|
Теория и технология производства стали 1. Учебник для вузов. М. Мир, ООО Издательство act
Рис. 5.3. Диаграмма состояния 8Ю2-А12Оз
Кремнеземистые огнеупорные материалы, изготавливаемые из кварцитов2 и состоящие в основном из кремнезема (>93 % SiO2), в сталеплавильном производстве используют для изготовления сводов печей. До недавнего времени динасовый кирпич являлся основным материалом для изготовления сводов печей. Однако большое количество плавильной пыли и высокие температуры, характерные для работы печей в условиях интенсификации процесса кислородом, вынудили почти повсеместно отказаться от динаса (плавильная пыль, состоящая главным образом из оксидов железа, активно взаимодействовала с кислой футеровкой динасового свода, приводя к быстрому выходу его из строя). В настоящее время почти все печи оборудованы сводами из основного маг-незитохромитового кирпича. Магнезитохромитовые изделия, изготавливаемые из смеси магнезитового порошка (65-80 %) и молотого хромита (20—35 %), получили широкое распространение благодаря достаточно высоким температуре начала деформации под нагрузкой (>1600°С), термостойкости (>10 тешюсмен), а также высокой стойкости против воздействия основных шлаков и плавильной пыли. В результате высокотемпературного обжига тонкоизмельченных чистых магнезита MgO и хромита СгО3 получают изделия с прямыми связями, образовавшимися при обжиге периклаза4 и шпинелидов. Такие изделия, характеризующиеся высокой стойкостью, называют перикла-зошпинелидными. Материалы на основе MgO и СгО3 получили широкое распространение в сталеплавильном производстве для изготовления сводов мартеновских и двухванных печей, футеровки конвертеров и др. Для изготовления насадок регенераторов мартеновских печей широко применяют форстерит4, характеризующийся слабым взаимодействием с плавильной пылью при <1400º С.
1 Обычо под словом шамот понимается обожженная огнеупорная глина Chamotte (франц.).
2Эти материалы называют динасовыми, что связано с названием скалы Динас («Craig-y-Dinas») в Уэльсе (Великобритания).
3 Периклаз — природный минерал (оксид магния MgO, иногда с примесью FeO, MnO и др.).
4 Форстерит (по имени немецкого ученого И. Форстера) — минерал, магниевый оливин состава Mg2[SiO4]. Чистый магнезит (<10 % примесей, остальное MgO) используют в виде порошка для изготовления и ремонта подин электропечей, мартеновских и двухванных печей, а также для изготовления магнезитовых кирпичей. Магнезитовые огнеупоры характеризуются высокой огнеупорностью и хорошей устойчивостью против основных шлаков, однако имеют низкую термостойкость. Из магнезита обычно изготавливают стенки рабочего пространства печей. В тех случаях, когда от магнезитовых огнеупоров требуются особо высокие свойства, магнезитовый порошок предварительно плавят в дуговых печах, получая плавленый периклаз, который после измельчения используют в качестве сырья для изготовления высокостойких огнеупорных материалов.
В конвертерном производстве широкое распространение получили также доломитовые огнеупоры, изготавливаемые из обожженного до спекания дробленого доломита1 на смоляной связке. В зависимости от состава и технологии изготовления доломитовые материалы имеют огнеупорность 1800—2000 °С и характеризуются высокой стойкостью против воздействия жидких основных шлаков. Дробленый доломит широко используют также для проведения ежеплавочных ремонтов подин мартеновских и двухванных печей.
Достаточно широкое распространение получили огнеупоры, изготавливаемые из порошка магнезита с добавлением хромистой руды. Изделия (кирпичи) прессуют под высоким давлением и подвергают температурному отжигу при 1600—1650 °С. В металлургической практике приняты следующие обозначения высокоогнеупорных магнезитохромитовых изделий: ПШСП —периклазошпинелидные магнезитохромитовые плотные с тонкомолотой хромовой рудой в шихте; МХСП —магнезитохромитовые плотные с крупнозернистым хромитом в шихте; ПШСО — периклазошпинелидные магнезитохромитовые обычные с тонкомолотой хромовой рудой в шихте; МХСО — магнезитохромитовые обычные с крупнозернистой хромовой рудой в шихте. Основной составляющей этих изделий является MgO в виде периклаза.
