Методичка. Методичка Контроль качества (2010). Методические указания к лабораторным работам по дисциплине Контроль качества сварки Составители Добрынин В. П
![]()
|
|
Номер эталона | d1 | d2 | d3 | d4 | d5 | d6 | d7 | h |
1 | 0,2 | 0,16 | 0,125 | 0,10 | 0,08 | 0,063 | 0,05 | 1,2 |
2 | 0,4 | 0,32 | 0,25 | 0,20 | 0,16 | 0,125 | 0,10 | 1,4 |
3 | 1,25 | 1,00 | 0,80 | 0,63 | 0,50 | 0,40 | 0,32 | 2,2 |
4 | 4,0 | 3,20 | 2,50 | 2,00 | 1,60 | 1,25 | 1,00 | 5,0 |
Ф
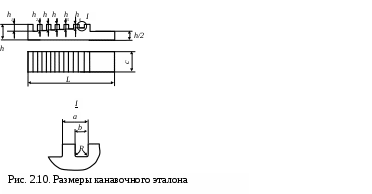
Таблица 2.2. Размеры канавочного эталона, мм.
Номер эталона | Глубина канавок | Предельные отклонения глубины канавок | |||||
h1 | h2 | h3 | h4 | h5 | h6 | ||
1 | 0,6 | 0,5 | 0,4 | 0,3 | 0,2 | 0,1 | - 0,025 |
2 | 1,75 | 1,5 | 1,25 | 1,0 | 0,75 | 0,5 | - 0,06 |
3 | - | - | 3,0 | 2,5 | 2,0 | 1,5 | -0,1 |
4,0 | 3,5 | - | - | - | - | - 0,12 |
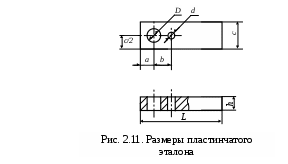
Таблица 2.3. Размеры пластинчатого эталона.
Номер эталона | h | D | d | |||
Ном. | Пред. откл. | Ном. | Пред. откл. | Ном. | Пред. откл. | |
1 | 0,1 | - 0,01 | 0,2 | + 0,01 | 0,1 | + 0,01 |
2 | 0,2 | -0,025 | 0,4 | +0,025 | 0,2 | +0,025 |
3 | 0,3 | 0,6 | 0,3 | |||
4 | 0,4 | 0,8 | 0,4 | |||
5 | 0,5 | 1,0 | 0,5 | |||
6 | 0,6 | - 0,06 | 1,2 | + 0,06 | 0,6 | + 0,06 |
7 | 0,75 | 1,5 | 0,75 | |||
8 | 1,0 | 2,0 | 1,0 | |||
9 | 1,25 | 2,5 | 1,25 | |||
10 | 1,5 | -0,1 | 3,0 | + 0,1 | 1,5 | + 0,1 |
11 | 2,0 | 4,0 | + 0,12 | 2,0 | ||
12 | 2,5 | 5,0 | 2,5 |
Магнитные держатели обеспечивают усилие прижатия не менее 50 Н. С их помощью кассеты, заряженные пленкой с экранами или без них, устанавливают и фиксируют на сварных соединениях из ферромагнитных материалов.
Для расшифровки рентгенограмм служат негатоскопы, с плавной регулировкой яркости освещения.
2.4. ПОДГОТОВКА К КОНТРОЛЮ
Радиографический контроль следует проводить после устранения обнаруженных при внешнем осмотре сварного соединения недопустимых наружных дефектов и зачистки его от неровностей, шлака, брызг металла, окалины и других загрязнений, изображения которых на снимках могут помешать расшифровке снимка.
После зачистки сварного соединения и устранения недопустимых наружных дефектов должна быть произведена разметка сварного соединения на участки и маркировка (нумерация) участков.
При контроле на каждом участке должны быть установлены эталоны чувствительности и маркировочные знаки.
Эталоны чувствительности следует устанавливать на контролируемом участке со стороны, обращенной к источнику излучения.
Проволочные эталоны следует устанавливать непосредственно на шов с направлением проволок поперек шва.
Канавочные эталоны следует устанавливать на расстоянии не менее 5 мм от шва с направлением канавок поперек шва.
Пластинчатые эталоны следует устанавливать вдоль шва на расстоянии не менее 5 мм от него или непосредственно на шов с направлением эталона поперек шва так, чтобы изображения маркировочных знаков эталона не накладывалось на изображение шва на снимке.
