|
Госник. 1. Устройство и принцип работы турбобура. Характеристика турбобурдолотозабой. Определение момента затяжки деталей
Электролитическое осталивание
При прохождении пост тока низкого напряжения ч/з раствор солей железа происходит осаждение на катоде электролитического железа. Прочность и твердость осаждаемого слоя приближается к свойствам углеродной стали, поэтому процесс назвали осталиванием. Для электролит-ого осталивания прмен-ся несколько типов электролитов: хлористые, бор-хлористо-водородные на основе железа. Для осталивания примен холодные и горячие электролиты. Аноды изготовляются из малоуглерод стали. Для приготовления электролит очищают, загружают в раствор НСL c дистиллированной водой. Затемзасыпают остальные соли. И после осталивания 12…18 ч фильтруют и корректируют кислотность и содержание железа. Введение хлористого натрия обеспечивает снижение напряжения, уменьшение испарения электролита и повыш твердость покрытия. А введение хлористого марганца - увеличивает сцепление.
В зависимости от состава электролита и режима осталивания получают мягкие покрытия с твердостью, соответствующей углеродистой незакаленной стали (НВ 120-220), и твердые покрытия с твердостью, соответствующей закаленной стали (НВ 250-600).
Преимущества: исходные материалы, входящие в состав электролита, дешевы; выход металла по току составляет 75…95%; скорость осаждения металла и толщина покрытия значительно выше, чем при хромировании; механическую обработку покрытия после осталивания производят при обычных режимах резания; процесс осталивания легко регулируется и может быть автоматизирован.
Недостатки:высокая коррозионная активность электролита; сложность техпроцесса; необходим-ть частой фильтрации электролита.
Электролитическое меднение.
Для меднения деталей применяют электролиты двух типов: сернокислые и цианистые.
Электролитическое никелирование.
Электролитический процесс осаждения никеля называется твердым никелированием.
66. Поверхностное упрочнение деталей. Выбор метода поверхностного упрочнения.
Под упрочнением понимается повышение сопротивляемости материала или заготовки разрушению или остаточной деформации.
При обработке поверхности шлифованием и полированием, устраняющей неровности, которые служат концентраторами напряжений, повышается усталостная прочность детали. Поверхности деталей дополнительно упрочняют более эффективными методами упрочняющей обработки: термической, химико-термической, электроискровой, пластическим деформированием и нанесением износостойких материалов.
Назначение метода упрочняющей обработки зависит от условий работы детали в машине и ее технологических особенностей.
Термическая обработка. Поверхностная закалка — один из видов упрочняющей термической обработки стальных и чугунных деталей. Закалка позволяет значительно повысить прочность и износостойкость деталей. Прочность углеродистой стали можно увеличить обычной закалкой и отпуском в 1,5—2 раза, а легированной стали даже в 2—3 раза.
Поверхностная закалка с нагревом токами высокой частоты основана на использовании явлений индукции и поверхностного эффекта. Деталь помещают внутри спирали (индуктора) или под проводником, по которому пропускается переменный ток большой частоты; он вызывает появление вихревых токов на поверхности детали, и быстро разогревает слой с наибольшей плотностью индуцированного тока. По достижении заданной температуры нагрева деталь интенсивно охлаждают струей жидкости. Имеющая небольшое применение в промышленности поверхностная закалка в электролите заключается в нагреве детали (катода), помещенной в электролит, через который пропускается постоянный ток высокого напряжения. Закалка осуществляется опусканием детали в специальную ванну или в струе электролита при выключенном токе, а также при помощи специального спрейера.
Упрочняющая химико-термическая обработка (ХТО) — это процесс диффузионного насыщения поверхностного слоя металлических деталей активными элементами, обеспечивающими получение определенных физико-механических свойств для повышения твердости, усталостной прочности, износостойкости, жаростойкости и коррозионной стойкости.
