Пояснения к 1 и 2 задания по кр
![]()
|
|
Компонент | Копченый лист | Светлый креп |
Влага | 0,6 | 0,4 |
Ацетонорастворимый материал | 2,9 | 2,9 |
Белки | 2,8 | 2,8 |
Зола | 0,4 | 0,3 |
Водорастворимый материал | 1,0 | 1,0 |
Сложные эфиры, не растворимые в ацетоне | 1,0 | 1,0 |
Углеводород каучука | 91,3 | 91,6 |
Углеводород каучука – это полиизопрен, углеводородное полимерное химическое соединение, имеющее общую формулу (C5H8)n. Как именно в дереве синтезируется углеводород каучука, неизвестно. Невулканизованный каучук становится мягким и липким в теплую погоду и хрупким – в холодную. При нагреве выше 180º С в отсутствие воздуха каучук разлагается и выделяет изопрен.
Углеводород каучука присутствует в латексе в виде суспензии мельчайших частиц, размер которых составляет от 0,1 до 0,5 мкм. Самые крупные частицы видны через ультрамикроскоп; они находятся в состоянии непрерывного движения, которое может служить иллюстрацией явления, называемого броуновским движением.
Каждая каучуковая частица несет отрицательный заряд. Если через латекс пропускать ток, то такие частицы будут двигаться к положительному электроду (аноду) и осаждаться на нем. Это явление используется в промышленности для нанесения покрытий на металлические предметы. На поверхности каучуковых частиц присутствуют адсорбированные белки, которые препятствуют сближению латексных частиц и их коагуляции. Заменяя вещество, адсорбированное на поверхности частицы, можно изменить знак ее заряда, и тогда каучуковые частицы будут осаждаться на катоде.
Синтетический каучук начали производить с 1923 г. Каучук относится к классу ненасыщенных органических соединений, которые проявляют значительную химическую активность при взаимодействии с другими реакционноспособными веществами. Так, он реагирует с хлороводородной кислотой с образованием гидрохлорида каучука, а также с хлором по механизмам присоединения и замещения с образованием хлорированного каучука. Атмосферный кислород действует на каучук медленно, делая его жестким и хрупким; озон делает то же самое быстрее. Сильные окислители, например азотная кислота, перманганат калия и перекись водорода, окисляют каучук. Он устойчив к действию щелочей и умеренно сильных кислот. Каучук реагирует также с водородом, серой, серной кислотой, сульфоновыми кислотами, окислами азота и многими другими реакционноспособными соединениями, образуя производные, часть из которых имеет промышленное применение.
Каучук обладает двумя важными свойствами, которые обусловливают его промышленное применение. В вулканизованном состоянии он упруг и после растяжения принимает первоначальную форму; в невулканизованном состоянии он пластичен, т.е. течет под воздействием тепла или давления.
Одно свойство каучуков уникально: при растяжении они нагреваются, а при сжатии – охлаждаются. Наоборот, при нагревании каучук сжимается, а при охлаждении – расширяется, демонстрируя явление, называемое эффектом Джоуля. При растяжении на несколько сот процентов молекулы каучука ориентируются до такой степени, что его волокна дают рентгенограмму, свойственную кристаллу. Молекулы каучука, добытого из гевеи, имеют цис-конфигурацию, а молекулы балаты и гуттаперчи – транс-конфигурацию. Будучи плохим проводником электричества, каучук используется и как электрический изолятор.
Синтез каучука, происходящий в дереве, никогда не выполнялся в лаборатории. Синтетические каучуки являются эластичными материалами; они сходны с натуральным продуктом по химическим и физическим свойствам, но отличаются от него структурой.
Синтез аналога натурального каучука (1,4-цис-полиизопрена и 1,4-цис-полибутадиена). Натуральный каучук, получаемый из гевеи бразильской, имеет структуру, состоящую на 97,8% из 1,4-цис-полиизопрена:
Синтез 1,4-цис-полиизопрена проводился несколькими различными путями с использованием регулирующих стереоструктуру катализаторов, и это позволило наладить производство различных синтетических эластомеров. Катализатор Циглера состоит из триэтилалюминия и четыреххлористого титана; он заставляет молекулы изопрена объединяться (полимеризоваться) с образованием гигантских молекул 1,4-цис-полиизопрена (полимера). Аналогично, металлический литий или алкил- и алкиленлитиевые соединения, например бутиллитий, служат катализаторами полимеризации изопрена в 1,4-цис-полиизопрен. Реакции полимеризации с этими катализаторами проводятся в растворе с использованием углеводородов нефти в качестве растворителей. Синтетический 1,4-цис-полиизопрен обладает свойствами натурального каучука и может использоваться как его заместитель в производстве резиновых изделий.
