Глава 4. ТИТАН И ЦИРКОНИЙ. Титан и цирконий общие сведения
![]()
|
1 % от содержания ТiO2. После нагревания до кипения в осадок выпадает 95-96% ТiO2.96 %.400 кг/(м2 • ч) высота реакционной зоны, в пределах которой концентрация хлора изменяется примерно от начальной вблизи фурм практически до нуля (у верхней границы зоны), равна 0,8-1,0 м.85-90 % хлора или испаренный хлор из цистерн с жидким хлором.Рисунок 41 Шахтный хлоратор непрерывного действия: 1-водоохлаждаемый конус; 2 - фурма; 3 -хлорный коллектор; 4 - корпус хлоратора; 5 -волдохлаждаемый свод; 6 - бункер; 7 - золотниковый питатель; 8 - редуктор; 9 - электродвигатель; 10 - сборник огарка; 11 - разгрузочный шнек. В печах подобного типа можно хлорировать шлаки с низким суммарным содержанием СаО и МgО (не выше 4-5 %). При (более высоком содержании образующиеся жидкие хлориды CaCl2 и МgС12 приводят к слипанию брикетов и нарушению схода шихты вдоль шахты печи. Расход хлора составляет 0,85-0,9 т на 1 т тетрахлорида титана, что выше теоретического расхода ( |
При температурах 900-1000 °С хлорирование брикетов протекает во внешне диффузионной области, т.е. скорость процесса определяется скоростью подачи хлора. Энергия активации процесса хлорирования
Удельная производительность шахтных хлораторов непрерывного действия при температурах хлорирования 900-1000 °С равна 1,8-2 т ТiС14 на 1 м3 объема хлоратора.
Повышение единичной мощности шахтного хлоратора путем увеличения его диаметра нецелесообразно, так как возрастает неравномерность схода шихты (центральная часть брикета перемещается быстрей периферийной) и неоднородность температурного поля по его сечению (у стен температура выше вследствие неравномерности распределения хлора).
Отношение по массе СО:СО2 в парогазовой смеси, выходящей из хлоратора, колеблется (в зависимости от режима) от 5:1 до 2:1.

Рисунок 42 Хлоратор для хлорирования в солевом расплаве:
Недостаток хлорирования брикетированной шихты - высокие затраты на приготовление брикетов, что повышает 10-15 % себестоимость хлорида; взрывоопасность отходящих газов, в которых преобладает СО.
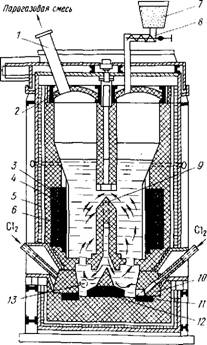
1 - газоход; 2 - свод; 3 -графитовый электрод; 4 -стальные трубы для отвода тепла; 5 - кожух хлоратора; 6 -шамотная футеровка; 7 - бункер с шихтой; 8 - шнековый питатель; 9 - перегородка для создания циркуляции расплава; 10 - фурма; 11,12 - донные графитовые электроды; 13 -нижний слив расплава
Хлорирование в солевом расплаве. Этот способ разработан в СНГ. Хлорирование шлака проводится в ванне из расплава хлоридов щелочных и щелочно-земельных металлов, куда подают компоненты шихты (измельченные шлак и кокс) и хлор. В качестве расплава используют отработанный электролит магниевых электролизеров, имеющий следующий примерный состав, %: КС1 72-76; NаС1 14-16, МgС12 4-6. Шихта подается шнеком на поверхность расплава, хлор поступает в нижнюю часть хлоратора через фурмы и газораспределительную решетку (рис. 42). При удельном расходе хлора 40-60 м3/ч на 1 м3 расплава обеспечивается хорошее перемешивание его барботирующим хлором. В расплаве поддерживают концентрацию ТiO2 2-3 %, углерода 7-9 %. При высоте расплава 3-3,2 м хлор успевает полностью прореагировать в объеме расплава, лишь незначительная часть его уходит с отходящимися газами.
Необходимая температура расплава (800 - 850 oС) поддерживается за счет тепла экзотермических реакций. Избыточное тепло отводится с помощью установленных в стенке хлоратора кессонов из графитовых плит, в которые вмонтированы стальные трубы, куда подается вода.
В процессе хлорирования в расплаве накапливаются нелетучие хлориды (MgCl2, СаС12, а также FeCl2 и FeCl3 в форме комплексов KFeCl3 и KFeCl4 и др.). Периодически часть расплава выпускают и в хлоратор заливают свежий расплав. Отработанный расплав содержит, %: KCl 30 - 40, NaCl 2 - 5, MgCl2 25 - 35, FeCl2 + FeCl3 + MnCl2 10 - 20, SiO2 3 - 6, CaCl2 2 - 4, С 7 - 9, TiO2 0,5 - 1. В отличие от хлорирования брикетированных шихт в хлораторах с расплавом в составе парогазовой смеси преобладает СO2 [объемное соотношение СO2: СО = (10÷20):1], что объясняется неблагоприятными условиями для взаимодействия СO2 с частицами углерода.
