Существует группа материалов с естественным наноструктурированием, что делает их привлекательными для использования в наноэлектронных и оптоэлектронных приборах. Среди таких материалов - пористый кремний, пористый оксид алюминия и углеродные нанотрубки.
4.6.1.Пленки пористого кремния.
Ансамбли кремниевых наноструктур, состоящих из квантовых шнуров и квантовых точек, образуются в пористом кремнии, получаемом локальным анодным электрохимическим растворением монокристаллического кремния в электролитах на основе плавиковой кислоты (HF). Пористый кремний обладает уникальными физическими и химическими свойствами, которые определяются плотной сетью наноразмерных пор в кристаллической матрице и развитой внутренней поверхностью этих пор. Квантовое ограничение и поверхностные эффекты в наноструктурах пористого кремния приводят к тому, что этот материал, в отличие от монокристаллического кремния, ведет себя как прямозонный полупроводник, демонстрируя достаточно интенсивную фото- и электролюминесценцию. Это используется при создании светоизлучающих приборов, интегрированных с монокристаллическим кремнием. Кремний является одним из немногих материалов полупроводниковой электроники, в котором возможно формирование наноразмерных пор. Поры удается создать и в других полупроводниках, а именно в SiC, SiGe, GaAs, GaP, InP. Однако проявления в них таких же, как в пористом кремнии наноструктурных эффектов, обнаружить не удалось.
Простейшая ячейка для проведения электрохимической обработки состоит из химически инертной ванны, наполненной раствором HF, в который помещают кремниевую пластину и платиновый электрод. Для инициирования электрохимического растворения на пластину кремния подают положительный (анодный) относительно платинового электрода потенциал. Процесс электрохимической обработки проводят при определенной плотности анодного тока, что позволяет получать требуемую пористость, толщину пористого слоя и обеспечить их воспроизводимость от процесса к процессу. Если кремниевая пластина просто погружается в ванну на токоподводящем зажиме, остающемся над поверхностью электролита, то пористый слой образуется на обеих поверхностях и кромке пластины, контактирующих с электролитом. При этом имеет место неравномерное распределение плотности тока по поверхности пластины. Ее более глубоко погруженная часть находится под меньшим потенциалом, чем верхняя из-за резистивного падения напряжения в объеме самой пластины. В результате имеет место понижение плотности анодного тока от верхней части пластины к нижней, что приводит к соответствующей неравномерности свойств пористого слоя. Этот эффект наиболее сильно проявляется в слаболегированных высокоомных кремниевых пластинах.
Формирование пористого слоя с лучшей однородностью и только с одной стороны достигается в электрохимической ячейке с плоским электрическим контактом по всей поверхности кремниевой пластины. Одна из таких конструкций показана на рис. 5.1.
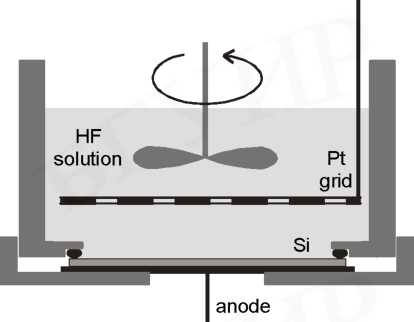
Рис. 5.1. Принципиальное устройство однокамерной ячейки для электрохимического анодирования.
В ней с электролитом соприкасается только одна сторона кремниевой пластины, а металлический или графитовый токоподводящий контакт прижимается к ее обратной стороне. Для низкоомного кремния (сопротивление ниже нескольких мОм-см) достаточно хорошая однородность пористого слоя по анодируемой поверхности обеспечивается без специальной подготовки токоподводящей поверхности пластины. Для высокоомного кремния на токоподводящую поверхность осаждают пленку металла или подлегируют ее с целью улучшения электрического контакта и обеспечения равномерного протекания тока. Перемешивание электролита в процессе анодирования, удаляющее с поверхности пузырьки газообразных продуктов реакции, также улучшает однородность формируемого пористого слоя.
Химические превращения, ответственные за локальное электрохимическое растворение кремния в электролитах на основе HF, предполагают участие в них дырочно(h+) -электронного(е-) обмена, протекающего по следующей схеме: Si + 2∙HF + l∙h+ → SiF2 + 2∙Н+ + (2 — l) ∙ e- , SiF2 + 2∙HF → SiF4 + H2↑, SiF4 + 2∙HF→SiH2F6, где l- количество элементарных зарядов, участвующих в обмене на каждой ступени. Растворение кремния требует наличия в зоне реакции молекул HF (со стороны электролита) и дырок (в кремнии). Для создания достаточного количества электронов и дырок в кремнии его поверхность в процессе анодирования часто облучают светом. Это особенно актуально для кремния n-типа проводимости и слаболегированного (ниже 1018 см-3 ) р-типа. Газообразный водород и растворимое соединение SiH2F6 являются основными продуктами реакции. При анодировании в чистых водных растворах HF пузырьки водорода прилипают к поверхности кремния, что приводит к неоднородности пористого слоя по глубине в различных местах поверхности пластины. Эффективному удалению пузырьков способствует введение в электролит смачивающих поверхностно-активных веществ. Такими свойствами обладает абсолютный этанол, который добавляют до концентрации не более 15 %. Другой подходящей добавкой является уксусная кислота, нескольких процентов которой достаточно для эффективного удаления пузырьков с поверхности анодируемой пластины кремния и регулирования pH электролита.
