|
ТКМ шпоры. 1. Исходные материалы для металлургии руда, флюсы, огнеупоры, топливо пути повышения температуры горения металлургического топлива. Дайте определения и примеры химических формул
35п
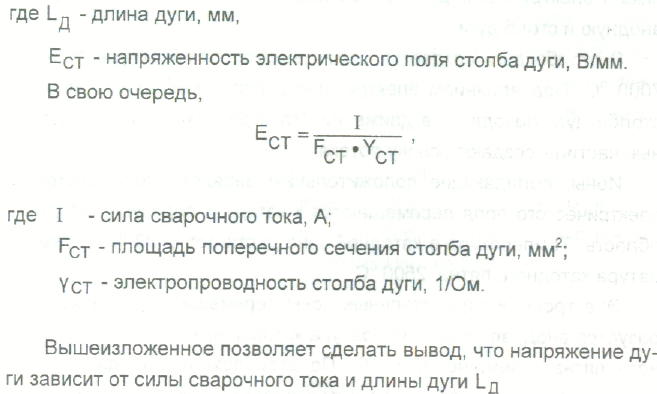
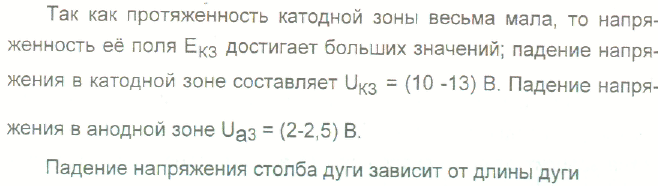
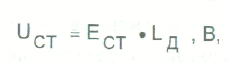
Стабильность горения дуги зависит от концентрации заряженных частиц в дуговом промежутке, которая, в свою очередь, определяется процессами ионизации (образование заряженных частиц). Основными механизмами образования заряженных частиц являются: автоэлектронная и термоэлектронная эмиссии, а также ионизация ударом, термическая ионизация, фотоэмиссия и фотоионизация.
Напряжение холостого хода источника сварочного тока должно быть достаточным для легкого зажигания сварочной дуги. Оно должно отвечать требованию
| 3пп
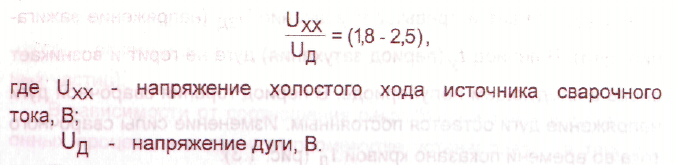

36 Распавляемое при сварке электродное покрытие кроме шлака выделяет газы, осуществляя, таким образом, газошлаковую защиту металла. В зависимости от состава покрытия или флюса может выделяться значительное количество газа и меньшее количество шлака, или наоборот. В первом случае покрытиё называют газозашитным, а во втором— шлакозащитным. Обычно применяют смешанную защиту. Металлургическая обработка металла выделяющимися при сварке шлаком и газами заключается в процессах раскисления, легирования и рафинирования металла шва.
Раскисление — это освобождение стали от кислорода, попадающего в ванну из воздуха, покрытий и других источников. В процессе сварки происходит осаждающее раскисление, при котором удаление кислорода из расплавляемого металла капли или ванпы осуществляется реакциями с другими элементами, более активно взаимодействующими с кислородом, чем железо. Удаление кислорода происходит путем восстановления железа из оксида FeO по реакциям:
При этом MnO и SiO2 переходят в шлак, а СО — в атмосферу. Процесс идет беспрерывно: окисление Fe идет в передней части ванны, где температура более высокая, а восстановление железа из оксида — в задней части, где температура более низкая. Наряду с осаждающим раскислением происходит процесс диффузионного раскисления путем реакции между оксидом железа и другими оксидами
FeO, таким образом, связывается в стойкий силикат, который переходит в шлак. При большом содержании в шлаке силиката кремния реакция может пойти в обратную сторону, и металл будет окисляться, растворяя FeO. Поэтому содержание 5Юг в шлаке должно быть в количестве, необходимом для диффузионного раскисления. Следует иметь в виду, что SiO2 делает шлак «длинным», малоподвижным и ухудшает его газопроницаемость. При необходимости добавляют в покрытие другие материалы, повышающие жидкотекучесть шлака. Из приведенных выше химических реакций видно, что раскисление металла при сварке осуществляется при введении в покрытие химических элементов-раскислителей: Mn, Si, Al, T и др. в виде порошка или ферросплавов (сплавов с железом), а также при увеличении содержания этих элементов в электродных стержнях.
