Производство пластических масс на основе полимеров, получаемых поликонденсацией и ступенчатой полимеризацией. Фенолоальдегидные смолы и пластмассы на их основе находят широкое применение в технике. В качестве сырья для их получения используют фенолы (крезол, ксилолы, фенол и др.) и альдегиды (формальдегид, фурфурол). Наибольшее применение для получения смол находят фенол и формальдегид.
Фенол представляет собой кристаллическое вещество, плавящееся при 40,9 °С. В основном его получают синтетическим методом и лишь в небольшом количестве (3,5%) из каменноугольной смолы. Он смешивается в любых соотношениях со спиртом, водой при нагревании свыше 66 °С, растворим в эфире, глицерине, сероуглероде и др.
Смолы, полученные на основе фенола и формальдегида, получили название фенолоформальдегидных. Они находят наибольшее применение из других смол этой группы. В зависимости от соотношения между фенолом и формальдегидом и применяемого катализатора получаемые смолы могут быть термопластичными (новолачные) и термореактивными (резольные).
Новолачные смолы получают в водной среде при конденсации избытка фенола и формальдегида в присутствии кислоты (соляная, щавелевая, серная кислоты) по схеме:

Обычно взаимодействие протекает при мольном соотношении фенола и формальдегида, равном 7:6. Новолаки являются низкомолекулярными соединениями (n = от 4 до 8). При нагревании они плавятся, легко растворяются в спирте. Новолачные смолы применяют для получения пресспорошков, абразивных изделий, газонаполненных материалов. Для перевода этих смол из термопластичного состояния в термореактивное в качестве отвердителя используют уротропин.
Резольные смолы получают из фенола и небольшого избытка формальдегида в присутствии щелочных катализаторов NH4OH, NaOH, Ва(ОН)2.
Процесс образования смолы состоит из двух стадий: реакции фенола с формальдегидом с образованием фенолоспиртов и конденсации фенолоспиртов с образованием резола (смесь полифенолов):
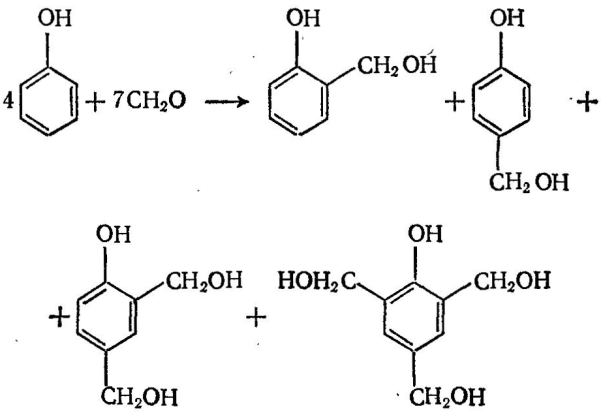
Фенолоспирты реагируют между собой с образованием резолов
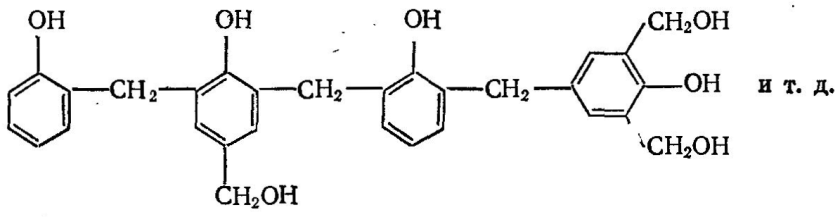
Резолы представляют собой смесь линейных и разветвленных полимеров общей формулы
Н—[—С6Н2(ОН) (СН2ОН)СН2—]m[— С6Н3(ОН)СН2—]n—ОН
где n = 2+5, а m+n — 4+10.
Резольная смола является низкомолекулярным соединением (от 400 до 1000). При нагревании смолы происходит дальнейшая конденсация макромолекул, в результате чего образуется резит, представляющий собой неплавкий и нерастворимый полимер следующего строения:
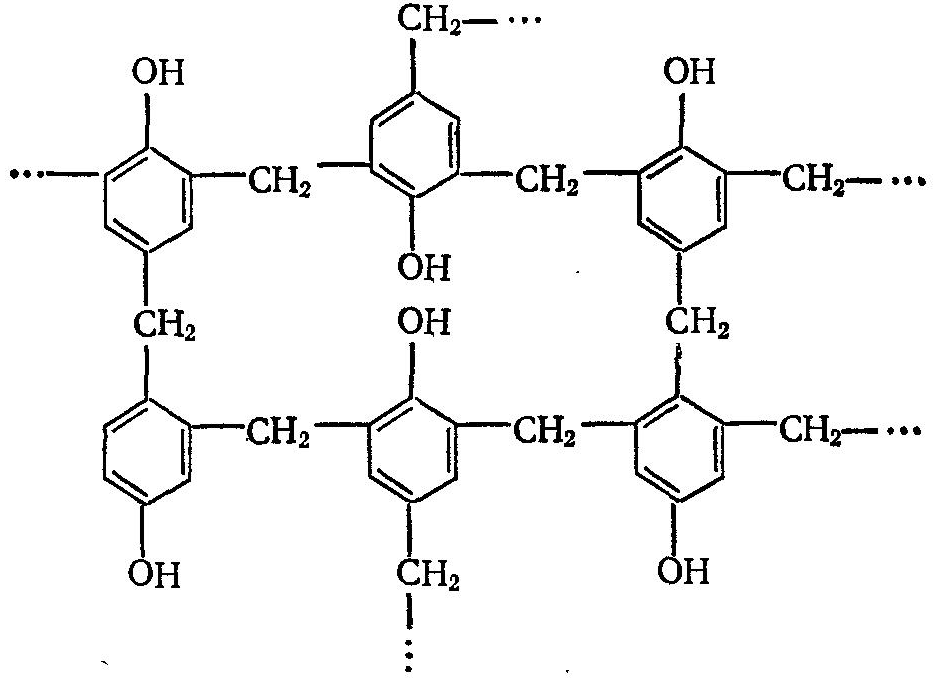
Процессы получения новолачной и резольной смолы практически не отличаются друг от друга. В реактор вводят фенол, формальдегид, различные добавки и катализатор и смесь нагревают в реакторе до 70— 75 °С с помощью пара, подаваемого в рубашку реактора. Поликонденсация фенола с формальдегидом протекает с выделением тепла. Оптимальная температура в реакторе должна быть не выше 80 °С, поэтому по достижении этой температуры отключают подачу пара и ведут охлаждение смеси, подавая в рубашку реактора воду. В процессе поликонденсации пары воды поступают в трубчатый холодильник и конденсируются. Образовавшаяся смола плавится и в жидком состоянии выдавливается из реактора по трубе сжатым воздухом в противень, здесь она затвердевает и измельчается в порошок.