Свойства пористого слоя, такие, как пористость (доля пустот в слое), толщина, размер и структура пор, зависят от свойств кремния и условий анодирования. Наиболее значимыми факторами являются: тип проводимости, удельное сопротивление и кристаллографическая ориентация кремния, также как и концентрация HF в электролите, pH электролита и наличие в нем других соединений, температура, плотность анодного тока, освещенность анодируемой поверхности, перемешивание электролита и продолжительность анодной обработки. Оптимальное управление процессом формирования пористого слоя и воспроизводимость характеристик от процесса к процессу требуют тщательного контроля за этими факторами.
В одном из них каналы пор имеют более - менее упорядоченную деревообразную структуру, прорастающую от поверхности в объем. Такие поры обычно формируются в монокристаллическом кремнии с п-типом проводимости.
Другой тип структуры пористого слоя характеризуется хаотическим расположением пересекающихся пор, что типично для пористых слоев в р-типе монокристаллического кремния. Кроме того, в сильнолегированном кремнии (удельное сопротивление материала ниже 0,05 Ом-см) обоих типов проводимости поры представляют собой каналы диаметром порядка 10 нм, идущие практически перпендикулярно поверхности. В них пористость может достигать 60 %. В слаболегированном кремнии ситуация несколько иная. Пористый слой, сформированный в р-кремнии и в п-кремнии при подсветке, состоит из сети хаотично расположенных пор диаметром 2-4 нм. Достижимая пористость в этом случае выше. Поры в п-кремнии, проанодированном в темноте, выглядят как параллельно расположенные цилиндры. Пористость таких слоев обычно ниже 10 %.
Влияние кристаллографической ориентации проявляется только в монокристаллическом кремнии с n-типом проводимости, в котором поры растут вдоль главных кристаллографических направлений. В других же случаях пористые слои, сформированные в аморфном, поликристаллическом и монокристаллическом кремнии с одним и тем же типом проводимости и одинаковой концентрацией основных носителей заряда, имеют одинаковые свойства, хотя их поведение при анодировании различно.
Пористость увеличивается при увеличении плотности тока от 10 до 200 мА/см . Повышение концентрации HF в электролите снижает пористость. Толщина пористого слоя - от десятков нанометров до десятков микрометров, линейно зависит от продолжительности анодной обработки. Тонкопленочные маски из Si3N4 или других устойчивых к HF материалов используют для локального формирования областей пористого кремния в монокристаллической подложке по требуемому рисунку.
Кремний в промежутках между порами сохраняет свою исходную кристаллическую структуру. Так, поры сами по себе и их пересечения создают различные наноструктуры в виде нанокристаллических кластеров и шнуров. Они произвольно распределены по толщине пористого слоя, хотя их интегральная концентрация и распределение по размерам определяются свойствами исходного кремния и условиями анодной обработки. Выделение каких-либо наноструктур из пористого слоя невозможно. Все они действуют в ансамбле. Поэтому практическое применение пористого кремния ограничено оптическими и оптоэлектронными приборами, работа которых основана на статистическом поведении ансамблей квантово-размерных частиц монокристаллического кремния.
4.6.2.Пленки пористого оксида алюминия. Пористый анодный оксид алюминия обладает уникальной «собственной» структурой, позволяющей изготавливать столбиковые, нитевидные, точечные, конусообразные и другие элементы с нанометровыми размерами, которые невозможно получить и воспроизвести известными методами микрообработки, в частности, литографии. Особенностями структуры являются: равномерное распределение микроскопических пор с диаметром от субмикронного до нанометрового диапазона; расположение вертикально направленных пор с высоким аспектовым отношением (до 1000) на почти одинаковом расстоянии друг от друга; высокая воспроизводимость геометрических параметров структуры на образцах большой площади; возможность управления геометрическими размерами пор и ячеек пористого оксида путем изменения состава электролита и режимов электрохимической обработки.
Оборудование для получения анодных оксидов алюминия включает двухэлектродную ячейку с термостатированием и мешалкой, а также систему синхронного контроля за электрическими параметрами анодирования. Электрохимическая ячейка аналогична той, которая используется для анодирования кремния. Но так как используются неагрессивные электролиты, ячейка может быть изготовлена из стекла или металла, а катод из графита или любого, не растворяющегося в электролите металла или сплава, например, тантала, титана, алюминия, ниобия, стали.
