|
ТКМ шпоры. 1. Исходные материалы для металлургии руда, флюсы, огнеупоры, топливо пути повышения температуры горения металлургического топлива. Дайте определения и примеры химических формул
39 . КОНТАКТНАЯ СВАРКА
Контактная сварка относится к видам сварки с кратковременным нагревом места соединения без оплавления или с оплавлением и осадкой разогретых заготовок. Характерная особенность этих процессов — пластическая деформация, в ходе которой формируется сварное соединение.
Место соединения разогревается проходящим по металлу электрическим током, причем максимальное количество теплоты выделяется в месте сварочного контакта (рис. 5.24). Количество выделяемой теплоты определяется законом Джоуля — Ленца:
Q=I2Rt
где Q — количество теплоты, выделяемое в сварочном контуре, Дж; R — полное электросопротивление сварочного контура, Ом; I — сварочный ток, А; t — время протекания тока, с.
Полное электросопротивление сварочного контура R состоит из электросопротивлений выступающих концов L, свариваемых заготовок Rзаг, сварочного контакта Rк и электросопротивления между электродами и заготовками Яэл, т. е,
R=Rзаг+Rн+Rэл
Контактную сварку классифицируют по типу сварного соединения, определяющего вид сварочной машины, и по роду тока, питающего сварочный трансформатор. По типу сварного соединения различают сварку стыковую, точечную и шовную. Стыковая сварка — разновидность контактной сварки, при которой заготовки свариваются по всей поверхности соприкосновения. Свариваемые заготовки закрепляют в зажимах стыковой машины (рис. 5.26). Зажим 3 установлен на подвижной плите 4, перемещающейся в направляющих, зажим 2 укреплен на неподвижной плите 1. Сварочный трансформатор соединен с плитами гибкими шинами и питается от сети через включающее устройство. Плиты перемещаются, и заготовки сжимаются под действием усилия Р,развиваемого механизмом осадки,
Точечная сварка — разновидность контактной сварки, при которой заготовки соединяются в отдельных точках. При точечной сварке заготовки собирают внахлестку и зажимают с усилием Р между двумя электродами, подводящими ток к месту сварки (рис. 5.31). Соприкасающиеся с медными электродами поверхности свариваемых заготовок нагреваются медленнее их внутренних слоев. Нагрев продолжают до пластического состояния внешних слоев и до расплавления внутренних слоев. Затем выключают ток и снимают давление. В результате образуется литая сварная точка.
Точечная сварка в зависимости от расположения электродов по отношению к свариваемым заготовкам может быть двусторонней и односторонней. При двусторонней сварке (рис. 5.31, а) две (или больше) заготовки 1 сжимают между электродами 2 точечной машины. При односторонней сварке (рис. 5.31, б) ток распределяется между верхним и нижним листами 3 и 4, причем нагрев осуществляется частью тока, протекающего через нижний лист. Для увеличения тока, проходящего через нижний лист, предусмотрена медная подкладка 5. Односторонней сваркой можно соединять заготовки одновременно двумя точками. Параметры режима точечной сварки: удельное усилие сжатия, МПа; плотность тока j, А/мм2; время протекания тока t, с.
| 39п Шовная сварка — разновидность контактной сварки, при которой между свариваемыми заготовками образуется прочное и плотное соединение. Электроды выполняют в виде плоских роликов, между которыми пропускают свариваемые заготовки.
В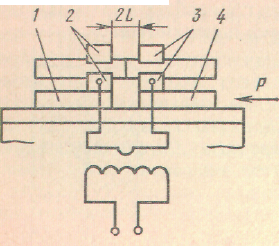 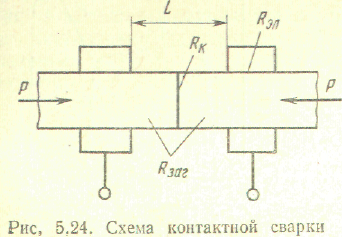 процессе шовной сварки листовые заготовки 1 соединяют внахлестку, зажимают между электродами 2 (рис. 5.35) и пропускают ток. При движении роликов по заготовкам образуются перекрывающие друг друга сварные точки, в результате чего получается сплошной герметичный шов. Шовную сварку, так же как и точечную, можно выполнить при двустороннем а и одностороннем б расположениях электродов.
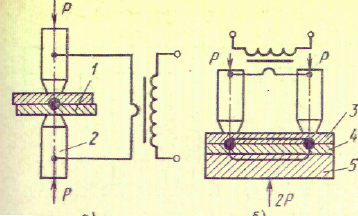
| 40 СУЩНОСТЬ ПРОЦЕССА И МАТЕРИАЛЫ ДЛЯ ПАЙКИ
Пайкой называется процесс получения неразъемного соединения заготовок с нагревом ниже температуры их автономного расплавления путем смачивания, растекания и заполнения зазора между ними расплавленным припоем и сцепления их при кристаллизации шва. Образование соединения без расплавления основного металла обеспечивает возможность распая изделия.
