|
Теория и технология производства стали 1. Учебник для вузов. М. Мир, ООО Издательство act
27. СТАЛЕПЛАВИЛЬНЫЕ ЦЕХИ И ОРГАНИЗАЦИЯ ИХ РАБОТЫ
Современный сталеплавильный цех — это сложное инженерное сооружение с высокой единичной мощностью агрегатов. Устройство и организация работы сталеплавильного цеха определяются радом условий, к числу которых относятся:
состав завода — имеется в виду наличие или отсутствие в составе завода доменного цеха. Если доменный цех есть в составе завода (завод с полным металлургическим циклом), то чугун в сталеплавильный цех подают в жидком виде и баланс металла по заводу рассчитывают таким образом, чтобы практически весь чугун был израсходован в качестве шихты сталеплавильных цехов непосредственно в жидком виде на самом заводе, т. е. чтобы лишь небольшая часть выплавляемого чугуна разливалась на чушки. В зависимости от состава и расхода чугуна изменяются расходы необходимых для плавки железной руды, известняка, извести и т. п. От этого зависит, какое оборудование используется для хранения и транспортировки материалов, устройство необходимых пролетов и отделений цеха и т. п.;
мощность прокатных цехов. Мощность сталеплавильных цехов должна соответствовать мощности прокатных цехов, с тем чтобы вся выплавляемая сталь прокатывалась непосредственно на заводе, тем самым исключались бы нерациональные перевозки слитков с завода на завод. В прокатных цехах образуется определенное (иногда значительное) количество отходов стали (в основном обрезь проката, включающая головную и хвостовую части слитка). При составлении баланса металла по заводу обычно принимают, что вся образующаяся в прокатных цехах обрезь должна поступать на переплав в сталеплавильные цехи завода; недостающее по расчету количество лома поступает с расположенных поблизости специализированных ломоперера-батывающих предприятий. В зависимости от количества и характера поступающего в сталеплавильный цех металлического лома используется соответствующее оборудование для хранения и транспортировки этих материалов, изменяются размеры необходимых пролетов и отделений цеха и т.д.;
масштабы производства. Мощность современных сталеплавильных цехов достигает 6—10 млн. т стали в год.
В числе действующих в России сталеплавильных цехов еще имеются цехи, построенные 60—70 лет назад. Они строились в условиях, резко отличающихся от современных; все эти цехи реконструируются. Учитывая, что в старых цехах уже имеются подводы электроэнергии, топлива, воды, имеются вспомогательные отделения, здание с колоннами и перекрытиями, крановым оборудованием и т. п., затраты на реконструкцию таких цехов часто оказываются ниже, чем затраты на строительство нового цеха аналогичной мощности;
сортамент выплавляемых сталей и требования к качеству продукции цеха. От состава выплавляемой на заводе стали зависят ассортимент и расход ферросплавов и легирующих. От уровня требований к качеству продукции зависят состав оборудования и число соответствующих пролетов и отделений для размола ферросплавов, подготовки шлакообразу-ющих материалов, плавления синтетического шлака, расплавления ферросплавов и лигатуры, для обработки металла вакуумом, продувки инертным газом и т. п;
требования, предъявляемые существующим законодательством к охране окружающей среды, охране труда и безопасности жизнедеятельности. Эти требования определяют конструктивные особенности устройств, соответствующего оборудования и отделений цеха для улавливания пыли и очистки отходящих газов, очистки и повторного использования воды, поступающей для охлаждения агрегатов, утилизации шлака, а также наличие оборудованных производственных и бытовых помещений для персонала цеха (душевых отделений, гардеробов, комнат отдыха, столовых, медсанчасти, клуба и т. д.).