Фенолоформальдегидные смолы находят широкое применение в качестве связующего при получении пресспорошков, волокнистых материалов, слоистых пластиков, поропластов. Кроме того, они используются для получения лаков и клеев.
Пластические массы, получаемые на основе фенолоформальдегидных смол, получили название фенопластов. Литой резит относится к ненаполненным фенопластам, так как он состоит только из одной смолы. Он имеет низкие физико-механические свойства, трудно перерабатывается в изделия, поэтому практического значения не имеет.
Композиционные фенопласты в зависимости от наполнителя делятся на прессовочные, волокнистые и слоистые материалы.
Изделия из пресспорошков. Выпускаемые промышленностью пресспорошки классифицируются в зависимости от назначения, по виду сырья, применяемого для получения смол; по поведению смолы при нагревании. Ассортимент выпускаемых порошков очень велик (примерно 100 марок).
Пресспорошки в зависимости от связующего подразделяются на новолачные и резольные.
Новолачные пресспорошки готовят из смеси твердых фенолоформальдегидных смол, наполнителей (древесная мука, каолин, тальк, слюда, графит, кварц, асбест и др.), отвердителей (уротропина, окиси магния, кальция и др.), смазки (олеиновая, стеариновая кислоты и их соли), красителей и пигментов (мулия, охра, литопон и др.). Получают их вальцеванием и шнековым методом.
Резольные пресспорошки отличаются по составу от новолачных только тем, что при их получении применяются фенолоформальдегидные смолы резольного типа. Пресспорошки перед прессованием таблетируют.
Свойства изделий, получаемых из пресспорошков, зависят от свойств и количества применяемых связующего и наполнителя. Например, тепло- и жаростойкость изделий можно повысить, вводя в пресспорошки кварц, слюду, асбест.
Технологические свойства пресспорошков зависят от типа смолы, рода наполнителя и его содержания, количества отвердителя. Изделия из пресспорошков готовят методом горячего прямого и литьевого прессования при 160—200 °С под давлением и другими специальными методами.
Рассмотрим примеры использования пресспорошков для изготовления изделий.
Изделия общетехнического назначения получают из пресспорошков, содержащих фенолоформальдегидные смолы и древесную муку. К ним относятся ненагруженные армированные и неармированные детали и изделия широкого потребления (розетки, рукоятки, корпуса проигрывателей и др.).
Радиодетали и другие изделия, работающие при высоких температурах, готовят из пресспорошков, содержащих смолы, асбест или слюду. Изделия, устойчивые к действию воды и кислот, готовят из пресспорошков, имеющих в своем составе новолачные смолы, совмещенные с поливинилхлоридом, каучуком и другими полимерными соединениями. В качестве наполнителей применяют кокс, графит, каолин и др.
Волокниты - прессовочные материалы, получаемые на основе волокон различного типа и растворов фенолоформальдегидных или других смол.
Из волокнита (наполнитель — хлопковая целлюлоза) прессуют детали общетехнического назначения, работающие на изгиб, истирание, кручение, а также изделия, обладающие антифрикционными свойствами (переключатели, фланцы, рукоятки, шестерни и т. д.). Изделия из них устойчивы в воде, слабых кислотах и основаниях, но разрушаются при действии сильных кислот и щелочей.
Асбоволокнит готовят прессованием асбеста и других составляющих, пропитанных фенолоформальдегидной или другой смолой. Материал применяют для изготовления деталей электротехнического назначения и изделий, обладающих фрикционными свойствами, высокой теплостойкостью и механической прочностью, например, тормозные колодки экскаваторов, подъемных кранов.
Фаолит получают прессованием асбеста или смеси графита и асбеста, пропитанных фенолоформальдегидной смолой. Он устойчив в растворах соляной кислоты любой концентрации, в 40%-ной серной, в 50%-ной ортофосфорной и уксусной кислотах, в хлорированных углеводородах, но, разрушается иодом, бромом, щелочами, ацетоном, спиртом и кислотами, обладающими окислительными свойствами.
Из фаолита при обычной температуре, без давления готовят крупногабаритные изделия: трубы, ванны, адсорберы, различного вида емкости и т. д., которые затем отверждаются при температуре 60—130°С. Теплостойкость фаолита около 145°С.
Фенопласты, содержащие стеклянное волокно в качестве наполнителя, называются стекловолокнитами. Эти материалы обладают высокой удельной прочностью, жесткостью, устойчивы к вибрационным нагрузкам, к многим химическим реагентам и микроорганизмам, имеют хорошие диэлектрические и теплоизоляционные свойства.