Образование анодных оксидов из тонких пленок или массивного алюминия в жидких электролитах при электрохимическом анодном окислении (оксидировании) происходит в результате встречной миграции ионов А1+3 и О-2 в электрическом поле большой напряженности. Сложный процесс пористого анодного окисления алюминия целесообразно разделить на три стадии:
1) протекание реакции передачи кислорода от анионов или молекул раствора на анодируемый металл и возникновение первичного соединения алюминия с кислородом;
2) формирование сплошной тонкой оксидной пленки барьерного типа;
3) рост утолщенной пленки пористого типа. Донорами кислорода могут быть все кислородсодержащие ионы электролита (SO42-, HS041- , PO43-, C2O42-, ОН1-), а также недиссоциированные молекулы раствора и, прежде всего, молекулы воды. Так как при анодировании в водных растворах кислот (например, серной) не наблюдается восстановления кислоты (например, H2SO4до SO2 или элементарной серы), можно заключить, что анионы кислот (SO42- ) в водных растворах электролитов являются только переносчиками кислорода, а основным донором кислорода являются молекулы воды. Реакция анодного окисления Al в общем виде
2∙А1 + З∙Н20 → А12О3 + 6∙Н++ 6∙е (5.4)
является суммарной ряда частных процессов, наиболее вероятным из которых является анодная ионизация А1 на границе раздела металл-барьерная окисная пленка Al ->Al3+ + 3∙e–. (5.5) (5.5) Образующиеся по этой реакции электроны уходят во внешнюю цепь, образуя ток анодирования. Ионы Аl3+ мигрируют в электрическом поле оксида (в ионной решетке оксида) к внешней поверхности барьерного слоя.
При анодировании алюминия заметного выделения кислорода не происходит, поэтому процесс передачи кислорода на алюминий, который протекает на границе раздела барьерный слой-электролит, следует представить непосредственно как анодный процесс образования иона кислорода
Н20 → 2∙H+ + 02- (5.6)
а не процесс выделения кислорода на аноде
Н20→ 2∙H++ 0.5∙O + 2∙е-. (5.7)
Ион кислорода, образующийся на поверхности барьерного слоя по реакции (5.7), может мигрировать в барьерном слое под действием электрического поля по направлению к металлу навстречу иону алюминия.
Толщина беспористого оксидного слоя зависит от напряжения формовки и составляет 1,4 нм/В в электролитах с pH, равным 5,5, не растворяющих оксид алюминия. Рассчитанный из этой величины градиент потенциала (Uf/h) соответствует критической напряженности электрического поля Екр = = (7-8) 106 В/см, ниже которой движение ионов алюминия и кислорода прекращается, а следовательно, прекращается и рост пленки.
Толщина пористой части пленки (если еще не достигнута предельная величина) зависит от количества электричества, прошедшего через анод, т.е. растет в соответствии с законом Фарадея. Толщина барьерного слоя в пористой пленке является функцией формующего напряжения и в процессе анодирования остается практически постоянной и пропорциональной 1,0 нм/В в большинстве используемых электролитов.
Образование пор начинается не одновременно по всей поверхности металла, а в энергетически выгодных местах, которыми могут быть места выхода дислокаций на поверхность, линии скольжения, границы зерен, примеси, структурные дефекты и др. Так, первоначальное распределение пор на поверхности алюминия случайно, хаотично и не поддается упорядочению. Одновременно с ростом пор на внешней поверхности на границе раздела металл-оксид начинает расти новый слой оксида, отдельные ячейки которого имеют вид полусферы. Вначале на поверхности металла возникают отдельные ячейки.
По мере роста напряжения формовки между имеющимися ячейками начинают образовываться новые, постепенно заполняя всю поверхность металла. Очевидно, что самые первые ячейки с полусферическим основанием не могут расти безгранично, так как размеры ячейки будут определяться приложенным напряжением и проводимостью пленки. Но в начальный момент размеры ячеек будут отличаться друг от друга, так как ячейки, возникшие позже, будут иметь меньше времени для роста, а центры ячеек будут расположены хаотично. После того как отдельные ячейки сомкнутся и покроют всю поверхность металла, возможным останется рост каждой ячейки только в глубину. В этих условиях ячейки, имеющие меньшую полусферу в основании (запоздавшие), будут иметь большую возможность для роста, так как имеют меньшую толщину барьерного слоя. Следовательно, они будут выравнивать свои размеры за счет остальных (соседних), т.е. процесс образования строго упорядоченной ячеистой структуры состоит в перестройке самих ячеек в период роста.
