РД-25.160.10-КТН-016-15_с_Изм2. Публичное акционерное общество транснефть
![]()
|
Приложение Е |
| Дата и подпись ответствен-ного лица об устранении нарушений | 10 | | | ||
Замечания контролирующих лиц по качеству выполняемого контроля физическими методами сварных соединений с указанием фамилии, должности и даты записи | 9 | | | |||
Заключение о качестве проконтролированного сварного соединения | Подписи | Началь-ник/ инженер службы контроля качества | 8 | | | |
Специа-лист по ВИК/РК/ УЗК/ПВК/МК | 7 | | | |||
Заключение о годности («годен», «ремонт», «вырезать») | 6 | | | |||
Номер заключения и дата его выдачи | 5 | | | |||
Метод контроля и дата его проведения | 4 | | | |||
Шифр сварщика/бригады; фамилия, инициалы | 3 | | | |||
Наименова-ние узла, детали; номер соединения по журналу или сварочной схеме; номер журнала /схемы | 2 | | | |||
№ п/п | 1 | | |
Приложение И
(обязательное)
Ультразвуковой контроль с применением систем автоматизированного ультразвукового контроля
Требования к средствам и персоналу для проведения автоматизированного ультразвукового контроля
Общие требования
Средства АУЗК, применяемые для контроля кольцевых стыковых сварных соединений труб должны обеспечивать обнаружение дефектов стыковых кольцевых сварных соединений и околошовной зоны согласно нормам, указанным в И.4 (приложение И), и регистрацию их параметров (координат и условных размеров, уровня отраженного сигнала)
Затраты времени на установку сканера на трубу, сканирование, предварительную обработку данных и подготовку предварительного заключения должны соответствовать темпу движения сварочной колонны.
АУЗК, использующий зональный метод контроля, не применяется на сварных соединениях, выполненных ручным способом сварки.
Требования к оборудованию АУЗК
Установка АУЗК должна обеспечивать двухсторонний контроль всего объема стыкового кольцевого сварного шва (включая околошовную зону) труб диаметром от 530 до 1220 мм с толщиной стенки трубы от 8 до 40 мм за один проход сканера по всей длине сварного шва.
Установки АУЗК, применяемые для НК кольцевых стыковых сварных соединений труб, должны:
быть внесены в реестр утвержденных типов средств измерения в соответствии с Федеральным законом [7];
иметь свидетельство о метрологической поверке (калибровке) установленной формы и другие разрешительные документы в соответствии с действующими требованиями;
пройти квалификационные испытания в соответствии с И.6 (приложение И);
иметь согласованную с ПАО «Транснефть» методику проведения и интерпретации результатов контроля (оценки годности) сварных соединений на соответствие нормам оценки качества сварных соединений, приведенных в И.4 (приложение И).
Системы АУЗК должны иметь следующие технические характеристики:
температура контролируемой поверхности от минус 40 °С до 60 °С;
температура эксплуатации сканирующего устройства от минус 40 °С до 60 °С.
Если внешние условия (сильный ветер, отрицательные температуры) ниже допустимых, работы по АУЗК должны выполняться в укрытиях с подогревом. Установка укрытий и систем обогрева осуществляется производителем строительно-монтажных работ.
ПЭП, используемые в работе установки, должны иметь паспорт, в котором указывается:
тип и заводской номер ПЭП;
угол ввода;
частота преобразователя.
Для преобразователей с ФАР указывается:
скорость продольных волн в призме;
геометрические характеристики призмы;
количество элементов в преобразователе;
расстояние между элементами;
частота.
Для преобразователей, предназначенных для работы по методу TOFD, указывается угол ввода, диаметр ПЭП и частота.
Установка АУЗК должна быть укомплектована метрологически аттестованным НО.
Требования к калибровочным образцам для настройки установок АУЗК
Для настройки установок НК следует использовать калибровочные образцы, предусмотренные методикой проведения и интерпретации результатов контроля.
НО применяемые для настройки установок НК должны иметь свидетельства о поверке и/или свидетельства об аттестации установленной формы.
