|
Теория и технология производства стали 1. Учебник для вузов. М. Мир, ООО Издательство act
3.2. МАРКИРОВКА СТАЛЕЙ ЗА РУБЕЖОМ 3.2.1. Маркировка сталей в США. Обозначение государственного стандарта — ASA (American Standards Association). Ведущие организации по стандартизации: ASTM (American Society for Testing and Materials); AISI (American Iron and Steel Institute). По ASA стали маркируют цифрами, добавляя в некоторых случаях прописную букву. По ASTM конструкционные стали, за исключением коррози-онностойких и жаростойких, обозначают четырехзначным числом, в котором две последние цифры — среднее содержание углерода в сотых долях процента.
Марки коррозионностойких и жаростойких сталей обозначают трехзначным числом, из которых первая цифра имеет следующее значение:
2 — хроммарганецникелевые стали с азотом;
3 — хромникелевые стали;
4 — хромистые стали;
5 — хроммолибденовые стали;
6 — хромникельмолибденовые стали и хроммолибденовые стали с содержанием других элементов.
Пример: сталь марки 302 — хромни-келевая сталь, содержащая 17—19 % Сг и 8-10% Ni.
3.2.2. Маркировка сталей в Германии. Обозначение государственного стандарта — DIN (Deutsche Industrie-norm). Организация по стандартизации — DNA (Deutsche Normenaus-shuss).
Стали маркируют двумя способами: с помощью цифр, которыми обозначают номер материала, и с помощью комбинации букв и цифр, которая обозначает марку стали.
Маркировка с помощью букв и цифр (марка стали) — при этом способе маркировки стали подразделяют на группы в зависимости от степени легирования и вида термической обработки:
Группа 1. Маркировка углеродистых неулучшаемых сталей. На первом месте в марке стали ставится заглавная буква (по способу разливки стали: U — кипящая сталь, R — спокойная или полуспокойная, RR —сталь, успокоенная по специальной технологии), на втором месте ставятся буквы St (от слова «сталь»), на третьем месте — двузначное число, указывающее минимальный предел прочности (кгс/мм2), на четвертом месте — номер группы качества. По содержанию фосфора, серы, а иногда и углерода стали разделяются на три группы, обозначаемые цифрами 1, 2, 3, из которых 3-я группа имеет самое низкое содержание фосфора, серы, а также углерода. Номер группы качества отделяется от показателя минимального предела прочности дефисом. Приведенные четырех-компонентные обозначения составляют основу марки, которая может быть дополнена перед первым обозначением буквами: Е (указание на то, что сталь выплавлена в электропечах), М (сталь выплавлена в мартеновских печах), Y (при выплавке стали применена продувка кислородом).
Пример: сталь марки RSt42-2 — углеродистая неулучшаемая сталь с минимальным пределом прочности 42 кгс/мм2 2-й группы качества. Сталь MRSt42-2N — та же сталь, мартеновская, после нормализации.
Группа 2. Маркировка углеродистых качественных сталей. Сначала в марке приводится буква С, а затем двузначное число, указывающее среднее содержание углерода, умноженное на 100.
Пример: сталь С35 — углеродистая качественная сталь со средним содержанием углерода 0,35 %.
3.2.3. Маркировка сталей в Японии. Обозначение государственного стандарта — JIS (Japanese Industrial Standards). Организация по стандартизации — JISC (Japanese Industrial Standards Committee).
Марки конструкционных сталей в Японии состоят из нескольких прописных букв и однозначного или двузначного числа. В зависимости от характеристик стали делятся на группы, причем каждую группу обозначают несколькими заглавными буквами.
