|
вивчення ПТЕ повний. Державна адміністрація залізничного транспорту України коментарі та розяснення щодо застосування положень правил технічної експлуатації залізниць україни
Технічні характеристики візка типу 25AN/S5 Таблиця. 9.5 -
Параметр
| Значення
| Ширина колії, мм
| 1435/1520
| База візка, мм
| 2500
| Колісні пари розсувні
| Система SUW 2000
| Діаметр кола кочення нового колеса, мм
| 920
| Відстань між серединами шийок осей колісної пари, мм
| 2080
| Розміри шийки осі, мм
| Ø130x191
| Розміри циліндричних підшипників, мм
| Ø130/240x80
| Гальмівні диски (2 диски на осі), мм
| Ø610/110
| Гальмівні циліндри
| 10"
| Маса візка, кг
| 7500
| Маса колісної пари з буксами, кг
| 2000
|
В ізки типу 25AN/S5 обладнані розсувними колісними парами типу SUW2000, що забезпечують можливість експлуатації вагона на мережі залізниць як колії 1435 мм, так і колії 1520 мм та 1668 мм.Основними елементами колісної пари SUW2000 є (рис. 2): вісь (1); колесо з подовженою ступицею (2); блокувальний механізм (3); буксовий вузол (4); зовнішній кожух (5); внутрішній кожух (6); опорне кільце (7); самофіксуюча гайка (8); гальмівний диск (9).
Основними елементами колісної пари SUW2000 є (рис. 2): вісь (1); колесо з подовженою ступицею (2); блокувальний механізм (3); буксовий вузол (4); зовнішній кожух (5); внутрішній кожух (6); опорне кільце (7); самофіксуюча гайка (8); гальмівний диск (9).
Колеса, підготовлені до розблокування, розміщуються на осі колісної пари відповідно до ширини колії прямування і фіксуються без можливості обертання відносно осі.
Перехід з колії 1520 мм на 1435 мм і навпаки відбувається на колієперевідному пристрої довжиною 27100 мм шляхом почергового розблокування коліс на осі, перестановки їх на потрібні відстані і подальшим блокуванням. Робоча швидкість переходу становить від 5 до 30 км/год.
Візки обладнані дисковими гальмами. Гальма знаходяться в робочому положенні під час руху з будь-якою швидкістю до повної зупинки вагона. Гальма, які розміщені на візку, управляються пневматично за допомогою гальмівних приладів, які знаходяться на рамі вагона.
Циліндри дискового гальма з автоматичним регулюванням виходу штока закріплені на кронштейні рами візка. Затискний механізм дискового гальма показано на рис. 3. До кришки (1) циліндра прикріплено важіль циліндра (8), тоді як важіль штока поршня (7) з'єднано з головкою регулятора (6). Ці важелі з'єднані між собою кулісою (5). На кінці важеля циліндра (8) прикріплена права колодка (9) із фрикційною накладкою (4), а на кінці важеля штока поршня (7) прикріплена ліва колодка (3) із фрикційною накладкою (2). Розміри фрикційних накладок 200х35 мм. Затискний механізм підвішений на підвісках до рами візка, співвісно з гальмівним диском Ø610/110 мм (10).
Ручне гальмо управляється з вагона за допомогою механічної системи, що переміщує затискний механізм на одному з візків.
Вагони оснащені пристроями індикації, що інформують про стан гальмування дискового гальма і ручного гальма. Ці пристрої розміщені по обидва боки вагона на середині рами. Один з індикаторів стосується роботи автогальма, а інший - ручного. В залежності від типу вагона:
Вагони оснащені пристроями індикації, що інформують про стан гальмування дискового гальма і ручного гальма. Ці пристрої розміщені по обидва боки вагона на середині рами. Один з індикаторів стосується роботи автогальма, а інший - ручного. В залежності від типу вагона:
положення “розгальмовано” - у вікні індикатора зелений або білий колір;
положення “загальмовано” - у вікні індикатора колір червоний;
положення “гальмо не працює” - у вікні індикатора білий колір зі знаком X.
Основні характеристики гальм вагону приведені в табл. 9.6. Табл. 9.6Технічні характеристики гальмівного обладнання Параметр
| Значення
| Тип повітророзподільника
| KEs SL
| Тиск в гальмівній магістралі, МПа
| 0,5
| Тиск в гальмівному циліндрі при повному службовому гальмуванні, МПа:
|
| - на пасажирському режимі (П)
| 0,25-0,3
| - на пасажирському швидкісному режимі (ПС)
| 0,36-0,39
| Час наповнення, с:
|
| - основного резервуара
| 100-300
| - допоміжного резервуара
| 100-300
| - гальмівного циліндра
| 3-5
| Час відпуску гальм (випуск повітря з гальмівного циліндра), с
| 15-20
|
При заповненні довідки форми ВУ-45 приймати гальмівне натиснення на вісь згідно Інструкції ЦТ-ЦВ-ЦЛ-0015, табл.1:
на пасажирському режимі (П) – 10 тс на вісь;
на пасажирському швидкісному режимі (ПС) – 15 тс на вісь.