Полибутадиен, на 90–95% состоящий из 1,4-цис-изомера, также был синтезирован посредством регулирующих стереоструктуру катализаторов Циглера, например триэтилалюминия и четырехиодистого титана. Другие регулирующие стереоструктуру катализаторы, например хлорид кобальта и алкилалюминий, также дают полибутадиен с высоким (95%) содержанием 1,4-цис-изомера. Бутиллитий тоже способен полимеризовать бутадиен, однако дает полибутадиен с меньшим (35–40%) содержанием 1,4-цис-изомера. 1,4-цис-полибутадиен обладает чрезвычайно высокой эластичностью и может использоваться как наполнитель натурального каучука.
Тиокол (полисульфидный каучук). В 1920, пытаясь получить новый антифриз из этиленхлорида и полисульфида натрия, Дж.Патрик вместо этого открыл новое каучукоподобное вещество, названное им тиоколом. Тиокол высокоустойчив к бензину и ароматическим растворителям. Он имеет хорошие характеристики старения, высокое сопротивление раздиру и низкую проницаемость для газов. Не будучи настоящим синтетическим каучуком, он, тем не менее, находит применение для изготовления резин специального назначения.
Неопрен (полихлоропрен). В 1931 компания «Дюпон» объявила о создании каучукоподобного полимера, или эластомера, названного неопреном. Неопрен изготавливают из ацетилена, который, в свою очередь, получают из угля, известняка и воды. Ацетилен сначала полимеризуют до винилацетилена, из которого путем добавления хлороводородной кислоты производят хлоропрен. Далее хлоропрен полимеризуют до неопрена. Помимо маслостойкости неопрен имеет высокую тепло- и химическую стойкость и используется в производстве шлангов, труб, перчаток, а также деталей машин, например шестерен, прокладок и приводных ремней.
Буна S (SBR, бутадиенстирольный каучук). Синтетический каучук типа буна S, обозначаемый как SBR, производится в больших реакторах с рубашкой, или автоклавах, в которые загружают бутадиен, стирол, мыло, воду, катализатор (персульфат калия) и регулятор роста цепи (меркаптан). Мыло и вода служат для эмульгирования бутадиена и стирола и приведения их в близкий контакт с катализатором и регулятором роста цепи. Содержимое реактора нагревается до примерно 50° С и перемешивается в течение 12–14 ч; за это время в результате процесса полимеризации в реакторе образуется каучук. Получающийся латекс содержит каучук в форме малых частиц и имеет вид молока, очень напоминающий натуральный латекс, добытый из дерева.
Латекс из реакторов обрабатывается прерывателем полимеризации для остановки реакции и антиоксидантом для сохранения каучука. Затем он очищается от избытка бутадиена и стирола. Чтобы отделить (путем коагуляции) каучук от латекса, он обрабатывается раствором хлорида натрия (пищевой соли) в кислоте либо раствором сульфата алюминия, которые отделяют каучук в форме мелкой крошки. Далее крошка промывается, сушится в печи и прессуется в кипы.
Из всех эластомеров SBR используется наиболее широко. Больше всего его идет на производство автомобильных шин. Этот эластомер сходен по свойствам с натуральным каучуком. Он не маслостоек и в большинстве случаев проявляет низкую химическую стойкость, но обладает высоким сопротивлением удару и истиранию.
Латексы для эмульсионных красок. Бутадиен-стирольные латексы широко используются в эмульсионных красках, в которых латекс образует смесь с пигментами обычных красок. В таком применении содержание стирола в латексе должно превышать 60%.
Низкотемпературный маслонаполненный каучук. Низкотемпературный каучук – особый тип каучука SBR. Он производится при 5° С и обеспечивает лучшую износостойкость шин, чем стандартный SBR, полученный при 50° С. Износостойкость шин еще более повышается, если низкотемпературному каучуку придать высокую ударную вязкость. Для этого в базовый латекс добавляют некоторые нефтяные масла, называемые нефтяными мягчителями. Количество добавляемого масла зависит от требуемого значения ударной вязкости: чем оно выше, тем больше вводится масла. Добавленное масло действует как мягчитель жесткого каучука. Другие свойства маслонаполненного низкотемпературного каучука такие же, как у обычного низкотемпературного.
Буна N (NBR, бутадиенакрилонитрильный каучук). Вместе с буна S в Германии был также разработан маслостойкий тип синтетического каучука под названием пербунан, или буна N. Основной компонент этого нитрильного каучука – также бутадиен, который сополимеризуется с акрилонитрилом по существу по тому же механизму, что и SBR. Сорта NBR различаются содержанием акрилонитрила, количество которого в полимере варьирует от 15 до 40% в зависимости от назначения каучука. Нитрильные каучуки маслостойки в степени, соответствующей содержанию в них акрилонитрила. NBR использовался в тех видах военного оборудования, где требовалась маслостойкость, например в шлангах, самоуплотняющихся топливных элементах и конструкциях транспортных средств.
Бутилкаучук. Бутилкаучук – еще один синтетический каучук – был открыт в 1940. Он замечателен своей низкой газопроницаемостью; камера шины из этого материала удерживает воздух в 10 раз дольше, чем камера из натурального каучука. Бутилкаучук изготавливают полимеризацией изобутилена, получаемого из нефти, с малой добавкой изопрена при температуре 100° С.
