|
Теория и технология производства стали 1. Учебник для вузов. М. Мир, ООО Издательство act
17.5. СОВРЕМЕННЫЕ ПРИЕМЫ ОРГАНИЗАЦИИ РАБОТЫ ДСП Главные особенности организации работы современных ДСП сводятся к следующему:
1. Переход на двустадийную технологию производства: а) быстрое расплавление в печи металлошихты, окисление углерода и фосфора, удаление окислительного шлака; б) окончательное рафинирование (десульфурация, дегазация и т. п.) и доводка вне печи методами внепечной обработки.
2. Использование мощных и сверхмощных трансформаторов (до 1000 кВ-А/т) и стремление к эффективному использованию этой мощности.
3. Возможно более полное использование тепла отходящих газов для предварительного подогрева металлошихты.
4. Широкое применение для интенсификации процессов нагрева и расплавления металлошихты кислорода и топливно-кислородных горелок (несмотря на повышенный угар шихты).
5. Повсеместное использование устройства для водяного охлаждения отдельных деталей конструкций печи, свода и стенок.
6. Организация непрерывного процесса плавления металлошихты в печи.
7. Стремление получать максимальную часовую производительность агрегата.
новые конструкции ДСП. Дать общую классификацию новых конструктивных решений пока еще затруднительно. Приведем несколько характерных примеров.
17.5.1. Топливно-дуговой сталеплавильный агрегат (и двустадийный топ-ливно-дуговой сталеплавильный процесс в нем) разработан Челябинским научно-исследовательским институ-
том металлургии (Россия) на основании опыта комбинированного использования в дуговых печах электроэнергии, газообразного и твердого топлива, а также теплоты отходящих технологических газов для предварительного высокотемпературного нагрева лома. В топливно-дуговой сталеплавильный агрегат входят ДСП и многокамерный шахтный водоохлаж-даемый подогреватель лома (рис. 17.11). Печь оборудована эркерными топливно-кислородными горелками мощностью по 25—30 МВт каждая и фурмами для вдувания угля и кислорода. В стенах печи установлены также кислородные фурмы для дожигания технологических газов.
Плавка в топливно-дуговом агрегате проводится в две стадии. На пер-
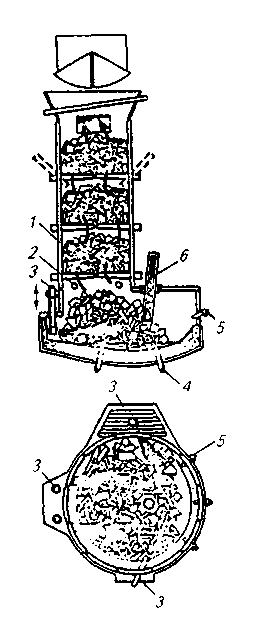
Рис. 17.11. Топливно-дуговой сталеплавильный агрегат:
/ — шахта; 2—газо-воздушные горелки; 3— высокомощные вращающиеся топливно-кислородные горелки; 4— подовые фурмы для вдувания угля и кислорода; 5— стеновые кислородные фурмы; 6— внецентренный графитированный электрод вой стадии лом, уже подогретый до 700 "С в нижней камере шахты, нагревается в объеме печи до температуры плавления только за счет сжигаемого в кислороде топлива (природного газа и угольной пыли). На второй стадии расплавление шихты и нагрев жидкой ванны проводятся при одновременном использовании электроэнергии и порошкообразного угля. За 4 мин до выпуска плавки с целью гомогенизации состава ванны и выравнивания ее температуры вдувание угля прекращают и плавку доводят только на электрических дугах. Для 100-т печи расчетная производительность 900 тыс. т/год.
За счет высокотемпературного нагрева лома технологическими газами и использования больших количеств топлива расход электроэнергии может быть снижен до 180 кВт-ч/т, расход электродов — до менее 1,2 кг/т. При этом по сравнению с обычной ДСП затраты первичной энергии на выплавку стали могут быть уменьшены в 1,5—1,6 раза, что способствует не только повышению экономической эффективности процесса, но и улучшению экологии.
17.5.2. Двухэлектродная дуговая печь постоянного тока разработана фирмами Японии и Швейцарии. Первая такая печь емкостью 250т (мощностью 100 MB • А, производительностью 0,8 млн т/год) введена в эксплуатацию на заводе фирмы Tokyo Steel в 1996 г. Установка состоит из двух основных элементов: овальной печи и системы загрузки лома (рис. 17.12). В последнюю входят криволинейный шахтный подогреватель и загрузочное устройство с двумя толкателями, расположенными на разных уровнях. Лом из бункера поступает в шахту и нагревается технологическими газами до температуры 800 °С (температура выходящих газов около 200 °С).
Печь оборудована двумя верхними графитовыми электродами и двумя подовыми электродами, выполненными из токопроводящих огнеупоров. Дуги отклонены к центру печи, куда загружается лом; этим достигается уменьшение тепловой нагрузки стен, в результате можно не устанавливать стеновые панели и снизить теплопоте-
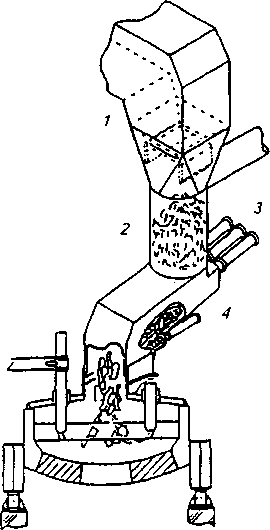
Рис. 17.12. Двухэлектродная ДСП постоянного тока:
1 — бункер; 2— шахта; 3 — верхний толкатель; 4 — нижний толкатель ри печи. Печь работает с очень большой массой оставшегося от предыдущей плавки расплава (110т при массе выпускаемой плавки 140т). Это обеспечивает постоянство условий работы печи (имеются в виду температура металла, подводимая мощность, газовыделение, температура технологических газов). Загрузка лома в шахту полностью автоматизирована и основана на контроле уровня лома в шахте. Автоматизированы процессы вдувания кислорода, углерода, шлакообразую-щих, управление перемещением графитовых электродов.
Преимуществами такой печи являются: 1)расход электроэнергии 260 кВт • ч при расходе вдуваемого угля 25 кг и кислорода 33 м3 на 1 т стали; 2) снижение уровня шума (на 15— 20 дБ по сравнению с обычной дуговой печью постоянного тока); 3) снижение фликкера на 50—60 % по сравнению с одноэлектродной дуговой печью постоянного тока; 4) уменьшение пылевыделения; 5) высокая доля токового времени плавки.
Так как все операции плавки автоматизированы, ожидается, что печь в комплексе с печью-ковшом будут обслуживать только два оператора.
Двухэлектродные печи постоянного тока конструкции фирмы Danieli работают на заводах фирмы Hylsa (Мексика) в Монтеррее (емкость 135т, мощность трансформатора 208 MB • А, шихта —лом, холодные и горячие ме-таллизованные окатыши) и в Пуэбло.
17.5.3. ДСП постоянного тока Comelt с несколькими наклонными под углом 40° электродами, пропущенными через периферийную часть свода, и с сочлененной со сводом шахтой, где происходит подогрев лома отходящими газами, разработана австрийской фирмой Voest Alpine Industrie-anlagenbau. Опытная печь постоянного тока с четырьмя графитовыми электродами диаметром 250 мм и подовым анодом (рис. 17.13) была сооружена на базе плазменной печи емкостью 50т на заводе в Линце (Австрия). Дуги длиной 0,5—1,2 м горят по оси электродов, образуя в шихте полости длиной до 1,7 м. Лом поступает по транспортеру в верхнюю часть шахты со скоростью около 25 т/мин. После выпуска металла в печь загружают 60— 80 % всей шихты вместе с известью и коксом. Печь оборудована тремя газокислородными горелками и тремя кислородными фурмами для дожигания СО. Каждая пара электродов питается через свой трансформатор мощностью 48 MB • А. Максимальные значения силы тока и напряжения на дуге составляют соответственно 29 кА и 850 В. Печь тщательно герметизирована; отходящие газы проходят через слой шихты. Собираемую пыль можно возвращать в печь, вдувая с током азота через полый электрод. Плавку ведут под вспененным шлаком.
