Тема 1. Процесс термитной сварки. Тема Процесс термитной сварки
![]()
|
0,11%).Технология производства железоалюминиевого термита.Качество термитной шихты по экзотермическому эффекту и по составу термитного металла по основным легирующим элементам напрямую зависит от технологии изготовления термита. Экзотермический эффект (калорийность) термита колеблется в пределах 18—20% в зависимости от способа производства термитной шихты из-за колебаний в содержании легирующих компонентов. Ряд процессов (получение алюминиевого порошка распылением, магнитная сепарация окалины и т.п.), несмотря на их появление в 30-х годах, не утратили своего значения и до настоящего времени. Производство алюминиевого порошка. Для производства сварочных термитных смесей целесообразно использовать алюминиевый порошок с повышенным против содержанием активного алюминия. Для производства алюминиевых порошков используется алюминий, изготовляемый по ГОСТ 11070-2019. Он подвергается измельчению и в порошкообразном состоянии имеет следующий химический состав (табл. 1.10). Таблица 1.10 Химический состав алюминиевого порошка
![]() Рис. 1.11. Устройство для распыления жидкого алюминия: 1 — реторта; 2 — форсунка; 3 — штуцер; 4 — гранулы алюминия; 5 — трубка Самый эффективный способ получения порошка алюминия предложил М.А. Карасев в 1925 г. Сущность данного метода заключается в воздушной пульверизации жидкого алюминия. В настоящее время используется модернизированный метод пульверизации, который обеспечивает минимум потерь алюминия. Схема установки для производства порошка алюминия представлена на рис. 1.11. Данная установка состоит из реторты 1 вместимостью до 100 кг алюминия. Жидкий алюминий при температуре около 750 °С воздухом, подаваемым под давлением 0,5—1,0 атм., вытесняется по трубке 5 и фонтанирует через штуцер 3. Жидкий алюминий вытекает через отверстие штуцера диаметром 3,2—3,3 мм со скоростью 5,44—5,62 м/с. Вертикальная струя фонтанирующего алюминия распыляется направленным под прямым углом потоком сжатого воздуха. Сжатый воздух под давлением 5—6 атм. выбрасывается через 18 отверстий, расположенных в корпусе форсунки 2. Диаметр этих отверстий составляет 1,8 мм. В приемной камере распыленный сжатым воздухом порошок алюминия оседает и ссыпается в бункер. При штатном режиме работы установка с двумя ретортами может обеспечить получение в сутки до 3 т порошка алюминия. Две реторты, имеющие по боковым сторонам ребра жесткости, встроены в печь, где они прогреваются двумя газовыми горелками низкого давления, с подачей 20 куб. м газа в час через каждую горелку. ![]() Рис. 1.12. Установка для распыления падающей струи жидкого алюминия: 1 — гранулы алюминия; 2 — защитное пламя В промышленности применяются установки с раздельной плавкой алюминия и последующим распылением его из другой реторты. Упрощенным является способ, основанный на распылении сливаемой струи жидкого металла (рис. 1.12). В этой установке жидкий алюминий тонкой струей сливается из ковша на приемный лоток. При стекании металла с лотка он распыляется сжатым воздухом под давлением 5,2—6,0 атм. Алюминиевый порошок, полученный в рассматриваемом устройстве, имеет следующий гранулометрический состав: зерно более 3,0 мм..............................................................0,18% зерно болен 2,5 мм..............................................................0,15% зерно более 2,0 мм..............................................................0,21% зерно более 1,0мм...............................................................1,33% зерно более 0,6 мм..............................................................7,68% зерно более 0,5 мм..............................................................7,73% зерно более 0,4 мм.............................................................11,72% зерно более 0,25 мм...........................................................23,60% зерно более 0,20 мм...........................................................13,50% зерно более 0,10 мм...........................................................18,59% зерно более 0,09 мм.............................................................3,94% зерно менее 0,09 мм...........................................................10,71% Эта