Эта полимеризация не является эмульсионным процессом, а проводится в органическом растворителе, например метилхлориде. Свойства бутилкаучука могут быть сильно улучшены термообработкой маточной смеси бутилкаучука и газовой сажи при температуре от 150 до 230º С. Недавно бутилкаучук нашел новое применение как материал для протекторов шин ввиду его хороших ходовых характеристик, отсутствия шума и превосходного сцепления с дорогой. Бутилкаучук несовместим с натуральным каучуком и SBR и, значит, не может быть смешан с ними. Однако после хлорирования до хлорбутилкаучука он становится совместимым с натуральным каучуком и SBR. Хлорбутилкаучук сохраняет низкую газопроницаемость. Это свойство используется при изготовлении смешанных продуктов хлорбутилкаучука с натуральным каучуком или SBR, которые служат для производства внутреннего слоя бескамерных шин.
Этиленпропиленовый каучук. Сополимеры этилена и пропилена могут быть получены в широких диапазонах составов и молекулярных масс. Эластомеры, содержащие 60–70% этилена, вулканизуются с пероксидами и дают вулканизат с хорошими свойствами. Этиленпропиленовый каучук имеет превосходную атмосферо- и озоностойкость, высокую термо-, масло- и износостойкость, но также и высокую воздухопроницаемость. Такой каучук изготавливается из дешевых сырьевых материалов и находит многочисленные применения в промышленности.
Наиболее широко применяемым типом этиленпропиленового каучука является тройной этиленпропиленовый каучук (с диеновым сомономером). Он используется в основном для изготовления оболочек проводов и кабелей, однослойной кровли и в качестве присадки для смазочных масел. Его малая плотность и превосходная озоно- и атмосферостойкость обусловливают его применение в качестве кровельного материала.
Вистанекс. Вистанекс, или полиизобутилен, – полимер изобутилена, также получаемый при низких температурах. Он подобен каучуку по свойствам, но в отличие от каучука является насыщенным углеводородом и, значит, не может быть подвергнут вулканизации. Полиизобутилен озоностоек.
Коросил. Коросил, каучукоподобный материал, – это пластифицированный поливинилхлорид, приготовленный из винилхлорида, который, в свою очередь, получают из ацетилена и хлороводородной кислоты. Коросил замечательно стоек к действию окислителей, в том числе озона, азотной и хромовой кислот, и поэтому используется для внутренней облицовки цистерн с целью защиты их от коррозии. Он непроницаем для воды, масел и газов и в силу этого находит применение как покрытие для тканей и бумаги. Каландрованный материал используется в производстве плащей, душевых занавесок и обоев. Низкое водопоглощение, высокая электрическая прочность, негорючесть и высокое сопротивление старению делают пластифицированный поливинилхлорид пригодным для изготовления изоляции проводов и кабелей.
Полиуретан. Класс эластомеров, известных как полиуретаны, находит применение в производстве пеноматериалов, клеев, покрытий и формованных изделий. Изготовление полиуретанов включает несколько стадий. Сначала получают сложный полиэфир реакцией дикарбоновой кислоты, например адипиновой, с многоатомным спиртом, в частности этиленгликолем или диэтиленгликолем. Полиэфир обрабатывают диизоцианатом, например толуилен-2,4-диизоцианатом или метилендифенилендиизоцианатом. Продукт этой реакции обрабатывают водой и подходящим катализатором, в частности n-этилморфолином, и получают упругий или гибкий пенополиуретан. Добавляя диизоцианат, получают формованные изделия, в том числе шины. Меняя соотношение гликоля и дикарбоновой кислоты в процессе производства сложного полиэфира, можно изготовить полиуретаны, которые используются как клеи или перерабатываются в твердые или гибкие пеноматериалы либо формованные изделия. Пенополиуретаны огнестойки, имеют высокую прочность на растяжение, очень высокое сопротивление раздиру и истиранию. Они проявляют исключительно высокую несущую способность и хорошее сопротивление старению. Вулканизованные полиуретановые каучуки имеют высокие прочность на растяжение, сопротивление истиранию, раздиру и старению. Был разработан процесс получения полиуретанового каучука на основе простого полиэфира. Такой каучук хорошо ведет себя при низких температурах и устойчив к старению.
Кремнийорганический каучук. Кремнийорганические каучуки не имеют себе равных по пригодности к эксплуатации в широком температурном интервале (от -73 до 315° С). Для вулканизованных кремнийорганических каучуков была достигнута прочность на растяжение около 14 МПа. Их сопротивление старению и диэлектрические характеристики также весьма высоки.
Хайпалон (хлорсульфоэтиленовый каучук). Этот эластомер хлорсульфонированного полиэтилена получают обработкой полиэтилена хлором и двуокисью серы. Вулканизованный хайпалон чрезвычайно озоно- и атмосферостоек и имеет хорошую термо- и химическую стойкость.