Для виключення гальм вагона необхідно перемкнути рукоятку перемикача з позиції “Вкл” в позицію “Викл” (відключити повітророзподільник від гальмівної магістралі), після чого випустити повітря з запасних резервуарів через випускний клапан.
Вагон обладнано мікропроцесорною системою протиюзного захисту MGS1.
Принципова схема системи показана на рис. 9.22.
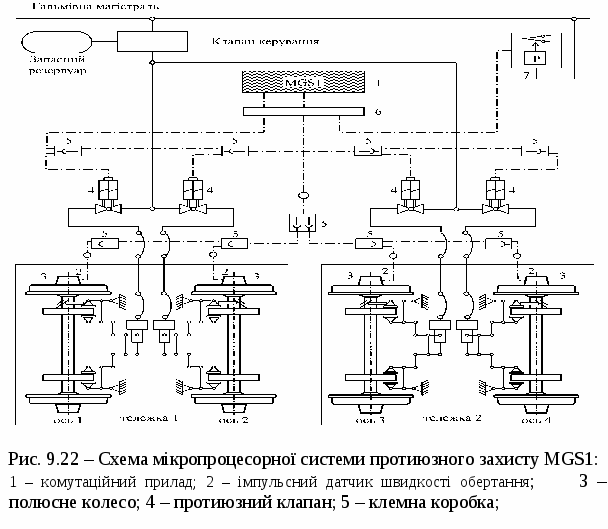
Автозчеп типу laf
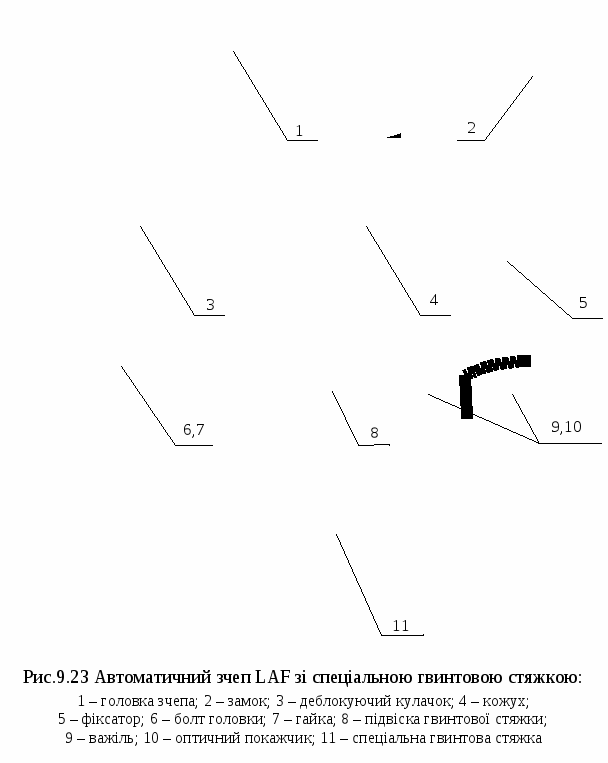 Застосовуваний в першому й останньому вагоні, а також у середньому вагоні поїзда автозчеп LAF є автозчепом змішаного типу, завдяки якому можна зчіпляти вагони з рухомим складом оснащеним автозчепом СА-3, а також оснащеним гвинтовим зчепом UIC. На рис. 5 показані основні складові частини цього зчепу.