27.1. ОСОБЕННОСТИ ОРГАНИЗАЦИИ РАБОТЫ В современном цехе, в котором выплавляют в год 8 млн. т стали, работает 1,5—2,0 тыс. человек. Цех за год потребляет 6 млн. т жидкого чугуна, 2 млн. т металлического лома, -100 тыс. т ферросплавов, 1 млн. т извести, 500 тыс. т шлакообразующих. 100—150 тыс. т огнеупоров, 3—5 млрд. м^ кислорода, > 10 млн. м3 воды и т. п. Ежегодно из цеха вывозится 8 млн. т стальных слитков или непрерывноли-тых заготовок и более 1 млн. т шлака.
Таким образом, грузопоток современного сталеплавильного цеха огромен. При решении вопросов, связанных с планировкой цеха и его отделений, а также местом цеха на заводской площадке, прежде всего учитывается система грузопотоков на заводе в целом и внутри цеха в частности. Кроме того, учитывается направление господствующих ветров (по отношению к другим цехам и к городу), а также расстояние от заводских ворот до рабочего места персонала цеха и пр. При проектировании цеха учитываются также местные особенности (например, высокий или низкий уровень грунтовых вод, насколько морозная и ветреная погода зимой или жаркая и влажная погода летом и т. п.). При строительстве завода приходится занимать сельскохозяйственные угодья, вырубать леса и т. п., поэтому площадь, которую будет занимать завод (соответственно цех), должна быть по возможности меньше.
При определении планировки цеха и емкости основных сталеплавильных агрегатов приходится учитывать также ряд других факторов (зачастую взаимоисключающего характера).
Для достижения максимальной производительности основные технологические операции (хранение и транспортировка шихтовых материалов, собственно операция плавки металла, разливка стали и т. д.) должны быть четко разделены по отдельным участкам (пролетам, отделениям) с учетом соответствующего специализированного оборудования: для транспортировки жидкого чугуна необходимы ковши и соответствующее ковшовое и крановое хозяйство, миксеры, оборудование для обработки чугуна в потоке и т. п.; для хранения, транспортировки и подачи к агрегатам металлического лома — соответствующие бункера, магнитные краны и т. п.; для хранения и транспортировки сыпучих материалов (извести, железной руды, боксита и т. п.) — грейферные краны, транспортеры, промежуточные и раздаточные бункера, течки и т. п. Потоки транспорта (и отделения цеха) для жидкого чугуна, металлического лома, сыпучих материалов в современных цехах должны быть раздельными. Для получения высокой производительности агрегатов, снижения затрат на их эксплуатацию, обслуживание и ремонт целесообразно увеличивать вместимость (емкость) агрегатов.
Небольшое число очень крупных агрегатов в цехе с высокой производительностью создает известные трудности при организации производства: 1) остановка одного из таких крупных агрегатов на ремонт, который обычно продолжается несколько суток, приводит к резкому изменению общей суточной производительности цеха. При этом существенно изменяется загрузка оборудования, часть оборудования бездействует, изменяются условия снабжения слитками прокатных станов и т. п.; 2) выпуск плавок из крупных агрегатов сопровождается резким увеличением загрузки оборудования, создает известные трудности при разливке больших масс металла (охлаждение металла, длительное воздействие на футеровку ковша и т. п.), затрудняются условия ритмичного снабжения слитками прокатных цехов (сразу поступает очень крупная партия слитков и т. д.).
Все перечисленные моменты необходимо принимать во внимание при решении вопросов о планировке сталеплавильного цеха и организации его работы.
27.2. ОСНОВНЫЕ ОТДЕЛЕНИЯ
СТАЛЕПЛАВИЛЬНОГО ЦЕХА Сталеплавильные цехи большой производительности строят на заводах с полным металлургическим циклом; они состоят обычно из нескольких основных отделений: 1) шихтового; 2) конвертерного или печного (это отделение часто называют главным зданием цеха); 3) разливочного, а также остальных не менее важных отделений: 4) миксерного, если в цехе установлен стационарный миксер (или миксеры); 5) стрипперного1, в котором производится «раздевание» слитков, т. е. извлечение слитков из изложниц; 6) подготовки составов с изложницами; 7) подготовки ковшей и др.2.