Слоистые пластики — прессматериалы, содержащие листовой наполнитель: хлопчатобумажную ткань (текстолит), бумагу (гетинакс), асбестовую (асботекстолит) или стеклянную (стеклотекстолит) ткань, стеклянный и древесный шпон (древеснослоис- тыепластики ДСП). Получают слоистые материалы горячим прессованием уложенных правильными рядами слоев листового наполнителя, пропитанного резольной смолой. Полученный материал обладает хорошими физико-механическими и химическими свойствами (см. табл. XV. 3).
Текстолит используется для изготовления изделий, обладающих стойкостью к вибрационным нагрузкам; износостойкостью и электроизоляционными свойствами. Из него готовят шестерни, вкладыши, детали, работающие в условиях трения, декоративные и отделочные материалы.
Гетинакс широко применяется в электро- и радиотехнической промышленности и, в частности, в производстве печатных схем для радио и телевизоров, переключателей и т. п.
Стеклотекстолиты выпускаются в виде листов различных размеров длиной до 2,5 м, шириной до 1 м и толщиной 0,5—15 мм. Они широко применяются для изготовления фюзеляжей самолетов, кузовов автомобилей, деталей машин, лодок, судов, самолетов и т. д. Теплостойкость стеклотекстолита 200°С при продолжительной эксплуатации и 300°С при кратковременной работе.
Стекловолокнистый анизотропный материал (СВАМ) готовят горячим прессованием стеклянного шпона с нанесенным на его поверхность связующим (совмещенные фенолформальдегидные смолы с поливинилбутиралем или с эпоксидыми олигомерами). Прессование проводят в гидравлических прессах при температуре 150—160°С и давлении 4 МПа с последующей вытяжкой изделий, продолжительность вытяжки 6 мин на 1 мм толщины получаемого изделия.
СВАМ, подобно фанере, обладает упругими анизотропными свойствами и в зависимости от укладки волокон может иметь высокую прочность вдоль расположения стекловолокон и низкую в поперечном направлении. Из него готовят трубы и другие изделия, устойчивые к действию химических реагентов, детали катеров, лодок, конструкций кораблей, кузовов автомашин, прицепов, цистерн, хранилищ и т. д., а также применяют как электроизоляционный материал (электрощиты, электроаппаратура). СВАМ нашел широкое применение в строительстве: из него готовят плиты перекрытий и несущие панели стен, тепло- и звукоизолирующие строительные элементы, шахтную крепь и кузова шахтных вагонеток и др.