Для зчеплення з гвинтовим зчепом служить спеціальний гвинтовий зчеп, виготовлений з типових частин стандартного зчепу UIC. Гвинтовий зчеп прикріплено до головки автозчепу за допомогою гвинта. Якщо він не використовується, то необхідно повісити вільну скобу на підвіску. ТЕХНІЧНІ ВИМОГИ ДО ВУЗЛІВ І ДЕТАЛЕЙ ВАГОНІВ
В ЕКСПЛУАТАЦІЇ
Візки
Забороняється постановка в поїзди і прямування в них вагонів, у візках яких є хоча б одна з наступних несправностей:
тріщини у балках та у зварних швах рами;
тріщини у гніздах та у зварних швах гнізд розміщення пружин буксового та центрального ступеню підвішування;
тріщини у кронштейнах та зварних швах рами візка:
кріплення причіпного пристрою для підняття та транспортування візка;
кріплення стискаючого механізму дискового гальма;
кріплення стабілізатора крену кузова;
кріплення горизонтальних направляючих тяг;
кріплення роликів обмеження бокових переміщень кузова в кривих;
кріплення запобіжних стальних тросів;
тріщини у поперечній балці та у зварних швах;
тріщини у кронштейнах та зварних швах поперечної балки:
кріплення стабілізатора бокової качки;
кріплення запобіжних стальних тросів;
тріщини в деталях стабілізатора крену кузова, несправності його кріплення, а також тріщини в запобіжних скобах;
тріщини в горизонтальних направляючих тягах, несправності їх кріплення, руйнування гумових сайлент-блоків;
тріщини в деталях одностороннього балансиру (важіль, обойма) литої конструкції, несправності шарніру, його кріплення та руйнування амортизуючих гумових колець;
несправність або відсутність еластичного конусного гумового обмежувача бокового переміщення кузова;
несправність кріплення та руйнування гумово-металевих блоків опори кузова;
несправність в деталях обмеження бокового переміщення кузова в кривій;
несправності захисного заземлення, обладнання сигналізації перегріву підшипників та протибуксовочної системи;
тріщини у кронштейнах та зварних швах куліси шворневого вузла;
тріщини шворневого вузла, несправності його кріплення на кузові вагона;
несправності кріплення куліси на шворневому вузлі.
Відстань між вершиною рами візка та рівнем голівок рейок повинна становити 900±3 мм (див. рис. 1). Цю відстань перевіряють під тарою вагона, перед постановкою його у поїзд, на прямолінійній ділянці колії.
Забороняється постановка в поїзди у пунктах формування вагонів, у яких візки з гідравлічними гасителями коливань мають:
тріщини, обриви або погнутість кронштейнів кріплення гасителів коливань (вертикальних або горизонтальних), ослаблення кріплення або від'єднання гасителя;
тріщини, зминання та злам корпусу захисного кожуха гасителя;
заклинювання гасителя.
При виявленні на проміжній станції у вагоні несправностей, зазначених (за умови, якщо тріщини і обриви кронштейнів не виходять на відповідні балки), дозволяється прямування такого вагона до пункту формування або обороту без обмеження маршрутної швидкості у складі поїзда.
У пунктах формування та обороту також не допускається постановка у поїзд вагона з візками, гідравлічні гасителі коливань у яких мають наступні несправності:
витік робочої рідини з гасителів коливань (у вигляді крапель чи сильного замаслювання корпусу);
відсутність або сильне спрацювання гумових кілець в місцях кріплення гасителів коливань;
протертість корпусу гасителя коливань більше 2 мм.
Забороняється постановка у поїзди та прямування в них вагонів, у яких ресорне підвішування має хоча б одну з наступних несправностей:
зрушення або перекіс пружин ресорного комплекту;
змикання витків пружин;
злам або тріщина пружини буксового або центрального ступеня ресорного підвішування.
Забороняється випускати в експлуатацію і допускати до слідування в поїздах вагони з не заміненими колісними парами після сходів, із тріщиною в будь-якій частині осі колісної пари або тріщиною в ободі, диску та ступиці колеса, а також при таких зношеннях та пошкодженнях колісних пар, які порушують нормальну взаємодію колії та рухомого складу:
діаметр кола кочення колеса менше 860 мм;
ширина обода колеса більше 140 мм і менше 130 мм;
товщина обода колеса менше 35 мм;
відстань між внутрішніми гранями ободів коліс для колії 1435 мм повинна бути 1360 3 мм; для колії 1520 – 1440 3 мм;
товщина одного гребеня колеса колісної пари менше 25 мм при вимірюванні на відстані 10 мм зовні від кола кочення;
висота гребеня обода колеса, заміряна від кола кочення, більше 34 мм або менше 25 мм;
гострий гребінь не допускається; виміряний на гребені шаблоном розмір “qR” повинен бути більше 7,0 мм (рис. 6), причому в зоні напрямної поверхні гребеня на відстані більше 2 мм від його вершини не повинно бути уступів і гострокінцевих накатів;
вибоїна (повзун) глибиною більше 1 мм або довжиною більше 60 мм на поверхні кочення коліс;
вищербина, викришування (раковина) на поверхні кочення колеса глибиною більше 3 мм або довжиною більше 25 мм. Тріщина у вищербині або розшарування, що йде вглиб металу, не допускаються. Товщина обода колеса в місці вищербини не повинна бути менше допустимої;
пошкодження поверхні кочення колеса, викликане зсувом металу (“навар”) висотою більше 0,5 мм і довжиною 60 мм;
потертість осі з гострими краями та потертість глибиною більше 1 мм;
сліди контакту з електродом або електрозварювальним дротом у будь-якій частині осі, усунення дефектів за допомогою електрозварювання;
розблокування блокувального механізму. Колісна пара вагона вважається заблокованою в положенні колії 1520 мм або 1435 мм тільки тоді, коли на поверхні внутрішньої втулки не видно відкритої металевої частини (незабарвленої). На поверхні внутрішньої втулки, для полегшення контролю, намальовано смужку жовтого кольору. Виступ відкритої частини незабарвленої поверхні внутрішньої втулки (незабарвлений метал) свідчить про те, що колесо розблоковано.