По прочности паяные соединения уступают сварным. Паять можно углеродистые и легированные стали всех марок, твердые сплавы, цветные металлы, серые и ковкие чугуны. При пайке металлы соединяются в результате смачивания и растекания жидкого припоя по нагретым поверхностям и затвердевания его после охлаждения,Прочность сцепления припоя с соединяемыми поверхностями зависит от физико-химических и диффузионных процессов, протекающих между припоем и основным металлом.
По условию заполнения зазора пайку можно разделить на капиллярную и некапиллярную. По механизму образования шва капиллярная пайка подразделяется на пайку с готовым припоем, когда затвердевание шва происходит при охлаждении; контактно-реактивную пайку; реактивно-флюсовую; диффузионную. К некапиллярным способам относятся пайка-сварка и сварка-пайка.
При капиллярной пайке припой заполняет зазор между соединяемыми поверхностями и удерживается в нем за счет капиллярных сил. Соединение образуется за счет растворения основы в жидком припое и последующей кристаллизации раствора. Капиллярную пайку используют при соединении внахлестку.
При диффузионной пайке соединение образуется за счет взаимной диффузии компонентов припоя и паяемых материалов, причем возможно образование в шве твердого раствора или тугоплавких хрупких интерметаллидов. Для диффузионной пайки необходима продолжительная выдержка при температуре образования паяного шва и после завершения процесса —при температуре ниже солидуса
припоя.
При контактно-реактивной пайке между соединяемыми металлами или соединяемыми металлами и прослойкой промежуточного металла в результате контактного плавления образуется сплав, который заполняет зазор и при кристаллизации образует паяное соединение При реактивно-флюсовой пайке припой образуется за счет реакции вытеснения между основным металлом и флюсом. Реактивно-флюсоую пайку можно вести без припоя и с припоем.
При пайке-сварке соединение образуется так же, как при сварке плавлением, но в качестве присадочного металла применяют
припой
При сварке-пайке соединяют разнородные материалы с применением местного нагрева, при котором более легкоплавкий материал нагревается до температуры плавления и выполняет роль
припоя.
Наибольшее применение получили капиллярная пайка а пайка-сварка. Диффузионная и контактно-реактивная пайки более трудоемки, но обеспечивают высокое качество соединения.
Припой —должен хорошо растворять основной металл, обладать смачивающей способностью, быть дешевым и недефицитным.
Припои представляют собой сплавы цветных металлов сложного состава. Все припои по температуре плавления подразделяют на особо легкоплавкие (температура плавления меньше145 °С), легкоплавкие (температура плавления 145< 450 °С), среднеплавкие (температура плавления 450 <1100°С) и тугоплавкие (температура плавления >1050°С).
|
40п К особолегкоплавким и легкоплавким припоям относятся оловянно-свинцовые, на основе висмута, индия, кадмия, цинка, олова, свинца. К среднеплавким и высокоплавким припоям относятся медные, медно-цинковые, медно-никелевые, с благородными металлами (серебром, золотом, платиной). Припои изготовляют в виде прутков, проволок, листов, полос, спиралей, дисков, колец> зерен и т, д., укладываемых в место соединения.
Изделия из алюминия и его сплавов паяют с припоями на алюминиевой основе с кремнием, медью, оловом и другими металлами. Магний и его сплавы паяют припоями на основе магния с добавками алюминия, меди, марганца и цинка. Изделия из коррозионно-стойких сталей и жаропрочных сплавов, работающих при высоких температурах (выше 500 °С), паяют тугоплавкими припоями на основе железа, марганца, никеля, кобальта, титана, циркония, гафния, ниобия и палладия.
Флюсы паяльные применяют для очистки поверхности паяемого металла, а также для снижения поверхностного натяжения и улучшения растекания и смачиваемости жидкого припоя. Флюс (кроме реактивно-флюсовой пайки) не должен химически взаимодействовать с припоем. Температура плавления флюса должна быть ниже температуры плавления припоя. Флюс в расплавленном и газообразном состояниях должен способствовать смачиванию поверхности основного металла расплавленным припоем.
10. ГАЗОВАЯ СВАРКА
При сварке место соединения нагревают до расплавления высокотемпературным газовым пламенем (рис. 5.17). При нагреве газосварочным пламенем 4 кромки свариваемых заготовок 1 расплавляются, а зазор между ними заполняется присадочным металлом 2, который вводят в пламя горелки 3 извне. Газовое пламя получают при сгорании горючего газа в атмосфере технически чистого кислорода.
| 41 Обр. металлов резанием – процесс срезания режущим инструментом с поверхности заготовки слоя металла для получения требуемой геометрич формы, точности размеров и шероховатости поверхности детали.
Сущность метода пласт деформ-я: поверхностные слои металла, контактируя с инструментом высокой твердости, в результате давления оказываются в состоянии всестороннего сжатия и пластически деформируются. Давление осуществляется только по зоне контакта. Инструмент – ролики и шарики, перемещающиеся относительно заготовки.
Электроэрозионный метод основан на явлении эрозии(разрушния) электродов из токопроводящих материалов при пропускании между ними импульсного Эл тока. Температура на поверхности обрабатываемой заготовки-электрода возрастает до 10000-12000 С. При этой температуре мгновенно испаряется элементарный объем металла.