Сталеплавильное производство потребляет также некоторое количество относительно дорогих, но обладающих особыми свойствами огнеупорных материалов на основе циркона ZrO2, карборунда SiC, глинозема (корунда)2, карбидов циркония, нитрита бора и др. Их используют в тех случаях, когда требуется особая стойкость (например, при изготовлении сталеразливочных стаканов, труб для транспортировки жидкого металла, при обработке вакуумом и др.).
Особо высокие требования предъявляются к качеству огнеупоров, используемых для внепечной обработки стали (например, типа ковш-печь). Российские заводы БКО (Боровичский комбинат огнеупоров) и «Магнезит» освоили производство огнеупоров на базе MgO-C. Их обозначения: ПУСК (периклазоуглеродистый спеченный клинкер), ПУПК (периклазоуглеродистый плавленый клинкер). Такие огнеупоры могут выдерживать длительный контакт с металлом и шлаком при высоких температурах.
Для производства огнеупорной футеровки в конце 70-х годов минувшего века химическая промышленность разработала ряд добавок — материалов, называемых тиксотропными3. Использование тиксотропных добавок позволяет широко применять метод вибролитья. Вибролитье тиксотропных бетонов получило широкое распространение на металлургических предприятиях. Одно из названий процесса, используемое обычно в зарубежной литературе, CL-L (Cast Lining Process of Ladie). В качестве огнепорного наполнителя используют высокоглиноземистый шамот, циркон ZrO2, магнезиальный клинкер, периклазохромит, электрокорунд и др.
Установка для вибролитья состоит обычно из смесителя, ленточного конвейера, устройства для заливки массы, шаблона и вибраторов.
1 Доломит (по имени французского геолога Д. Доломье) имеет состав CaMg [CO3h-
2 Корунд — минерал, природный безводный глинозем А12О3; корундовые огнеупорные изделия содержат >90 % А12О3.
3 От греч. thixis — прикосновение и trope — поворот, изменение. Тиксотропия проявляется в разжижении при интенсивном встряхивании или перемешивании гелей, паст, суспензий и других систем с коагуляционной дисперсной структурой и их загущении (затвердевании) после прекращения механического воздействия. Тиксотропными свойствами обладают, например, плывуны.
Продолжительность затвердевания несколько часов летом и до 8 ч зимой (для ускорения применяют подогрев горячим воздухом). Продолжительность последующей сушки 1,5-2 сут.
Чаще всего вибролитье используют для футеровки ковшей. Способ вибролитья позволяет также ремонтировать изношенные участки (для так называемой «вечной» футеровки).
5.5.3. Расход огнеупоров. При выплавке и разливке стали требуются огромные количества огнеупорных материалов. Общий расход огнеупоров в мировом сталеплавильном производстве составляет 20 млн. т в год. От стойкости огнеупорных материалов зависит не только их расход, но и производительность сталеплавильных агрегатов (частота ремонтов, их трудоемкость), а также качество металла. В частности, для современных методов внепечной обработки металла (продувка инертным газом, обработка вакуумом и т. п.), связанных с интенсивным перемешиванием металла, требуются огнеупоры особо высокого качества (в противном случае перемешивание приведет к загрязнению металла, а не к очищению). Низкая пористость и высокая плотность огнеупорного материала, зависящие в значительной мере от технологии изготовления, должны обеспечить в этих случаях почти полное отсутствие его разрушения и исключить взаимодействие огнеупора с перемешиваемым металлом и шлаком.
Снижения расхода огнеупорных материалов добиваются следующими способами: 1) повышением качества огнеупорных материалов; 2) тщательным хранением отходов огнеупоров, образующихся при периодических ремонтах и вторичном их использовании; 3) организацией процесса плавки с учетом условий эксплуатации огнеупорных материалов; 4) полной или частичной заменой огнеупорной футеровки деталями с искусственным (например, водяным) охлаждением; 1 Доломит (по имени французского геолога Д. Доломье) имеет состав CaMg [CO3h-
2 Корунд — минерал, природный безводный глинозем А12О3; корундовые огнеупорные изделия содержат >90 % А12О3.