Примеры обозначения сталей обычных групп:
1) стали марок SSxx—углеродистые рядовые стали, где хх — двузначное число, указывающее минимальный предел прочности (кгс/мм2), например SS34;
2) стали марок SxxC — углеродистая сталь гарантированного химического состава (хх — двузначное число, указывающее среднее содержание углерода в сотых долях процента; например, в стали S20C среднее содержание углерода составляет 0,20 %);
3) стали марок SUMx— автоматная сталь (х— однозначное число, указывающее на порядковый номер стали в группе);
4) стали марок SFxx —углеродистая сталь для поковок и т. д. в зависимости от назначения (хх — двузначное число, выражающее минимальный предел прочности, кгс/мм2; например, сталь марки SF42). 4. ОСНОВНЫЕ ШИХТОВЫЕ МАТЕРИАЛЫ 4.1. МЕТАЛЛОШИХТА Производство стали связано с использованием значительных количеств различных материалов и в первую очередь металлошихты (включает чугун, металлолом, различные металлодобавки), а также добавочных материалов или флюсов (известь, известняк, боксит, плавиковый шпат и др.), окислителей (воздух, кислород, железная руда, окалина и др.), топлива (природный газ, мазут, коксовый газ, доменный или колошниковый газ), электроэнергии, воды, инертных газов (аргон), огнеупорных материалов, электродов и др. Расход каждого из этих материалов наряду с затратами на электроэнергию влияет на себестоимость стали.
Более чем на 80 % себестоимость стали определяется стоимостью используемого сырья, прежде всего расходом и стоимостью металлошихты.
В качестве металлошихты используют: а) чугун (жидкий или твердый); б) металлолом (в технической литературе часто используют термин «скрап»');
в) металл одобавки, например продукты прямого восстановления железа и др.
Расход металлошихты, составляющий 1100—1150 кг/т жидкой стали, определяется: 1) составом шихты (доля чугуна, доля скрапа в шихте и т. п.); 2) характером шихты и химическим составом ее составляющих (степень «зашлакованности» чугуна, концентрация в нем легкоокисляющихся примесей, «замусоренность» скрапа и т. п.); 3) технологией плавки (будет применяться кислород для продувки ванны или нет, большое или умеренное количество образующегося шлака и т. п.). Расход металлошихты снижают при использовании в качестве окислителей железной руды, окалины или других материалов, в состав которых входит железо (оно частично восстанавливается и переходит в металл).
Выход жидкой стали (по отношению к массе металлошихты) существенно возрастает в тех случаях, когда в ванну вводится большая масса легирующих элементов (обычно в виде ферросплавов, т. е. сплавов с железом). 1 От англ, scrap— остатки (отходы металлургических производств), металлический лом.
4.2. ЧУГУН Напомним, что чугун получают в доменных печах восстановлением железа из железорудных материалов (агломерата, окатышей и др.). При горении кокса идут реакции С + О2 + 3,762N2 = С02 + 3,762N2,
С + СО2 + 3,762N2 = 2CO + 3,762N2. При частичном обогащении воздуха кислородом коэффициент 3,762 соответственно уменьшается (это соотношение долей азота и кислорода в воздухе: 79/21 = 3,762).
В области высоких температур при наличии углерода идет реакция С02 + С = 2СО. Образующийся оксид СО — восстановитель, и атмосфера в доменной печи восстановительная. В зоне высоких температур идет прямая реакция восстановления железа углеродом кокса: FeO + С = Fe + СО - Q. Степень восстановления железа в доменной печи 99—99,9 %, поэтому доменный шлак содержит < 1 % FeO. В восстановительных условиях печи восстанавливаются и другие оксиды, поступающие в доменную печь с шихтой (оксиды кремния, марганца, фосфора и др.): SiO2 + 2С = [Si] + 2CO - Q,
МпО + С = [Мп] + СО - Q,
ЗСаО • Р2О5 + 5С = 2[Р] + ЗСаО + SCO - Q. Используемый в доменной печи кокс содержит некоторое количество серы. Сера содержится и в железорудных материалах (в виде FeS, CaS, CaSO3). Около 10 % содержащейся в шихте серы удаляется из печи вместе с газами. .