Древесно-слоистые пластики (ДСП) используются для изготовления мебели, спортивных лодок, деталей катеров, вкладышей подшипников, шестерен, опорных рам, фрикционных шкивов, втулок небольшого диаметра и других деталей.
Эпоксидные смолы получают взаимодействием эпоксисоединенин с веществами, содержащими подвижные атомы водорода, или введением эпоксидных групп
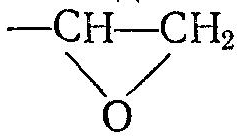
в ненасыщенные соединения под действием надкислот, например, надуксусной кислоты СНзСОООН.
Наиболее широко применяется первый метод получения эпоксидных смол, где в качестве сырья используют мономеры, содержащие эпокси-группы, и многоатомные фенолы (дифенилолпропан, гидрохинон, пирогаллол и др.).
Образование эпоксидной смолы при взаимодействии эпихлоргидрина и дифенилолпропана в присутствии щелочи происходит по схеме
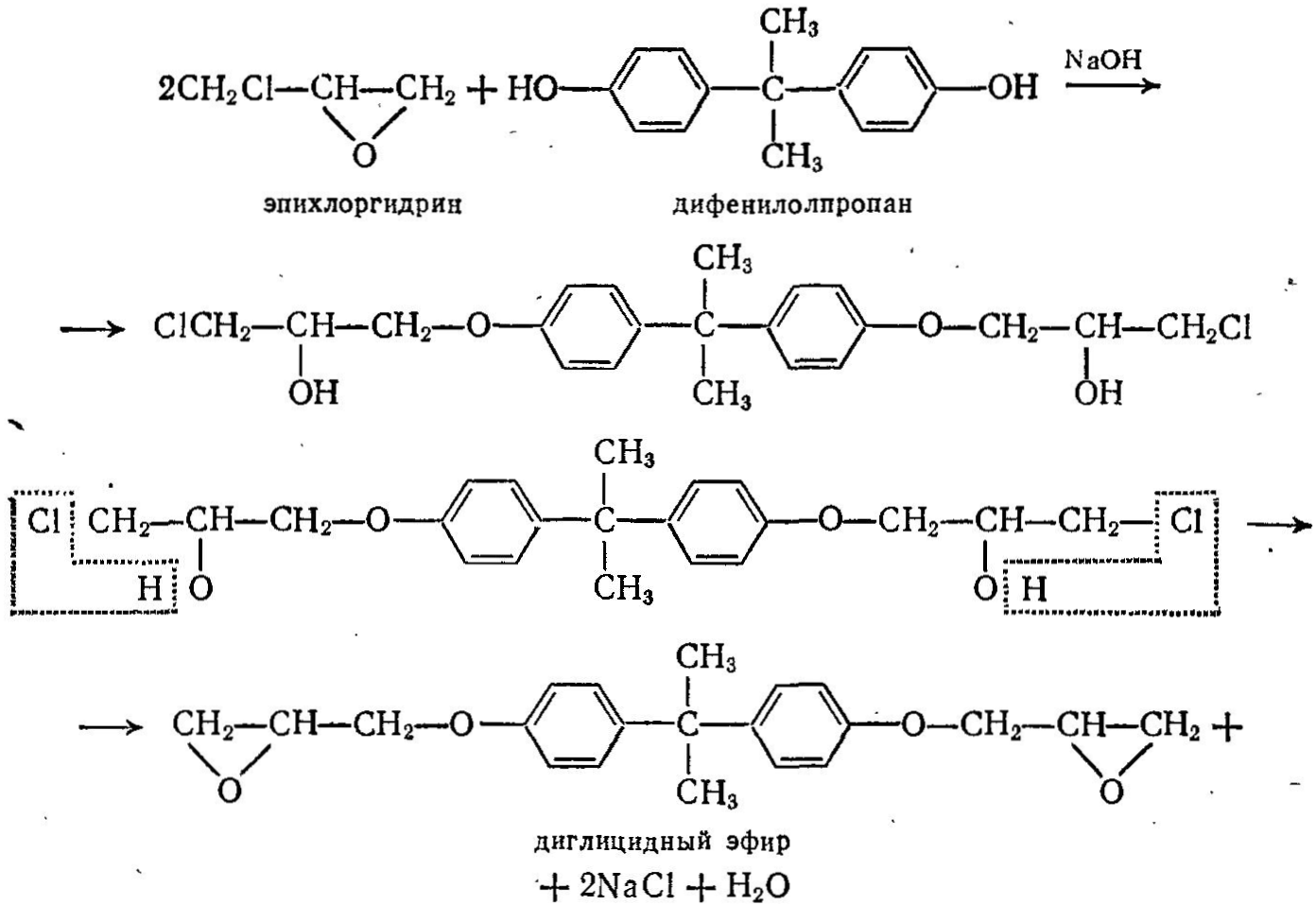
Кроме диглицидного эфира в смеси содержатся полимеры большей молекулярной массы (т. е. с числом звеньев от 2 до 16), которые имеют следующую структуру:
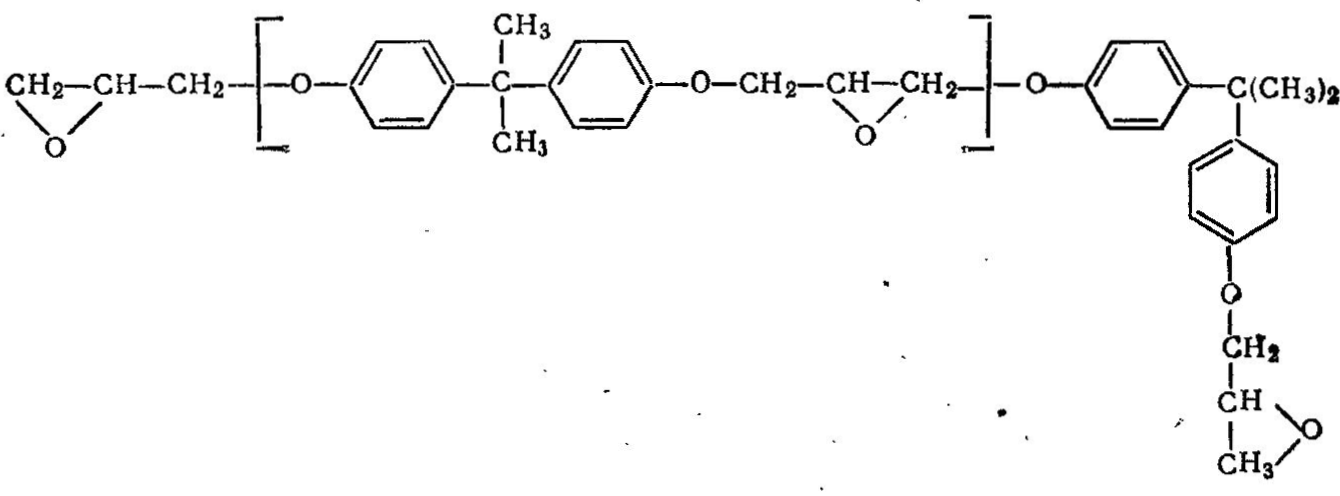
Эпоксидные смолы такого строения имеют линейную структуру, поэтому они плавятся и растворяются в органических растворителях.
Эпоксидные смолы получают и при взаимодействии эпихлоргидрина с аминами (например, с анилином), гликолями (например, этиленгликолем) и др.
По второму методу эпоксидные смолы можно получать при взаимодействии непредельных углеводородов (например, дивинила) с надуксусной кислотой:

Образующиеся соединения могут далее реагировать с мономерами по реакциям, приведенным для первого способа.
Эпоксидные смолы представляют собой олигомеры, содержащие свободные концевые эпокси-группы, которые при взаимодействии с некоторыми веществами (отвердителями) и между собой образуют полимеры сетчатого строения. В качестве отвердителей применяются гексаметилендиамин, этиленполиамин, меламин, смолы, фталевый ангидрид, кислоты и др. Эпоксидные смолы допускают высокую степень наполнения (50%) их различными наполнителями (кварцем, стеклом, тальком, асбестом, графитом и др.). Присутствие наполнителей способствует увеличению твердости и теплостойкости, снижению усадки и стоимости пластмассы, при использовании же армирующих наполнителей в виде волокна и тканей можно получать высокопрочные материалы.