установка с емкостью ковша 0,6 т жидкого металла позволяет получать 0,5 т алюминиевого порошка в час. При использовании для получения порошка способа пульверизации порошок состоит из застывших гранул жидкого металла каплевидной формы. Каждая гранула покрыта тонким слоем оксида алюминия, который предотвращает ее от дальнейшего окисления. В алюминиевом порошке содержание оксида алюминия А12Оэ находится в пределах (табл. 1.11): алюминиевый порошок, получаемый методом распыления, имеет объемный вес в пределах 0,85—1,4 г/см3. Более крупные фракции порошка имеют меньший объемный вес. При распылении алюминиевый порошок насыщается железом и кремнием. При использовании для изготовления порошка алюминия с чистотой на уровне 99% содержание железа и кремния находится в пределах, указанных в табл. 1.12. Таблица 1.11 Содержание оксида в алюминиевом порошке
Таблица 1.12 Содержание железа и кремния в алюминиевом порошке
Технология обработки железной окалины. Железная окалина, применяемая для получения сварочного термита, должна быть очищена от органических примесей и различного рода включений, ухудшающих химический состав термитной стали. Кислородный баланс железной окалины должен находиться на уровне 30,06%, который соответствует состоянию, когда окалина полностью состоит из оксида железа Fe203. Окалина, получаемая с рельсопрокатных станов, имеет средний химический состав: Fe |
Измельчение сита по ГОСТ 2138-91 | 1 | 063 | -063 | Промышленная поставка окалины |
Процентное содержание фракции | 63,5 | 12,5 | 24,0 | 100 |
Содержание кислорода, % | 24,9 | 27,09 | 28,27 | 25,96 |
При смешении в требуемых количествах различных фракций окалины можно достичь стабильного кислородного баланса в ней, который подбирается с точностью до 0,05%. При этом условии обеспечивается постоянный экзотермический эффект горения в выпускаемых партиях термита.
В процессе обработки промышленной партии окалины она распределяется на технологических объектах в следующих долях:
крупный отход на грохоте........................................9%
вальцованная окалина.........................................27,8%
сеяная окалина (сито 063—016)...........................34,4%
отходы при магнитной сепарации.......................14,6%
пыль и прочие отходы..........................................14,2%
Итого:............100%
Окалина проходит обработку по технологическому процессу, который включает следующие технологические операции:
• просушка;
• просев через грохот;
• обжиг в окислительной атмосфере при 780—800 °С;
• охлаждение;
• просев по величине верхнего предела измельчения;
• магнитная сепарация;
• последовательный просев на трех ситах.
Операция просушки устраняет комковатость окалины из-за наличия влаги, что особенно актуально в осенне-зимний период. В зимний период может наблюдаться смерзание окалины при ее транспортировке, что существенно затрудняет последующую обработку. Операция просушки выполняется за счет газов, отходящих при обжиге.
Удаление крупных включений (металлических частиц, осколков кирпича и т.д.) производится путем пропускания окалины через грохот.
Обжиг окалины осуществляется во вращающейся нагревательной печи с размерами рабочего барабана: диаметр 1 м при длине 10 м. При обжиге организуется встречное направление потоков окалины и топочных газов.
Обжиг окалины производится в окислительной бессернистой рабочей атмосфере при температуре 780—800 °С. Окалина охлаждается после обжига путем воздушной аэрации.
Просев окалины ведется через сито 063 по ГОСТ 2138—91 по верхнему пределу измельчения. Сброс с сита считается отходом.
На магнитном сепараторе выполняется отделение от окалины кварцевого песка и других немагнитных примесей. Величина отхода немагнитной составляющей из окалины при сепарации приведена в табл. 1.14.
Таблица 1.14
Отход немагнитной составляющей при магнитной сепарации фракции окалины
Сито по ГОСТ 2138-91 | +1 | +063 | -063 |
Немагнитная часть | 1,54% | 3,28% | 7,30% |
Возможность регулировки окалины по кислородному балансу обеспечивается путем ее рассеивания на несколько различных фракций. Наиболее часто разбивку осуществляют на три фракции: первая фракция — 063. +04; вторая фракция — 04.+025; третья фракция — 025. +01.