Фторсодержащие эластомеры. Эластомер кель-F – сополимер хлортрифторэтилена и винилиденфторида. Этот каучук имеет хорошую термо- и маслостойкость. Он стоек к действию коррозионно-активных веществ, негорюч и пригоден к эксплуатации в интервале от -26 до 200° С. Витон А и флюорел – сополимеры гексафторпропилена и винилиденфторида. Эти эластомеры отличаются превосходной стойкостью к действию тепла, кислорода, озона, атмосферных факторов и солнечного света. Они имеют удовлетворительные низкотемпературные характеристики и пригодны к эксплуатации до -21° С. Фторсодержащие эластомеры используются в тех приложениях, где требуется стойкость к действию тепла и масел.
Специализированные эластомеры. Производятся специализированные эластомеры с разнообразными физическими свойствами. Многие из них очень дороги. Наиболее важные из них – акрилатные каучуки, хлорсульфонированный полиэтилен, сополимеры простых и сложных эфиров, полимеры на основе эпихлоргидрина, фторированные полимеры и термопластичные блок-сополимеры. Они используются для изготовления уплотнений, прокладок, шлангов, оболочек проводов и кабелей и клеев.
Резина (от латинского resina-смола) (вулканизат) – эластичный материал, образующийся в результате вулканизации натурального и синтетических каучуков. Представляет собой сетчатый эластомер - продукт поперечного сшивания молекул каучуков химическими связями.
Резину можно рассматривать как сшитую коллоидную систему, в которой каучук составляет дисперсионную среду, а наполнители - дисперсную фазу. Важнейшее свойство резины – высокая эластичность, т. е. способность к большим обратимым деформациям в широком интервале температур (высокоэластическое состояние). Полимеры в высокоэластичном состоянии отличаются способностью к огромным обратимым деформациям растяжения (до многих сотен процентов), низкими значениями модуля эластичности [0,1—10 Мн/м2 (1—100 кгс/см2)], выделением тепла при растяжении, возрастанием равновесного модуля эластичности с температурой и другими особенностями.
Высокоэластичное состояние возникает благодаря способности цепных молекул полимеров к изменению формы. Гибкие цепные молекулы под влиянием теплового движения непрерывно меняют свою форму, т. е. принимают ряд различных конформаций. При достаточно большой длине молекул число разрешённых скрученных конформаций подавляюще велико. Воздействие растягивающих сил распрямляет макромолекулы; после прекращения действия сил она вновь скручивается благодаря хаотическому характеру теплового движения. Таким образом, сопротивление изменению формы полимерного тела в основном обусловлено не изменением внутренней энергии, как в кристаллических телах, а увеличением числа более распрямлённых конформаций.
Резина сочетает в себе свойства твердых тел (упругость, стабильность формы), жидкостей (аморфность, высокая деформируемость при малом объемном сжатии) и газов (повышение упругости вулканизационных сеток с ростом температуры, энтропийная природа упругости).
Резина - сравнительно мягкий, практически несжимаемый материал. Комплекс ее свойств определяется в первую очередь типом каучука (см. табл. 1); свойства могут существенно изменяться при комбинировании каучуков различные типов или их модификации (см. табл.1).
Модуль упругости резины различные типов при малых деформациях составляет 1-10 МПа, что на 4-5 порядков ниже, чем для стали; коэффициент Пауссона близок к 0,5. Упругие свойства резины нелинейны и носят резко выраженный релаксационный характер: зависят от режима нагружения, величины, времени, скорости (или частоты), повторности деформаций и температуры. Деформация обратимого растяжения резины может достигать 500-1000%.
Нижний предел температурного диапазона высокоэластичности резины обусловлен главным образом температурой стеклования каучуков, а для кристаллизующихся каучуков зависит также от температуры и скорости кристаллизации. Верхний температурный предел эксплуатации резины связан с термодинамической стойкостью каучуков и поперечных химических связей, образующихся при вулканизации. Ненаполненные резины на основе некристаллизующихся каучуков имеют низкую прочность. Применение активных наполнителей (высокодисперсных саж, SiO2 и др.) позволяет на порядок повысить прочностные характеристики резины и достичь уровня показателей резины из кристаллизующихся каучуков. Твердость резины определяется содержанием в ней наполнителей и пластификаторов, а также степенью вулканизации. Плотность резины рассчитывают как средневзвешенное по объему значение плотностей отдельных компонентов. Аналогичным образом могут быть приближенно вычислены (при объемном наполнении менее 30%) теплофизических характеристики резины: коэффициент термодинамического расширения, удельная объемная теплоемкость, коэффициент теплопроводности. Циклическое деформирование резины сопровождается упругим гистерезисом, что обусловливает их хорошие амортизационные свойства. Резина характеризуются также высокими фрикционными свойствами, износостойкостью, сопротивлением раздиру и утомлению, тепло- и звукоизоляционными свойствами. Они диамагнетики и хорошие диэлектрики, хотя может быть получены токопроводящие и магнитные резины.