Эпоксидные смолы и компаунды широко применяются для изоляции и герметизации изделий; в машиностроении (изготовление штампов холодной вытяжки, прессформ, литейных моделей и т. п.); для изготовления клеев, исправления дефектов литых изделий, ремонта металлических деталей и трубопроводов и для изготовления различного вида фасонных изделий. Так, из стеклопластиков и СВАМ, полученных из эпоксидных смол, готовят корпуса моторных лодок, разнообразные детали, используемые в авиа-, судо- и ракетостроении и т. д. Обладая высокой адгезией ко многим материалам, прочностью и химической стойкостью к растворителям, кислотам, щелочам и растворам солей, эпоксидные смолы широко используются для защиты металлов, сплавов и других материалов от коррозии.
различного вида фасонных изделий. Так, из стеклопластиков и СВАМ, полученных из эпоксидных смол, готовят корпуса моторных лодок, разнообразные детали, используемые в авиа-, судо- и ракетостроении и т. д. Обладая высокой адгезией ко многим материалам, прочностью и химической стойкостью к растворителям, кислотам, щелочам и растворам солей, эпоксидные смолы широко используются для защиты металлов, сплавов и других материалов от коррозии.
Производство каучука и резино - технических изделий. Основные свойства и применение. Примеры.
Среди большого числа высокомолекулярных соединений в современной технике и технологии каучук находит особенно широкое применение.
Каучук является основным компонентом при изготовлении резиновых, резино-тканных и резино-металлических изделий, используемых в промышленности, сельском хозяйстве, на транспорте и в домашнем обиходе. На основе каучуков получают более 40000 наименований резиновых изделий, к их числу относятся автомобильные и авиационные шины, приводные ремни, потребность в которых исчисляется в десятках миллионов квадратных метров в год, гибкие шланги и рукава, детали машин и механизмов, предметы санитарии н гигиены и т. д. Такое широкое применение резин объясняется тем, что они обладают уникальной способностью к обратным деформациям в сочетании с высокой прочностью, эластичностью, сопротивляемостью к истиранию.
Резины устойчивы к действию многих химических реагентов, что позволяет использовать их для футеровки химической аппаратуры и при изготовлении деталей уплотнений. Они газо- и водонепроницаемы, имеют высокие диэлектрические свойства и являются незаменимым материалом при производстве кабеля, аэростатов, надувных лодок, скафандров и т. п. Новые быстро развивающиеся отрасли техники требуют разработки современных типов каучуков и резин, выдерживающих температуры от —100 до +350 °С, устойчивых к действию окислителей, бензина, масел, растворителей, облучения и т. п.
Сырье и материалы резинового производства
Сырьем для получения резины служат сырой каучук, синтетические латексы и смолы, регенерат, вулканизующие вещества, ускорители вулканизации, активаторы или замедлители вулканизации, красители, пластификаторы, противостарители, активные наполнители, армирующие и вспомогательные материалы. Основным сырьем, определяющим свойства резин, является каучук.
Каучуки являются высокомолекулярными соединениями. Они имеют линейное строение и обладают способностью к обратной деформации в сочетании с высокой прочностью.
Для изготовления резин применяется натуральный и синтетические каучуки.
Натуральный каучук относится к каучукам общего назначения, т. е. к каучукам, применяемым для изготовления резиновых изделий широкого потребления (шин, ремней, обуви и т. д.).
Синтетические каучуки в зависимости от строения макромолекулы подразделяются на органические, элементоорганические и неорганические. Они могут быть гомополярными, т. е. макромолекулы их состоят из звеньев одного мономера, и сополимерными, когда макромолекулы содержат два или несколько мономерных звеньев.
Натуральный каучук до 1932 г. был единственным сырьевым материалом, применяемым для производства резины. Получают натуральный каучук (НК) из млечного сока некоторых каучуконосных растений («Као-чу», т. е. «слезы дерева»), преимущественно из тропического дерева гевеи, из которого выделяют 99% всего мирового каучука. Млечный сок (латекс) дерева гевеи содержит частички каучука (до 30%), взвешенные в воде (до 60%), белковые вещества (2—2,7%), смолы (1,65—3,4%), сахаристые (1,5— 4,2%) и минеральные (0,2—0,7%) вещества. На состав латекса влияют возраст дерева, время года, климатические условия.
При обработке млечного сока на месте его добычи кислотами, например уксусной, происходит коагуляция сока с образованием гелеобразного продукта. Этот продукт пропускают через вальцы, сушат, коптят (для предохранения от загнивания при хранении) и в виде листов, упакованных в кипы, направляют потребителю.
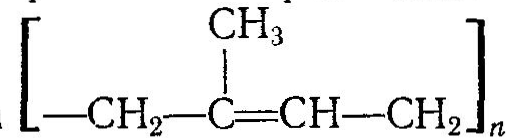
Макромолекулы натурального каучука состоят из элементарных звеньев изопрена; он имеет малую плотность (917—937 кг/м3) и большую молекулярную массу (от 150000 до 500000), что соответствует длине макромолекулы 10000— 40000 А при поперечном сечении 3 А. Такие длинные нитевидные гибкие макромолекулы и определяют физические и механические свойства каучука. Он обладает высокой эластичностью, прочностью, малой гигроскопичностью и теплопроводностью и является превосходным изолятором. Прочность при разрыве его составляет от 1 до 4 МПа, а в вулканизированном состоянии — до 30 МПа.
НК является термопластичным полимером. При нагревании выше 200 °С он разлагается с образованием изопрена и других низкомолекулярных соединений, а при радиационном облучении выделяется водород. Натуральный каучук растворяется в бензине, бензоле, сероуглероде и др. с образованием вязких растворов, которые используются как клеи.