27.2.1. Устройство и оборудование конвертерных цехов. Варианты планировки современного конвертерного цеха приведены на рис. 27.1—27.3. Цех состоит из шихтового, конвертерного и разливочного отделений. Шихтовое отделение, в свою очередь, состоит из отделений магнитных материалов, немагнитных материалов и миксерного. Основными грузопотоками являются:
1) доставка и заливка жидкого чугуна;
2) подача и загрузка лома в конвертер;
3) подача и загрузка шлакообразующих материалов (сыпучих материалов при продувке кислородом сверху и порошкообразных при продувке снизу);
4) подача кислорода (а также защитных составляющих при продувке снизу);
5) подача ферросплавов (в твердом виде или с предварительным расплавлением) в сталеразливочные ковши;
6) прием, транспортировка и разливка жидкой стали;
7) прием и транспортировка шлака;
8) вывоз из цеха стальных слитков или заготовок непрерывной разливки;
9) подача под разливку составов с изложницами (при разливке в слитки);
10) подача к месту ремонта конвертеров и ковшей огнеупорных материалов и вывоз огнеупоров, бывших в употреблении.
Лом подают железнодорожным транспортом в отделение магнитных материалов и разгружают при помощи магнитных кранов в приемные бункера. Для бесперебойной работы цеха желательно иметь в приемных бункерах суточный запас лома. В зимнее время (в зависимости от месторасположения завода) этот запас должен быть большим. Размеры и вместимость бункеров для хранения лома рассчитывают, исходя из данных о его насыпной плотности и необходимом для бесперебойной работы запасе. Из приемных бункеров лом на каждую плавку загружают при помощи магнитных кранов в совки, взвешивают, устанавливают на скраповоз и подают на рабочую площадку. При расходе лома 20-25 % для одной плавки в 350-т конвертер необходимо загрузить 70— 90 т лома. Для уменьшения продолжительности завалки и снижения потерь тепла кладкой печи это количество желательно вместить в один совок, поэтому очень важно получать качественный, заранее подготовленный лом. Вместимость совков в современных цехах достигает 100 м3; их перемещают кранами грузоподъемностью до 200 т. Размеры кусков лома не должны превышать 1500 х 50 х 500 мм. 1 От англ, stripping— выталкивание, девание», извлечение (слитка).
2Стрипперное отделение и отделение подготовки составов имеются в цехах, в которых сталь разливают в слитки. Жидкий чугун поступает в главное здание цеха или из миксерного отделения, или из отделения перелива, куда его привозят передвижными миксерами из доменного цеха. По рабочей площадке конвертерного отделения ковши с жидким чугуном перемещают при помощи самоходных чугуновозов. Состав с ковшами останавливают против соответствующего конвертера, конвертер наклоняют, ковш с чугуном при помощи мостового крана снимают с чугуновозной тележки и чугун выливают в конвертер. Грузоподъемность заливочного крана в цехах с 35-т конвертерами составляет 450/100/20 т. Сыпучие материалы доставляют в отделение немагнитных материалов в саморазгружающихся вагонах или автомобильным транспортом и разгружают в приемные бункера, затем на передвижные конвейеры, при помощи которых материалы передают в приемные бункера.
Современные системы подачи материалов в конвертеры достаточно сложны. В качестве примера приведена объединенная схема подачи сыпучих материалов и ферросплавов, спроектированная для конвертерного цеха металлургического комбината «Азов-сталь» (рис. 27.4).