Резины незначительно поглощают воду и ограниченно набухают в органических растворителях. Степень набухания определяется разницей параметров растворимости каучука и растворителя (тем меньше, чем выше эта разность) и степенью поперечного сшивания (величину равновесного набухания обычно используют для определения степени поперечного сшивания). Каучук не растворяется в воде, спирте или ацетоне, однако набухает и растворяется в бензоле, толуоле, бензине, сероуглероде, скипидаре, хлороформе, четыреххлористом углероде и других галогенсодержащих растворителях, образуя вязкую массу, применяемую в качестве клея. Известны резины, характеризующиеся масло-, бензо-, водо-, паро- и термостойкостью, стойкостью к действию химический агрессивных сред, озона, света, ионизирующих излучений. При длительном хранении и эксплуатации резина подвергаются старению и утомлению, приводящим к ухудшению их механические свойств, снижению прочности и разрушению. Срок службы резины в зависимости от условий эксплуатации от несколько дней до несколько десятков лет.
Классификация. По назначению различают следующие основные группы резин: общего назначения, теплостойкие, морозостойкие, маслобензостойкие, стойкие к действию химический агрессивных сред, диэлектрическая, электропроводящие, магнитные, огнестойкие, радиационностойкие, вакуумные, фрикционные, пищевая и мед. назначения, для условий тропического климата и другие (табл. 2); получают также пористые, или губчатые, цветные и прозрачные резины.
Применение. Резина широко используют в технике, сельском хозяйстве, быту, медицине, строительстве, спорте. Ассортимент резиновых изделий насчитывает более 60 тысяч наименований. Среди них: шины, транспортные ленты, приводные ремни, рукава, амортизаторы, уплотнители, сальники, манжеты, кольца, кабельные изделия, обувь, ковры, трубки, покрытия и облицовочные материалы, прорезиненные ткани, герметики и др. Более половины объема вырабатываемой резины используется в производстве шин.
Мировое производство резиновых изделий более 20 млн. тонн/год.
В данном проекте рассмотрено производство этиленпропиленовых каучуков и резин на их основе.
Структура и свойства этиленпропиленовых каучуков
Этиленпропиленовые качуки – сополимеры этилена с пропиленом или терполимеры этих двух мономеров с несопряженным диеном.
Макромолекула этиленпропиленового каучука содержит от 50 до 70 мол. % этиленовых звеньев, сополимеры с большим количеством этих звеньев в молекуле являются термопластами (термопласты - пластмассы, которые после формования изделия сохраняют способность к повторной переработке).
Молекулярная масса: 80-250 тыс.;
Плотность: 0,85-0,87 г/см3;
теплопроводность 20,81·10-4 Вт(м·К);
Этиленпропиленовые каучуки мало набухают в полярных растворителях, но нестойки к действию углеводородных масел и неполярных растворителей.
Основные цепи сополимера и терполимера не содержат двойных связей, поэтому этиленпропиленовые каучуки превосходят другие типы синтетических каучуков по озоно-, свето- и атмосферостойкости; обладают длительной теплостойкостью при температурах до 150 °С и кратковременной при 200 °С; стойки к воздействию окислительных и агрессивных сред. Недостатки этиленпропиленовых каучуков - низкая масло- и огнестойкость.
Каучуки с низким содержанием пропилена (20-30%) характеризуются высокой прочностью невулканизованной смеси, каучуки с высоким его содержанием (45-50%) - низкой прочностью, но достаточно высокой морозостойкостью. В зависимости от молекулярной массы этиленпропиленовые каучуки делят на низко-, средне- и высоковязкие; их вязкости по Муни, измеренные при 100 °С, 120 °С, 125-200 °С, составляют соотв. 25-60, 60-100 и 100-120 единиц.
Общие сведения о получении этиленпропиленовы каучуков
Получение этиленпропиленовых каучуков стало возможно после открытия катализаторов Циглера-Натта (каталитические комплексы, образующиеся при взаимодействии соединений переходных металлов [TiCl4, TiCl3, VOC13, (C5H5)2TiCl2 и т. п.] с алкильными производными и другими соединениями металлов I - III групп (AlR3, A1R2C1, LiR, MgRCl, ZnR2 и др.); один из видов катализаторов полимеризации).
Сырьём для получения этих каучуков являются продукты пиролиза (термическое разложение органических соединений без доступа воздуха) нестабильного бензина: этилен и пропилен.
Этиленпропиленовые каучуки выпускаются в виде двойных (СКЭП) и тройных (СКЭПТ) сополимеров этилена с пропиленом. В качестве третьего мономера применяют диеновые углеводороды, как например 1,4-гексадиен:

1,5-циклооктадиен:
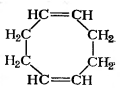
дициклопентадиен:
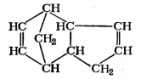
этилиденноборнен:
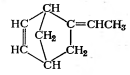
Наиболее доступным из этих мономеров является дициклопентадиен. Однако тройные сополимеры с дициклопентадиеном обладают низкими физико-механическими показателями. В последнее время в качестве третьего мономера стали применять этилиденноборнен.