При емкости печи Comelt более 150 т продолжительность плавки должна быть менее 40 мин. При этом по сравнению с обычной дуговой печью общая экономия энергии составит около 100 кВт • ч/т, расход электродов будет на 30 % меньше (0,9 вместо 1,4 кг/т), снизятся удельные капитальные расходы и затраты на ремонт (на 15—20%). Конструкция печи Comelt обеспечивает полное улавливание выделяющихся газов при уменьшении их объема на 70 %, снижение шумовыде-ления на 15—20 дБ, уменьшение фликкера.
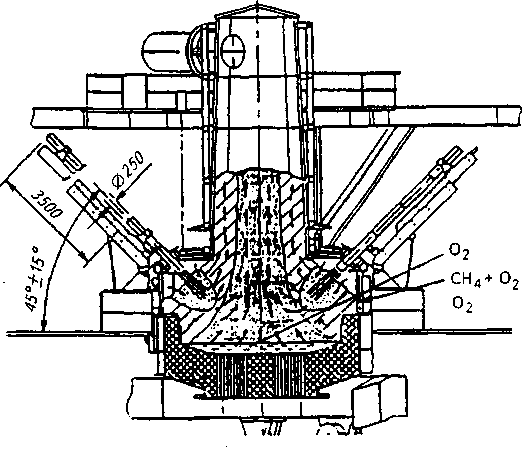
Рис. 17.13. ДСП постоянного тока Comelt 17.5.4. ДСП Consteel постоянного тока с непрерывной загрузкой металло-шихты, подогретой в тоннельной печи отходящими газами (рис. 17.14), впервые была введена в эксплуатацию в 1990г. на заводе фирмы Florida Steel, США. Емкость печи 74т, производительность 54 т/ч при мощности трансформатора 24 МБ • А. За время работы процесс был значительно усовершенствован: исключены топливно-кисло-родные горелки для подогрева лома в тоннельной печи, изменена система охлаждения конвейера, расходуемые кислородные фурмы заменены на во-доохлаждаемые, введен свод над загрузочной частью нагревательной печи. В результате в 1995 г. средний удельный расход электроэнергии составил 389 кВт•ч/т, кислорода — 22 м3/т (без использования природного газа), электродов—1,7 кг/т. При подогреве лома до 540 °С получена экономия расхода электроэнергии 109 кВт • ч/т стальной заготовки.
Аналогичные печи введены в эксплуатацию на заводах Kyoei Stell, Япония (печь постоянного тока с трансформатором мощностью 51 МВт, емкостью 192т), Nucor Steel, США (печь постоянного тока с трансформатором мощностью 39 МВт) и Jersey Steel, США (печь переменного тока с трансформатором мощностью 35 МВт).
Производительность этих печей составила соответственно 120; 92 и 82 т/ч при удельных расходах на 1 т стали: электроэнергии 320; 351 и 390 кВт-ч, кислорода 34; 33,4 и 23 м3 и электродов 1,2; 1,3 и 1,75кг.
На установке фирмы Nippon Steel Plant and Machinery Division (Япония) усовершенствован нагрев лома на конвейере. Горячие отходящие газы проходят сквозь слой лома, а не над ним, как в первых печах Consteel, что повышает эффективность нагрева лома.
Преимуществами печи Consteel являются снижение шумовыделения, выбросов пыли на 40 % и значительное снижение издержек производства. К недостаткам этой печи следует отнести необходимость тщательной подготовки металлошихты к загрузке по размерам кусков и большую протяженность эстакады для загрузочного конвейера.
17.5.5. Шахтная дуговая печь с удерживающими пальцами разработана фирмой Fuchs Systemtechnik, Германия (рис. 17.15). Шахта этой печи в нижней части оборудована водоох-лаждаемыми пальцами, удерживающими лом уже в период рафинирования предыдущей плавки. После выпуска стали пальцы «открываются» и горячий лом падает в жидкую массу
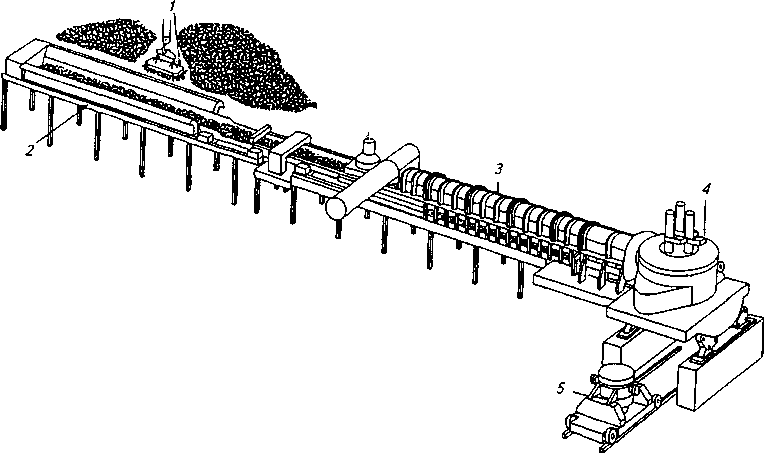
Рис 17.14. ДСП Consteel:
1 — магнитный кран; 2 — загрузочный конвейер; 3 подогреватель; 4 — печь; 5—сталевоз
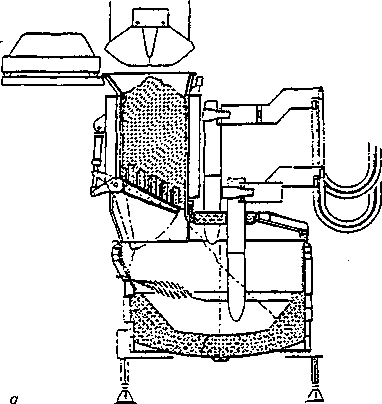
Рис. 17.15. Шахтная ДСП с удерживающими пальцами и непрерывной подачей металлошихты:
и —схема; б— реконструкция обычной ДСП; в —
общий вид в цехе (см. рис. 17.15, б, в на цветной
вклейке) металла и шлака, оставшихся от предыдущей плавки, затем сразу в.шахту загружается вторая корзина.
При плавке стали в этой печи в шихту могут входить металлизованные окатыши, твердый или жидкий чугун либо 100 % лома. Показатели работы шахтных печей с удерживающими пальцами очень высоки, поэтому они быстро нашли применение во всем мире; в 1996г. в эксплуатацию введены две такие печи, в 1997г.—три, в 1998 г. — шесть печей и т. д. В августе 1998г. 120-т печь такой конструкции (мощность трансформатора 85 MB • А) пущена в России на комбинате «Северсталь» (г. Череповец).
В результате дальнейшего развития шахтной дуговой печи с удерживающими пальцами появилась двухкамерная шахтная дуговая печь с удерживающими пальцами типа MSP (Multistage Scrap Preheater — многокамерный подогрев лома) конструкции фирмы Mannesmann Demag Metallurgy, Германия. Лом в шахте этой печи подогревается в двух камерах, разделенных удерживающими пальцами, что гарантирует более полное ис-
пользование теплоты дожигания технологических газов. При работе на шихте, состоящей только из лома, расход электроэнергии в такой печи составляет менее 290 кВт • ч/т. Печь рассчитана на использование в шихте жидкого чугуна, что позволит дополнительно уменьшить расход электроэнергии. На рис. 17.16 показана схема двухкамерной (двухкорпусной) 135-т печи постоянного тока с удерживающими пальцами с трансформатором мощностью 156 MB • А. Печь установлена в Монтеррее (Мексика). В шихте используется до 55 % металлизованных окатышей.