Поскольку в макромолекуле каучука имеются двойные связи, он вступает во взаимодействие с галогенами, тиоспиртами, тиокислотами, кислородом, озоном и др. При взаимодействии с серой и органическими перекисями линейная структура макромолекул нату- рального каучука превращается в сетчатую (процесс вулканизации). Это свойство каучука лежит в основе получения резины.
Натуральный каучук в основном применяется для изготовления резины, причем большая его часть используется для получения автомобильных шин и только около 1 % применяется в обувной промышленности и для получения резинового клея.
Синтетические каучуки (СК) в настоящее время занимают ведущее место (около 2/3 всего производимого в мире каучука) при производстве резины.
В зависимости от применения СК подразделяют на каучуки общего назначения: бутадиеновый (СКВ), бутадиен-стирольный (СКС), бутадиен-метилстирольный (СКМС), изопреновый (СКИ); каучуки специального назначения: бутадиен-нитрильный (СКН), хлоропреновый (наирит), бутилкаучук, тиоколовый, силиконовый (СКТ) и др.
Первый в мире синтетический каучук был получен в СССР в 1932 г., несколько позже каучук ехали получать в Германии (1938 г.) и США (1942 г). Процесс получения синтетического каучука включает две стадии: синтез мономеров и полимеризацию или поликонденсацию мономеров.
Для получения СК и латексов применяют так называемые каучукогенные мономеры: бутадиен, стирол, изопрен, хлоропрен, изобутилен и др.
Натрий-бутадиеновый каучук (СКВ) является первым каучуком, полученным синтетическим путем по методу акад. Лебедева С. В. полимеризацией бутадиена в присутствии металлического натрия. Бутадиен для этой цели получили из этилового спирта в присутствии катализаторов. В настоящее время его получают в основном, дегидрированием бутана.
Натрий-бутадиеновый каучук обладает низкими адгезионными свойствами и эластичностью, характеризуется невысокими прочностными свойствами и морозостойкостью по сравнению с натуральным и другими синтетическими каучуками, поэтому в настоящее время он практически не применяется.
Бутадиен-стирольные каучуки (СКС, СКМС) получают из бутадиена СН2 = СН — СН = СН2 и стирола С6Н5СН = СН2(СКС), бутадиена и метилстирола С6Н5ССН3 = СН2 (СКМС). Процесс сополимеризации приведенных выше мономеров проводят эмульсионным способом по непрерывной схеме.
В зависимости от содержания стирола бутадиен-стирольные каучуки маркируют различными числовыми индексами, например, каучук типа СКС-10, содержит 10% стирола и 90% бутадиена. При увеличении в каучуках стирола или метилстирола ухудшаются клеющая способность, эластические свойства, морозостойкость, но улучшаются показатели прочности.
Вулканизированные каучуки СКС и СКМС имеют низшую прочность, которая резко возрастает (в 10—12 раз) при введении в резиновую смесь газовой сажи. Диэлектрические свойства этих каучуков приближаются к свойствам натурального, а молекулярная масса увеличивается от 10000 до 100000.
Из этой группы каучуков наибольшее применение находят каучуки СКС40/СКС-30, СКМС-10, СКМС-30. Каучуки СКС-30 и СКМС-30 относятся к универсальным каучукам. Они используются для изготовления шин, транспортерных лент, обуви и других резиновых изделий. Каучуки СКС-10 и СКМС-10 обладают высокой прочностью при истирании, твердостью, растворяются в бензине, бензоле и других углеводородах, хорошо смешиваются с различными ингредиентами резиновых смесей. Прочность на разрыв не- наполненных резин на основе этих каучуков невысока. Для повышения механических свойств в состав резин вводят наполнители, например 50 масс, частей сажи. Такие резины имеют прочность на разрыв 20—25 МПа и температуру стеклования от —72 до —77°С.
Синтетический изопреновый каучук (СКИ), полученный впервые в Советском Союзе, находит широкое применение для получения резины. Его готовят полимеризацией изопрена (15%) в растворе изопентана или другого растворителя непрерывным методом при температуре 18—25 СС в присутствии комплексных катализаторов (металлического лития, тетрахлорида титана, триизобутил- алюминия, триэтилалюминия и др.):

СКИ обладает высокой прочностью и клеющей способностью, сохраняет свои свойства при нагревании до + 100°С. По своему строению, физическим, технологическим, эластическим и эксплуатационным свойствам СКИ близок к НК, поэтому, в отличие от других каучуков общего назначения, он вполне может заменить натуральный каучук при изготовлении резины.
Резины, получаемые из СКИ, набухают в маслах, бензине и других органических веществах, окисляются кислородом воздуха, морозостойки и газонепроницаемы.
Хлоропреновый каучук (наирит) получают эмульсионной полимеризацией хлоропрена:

Процесс проводят в водной среде в присутствии эмульгатора (олеинат натрия). Получаемый латекс коагулирует при взаимодействии с кислотами и солями, после чего гелеобразный продукт промывают, сушат и превращают в листы, блоки, бруски. Средняя молекулярная масса такого каучука — 100000. Наирит не требует специальной пластификации, так как обладает высокой клейкостью. Это упругое, но более жесткое по сравнению с натуральным каучуком вещество.
Прочностные свойства его близки к свойствам натурального каучука. Он нерастворим в углеводородах жиррого ряда, но растворяется в хлорированных и ароматических углеводородах, устойчив к воздействию света, озона, кислорода, огнестоек.
При получении резины каучук вулканизируют в присутствии' окислов цинка, ртути и др. Резины, получаемые на его основе, обладают высокой прочностью от 22 до 35 МПа при относительном удлинении 800—1000%.
Наирит неустойчив при изменении температур, твердеет при хранении, а при нагревании от него отщепляется хлористый водород. Применяется он главным образом в производстве ремней, транспортерных лент, клеев, для изготовления кабеля.