Поскольку просев ведется через три сита, то на выходе получается окалина с измельчением. Первая фракция, проходящая через третье сито, идет в отход.
Подготовка стального наполнителя. К наполнителю термитной шихты, используемой для сварки стыков рельсового пути, предъявляются следующие требования по химическому составу: С — 0,08—0,50% (отклонения в одной партии ±0,1%); Мп — 0,3—0,8%; Si < 0,37%. Р < 0,04%; S< 0,04%.
Для характеристики степени измельчения наполнителя используется параметр максимального и минимального сечения частиц по их толщине. По этому параметру к наполнителю предъявляются следующие требования: максимальная толщина частиц не должна превышать 4,5—5 мм, а минимальная — быть менее 0,45—0,55 мм. Плотность металлического наполнителя составляет 1,90—2,50 г/см3- Технологический процесс переработки гвоздевой обсечки и стружки включает следующие основные операции: просев через грохот, промывание в горячем содовом растворе, промывку в горячей воде, обжиг, охлаждение.
Для устранения крупных включений в виде кирпичных осколков и крупных гвоздей стальной наполнитель подвергается просеву на грохоте. Стружка со станков механической обработки после дробления весьма однородна по своему составу и просеву может не подвергаться.
Предварительно до обжига для предотвращения резкого задымления металлический наполнитель подвергают промывке в 5%-ном водном растворе соды, при температуре последнего в 65—85 °С для удаления масел и других веществ органической природы. После промывки в растворе соды выполняют операцию душирования водой при температуре 65—85 °С для удаления включений щелочи и дисперсных частиц.
После промывки стальной наполнитель подвергается обжигу при температуре 600—650 °С в барабанной печи. При обжиге из металлических частиц происходит диссоциация кристаллизационной и адсорбированной влаги. Также наблюдается выгорание остатков органических включений.
Стальной наполнитель охлаждается после обжига путем воздушной аэрации при воздушном напоре потоков с учетом обеспечения процесса выветривания дисперсных частиц окалины, которые возникают при обжиге стального наполнителя в барабанной печи.
При обжиге стальных частиц количество образующейся окалины не превышает 0,5—1,5%. Учитывая, что масса вводимого наполнителя не превышает 15% от массы основных составляющих шихты, то влияние образующейся окалины на состав термита не существенно.
Количество окалины, образующееся в процессе обжига на поверхности стальных частиц, не превышает 0,5—1,5%. Поскольку металлический наполнитель вводится в среднем до 15% от веса основных составляющих шихты, влияние этой окалины на состав термита незначительно.
Обработка и подготовка ферросплавов и других легирующих элементов, вводимых в термитную шихту. Легирующие элементы могут вводиться в термитную шихту следующим образом: в чистом виде или в составе различных сплавов.
В термитную шихту они могут вводиться:
• через восстановитель в виде сплава с алюминием;
• окислитель (окалину);
• металлический наполнитель (в составе легированной стали);
• через ферросплавы.
• в химически чистом состоянии.
Наиболее используемым вариантом легирования является введение элементов через ферросплавы и в чистом виде.
Ферросплавы и другие легирующие добавки перед их введением в шихту подвергаются измельчению с доведением до требуемой грануляции, устранению кристаллизационной влаги.
Для измельчения ферросплавов используются щековые дробилки, которые обеспечивают финишную грануляцию легирующих частиц в пределе 1 —5 мм.
По завершении операции дробления выполняется просев, который обеспечивает получение ферросплавов в требуемых диапазонах измельчения.
Прокалкой ферросплавов при температуре 320—360 °С устраняется влага. Прокалка при более высокой температуре сопровождается окислением частиц ферросплава, что вызывает их более интенсивное участие в реакции горения термита.
Графит, служащий в качестве легирующего элемента, вводится в порошковом состоянии. Для удаления крупных частиц графит просеивается через сито 025. После просева графитовый порошок подвергается прокаливанию при температуре 300—310 °С.
Технологические процессы изготовления термитных порций. Термитные компоненты в соответствии с разработанным составом шихты проходят следующие технологические операции.
