|
Теория и технология производства стали 1. Учебник для вузов. М. Мир, ООО Издательство act
Рис. 17.5. Загрузочные корзины объемом 50м3 с гибкими секторами (а) и грейферного типа (б):
I— пластинчатые секторы; 2 — поддон; 3— корпус; 4— замковая цепь; 5— цепь; 6— сектор; 7— стенд лении высокоосновного шлака в самом конце операции и перемешивании этого шлака с металлом в процессе выпуска плавки или при обработке металла специально выплавленным в другом агрегате синтетическим шлаком (см. гл. 19). Для эффективной обработки стали вне печи необходимо было разработать меры по предотвращению попадания печного шлака в ковш с тем, чтобы «отсечь» этот шлак. Соответственно меняются конструкции печей (рис. 17.7), создаются печи с донным (рис. 17.7, в) и эркерным (рис. 17.7, г) выпуском.
Одновременно возникают проблемы, связанные с желанием рационально использовать мощности дорогих трансформаторов, устанавливаемых на крупных печах. Полную мощность трансформатора можно использовать только в период расплавления шихты; по мере появления жидкой фазы мощность приходится снижать. В какой-то мере эта проблема решается при замене огнеупоров свода и стен водоох-лаждаемыми элементами (естественно, это связано с дополнительными расходами тепла).
В 60-е годы работы по созданию способов искусственного охлаждения свода и стен ДСП ведутся во многих странах. В России водоохлаждаемый свод ДСП конструкции МВМИ устанавливается вначале на 1,5-т печи литейного цеха, затем на всех 10-т печах электросталеплавильного цеха завода «Сибэлектросталь». Постепенно повсеместной становится практика замены огнеупорной кладки водоохлажда-емыми панелями. Соответственно снижается расход огнеупоров. На рис. 17.8 показаны разрезы рабочего пространства ДСП с огнеупорной футеровкой (рис. 17.8, а) и с водоохлаждае-мыми элементами (рис. 17.8, б и в).
В итоге проведение длительного восстановительного периода в печи с интенсивным охлаждением стен и свода (соответственно с большими потерями тепла) становится нерациональным. Таким образом, окончание третьего этапа в развитии электросталеплавильного производства связано с пониманием того, что рациональное использование ДСП — это применение данного типа печей как агрегата для расплавления шихты и получения полупродукта (т. е. отказ от проведения всех технологических операций с металлом непосредственно в печи), перенос необходимых операций с целью доводки металла (для получения стали той или иной марки) из печи в ковш или какой-то дополнительный агрегат.

Рис. 17.6. Схемы конструкций ДСП, загружаемых сверху (а и б), и общий вид ДСП с отворотом свода (в) (см. в на цветной вклейке)

Рис. 17.7. Схемы выпуска металла из ДСП: а — традиционная; 6 — сифоном; в — через донное отверстие; г — через отверстие в эркере
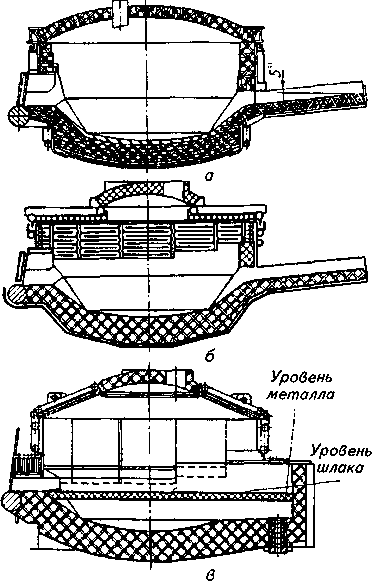
Рис. 17.8. Рабочее пространство ДСП с огнеупорной футеровкой (а) и с водоохлажда-емыми элементами (б и в)\ система водяного охлаждения ДСП (г); водоохлаждаемый свод печи (д); организация продувки металла снизу (е); схема современной ДСП (ж)', вид на ДСП в сталеплавильном цехе (з) (рис. 17.8, г—з см. на цветной вклейке) Так определился четвертый этап в развитии электросталеплавильного производства — этап массового производства электростали с использованием ДСП новых конструкций и последующей обработкой получаемого полупродукта вне печи. В настоящее время в России (и в мире) работают ДСП, созданные и на втором, и на третьем, и на четвертом этапах развития электрометаллургии (рис. 17.8, е).
17.3. ПЕРЕМЕННЫЙ ИЛИ ПОСТОЯННЫЙ ТОК? Успехи в развитии техники преобразования энергии, появление источников постоянного тока большой мощности, достижения огнеупорной промышленности, обеспечившие высокую стойкость подины, в которой смонтирован подовый электрод, привели к созданию ряда удачных конструкций ДСП постоянного тока (рис. 17.9, а, б).