Стремление в максимальной степени использовать мощность трансформатора, тепло, аккумулированное кладкой, и тепло отходящих газов привело к созданию серии конструкций двухкорпусных и двухшахтных ДСП.
Двухкорпусная дуговая печь с одним источником питания, электродом-катодом (тремя электродами на печи переменного тока) и короткой сетью имеет две ванны: когда в одной идет расплавление металлошихты дугами, другая находится в режиме загрузки и подогрева шихты. Двухкорпусная печь с одним источником пи- Рис. 17.16. Шахтная ДСП (с удерживающими пальцами) постоянного тока:
/ — окатыши + известь + углерод; 2 —нагретый
лом; 3 — две фурмы; 4— четыре горелки (О2 + СН4);
5— охлажденные газы СО2/02
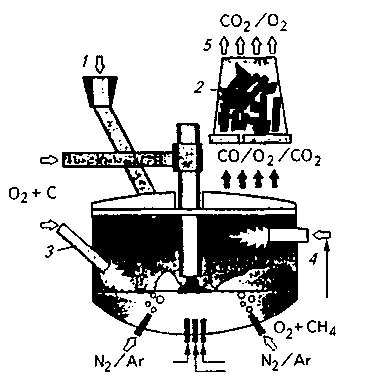 тания может иметь два комплекта то-коподвода и электродов (рис. 17.17) отдельно для каждого из корпусов, что позволяет еще более сокращать бестоковое время работы печи. На установке используют два способа подогрева лома: первый заключается в подаче технологических газов из находящегося под нагрузкой корпуса в «отключенный» корпус; при втором способе лом подогревают с помощью топливно-кислородных горелок, установленных в корпусах.
Использование двухкорпусных печей позволяет увеличить производительность при существующей мощности трансформатора или уменьшить мощность трансформатора при существующей производительности.
Двухкорпусная печь по сравнению с двумя печами той же емкости обеспечивает большую экономию капитальных затрат (минимум 35 % без учета расходов на сооружение подстанции), а также сокращение продолжительности плавки на 40 % и снижение расхода электроэнергии на 40— 60 кВт • ч/т. Двухкорпусные печи работают во многих странах (в Японии, США, Франции, Индии и др.). В зависимости от величины садки, мощности трансформатора, типа шихты (лом, горячие железосодержащие брикеты, твердый чугун, жидкий чугун и т. п.) производительность таких печей колеблется в пределах 1,0—1,6 млн. т/год.
Разновидностью двухкорпусных ДСП являются двухшахтные печи. В качестве примера на рис. 17.18 представлена работа двухшахтной печи завода SAM Montereau.
Две зеркально установленные шахтные печи емкостью по 90 т обслуживаются одним трансформатором мощностью 96 MB • А с одной системой электродов. Печь оборудована 12 горелками (по 6 на каждый корпус) мощностью по 3 МВт, четырьмя манипуляторами, системами управления дугами, перемешивания аргоном, по-
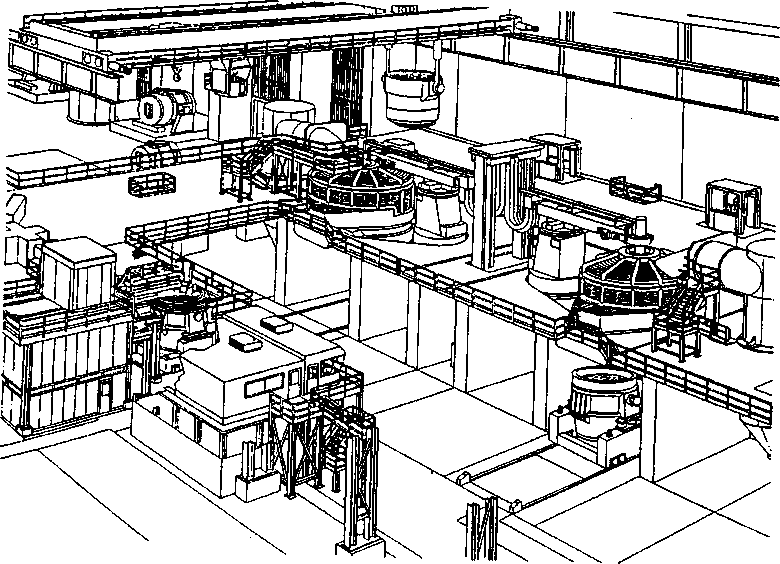
Рис. 17.17. Двухкорпусная ДСП постоянного тока с диаметром кожуха 7,6 м фирмы Gallatin
Steel, США
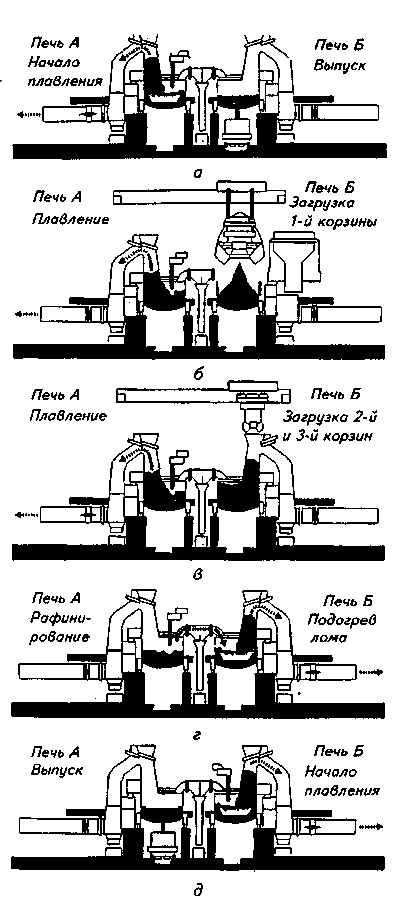
Рис. 17.18. Схема работы двухшахтной ДСП
дачи извести и углеродсодержащих материалов. Четыре горелки расположены в шахте, одна — в рабочем окне и одна — вблизи выпускного отверстия. В подине установлено пять пористых вставок для продувки ванны азотом. Своды снабжены соединительными патрубками с трехходовым краном дроссельного типа, позволяющим направлять часть отходящих газов от одной печи в другую. Последовательность работы двухшахтной печи представлена на рис. 17.18, а — д.
При выпуске плавки из печи Б электрододержатель перемещается к печи А, где начинается расплавление шихты. На начальной стадии расплавления шихты в печи А в печи Б начинается загрузка. В этот период в печь Б загружают 75 % завалки. Горелки в печи Б работают на полную мощность. Когда в печи А идет рафинирование металла, отходящий газ направляют в печь Б для подогрева лома на подине и в шахте. В это время в шахту печи Б загружают остаток лома. Когда печь А готова к выпуску плавки, печь Б должна быть полностью загружена ломом, чтобы избежать перерывов в энергоподводе. Время вспомогательных операций при такой работе уменьшается до 3 мин и время под нагрузкой достигает 92 % плавки. В 1995 г. средние удельные расходы на двухшахтной ДСП этой фирмы при массе плавки 95 т составили: электроэнергии 365 кВт • ч, электродов 1,45 кг, кислорода 30,0 м3, природного газа 8,0м3, загружаемого угля 11,5кг, угольного порошка 5,0 кг. Производительность печи составила 105 т/ч.
Появляются все новые варианты конструкций двухкорпусных агрегатов.
Сочетание преимуществ конвертерного и электросталеплавильного производств может быть получено при использовании Arcon-процесса, разработанного фирмой Concast Standard AG, Швейцария. Arcon (Arc in converter) — двухкорпусный агрегат, состоящий из конвертера с верхней кислородной продувкой и одноэлект-родной ДСП постоянного тока (рис. 17.19). В каждом из корпусов кислородная фурма 1 может быть заменена общим графитированным электродом 2 и наоборот. Размеры корпусов соответствуют размерам типового конвертера. Днище каждого корпуса выполнено из электропроводных пе-риклазографитовых огнеупоров и имеет подовый пластинчатый медный электрод. Для футеровки стен корпуса использованы периклазографитовые огнеупоры. Выпускное отверстие расположено в периферийной части то-копроводящей подины.