В промышленности освоен выпуск 4 марок СКЭП и 7 марок СКЭПТ.
Работы по синтезу этиленпропиленовых каучуков начаты в СССР в 1956 г. В результате были разработаны 2 способа получения каучуков: в среде инертного растворителя (гексан, изопентан) и в среде жидкого пропилена.
Технология получения этиленпропиленовых каучуков
В процессе полимеризации применяют этилен с содержанием основного вещества 99,9%, а пропилен – не менее 99,8%.
Схема полимеризации этилена с пропиленом:

Этилен Пропилен Сополимер этилена и пропилена

Вредное воздействие на процесс полимеризации оказывают примеси ацетилена, кислорода, влаги и сернистых соединений. Поэтому их предельное содержание в мономерах должно составлять не более 0,001-0,002%.
Сополимеризацию (полимеризация, в которой участвуют 2 или более мономера различных типов) этилена и пропилена ведут с применением каталитических систем на основе соединений ванадия и алюминия, ванадия и титана в сочетании с алкилами или алкилхлоридами алюминия.
Поскольку этилен и пропилен имеют различную активность, соотношение мономеров в сополимере отличается от соотношения в зоне реакции. Для получения каучуков заданного состава необходимо обеспечить постоянство концентрации исходных мономеров во времени и по всему объему реакционной зоны. Поэтому при сополимеризации применяются реакторы реального перемешивания. Теплота реакции отводится при испарении мономеров через теплопередающие поверхности реактора.
Процессы получения этиленпропиленовых каучуков в промышленности могут быть разделены на 2 типа в зависимости от состояния получаемого полимера на стадии полимеризации – в виде раствора или в виде суспензии.
Схема процесса полученя этиленпропиленовых каучуков в среде избытка пропилена с отводом теплоты реакции за счет испарения мономеров приведена на рис.1.
В реактор 1 поступают мономеры (этилен, пропилен и третий мономер), компоненты каталитического комплекса, а также циркулирующая газожидкостная смесь.
Температура полимеризации поддерживается в пределах 0-20˚С, давление 0,3-0,6 МПа.
Газовая фаза состоит из смеси этилена, пропилена и регулятора молекулярной массы. Их соотношение определяется динамическим равновесием между газом и жидкостью в реакторе. Газовая фаза непрерывно выводится из реактора и поступает на охлаждение и конденсацию в конденсатор 2.
Суспензия полимера из реактора поступает в смеситель 3, в котором происходит смешение с водой и разрушение каталитического комплекса. После смесителя суспензия полимера поступает в отстойник 4 для разделения водного и углеводородного слоёв. Часть продуктов разрушения каталитического комплекса вместе с водным слоем поступает на отмывку, а часть после смешения со свежей водой возвращается в смеситель 3.
После отмывки полученный полимер поступает в дегазатор 5, в котором происходит отгонка с паром непрореагировавших мономеров. В дегазаторе в пульпу полимера вводят антиагломератор (порошкообразный графит, технический углерод) с целью предотвращения слипания крошки. Из дегазатора 5 пульпа поступает на вибросито 6 для отделения воды от крошки полимера. Вода возвращается в отстойник 4, а полимер поступает в червячно-отжимную машину 7, где сначала происходит предварительный отжим полимера от влаги, а на второй стадии – окончательная сушка каучука.
Непрореагировавшие мономеры после ректификационной колонны 8, колонны азеотропной сушки 9, и осушителя 10 возвращаются в процесс.
Преимуществом процесса получения этиленпропиленовых каучуков в избытке пропилена является простота технологического оформления и легкость регулирования соотношения мономеров в реакционной массе.
К недостаткам относится ограниченная возможность регулирования молекулярно-массового распределения полимера.