Механизм (стадии) хлорирования диоксида титана в сложной системе, содержащей газовую, жидкую и две твердые фазы (TiO2 и кокс), недостаточно изучен.
Очевидно, что с поверхностью частиц кокса и TiO2, находящихся в расплаве, могут вступать во взаимодействие только растворенные в расплаве хлор, СO2 и СО, так как при хорошем смачивании кокса расплавом его поверхность экранирована жидкой средой от непосредственного контакта с пузырьками газа.
Растворимость хлора, СО и СO2 в расплавах KCl - NaCl - MgCl2 при 800 - 900 oС равна примерно 0,04, 0,02 и 1,5 г/л соответственно. Растворимость TiO2 не превышает 0,05 г/л.
Согласно одной из предложенных схем растворенный хлор хемосорбируется на поверхности частиц углеродистого материала с образованием активного (атомарного) хлора, переносимого через расплав к поверхности оксида, где при участии растворенного СО протекает реакция:
ТiO2 + 4С1акт + 2СО = ТiС14 + 2СО2.
Далее СО2 частично взаимодействует с углеродом с образованием СО. Эта схема объясняет наблюдаемое повышение скорости хлорирования с увеличением удельной поверхности кокса и преобладание СО2 над СО в газовой фазе.
Присутствие хлоридов железа в расплаве повышает скорость хлорирования. Это объясняется хлорирующим действием FеС13, легко отщепляющего активный хлор. Как указано выше, хлориды железа находятся в расплаве в форме комплексов






Таким образом, хлориды железа выполняют роль переносчиков хлора.
Поскольку хлориды железа хорошо растворимы в расплаве, концентрация хлорирующего агента будет зависеть от содержания в нем железа. Так, достаточно содержания 1 % FeCl3 в расплаве для существенного увеличения скорости процесса. При нормальной работе хлоратора (без проскока хлора) в расплаве устанавливается отношение FeCl2 : FeCl3 = 20 + 200 (по массе), причем концентрация FeCl2 находится в пределах 15 - 20 %, a FeCl3 0,1 - 1,0 %.
Вследствие образования комплексов большая часть железа (а также алюминия, образующего комплекс КA1Cl4) остается в солевом расплаве.
Основные преимущества хлорирования в солевом расплаве по сравнению с хлорированием брикетов следующие: исключены сложные операции подготовки брикетов, что снижает себестоимость хлорида. Возможно хлорирование шлаков с повышенным содержанием СаО и МgО. Быстрый тепло- и массообмен в расплаве обеспечивает высокую скорость хлорирования и возможность отвода избыточного тепла. Преобладание СО2 над СО в составе газов резко снижает их взрывоопасность.
К недостаткам хлорирования в расплаве следует отнести периодический вывод отработанного расплава (до 200 кг на 1 т ТiС14), с которым теряется часть титана. Хлориды -вредные производственные сбросы. Важная задача - их использование или регенерация с возвратом в процесс.
Пылеулавливание и конденсация хлоридов
Парогазовая смесь, выходящая из хлораторов, имеет сложный состав. Она содержит газы (СО, СО2, СОС12, N2, НС1, С12), низкокипящие хлориды - в нормальных условиях жидкости (ТiС14, SiС14,VОС13 и др.); низкокипящие хлориды - в нормальных условиях твердые (FеС13, А1С13); высококипящие хлориды СаС12, МgС12, FеС12, а также КС1, NаС1 (при хлорировании в расплаве). Высококипящие хлориды механически увлекаются парогазовым потоком в виде тумана.
На рис. 43 приведена распространенная схема пылеулавливания и конденсации. Она состоит из пылевых камер (кулеров) для улавливания твердых хлоридов; рукавного фильтра с рукавами из стеклоткани для дополнительной очистки парогазовой смеси от твердых частиц; двух оросительных конденсаторов (конденсаторов смешения) для жидких хлоридов (ТiС14, SiС14), орошаемых охлажденным тетрахлоридом титана; во втором конденсаторе тетрахлорид, поступающий на орошение, охлаждается до -10 С. Далее газы проходят санитарный скруббер, орошаемый известковым молоком, для улавливания небольших количеств хлора, фосгена, хлористого водорода и выбрасываются в атмосферу. В кулерах газы охлаждаются с 500-600 до 140-180 °С омывающим трубы воздухом. В нижней разгрузочной части кулеров поддерживается постоянная температура (120-130 °С) органическим теплоносителем, циркулирующим в рубашке разгрузочного корыта. Термостатирование рукавного фильтра (140-160 °С) также осуществляется жидким теплоносителем.