3 От греч. thixis — прикосновение и trope — поворот, изменение. Тиксотропия проявляется в разжижении при интенсивном встряхивании или перемешивании гелей, паст, суспензий и других систем с коагуляционной дисперсной структурой и их загущении (затвердевании) после прекращения механического воздействия. Тиксотропными свойствами обладают, например, плывуны.
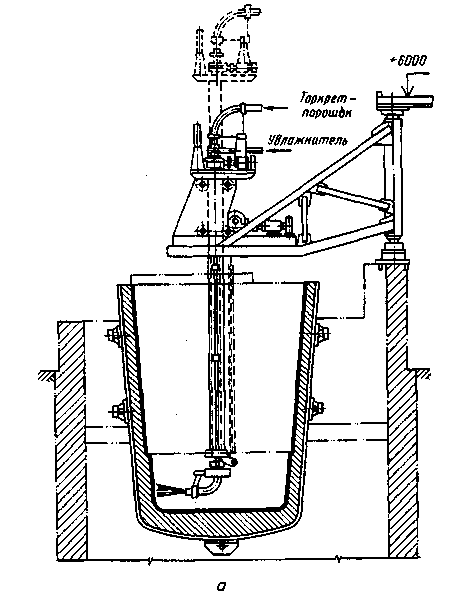
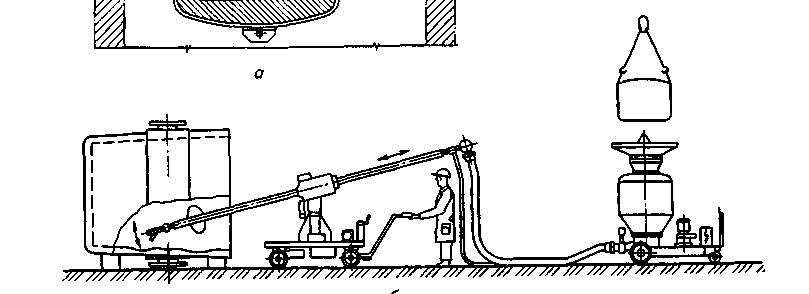
Рис. 5.4. Установка для торкретирования футеровки сталеразливоч-ных ковшей (а) и установка для торкретирования ковшей небольшой вместимости (б) 5) периодическим торкретированием рабочей поверхности огнеупоров. Существует несколько методов торкретирования (нанесения газовой струей покрытия) рабочих поверхностей сталеплавильных агрегатов: с увлажнением смеси, без увлажнения и т. п. (рис. 5.4); 6) посредством нанесения на футеровку определенного количества высокоосновного жидкого шлака (так называемый «раздув или разбрызгивание шлака»). Под воздействием специально направляемых газовых струй капли жидкого шлака (оставляемого в агрегате после выпуска металла) попадают на поверхность футеровки и постепенно покрывают ее тонким слоем. При этом шлак должен иметь определенное (высокое) содержание СаО и MgO.
Существуют и другие, менее распространенные способы. 6. ВНЕДОМЕННАЯ ОБРАБОТКА ЖИДКОГО ЧУГУНА 6.1. РЕГУЛИРОВАНИЕ СОСТАВА ЧУГУНОВ В доменных печах выплавляют литейный и передельный чугуны, а также ферросплавы. При использовании железных руд, содержащих такие ценные примеси, как ванадий, марганец, хром, никель, титан и др., получают чугун с повышенным (против обычного) содержанием этих компонентов. Разработаны специальные технологии для рационального использования получаемых при этом природнолегированных чугунов. Основная доля в выплавке приходится на передельныйчутун, предназначенный для передела в сталь. Среди используемых в сталеплавильном производстве чугунов в зависимости от сталеплавильного агрегата, от химического состава различают соответствующие марки, например чугун коксовый, мартеновский Ml или М2, чугун высококачественный древесно-угольный ПВД1 или ПВД2, бессемеровский (много кремния), томасовский (много фосфора) и т. д.