Таким образом, через несколько секунд (в порообразующем электролите) на поверхности металла вырастает барьерная пленка, внешний слой которой в результате воздействия электролита постепенно и непрерывно превращается в пористый оксид. Через поры осуществляется подход электролита к барьерному слою и таким образом поддерживается возможность дальнейшего формирования новых слоев оксида.
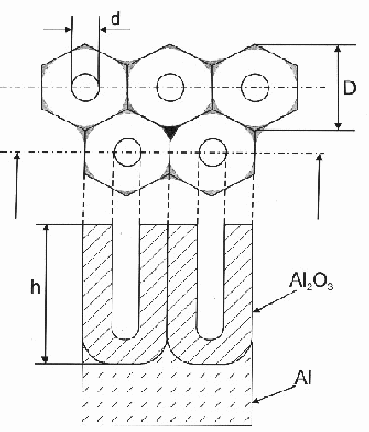 Рис. 5.3. Схематическое изображение фрагмента пористого оксида с плотно упакованными гексагональными ячейками в центре с порой (d - диаметр поры, D - диаметр ячейки, h - высота поры и пористого оксида). Рост и растворение оксида определяются (и усиливаются) локальным увеличением поля на дне пор. Этот механизм считается в настоящее время наиболее приемлемым. Для того чтобы объяснить тот факт, что поры возникают не сразу, а как только будет достигнута некоторая критическая толщина барьерного слоя, Гоар и Яхалом предположили, что для формирования пор необходимо проникновение в оксид протона, который участвует в реакции растворения против анодного поля. А это возможно при уменьшении этого поля до некоторой характеристической величины (т.е. до достижения некоторой критической толщины барьерного слоя на дне поры).
Исследования показали, что и барьерные и пористые пленки развивают ячеистую структуру только по истечении некоторого времени tmin , при котором ток имеет минимальное значение в режиме постоянного напряжения. В порообразующих электролитах это время равно примерно 2 с, в 3%-ном растворе тартрата аммония (pH = 5,5) tmin = 12 мин, а в том же электролите (pH = 7,0) - 90 мин. В порообразующих электролитах минимум плотности тока в точке tmin соответствует началу формирования пор. Последующее увеличение тока (Uf = const) отражает утонение барьерного слоя на дне пор по мере их роста. Дальнейшая стабильность тока означает стабильность роста барьерной пленки (с постоянной анодирования 1,0 нм/В) и поры растут (развиваются) преимущественно в пленке, а не за счет подложки (металла). По мере роста пор более развитые поры поглощают соседние, образуя новые поры.
Таким образом, в каждый данный момент потенциостатического анодирования имеет место распределение пор по размерам и формам. И только после некоторого времени диаметр пор становится постоянным. До этого момента он подчиняется распределению
d/1,31 - h∙ ln ((d/1,31 + h)∙h) = K(t- t0),
(5.8) где d - диаметр nop, h - толщина барьерного слоя, t - время анодирования, t0 - время зарождения пор, К - постоянная анодирования.
Полная застройка оксидными ячейками поверхности металла происходит через несколько секунд (4-7 с) и в дальнейшем структура пленки не изменяется, если условия анодного окисления остаются постоянными. Толщина барьерного слоя изменяется только в первые секунды процесса (4-7 с), в дальнейшем оставаясь постоянной даже после длительного анодирования (часы).
На второй стадии происходит упорядочение ячеисто-пористой структуры путем доанодирования участков алюминия в тангенциальном направлении (между растущими оксидными ячейками). Замедление растворения можно объяснить снижением количества эжектируемых ионов алюминия и/или возрастанием вклада процессов встраивания в оксид анионных комплексов алюминия.
Так как электрическое поле около точки (единичная пора на начальном участке) стремится быть сферическим, то передний фронт растущей оксидной ячейки также будет сферическим, если пора действительно является точечным источником. Но так как пора имеет конечный размер, передний фронт ячейки будет иметь форму сектора. После длительного анодирования и слияния отдельных ячеек образуются ячейки с цилиндрическими порами в центре и с промежуточными, сквозными металлическими столбиками с треугольным сечением (рис. 5.3).
Эти столбики на репликах с поверхности оксида выглядят как темные участки, увеличивая видимую плотность пор, которые также являются темными на фотографиях.
Остатки металла между ячейками все еще находятся в действующей электрической цепи и поэтому будут превращаться в оксид анодным способом до окончательного смыкания ячеек. Металл будет расходоваться в равной степени с каждой стороны под влиянием тока в порах трех окружающих ячеек. Когда весь металл из этих столбиков израсходуется полностью, слой оксида станет непрерывным, и ячейки приобретут форму гексагональных призм, а не цилиндров. При таком преобразовании идеальной цилиндрической ячейки в плотно упакованный ряд гексагональных ячеек должна изменяться и форма пор. Поперечное сечение поры окончательно сформированной ячейки будет иметь форму шестигранника.