Кремнийорганические (силиконовые) каучуки получают при поликонденсации циклических силоксанов или линейных силоксан- диолов. Полимеры имеют линейное строение, например
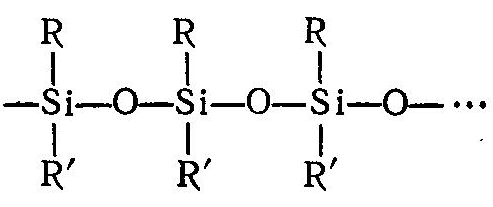
где R, R'— метальные, этильные, фенильные, винильные и другие группы.
Кремнийорганические каучуки могут быть высокомолекулярными (молекулярная масса от 500000 до 1000000) и низкомолекулярными от 20000 до 100000. Каучуки озоно-, морозо- и термостойки, но механические их свойства, масло- и нефтестойкость хуже, чем любого другого каучука. В отличие от других видов вулканизацию кремнийорганических каучуков ведут в присутствии органических перекисей (например перекиси бензоила) при нагревании до 200 °С. Силиконовые каучуки используются при получении резин с повышенной морозо- и теплостойкостью, а также для изготовления деталей, работающих на сжатие. Из резины готовят жароупорные прокладки, уплотнения, клапаны, электроизоляцию и т. д.
В настоящее время выпускается несколько видов каучуков: ди- метилсилоксановый СКТ, метилвинилсилоксановый СКТВ, этил- силоксановый СКТЭ, фенилсилоксановый СКТ ФВ, бор- и фосфор- силоксановые, низкомолекулярные каучуки СКТН, СКТН-1 и др.
Резины, изготовленные на основе силиконовых каучуков, начинают разлагаться при температуре 600—700°С, но в течение нескольких секунд они могут выдерживать температуру 3000 °С.
Вспомогательные материалы. Синтетические латексы - сложные коллоидные системы, содержащие до 35% каучуков с частицами размером от 5-10-6 — 5- 10-4см. Они устойчивы в воде благодаря присутствию в системе эмульгатора.
Латексы получают эмульсионной полимеризацией и сополимеризацией. Наибольшее применение находят бутадиен-стирольные, хлоропреновые, бутадиен-нитрильные, бутадиен-винилиденхлоридные латексы. Они широко используются в производстве губчатых изделий, нетканных материалов, тонкостенных изделий, для пропитки волокон, в производстве бумаги, кожи, красок и т. д. Особенно незаменимы латексы при изготовлении изоляционных изделий и как пропиточный материал для тканей, используемых при изготовлении шин и резино-технических изделий, что позволяет усилить прочность корда и тем самым увеличить срок эксплуатации шин.
Синтетические смолы - вводят в резиновую смесь и в пропиточные составы как добавки к каучуку для улучшения обработки резиновой смеси, повышения ее износостойкости и прочности резиновых изделий. Наибольшее применение из полимеров находят поли- изобутилен, полипропилен, поливинилхлорид, фенолоформальдегидные смолы.
Регенерат - материал, получаемый в результате переработки отходов резинового производства, резин, изношенных шин и других изделий. Получают регенерат тепловой обработкой тонко измельченной резины в течение 10—16 ч при 150—200 °С в присутствии пластификаторов и других веществ. В результате нагревания происходит девулканизация резины и материал превращается в пластичную массу.
Регенерат широко применяется в резиновой промышленности, так как он в 3—5 раз дешевле каучука. Кроме того, введение регенерата в резиновую смесь облегчает ее обработку и изготовление изделий, увеличивает химическую стойкость резин и их сопротивление старению.
Армирующие материалы - применяемые при изготовлении резиновых изделий, позволяют им сохранять свои размеры под нагрузкой или при нагревании. При работе вводимый в резиновые изделия каркас из ткани или металла воспринимает всю механическую нагрузку, регулирует деформируемость изделия, а резина придает ему необходимую эластичность. В зависимости от назначения изделий армирующими материалами могут быть стальные тросы и проволока, природные и химические волокна, различные ткани и т. д.
Ингредиенты резиновых смесей. Резина - материал, способный к большим высокоэластичным деформациям. Получают ее из каучука (или регенерата) или из смеси каучука и других веществ, получивших название ингредиентов. Число веществ, входящих в состав резиновой смеси, зависит от условий работы резины и изделий на ее основе и колеблется от 5 до 20.
Как указывалось ранее, макромолекулы каучука имеют линейное или разветвленное строение, поэтому для превращения линейной структуры в пространственную (сетчатую) в резиновую смесь вводят .вулканизующие вещества (серу, окислы и перекиси металлов и др.). которые образуют поперечные мостики между длинными цепями макромолекул (процесс вулканизации). Вулканизация может быть вызвана ядерным облучением, в этом случае вулканизатор не требуется.
Процесс вулканизации можно ускорить введением в резиновую смесь ускорителей вулканизации (полисульфиды, каптакс и др.), которые способствуют также улучшению физико-механических свойств резины. В ряде случаев при получении резины для ускорения или замедления действия ускорителей в смесь вводят активаторы, а при необходимости и замедлители процесса вулканизации.
Механические и другие свойства резины улучшают введением в смесь активных наполнителей (сажи, двуокиси кремния, титана, окиси цинка и др.) в виде тонкоизмельченных порошков, количество которых колеблется от 15 до 100 масс, частей и более на ,100 масс, частей Каучука. Неактивные наполнители (мел, тальк, каолин и др.) незначительно повышают прочностные свойства резины, но они улучшают обрабатываемость сырой резины и снижают ее стоимость.