Оставшаяся сера распределяется между металлом (чугуном) и шлаком в соответствии с коэффициентом распределения LS = (S)/[S], величина которого в значительной мере зависит от основности шлака:
[S] + Реш+ (СаО) = (CaS) + (FeO).
При наличии в доменной шихте оксидов марганца возможна реакция
(МпО) + [S] + С = (MnS) + CO.
Из предыдущей формулы видно, что в доменной печи благоприятные условия для удаления серы в шлак, так как благодаря восстановительной атмосфере содержание FeO в шлаке минимально. При этом важно по возможности повысить а(СаО) т.е. работать со шлаками высокой основности. В то же время при повышении основности растет вязкость шлака, т. е. соответственно требуется увеличить расход кокса для поддержания более высокой температуры и расход известняка. При этом снижается производительность печи, так как часть объема печи занята дополнительными количествами кокса, известняка и шлака. Практически величина LS колеблется в пределах 30—70, а содержание серы в чугуне составляет 0,015— 0,050 %. При работе на сернистом коксе (например, из углей Донбасса) содержание серы выше.
Таким образом, выплавляемый в доменных печах чугун содержит некоторое количество серы, фосфора (практически весь фосфор, содержащийся в доменной шихте, восстанавливается и переходит в чугун), кремния, марганца. Кроме того, в процессе контакта капель жидкого чугуна, стекающих в горн печи через слой раскаленного кокса, происходит науглероживание металла. Содержание углерода в чугуне во многом определяется наличием в чугуне тех или иных примесей. Мп, Сг, V образуют карбиды, способствуя увеличению содержания углерода в чугуне. Si, P, Си способствуют снижению содержания углерода. Поэтому в ферромарганце и в высокомарганцовистом чугуне содержание углерода выше, чем в обычном передельном (до 7 %), а в литейных чугунах с повышенными концентрациями кремния содержание углерода ниже (3,5-4,5 %).
Одна из эмпирических формул для расчета содержания углерода в чугуне: %С = 4,8 + 0,03 %Мп - 0,27 %Si -- 0,32 %Р-0,03 %S.
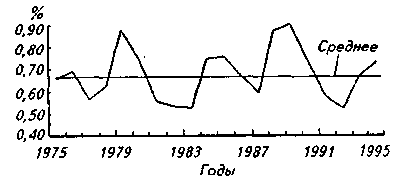
Рис. 4.1. Отношение цены скрапа к стоимости чугуна в Германии 1975-1995 гг. Обычно передельный (используемый для передела чугуна в сталь) чугун имеет состав, мас.%: С 4,4—4,6; Si 0,2-0,8; Мп 0,2-0,6; Р < 0,3; S < 0,05.
Таким образом, в чугуне 94 % Fe и 6 % различных примесей. В процессе передела чугуна в сталь в окислительных условиях основная масса примесей окисляется. Кроме того, при использовании кислорода для продувки сталеплавильной ванны часть железа (1—2%) испаряется, окисляется и в виде пылегазовых выбросов покидает агрегат. Масса шлака в момент окончания плавки стали составляет 10— 20 % от массы металла. Шлак содержит 20—25 % оксидов железа, или 1,5— 2,5 % Fe от массы металла. Этот расчет показывает, что при плавке стали из шихты, состоящей на 100 % из жидкого чугуна, около 10 % ее массы переходит в шлак и в газовую фазу и расход металлошихты на 1 т жидкой стали превышает 1100 кг.
Мировая цена 1 т жидкого чугуна 140—160 долл. США, цена металлолома ниже, она меняется в зависимости от конъюнктуры рынка (рис. 4.1). Этим объясняется стремление металлургов гибко реагировать на колебание цен и максимально использовать в шихте металлолом.