Изменение формы ячеек требует изменения формы дна оксидной ячейки в месте контакта с металлом. В месте соединения трех соседних ячеек металл находится под влиянием тока в этих трех ячейках (порах) и будет преобразовываться в оксид быстрее из-за более высокой плотности тока, получающейся в результате перекрещивающихся электрических полей.
Следовательно, дно единичной ячейки в плотно упакованной регулярной структуре будет иметь больший радиус кривизны, чем в единичной, изолированной ячейке (от точечного источника). Плотность пор, определенная по репликам поверхности и по РЭМ-фотографиям, будет примерно одинаковой и соответствует действительной плотности пор.
Размер ячейки и для плотных, и для пористых электролитов является линейной функцией напряжения формовки и, кроме того, зависит от электролита через величину толщины оксида на каждый вольт напряжения (через постоянную анодирования). Диаметр поры определяется только типом электролита и не зависит от формующего напряжения. Толщина барьерного слоя в основании оксидных ячеек для оксидов, сформированных в четырех различных электролитах (3%-ной хромовой, 15%-ной серной, 4%-ной фосфорной, 2%-ной щавелевой кислотах) примерно одного порядка.
Объем поры должен уменьшаться с увеличением напряжения формовки, так как размер ячейки при этом увеличивается, количество ячеек на единице площади уменьшается, а диаметр поры остается постоянным.
Таким образом, основные структурные параметры (размеры) пористого оксида будут пропорциональны только одному саморегулирующемуся, самоуправляемому, самоконтролируемому размеру - толщине барьерного слоя в устойчивом состоянии, т.е. толщине барьерного слоя полностью формованного оксида.
Интересным является тот факт, что ячеисто-пористая структура анодного оксида Аl формируется и в барьеробразующих электролитах, например, в 3%- ном растворе тартрата аммония. Образованию пор в этих электролитах предшествует очень длительный период (в данном конкретном случае 90 мин), в течение которого барьерный окисный слой утолщается, среднее поле в оксиде уменьшается до значения Екр, при котором возможна диффузия протонов в пленку оксида против поля и порообразование.
Учитывая значительное временное различие процессов, происходящих в барьеро- и порообразующих- электролитах, можно считать, что поры, изображенные на рис. 5.3, имеют место на начальной стадии роста, и что через некоторое время (32 ч) диаметр поры принимает постоянное значение, глубина поры становится линейной функцией времени анодирования, а сами поры принимают цилиндрическую форму (рис. 5.3, сплошные штриховые линии).
Скорость роста глубины пор (высота пор) не зависит от напряжения формовки. Глубина поры становится линейной функцией времени анодирования после 8 часов анодирования (формовки). РЭМ-фотографии показывают, что оксид является прозрачным на непрозрачном основании. Граница раздела оксид-электролит является фактически планарной и каждой поре соответствует ямка на поверхности металла. Каждая пора отделена от поверхности металла со всех сторон относительно однородным барьерным слоем. Этот слой немного тоньше в основании пор, чем по стенкам пор.
Анализ теоретических и экспериментальных результатов позволяет определить последовательность процессов при формировании самоупорядоченной структуры пористого оксида алюминия:
- образование безпористой пленки оксида алюминия барьерного типа;
- зарождение пор хаотично распределенных по поверхности;
- развитие пор и ячеек на границе раздела оксид-металл в барьерном слое;
- формирование регулярных ячеек и пор цилиндрической формы с постоянным диаметром за счет подложки (в глубину);
- формирование гексагонально-упорядоченных ячеек пористого оксида. Первые стадии зарождения и роста пор достаточно полно исследованы в ранних (классических) работах по анодированию вентильных металлов. Однако процесс самоупорядочения при росте пористого оксида наиболее наглядно проявляется на последней самой длительной стадии процесса. При этом образуются оксиды большой толщины, так как последняя прямо пропорциональна времени анодирования.
В последнее время интерес к пористому анодному оксиду алюминия повысился в связи с широкими возможностями формирования наноструктур на его основе. К таким структурам относятся столбики, наноточки, мембраны, сетки, нанонити, рельефные металлические поверхности и др.
Целый ряд экспериментальных исследований подтверждает формирование регулярной периодической структуры при длительном анодировании алюминия в специальных режимах.
Специальный режим анодирования предполагает жесткую фиксацию подложки, понижение температуры электролита вплоть до 0 °С, циркуляцию электролита (для сохранения постоянства концентрации и pH), удаление пузырьков газа с поверхности подложки (посредством перемешивания
Рис. 5.4. Двухступенчатый режим формирования регулярной пористой матрицы из анодного оксида алюминия (А) и последовательность формирования матрицы наноточек (Б).