НО должны быть изготовлены из материала с аналогичными акустическими свойствами материалу контролируемого объекта, и иметь паспорт, выданный аккредитованным центром метрологии и стандартизации или производителем, если он имеет право первичной поверки, в котором указано:
номер НО;
диаметр и толщина трубы, для контроля которой используется НО;
ТУ на трубу, из которой изготовлен НО;
тип, размеры, положение и углы наклона отражателей.
Эскиз НО, параметры искусственных отражателей и схемы контроля должны быть приведены в операционной технологической карте на АУЗК.
Количество искусственных отражателей в НО, их ориентация должны соответствовать параметрам разделки кромок свариваемых элементов. Торцы образца и отражатели, расположенные в соседних зонах, не должны создавать акустических помех при настройке.
Для установок, использующих зональный метод контроля каждому типу разделки кромок и типоразмеру труб должен соответствовать определенный НО (калибровочный образец).
Шероховатость поверхности НО не хуже Rz 40 мкм.
Фрагменты трубы для изготовления НО должны передаваться исполнителю заказчиком. Размеры фрагментов трубы для НО должны быть указаны исполнителем работ по НК. Рекомендуемые размеры заготовок указаны в таблице И.1.
Таблица И.1 – Рекомендуемые размеры заготовок для НО
№ п/п | Диаметр трубы, мм | Длина заготовки, мм | Примечание |
1 | 2 | 3 | 4 |
1 | От 530 до 600 | 305 | Заготовка представляет собой отрезок трубы |
2 | От 601 до 1220 | 610 (в осевом направлении) 610 (по окружности) | Заготовка представляет собой фрагмент материала трубы |
Заготовка для изготовления НО должна быть проконтролирована заказчиком на отсутствие внутренних расслоений и внешних дефектов. Наличие продольных и поперечных швов на заготовке недопустимо, шероховатость поверхности заготовки не более Rz 40 мкм.
НО должен иметь следующие искусственные отражатели:
отверстия с плоским дном по таблице 8.10 для настройки чувствительности и длительности строба для обнаружения внутренних дефектов плоскостного характера по линии разделки кромок;
отверстия с плоским дном диаметром от 1,5 до 2, 0 мм по оси шва для обнаружения внутренних дефектов объемного характера;
зарубки по таблице 8.10 на верхней и нижней границе разделки шва для настройки чувствительности и длительности строба при контроле корня и верхней части шва;
вертикальные пазы с заостренной нижней гранью на оси шва для проверки работоспособности преобразователей TOFD. Размеры пазов, используемые при контроле TOFD, приведены в таблице И.2.
Таблица И.2 – Размеры пазов, используемые при контроле TOFD
№ п/п | Номинальная толщина стенки трубы S, мм | Глубина паза на поверхности, мм | Длина паза, мм | |
наружной | внутренней | |||
1 | 2 | 3 | 4 | 5 |
1 | От 8,0 до 10,0 включ. | 3,0 | 2,0 | 15 |
2 | От 10,0 до 12,0 включ. | 4,0 | ||
3 | От 12,0 до 15,0 включ. | 5,0 | ||
4 | От 15,0 до 20,0 включ. | 6,0 | ||
5 | От 20,0 | 7,0 |
Пазы в НО должны быть выполнены безударным способом.
Допуски на отклонение параметров искусственных отражателей указаны в таблице И.3.
Таблица И.3 – Допуски на отклонение параметров искусственных отражателей в НО
№ п/п | Параметр | Допуск на отклонение размеров |
1 | 2 | 3 |
1 | Диаметр плоскодонного отверстия | ±0,2 мм |
2 | Плоскостность торца плоскодонного отверстия | ±0,1 мм |
3 | Угол | ±1° |
4 | Глубина пазов (рисок) | ±0,1 мм |
5 | Длина пазов (рисок) | ±0,1 мм |
6 | Отклонение положения центра отражателя от заданного значения | ±0,1 мм |
7 | Глубина плоскодонного отверстия | ±0,2 мм |
Искусственные отражатели НО должны быть маркированы в соответствии с чертежом и залиты герметиком.
На поверхности калибровочного блока должны отсутствовать следы коррозии, смазки или другого материала, которые могут препятствовать проникновению ультразвуковых волн в металл. Калибровочные блоки должны проверяться на наличие признаков износа (рисок, царапин) в области ввода/приема. Подобные дефекты должны удаляться полировкой. Если в результате шлифовки толщина стенки калибровочного блока снижается более чем на 0,5 мм от первоначальной толщины, калибровочный блок следует заменить.