Для питания постоянным током используют как тиристорные, так и диодные преобразователи. Разработан ряд конструкций токопроводящих узлов подины и подовых электродов с воздушным или водяным охлаждением, в том числе одностержневых, многостержневых, многопластинчатых (рис. 17.10).
Обычно приводят следующие преимущества печей постоянного тока по сравнению с печами переменного тока: меньший удельный расход электродов; снижение уровня фликкера1; возможность подводить большую мощность; надежность электрооборудования; работа с длинными дугами; перемешивание ванны за счет электродинамических сил; упрощение технического обслуживания и сокращение трудовых затрат; равномерная тепловая нагрузка на футеровку; снижение уровня шума; стабилизация технологии; лучшее формирование колодцев при их проплавлении; снижение угара легирующих элементов; снижение содержания азота в стали; уменьшение газовыделения и пыле-образования; снижение расхода огнеупоров; повышение производительности.
Однако, несмотря на широко рекламируемые преимущества печей постоянного тока, некоторые фирмы предпочитают устанавливать новые трехфазные печи. Причина в следующем: ниже капитальные затраты на печь переменного тока; практически одинаковый суммарный расход электроэнергии; сближение показателей по торцовому расходу электродов и воздействию на питающую сеть высокоимпеданс-ных трехфазных печей и печей постоянного тока; большая гибкость в регулировании температуры ванны у печей переменного тока. 1 От англ, flicker— мерцание.

Рис. 17.9. Схемы дуговых печей переменного (а) и постоянного (б) тока (1 — электроды; 2 — свод; 3— рабочее окно; 4— ванна; 5— механизм наклона; 6— сливной желоб; 7— корпус; 8 — подовый электрод— анод); система быстрой замены анода на ДСП постоянного тока (в)
(см. на цветной вклейке)
Вполне вероятно, что в ближайшем будущем продолжится соревнование дуговых печей постоянного и переменного тока, будут строиться и те и другие печи (может быть, в большем количестве дуговые печи постоянного тока).
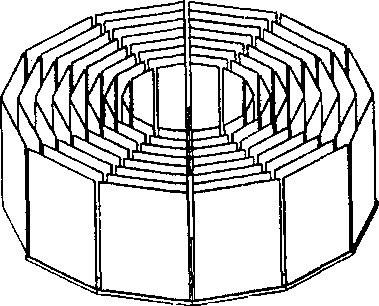
Рис. 17.10. Многопластинчатый подовый электрод
17.4. ТЕХНОЛОГИЯ ПЛАВКИ СТАЛИ В ОСНОВНОЙ ДСП Организация технологических процессов в ДСП малой и средней емкости основывалась на следующих моментах:
1) возможность сравнительно быстро и без больших потерь нагреть и расплавить необходимое количество (иногда весьма значительное) легирующих добавок и раскислителей;
2) возможность провести восстановительный период плавки, добиться получения металла с очень малым содержанием кислорода, успешно провести операцию десульфурации под высокоосновным малоокисленным шлаком;
3) возможность получения стали и сплавов нужного (даже весьма сложного) состава (включая операции, связанные с отбором проб, их анализом, вводом корректирующих добавок и т. п.) и нужной (иногда весьма высокой) температуры непосредственно в самой печи.
В СССР существовала практика, при которой техническое управление министерства, в подчинении у которого находилось данное предприятие, утверждало типовые инструкции, на основе которых составлялись уже заводские инструкции. Типовая технология выплавки стали в основных дуговых печах предусматривала возможность ведения плавки двумя способами: 1) с полным окислением и применением свежих легирующих; 2) методом переплава легированных отходов (как без окисления, так и с окислением технически чистым кислородом).
По первому варианту шихту рекомендовалось составлять с таким расчетом, чтобы содержание углерода в ванне по расплавлении обеспечило выгорание в процессе окисления не менее 0,3 % С при выплавке высокоуглеродистых сталей и не менее 0,4 % С при выплавке средне- и низкоуглеродистых сталей. После полного расплавления шихты скачивают 75—80 % шлака, дают в печь известь и плавиковый шпат и начинают окислительный период с целью дегазации металла, удаления фосфора, очищения от неметаллических включений и повышения до требуемого уровня температуры металла. Окисление ведется посредством подсадок железной руды или продувки ванны кислородом и заканчивается при достижении в ванне содержания углерода, несколько меньшего, чем нижний предел марочного состава стали (с учетом содержания углерода в ферросплавах, которые будут вводиться на последующих этапах). Окислительный шлак скачивается «начисто» (очень тщательно). При введении окислителей в ванну окисляются кремний (в основных печах до следов), марганец и фосфор (в зависимости от содержания этих элементов в шихте), углерод (до пределов, определяемых маркой стали).