1. Взвешивание порошка алюминия на весах с точностью до
±0,1%.
2. Взвешивание порошка железной окалины, состоящего из нескольких фракций, которые отличаются по кислородному балансу и измельчению.
3. Каждая из фракций в соответствии с требованиями расчета по стабильности кислородного состава в окалине взвешивается с точностью до ±0,15%.
4. Взвешивание стального наполнителя с точностью до ±0,5%.
5. Затем компоненты поступают в смеситель, где в течение 30 с смешиваются четырехлопастным ротором. Из смесителя шихта ссыпается в бумажный пакет или хлопчатобумажные мешочки.
6. Взвешивание легирующих компонентов. Ферросплавы и порошок графита взвешиваются с точностью до ±0,1%. После взвешивания они упаковываются в бумажную тару.
7. Взвешивание огнеупорного порошка и упаковка запорного устройства. Огнеупорный порошок глинозема А1203 измельчается по верхнему пределу, определяемому ситом 016. В каждую порцию термита для запорного устройства добавляется порошок глинозема в количестве 35 + 1 г. Он расфасовывается в бумажный пакет. Туда же закладывают асбестовый кружок диаметром 24 х 3 мм.
Пакет с легирующими компонентами и запорным устройством упаковывается в бумагу, в которую закладывается запорный гвоздь (стержень диаметром 6 мм и длиной 120 мм, имеющий на одном конце шляпку диаметром 17 мм и толщиной 1,5 мм из стали 10). Затем все это упаковывают вместе с термитной шихтой в бумажный пакет или хлопчатобумажный мешочек.
При серийном производстве развеску компонентой шихты следует вести только на весовых дозаторах, так как объемные дают относительно высокие отклонения количества отмеряемой шихты.
На пакете с легирующими компонентами ставится штамп (обычно это делается до упаковки ферросплавов), на котором указываются завод-изготовитель, марка термита, номер партии, даты изготовления и предупреждение «Беречь от сырости!»
В зависимости от дальности транспортировки используются контейнеры или специальная тара, в которую складываются порции с термитом.
Порции сварочного термита. Применяемый для сварки стыков рельсов трамвайных путей сварочный термит имеет недостаточную калорийность, поэтому его берут две-три порции по 6—7,5 кг в зависимости от типа и профиля рельсов.
Использование сварочного термита с кислородным балансом окалины > 28,65% 02, алюминиевым порошком с химической чистотой выше 99% и с добавлением 10% стальной обсечки дает возможность употреблять для рельсов Р-50 (оптимальный стыковой зазор 12 мм, площадь сечения 65,8 кв. см) термит в количестве 4 кг основных компонентов, а для Р-43 (оптимальный стыковой зазор 12 мм, площадь сечения 57,0 кв. см) — 3,5 кг.
Для сварки рельсов S-49 (площадь сечения 62,97 см2) в Германии используется 3,5—4,0 кг термита. Для сварки рельсов трамвайного типа 180x180 мм хорошие результаты дает термит марки 5520 — 6,5 кг основных компонентов и 20% стальной обсечки (сварка с зазором 13 мм). Этой маркой термита сваривают рельсы Р-65 (площадь сечения 82,92 см2).
В Чехии для рельсов сечением 63,3 см2 использовали сварочный термит весом 5,5 кг. Постепенно вес основных компонентов был доведен до 4,5 кг.
Для сварки рельсов крупных сечений Р-65 в Чехии применяют сварочный термит марки 6520 (6,5 кг основных компонентов и 20% стальной обсечки).
Используя данные из практики количественного применения сварочного термита для сварки рельсов Р-65, Р-50 и Р-43 и основные показатели табл. 1.15, приводим диаграмму весового количества основных компонентов термита.