Транспортировку сыпучих матери алов и твердых ферросплавов из соответствующего отделения в расходные бункера осуществляют по одному общему конвейерному тракту. Предусмотрены два параллельно расположенных конвейера 7 с автоматически сбрасывающими тележками 2. Конвейеры расположены над бункерами 3, в которые загружают все сыпучие материалы, в том числе и ферросплавы (Б1 — ферросилиций/ферромарганец, Б2 — феррохром/силикомарганец, БЗ — плавиковый шпат, Б4 — известняк, Б5— известь, Б6— агломерат, Б7— руда/кокс, Б8 — ферротитан/ферросилиций, Б9 — ферромарганец/коксик, Б9а — ферротитан/феррохром, Б10 — ферросилиций/силикомарганец). Под бункерами установлены электровибропитатели 4 (грохоты), предназначенные для отсева мелкой фракции извести (10—0 мм) и загрузки весовых дозаторов 5. Электровибропитатели, установленные под бункерами ферросплавов и других компонентов, рассчитаны на работу без отсева. Для увеличения точности дозирования весовые дозаторы выполнены с приемными воронками, в которые введены носки электровибропитателей. Места ввода носков защищены кожухами, а в кожухах воронок имеются воздухосборники с жалюзи и отсасывающими патрубками, которые соединены с системой очистки их бункерами-осадителями. У оснований весовых дозаторов 5 установлены трубчатые приемники 6 , под которыми расположен промежуточный бункер 7 с затвором. Под затвором находятся течки 8, опущенные в патрубки 9, которые, в свою очередь, соединены с газоотводящим трактом 10 конвертера 77. В системе тракта сыпучих материалов расположены весовые дозаторы 72 для ферросплавов и предусмотрена тележка 13 для передачи ферросплавов также и к электропечам. Под весовыми дозаторами установлены двухрукавные течки 14, а под ними — печи 75 для прокаливания ферросплавов. Между двухрукавными течками и печами расположены качающиеся течки 16, обеспечивающие загрузку ферросплавов либо в печи для прокаливания, либо прямо в воронки 77, в весовые дозаторы 18 и далее по течке 19 в ковш. При выдаче из печей прокаленные ферросплавы поступают в воронки 77 и аналогично ссыпаются в ковш.