271 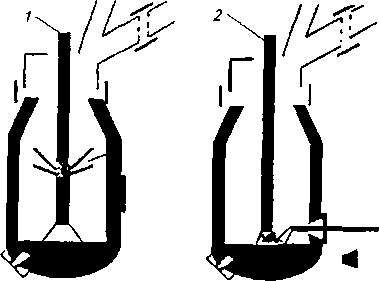
Рис. 17.19. Двухкорпусный агрегат Агсоп Чугун заливают через горловину корпуса или с помощью желоба через боковое окно, являющееся частью футеровки корпуса. Окно при работе корпуса по режиму дуговой печи служит для ввода фурм для вдувания извести, угля и кислорода, манипулятора и спуска шлака. Общий для обоих корпусов графитированный электрод крепится на электрододержателе, расположенном между корпусами со стороны выпускного отверстия. Кислородные фурмы, отдельные для каждого из корпусов, имеют дополнительные боковые сопла для вдувания кислорода на дожигание СО технологических газов. Электрическое питание агрегата осуществляют с использованием шестипульсного выпрямительного блока, обеспечивающего подвод тока силой до 80 кА. Подстанция с печным трансформатором и выпрямительным блоком расположена рядом с агрегатом. Помещение для управления работой корпусов общее, однако каждый корпус оснащен самостоятельным комплексом контрольно-измерительных приборов.
Агрегат Агсоп имеет производительность 1,6 млн. т/год. В качестве металлошихты используют жидкий чугун (40 %), гранулированный чугун (5 %) и горячебрикетированное губчатое железо (55 %). Масса выпускаемой плавки 170т (170т стали выпускают каждые 46 мин), продолжительность работы агрегата 7300 ч в год. Цикл работы агрегата составляет 92 мин. Технология основана на использовании оставленного от предыдущей плавки жидкого расплава массой 50 т, т. е. емкость каждого корпуса 220т жидкой стали.
После выпуска плавки (в течение 5 мин) из корпуса № 1 проводят осмотр и текущий ремонт шиберного затвора, выпускного отверстия и т. п На оставшуюся от предыдущей плавки жидкую массу стали и шлака загружают ферроалюминий или ферросилиций для предотвращения вскипания ванны при последующей заливке чугуна. Затем через желоб заливают 75т чугуна, выводят желоб, закрывают боковое окно, поворачивают кислородную фурму, опускают ее в рабочее пространство и проводят продувку кислородом с интенсивностью 12 тыс. м3/ч в течение 27 мин. По ходу продувки через горловину непрерывно загружают горячебрикетированное губчатое железо (35 т), гранулированный чугун (10 т), известь и доломит.
По окончании продувки фурму поднимают, отворачивают в сторону и на ее место поворачивают электрод от корпуса № 2. Электрод опускают в рабочее пространство, зажигают дугу и ведут дуговой нагрев ванны в течение 37 мин при подводимой мощности 60 МВт. По ходу дугового нагрева непрерывно загружают 70 т горячебри-кетированного губчатого железа. Через боковое окно с помощью фурм манипулятора вдувают порошкообразные известь, домолит и уголь для формирования вспененного шлака. Затем на 7 мин снижают подводимую мощность до 10 МВт и скачивают шлак. Перед выпуском плавки электрод поднимают и переводят на корпус № 2, где в это время заканчивается продувка ванны кислородом.
При такой работе удельный расход электроэнергии составляет 225 кВт • ч, кислорода — 45 м3, электродов — 0,7 кг! Токовое время работы двухкорпусного агрегата достигает 95%.
Комбинация конвертера и дуговой печи в одном агрегате дает следующие преимущества по сравнению с обычной дуговой печью: 1) широкий выбор металлошихты; 2) высокая производительность; 3) низкий расход электроэнергии в результате использования химической энергии окисления при месей металлошихты; 4) уменьшение требуемой электрической мощности; 5) снижение удельного расхода электродов; 6) меньшее влияние на токо-подводящие сети; 7) возможность работы при маломощных электросетях; 8) снижение затрат на электрооборудование.
Фирма Mannesmann Demag Metallurgy разработала конструкцию двухкорпусной печи переменного тока, подобную печи Агсоп, назвав ее Conarc (Converter-arc-furnace) (рис. 17.20). Эта печь характеризуется гибкостью в выборе сырья и источников энергии. Часть кислорода (до 85 %) вдувается через многосопловую верхнюю фурму с интенсивностью до 330 м3/мин. Расход электроэнергии составляет 187—244 кВт • ч/т.
Приведенные примеры показывают, что современные технологии производства стали в ДСП существенно отличаются от традиционных. При этом возникает ряд проблем и вопросов, на которые пока нет окончательных ответов.
Какая шихта предпочтительнее? Традиционной шихтой ДСП является металлолом. В настоящее время в мире сложился дефицит качественного металлолома (см. гл. 4), который сохранится и в обозримом будущем. Варианты выхода из ситуации: использование губчатого железа и жидкого продукта процессов ПЖВ (см. гл. 7),
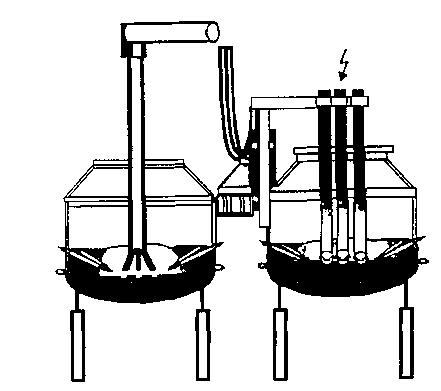
Рис. 17.20. Двухкорпусный агрегат Conarc твердого или жидкого чугуна; получение и использование новых видов металл ошихты. В России — это получение материала суперком (или синти-ком), за рубежом — карбиды железа (см. гл. 4) или новый материал — один из видов первородной шихты, получившей название ITmk3 (Ironmaking-Techono-logy-mark-three — технология получения железа (чугуна) номер три). Первородную шихту ITmk3, содержащую 97-98 % Fe, 2 % С, 0,17 % S, получают восстановлением рудной мелочи углем при 1350—1500 °С. Этот продукт, практически чистое железо, может быть получен в жидком виде или в виде дроби.
В каждом конкретном случае технологи принимают решение сами. В некоторых электросталеплавильных печах, расположенных вблизи от «источника» чугуна, его эффективнее использовать жидким, так как при этом обеспечивается поступление значительного количества тепла (100 кВт • ч/т и более), уменьшение расхода электроэнергии, электродов и снижение уровня остаточных примесей при повышении производительности печи. В некоторых случаях целесообразно получать чугун в вагранках с кислородным дутьем, так как в этом случае снижаются расходы на очистку отходящих газов, создаются условия для переработки загрязненного лома и появляется возможность уменьшить нагрузку на систему очистки газов дуговой печи. Еще более перспективно использование жидкого чугуна, получаемого на установках ПЖВ.
Пути снижения расхода электроэнергии. Удельный расход электроэнергии при плавке стали в ДСП зависит от таких факторов, как: 1) конструкция и емкость печи, мощность трансформатора; 2) наличие сырьевых материалов; 3) портфель заказов; 4) технология плавки; 5) дожигание технологических газов; 6) вдувание кислорода; 7) предварительный подогрев лома; 8) автоматизация процесса; 9) использование альтернативных источников энергии и т. д. Удельный расход электроэнергии на печах постоянного или переменного тока (однокорпусных или двухкорпус-ных) примерно одинаков. Различие вносят только операции дожигания
ЛТО технологических газов и подогрева шихты (шахтные печи и печь Consteel), которые способствуют снижению расхода электроэнергии во всех случаях. Минимальный расход электроэнергии на двухэлектродных печах постоянного тока и печах Contiarc обусловлен большей эффективностью электрических дуг и уменьшением теплопотерь при большей газоплотности печей. Снижение удельного расхода электроэнергии до уровня менее 200 кВт • ч/т при работе двухкорпусных печей по технологии Агсоп или Сопагс получено за счет тепла, вносимого жидким чугуном.
