|
Теория и технология производства стали 1. Учебник для вузов. М. Мир, ООО Издательство act
Рис. 19.22. Конструкция конвертера для аргоно-кислородной продувки:
а — конвертер; б— фурма
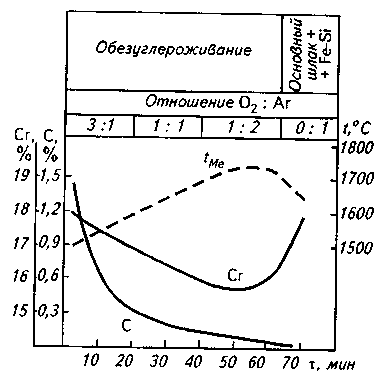
Рис. 19.23. Продувка металла в агрегате АКР
(AOD) при производстве низкоуглеродистой
высокохромистой стали шего снижения концентрации кислорода и серы (в результате перемешивания металла под высокоосновным шлаком), а также для возможно большего восстановления окисленного в процессе продувки кислородом хрома. Существуют также варианты продувки, при которых кислород подают через фурму сверху, а снизу — смесь О2 + Аг или только аргон (иногда азот).
На рис. 19-24 показано, что снижение парциального давления СО при 1700 ºС в случае аргоно-кислородной продувки обеспечивает получение заметно более низких концентраций углерода, чем при той же температуре, но при нормальном давлении. Сравнительная простота организации аргонно-кислородной продувки, высокая производительность агрегатов и возможность изменять в широких пределах окислительный потенциал газовой фазы (отношение О2: Аг) привели к непрерывному расширению сферы распространения этого метода, который используют для производства не только коррозионностойких, но и электротехнических, конструкционных и других сталей.
Этот метод делает возможным получение в конвертере высокохромистых сталей непосредственно из чугуна с использованием в качестве шихтового материала хромистой руды. Жидкий чугун подвергают внедоменной обработке (обескремниванию, дефос-форации), после чего заливают в конвертер. В процессе продувки в конвертере осуществляют обезуглероживание, десульфурацию и легирование хромом. Одну часть хрома вводят в металл с феррохромом, а другую — с хромистой рудой, оксиды которой восстанавливаются углеродом чугуна. На одном из заводов Японии организовано производство коррозионостойкой стали из расплава никелевых и хромистых руд. Никелевую руду с высоким содержанием железа после дробления, обогащения и предварительного нагрева в смеси с углеродистым восстановителем в нагретом до 1000 °С состоянии загружают в рудовосстанови-тельную печь, в которой получают расплав с 13—15 % Ni. Хромистую руду также подвергают предварительной обработке и в нагретом до 500 ºС состоянии загружают в рудовосстано-вительную печь, где получают расплав с 40—43 % Сг. Расплавы смешивают в ковше и заливают в конвертер, в котором подвергают аргоно-кислородной продувке для получения специальных высокохромистых никельсодержащих сталей.
По сравнению с известным способом получения таких сталей из скрапа по схеме дуговая печь — конвертер аргоно-кислородной продувки затраты
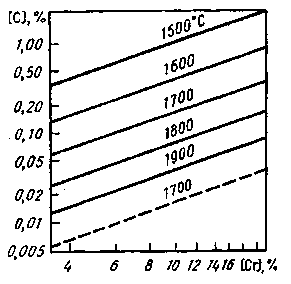
Рис. 19.24. Соотношение между содержанием углерода и хрома при различных температурах металла при продувке его в печи (сплошные линии, рсо = О,1 МПа) и в AOD-конвертере (штриховая линия, рсо = = 0,01 МПа) энергии в новом процессе ниже, содержание неметаллических включений и азота меньше, поскольку используют первородную шихту и не происходит образования атомарного азота в зоне.
Возможности, которые появляются при использовании метода аргоно-кислородного рафинирования, велики, и в мировой практике рождаются все новые и новые варианты процесса. Разрабатываются, в частности, варианты использования метода расплавления хромсодержащего и никельсо-держащего металлолома при вдувании в конвертер каменноугольной пыли с последующей аргоно-кислородной продувкой расплава и получением коррозионностойкой стали.