Эл/химические методы основаны на явлении анодного растворения при электролизе. При прохождении пост Эл тока ч/з электролит на пов-ти заготовки, являющейся анодом происходят хим реакции и поверхностный слой, превращаясь в хим соединение, уходит в раствор или удаляются механически.
Ультразвук-е методы. УЗО – разновидность механич обработки Основана на явлении магнитострикции(способность ферромагнитных сплавов или металлов изменять размеры в переменном магнитном поле). Колебании Эл/м поля при УЗО 16-20кГц, амплитуда колебаний сердечника 5-10мкм(со стержнем-концентратором до 40-60мкм). К концентратору крепят рабочий инструмент - пуассон.
Лучевые методы. Электронно-лучевая(метод основан на превращении кинетич энергии пучка в тепловую. Под дейтвием высокой температуры происхдит испарение металла с поверхности заготовки). Лазерная обраб-ка(тепловое воздействие светового луча высокой энергии). Плазменный(плазму, имеющюю температуру 10000-30000 С направляют на обрабатываемую поверхность заготовки).
42 Обр. металлов резанием – процесс срезания режущим инструментом с поверхности заготовки слоя металла для получения требуемой геометрич формы, точности размеров и шероховатости поверхности детали.
Скорость резания–путь точки режущего лезвия инструмента относительно заготовки в направлении главного движения резания за единицу времени. Измеряют в м/мин, кроме шлифования, полировки и некоторых др видах обраб резанием, где ее измеряют в м/с.
Подача s – путь точки лезвия режущего инструмента относительно заготовки в направлении движения подачи за оборот или за двойной ход заготовки или инструмента. мм/об – сверление, точение; мм/дв. хода – строгание, долбление; мм/мин – фрезерование и т.д. Подачи: продольная, поперечная, вертикальная, наклонная, круговая, тангенциальная, окружная и т.д.
Глубина резания t – расстояние между обрабатываемой и обработанной поверхностью заготовки, измеренное перпендикулярно последней, за один рабочий ход инструмента относительно обраб-емой пов-ти.
Основное технологическое время – время, затрачиваемое непосредственно на процесс изменения формы и размеров заготовки и получения пов-ти требуемой шероховатости.
[При токарной T0=(L*i)/(nsпр)]
Главное движение резания Dr – прямолинейное поступательное или вращательное движение заготовки или режущего инструмента, происходящее с наибольшей скоростью и в процессе резания; движение подачи Ds – прямолинейное поступательное или вращательное движение режущего инструмента или заготовки; касательное движение Dк – прямолинейное поступательное или вращательное движение режущего инструмента; результирующее движение резания De – суммарное движение режущего инструмента относительно заготовки, включающее главное движение резания, движение подачи и касательное движение.
| 43 Образование поверхностей по методу копирования заключатся в том, что форма режущего лезвия инструмента является образующей линией, совпадающей по форме с образующей линией поверхности, или имеющей форму, обратную ей. Направляющая лиия воспроизводится вращением заготовки или поступательным движением инструмента. это формообразующее движение. Второе движение, направленное перпендикулярно пов –ти необходимо для получения определенного размера поверхности.
Образование поверхностей по методу следов заключатся в том, что образующая линия является траекторией движения точки(вершины) режущего лезвия инструмента, а направляющая линия – траектория движения точек заготовки. Оба движения формообразующие.
Образование поверхностей по методу касания заключатся в том, что направляющей линией служит касательная к ряду геометрических вспомогательных линий, являющихся траекториями движения точек режущего инструмента. Образующей линией служит режущее лезвие инструмента. Формообраз движение – подача sпр.
Образование поверхностей по методу обкатки заключатся в том, что образующая линия является огибающей кривой ряда последовательных положений режущего лезвия инструмента в результате двух согласованных относительных движений заготовки и инструмента. Направляющая линия образуется поступательным движением инструмента.
44 Схема: Движущийся резец под действием силы Р вдавливается в металл, в металле возникают упругие деформации. При дальнейшем движении резца упругие деф-ции переходят в пластические. Пластические деформации приводят к сдвиговым. Сдвиговые деформации вызываю скольжение отдельных частей зерен по кристаллографическим плоскостям(плоскостям скольжения) в определенных направлениях. Когда пластические деформации достигают наибольшей величины, а напряжения превысят силы внутреннего сцепления зерен металла, скалывается элементарный объем металла.
Виды стружек: 1) Сливная стружка образуется при резании пластичных металлов и сплавов и представляет собой сплошную ленту с гладкой внутренней(прирезцовой) стороной. С внешней стороны слабо выраженные зазубрины.
2) Стружка скалывания образуется при резании средних по твердости материалов. Гладкая c внутренней стороны и с явно выраженным зазубринами с наружней.
3) Стружка надлома образуется при обработке хрупких металлов, состоит из отдельных элементов, не связанных между собой.
Для получения стружки надлома на режущем инструменте выполняют стружкозавивательные и стружколомательные устройства, применяют прерывистый процесс резания,измняют геометрию режущего инструмента, режим резания, а при мизготовлении деталей на автоматах используют специальные автоматные стали.
| |
|
|