Расход электроэнергии заметно снижается при использовании газокислородных горелок и кислородных фурм (или «копий») в процессе расплавления металлошихты. Однако при этом существенно возрастает угар металла, достигая 6-8 % и более. При решении вопроса об использовании таких способов интенсификации процессов необходимо анализировать структуру себестоимости стали и влияния на нее как оплаты труда персонала, так и стоимости металлошихты.
На рис. 17.21 представлен вариант расчета общего расхода энергии для трех технологических схем сталеплавильных процессов. В соответствии с данным вариантом минимальный расход энергии имеет место при переработке в ДСП металлолома.
Проблема электродов. На ДСП применяют, как правило, графитирован-ные электроды (они дороже, чем угольные, но обладают более высокими свойствами по таким показателям, как плотность, механическая прочность, теплопроводность, допустимая плотность тока, температура окисле-
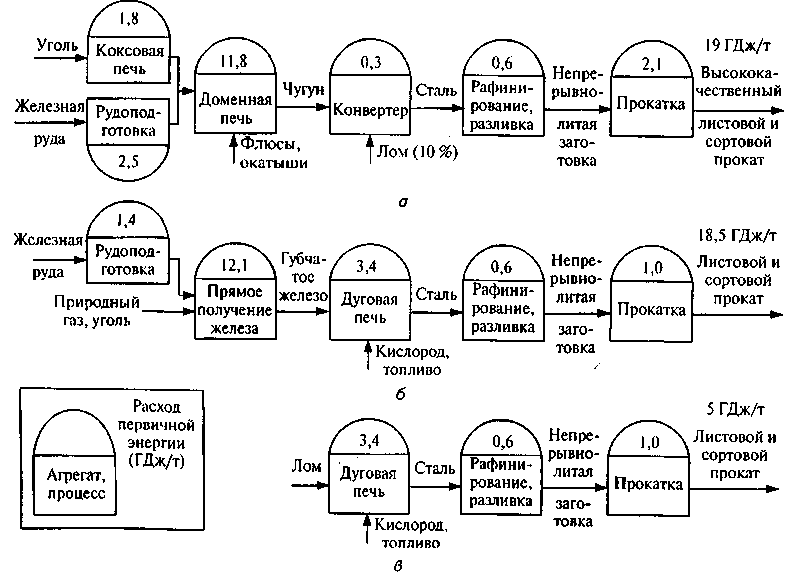
Рис. 17.21. Удельный расход энергии (ГДж/т жидкой стали) на отдельных стадиях процессов по трем схемам производства стали-проката:
а - интегрированный металлургический завод производительностью 3-5 млн. т/год; б -завод производительностью 1—2 млн. т/год, работающий по схеме прямое получение железа — электроплавка; в — мини-завод производительностью 0,5-1,0 млн. т/год ния). Расход электродов для ДСП, работающих по традиционной технологии, 5—6 кг/т стали; затраты на электроды составляют 8—15 % себестоимости стали, поэтому снижение расхода электродов — важная производственно-экономическая проблема.
Такие приемы, как покрытие поверхности электродов защитными составами или использование водяного охлаждения срединной полости электрода, позволяют снизить расход электродов. Естественно, что расход электродов снижается (при их хорошем качестве) по мере повышения производительности ДСП. Расход электродов в современных высокопроизводительных ДСП 1—3 кг/т стали (на ДСП постоянного тока расход электродов несколько ниже, чем на ДСП переменного тока).
На мощных современных ДСП требуются электроды большого диаметра — более 600 и даже 700 мм. По отечественному ГОСТ 4426—71 диаметр электродов составляет от 75 до 555 мм. Производство качественных электродов больших диаметров требует сложной технологии. В настоящее время электроды диаметром 600 мм и более производятся всего в нескольких промышленно развитых странах.
Как решать проблемы ресурсосбережения и экологии? Высокомощные ДСП характеризуются значительным выделением пыли. На шахтных печах выделение пыли ниже; меньше пыли выделяется на ДСП постоянного тока. Однако проблема улавливания пыли остается для печей всех конструкций. При этом важными являются, по крайней мере, три момента, которые приходится иметь в виду:
а) по мере усиления средств газо-пылеотсоса увеличиваются скорости газовых потоков в объеме печи, что, в свою очередь, отрицательно влияет на угар металла и электродов;
б) в последние годы для России характерно заметное увеличение автопарка, например, возросло число зарубежных автомашин, на которых обычно более основательна антикоррозионная обработка с использованием цинковых покрытий и др.; растет доля соответствующего металлолома, и улавливание пыли становится более
целесообразным и с экономической точки зрения (см. п. 25.10.3);
в) последние годы характеризуются непрерывным ростом использования различных пластиков, полихлорвиниловых покрытий и т. п. Соответствующие отходы попадают с металлоломом в печь, т. е. в процессе нагрева в печи образуются различные летучие органические соединения, в том числе диоксины и фураны (см. гл. 26). Решать эту проблему очень трудно, но необходимо. Эти вопросы более подробно рассмотрены ниже, в материалах шестой части.
17.6. ТЕХНОЛОГИЯ ПЛАВКИ СТАЛИ В КИСЛЫХ ДСП Футеровка кислых ДСП аналогична футеровке кислых мартеновских печей и состоит из почти чистого кремнезема; соответственно шлаки кислых печей насыщены SiO2. Ни серу, ни фосфор удалить из металла под кислым шлаком нельзя, и это должно учитываться при шихтовке плавки. В кислых печах сталь обычно выплавляют методом переплава с проведением короткого периода кипения для дегазации расплава. Кислые шлаки менее проницаемы для газов, чем основные; растворимость газов в кислых шлаках также меньше. В кислых шлаках низка активность FeO (основного оксида). При повышении температуры восстанавливается кремний, например, по реакциям
SiO2 + 2[C] = [Si] + 2CO-Q;
К=[Si] ∙Р2СО/a(Si02).[C]2,
откуда
[Si]= К.a(Si02) ∙ [C]2/Р2СО.
ї
В кислых шлаках, насыщенных SiO2, а(SiО2) приближается к единице, поэтому скорость восстановления кремния может быть весьма заметна (до 0,01 %/мин), особенно при высоком содержании углерода. О мерах регулирования этого процесса см. разд. 16.9.
В связи с отсутствием условий для десульфурации и дефосфорации удельная (на 1 т стали) поверхность контакта металл—шлак для кислых печей не имеет такого значения, как для основных, поэтому для уменьшения тепловых потерь можно иметь более глубокую ванну. Меньшая теплопроводность кислых огнеупоров также способствует снижению тепловых потерь и более быстрому нагреву металла. Из-за отсутствия длительных периодов рафинирования металла от фосфора и серы все это приводит к получению более высокого теплового к. п. д., сокращению длительности плавки, уменьшению расходов электроэнергии и электродов. Кислая футеровка и кислые шлаки, большая глубина ванны кислых печей, невысокая стоимость материалов, из которых формируется футеровка (песок, динасовый кирпич), — вот неполный перечень достоинств кислых печей. К недостаткам относится невозможность проводить в печи операции десульфу-рации и дефосфорации. О возможных перспективах развития кислых процессов см. гл. 21.
В настоящее время емкость кислых печей не превышает Ют. Число кислых печей достаточно велико; их устанавливают в литейных цехах и используют в основном для производства фасонного литья.