В свое время были разработаны государственные стандарты, определявшие составы чугунов. Обоснованием этих составов служили дальнейшее рациональное использование чугуна и имеющееся в то время сталеплавильное оборудование, а также технологии. Например, в чугуне марки Ml должно содержаться 0,75—1,25 % Si, в чугуне марки М2 — до 0,75 % Si. В зависимости от содержания марганца чугуны делятся на группы (<1,00 % Мп, 1,01 % Мп и т.д.), в зависимости от содержания фосфора — на классы (<0,15 % Р, <0,20 % Р, <0,30 % и т.д.), в зависимости от содержания серы — на категории (в обычных чугунах в зависимости от категории содержится <0,03 % S, <0,05 % S, <0,07 % S, в высококачественных чугунах —<0,015 % S, <0,020 % S или <0,025 % S и т. д.) и т. п. В последние годы ситуация изменилась: наряду с разнохарактерными требованиями сталеплавильщиков (в зависимости от конкретных условий передела, марочного состава выплавляемых сталей и т. п.) современное металлургическое производство теперь располагает апробированными методами внедоменной (на пути от доменного цеха к сталеплавильному) обработки жидкого чугуна. Данные методы обеспечивают поставку в каждом конкретном случае чугуна именно такого состава, который требуется для данного сталеплавильного цеха.
Целями внедоменной (внепечной) обработки чугуна являются его десульфурация, дефосфорация и обескремнивание. В отдельных случаях осуществляется дополнительный подогрев чугуна. 6.2. ВНЕДОМЕННАЯ ДЕСУЛЬФУРАЦИЯ ЧУГУНА В качестве реагентов-десульфураторов при внепечной обработке чугуна используют магний (в виде чистого магния, смеси извести и магния, кусков кокса, пропитанных магнием, в виде гранул магния, покрытых солевыми покрытиями и др.), кальцийсодержа-щие материалы (в виде извести, известняка, карбида кальция) и соду. Основные реакции десульфурации чугуна:
Mgr+[S] = MgS, ΔG º = -104100 + 44,077;
СаОт + [S] + С = CaST + СОГ, ΔG º = 25 321)-26,337;
СаС2 + [S] = CaS + 2С, ΔG º = -86900 + 28,727;
Na2O + [S] + С = Na2 S + COr, ΔG º = -2000 -26,78 Т.
Расчеты показывают, что для связывания 1кг серы необходимо 0,75 кг Mg, 1,75кг СаО, 2кг СаС2, 3,31кг Na2CO3, т. е. в случае использования металлического магния расход реагента самый низкий. При этом обеспечивается высокая степень десульфурации. К преимуществам использования именно магния можно отнести и такие факторы, как малое количество образующегося шлака, и то, что в процессе десульфурации магнием практически не образуется продуктов, вредных для окружающей среды. Однако из-за сравнительно высокой стоимости магния выбор реагента определяется в конечном счете экономическими соображениями.
Ввод реагентов в металл может осуществляться в виде кусков, гранул, порошков, проволоки. При использовании порошкообразного реагента в качестве несущего газа для его вдувания используют воздух, азот, природный газ. Для перемешивания реагента с металлом используют разные способы, в том числе: 1) падающую струю металла; 2) разные механические мешалки; 3) барботаж в процессе продувки газом; 4) пульсирующую затопленную струю; 5) воздействие вибрации и ультразвука; 6) газолифтное перемешивание и др. Перемешивание массы металла достигается при этом дополнительной продувкой ванны газом (азотом). При использовании азота необходимо учитывать реакцию
3Mgr + N2 = Mg3N2 + Q.
Лучшие результаты получают при использовании в качестве несущего газа природного газа, так как в зоне реакции в результате диссоциации метана происходит снижение температуры до 1200°С, способствующее протеканию экзотермической реакции образования MgS, и создается защитная восстановительная атмосфера над поверхностью расплава в ковше, блокирующая поступление кислорода из атмосферы.