19.5. ОБРАБОТКА МЕТАЛЛА
СИНТЕТИЧЕСКИМИ ШЛАКАМИ Перемешивание металла со специально приготовленным (синтетическим) шлаком интенсифицирует переход в шлак тех вредных примесей, которые должны удаляться в шлаковую фазу (сера, фосфор, кислород). В тех случаях, когда основную роль в удалении примеси выполняет шлаковая фаза, скорость процесса пропорциональна площади межфазной поверхности. Если ставится задача удаления из металла неметаллических включений определенного состава, то соответственно подбирают состав синтетического шлака (например, металл, выплавленный в кислой печи, обрабатывают основным шлаком, металл, выплавленный в основной печи, — кислым). Если ставится задача снизить содержание серы в металле, то подбирают шлак с максимальной активностью СаО и минимальной активностью FeO и т. п. Во многих случаях задача заключается, во-первых, в получении шлака заданных состава и температуры и, во-вторых, в разработке способа получения максимальной поверхности контакта шлаковой и металлической фаз. При этом должны быть обеспечены условия, необходимые для последующего отделения шлака от металла. Способ обработки металла в ковше жидкими синтетическими шлаками для удаления из металла нежелательных примесей был предложен в 1925 г. советским инженером А. С. Точинским; в 1933 г. способ обработки металла жидкими известково-глиноземистыми шлаками был запатентован французским инженером Р. Перреном. Практическую проверку прошли многие способы, являющиеся вариантами способа обработки металла шлаками. Например, использовались шлаки:
1) жидкие известково-железистые для снижения содержания фосфора;
2) кислые для снижения содержания кислорода и оксидных неметаллических включений в основной стали;
3) жидкие известково-глиноземистые для десульфурации и раскисления металла; 4) шлаки разного состава во время разливки и кристаллизации для удаления вредных примесей и получения хорошей поверхности слитка.
А. С. Точинским в 1927 г. впервые в мире была проведена в промышленных масштабах дефосфорация бессемеровской стали известково-железис-тым шлаком, а в 1928-1929 гг.— рафинирование основной мартеновской стали кислым шлаком для раскисления (содержание кислорода в металле удавалось снизить на 30—55 %). Позднее известково-железистые шлаки (60-65 % СаО и 20-35 % оксидов железа) неоднократно применяли для обработки конвертерной стали, получая высокую степень дефосфорации. Так, содержание фосфора в томасов-ской стали удавалось снизить с 0,06 до 0,01 %, а в рельсовой бессемеровской стали-с 0,05-0,09 до 0,01-0,03%. Однако, как показала практика, обработка известково-железистым шлаком углеродистого металла приводит вследствие протекания реакции (FeO) + [С] = СОГ + Fеж к бурному вскипанию и выбросам. Кроме того, обработка железистым шлаком затрудняла проведение операции раскисления металла. Начиная с 1959 г. в ЦНИИЧМ и на ряде отечественных заводов проведены широкие исследования метода обработки стали извест-ково-глиноземистым шлаком. В соответствии с разработанной технологией шлак с высоким содержанием СаО и добавками А12О3 (для снижения температуры его плавления и обеспечения необходимой жидкотекучести) расплавляют в специальной электропечи и заливают в сталеразливочный ковш при выпуске стали из сталеплавильной печи или из конвертера. При сливе металла на находящийся в ковше синтетический шлак обе взаимодействующие фазы (сталь и шлак) интенсивно перемешиваются, шлак эмульгирует в металле и в какой-то степени металл эмульгирует в шлаке с последующим разделением фаз.
Интенсивность и глубина протекания процесса зависят от высоты падения струи металла и шлака, физических характеристик и состава шлака и др. Задача заключается в том, чтобы обеспечить в процессе обработки максимальную межфазную поверхность. Наибольшее влияние при этом имеет высота падения струи металла, а также вязкость шлака. Содержащаяся в металле сера взаимодействует с СаО шлака и переходит в шлак. Поскольку синтетический шлак содержит обычно ничтожно малые количества таких оксидов, как FeO и МпО, обработка шлаком сопровождается снижением окисленности металла; в шлак переходит также некоторое количество таких оксидных включений, которые хорошо смачиваются синтетическим шлаком или взаимодействуют с ним.
Основными требованиями, предъявляемыми к синтетическим известково-глиноземистым шлакам, являются минимальная окисленность (это обеспечивает хорошие условия для раскисления стали и ее десульфура-ции) и максимальная активность СаО (это обеспечивает хорошие условия для десульфурации стали). В связи с этим в синтетических известково-гли-ноземистых шлаках не должно содержаться оксидов железа, а содержание кремнезема должно быть минимальным. Содержание фосфора в таких шлаках исключается, иначе он при обработке перейдет в металл. В тех случаях, когда в шихте, из которой плавят шлак, содержится некоторое количество кремнезема, в состав шлака вводят магнезию, образующую силикаты магния и уменьшающую таким образом вредное воздействие кремнезема, снижающего активность СаО. Обычный состав заводского синтетического шлака следующий, %: СаО 50—55; А12О3 37-43; SiO2 до 7 (в некоторых случаях до 10—15); MgO до 7 и (FeO + МпО) не более 1,0-1,5. Температура плавления шлака в зависимости от состава изменяется от -1400 ºС (в шлаке 50-55 % СаО, 38-43 % А12О3 и <4,0 % SiO2) до -1300 °С (в шлаке до 6-7% SiO2 и 6-7% МпО). Расход шлака 3—5 % от массы металла. При обработке металла синтетическим шлаком такого состава (высокая основность и низкая окисленность) протекают следующие процессы.