17.7. ПЛАВКА СТАЛИ В ИНДУКЦИОННЫХ ПЕЧАХ Некоторое количество стали выплавляется в тигельных индукционных печах, в которых расплавляемый металл находится в керамическом тигле, помещенном внутрь многовиткового цилиндрического индуктора (рис. 17.22). Диапазон емкостей современных тигельных индукционных печей весьма велик — от нескольких килограммов (в основном для исследовательских работ в лабораториях) до десятков тонн. Под действием переменного магнитного поля, создаваемого индуктором, в нагреваемом металле индуцируется электродвижущая сила. За счет джоулева тепла, выделяющегося в металле под действием тока, металл нагревается и плавится.
Электромагнитные силы оказыва-
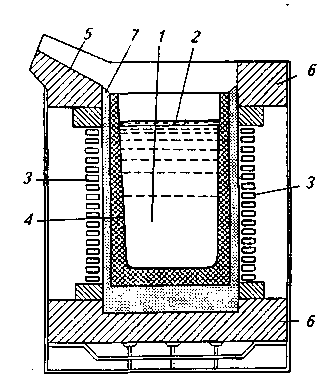
Рис. 17.22. Тигельная индукционная печь:
1 — жидкая сталь; 2— шлак; 3 — водоохлаждаемая катушка индуктора; 4— огнеупорная футеровка; 5— сливной носок; 6 — огнеупорный кирпич; 7—термоизоляция
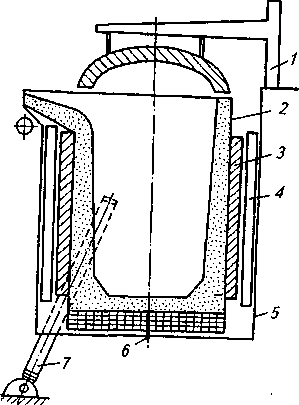
Рис. 17.23. Промышленная тигельная открытая индукционная печь:
1 — механизм подъема и отворота свода; 2 — тигель; 3— индуктор; 4 — магнитопроводы (ферромагнитные экраны); 5— кожух; 6—сигнализатор; 7—механизм наклона ют на жидкий металл статическое и динамическое воздействия, в результате чего верхняя часть металла отжимается от стенок тигля, а во всем объеме возникает электродинамическая циркуляция. Выпуклый мениск затрудняет обработку металла шлаком, поскольку шлак стекает к стенкам тигля; достаточно высокая скорость турбулентного движения металла усиливает износ футеровки. В принципе, если электромагнитные силы достаточно велики и могут уравновесить действие гравитационных сил тяжести, можно осуществить индукционную плавку во взвешенном состоянии, без тигля (бестигельная плавка).
Практически в обычных индукционных печах шлак нагревается от жидкого металла. Если шлак холодный и вязкий, то соответственно нет условий для удаления серы и фосфора. Этот недостаток таких печей в какой-то мере устраняется использованием крышек (рис. 17.23), а в некоторых современных установках — плазменных горелок.
К достоинствам индукционных печей относятся: 1) отсутствие электродов и соответственно отсутствие науглероживания металла; 2) отсутствие дуг и соответственно меньше насыщение металла азотом и водородом; 3) перемешивание металла; 4) возможность выплавлять металл в любой контролируемой атмосфере и вообще в вакууме (рис. 17.24), а соответствен но и малый угар легирующих, отсутствие газов и т. п.
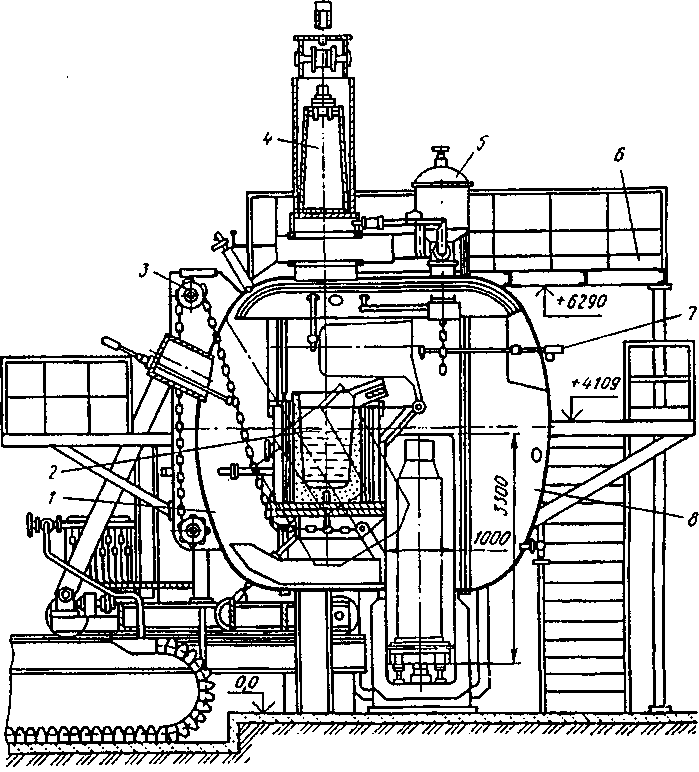
Рис. 17.24. Тигельная вакуумная индукционная печь:
7 8— подвижная и неподвижная части корпуса соответственно; 2— тигель; 3 — механизм наклона; 4— камера загрузки; 5 — дозатор; 6— рабочая площадка; 7— устройство для чистки тигля Другими словами, качество металла, выплавляемого в индукционных печах, в значительной мере определяется качеством шихты. По существу, плавка в таких печах есть переплав чистой, специально отобранной метал-лошихты с добавкой ферросплавов, лигатуры и некоторого количества шлакообразующих добавок.
Футеровка тиглей может быть кислой (кварцевый песок, кварцит) или основной (порошок магнезита или хромомагнезита). В огнеупорах для печей высокой частоты должны отсутствовать токопроводящие и магнитные примеси, так как в высокочастотном поле они нагреются, оплавятся, что может привести к прогоранию тигля. Стойкость основной футеровки может достигать 100 плавок, стойкость кислой футеровки выше. а
18. ПРОИЗВОДСТВО СТАЛИ В АГРЕГАТАХ НЕПРЕРЫВНОГО ДЕЙСТВИЯ Существующие в настоящее время сталеплавильные агрегаты (конвертеры, мартеновские, дуговые, индукционные печи и т. д.) являются агрегатами периодического действия. Из опыта многих производств следует, что замена периодического процесса непрерывным способствует увеличению производительности, снижению эксплуатационных затрат, повышению качества и однородности (стандартности) продукции, уменьшению технологических отходов, более эффективному использованию добавочных материалов. Современная технология позволяет осуществлять непрерывную разливку многих десятков плавок, тысяч тонн стали. Успешными оказались попытки создания непрерывной линии: непрерывная разливка стали —прокатный стан. Производства, смежные со сталеплавильным (доменное, прокатное), по существу, непрерывные. Процессы подготовки железорудного сырья (агломерация и получение окатышей) также являются непрерывными, поэтому вся схема современного металлургического производства, включающая подготовку сырья, выплавку чугуна, стали и получение проката, близка к переводу на непрерывный процесс.
Проблемы, связанные с организацией непрерывного сталеплавильного процесса, выбором удобной для практического использования конструкции сталеплавильного агрегата непрерывного действия (САНД) и отработкой технологии выплавки стали в этом агрегате, пока еще не решены. В частности, основные трудности, возникающие при разработке конструкции САНД, можно подразделить на две группы:
1. Технологические, заключающиеся в необходимости организации одновременного удаления из чугуна разнородных по своим термохимическим свойствам элементов: для удаления углерода требуются окислительная атмосфера, железистые шлаки, достаточный уровень перегрева металла; для удаления фосфора желательно иметь же-лезистоизвестковые шлаки и умеренные температуры; для удаления серы важно интенсивное перемешивание основного шлака с металлом при достаточно высоком уровне нагрева ванны, а содержание оксидов железа в шлаке и кислорода в металле при этом должно быть минимальным; для удаления кремния требуется иметь окислительную атмосферу и железистый шлак; заданная степень раскисления металла достигается при минимальной окисленности шлака и т. д.