4.3. МИКСЕРЫ Практически на всех заводах, в составе которых имеются доменные печи, смонтированы специальные разливочные машины для получения из жидкого чугуна так называемых «чушек». Полученные чушки твердого чугуна направляют для использования на заводы, не имеющие доменных печей. Однако основная масса выплавляемого чугуна поступает в сталеплавильные цехи в жидком виде — использование в качестве шихты жидкого чугуна экономически более выгодно, так как при этом снижаются затраты энергии и сокращается продолжительность плавки. Состав и температуру чугуна нескольких плавок (выпусков из доменной печи) необходимо выравнять. Для этой цели служат специальные агрегаты—миксеры1. Использование миксера позволяет иметь некоторый запас чугуна, что гарантирует ритмичную работу сталеплавильного цеха. Если доменный цех не обеспечивает выпуск чугуна строго определенного состава и температуры и сталеплавильному цеху необходимо все время иметь определенный запас жидкого чугуна, строят специальное миксерное отделение, в котором устанавливают один или два стационарных миксера. Вместимость типовых стационарных миксеров составляет 1300 и 2500 т. 1 От англ, mixer— смеситель.
В миксер с одной стороны заливают чугун, поступающий в чугуновозных ковшах из доменного цеха, а сдругой (противоположной) стороны по мере необходимости чугун из него сливают в ковши для подачи к сталеплавильным агрегатам. Миксерное отделение связано эстакадой с рабочей площадкой сталеплавильного цеха. По эстакаде составы с чугуно-возными ковшами транспортируются непосредственно к печам или конвертерам. Миксеры, в которых проводят какие-либо технологические операции (например, удаление кремния), называют активными (в отличие от обычных, которые можно назвать неактивными).
На рис. 4.2 приведены план и разрез миксерного отделения с двумя миксерами вместимостью по 2500т, входящего в состав цеха с 350-т конвертерами. В миксерном отделении установлены два миксера 5 и 10, два миксерных (заливочных) крана 7 и 11, машины 75 для скачивания шлака из миксеров, машина 8 для скачивания шлака из чугуновозных ковшей, установки 16 для улавливания графита, весы 2 для взвешивания жидкого чугуна, стенды 7 для шлаковых ковшей и
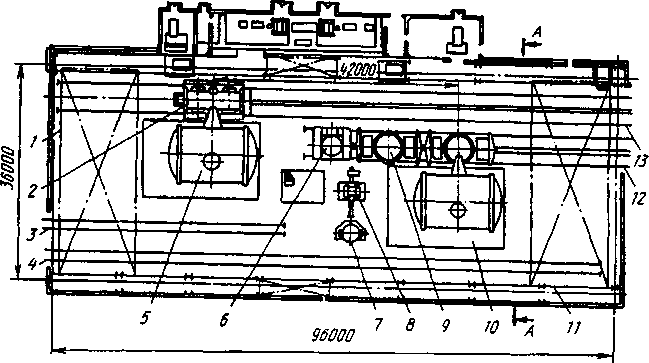
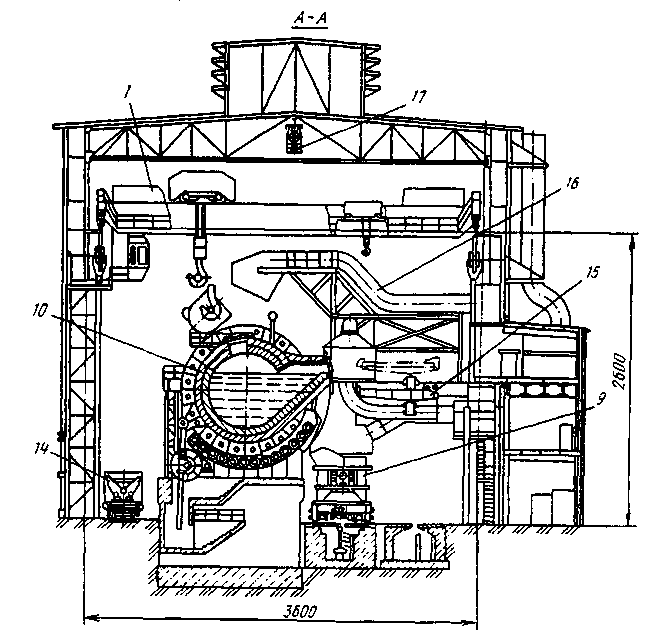
Рис. 4.2. План и разрез миксерного отделения тельфер 17 для проведения ремонтных работ. Железнодорожные пути 3 и 4 служат для подачи чугуновозов 14, прибывающих из доменного цеха. Рельсовые пути 12 и 13 широкой колеи предназначены для передвижения самоходных чугуновозов 9, доставляющих чугун к конвертерам.