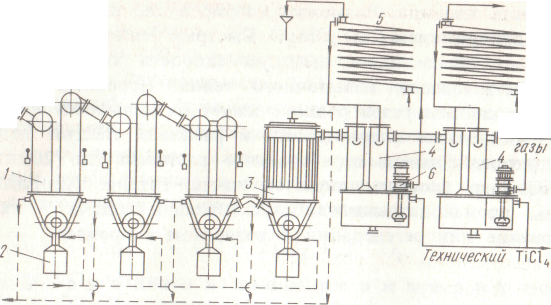
РBс.43. Схема раздельной конденсационной системы (пунктиром показан путь циркуляции теплоносителя):
1 - пылевые камеры (кулера); 2 — сборник твердых хлоридов; 5 - рукавный фильтр; 4 – оросительные конденсаторы; 5 - водяной холодильник; 6 - погружной насос; 7 - холодильник, охлаждаемый рассолом до -10 С (раствор СаС12)
Для снятия с рукавов из стеклоткани уловленной пыли производится их отдувка парами тетрахлорида титана.
В связи с осложненностью эксплуатации фильтров с рукавами из стеклоткани на некоторых предприятиях они заменены солевым расплавом NаС1 + КС1. (см. рис. 25). Расплав циркулирует с помощью аэролифтного устройства. Принцип работы солевого фильтра рассмотрен в гл. 2.
Извлечение титана из шлака в жидкий технический тетрахлорид составляет 92-93 %.
Очистка технического тетрахлорида титана
Содержание примесей в техническом ТiС14 колеблется примерно в следующих пределах, % (по массе): Si 0,01-0,3; А1 0,01-0,1; Fе 0,01-0,02; V 0,01-0,3; ТiOС12 0,04-0,5; СОС12 0,005-0,15; С1 0,003-0,08; S 0,01-0,08.
Кроме перечисленных, в хлориде титана часто содержатся примеси хлоридов ниобия, тантала, хрома и примеси органических соединений, например ацетилхлориды (СС13СОС1, СН2ClОСl), гексахлорбензол С6С16 и др.
Хлорид титана очищают от большинства примесей ректификацией, основанной на различии температур кипения хлоридов. Однако ректификации предшествует очистка от примеси ванадия.
Очистка от ванадия. Ванадия содержится в ТiС14 в составе оксихлорида VОС13. Отделение его от ТiС14 ректификацией затруднительно вследствие близости точек кипения ТiС14 и VОС13 (136 и 127 °С соответственно). Все известные методы очистки от ванадия основаны на восстановлении VОС13 до малорастворимого в тетрахлориде титана VОС12. На заводах в качестве восстановителей применяют медные или алюминиевые порошки.
Восстановление медным порошком протекает через стадию
образования СuТlС14:
Сu + ТiС14 = СuТiС14; (4.15)
СuТiС14 + VОС13 = VОС12 + CuС1 + ТiС14. (4.16)
Получаемые медно-ванадиевые осадки содержат, % Тi 6-8; V 4-6; С1
Производство диоксида титана
Сернокислотный способ
Основное количество выпускаемого диоксида титана из ильменитового концентрата (или титановых шлаков) получают сернокислотным способом, который включает следующие стадии:
разложение концентрата серной кислотой;
очистку растворов от железа;
гидролитическое выделение метатитановой кислоты из сернокислотного раствора;
прокаливание осадка с получением диоксида титана.
Этот способ обеспечивает высокое извлечение титана в готовый продукт, причем в технологии практически используют один реагент - серную кислоту.
Разложение концентрата. Разложение ведут концентрированной Н2SО4 (92-94 %) или олеумом в стальных реакторах. Вследствие экзотермичности процесса после нагревания кислоты с измельченным концентратом до 125-135°С реакция проходит интенсивно с саморазогревом до 180-200°С и заканчивается за 5-10 мин. Получающаяся полусухая масса ("плав") содержит оксосульфат титана (IV) (ТiOSО4 • Н2О), FеSО4) избыточную Н2SО4. Плав выщелачивают водой.
Очистка растворов от железа.
Растворы содержат 110-120 г/л ТiO2 (в составе ТiOSО4),
сульфаты железа SеSО4 и Fе2(SО4)3 и 200-240 г/л активной Н2S04.
Для очистки от основной массы железа восстанавливают Fе3+ до Fе2+ железной стружкой, а затем проводят кристаллизацию железного купороса FеSО4-7 Н2О, охлаждая растворы до -5 °С. В результате кристаллизации содержание железа растворе понижается до