Для улучшения обрабатываемости сырой резины, равномерного распределения ингредиентов в смеси, повышения ее эластических свойств в состав смеси вводятся мягчители или пластификаторы, которые несколько снижают прочностные, но повышают пластические свойства резины. При использовании каучуков общего назначения в качестве пластификаторов применяются углеводороды (от 5 до 30 масс, частей), органические жирные кислоты (1—2 масс, части), смолы (3—10 масс, частей), а в каучуки специального назначения— эфиры (дибутилфталат) и синтетические смолы (фенолоформальдегидные и др.).
Изделия из каучука и резины под действием кислорода воздуха даже в состоянии покоя стареют, становятся хрупкими и ломкими. Для предотвращения или замедления этого процесса в состав резиновой смеси вводят противостарители (фенолы, ароматические амины и др.). Для придания цвета изделиям из резины применяют наполнитель — коллоидальную кремневую кислоту (белую сажу) или окись цинка и красители. Пористую резину (резину, содержащую ячейки, заполненные газом) получают введением в смесь порообразователей (углекислого аммония, диазосоединений и др.), разлагающихся при нагревании с выделением газов. Кроме перечисленных выше, в изделия добавляют резиновые клеи, смазки, растворители, пудры, (для снижения слипания полуфабрикатов) и др.
Процесс изготовления резиновых изделий состоит из нескольких стадий:
приготовление сырой резиновой смеси из ингредиентов;
изготовление или формование заготовок или изделий из сырой резиновой смеси;
вулканизация изделий;
отделка изделий.
Приготовление резиновой смеси включает операции, связанные с подготовкой сырьевых материалов (развеска, дозировка сырья, прорезинивание тканей, пластикацию каучука под действием тепла и др.) и их смешение.
Смешение составляющих резиновой смеси осуществляют в резиносмесителях, червячных прессах или на вальцах
Резиновая смесь подается в вальцы между двумя валками, укрепленными в станине. Поскольку передний валок вращается медленнее заднего валка, окружные скорости вращения валков различны. При прохождении резиновой смеси через зазор между валками в ней возникают деформации сдвига, что приводит к равномерному смещению ингредиентов.
Для изготовления заготовок, деталей, трубок, прорезиненных тканей и т.д. применяются червячные прессы (шприц-машины), каландры.
Изделия сложного профиля собирают из предварительно заготовленных частей и деталей (прорезиненные ткани, металлические каркасы и т. п.), соединяя их между собой склеиванием или подпрессовкой. Отдельные изделия получают из латексов, например пористые резины (вспенивание латекса), а тонкостенные изделия (перчатки и др.) получают методом окунания формочек в латекс, с последующей его коагуляцией, сушкой и вулканизацией получаемых изделий.
Вулканизация является заключительной стадией изготовления резиновых изделий, основное назначение которой состоит в закреплении полученной формы изделием и придании изделию свойств резины.
Количество вулканизатора, вводимого в резиновую смесь, оказывает сильное влияние на свойства резины.
Большое число резиновых, резино-тканевых и других изделий подвергают вулканизации при температуре 125—180°С в аппаратах, работающих под давлением в атмосфере насыщенного пара, горячего воздуха и др.
Продолжительность вулканизации изделий зависит от температуры, давления, габаритов изделия, состава резиновой смеси, греющей среды, аппаратуры, применяемой при вулканизации. Должен поддерживаться оптимальный режим вулканизации, так как от этого в значительной степени зависят прочностные свойства резины.
Вулканизацию резиновых изделий проводят в аппаратах различного типа, устройство которых зависит от сложности изготовляемых изделий и типа их конструкции. Наибольшее применение находят вулканизационные прессы, автоклавы, камеры, аппараты барабанного типа и другие.
Изделия, полученные после вулканизации, полностью теряют свои пластические свойства, но приобретают эластичность, повышенные прочностные свойства и износоустойчивость и др.
После вулканизации все резиновые изделия подвергаются отделке. При этом устраняются заусенцы, производится зачистка, обточка, шлифовка изделий, а в ряде случаев и их окраска с целью предохранения от старения (автомобильные шины) или для улучшения внешнего вида (галоши, мячи и др.). Все изделия для определения сортности подвергаются осмотру с целью выявления дефектов и выяснения возможности их устранения без изменения качества изделий.
Определение свойств и качества изделий осуществляется лабораторными, стендовыми, эксплуатационными испытаниями. При этом определяются физико-механические свойства, тепло- и морозостойкость, долговечность, сопротивление старению и истиранию.
В настоящее время выпускается большой ассортимент резиновых изделий, свойства и назначение которых определяются в основном свойствами применяемого каучука.
В зависимости от свойств и применения резины их делят на следующие группы:
резины общего назначения (шины, обувь, ремни и др.), эксплуатируемые при интервале минус 50 — плюс 110°С; такие резины изготавливаются на основе каучуков НК, СКВ, СКИ, СКС, СКМС и др.;
теплостойкие резины (детали самолетов, машин и др.), получаемые из силиконовых каучуков и фторкаучуков;
резины, устойчивые к действию низких температур, получаемые из силиконовых и фторкаучуков;
резины, устойчивые в окислительных средах, в растворах кислот, щелочей и солей и т. д.; их готовят на основе наирита, фторкаучуков, бутилкаучуков и др.;
маслостойкие резины, устойчивые к действию нефти и продуктам ее. переработки, получаемые из фторкаучуков, бутадиен- нитрильных и других каучуков.
Наряду с этими резинами находят применение газонаполненные резины, стойкие к воздействию радиации, обладающие высокими диэлектрическими свойствами.
|