При контроле кольцевых швов трубопроводов с диаметром менее 100 мм допускается устанавливать канавочные эталоны на расстоянии не менее 5 мм от шва с направлением канавок вдоль шва.
При невозможности установки эталонов со стороны источника излучения при контроле сварных соединений цилиндрических, сферических и других пустотелых изделий через две стенки с расшифровкой только прилегающего к пленке участка сварного соединения, а также при панорамном просвечивании допускается устанавливать эталоны чувствительности со стороны кассеты с пленкой.
Если суммарная толщина канавочного или пластинчатого эталона чувствительности и контролируемого металла сварного соединения в месте установки эталона меньше максимальной толщины контролируемого металла сварного соединения и разность оптических плотностей их изображения на снимке превышает 1,0, тогда эталоны следует устанавливать на прокладку, компенсирующую разность толщин.
Маркировочные знаки, используемые для ограничения длины контролируемых за одну экспозицию участков сварных соединений, следует устанавливать на границах размеченных участков, а также на границах наплавленного и основного металла при контроле сварных соединений без усиления или со снятым усилением шва.
Маркировочные знаки, используемые для нумерации контролируемых участков, следует устанавливать на контролируемом участке или непосредственно на кассете с пленкой так, чтобы изображения маркировочных знаков на снимках не накладывались на изображение шва и околошовной зоны.
Рентгеновскую пленку, усиливающие и свинцовые экраны помещают в кассету в различных комбинациях рис.2.12. в зависимости от источника излучения, требований, предъявляемых к снимку и т.д.

2.5. МЕТОДИКА ПРОСВЕЧИВАНИЯ СВАРНЫХ СОЕДИНЕНИЙ.
Схемы просвечивания. В основном используют схемы просвечивания рис. 2.13 – 2.14, обеспечивающие контроль качества шва по участкам, как плоских протяженных изделий, так и изделий типа полых тел вращения. Анализ приведенных схем показывает, что только при кольцевом просвечивании фокусное расстояние и толщина стенки являются относительно постоянными величинами, при всех остальных способах контроля их значения меняются от центра к краю контролируемого участка. Суммарное воздействие этих двух факторов оказывает существенное воздействие на получаемые результаты. В частности, радиографический снимок имеет, как правило, различные контрастности, плотности почернения, общие нерезкости изображения и, как следствие, различные значения относительной чувствительности контроля по центру и краю снимка.
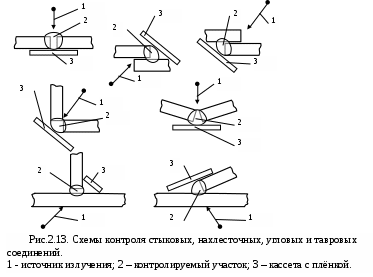
Таким образом, основным ограничением при использовании в промышленной радиографии любой из схем просвечивания является получение:
допустимой разности плотностей почернения и допустимых общих нерезкостей изображения по центру и краю снимка;
требуемой правилами контроля относительной чувствительности просвечивания по центру и краям снимка;
экономически оправданной производительности контроля.
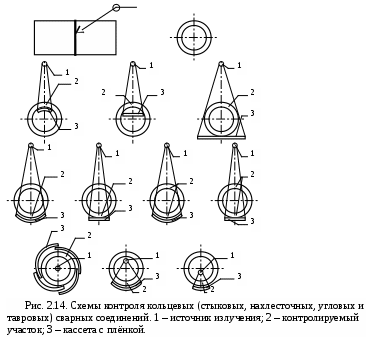
Для всех видов сварных соединений и схем просвечивания угол между направлением излучения и нормалью к пленке в центре снимка и расстояние между контролируемым сварным соединением и пленкой должны быть минимальными и в любом случае не превышать 450 и 150 мм.
Выбор параметров радиографического контроля. После выбора схемы просвечивания устанавливают величину фокусного расстояния. Фокусное расстояние – расстояние от источника излучения до пленки. С увеличением фокусного расстояния несколько увеличивается чувствительность метода, но возрастает (пропорционально квадрату расстояния) время экспозиции. Фокусное расстояние рассчитывается в зависимости от размера и толщины контролируемого участка сварного соединения, схемы просвечивания и т.д. в соответствии с ГОСТ 7512.