У випадку, коли блокування колеса не підтверджується візуальним оглядом, експлуатація вагона до заміни колісної пари забороняється.
4.2.2 Огляд колісних пар робити в незагальмованому стані з простукуванням молотком поверхні кочення коліс з метою виявлення тріщин.
4.2.3 Обмір коліс колісних пар виконується за допомогою спеціального шаблону, показаного на рис. 7, який дозволяє заміряти наступні параметри:
висоту гребеня – Ow;
товщину гребеня – Oq;
крутизну зовнішньої напрямної поверхні гребеня – qR.
Основні частини шаблону:
базова поверхня;
напрямна шаблону;
хрестоподібний повзун;
висувна лінійка зі шкалою для виміру висоти гребеня Ow;
гвинт, що фіксує положення висувної лінійки 4;
гвинт, що фіксує положення повзуна 9;
опорне плече, що встановлює положення шаблону відносно точки на колі кочення;
базова поверхня опорного плеча;
повзун;
смуга з противопокажчиком для вимірювання крутизну зовнішньої напрямної поверхні гребеня qR;
край висувної лінійки 4, для вимірювання крутизну зовнішньої напрямної поверхні гребеня qR;
гвинт, що фіксує положення хрестоподібного повзуна 3 на напрямній шаблону 2;
ручка шаблону.
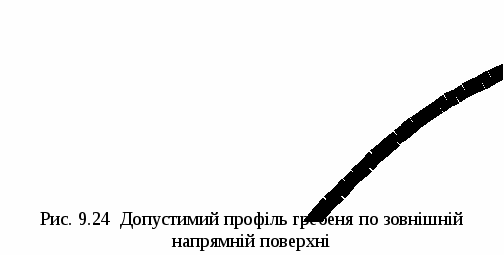
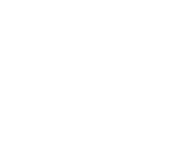
О Рис. 9.25 - Шаблон для виміру геометричних параметрів профілю колеса колісної пари
бмір коліс колісних пар виконується в наступній послідовності:
перед встановленням шаблона на гребінь колеса необхідно два повзуни 3 та 9 переставити вправо, а висувну лінійку 4 - вверх. Це полегшує правильне встановлення шаблону;
тримаючи за ручку 13, необхідно притиснути базову поверхню 1 шаблона до внутрішньої поверхні обода колеса – слідкуючи за приляганням цих поверхонь одна до одної – пересунути шаблон вниз до зіткнення базової поверхні 8 опорного плеча 7 з поверхнею кола кочення у точці А;
перевірити і можливо скорегувати положення шаблону точно вздовж діаметра колеса;
при відкручених фіксуючих гвинтах 5, 6 і 12 необхідно пересунути повзун 9 вздовж напрямної шаблону 2 до зіткнення його крайньої стінки з зовнішньою напрямною поверхнею гребеня колеса (точка В) і зафіксувати його в цьому положенні за допомогою гвинта 6;
опустити висувну лінійку 4 до зіткнення її плоскої (більш довгої) поверхні з верхньою частиною гребеня (точка С) і зафіксувати її в цьому положенні гвинтом 5.
пересунути хрестоподібний повзун 3 по напрямній шаблону 2 убік ручки шаблона 13, до зіткнення краю 11 висувної лінійки 4 з зовнішньою напрямною поверхнею гребеня (точка D) і зафіксувати положення гвинтом 12;
після виконання цих дій усі вимірювальні кінцівки шаблона дотикаються з профілем колеса в точках А, В, С і D, як показано на рис. 6, після чого необхідно зняти шаблон з колеса для зчитування на відповідних шкалах і шкалі ноніуса результатів вимірювань Ow, Oq та qR.
Перевірка правильності показань шаблона виконується за допомогою контрольного шаблона.