Легирование металла шва различными полезными примесями для улучшения его качества осуществляется путем введения полезных элементов в электродные стержни или проволоку, а также в состав электродного покрытия. Такие элементы, как кобальт, никель и др., полностью усваиваются наплавленным металлом. Элементы Мп и Si, участвующие в раскислении, при их достаточной концентрации в шлаке в электродном металле также частично усваиваются, переходя в сварной шов.
| 36п Рафинирование металла шва заключается в освобождении его от вредных примесей, главным образом от серы и фосфора, которые попадают в ванну из основного металла, электродного стержня и покрытия, проволоки и флюса. Сера может остаться в шве в виде сульфида железа FeS, располагаясь между кристаллами стали. Это приводит к появлению горячих трещин в стали (см. § 9.7). Фосфор, находясь в шве в виде фосфидов Fe3P H^Fe2P, снижает его ударную вязкбсть, особенно при низкой температуре, поэтому удаление из шва серы и фосфора необходимо. Это осуществляется путем связывания серы и фосфора в химические соединения, не растворимые в стали и удаляемые в шлак, по реакциям:
37 . сварочные проволки
При содержании в проволоке менее 1% легирующих элементов ставят только букву этого элемента, если содержание легирующего элемента превышает 1%, то после буквы в целых единицах указывают содержание этого элемента.
Условные обозначения марок проволоки состоят: из индекса Св-сварочная и следующих за ним цифр, показывающих содержание углерода в сотых долях процента и буквенных обозначений элементов, Входящих в состав проволоки. Буква А в конце условных обозначений марок низкоуглеродистой и легированной проволоки указывает на повышенную чистоту металла по содержанию серы и фосфора.
Например, условное обозначение проволоки диаметром 2 мм из низкоуглеродистой кремнемарганцевой стали, содержащего 1.4 -1.7 Mn и 0.60-0.85 Si, 2Св-08ГС.
По виду поверхности низкоуглеродистая и легированная проволока подразделяется на неомедненную и омедненную. Последняя поставляется по особому требованию заказчика. Кроме того, по особому требованию заказчика изготовляют проволоку из стали, выплавленной электрошлаковым, вакуум-дуговым или вакуум-индукционным методом.
Различные виды проволоки имеют условное обозначение:
Э- для изготовления электродов;
О-омедненная;
Ш-полученная из стали, выплавленной электрошлаковым переплавом;
Вд-полученная из стали выплавленной вакуум-дуговым переплавом;
ВИ-полученная из стали, выплавленной в вакуум-индукционной печи.
Поверхность проволоки должна быть чистой без окалины, ржавчины, грязи и масла. Предусматривается выпуск проволоки следующих диаметров, мм: 0.3; 0.5; 0.8; 1.0; 1.2; 1.4; 1.6; 2.0; 3.0; 4.0; 5.0;6.0; 8.0; 10.0; 12.0.
Классификация электродов. Электроды классифицируются по следующим признакам:
по материалу, из которого они изготовлены;
по назначению для сварки определенных сталей;
по толщине покрытия, нанесенного на стержень;
по видам покрытия;
характеру шлака образующегося при расплавлении покрытия;
техническим свойствам металла шва;
по допустимым пространственным положениям сварки или плавки;
по роду и полярности применяемого при сварке или наплавке тока.
Применение электродов должно обеспечивать следующие необходимые технические условия: легкое зажигание и устойчивое горение дуги, равномерное расплавление покрытия, равномерное покрытие шва шлаком, легкое удаление шлака после сварки, отсутствие непроваров, пор, трещин в металле шва.
| 37п Электроды подразделяются на группы в зависимости от свариваемых материалов: углеродистых и низкоуглеродистых конструкционных сталей-У ( условное обозначение); легированных конструкционных сталей-Л; легированных теплоустойчивых сталей-Т; высоколегированных сталей с особыми свойствами-В; для наплавки поверхностных слоев с особыми свойствами -Н.