2. Конструктивные, заключающиеся в необходимости создания агрегата, который бы обеспечивал возможность проведения технологических операций в требуемой последовательности. При этом одновременно должна быть обеспечена высокая стойкость агрегата и отдельных его элементов в условиях высоких температур и непрерывной работы при отсутствии даже кратковременных остановок для профилактического ремонта конструкций и т. д.
18.1. КОНСТРУКЦИИ САНД К настоящему времени предложено множество различных вариантов конструкций САНД и технологий выплавки в них стали. Можно дать следующую условную классификацию непрерывных сталеплавильных процессов.
18.1.1. По организации процесса: 1) многостадийные (с разделением операции на стадии), при этом в каждой емкости или части агрегата проводится одна или несколько технологических операций: дефосфорация, десульфурация, раскисление и т. п.; 2) одностадийные, когда все операции удаления примесей и превращения чугуна в сталь протекают одновременно или почти одновременно.
18.1.2. По конструкции агрегата: 1) операция проводится на поду; при этом газообразные и твердые реагенты (кислород, флюсы, руды и т. п.) поступают в так называемые подовые, желобные реакторы; 2) операция проводится таким образом, что металл, шлак, добавочные материалы находятся во взвешенном распыленном каплеобразном состоянии (так называемые струйные реакторы).
18.1.З. По организации технологии: 1) движение шлака и металла происходит в одном направлении; 2) встречное движение шлака и металла (принцип противотока) (рис. 18.1).
Примером одностадийного непрерывного сталеплавильного процесса может служить схема, разработанная BISRA (Британским научно-исследовательским институтом черной металлургии). В процессе BISRA падающую струю чугуна окружает кольцевая струя кислорода, которая разбивает металл на капельки диаметром 1—2мм. Поверхность контакта между каплями металла и кислородом оказывается настолько большой, что выгорание примесей происходит мгновенно. Процесс обработки металла в струе называют струйным рафинированием.
Схема процесса представлена на рис. 18.2. Падающая вниз струя чугуна, непрерывно поступающая в установку, обрабатывается тонкоизмельченными флюсами и кислородом. Капельки рафинированного металла и шлака падают в приемный ковш; металл собирается внизу под пенящимся шлаком, отстаивается и непрерывно выпускается в ковш для последующей разливки. Последующие капельки металла должны проходить через этот шлаковый слой, дополнительно рафинирующий металл. Отработанный шлак непрерывно стекает в шлаковую чашу. В процессе рафинирования происходит окисление капелек металла; это имеет место: 1)в зоне распыления струи чугуна; 2) при свободном падении капель в окислительной атмосфере; 3) при прохождении через слой вспененного шлака; 4) в ковше. Опыты показали, что при температуре металла 1500— 1600 "С и диаметре капли металла 2—3 мм скорость обезуглероживания превышает 3 %С/с; при образовании капель размером < 3 мм степень десульфурации превышает 50%.
Достоинством процесса струйного рафи-
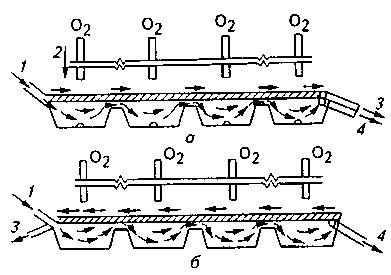
Рис. 18.1. Технологическая схема САНД конструкции МИСиС:
а принцип прямотока; б — принцип противотока;
1 — чугун; 2 — ввод шлакообразующих смесей; 3 —
спуск шлака; 4— выпуск металла
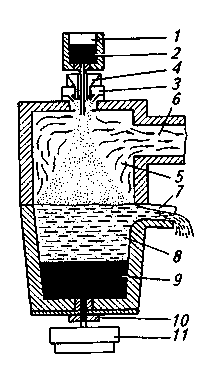
Рис. 18.2. Установка струйного типа для непрерывного рафинирования жидкого чугуна института BISRA:
1 — промежуточное устройство; 2 —чугун; 3— кислород; 4— известь; 5— реакционная камера; 6— отходящие газы; 7—шлак; 8— отстойник; 9— сталь; 10— шиберный затвор; 11 — ковш для УНРС нирования является то обстоятельство, что основные реакции здесь протекают в условиях отсутствия контакта металла с огнеупорной футеровкой. Однако условия эксплуатации футеровки приемного ковша (отстойника) сложны, так как происходит взаимодействие футеровки с высокоактивным окислительным шлаком. Трудной задачей является также разработка технологии, при которой спускаемый из агрегата шлак содержит минимальное количество оксидов и, следовательно, обеспечивается максимальный выход годного металла. Из-за этих недостатков предложенный процесс в промышленность не внедрен.
В большинстве конструкций САНД предусмотрена возможность организации ведения плавки на поду. Широкую известность получила конструкция САНД, разработанная Французским институтом черной металлургии IRSID. Агрегат (рис. 18.3) состоит из трех частей: реакционной камеры 1, отстойника 3 и камеры доводки 5. Чугун непрерывной струей поступает в камеру по желобу. Одновременно при помощи водоохлаждаемого устройства (фурмы) 2 в камеру непрерывно подается кислород с молотой известью. Реакционная камера содержит небольшое количество жидкого металла и слой металл-шлак-газовой эмульсии. Под действием подъемной силы пузырей газа эта эмульсия поднимается и перетекает в отстойник, где шлак отделяется от металла. Шлак стекает через отверстие 4, а металл сифоном передается в камеру доводки, где подвергается раскислению и доводке по составу. В конструкции установки предусмотрена возможность устройства желоба, по которому шлак из вто-
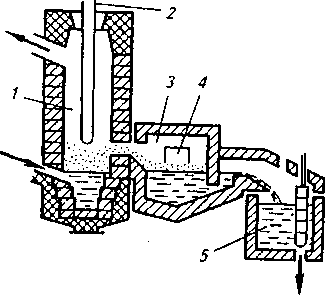
Рис. 18.3. Схема установки для непрерывного рафинирования конструкции IRSID рой камеры (отстойника) мог бы перетекать в первую камеру для повышения степени использования шлакообразующих и уменьшения потерь железа с уходящим шлаком.
В 1971—1976гг. проводили испытания САНД конструкции МИСиС. Установка включала четыре ванны, соединенные последовательно (см. рис. 18.1). В первых трех осуществлялось рафинирование вдуванием газообразного кислорода через верхние фурмы, а в последней — регулирование содержания углерода и раскисление. Вместимость каждой ванны составляла 0,86м3 при глубине расплава 600 м и массе 6 т. Производительность этого опытно-промышленного агрегата достигала 21 т/ч, степень удаления серы — 21 %, фосфора —93 %.
Окончательные выводы о показателях работы агрегатов такого типа в промышленных условиях и соответственно о перспективах внедрения сделать пока трудно.