Требования к контактной жидкости
Для контроля при температуре окружающего воздуха и поверхности трубы выше 0 °С в качестве контактной жидкости использовать воду. При температурах ниже 0 °С использовать водные растворы пропиленгликоля или этилового спирта. Рекомендуемое содержание пропиленгликоля в растворе указано в таблице И.4.
Таблица И.4 – Рекомендуемое содержание пропиленгликоля в контактной жидкости в зависимости от температуры окружающего воздуха
№ п/п | Температура воздуха, °С | Содержание пропиленгликоля, % |
1 | 2 | 3 |
1 | От 0 до минус 5 | 30 |
2 | От минус 5 до минус 10 | 40 |
3 | От минус 10 до минус 20 | 54 |
4 | От минус 20 до минус 40 | 70 |
Требования к персоналу
Персонал должен пройти обучение правилам эксплуатации применяемого оборудования в соответствии с требованиями производителя оборудования.
Специалисты должны иметь документ, подтверждающий факт прохождения обучения работе с установкой АУЗК от производителя оборудования или уполномоченной организации на территории Российской Федерации.
Количество специалистов, эксплуатирующих установку АУЗК, должно быть регламентировано инструкцией по эксплуатации на систему АУЗК.
Требования к программному обеспечению систем АУЗК
Программное обеспечение должно производить:
запись первичных результатов контроля для последующего анализа;
сигнализацию отсутствия акустического контакта между ПЭП и контролируемым изделием, регистрацию участков сканирования с отсутствием акустического контакта с отметкой пропущенных зон на развертке (скане);
визуализацию данных во время контроля в реальном режиме времени, после выполнения контроля при анализе данных и подготовке заключения по результатам контроля;
формирование списка дефектов в формате, пригодном для дальнейшего редактирования.
Подготовка и порядок проведения неразрушающего контроля с применением автоматизированных систем ультразвукового контроля
АУЗК проводят в соответствии с операционной технологической картой контроля. Карта должна быть утверждена в организации, выполняющей контроль, и согласована с ООО «НИИ Транснефть».
В срок не менее чем за 1 календарный месяц до планируемого начала работ заказчик должен предоставить исполнителю работ по НК заготовку из трубы (темплет или катушку) для изготовления калибровочного образца для каждого номинала диаметра трубы, толщины стенки и класса прочности. Требования к размерам заготовки указаны в
И.1.3.8 – И.1.3.9.
Подготовка контролируемых поверхностей выполняется производителем строительно-монтажных работ.
Нижняя часть поверхности сварного соединения должна находиться на расстоянии не менее 0,5 м от поверхности грунта.
При работе в траншее должен быть обеспечен безопасный спуск персонала с оборудованием НК в траншею.
Для труб, контролируемых установками АУЗК, должны выполняться следующие условия:
наружный валик продольных швов труб должен быть удален производителем трубной продукции до остаточной высоты от 0 до 0,5 мм, при этом должен быть обеспечен плавный переход от металла трубы к наружному продольному шву. Удаление участка наружного продольного шва должно быть предусмотрено ТУ на тубы электросварные и составлять от 200 до 250 мм;
концы труб должны быть свободны от антикоррозионного изоляционного покрытия на длину от 150 до 200 мм от торца трубы для труб с толщиной стенки до 30 мм включительно и на длину от 200 до 250 мм для труб с толщиной стенки свыше 30 мм. Освобождение концевых участков труб от наружного антикоррозионного покрытия должно быть предусмотрено ТУ на антикоррозионное изоляционное покрытие (если указанные требования не предусмотрены ТУ (до внесения изменений в ТУ), удаление наружного продольного сварного шва концевых участков и освобождение концевых участков труб от антикоррозионного изоляционного покрытия выполняется производителем строительно-монтажных работ в полевых условиях);
производитель строительно-монтажных работ должен нанести на внешнюю поверхность труб реперную линию на расстоянии 40 мм от притупления кромки после операции торцевания и перед началом операции сборки (инструмент для разметки предоставляется ЛНК).