Цементация — процесс науглероживания поверхностного слоя стальных деталей, нагретых до температуры свыше 900—940° С, что определяет наибольшую скорость протекания процесса
Детали после цементации и последующей закалки имеют повышенную твердость (HRC58—62) и прочность поверхностного слоя. Цементация повышает усталостную прочность деталей, благодаря увеличению твердости, прочности цементированного слоя и образованию в нем внутренних напряжений сжатия, которые снижают влияние концентраторов напряжений.
Азотирование— один из процессов химико-термической обработки, при котором поверхностные слои насыщаются расплавленными серосодержащими солями или в газовых средах. Его можно применять для обработки деталей нефтегазопромыслового оборудования, так как при этом способе облегчаются и доводочные операции.
Цинкование - процесс насыщ цинком. Детали погружаюти в расплавленный цинк или порошок цинка.
Упрочняющая электроискровая обработка (ЭИО) основана на протекании импульсного разряда между электродом (анодом) и деталью (катодом).Сущность ЭИО заключается в полярном переносе материала электрода на деталь (наращивание) при одновременном термическом воздействии тока и легировании поверхности детали элементами упрочняющего электрода и азота воздуха. Упрочненный слой отличается высокой твердостью, обусловленной образованием карбидов, нитридов, карбонитридов и закалочных структур. Электроискровое упрочнение и нанесение металла происходит в воздушной или газовой среде при тепловом и химическом действии электрического разряда между поверхностью изделия и упрочняющим электродом, которому сообщается колебательное движение от вибратора. За очень короткое время электроискрового разряда (105 — 108 с) через электроды проходит мощный (до 106 А/мм2) импульс тока, накопленного в конденсаторах. Температура в межэлектродном зазоре повышается до 11 000° С. При такой температуре азот и легирующие элементы, содержащиеся в электроде, легируют поверхность детали, повышая ее физико-механические свойства.
Недостаток метода: невозможность получения упрочненного слоя значительной толщины и снижение усталостной прочности. Упрочняющую обработку поверхностным пластическим деформированием (ППД) применяют в основном для повышения усталостной прочности деталей.
Поверхностный наклеп (ПН) представляет собой поверхностное пластическое деформирование с изменением структуры материала без его полной рекристаллизации. Пластическая деформация приводит к измельчению зерен и уменьшению их размеров, создает текстуру. Обработка дробью – пластич деформирование под действием кинетическ энергии потока дроби. При этом повышается твердость, предел выносливости. Раскатывание применяют для упрочняющей обработки вогнутых поверхностей деталей из стали, чугуна и цветных металлов. Гидроабразивная – струя жид-ти, содержащая абразивный материал выбрасывается со скоростью 50…70м/с.при этом методе снимается верхний слой и пластич деформируются нежележащ слои.
Упрочняющая чеканка – основана на ударном воздействии бойков на обрабатываемую пов-ть, в результате происходит наклеп.
Термомеханич обработка – сочетание операций термо и мех обработок. Для осущест-я использ-ся прокатное, волочильное, ковочное, и штампов-е оборудов-е. Для закалки устанавл охлажд устройство. Эффективным методом поверхностного упрочнения деталей машин является наплавка материалов с высокими эксплуатационными свойствами. Этот метод экономичен, так как наплавке подвергают только те поверхности, которые работают в условиях интенсивного изнашивания и, как правило, масса наплавленного материала составляет малую долю от массы детали.Долговечность упрочненных деталей определяется свойствами наплавленного материала, поэтому наносимый материал или сплав выбирают с учетом условий эксплуатации детали и применяемого метода наплавки. Большое применение имеют следующие группы наплавочных материалов: 1) стали, легированные марганцем, хромом, никелем, вольфрамом, молибденом; 2) сплавы на основе железа — высокохромистые, вольфрамовые, молибденовые, чугуны, а также сплавы с высоким содержанием хрома, вольфрама, кобальта, молибдена; 3) сплавы на основе вольфрама, кобальта, никеля.