18.2. ПЕРЕПЛАВ МЕТАЛЛОЛОМА Если САНД, основанные на переработке в сталь жидкого чугуна, не вышли из стадии полупромышленных испытаний, то САНД с использованием в качестве шихты дешевого
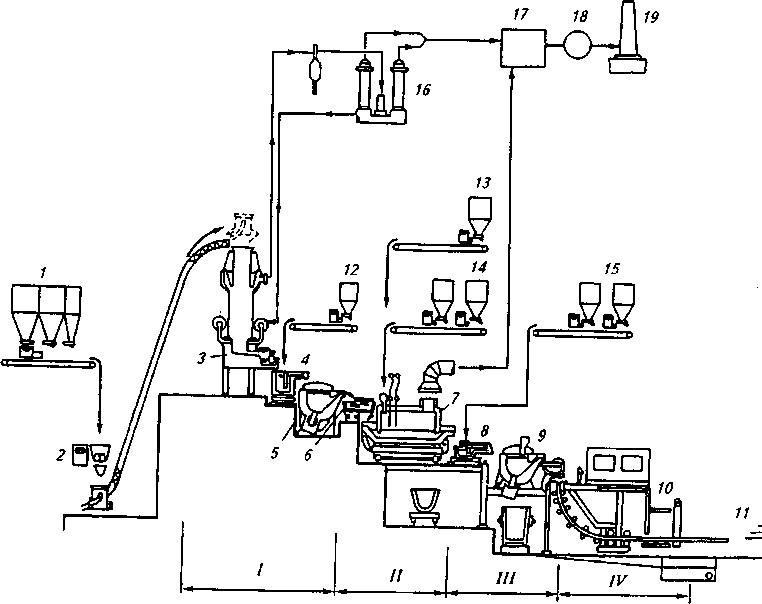
Рис. 18.4. Схема CSM-процесса:
/—плавление; //—рафинирование; ///—легирование; IV— разливка; / — кокс и известняк; 2— окалина;
3— вагранка; 4 — десульфурация; 5 —копильник; 6— ковш; 7—рафинировочный агрегат; 8— раскисление;
9— доводка; 10— УНРС; // —заготовки; 12 — десульфурирующие реагенты; 13 — охладители; 14— флюсы;
/5—ферросплавы; 16— теплообменник; /7—пылесборник; 18— эксгазустер; 19— труба
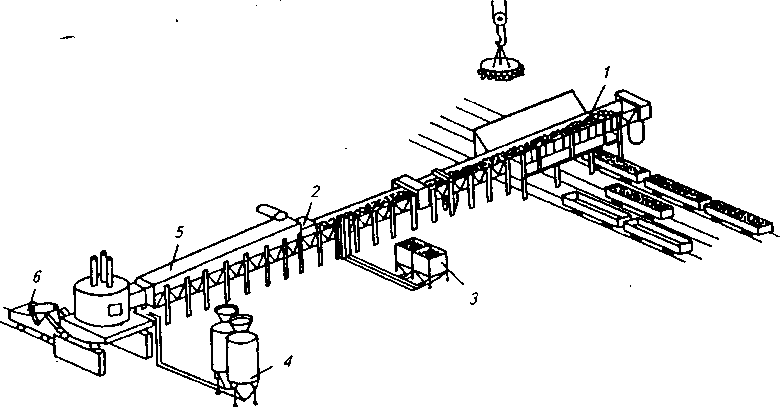
Рис. 18.5. Общий вид установки Consteel:
/ — загрузочный конвейер; 2 —тепловой затвор; 3 — бункера для стружки, скрапин, известняка и др.; 4 — бункера для добавок; 5— подогрев; 6— сталевоз металлического лома (скрапа) получают все большее распространение. Работы ведутся во многих странах мира. Изыскание рациональных методов непрерывной переработки металлолома происходит в основном по двум направлениям. В одном случае в качестве плавильного агрегата используют высокомощную дуговую сталеплавильную печь с периодической выдачей порции металла. В другом в качестве плавильного агрегата используют шахтную печь (типа вагранки). В обоих случаях получаемый полупродукт доводится затем во вспомогательных агрегатах. В качестве примера организации непрерывного сталеплавильного процесса может служить процесс, разработанный Японским научно-исследовательским институтом металлургии NRIM.
Построенный по предложенной схеме комплекс (рис. 18.4) включает металлургическую вагранку, работающую на подогретом до 500 °С дутье, производительностью 20 т/ч. В качестве шихты используют металлолом и пакеты. Полученный в вагранке углеродистый полупродукт (2,7— 3,5 %С) попадает в ковш, где обрабатывается десульфурирующими смесями, после чего переливается в канальную (с индуктором для подогрева) индукционную печь — копильник. Из копильника металл попадает в рафинировочную печь, оборудованную сводовыми кислородными фурмами и устройствами для присадки охладителей и флюсов. После рафинировочной печи металл попадает в оборудованный пористой пробкой для вдувания инертного газа ковш, где производится его раскисление.
На рис. 18.5 показан общий вид агрегата непрерывного сталеплавильного процесса Consteel на базе ДСП. Шихту (металлолом или металлизованные окатыши), подогреваемую за счет дожигания СО, выделяющегося из ванны дуговой печи при ее продувке кислородом, подают непрерывно в печь. Температура металлолома перед поступлением в печь составляет 500—700 °С. Печь с эркерным выпуском обеспечивает периодическую выдачу порций стали, поступающих далее на установки внепечной обработки. Процесс Consteel был создан в начале 80-х годов XX в. в США. Различные варианты процесса с непрерывной подачей подогреваемой отходящими газами металлошихты в печь получают все большее распространение во многих странах.
В начале 80-х годов в Германии разработан процесс (Energy Optimizing Furnace) (с оптимальным расходом энергии), названный процессом EOF. Первый промышленный агрегат (рис. 18.6) был введен на одном из заводов Бразилии. Емкость этого агрегата 30 т, производительность 200 тыс. т стали в год, стойкость футеровки > 500 плавок, расход жидкого топлива 8—9 кг, кокса 1,0кг на 1т стали, расход кислорода 60—78 М3/т, расход огнеупоров 6 кг/т стали.
Опыт показал, что утилизация тепла отходящих газов позволяет нагреть подаваемую твердую металлошихту до 850 °С. Состав шихты (соотношение расхода чугуна и металлолома), как и в мартеновских печах, может ме-
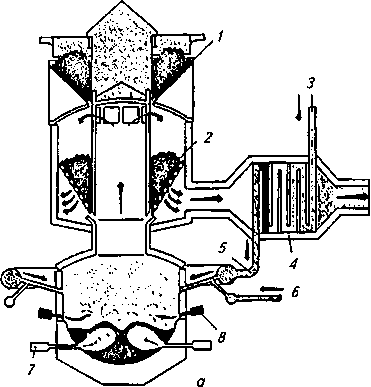
Рис. 18.6. Печь с оптимальным расходом энергии (EOF):
а —схема (1 — металлолом; 2 — нагретый лом; 3 — холодный воздух; 4 — рекуператор; 5— нагретый воздух; 6— добавка кислорода; 7—кислородные фурмы; —топливно-кислородные горелки); 6— общий вид (см. на цветной вклейке) няться в широких пределах. К 1993 г. в мире работало 10 установок EOF (в Бразилии, Индии, Италии, США, Венгрии) производительностью 200—600 тыс. т/год каждая.
18.3. ПЕРСПЕКТИВЫ РАЗВИТИЯ НЕПРЕРЫВНЫХ ПРОЦЕССОВ Пока еще не найдены окончательные решения организации непрерывного процесса сталеварения и не разработаны оптимальные конструкции САНД, которые могли бы успешно конкурировать с современными процессами массового производства стали в конвертерах и дуговых сталеплавильных печах периодического действия. Однако усилия, затрачиваемые на разработку рациональных схем САНД, можно считать вполне оправданными по следующим причинам.
В современных сталеплавильных агрегатах периодического действия развитие технологии достигло очень высокого уровня. Время, затрачиваемое на выполнение собственно металлургических операций, во многих случаях сопоставимо с продолжительностью простоя агрегатов, связанного с проведением вспомогательных операций (загрузки печи, анализа металла по ходу плавки, выпуска готового металла и т. д.).
Например, для крупных конвертеров продолжительность проведения вспомогательных операций составляет около половины длительности всей плавки. Резервы дальнейшего повышения производительности, очевидно, следует искать в направлении сокращения времени, затрачиваемого именно на вспомогательные операции. В этом отношении использование сталеплавильных агрегатов непрерывного действия представляется одним из наиболее вероятных решений проблемы.
|
|
|