После полного скачивания окислительного шлака начинается наиболее ответственный период электроплавки — раскисление металла и доведение его химического состава до заданного для данной марки стали — восстановительный период (рафинировка). Присадками извести, плавикового шпата и шамотного боя (в соотношении приблизительно 5 : 1 : 1) в количестве 2,5—3,5 % от массы металла в печи наводят шлак, который затем раскисляют присадками смеси из извести, плавикового шпата и раскислителя. В качестве раскислителей используют молотый кокс, ферросилиций, алюминий. Начинается диффузионное раскисление стали, в процессе которого содержание оксидов железа в шлаке снижается до значений 1 % (FeO).
В печах малой емкости сравнительно легко можно герметизировать рабочее пространство печи. При наличии высокоосновного шлака и повышенном расходе кокса (2—3 кг/т стали) в зоне высоких температур идет реакция с образованием карбида кальция: (СаО) + ЗС = (СаС2) + СО. Такой шлак называют карбидным. Наличие карбидного шлака — показатель нормального протекания восстановительных процессов. Выдержка металла под восстановительным шлаком обеспечивает получение глубокораскисленного металла и благоприятствует протеканию реакции десульфурации [S] + (СаО) + Реж = (CaS) + (FeO); константа реакции К = а(CaS) ∙а (FeO)/[S] ∙ а(СаО) , т.е.
[S] = (l/K)а (caS)а (FeO)/а (CaO). Таким образом, при малых значениях а(FeO) и больших а(СаО) обеспечивается высокая степень десульфурации.
Карбидный шлак хорошо смачивает металл (и плохо от него отделяется). Во избежание возможных загрязнений металла шлаковыми включениями в процессе выпуска и разливки обычно перед выпуском открывают рабочее окно печи и за счет подсоса воздуха в печь происходит окисление CaQ, но шлак остается высокоосновным и малоокисленным. При охлаждении такой шлак (до 60 % СаО и менее 1 % оксидов железа и марганца) рассыпается в порошок белого цвета, образуется так называемый «белый шлак» -{карбидный шлак серого цвета). Во многих случаях плавку вообще ведут под белым шлаком (без стадии образования карбидного шлака).
В восстановительный период содержание азота в стали возрастает (нет реакции окисления углерода). Это недостаток технологии. Необходимо также иметь в виду повышенную растворимость азота в восстановительных шлаках (в белых 0,03-0,06 %, а в карбидных —до 0,2%). Содержание азота в электростали выше, чем в конвертерной.
По второму варианту при ведении плавки методом переплава окислительный период сводят к минимуму, проводя лишь короткую продувку кислородом для некоторого обезуглероживания, дегазации и нагрева металла. Рафинировку металла в восстановительный период проводят так же, как при плавке с полным окислением.
Учитывая, что при такой технологии трудно удалить из металла фосфор, особое внимание уделяется чистоте шихты. Обычно она составляется из прокатной обрези легированных сталей и некоторого количества отходов низкоуглеродистых (мягких) сталей, содержащих мало фосфора1. 1 В настоящее время в связи с переходом на непрерывную разливку масса прокатных отходов легированных сталей существенно сократилась. Помимо отмеченных выше существует ряд вариантов технологии ведения плавки в ДСП, например: 1) используют продувку ванны смесью 65 % извести, 25 % железной руды и 10 % плавикового шпата (несущий газ — кислород), которая обеспечивает снижение содержания фосфора в металле до следов (расход смеси 2,5-3,0 % от массы садки); 2) на крупных печах, где затруднено проведение восстановительного периода, принимают меры для ускорения шлакообразования (загрузка в печь железной руды или агломерата и извести, продувка кислородом, обновление шлака и присадки извести и др.), добиваясь получения низких содержаний фосфора и требуемых содержаний углерода, а окончательное раскисление и легирование проводят в ковше. Такую технологию называют одношлаковой', 3) оставляют часть (10—15 %) жидкой стали в печи. Эта мера позволяет эффективно использовать конечный высокоосновной шлак, сократить расход шлакооб-разующих, ускорить процесс плавления, снизить расход энергии. Несмотря на снижение массы порции выпускаемого металла, производительность печи не снижается. Такой метод работы металлурги называют работа на болоте.
В технологии работы на современных высокопроизводительных («высокомощных») печах предусмотрено проведение доводки металла вне самой печи. Однако как в нашей стране, так и во многих странах мира работают сотни ДСП малой и средней емкости, в которых выплавляются качественные легированные и высоколегированные стали с использованием традиционных технологий получения готовой стали непосредственно в самом агрегате.
Для высокомощных ДСП современная технология выплавки стали включает следующие основные элементы.