67. Ремонт поверхностей деталей. Способ дополнительных ремонтных деталей, способ замены части де-тали. Ремонт корпусных деталей.
Способы восстановления поверхностей деталей
А) С изменением первоначальных размеров ремонтируемых дет (способ ремонтных размеров)
Б) с восстановление первоначальных размеров дет
Выбор метода наращивания определяется
1 материала и конструкции дет 2 характером дефектов 3 назначением и режимом работы детали, при этом полностью восстанавливается ресурс
1) способ наращивания доп слоя материала
2) способ доп ремонтных дет
Эти установки устанавливаются на изношенные поверхности при этом толщина износа значительно превышает величину износа ремонтируемых дет.
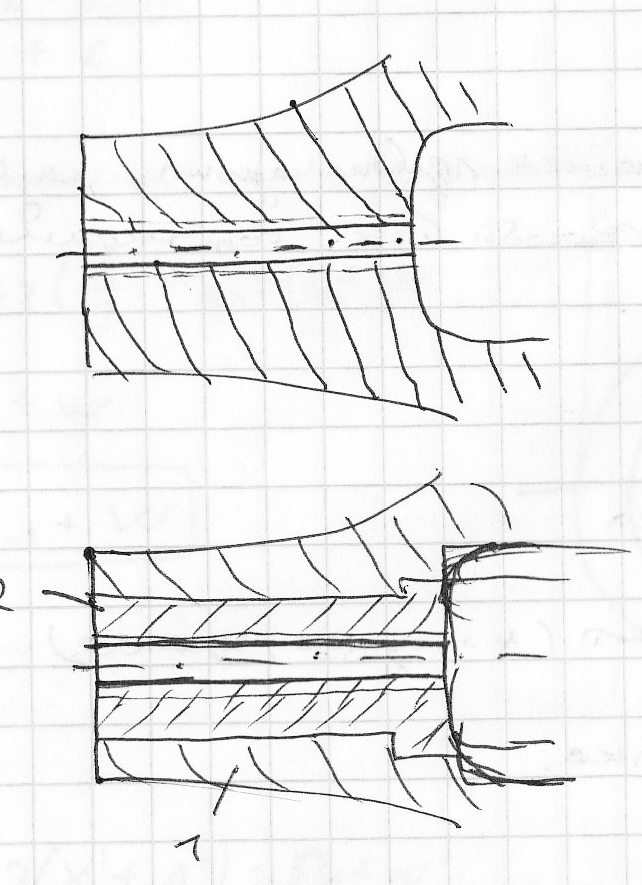
3) способ замены части детали
Удлиняется изношенная часть дет, присоединяется новая.
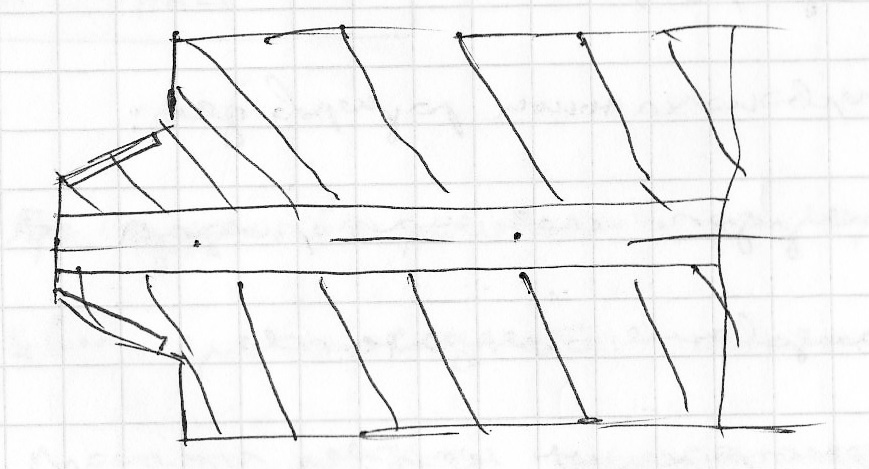
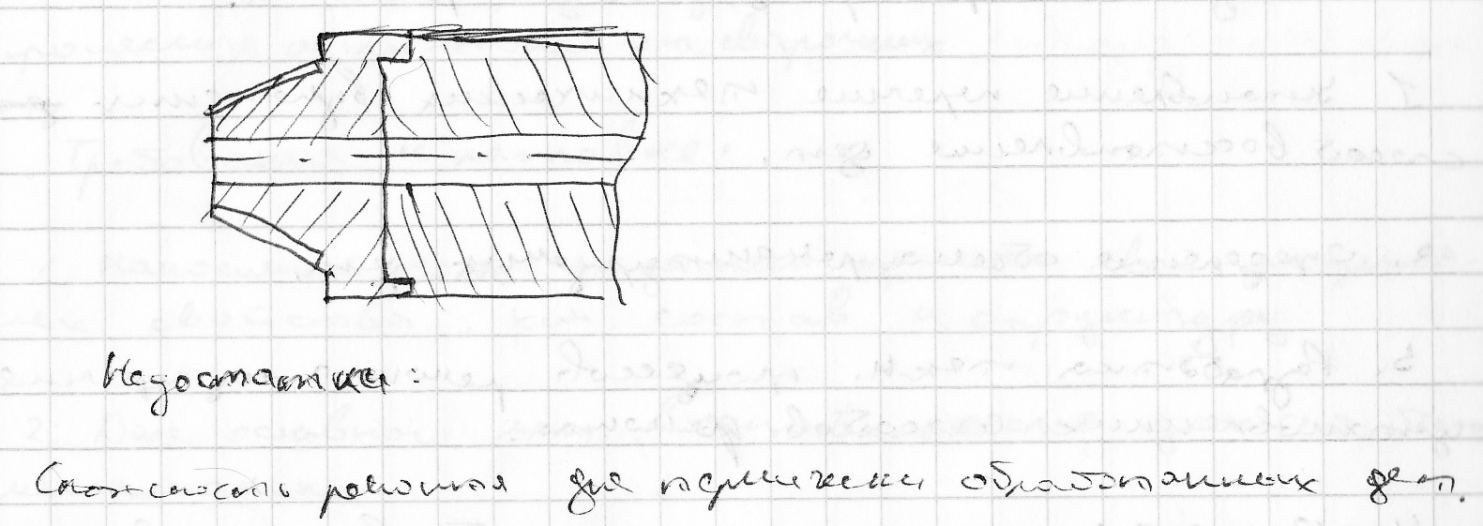
Метод дополнительных деталей, являющийся разновидностью метода ремонтных размеров, широко распространен при восстановлении под ремонтный размер цилиндров блоков, прошедших последний ремонтный размер, гнезд клапанов, посадочных отверстий под подшипники коробок передач, задних мостов. Метод предусматривает замену изношенной части детали дополнительной, специально для этой цели изготовленной. Наиболее часто таким образом ремонтируют отверстия деталей. В ступицу шкива, шестерни или другой детали, предварительно расточенную до некоторого размера, запрессовывают ремонтную втулку или гильзу.
Если в ступице имеется отверстие для смазки, то запрессованную деталь по торцу прихватывают сваркой в нескольких точках или фиксируют резьбовыми штифтами. После этого втулку растачивают под требуемый размер, сверлят отверстие для смазки и прорубают смазочные канавки.
Для восстановления резьбовых отверстий применяют резьбовые втулки (ввертыши), в которых после установки на место нарезают резьбу номинального шага.