При перевірці дискового гальма необхідно дотримуватись наступних правил:
гальмівний диск повинен бути гладкий і блискучий по всій поверхні притискання фрикційної накладки, без гострих подряпин і косих тріщин;
сумарний зазор між накладками і сегментами диску повинен становити 1...2 мм, із припустимим зазором, що не перевищує 6 мм. У випадку, коли зазор більше, то необхідно 3...4 рази виконати гальмування. Якщо після цих операцій зазор не зменшився до необхідних розмірів, то це означає, що пошкоджено автоматичний регулятор виходу штока;
фрикційні накладки не повинні тертися і виступати за диск;
косий або нерівномірний знос фрикційної накладки з однієї сторони диска в порівнянні з іншої, свідчить про неправильне функціонування затискного механізму або скривлення його підвіски;
товщина фрикційних накладок по обидва боки одного й того ж диска повинна бути приблизно однакова;
мінімальна товщина фрикційної накладки становить 5 мм (у новому стані - 35 мм);
мінімальна товщина сегментів гальмівного диску визначається по контрольним рискам на їх торці.
Крім того, при перевірці необхідно звертати увагу на стан шарнірних з'єднань затискних механізмів, на наявність та розташування запобіжних ригелів фрикційних накладок в колодках, на з’єднання втулки дискового гальма на осі (можливе ослаблення), а також на стан ручного гальма.
Забороняється випускати в експлуатацію і допускати до слідування в поїздах вагони при таких зношеннях та пошкодженнях дискового гальма:
будь-які тріщини в ступиці гальмівного диску;
іржа, що виступає з-під ступиці (ослаблення посадки);
сліди переміщення ступиці відносно місця посадки на осі;
заглиблення на поверхні фрикційного кільця сегменту гальмівного диску глибиною більше 3 мм;
знос фрикційного кільця сегменту гальмівного диску понад норми (відсутність контрольної риски на його торці);
ослаблення кріплення сегменту гальмівного диску до ступиці диску (перевіряють легким постукуванням молотком сегменту, тримаючи палець в місці з’єднання сегменту та диску);
вищербина, викришування матеріалу фрикційного кільця сегменту на площі більше 5 см2 і глибині більше 1,5 мм;
елементи затискних механізмів мають тріщини або деформації. Зазори в елементах механізмів не повинні перевищувати 0,8 мм.
Заміну зношених фрикційних накладок виконують у пунктах формування та обороту в такій послідовності:
необхідно запобігти потраплянню стиснутого повітря в гальмівний циліндр дискового гальма;
викрутити шток гальмівного циліндра, який змонтовано у затискному механізмі, до того рівня, поки не буде чутний звук западаючої засувки. Вигвинчувати шток необхідно за допомогою гайки або шківа, що знаходяться на кінці стержня регулятора;
що стосується гальмівного циліндра, що не з'єднаний з ручним гальмом, то вигвинчувати шток необхідно за допомогою шківа з чотирма отворами під 900, тоді як у випадку гальмівного циліндра з приєднаним ручним гальмом вигвинчування штоку необхідно здійснювати гайкою (розмір ключа 46).
Ці операції (вигвинчування штока) виконують з метою одержання відповідного зазору для монтажу нової фрикційної накладки.
Після заміни фрикційних накладок немає необхідності послаблення штока. Після першого гальмування автоматичним регулюванням буде встановлено відповідний зазор між накладкою і гальмівним диском.
Дія мікропроцесорної системи протиюзного захисту перевіряється за показанням комутаційного приладу MGS1, який розміщено в електрощиту службового купе вагона. Про справність системи сигналізує цифровий індикатор з’ємної плати ”Самодіагноз” числом “9.9.” (помилок немає).
Перевірку справності системи протиюзного захисту виконується з допомогою провідника або поїзного електромеханіка.
Для того, щоб зчепити автозчеп LAF із гвинтовим зчепом UIC необхідно:
зняти скобу спеціального гвинтового зчепу з підвіски біля головки зчепу;
надіти цю скобу на тяговий гак сусіднього вагона або локомотива із зчепом UIC;
за допомогою важеля стягти гвинтом зчеп до зіткнення тарелів буферів, після чого зробити ще один оберт важеля гвинтового зчепу. Розчеплення гвинтового зчепу виконують в зворотному порядку.
Зчеплення автозчепу LAF з автозчепом СА-3 відбувається так само, як зчіпляються два звичайні зчепи СА-3. Розчеплення автозчепу LAF і автозчепу СА-3 виконують за допомогою розчіпного важеля одного з автозчепів.
|
|
|