1 - пленка алюминия; 2 - пористый оксид алюминия, сформированный на первой стадии анодирования; 3 - регулярная пористая матрица из пористого оксида алюминия, сформированного на второй стадии анодирования; 4 - защитное покрытие; 5- кремниевая подложка; 6 – наноточки.
электролита или добавления смачивателей). Все эти мероприятия позволяют проводить процесс анодирования очень длительное время - до 160 часов.
Другой специальный режим включает две стадии анодирования. На рис. 5.4 показаны метод двухступенчатого улучшения регулярности пористого оксида (А) и последовательность формирования матрицы наноточек (Б) с использованием аналогичного метода.
Первая, длительная стадия анодирования (см. рис. 5.4), используется для формирования пористого оксида алюминия с регулярной пористой структурой из пленки алюминия (а). После селективного травления сформированного оксида на поверхности пленки металла остаются отпечатки дна ячеек регулярного пористого оксида (б). Эти участки (углубления) являются местами зарождения пор в металле (в) и формирования пористого оксида алюминия с более регулярной структурой (г) на второй стадии. Далее проводят осаждение защитного покрытия, например, нитроцеллюлозы, полиэфириримида в этилацетате, бутилацетате или гептане (д); удаление оставшегося непрокисленного слоя алюминия (е) и защитного слоя (ж). Следующей операцией является осаждение слоя золота через маску из пористого оксида на кремниевую подложку и селективное травление маски (з), после которого пленка золота остается только в порах оксида (процесс похожий на обратную литографию). Диаметр точек составляет 40 нм с интервалом 100 нм [5].
Углубления на поверхности металла можно создавать механически с помощью специальных прецизионных штампов (SiC Mold), как показано на рис. 5.5. В этом случае места зарождения будущих пор создаются искусственно на поверхности пленки алюминия (А) в строго определенном порядке (В). Последующее анодирование приводит к формированию регулярной пористой структуры (С). Однако этот вариант требует дополнительных затрат на создание штампов с микроскопическими выступами методом электроннолучевой литографии. Данный режим используется при необходимости получения пористого оксида небольшой толщины, когда длительное анодирование (необходимое условие получения регулярной структуры) становится неприемлемым.
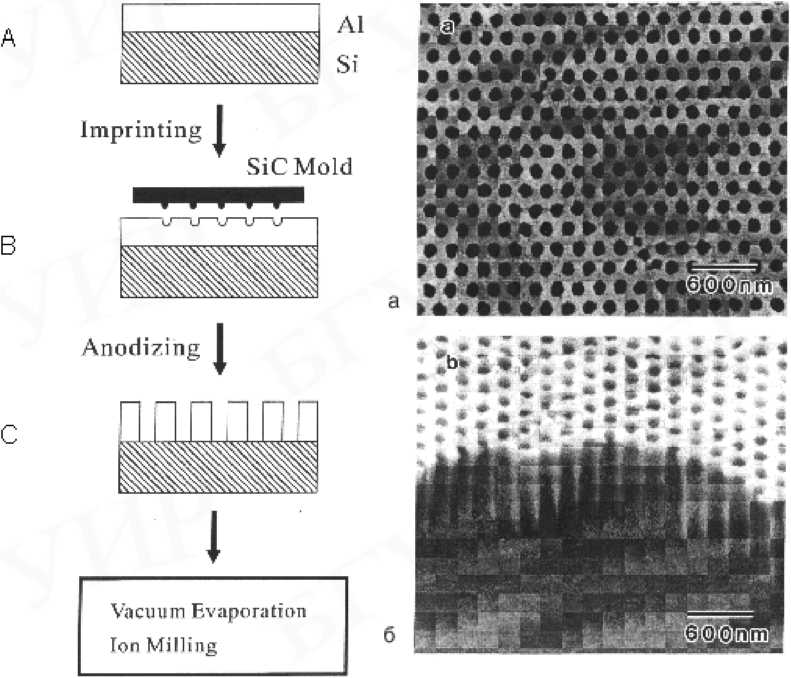
Рис. 5.5. Формирование пористого оксида алюминия с регулярными порами, зарождающимися в местах контакта пленки Аl с SiC-штампом (А, В, С) и РЭМ-фотографии пористого оксида алюминия, сформированного этим методом: а - вид сверху; б – поперечное сечение (скол).
Как уже говорилось, пористый оксид алюминия с регулярной структурой используют для формирования металлических и полупроводниковых наноточек и нанонитей. Возникающая в результате реализации эффекта самоорганизации и последующей электрохимической обработки сеть ячеек правильной гексагональной формы с управляемо варьируемым размером может быть использована в качестве масок для массивов мезоскопических структур. В качестве примера на рис. 5.6 приведены фотографии наноточек, изготовленных из пленки Ag, осажденной на Si через пористый оксид алюминия, предварительно подвергнутый электрохимической полировке. Такой оксид использовался как естественная маска, а сам процесс в литературе называют естественной литографией. Геометрические параметры маски (толщина, диаметр пор и расстояние между ними) и режим осаждения пленки серебра подбирали так, чтобы при селективном травлении оксида серебро оставалось только в порах матрицы (по аналогии с обратной «взрывной» литографией).