1. Работа на болоте (или жидкий старт) — начало плавки основано на использовании остатка расплава предыдущей плавки. При этом: а) остаток металла закрывает подину, т. е. защищает ее от опасности прожога мощными дугами; б) остаток шлака способствует более легкому шлакообразованию в последующей плавке; в) обеспечивается возможность эффективной подачи кислорода с самого начала плавки; г) обеспечивается возможность увеличить среднюю потребляемую мощность путем устранения ограничений начального периода плавления; д) улучшаются условия более надежной отсечки шлака; е) создаются самые благоприятные условия ведения плавки при использовании в качестве шихты непрерывно загружаемых металлизованных материалов (окатышей и др.).
2. Интенсивное перемешивание путем организации продувки ванны снизу, через подину (см. рис. 17.8, ж).
3. Организация вспенивания шлака, чему способствуют получение шлака оптимального состава, вдувание угольного порошка и продувка кислородом (или использование ме-таллизованных окатышей, содержащих и углерод, и кислород). Вспенивание обеспечивается протеканием реакции обезуглероживания с образованием пузырьков СО.
4. Применение топливно-кисло-родных горелок — в основном в зонах межэлектродных пространств со сравнительно меньшим тепловым потенциалом («холодные» зоны).
Перечисленные технологические моменты являются составной частью общей технологии высокого уровня (ТВУ) работы ДСП. Основными признаками ТВУ являются: а) ДСП предназначена только для расплавления шихты и выплавки полупродукта, а рафинировочные операции, легирование, доводка по составу и т. д. осуществляются вне печи методами внепеч-ной обработки (см. гл. 19); б) к ТВУ относятся и подготовка шихты, и организация выпуска металла, и вопросы контроля и автоматизации процесса. Особый вопрос — об использовании в шихте чугуна. Чугун (как шихтовый материал) имеет ряд достоинств: во-первых, содержит мало примесей цветных металлов, что очень важно при производстве ряда высококачественных сталей; во-вторых, химический состав используемого чугуна известен, что важно при шихтовке плавки; в-третьих, он имеет высокую «насыпную» (твердый чушковый чугун) или «наливную» массу (т/м3), что облегчает организацию загрузки печи; в-четвертых, жидкий чугун приносит значительное количество тепла, что позволяет сократить продолжительность плавки, уменьшить расход электроэнергии и т. д.
При всем этом необходимо учитывать, что содержание углерода в чугуне (- 4,5 %) существенно выше, чем при использовании обычного металлолома. Кроме того, чугун дороже амортизационного и бытового лома.
Решение об использовании чугуна принимается с учетом требований к качеству стали, баланса металла на заводе, соотношения стоимостей чугуна, металлолома, электроэнергии и т. п. Вполне возможно, что практика использования чугуна в качестве шихтового материала будет расширяться. Так, например, в 1996г. на заводе фирмы Cockerill-Sambre в Марчинел-ло (Бельгия) была введена в эксплуатацию 165-т шахтная ДСП постоянного тока с удерживающими лом пальцами, оборудованная системой непрерывной заливки передельного чугуна. Планировалось, что использование жидкого чугуна при плавке стали позволит: использовать избыточные мощности трех доменных печей; повысить качество выплавляемой стали в результате снижения в ней содержания азота и примесей цветных металлов; уменьшить удельный расход электроэнергии; сократить продолжительность плавки и повысить производительность печи.
Заливку чугуна в печь из 120-т чу-гуновозного ковша проводили через желоб, вмонтированный в стену печи.
По стандартной технологии плавки стали 35-40 т жидкого чугуна должно быть залито в период плавления лома со скоростью 2 т/мин. При таком режиме заливки исключаются выбросы металла и обеспечивается равномерное обезуглероживание расплава. Заливку чугуна из ковша проводят с тележки с помощью механизма подъема и наклона ковша; при этом высвобождается крановое оборудование и обеспечивается безопасность работы.
При использовании жидкого чугуна можно включать в шихту низкокачественный лом без изменения содержания меди в выплавляемой стали — менее 0,15%. Концентрация1 азота в стали может быть снижена до менее 40 млн-1 при технологии плавки, включающей вспенивание шлака
. 1 Исчисляется в миллионных долях (1 млн' = 1 ррт). Единственной дополнительной операцией при работе на шихте с жидким чугуном является удаление настылей из желоба и небольшой ремонт его футеровки.
В технологии с использованием чугуна при плавке стали в ДСП достигается увеличение производительности печи (+20 %), снижение расхода электроэнергии на 70 кВт • ч/т (310 кВт • ч/т) и электродов на 0,3 кг/т (1 кг/т). Экономическая эффективность определяется соотношением цен на жидкий чугун и лом и наличием жидкого чугуна.
|
|
|