Виды механического перемешивания чугуна приведены на рис. 6.1.
При использовании смесей типа известь + плавиковый шпат + реагент, снижающий окисленность ванны (алюминий, кокс и т. п.), используют мешалки (рис. 6.1, в).
Результаты десульфурации (обессе-ривания) при использовании смесей на базе СаО зависят от таких факторов, как: а) конструкция ковша (в открытом ковше результаты хуже, чем в ковше миксерного типа); б) количество попавшего в ковш миксерного шлака (при значительном количестве миксерного шлака получение низких концентраций серы в чугуне практически недостижимо); в) температура чугуна' (чем выше температура, тем лучше результаты десульфурации).
На рис. 6.2 представлена схема установки для десульфурации чугуна, располагающейся на пути жидкого
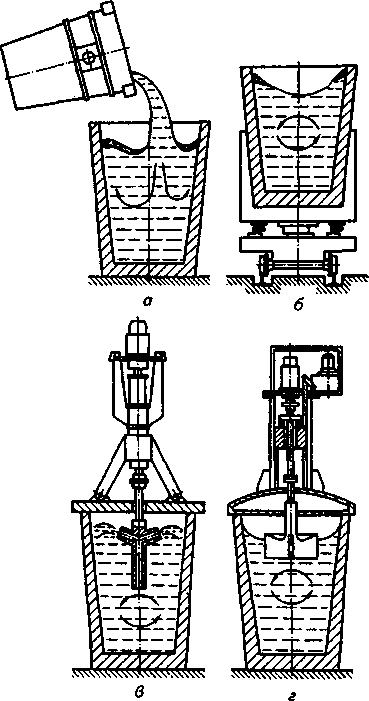
Рис. 6.1. Основные виды механического перемешивания металла:
а — падающей струей; б— вибрационным воздействием; в, г —с использованием мешалок чугуна от доменного цеха к сталеплавильному. Масса единовременно обрабатываемой порции чугуна (рис. 6.2, а) составляет до 100т. Перемешивание металла с реагентом достигается вращением ротора-мешалки и пропусканием через ротор некоторого количества инертного газа (обычно азота), создающего эффект кипения. Пропускная способность такой установки составляет 2 млн. т чугуна в год. При использовании данной установки для обработки чугуна смесью, состоящей из обожженной извести (90 %), плавикового шпата (5 %) и нефтяного кокса (5 %), добиваются снижения содержания серы в чугуне в 10 раз (с 0,0340 до
0,0031 %). В процессе такой обработки возможны реакции (с учетом участия в них содержащегося в чугуне кремния)
2(СаО) + [Si] + 2[S] → 2(CaS) + SiO2;
2(CaO) + [С] + 2[S] → 2(CaS) + CO2.
Используемую в составе смесей для десульфурации известь на ряде предприятий заменяют известняком СаСО3. При этом уменьшается расход энергии, затрачиваемой на разложение известняка при его обжиге в из-вестковообжигательных печах. Кроме того, термическая диссоциация частичек СаСО3 в зонах внедрения в металл способствует образованию очень мелких активных частичек СаО, а именно: СаСО3 = СаО + СО2. Образующийся оксид СО2, взаимодействуя с углеродом чугуна СО2 + С = 2СО, способствует значительному повышению турбулентности потока в реакционной зоне и циркуляции в объеме металла. Реакция разложения СаСО3 идет с поглощением тепла, однако эти потери тепла в какой-то мере компенсируются теплом, которое выделяется в процессе взаимодействия образующегося при разложении известняка СО2 с содержащимся в чугуне кремнием: СО2 + [Si] = SiO2 + С. Достигаемое при этом 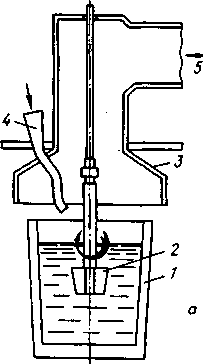 10> |
|
|