1.Десульфурация. Обычно после обработки шлаком содержание серы в металле снижается до 0,002—0,010 % (рис. 19.25).
2. Раскисление. В соответствии с законом распределения Lo= a(FeO) /a[О] и а[o] = =а(FeO) /LO.Поскольку в синтетическом шлаке значениеa(FeO) ничтожно масло, окисленность металла снижается (в 1,5—2 раза).
3. Удаление неметаллических включений. В тех случаях, когда межфазное натяжение на границе капля синтетического шлака — неметаллическое включение
с ш_вкл меньше, чем межфазное натяжение на границе металл — неметаллическое включение м-вкл т.е. при с. ш-вкл < м-вкл капли синтетического шлака будут рафинировать металл от включений (капли шлака, всплывая, уносят неметаллические включения). Соотношение между величинами с ш.вкл и М-ВКЛ зависит от состава включений. Практи ка показала, что общее содержание неметаллических включений после обработки синтетическим шлаком уменьшается примерно в 2 раза.
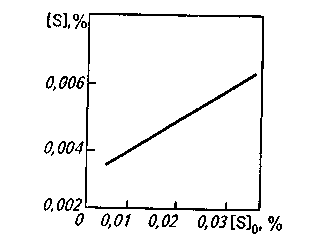
Рис. 19.25. Эффективность десульфурации трубной стали 09Г2ФБ с обработкой на заводе «Азовсталь» жидким известково-глинозе-мистым синтетическим шлаком:
[S]o — содержание серы в стали до обработки шлаком; [S] — то же, в готовой стали Достоинством метода обработки стали синтетическими шлаками является его небольшая продолжительность — вся операция полностью осуществляется за время выпуска (слива) металла из агрегата в ковш, т. е. за несколько минут. Производительность агрегатов при этом не только не уменьшается, но и возрастает, так как такие технологические операции, как десульфурация и раскисление, переносят в ковш. При проведении операции обработки металла шлаком приходится учитывать ряд ограничений: 1) нежелательно попадание в ковш, в котором проводится обработка, вместе с металлом и шлака из печи или из конвертера; 2) необходимо вводить в ковш помимо синтетического шлака раскислители (а при выплавке легированных сталей также и легирующие материалы); 3) в процессе обработки состав шлака изменяется. Особенно трудной задачей для практического осуществления является задача отсечки шлака при выпуске металла. В процессе обработки синтетическим шлаком несколько уменьшается окисленность металла, однако не настолько, чтобы полностью отказаться от применения раскислителей, поэтому кроме шлака в ковш вводят необходимое количество раскислителей.
Метод обработки металла синтетическим шлаком обеспечивает стандартные результаты десульфурации, но до известных пределов (обычно до 0,005-0,007 %), поэтому применение его особенно эффективно в случае обработки металла с высоким содержанием серы. В тех случаях, когда необходимо устойчиво получать более низкие концентрации серы, используют другие способы. Если по условиям производства нет возможности разместить оборудование для расплавления синтетического шлака, используют метод обработки металла на выпуске твердыми синтетическими шлаками. Обычно в состав таких смесей вводят СаО и CaF2. Расход таких смесей колеблется в пределах 3— 10 кг/т. И в этом случае наилучшие результаты по десульфурации и содержанию неметаллических включений получены при одновременном воздействии на металл и десульфури-рующей синтетической смеси, и раскислителей.
Чаще других используют два технологических приема: 1) подачу на струю металла порошка, состоящего из извести, плавикового шпата и алюминия; 2) присадку десульфурирую-щей смеси, состоящей из извести и плавикового шпата, на дно ковша перед выпуском металла; при этом одновременно на дно ковша присаживают все требуемое для раскисления количество ферросилиция. Температура металла при использовании для десульфурации синтетических смесей в твердом виде должна быть выше обычной на 10—15 °С.