На поверхности жидкого чугуна в миксерах всегда имеется слой шлака, называемого миксерным шлаком, состав которого может меняться в очень широких пределах, %: SiO2 35—55; CaO 20-35; MgO 3-15; A12O3 4-8; MnO 2—10; S до 2. Содержащиеся в миксерном шлаке сера, а также кремнезем являются нежелательными компонентами. Теоретически этот шлак не должен попадать в сталеплавильный агрегат, так как обычно он почти не содержит железа и в нем существенное количество SiO2 и серы. Кроме того, этот шлак, по существу, является балластом.
Рис. 4.3 иллюстрирует трудность обеспечения десульфурации стали в конвертере при попадании в конвертер значительных количеств доменного шлака. Существующие сегодня устройства часто не обеспечивают полного скачивания шлака перед заливкой жидкого чугуна в сталеплавильный агрегат, и это обстоятельство необходимо принимать во внимание при проведении различных расчетов. Обычно шлак скачивают из чугуновозных ковшей и перед заливкой чугуна в миксер, и из миксера по мере накопления в нем шлака. Шлак из миксера скачивают машиной 15 (см. рис. 4.2) в ковш шлаковоза 6, убираемого самоходным чугуновозом. Скачивание шлака из чугуновозных ковшей осуществляют машиной 8 в шлаковый ковш, установленный на стенде 7.
Количество шлака в миксере можно уменьшить, если перед заливкой чугуна в миксер удалить шлак с поверхности чугуна в чугуновозных ковшах. Содержащийся в миксерном шлаке кремнезем воздействует на футеровку миксера, снижая ее стойкость. Обычно футеровку миксера выполняют из магнезитового кирпича, а для свода используют шамотный кирпич. Стойкость футеровки миксера составляет около одного года. При систематическом торкретировании ее можно продлить до пяти лет.
Форма миксера определяется условиями минимальной теплоотдачи и рационального размещения заливочного и выпускного отверстий. Наиболее часто встречающийся тип конструкции миксера — цилиндр с отношением длины к диаметру -1,3.
Для уменьшения потерь тепла используют слой теплоизоляционного материала между металлическим кожухом и футеровкой; в торцовых стенках миксера устанавливают горелки для
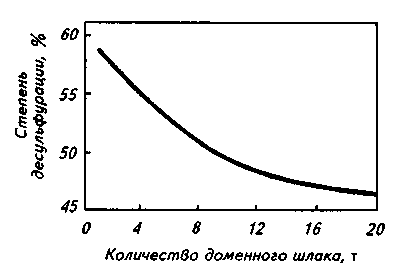
Рис. 4.3. Зависимость степени десульфурации в конвертере (300-т конвертеры НЛМК) от количества доменного шлака, попавшего в конвертер с жидким чугуном его отопления. Расход топлива на горелки невелик, и продукты сгорания выходят прямо в миксерное отделение. Несмотря на большой слой футеровки (-700 мм) и подачу топлива для отопления миксера, чугун в миксере несколько охлаждается. Особенно велики потери тепла во время переливов чугуна из ковшей в миксер и из миксера в ковш.