Чтобы получить качественный снимок, необходимо также правильно выбирать время экспозиции пленки (выдержку), которое прямо пропорционально квадрату фокусного расстояния и зависит от энергии и мощности источника ионизирующего излучения, толщины и плотности просвечиваемого материала, коэффициента усиления экранов и т.д. Расчетным путем определить выдержку с учетом этих факторов достаточно сложно. Поэтому на практике пользуются таблицами, построенными на основании экспериментальных данных, графиками, номограммами и т.д. Номограммы строятся для определенного фокусного расстояния, и дает зависимость экспозиции от толщины материала для различных напряжений на рентгеновской трубке и определенных типах пленок и экранов.
Ч
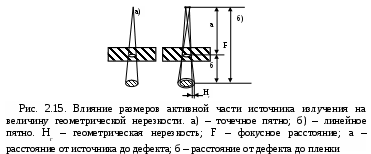
Н
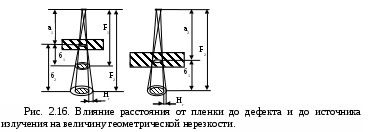
По приведенным схемам видно, что четкость изображения тем выше, чем меньше размер активной части источника и расстояния от пленки до дефекта, а также чем больше фокусное расстояние. Однако возрастание фокусного расстояния приводит к необходимости увеличения экспозиции.
ЛАБОРАТОРНАЯ РАБОТА № 3.
УЛЬТРАЗВУКОВОЙ КОНТРОЛЬ
3.1. ФИЗИЧЕСКИЕ ОСНОВЫ УЛЬТРАЗВУКОВОГО КОНТРОЛЯ И ОСНОВНЫЕ ПОНЯТИЯ
Типы ультразвуковых волн. Ультразвуковыми колебаниями называют механические колебания упругой среды, частота которых лежит за порогом слышимости человеческого слуха, т.е. более 20 кГц.
Процесс распространения колебаний в пространстве называется волной. Граница, отделяющая колеблющиеся частицы от частиц, еще не начавших колебаться, носит название фронта волны. Упругие волны характеризуются скоростью распространения С (м/с), длиной волны λ (м) и частотой f(с-1). Длина волны связана со скоростью её распространения и частотой колебаний соотношением
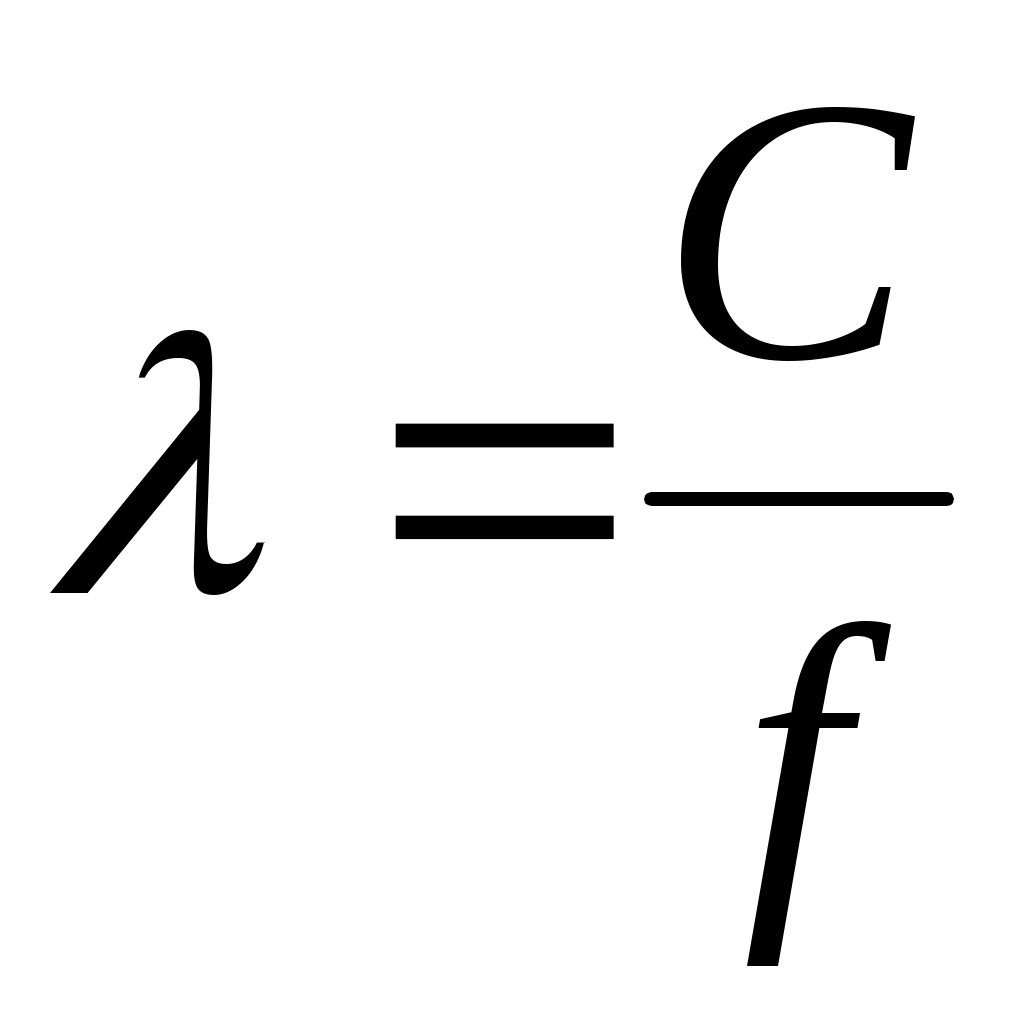
Скорость распространения волны определяется физическими свойствами среды. Поэтому изменение длины ультразвуковой волны в любой среде может быть достигнуто только путем изменения частоты возбуждаемых колебаний.