Таблица 1.15
Технические условия сварки рельсов с использованием термитных смесей
Тип рельсов | Площадь сечения, кв. мм | Максимальный стыковой зазор, равный толщине шейки рельса, мм | Стыковой объем V, куб. мм |
Р-38 | 40,063 | 13,0 | 63,8 |
Р-43 | 57,0 | 14,5 | 82,5 |
Р-50 | 65,8 | 15,5 | 102,0 |
Р-65 | 82,92 | 18,0 | 149,0 |
Т-55 | 70,47 | 12+2=14 | 98,5 |
Т-60 | 76,72 | 12+2=14 | 107,5 |
Т-65 | 82,55 | 12+2=14 | 115,5 |
S-49 | 62,97 | 14 | 88,0 |
На основании данных диаграммы (рис. 1.13) весовой состав термита (А1 + Ok) равен:
• для рельсов Р-38 — 2,7 кг;
• для рельсов Р-43 — 3,25 кг.
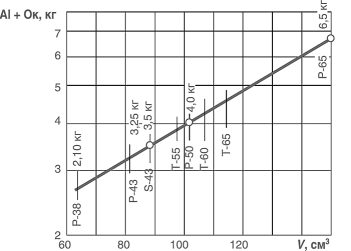
Рис. 1.13. Весовое содержание основных компонентов термита в порции
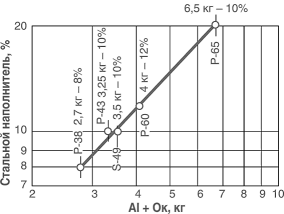
Рис. 1.14. Процентное содержание обсечки в термитной шихте
Принимая во внимание геометрическую сложность профиля рельсов для трамвайных путей, как правило, массовый состав шихты увеличивают в 1,5—1,6 раза. Поскольку для порции термита массой 6,5 кг содержание обсечки составляет 20%, а для порции массой 3,5 кг — 10%, то в логарифмической сетке для различных весовых значений процент обсечки будет следующим (рис. 1.14).
На основании диаграмм (рис. 1.13 и 1.14) весовой состав сварочного термита будет (табл. 1.16):
Таблица 1.16
Весовой состав сварочного термита
Тип рельсов | Состав порции термитной шихты | |||
основные компоненты (А1 + Ok), кг | стальной наполнитель | всего без легирующих компонентов, кг | ||
Р-38 | 2,70 | 0,216 кг | 8% | 2,916 |
Р-43 | 3,25 | 0,325 кг | 10% | 3,575 |
Р-50 | 4,00 | 0,480 кг | 12% | 4,480 |
Р-65 | 6,50 | 1,300 кг | 20% | 7,800 |
Т-55 | 6,00 | 0,900 кг | 15% | 6,900 |
Т-60 и Т-65 | 6,50 | 1.300 кг | 20% | 7,800 |
В ряде случаев применяют увеличенные порции сварочного термита для сварки стыков рельсов, которые собраны с завышенной величиной зазора. Масса основных компонентов в такой порции составляет 500 г.
В порцию вводят 10% стальной обсечки и требуемое количество легирующих компонентов, после чего осуществляют тщательное перемешивание всей шихты. Порции расфасовывают в бумажные пакеты и используют для увеличения количества термитной шихты при сварке.
Термит в обязательном порядке должен храниться в сухом проветриваемом помещении. Длительное хранение сверх гарантийного срока ведет к потере термитом оптимальной концентрации.
Сварочный термит взрывоопасен и может воспламениться от искры с температурой, превышающей 1350 °С. Поэтому электроосветительные устройства в складских помещениях и на предприятиях, использующих термит в технологических целях, должны быть взрывобезопасными.
Сварочный термит подлежит хранению в специальных отсеках (на деревянном настиле и стеллажах), вмещающих не более 10 упакованных порций. Под настилом выполняется бетонный приямок с хорошей гидроизоляцией, способный вместить до 10 т термитной шихты.
При соблюдении норм противопожарной безопасности термит безопасен при перевозке.
Не допускается тушение термита водой, так как в результате реакций между алюминием термита и кислородом воды может произойти взрыв большой разрушительной силы. При тушении термита необходимо рассыпать шихту тонким слоем или ввести в нее сухие инертные материалы (сухая земля, кирпич, песок, щебень, шлак) или металлический лом.