По видам покрытия электроды подразделяются:
А - с кислым покрытием, содержащим окислы железа, марганца, кремния, иногда титана. Металл шва отличается повышенной окисленностью, плотностью и позволяет выполнять сварку на постоянном ( прямой и обратной полярности) и переменном токе;
Б - с основным покрытием, имеющим в качестве основы фтористый кальций (плавиковый шпат) и карбонат кальция (мрамор, мел). Сварку электродами с основным покрытием осуществляют на постоянном токе при обратной полярности. Вследствие малой склонности металла шва к образованию кристаллизационных и холодны трещин электроды с этим покрытием используют для сварки больших сечений;
Ц - с целлюлозным покрытием, основные компоненты которых- целлюлоза, мука и другие органические составы, создающие газовую защиту дуги и образующие при плавлении тонкий шлак. Электроды с целлюлозным покрытием применяют, как правило, для сварки стали малой толщины;
Р - с рутиловым покрытием, основной компонент которых-рутил (TiO2). Для шлаковых и газовой защиты в покрытия этого типа вводят соответствующие минеральные и органические компоненты, а для повышения производительности иногда добавляют железный порошок. При сварке на постоянном токе разбрызгивание металла незначительно. Устойчивость горения дуги высокая, формирование швов во всех пространственных положениях хорошее.
П - прочие виды покрытий.
При покрытии смешанного вида используют соответствующее двойное условие обозначение.
Условное обозначение электродов для сварки конструкционных сталей состоит из обозначения марки электрода, его типа, диаметра стержня, типа покрытия и номера ГОСТа. Например обозначение электрода Э46А - УОНИИ-13/45-3.0-УД2 Е432(5)-Б10 ГОСТ 9467-75. При сварке под плавлеными флюсами защита зоны сварки от окружающего воздуха происходит более эффективно. Это доказано исследованием содержания азота в металле шва. Например, при сварке тонкопокрытыми электродами остаточный азот составляет около 0,2%; при сварке толстопокрытыми электродами - 0,03; при сварке под плавленым флюсом - 0,008%.
Имеется ряд особенностей металлургических процессов при сварке под флюсом. Особенно интенсивно протекают металлургические процессы между жидким (расплавленным) флюсом и металлом, в результате чего изменяется состав металла шва. Сварку низкоуглеродистых сталей рекомендуется проводить под марганцовистыми высококремнистыми флюсами, где наблюдается процесс восстановления кремния и марганца, частичное окисление углерода, при этом оксид железа растворяется в жидком металле шва, частично переходит в шлак.
На участках сварочной ванны позади дуги при охлаждении жидкого металла, вплоть до затвердевания, продолжается раскисление металла. Кремний и марганец подавляют реакцию окисления углерода, что уменьшает образование пор. Обогащение металла марганцем очень важно, так как он обеспечивает вывод сернистых соединений из металла шва, предупреждая тем самым появление горячих трещин.
Изменение режима сварки влияет на содержание серы и фосфора в шве. При увеличении сварочного тока увеличивается количество расплавленного флюса и, как следствие, содержание фосфора в шве уменьшается, а содержание серы несколько возрастает. Повышение напряжения дуги при неизменном токе приводит к тому, что расплавленного флюса становится значительно больше, чем требуется для защиты расплавленного металла. В этом случае увеличивается переход марганца и кремния в шов, но увеличивается и переход фосфора в металл шва.
| 37пп Одновременносодержание серы в металле шва уменьшается. Таким образом, невозможно идеально освободиться от вредных примесей. Улучшения качества сварного шва можно добиться за счет применения керамических флюсов.
Керамические флюсы содержат большое количество ферросплавов, что позволяет улучшить металлургические процессы при сварке. В процессе сварки происходит более полное раскисление наплавленного металла, легирование наплавленного металла осуществляется в широких пределах. Для улучшения структуры сварных швов в металл шва вводят специальные добавки (модификаторы). Металлургические процессы при сварке в защитных газах значительно отличаются от ранее рассмотренных. Из защитных газов наибольшее применение имеют инертные - аргон, гелий и активный - углекислый газ.