К достоинствам стационарных миксеров относятся: возможность запаса чугуна, необходимого для ритмичной работы цеха, хорошее перемешивание и усреднение состава чугуна и его температуры. Однако в условиях современных высокопроизводительных цехов проявились и основные недостатки стационарных миксеров: 1) необходимость существенных затрат на строительство миксерного отделения и соответствующего оборудования; 2) потери тепла чугуна при переливах; 3) недостаточное усреднение состава и температуры чугуна. Принято считать, что удовлетворительное усреднение состава и температуры чугуна в миксере имеет место в том случае, если продолжительность пребывания чугуна в миксере составляет -8 ч (т. е. если чугун в миксере обновляется полностью не более трех раз в сутки).
Современный конвертерный цех потребляет в сутки 12—20 тыс. т чугуна, в то время как даже миксер вместимостью 2500 т может в сутки усреднить не более 2500 • 3 = 7,5 тыс. т чугуна. По мере совершенствования работы современных мощных доменных печей объемом 4000—5000 м3 улучшается обеспечение снабжения сталеплавильного цеха чугуном постоянных состава и температуры. При четкой и равномерной работе доменных печей, а также при постоянстве состава и температуры чугуна вместо стационарных миксеров используют чугуно-возные ковши миксерного типа, называемые передвижными миксерами (рис. 4.4). К преимуществам передвижных миксеров по сравнению со стационарными относятся: 1) снижение капитальных затрат при строительстве и уменьшение сроков строительства; 2) уменьшение потерь тепла чугуна на 25-30 ºС вследствие исключения одного перелива (это позволяет увеличить долю лома в металлозавалке примерно на 2 %); 3) возможность приема всей плавки доменной печи в один ковш-миксер, что позволяет упростить организацию работ в доменном цехе; 4) улучшение условий для организации внедоменной обработки чугуна.
Основным недостатком передвижных миксеров является невозможность усреднения состава и температуры чугуна различных плавок. В нашей стране для новых сталеплавильных цехов изготавливают ковши миксерного типа вместимостью 600 т. Такая грузоподъемность обусловлена, с одной стороны, возможностью приема всей плавки доменной печи объемом 5000-5500 м3, с другой — возможностью обеспечить чугуном сразу две плавки в цехе с конвертерами вместимостью 300— 350 т. Передвижной 600-т миксер является довольно массивным сооружением — его масса (включая футеровку и оборудование) более 1,2 тыс. т; габаритные размеры, м: длина 39,56, ширина 3,5, высота от уровня головки рельсов 4,7 (рис. 4.4). Эксплуатация передвижных миксеров такой грузоподъемности предусмотрена лишь на внутризаводских железнодорожных путях (стандартной колеи). При перевозке чугуна на большие расстояния и из города в город обычно используют передвижные миксеры меньшей грузоподъемности.
В тех случаях, когда сталеплавильный цех входит в состав завода, не имеющего доменного цеха, в качестве шихты в сталеплавильных агрегатах используют твердый чугун, который привозят на завод в чушках. В некоторых (редких) случаях для ускорения плавки и повышения производительности сталеплавильных агрегатов чушковый чугун предварительно расплавляют в специальных агрегатах (обычно шахтного типа).
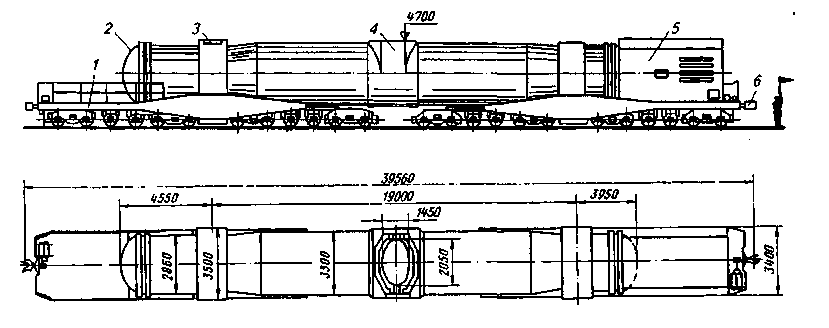
|
|
|