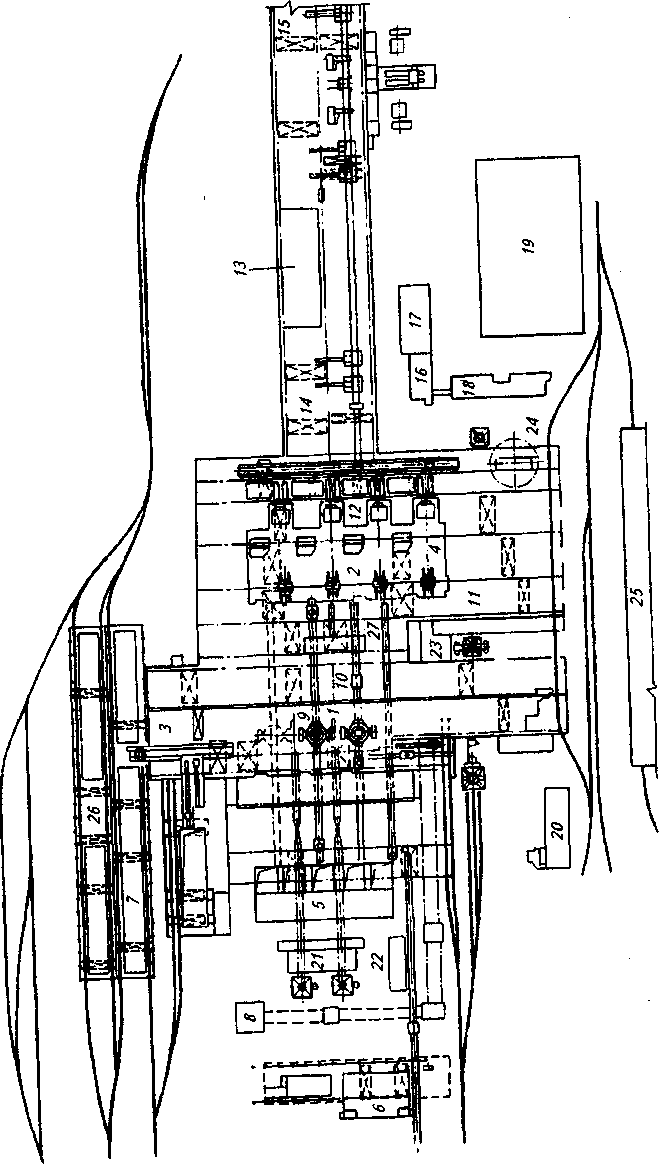

Рис. 27.2. Разрез конвертерного цеха череповецкого металлургического комбината ОАО
«Северсталь»:
а — конвертерное отделение; б— отделение непрерывной разливки; 1 — конвертер; 2— охладитель отходящих газов; 3 — бункера для сыпучих материалов; 4— мостовой заливочный кран; 5— заливочный кран; 6— самоходный шлаковоз; 7—мостовой кран; 8— экскаватор; 9—автосамосвал; 10— сталеразливочный ковш; 11 — консольный кран-оператор; 12 — самоходный сталевоз; 13 — установка стабилизации и доводки металла; 14— мостовой разливочный кран; 15— УНРС Жидкие ферросплавы получают в электропечах 20 и на специальной тележке 21 подают в ковше к желобу 22; по желобу ферросплавы сливают в сталеразливочный ковш 23. Тележкой 21 при помощи имеющегося на ней совка можно подавать в ковш различные добавки. Мелочь извести, отсеянная на электровибропитателях (грохотах), по трубчатым течкам поступает на виброконвейер и от него в специальный бункер 24 или при необходимости в сталеразливочный ковш. Установлен реверсивный конвейер 25 для транспортировки извести из-под бункерных весов системы одного конвертера в промежуточный бункер другого конвертера. Это позволяет сохранить и использовать известь в случае продолжительной остановки одного из конвертеров.
Для автоматического управления все механизмы для взвешивания, дозирования и загрузки сыпучих материалов в конвертер условно делят на три группы: к первой относятся механизмы, обеспечивающие транспортировку сыпучих материалов в бункера, ко второй— механизмы, обеспечивающие взвешивание и транспортировку сыпучих материалов из расходных бункеров в промежуточные, и к третьей — механизмы, обеспечивающие загрузку сыпучих материалов из промежуточных бункеров в конвертер.
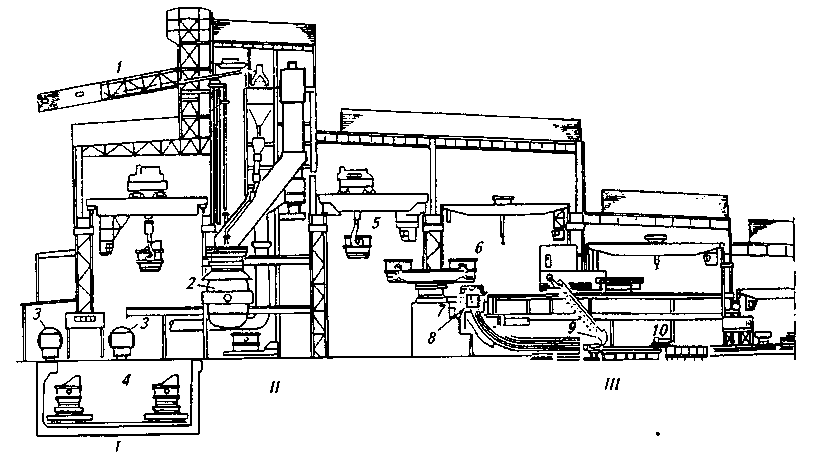 Рис. 27.3. Разрез здания конвертерного цеха (западноевропейский завод):