При сварке в инертных газах металлургические процессы протекают только между элементами, содержащимися в металле сварочной ванны. Кислород и азот воздуха оттесняются инертными газами из зоны сварки.
Для предотвращения образования пористости шва при сварке в инертных газах необходимо тщательно удалять ржавчину и загрязнения с кромок основного металла и с поверхности сварочной проволоки.
При сварке в С02 газ оттесняет от сварочной зоны окружающий воздух и защищает расплавленный металл от проникновения азота. При сварке С02 углекислый газ распадается под воздействием высокой температуры на СО и 02. Дуга активно окисляет металл сварочной ванны, и роль СО2 сводится лишь к защите сварочной ванны от проникновения азота из воздуха. Для предотвращения чрезмерного окисления железа большое количество элементов раскислителей (марганец и кремний) вводится в сварочную ванну только через сварочную проволоку Се-08ГС и Св-08Г2С. В этом случае наплавленный металл получается с высокими механическими свойствами.
Для уменьшения содержания водорода в металле шва необходима добавка в углекислый газ 5-15% кислорода. При этом в процессе сварки увеличивается глубина противления, так как энергичнее протекают реакции окисления марганца и кремния с выделением теплоты.
| 38 При конструировании сварных изделий необходимо учитывать, что в процессе сварки возникают сварочные напряжения, в результате которых происходит коробление элементов конструкций, могут возникать горячие и холодные трещины в металле сварного шва и околошовной зоны. По этой причине при выполнении сварочных и наплавочных работ необходимо правильно выбирать оптимальные режимы сварки.
Сварочная дуга является концентрированным источником тепловой энергии, полную тепловую мощность можно посчитать по формуле
Q = U I, дж/с,
где Q - полная тепловая мощность, Дж/с; U - напряжение, В; I - сила сварочного тока, А.
Однако не вся тепловая энергия вводится в плавящийся электрод и свариваемый металл; часть ее теряется в окружающей среде.
Тепловая мощность, которая полезно используется при сварке, называется эффективной тепловой мощностью и рассчитывается по формуле
Q(эф)=ήUI Дж/с
где ή - коэффициент полезного использования тепловой энергии.
ή = 0,75 при ручной дуговой сварке, ή. = 0,85 при автоматической сварке под флюсом.
Тепловая энергия вводимая в единицу длины сварного шва, называется погонной энергией и зависит от двух параметров: эффективной тепловой мощности и скорости сварки. Она подсчитывается по формуле
Qпог = Q(эф)/V(св)
где Qпог " погонная энергия, Дж/м;
QЭф - эффективная тепловая мощность, Дж/с; \/св - скорость сварки, м/с,
Причины возникновения напряжений в сварных конструкциях следующие:
-неравномерность нагрева металла,
-фазовые (структурные) превращения, происходящие в сварном шве и околошовной зоне.
Неравномерный нагрев и изменение объема металла вследствие температурного расширения, фазовых превращений, структурных превращений приводят к возникновению упругих и пластических деформаций. В результате пластических деформаций остаются напряжения, которые называются остаточными напряжениями. Это может привести как к короблению сварной конструкции, так и возникновению сварочных трещин. Мерами по предотвращению возникновения напряжений и, как следствие, деформаций являются следующие мероприятия.
Холодные трещины — локальное межкристаллическое разрушение металла сварных соединений, возникающие под действием собственных сварочных напряжений. Формальными признаками холодных трещин, отличающими их от горячих, являются факт обнаружения трещин при визуальном наблюдении, как правило, после полного охлаждения сварного соединения и блестящий излом без следов высокотемпературного окисления.
Горячие трещины при сварке — хрупкие межкристаллические разрушения металла шва и зоны термического влияния, возникающие в твёрдо-жидком состоянии при завершении кристаллизации, а также в твёрдом состоянии при высоких температурах на этапе преимущественного развития межзёренной деформации. Они могут возникать при неблагоприятном сочетании некоторых факторов, связанных с понижением деформационной способности металла вследствие наличия в структуре легкоплавких эвтектик, дефектов кристаллического строения, выделения хрупких фаз, включения водорода (водородная болезнь) и т. д.
| |
|
|