При использовании направляющего бандажа он устанавливается относительно реперной линии и не устанавливается относительно валика облицовки.
/Перед началом контроля необходимо несмываемым маркером/краской отметить точку начала отсчета (на отметке «12 ч») и направление отсчета координат на трубе, как показано на рисунке И.1.
Р
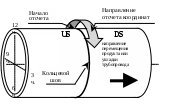
исунок И.1 – Пример установки точки начала отсчета и направления отсчета координат при контроле
Перед проведением контроля дефектоскопист должен:
получить задание на контроль с указанием типа сварного соединения, толщины стенок и диаметра трубы, параметров разделки сварного шва;
ознакомиться с конструкцией, особенностями технологии выполнения сварных соединений и документацией, в которой указаны допущенные отклонения от установленной технологии;
ознакомиться с результатами предыдущего контроля;
проверить размеры подготавливаемой зоны под АУЗК и качество подготовки поверхности.
Произвести настройку установки АУЗК в соответствии с инструкцией производителя оборудования.
Произвести проверку настройки установки АУЗК в соответствии с инструкцией производителя оборудования.
Проверка правильности настройки параметров контроля проводится:
после выполнения настройки;
в начале смены;
после выполнения контроля пяти стыков, но не реже 1 раза в 1 ч;
после замены ПЭП, используемых при контроле;
после падения сканера.
Проверка настройки установки выполняется на НО, установленном на стенде.
Проверка выполняется при той же температуре, что и контроль.
Проведение сканирования производится в соответствии с инструкцией производителя оборудования и операционной технологической картой.
Обработка и расшифровка результатов контроля
При анализе данных контроля необходимо обращать внимание на наличие акустического контакта, отсутствие пропусков данных, отсутствие смещения бандажа (при его наличии) и превышение эхо-сигналами браковочного уровня, появлением сигналов в зоне контроля TOFD.
При отсутствии акустического контакта на протяжении более чем 15 мм по любому из контролируемых каналов акустического контакта, отсутствии акустического контакта в смежных каналах на протяжении более 10 мм или смещении бандажа во время контроля, превышающего 1,0 мм необходимо устранить причины неполадок и повторить контроль всего шва.
Участки, на которых при повторном сканировании индицируется исчезновение акустического контакта, возможно, содержат расслоения. Участки с предполагаемыми расслоениями необходимо проверить ручным ультразвуковым дефектоскопом.
Расшифровку результатов контроля проводят с применением специализированного программного обеспечения в соответствии с методикой разработанной производителем оборудования.
По результатам расшифровки полученных в результате сканирования данных, оператор дает заключение о годности проконтролированного соединения. К заключению прилагается дефектограмма.
На основании заключения с дефектограммой, подготовленного оператором установки, производят разметку дефектов на сварном соединении. Разметка дефектов на трубе выполняется несмываемым маркером.
Нормы оценки качества для АУЗК
Оценка качества с использованием амплитудного критерия выполняются согласно нормам раздела 11.
Для оценки качества по условной протяженности и высоте дефекта допустимо применение альтернативных критериев, разработанных на основании инженерной оценки критического состояния и по методике, согласованной с ООО «НИИ Транснефть».
Требования к порядку оформления и хранения результатов АУЗК
Результатом проведения АУЗК являются:
первичные результаты контроля для последующего анализа;
дефектограмма;
заключение о годности сварного соединения.
Первичные результаты контроля и дефектограммы исполнитель работ по АУЗК передает заказчику на электронном носителе.
Результаты проведения АУЗК оформляются и хранятся в соответствии с разделом 7.
Требования к испытаниям установок АУЗК
Общие требования к испытаниям
Испытания установок АУЗК проводятся по договору между ООО «НИИ Транснефть» и производителем работ по АУЗК (производителем оборудования).
ООО «НИИ Транснефть» проводит техническое сопровождение испытаний и выдачу заключения о прохождении испытаний.
Испытания подразделяются на квалификационные и допускные.
Квалификационные испытания установок АУЗК проводятся с целью проверки технических характеристик установок контроля, определения области применения установок контроля, а так же установления соответствия их технических характеристик и методик контроля требованиям НД и ТД ПАО «Транснефть».
