальным или горизонтальным расположением плунжера, мощностью до 10 000 т.
Применяются две метода прессования: прямой и обратный (рис. 15.)
При прямом прессовании движение пуансона пресса и истечение металла через отверстие матрицы происходят в одном направлении. При прямом прессовании требуется прикладывать значительно большее усилие, так как часть его затрачивается на преодоление трения при перемещении металла заготовки внутри контейнера. Пресс-остаток составляет 18…20 % от массы заготовки (в некоторых случаях – 30…40 %). Но процесс характеризуется более высоким качеством поверхности, схема прессования более простая.
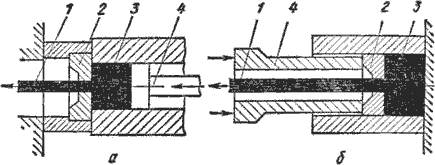
Рис. 15. Схема прессования прутка прямым (а) и обратным (б) методом
1 – готовый пруток; 2 – матрица; 3 – заготовка; 4 - пуансон
При обратном прессовании заготовку закладывают в глухой контейнер, и она при прессовании остается неподвижной, а истечение металла из отверстия матрицы, которая крепится на конце полого пуансона, происходит в направлении, обратном движению пуансона с матрицей. Обратное прессование требует меньших усилий, пресс-остаток составляет 5…6 %. Однако меньшая деформация приводит к тому, что прессованный пруток сохраняет следы структуры литого металла. Конструктивная схема более сложная
Процесс прессования характеризуется следующими основными параметрами: коэффициентом вытяжки, степенью деформации и скоростью истечения металла из очка матрицы.
К основным преимуществам процесса относятся:
· возможность обработки металлов, которые из-за низкой пластичности другими методами обработать невозможно;
· возможность получения практически любого профиля поперечного сечения;
· получение широкого сортамента изделий на одном и том же прессовом оборудовании с заменой только матрицы;
· высокая производительность, до 2…3 м/мин.
Недостатки процесса :
· повышенный расход металла на единицу изделия из-за потерь в виде пресс-остатка;
· появление в некоторых случаях заметной неравномерности механических свойств по длине и поперечному сечению изделия;
· высокая стоимость и низкая стойкость прессового инструмента;
· высокая энергоемкость.
Технико–экономические показатели получения изделий методом прессования
Волочение
Сущность процесса волочения заключается в протягивании заготовок через сужающееся отверстие (фильеру) в инструменте, называемом волокой. Конфигурация отверстия определяет форму получаемого профиля. Схема волочения представлена на рис. 16.
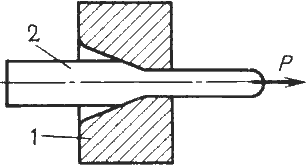
Рис.16. Схема волочения
Волочением получают проволоку диаметром 0,002…4 мм, прутки и профили фасонного сечения, тонкостенные трубы, в том числе и капиллярные. Волочение применяют также для калибровки сечения и повышения качества поверхности обрабатываемых изделий. Волочение чаще выполняют при комнатной температуре, когда пластическую деформацию сопровождает наклеп, это используют для повышения механических характеристик металла, например, предел прочности возрастает в 1,5…2 раза.
Исходным материалом может быть горячекатаный пруток, сортовой прокат, проволока, трубы. Волочением обрабатывают стали различного химического состава, цветные металлы и сплавы, в том числе и драгоценные.
Основной инструмент при волочении – волоки различной конструкции. Волока работает в сложных условиях: большое напряжение сочетается с износом при протягивании, поэтому их изготавливают из твердых сплавов. Для получения особо точных профилей волоки изготавливают из алмаза. Конструкция инструмента представлена на рис. 17.
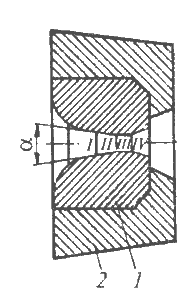
Рис.17. Общий вид волоки
Волока 1 закрепляется в обойме 2. Волоки имеют сложную конфигурацию, ее составными частями являются: заборная часть I, включающая входной конус и смазочную часть; деформирующая часть II с углом в вершине (6…18 0 – для прутков, 10…24 0 – для труб); цилиндрический калибрующий поясок III длиной 0,4…1 мм; выходной конус IV.
Технологический процесс волочения включает операции:
предварительный отжиг заготовок для получения мелкозернистой структуры металла и повышения его пластичности; травление заготовок в подогретом растворе серной кислоты для удаления окалины с последующей промывкой, после удаления окалины на поверхность наносят подсмазочный слой путем омеднения, фосфотирования, известкования, к слою хорошо прилипает смазка и коэффициент трения значительно снижается; волочение, заготовку последовательно протягивают через ряд постепенно уменьшающихся отверстий; отжиг для устранения наклепа: после 70…85 % обжатия для стали и 99 % обжатия для цветных металлов ; отделка готовой продукции (обрезка концов, правка, резка на мерные длины и др.)
Технологический процесс волочения осуществляется на специальных волочильных станах. В зависимости от типа тянущего устройства различают станы: с прямолинейным движением протягиваемого металла (цепной, реечный); с наматыванием обрабатываемого металла на барабан (барабанный). Станы барабанного типа обычно применяются для получения проволоки. Число барабанов может доходить до двадцати. Скорость волочения достигает 50 м/с.
Технико-экономические показатели работы волочильных станов.
|
|
|