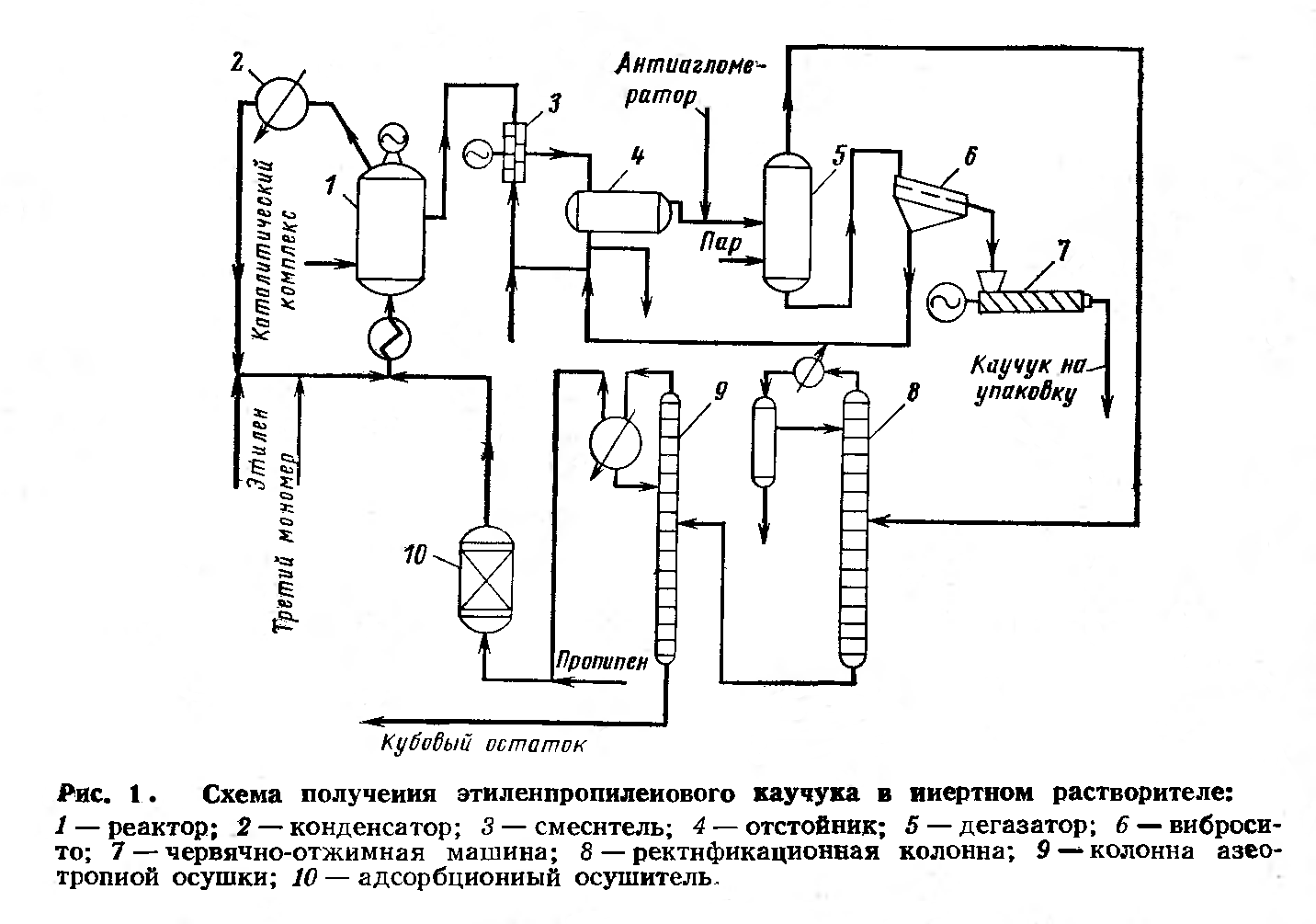
Рис. 1. Схема получения этилен пропиленового каучука в инертном растворителе:
1 – реактор; 2 – конденсатор; 3 – смеситель; 4 – отстойник; 5 – дегазатор; 6 – вибросито; 7 – червячно-отжимная машина; 8 – ректификационная колонна; 9 – колонна азеотропной осушки; 10 – адсорбционный осушитель.
2. Схема производства аммиака.
Промышленные способы синтеза аммиака в зависимости от применяемого давления можно разделить на три группы:
1) под низким давлением до 10 МПа;
2) средним до 20— 30 МПа;
3) высоким давлением до 75— 100 МПа.
В настоящее время в мировой азотной промышленности большая часть синтетического аммиака производится в системах среднего давления. В современных агрегатах синтеза аммиака большой единичной мощности процесс ведут на плавленых железных катализаторах при 420–500 °С и давлении 32 МПа, объемной скорости 15–25 тыс. ч–1; производительность 1 м3 контактной массы составляет 20–40 т/сут.
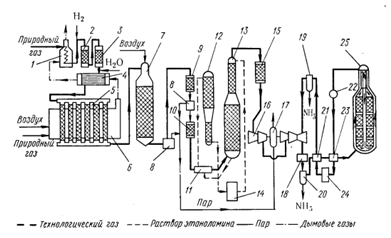
Рис. 2. Принципиальная схема синтеза аммиака под средним давлением:
1 – подогреватель природного газа; 2 – реактор гидрирования органической серы; 3 – адсорбер сероводорода; 4 – теплообменник; 5 – трубчатая печь – конвертор метана; 6 – топка; 7 – шахтный конвертор метана; 8 – паровой котел; 9 – конвертор СО I ступени; 10 – конвертор СО II ступени; 11 — теплообменник; 12 — регенератор СО2; 13 — абсорбер СО2; 14 – воздушный холодильник; 15 – метанатор; 16 – турбокомпрессор с газовой турбиной; 17 – паровая турбина; 18 – аммиачный холодильник; 19 – первичный сепаратор; 20 – вторичный сепаратор; 21 – холодильный теплообменник; 22 – водоподогреватель паровых котлов; 23 – "горячий" теплообменник; 24 – воздушный холодильник; 25 – полочная колонна синтеза.