Квалификационные испытания проводят по программе квалификационных испытаний, разработанной ООО «НИИ Транснефть» совместно с производителем работ по АУЗК (производителем оборудования) на договорной основе.
По результатам квалификационных испытаний ООО «НИИ Транснефть» письменно уведомляет производителя работ по АУЗК о возможности применения оборудования на объектах организаций системы «Транснефть».
Для работы на конкретном объекте требуется пройти допускные испытания, проводимые по программе допускных испытаний.
Программа допускных испытаний разрабатывается ООО «НИИ Транснефть» совместно с производителем работ по АУЗК (производителем оборудования).
Допускные испытания проводятся на месте проведения работ по АУЗК.
Квалификационные испытания
Для проведения работ по квалификационным испытаниям должна быть разработана и предоставлена следующая документация:
программа квалификационных испытаний установки;
операционные технологические карты сборки и автоматической сварки контрольных сварных соединений труб для изготовления КСС;
чертежи с расположением искусственных дефектов в КСС;
чертежи калибровочных блоков (НО);
акт метрологической экспертизы калибровочных блоков (НО);
требования к проведению РК;
методику металлографических исследований;
операционные технологические карты АУЗК для контроля КСС.
Квалификационные испытания проводятся по программе.
Программу квалификационных испытаний разрабатывают на основе технического задания, требований настоящего документа, НД и ТД ПАО «Транснефть».
Программа должна включать в себя требования:
к количеству КСС, типу сварки и разделки шва;
к типу вносимых дефектов (типы дефектов должны быть как естественными – полученными за счет нарушения технологии процесса сварки, так и искусственными, но имитирующими естественные дефекты – полученными за счет внедрения специальных вставок и механической обработки);
к размерам дефектов (должны быть как допустимые, так и недопустимые дефекты);
к количеству вносимых дефектов (количество дефектов должно быть достаточным для выполнения полного объема испытаний и проведения статистической обработки).
Программа должна содержать перечень, условия и последовательность проведения операций, а именно:
сканирование КСС средствами АУЗК с последующей разметкой дефектов, обнаруженных при контроле;
проверка температурной чувствительности системы АУЗК;
проверка работоспособности системы контроля акустического контакта;
проверка повторяемости результатов контроля;
радиографический контроль КСС;
вырезка образцов и проведение металлографических исследований;
сравнение результатов ультразвукового, радиографического и металлографического контроля КСС.
Количество дефектов в КСС при квалификационных испытаниях должно быть достаточным для выполнения полного объема испытаний. Искусственные несплошности, вносимые в КСС должны имитировать реальные дефекты.
Для проведения квалификационных испытаний установки АУЗК необходимо выполнить следующее:
изготовить НО (калибровочные блоки) для настройки оборудования ультразвукового дефектоскопа;
подготовить и сварить КСС в соответствии с разработанными технологическими картами сборки и автоматической сварки КСС труб и чертежами с расположением естественных и искусственных дефектов в КСС;
подготовить и настроить АУЗК, выполнить калибровку на НО;
провести все работы в соответствии с программой испытаний;
провести сравнение результатов ультразвукового, радиографического и металлографического контроля КСС;
подготовить отчет по результатам квалификационных испытаний.
По результатам квалификационных испытаний установки АУЗК должны быть подготовлены следующие документы:
отчет о результатах квалификационных испытаний;
заключение о результатах квалификационных испытаний.
Отчет о результатах квалификационных испытаний должен содержать:
информацию о разделке КСС, технологии сварки;
технические характеристики установки АУЗК с указанием уровней чувствительности при контроле;
результаты контроля КСС и тестов на повторяемость, работоспособность контроля акустического контакта и влияния температуры на чувствительность контроля;
программу проведения квалификационных испытаний;
протоколы по результатам радиографического, АУЗК и металлографического исследований;
ТД, разработанную для проведения квалификационных испытаний (включая карты расположения искусственных дефектов в КСС, исполнительную схему вырезки темплетов на различных участках КСС для проведения металлографических исследований);
результаты измерения размеров искусственных отражателей в НО;
результаты испытаний работы АУЗК в трассовых условиях.
В заключении должен быть выполнен анализ и сравнение результатов контроля с критериями приемки установки АУЗК. В выводе заключения должно быть указано:
область применения установки АУЗК;
соответствие установки АУЗК требованиям НД и ТД ПАО «Транснефть».