Так, например, твердые шлаковые смеси (сокращенно ТШС) использовали в конвертерном цехе комбината «Азовсталь» при производстве труб большого диаметра для магистральных трубопроводов (сталь должна была содержать не более 0,010 % S). Использовали ТШС следующего состава, %: известь 60; плавиковый шпат 20; магнезитовый порошок 10; отходы, содержащие алюминий, 10. При этом ввод в состав ТШС магнезитового порошка (используемого для торкретирования конвертеров или заправки мартеновских печей) обусловлен тем, что MgO при содержании его в шлаке до 10—12 % снижает температуру ликвидуса системы CaO-SiO2-Al2O3-MgO и вязкость таких шлаков, повышая коэффициент активности СаО и коэффициент распределения серы.
Отходы алюминия и алюминиевых сплавов (алюмошлак) представляют собой механическую смесь, состоящую из 85 % металлической части (корольки, всплески, нерасплавившаяся часть алюминиевого лома) и 15 % шлаковой части (состоящей в основном из А12О3). В составе металлической части содержится до 75 % А1. Металлический алюминий в составе алю-мошлака выполняет двоякую роль: во-первых, обеспечивает дополнительное раскисление металла, во-вторых, образующийся после окисления алюминия А12О3 остается в шлаке и является дополнительным разжижителем шлаковой смеси, находящейся в сталераз-ливочном ковше.
Обработку стали ТШС проводили в ковше во время выпуска металла из конвертера. Порядок присадки смеси был следующий. Известь и плавиковый шпат, предварительно смешанные, подавали в ковш емкостью 350 т по тракту сыпучих. Магнезитовый порошок и алюмошлак без предварительного смешивания присаживали в ковш с рабочей площадки конвертерного отделения из переносного бункера одновременно с известью и плавиковым шпатом. Очередность подачи в ковш материалов во время выпуска соответствовала существующей: 1-я порция чушкового алюминия, ТШС, науглероживатель и ферросплав; 2-я порция чушкового алюминия, алюминиевый слиток. В результате получали сталь, содержащую 0,009 % S.
19.6. ВВЕДЕНИЕ РЕАГЕНТОВ В ГЛУБЬ МЕТАЛЛА 19.6.1. Продувка металла порошкообразными материалами. Продувка металла порошкообразными материалами (или вдувание в металл порошкообразных материалов) проводится для обеспечения максимального контакта вдуваемых твердых реагентов с металлом, максимальной скорости взаимодействия реагентов с металлом и высокой степени использования вдуваемых реагентов. Достоинством этого метода является также то, что реагент в металл вдувается струей газа-носителя, который оказывает определенное воздействие на металл. Газом-носителем может быть: 1) окислитель (например, кислород или воздух); 2) восстановитель (например, природный газ); 3) нейтральный газ (азот, аргон). В качестве вдуваемых реагентов используют шлаковые смеси, а также металлы или сплавы металлов. Целью вдувания порошков является:
1.Дефосфорация металла. При использовании шлаковых смесей для удаления фосфора в металл обычно вдувается в струе кислорода смесь, состоящая из извести, железной руды и плавикового шпата.
2. Десульфурация. Для удаления серы в металл вводятся (в струе аргона или азота) флюсы на основе извести и плавикового шпата; смеси, содержащие кроме шлакообразующих также кальций или магний; реагенты, которые вследствие высоких энергий взаимодействия и соответствующего пиро-эффекта обычными способами вводить в металл нельзя (кальций, магний).
3. Раскисление и легирование, в том числе для введения металлов, которые вследствие вредного действия на здоровье человека обычными методами вводить опасно (свинец, селен, теллур).
4. Ускорение шлакообразования, например в конвертерных цехах вдувание порошкообразной извести используется при переделе высокофосфористых чугунов.
5. Науглероживание. Вдуванием в металл порошкообразных карбонизаторов (графита, кокса и т. п.) обеспечивается решение разных задач, в частности: корректировка содержания углерода в металле; при недостатке или отсутствии чугуна можно повысить в металле содержание углерода до пределов, необходимых для нормального ведения процесса; раскисление металла (вдувание в окисленный металл порошка углерода вызывает бурное развитие реакции обезуглероживания; содержание кислорода при этом уменьшается, а выделяющиеся пузыри СО промывают ванну от газов и неметаллических включений). Порошок графита или кокса можно вводить в металл непосредственно в печи, а также в ковш или на струю металла, выпускаемого из печи в ковш.
Существуют и другие цели использования метода вдувания. Наибольшее распространение получила практика использования метода для введения в сталь такого реагента, как кальций.
|
|
|