Изношенные участки плоских поверхностей деталей ремонтируют установкой накладок и планок. При этом дефектные участки строгают или фрезеруют, затем из полосовой стали изготовляют и тщательно подгоняют накладки. Их закрепляют винтами или сваркой и обрабатывают вровень с неизношенными поверхностями детали. Способ дополнительных деталей прост и экономичен, так как позволяет сохранить и использовать оставшуюся неизношенной работоспособную часть детали.
Способы ремонта корпусных деталей.
Ремонт базовых корпусных деталей является очень ответственным процессом, так как корпус в большинстве случаев несет не только защитную функцию от внешних факторов, которые могут повлиять на работу механизма, но также являлся и базовой опорой для расположенного внутри механизма. При обнаружении каких-либо дефектов, трещин или сколов на корпусе, следует немедленно провести полную диагностику всего аппарата чтобы оценить степень риска его дальнейшего использования и, в кратчайшие сроки восстановить первоначальный вид корпуса.
Ликвидация трещин: С помощью стяжек. С помощью штифтов. С помощью накладок Заваркой с последующей механической обработкой (при необходимости).
Ремонт пробоин и сколов производят:: Установкой ввертыша. Установкой пробки. Установкой вставки. Заваркой пробоин наплавкой сколов с последующей механической обработкой.
Ремонт изношенных отверстий производят: Установкой ремонтной втулки.Наплавкой отверстия.
Ремонт способом добавочных ремонтных деталей
У значительного количества деталей сложной формы изношенными или поврежденными являются отдельные небольшие элементы детали: гладкие и резьбовые отверстия, шейки валов, места посадки подшипников качения в корпусных деталях, венцы шестерен и т. п. При этом целесообразным является удаление дефектного слоя металла или дефектного элемента детали и восстановление ее постановкой дополнительной ремонтной детали (ДР) — втулки, ввертыша, венца, шестерни — или заменой дефектного элемента детали.
Этот способ имеет несколько характерных случаев применения: 1) ремонт отверстий постановкой ремонтной втулки, гильзы или кольца; 2) ремонт валов напрессовкой втулки, кольца или постановкой полувтулок; 3) ремонт элементов детали разнообразной формы способом удаления дефектного и установки нового элемента детали: заменой зубчатого венца, шлицевой ступицы, шлицевого конца и др.; 4) ремонт плоских поверхностей постановкой планок или накладок.
Ремонт гладких отверстий постановкой ремонтной втулки является наиболее простым и распространенным способом. Примерами такого способа ремонта являются места посадки наружных колец подшипника качения в корпусах коробок передач, раздаточных коробках, ступицах колес, отверстия в сателлитах, чашке дифференциала и в проушинах шкворня моторного катка, отверстие в полумуфте асфальтоукладчика.
Гильзование блоков цилиндров легких и пусковых двигателей применяется тогда, когда диаметр цилиндра больше предельно установленных ремонтных размеров. Для этого цилиндр двигателя растачивают под гильзу с учетом толщины стенок гильзы 3—4 мм.
При ремонте методом ремонтных размеров одну из износившихся деталей соединения обрабатывают до исчезновения следов износа или до получения определенного заранее установленного размера, а вторую, чаще всего более дешевую, заменяют новой. Например, изношенную шейку вала обрабатывают до исчезновения следов износа и комплектуют ее с новой втулкой, обеспечивающей с полученным размером шейки вала требуемую посадку. Такой ремонт может производиться последовательно несколько раз, причем диаметр вала постепенно будет уменьшаться, а диаметр отверстия ремонтируемой детали — увеличиваться. Таким образом, детали сопряжения будут иметь размеры, отличающиеся от первоначальных. Эти новые, заранее установленные размеры деталей соединения принято называть ремонтными.
Различают три вида ремонтных размеров: стандартные, регламентированные, свободные.
Стандартные ремонтные размеры, изготовляемые промышленностью, применяют при ремонте поршней, поршневых пальцев, толкателей, вкладышей, поршневых колец.
Регламентированные ремонтные размеры устанавливаются техническими условиями на восстановление деталей. При этом механическую обработку производят до достижения заданной величины.