В зависимости от упругих свойств среды в ней могут распространяться упругие колебания различных типов, отличающиеся направлением смещения колеблющихся частиц. В связи с этим различают следующие типы колебаний: продольные, поперечные, поверхностные и т.д.
Если колебания частиц среды происходят в направлении, совпадающем с направлением распространения волны, то такие колебания называются продольными (рис. 3.1 а).
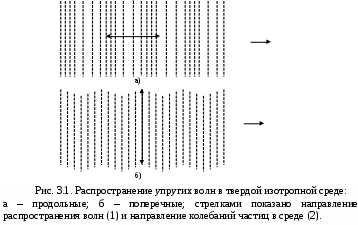
Эти колебания могут распространяться в твердой, жидкой и газообразной средах. Если направление колебаний частиц среды перпендикулярно направлению распространения волны, то такие колебания называются поперечными (рис. 3.1. б). Они могут распространяться только в твердой среде, которая обладает упругостью формы, т.е. способна сопротивляться деформации сдвига.
Значения скоростей распространения волн в безграничном твердом теле приведены в таблице 3.1.
Таблица 3.1. Скорости распространения волн в безграничном твердом теле
Волны | Скорость распространения | |
Тип и название | Характеристика | |
Продольные (волны расширения-сжатия) | Частицы колеблются в направлении распространения волны | ![]() |
Поперечные (волны сдвига) | Частицы колеблются перпендикулярно направлению распространения волны | ![]() |
Примечание: Е – модуль упругости; ν – коэффициент упругости; ρ – плотность среды. Для стали: Е≈20∙1010 Н/м2; ν≈0,3; ρ≈7,8∙103 кг/м3. |
Продольные и поперечные упругие волны (объёмные однородные волны) наиболее широко используются при дефектоскопии материалов для обнаружения внутренних дефектов. Помимо этого для выявления поверхностных и подповерхностных дефектов используются и другие типы волн (неоднородные).
Из неоднородных волн в дефектоскопии в основном применяются поверхностные (волны Рэлея) и нормальные (волны Лэмба). Поверхностная волна представляет собой линейную комбинацию продольной и поперечной волн. При её распространении частицы тела движутся по эллипсам, большая ось которых перпендикулярна границе. Эти фигуры вытягиваются с глубиной, т.е. в направлении, перпендикулярном от поверхности ввода. Проникновение волны вглубь тела приблизительно равно длине волны λ. Поверхностная волна способна распространяться на большое расстояние вдоль поверхности твердого тела.
Нормальные волны (Лэмба) образуются при наклонном падении волны на пластину, толщина которой соизмерима с длиной волны. В этом случае вследствие взаимодействия падающей волны с многократно отраженными волнами внутри пластины возникают резонансные явления. Они приводят к образованию нормальных волн, бегущих вдоль пластины, и стоячих в перпендикулярном направлении.
Условия образования нормальных волн в твердой пластине усложняется из-за наличия в ней продольных и поперечных волн. При отражении эти волны частично трансформируются одна в другую.
Волна Лэмба обеспечивает достаточную чувствительность при длине листа в направлении прозвучивания 0,3…0,5 м. Нормальные волны успешно применяются для контроля листов, труб, оболочек, имеющих небольшую толщину (3…5 мм и менее). Этими волнами обнаруживаются поверхностные трещины не только с наружной, но и с внутренней стороны, а также дефекты, ориентированные вдоль поверхности, которые трудно обнаружить объемными волнами.