/—загрузочный пролет; II — конвертерный пролет; ///—отделение непрерывной разливки; / — конвейер для подачи флюсов; 2— 310-т конвертер; 3— передвижной миксер типа «Торпедо» емкостью 7600 т; 4— приямок для ковшей перелива чугуна; 5— ковш со сталью; 6— сталеразливочный ковш на УНРС; 7— поворотная турель УНРС; 8— УНРС; 9— подъемник; 10— резка заготовок
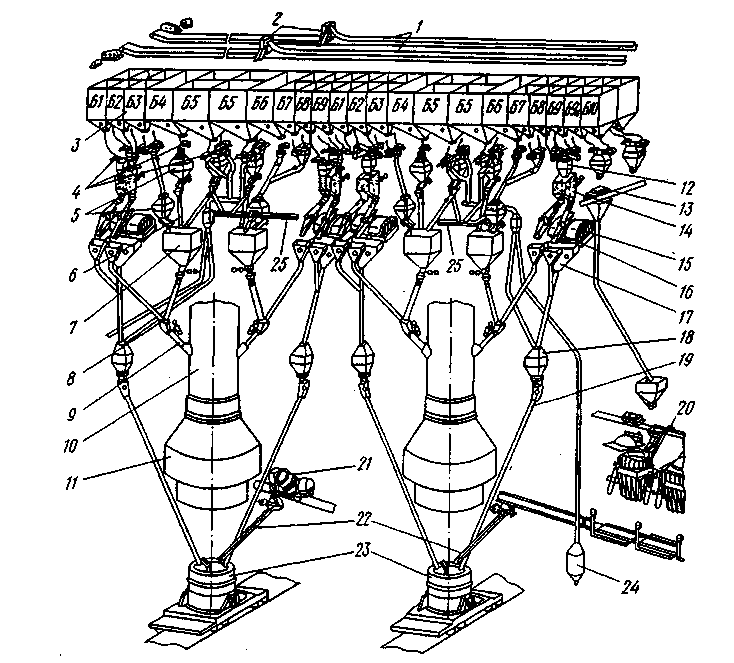
Рис. 27.4. Механизированная система подачи сыпучих материалов и ферросплавов в конвертерном цехе Система работает следующим образом. По сигналу датчиков уровня с конвейеров 7 тележки 2 загружают бункера 3. Затем включением электро-вибропитателей 4 (грохотов извести) загружают весовые дозаторы 5. Отсеянную мелкую известь подают в бункер 24. Из весовых дозаторов взвешенная порция поступает в промежуточный бункер 7 и от него по течке 8 и патрубкам 9 в конвертер. Тракт подачи ферросплавов работает аналогично: от двухрукавных течек 14 ферросплавы по качающимся течкам 16 поступают либо в печи 15 для прокаливания, либо прямо через воронки 17, весовые дозаторы 18 и по течке 19 в ковш.
По окончании плавки сталь из конвертера выпускают в сталеразливочный ковш, установленный на сталевозе (рис. 27.5). Сталевоз перевозит ковш со сталью в разливочное отделение, обычно примыкающее к конвертерному.
Поскольку современные конвертерные цехи имеют огромную производительность, организация цеховой работы представляет сложную проблему. Для беспрерывного действия цеха необходимо обеспечить ритмичную работу каждого участка; при этом выполнение каждой операции обеспечивается надежной работой сложного оборудования. В качестве примера рассмотрим операцию подготовки сталеразливочного ковша к плавке (рис. 27.6).
При нормальной работе двух конвертеров цех в сутки выдает более 60 плавок и ковш должен быть подготовлен к каждой плавке, причем каждые 2 ч должно быть готово пять-шесть ковшей. Не меньше организационных сложностей при выполнении операций ремонта ковшей, подготовки и подачи лома, доставки и заливки жидкого чугуна и т. д. Общее представление об этом дает схема на рис. 27.7.
|
|
|