На рис. 2 приведена схема агрегата мощностью 1360 т/сут, включающая двухступенчатую паровоздушную конверсию метана, высокотемпературную конверсию СО, моноэтаноламиновую очистку от СО2, окончательную очистку от СО и и СО2 каталитическим гидрированием (метанирование) и синтез аммиака. Природный газ под давлением 4 МПа после очистки от серосодержащих соединений смешивается с паром в соотношении 3,7 : 1, подогревается в теплообменнике отходящими газами и поступает в трубчатый конвертор с топкой, в которой сжигается природный газ. Конверсия метана с водяным паром до образования оксида углерода протекает на никелевом катализаторе при 800–850°С. Содержание метана в газе после первой ступени конверсии составляет 9–10%. Далее газ смешивается с воздухом и поступает в шахтный конвертор, где происходит конверсия остаточного метана кислородом воздуха при 900–1000°С и соотношение пар : газ = 0,8 : 1. Из шахтного конвертора газ направляется в котел-утилизатор, где получают пар высоких параметров (10 МПа, 480°С), направляемый в газовые турбины центробежных компрессоров. Из котла-утилизатора газ поступает на двухступенчатую конверсию оксида углерода. Конверсия осуществляется вначале в конверторе I ступени на среднетемпературном железохромовом катализаторе при 430–470°С, затем в конверторе II ступени на низкотемпературном цинкхромомедном катализаторе при 200–260°С. Между первой и второй ступенями конверсии устанавливают котел-утилизатор. Теплота газовой смеси, выходящей из II ступени конвертора СО, используется для регенерации моноэтаноламинового раствора, выходящего из скруббера очистки газа от СО2. Далее газ поступает на очистку от СО2 в скруббер, орошаемый холодным раствором моноэтаноламина, где при 30–40°С происходит очистка газа от СО2. На выходе из абсорбера газ содержит примеси кислородсодержащих ядов (СО до 0,3%, СО2 30–40 см3/м3), которые гидрируют при 280–350°С в метанаторе на никелевом катализаторе. Теплота очищенного газа после метанатора используется для подогрева питательной воды, дальнейшее охлаждение и сепарация выделившейся воды проводятся в аппарате воздушного охлаждения и влагоотделителе (на схеме не показано). Для сжатия азотоводородной смеси до 30 МПа и циркуляции газа в агрегате синтеза используют центробежный компрессор с приводом от паровой конденсационной турбины. Последнее циркуляционное колесо компрессора расположено в отдельном корпусе или совмещено с IV ступенью. Свежая азотоводородная смесь смешивается с циркуляционной смесью перед системой вторичной конденсации, состоящей из аммиачного холодильника и сепаратора, проходит далее два теплообменника и направляется в полочную колонну синтеза. Прореагировавший газ при 320–380°С проходит последовательно водоподогреватель питательной воды, «горячий» теплообменник, аппарат воздушного охлаждения и «холодный» теплообменник, сепаратор жидкого аммиака и поступает на циркуляционное колесо компрессора. Жидкий аммиак из сепараторов направляется в хранилище жидкого аммиака. Содержание аммиака в оборотной азотоводородной смеси над жидким аммиаком зависит от температуры и давления. Так, при давлении 30 МПа и температуре – 5°С в азотоводородной смеси остается приблизительно 2,5% NН3. Основным агрегатом установки синтеза аммиака служит колонна синтеза. Колонны синтеза изготовляют из специальных легированных сталей. При высоких температурах и давлении аммиак и особенно водород взаимодействуют со сталью, ухудшая ее механические свойства. Для снижения температуры стенок холодная азотоводородная смесь, поступающая в колонну синтеза, проходит вдоль внутренней поверхности цилиндрического корпуса колонны. Применяют полочные и трубчатые колонны.
При выбранных температуре и давлении достигается далеко не полное превращение в реакторе - выходящий газ содержит около 16% NH3 (степень превращения 27-28%). Для полноты использования азотовопородной смеси применяют рецикл после реактора отделяют продукт (аммиак), а непрореагировавшие Н2 и N2 возвращают в реактор.
3. Составьте материальный баланс на получение 1 т карбида кальция, содержащего 90%

Дано:

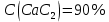


Найти:
Материальный баланс - ?
Решение:
Уравнение химической реакции

Расчёт ведем на 1 т технического продукта.
Молекулярная масса:




В 1 т технического карбида кальция содержится


Тогда на образование



Извести

На образование



Расход антрацита марки АК

Масса образующегося


Сводим материальный баланс получения 1 т карбида кальция в таблицу
Приход | Расход | |||
| т | | т | |
Известь | 0,9265 | ![]() | 1 | |
в т.ч. | | в т. ч. | | |
![]() | 0,7875 | ![]() | 0,9000 | |
примеси | 0,1390 | примеси | 0,1000 | |
Антрацит марки АК | 0,5273 | ![]() | 0,3938 | |
в т.ч. | | примеси (Известь) | 0,0390 | |
![]() | 0,5063 | примеси (Антрацит) | 0,0210 | |
примеси | 0,0210 | | | |
Итого | 1,4538 | Итого | 1,4538 |