3.2. ИСТОЧНИКИ УЛЬТРАЗВУКОВЫХ КОЛЕБАНИЙ
В практике ультразвуковой дефектоскопии металлов применяют ультразвуковые колебания частотой от 0,5 до 25 МГц. Для получения ультразвука таких частот используют генераторы электрических колебаний, являющиеся источниками переменного тока, и специальные искатели. Основной частью излучателя является пьезоэлектрический преобразователь, представляющий собой пластину, изготовленную особым образом из монокристалла кварца или из синтетических кристаллов титаната бария, цирконат-титаната свинца и других. Такие пластины обладают свойством прямого и обратного пьезоэлектрического эффекта. Если пьезоэлектрическую пластину сжимать или растягивать в определенном направлении, она поляризуется и на ее поверхностях появляются заряды, знак которых определяется направлением деформации, а величина – приложенной силой (рис. 3.2). Это явление называется прямым пьезоэлектрическим эффектом. Пьезоэлектрический эффект – явление обратимое, так как под влиянием электрического поля пластина деформируется. Если пьезоэлектрическую пластину внести в переменное электрическое поле, то ее толщина будет уменьшаться или увеличиваться с частотой подведенного тока, т.е. пластина будет совершать вынужденные колебания. В этом случае электрическая энергия преобразуется в энергию механических колебаний. Такое явление называется обратным пьезоэлектрическим эффектом.
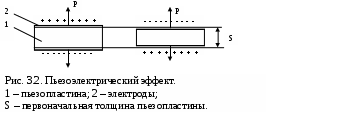
Мощность колебаний пластины зависит от напряжений на электродах и соотношения частоты переменного тока и собственной частоты колебаний пластины. Наибольшую излучаемую мощность можно получить при резонансе, когда собственная частота колебаний пьезопластины будет соответствовать частоте переменного тока генератора, возбуждающего её. Собственная частота пластины может быть определена из соотношения:

где S– толщина пьезопластины, мм;
λ – длина волны, мм;
С – скорость распространения ультразвука, м/с;
f – частота ультразвука, МГц.
Для создания электрического контакта на поверхность пьезопластины наносят тонкие слои серебра, служащие электродами. Если к электродам пластины подвести переменный ток частотой более 2х104 Гц, она будет колебаться с ультразвуковой частотой. Эти колебания могут быть переданы упругой среде, с которой она соприкасается, в виде ультразвуковых волн. Наоборот, если ультразвуковые волны воздействуют на пьезопластину, то с ее электродов можно снимать переменный ток с частотой равной частоте ультразвуковых колебаний.
Устройства, служащие при дефектоскопии для получения и ввода ультразвуковых волн в контролируемое изделие, называют излучающими искательными головками, а устройства, преобразующие ультразвуковые волны в переменный ток, - приемными искательными головками.
3.3. РАСПРОСТРАНЕНИЕ УЛЬТРАЗВУКОВЫХ КОЛЕБАНИЙ.
Распространение ультразвуковых колебаний происходит по законам геометрической акустики, которая по аналогии с геометрической оптикой соответствует предельному случаю малых волн, когда λ → 0. В однородной изотропной упругой среде ультразвуковые лучи ортогональны к волновым поверхностям и направлены в сторону внешних нормалей к этим поверхностям.
Рассмотрим волновое поле дискового излучателя (рис. 3.3). Если окружающая упругая среда однородна и изотропна, то излучатель создает в ней волновое поле, имеющее вблизи него почти цилиндрическую форму (ближняя зона, зона дифракции Френеля), а с некоторого расстояния r0 приобретающее форму усеченного конуса с углом 2θ при вершине (дальняя зона Фраунгофа).