Свободные ремонтные размеры предусматривают обработку до получения правильной геометрической формы и чистоты рабочей поверхности деталей. Сопряженную деталь подгоняют к восстановленной до свободного ее размера, оставляя припуск для окончательной подгонки по месту.
68. Ремонт деталей класса «Валы», «Втулки», «Диски». Восстановление шлицевых и шпоночных пазов.
Ремонт деталей типа валов
Большинство деталей этого типа в процессе работы воспринимают значительные крутящие моменты (валы, шпиндели) или знакопеременные осевые нагрузки (штоки, плунжеры и т.п.).
На валах, воспринимающих большие нагрузки, которые направлены перпендикулярно к оси, наблюдаются прогибы. Последние приводят к эксцентричному вращению вала и, как следствие этого, к быстрому изнашиванию опорных поверхностей. В местах посадки шестерен, шкивов или кулачковых муфт происходит разрушение или смятие шпоночного паза. Наиболее характерными дефектами валов являются:
1)износ поверхностей трения в опорах;
2)износ поверхностей, сопрягаемых с подшипниками качения;
3)разрушение или смятие шпоночных пазов; изгиб оси вала;
4)износ резьбовых поверхностей.
У деталей, передающих нагрузки вдоль оси и работающих в направляющих втулках или сальниковых устройствах, основными дефектами являются:
1) износ трущихся поверхностей;
2)продольный изгиб вала;
3)износ резьбовых поверхностей.
Восстановление размеров изношенных шеек вала ведется двумя путями - восстановлением первоначальных и введением ремонтных размеров. Так как в последнем случае может произойти ослабление вала, то наиболее правильным следует считать восстановление первоначальных размеров. Для этого применяют следующие способы ремонта: электродуговую наплавку, металлизацию, вибродуговую наплавку, хромирование, осталивание и полимерные покрытия.
Шейки валов буровых лебедок, насосов и трансмиссий силовых приводов, а также изношенные поверхности ствола вертлюга рекомендуется наращивать металлизацией, так как их изготовляют из сталей, чувствительных к перегреву.
Изношенные шпоночные пазы на валах восстанавливают несколькими способами. Если шпоночное соединение не должно фиксировать положение сопрягаемой детали относительно вала, то под некоторым углом к старому пазу размечают и фрезеруют новый паз по первоначальным размерам. Если шпоночное соединение строго фиксируется, то необходимо восстанавливать изношенный паз. Обычно наплавляют смятые кромки или шпоночный паз полностью, и фрезеруют новый паз на месте наплавки.
Вал с изношенной поверхностью или с наращенным слоем подвергают механической обработке для получения требуемой формы, размеров и шероховатости поверхности.
Установочными базами при механической обработке в большинстве случаев служат центровые отверстия и реже наружная цилиндрическая поверхность.
Наиболее сложно ремонтировать коленчатые валы. У большинства машин поршневого типа (насосы, компрессоры, двигатели внутреннего сгорания) это одна из наиболее ответственных и дорогостоящих деталей. Основными видами разрушения коленчатых валов являются износ рабочих поверхностей коренных и мотылевых шеек, а также изгиб вала и расхождение щек. Механическую обработку восстанавливаемых шеек коленчатых валов быстроходных двигателей осуществляют на специализированных шлифовальных станках. Коленчатые валы тихоходных двигателей, компрессоров, насосов с относительно большими габаритами обрабатывают, как правило, на токарных станках.
Одна из часто встречающихся операций при ремонте валов оборудования для бурения скважин и нефтегазодобычи - правка. В зависимости от диаметра и прогиба валы можно править в холодном и нагретом состояниях. Обычно длинные валы диаметром 10-100 мм при местном прогибе до 0,008 от длины вала правят в холодном состояний. При большей величине стрелы прогиба и больших диаметрах править валы рекомендуется с нагревом.
|
|
|