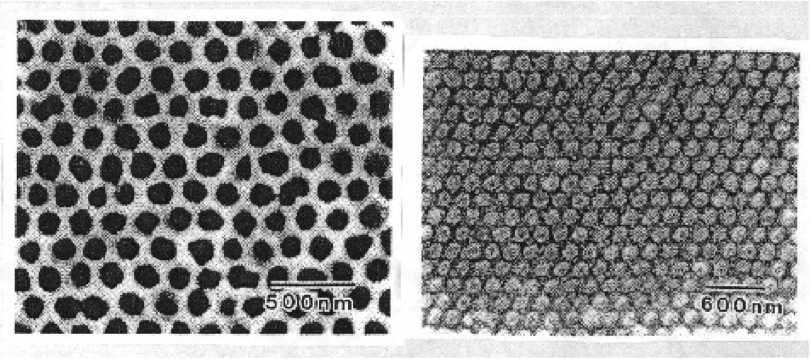
Рис. 5.6. РЭМ-фотографии сетки из пористого оксида алюминия (а) и Ag-точек на поверхности кремниевой подложки, сформированных осаждением пленки серебра через маску из пористого оксида алюминия (б).
На рис. 5.7 приведена еще одна схема использования пористого оксида в качестве «естественной» маски при формировании столбиков, а на рис. 5.8 - фотографии столбиков, выращенных локально в отверстиях фоторезистивной маски диаметром 4 мкм. В зависимости от условий анодирования столбики могут иметь различную форму: цилиндрическую, с углублением в центре, конусообразную. Конусообразные столбики, плакированные металлом, например, титаном, вольфрамом или молибденом, могут быть использованы при изготовлении холодных катодов.
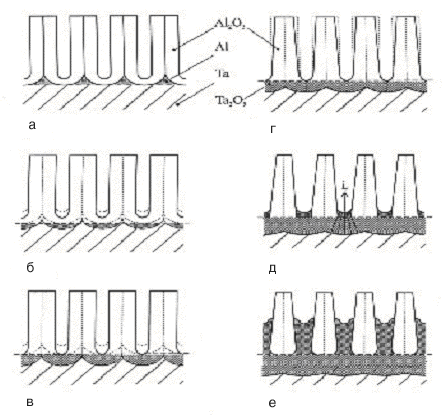
Рис. 5.7. Схема формирования столбиков Ta2O5 в матрице пористого оксида алюминия методом селективного двухступенчатого анодирования: а - пористое анодирование пленки алюминия; б, в - электрохимическое травление барьерного оксида алюминия на дне пор; г, д - электрохимическая полировка оксида Al2O3, е - высоковольтное анодирование пленки тантала через пористую матрицу в буферных (не растворяющих оксид алюминия) электролитах.
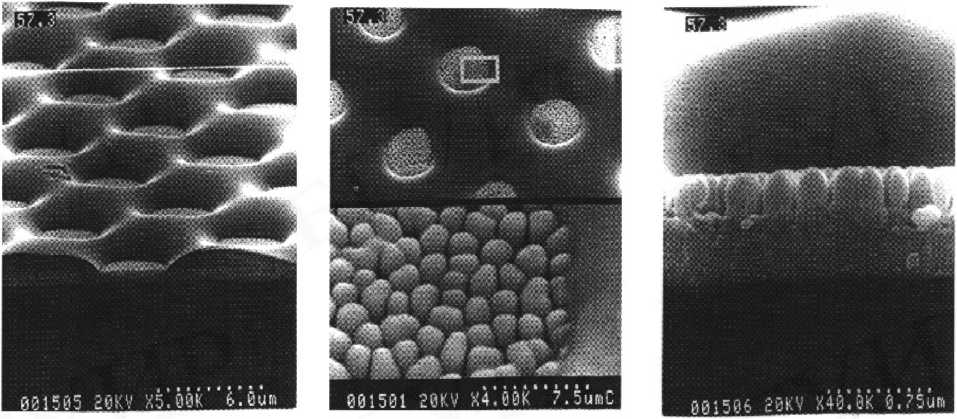 Рис. 5.8. РЭМ-фотографии столбиковых микроструктур, локально сформированных в отверстиях фоторезистивной маски через пористый оксид алюминия.