Величина погрешности оценки размеров дефектов для средств АУЗК должна подтверждаться результатами квалификационных испытаний.
Результаты квалификационных испытаний считают положительными, если установка АУЗК выдержала испытания по всем пунктам программы квалификационных испытаний и величина погрешности оценки размеров дефектов для средств АУЗК подтверждается результатами металлографических исследований.
Допускные испытания
Допускные испытания проводит ПО по НК, совместно с заказчиком работ по НК непосредственно на объекте, на товарных кольцевых сварных соединениях на минимальном и максимальном диаметрах из перечня труб, контролируемых испытываемым средством АУЗК. Проведение допускных испытаний должно быть выполнено на калибровочном образце и не менее чем десяти товарных сварных соединений.
Средства АУЗК, прошедшие квалификационные испытания, должны пройти допускные испытания на конкретном объекте строительства, реконструкции и капитального ремонта ПАО «Транснефть»:
перед началом работ на данном объекте;
при длительных вынужденных перерывах в проведении работ (более 6 месяцев);
при изменении типа или модели средств АУЗК.
Допускные испытания проводят в присутствии представителей ООО «Транснефть – Надзор», ООО «НИИ Транснефть», организации системы «Транснефть» – заказчика строительных работ.
Допускные испытания системы АУЗК проводят в два этапа:
проведение оценки выявляемости контрольных отражателей на калибровочном образце (НО) в соответствии с утвержденной методикой проведения и интерпретации результатов контроля;
проведение АУЗК на товарных сварных соединениях для оценки: работоспособности средств НК и соответствия действий персонала методике проведения и интерпретации результатов контроля операционно- технологической карте.
По результатам допускных испытаний оформляют акт, в соответствии с требованиями настоящего документа. В акте отражают фактические результаты АУЗК и соответствие оборудования требованиям настоящего документа и НД ПАО «Транснефть». Акт должен быть подписан представителями ПО, организации системы «Транснефть», в зоне которой выполняются сварочно-монтажные работы, ООО «Транснефть – Надзор» и ООО «НИИ Транснефть».
Приложение Л
(обязательное)
Особенности ультразвукового контроля стыковых кольцевых сварных соединений на подкладных кольцах
Л.1 Основной особенностью контроля стыковых кольцевых сварных соединений на подкладных кольцах является то, что сигналы от несплошности (дефекта), располагающейся над корневым слоем, трудно отличить от сигналов, получаемых от подкладного кольца.
Л.2 На рисунке Л.1 приведена схема обнаружения подкладного кольца и надкорневой несплошности и способ их идентификации путем измерения горизонтальных координат их расположения при различных положениях преобразователя при контроле прямым и однажды отраженным лучом.
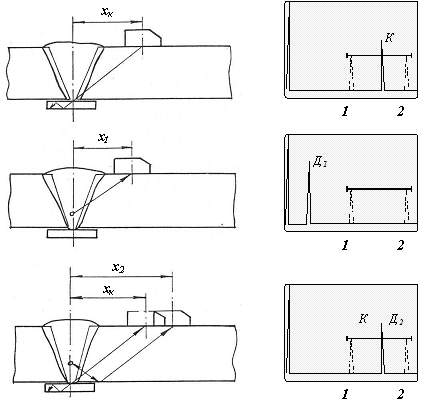
/
1 и 2 – положения сигналов от зарубок в НО; К – сигнал от подкладного кольца;
Д1 и Д2 –сигналы от надкорневой несплошности, обнаруживаемой соответственно прямым и однократно отраженным лучом;
хк, х1 и х2 – расстояния между серединой шва и точкой ввода ПЭП
Рисунок Л.1 – Схема обнаружения подкладного кольца и надкорневой несплошности (дефекта)
Примечание – Сигнал от подкладного кольца К наблюдается в одном положении ПЭП на расстоянии от шва хк. Сигналы от несплошности Д1 и Д2 наблюдаются в двух положениях ПЭП – на расстояниях х1 и х2.
1) Здесь и далее курсивом приведены указания по заполнению элементов формы журнала контроля сварных соединений методами НК.
С