Другой вариант предполагает избирательное электрохимическое осаждение металла, в частности никеля, в поры пористого оксида или пористой матрицы, изготовленной на его основе из специальных органических материалов. Селективное осаждение никеля проводят с использованием Pt- микроэлектрода в электролитах следующего состава: Ni(OSO2NH2)2∙4H2O(330 г/л), NiCO3 (0,5 г/л) и Н3ВO3 (30 г/л) при комнатной температуре. Максимальная высота Ni-столбиков составляет 10 мкм, диаметр - 70 нм. Каждая отдельная пора в пористой матрице Аl2O3 выступает в качестве индивидуальной нанометровой электрохимической ячейки, а протекающий ток ограничивается областью, непосредственно примыкающей к поверхности Pt- электрода. Такой пространственно ограниченный ток может быть ответственным за процесс селективного осаждения никеля с пространственным разрешением, идентичным размеру острия микроэлектрода.
В результате многочисленных операций получают конусообразные острия. При диаметре апертуры 160 нм диаметр острий автоэмиссионных катодов может составлять 5-35 нм.
Многочисленные исследования, которые ведутся в этом направлении, должны привести к созданию матриц эмиссионных катодов для широкоформатных индикаторов.
На рис. 5.9 показан процесс формирования металлической решетки (сетки) с наноотверстиями (A-F), и РЭМ-фотографии Pt-сетки, изготовленной по этому маршруту [9]: сначала формируют пористый оксид алюминия с регулярной пористой структурой в течение 160 часов при 0 °С в 0,3-мольной щавелевой кислоте при постоянном напряжении 40 В (А). Длительный период анодирования при постоянном напряжении обеспечивает формирование почти идеальной упорядоченной структуры оксида, который в дальнейшем используется как маска.
Далее методом вакуумного осаждения создают тонкий слой металла (В), который служит катализатором или электродом при последующем заполнении пор полиметилметакрилатом (ПММА), содержащим 5 вес.% бензол-пероксида (С). Последний служит инициатором полимеризации ПММА в вакууме под действием ультрафиолетового излучения.
Затем удаляют оксид алюминия в 10%-ном водном растворе NaOH (D) и проводят катодное осаждение платины в отверстия негативной маски из ПММА (Е). После получения слоя платины нужной толщины ПММА-матрицу удаляют в ацетоне (F). Точно так же изготавливают решетки с наноотверстиями из золота, используя метод электрохимического осаждения на затравочный подслой.
Далее удаляют оксид алюминия в 10%-ном водном растворе NaOH (D) и проводят катодное осаждение платины в отверстия негативной маски из ПММА (Е). После получения слоя платины нужной толщины ПММА-матрицу удаляют в ацетоне (F). Точно так же изготавливают решетки с наноотверстиями из золота, используя метод электрохимического осаждения на затравочный подслой.
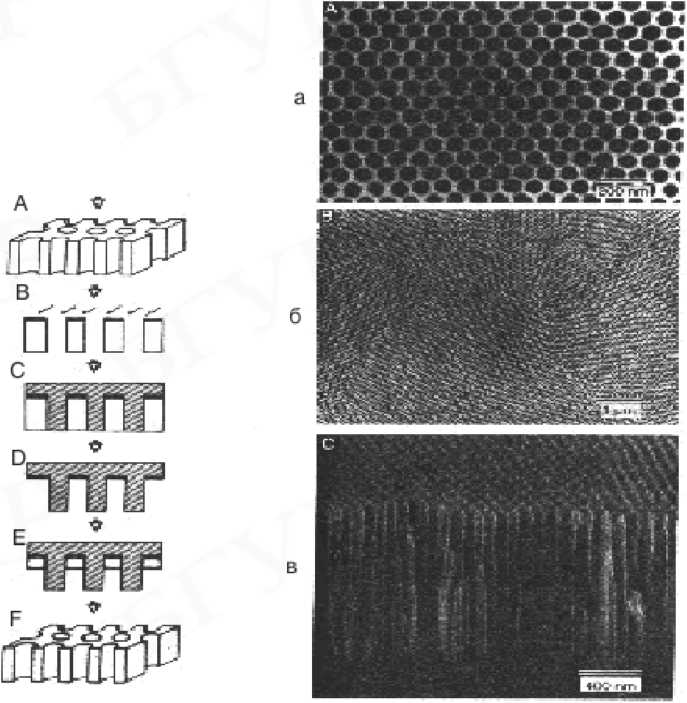 Рис. 5.9. Процесс формирования металлической сетки с наноотверстиями (A-F) и РЭМ-фотографии платиновой сетки с наноотверстиями: а - вид сверху (большое увеличение); б - вид сверху (малое увеличение); в - поперечное сечение [9] Рассмотренные структуры представляют интерес при разработке функциональных слоев для устройств оптоэлектроники, сенсорики, наноэлектроники, при изготовлении фильтров, мембран, фото- и эмиссионных приборов.
|