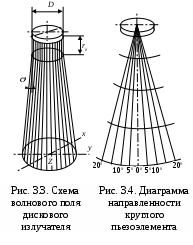
Протяженность ближней зоны может быть определена по формуле:
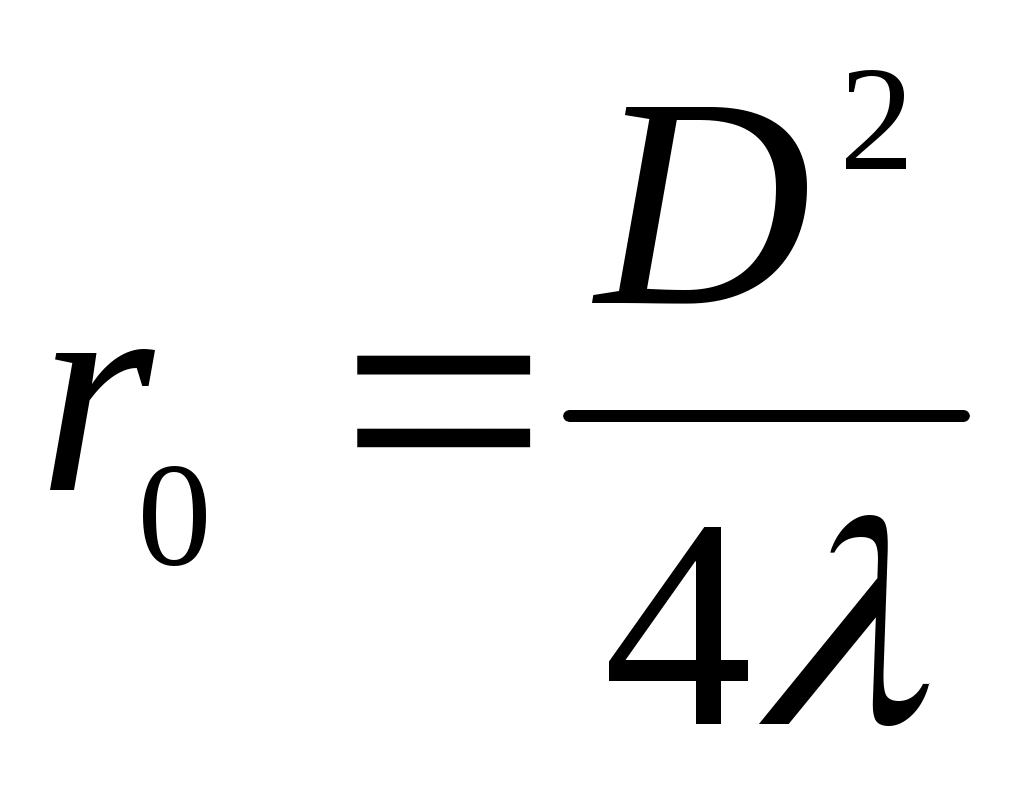
где D - диаметр излучателя, мм,
λ – длина волны УЗК, мм.
Половина угла раствора конуса, в котором почти полностью концентрируется генерируемая излучателем энергия, может быть определена из соотношения:
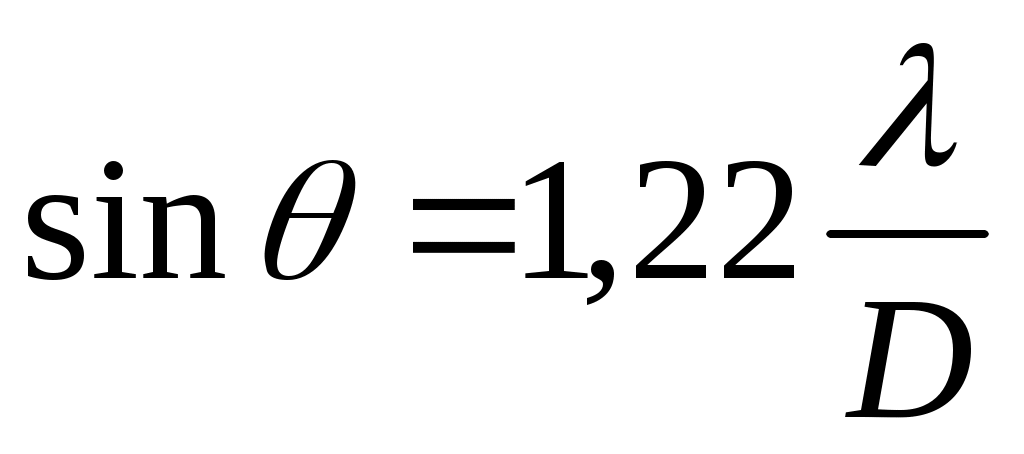
где θ – угол между осью пучка ультразвуковых колебаний и крайним лучом (рис3.3).
Однако в пределах этого конуса интенсивность ультразвука неодинакова: она уменьшается по направлению от оси пучка к периферии. Это свойство излучателя характеризуется его диаграммой направленности, представляющей собой полярную или прямоугольную диаграмму изменения акустического поля (интенсивности или давления) в зависимости от направления. Если размеры излучателя меньше длины волны, то от него распространяются сферические волны и излучение будет не направленным. Если размеры излучателя больше длины волны, то излучаемая энергия концентрируется преимущественно по одному направлению, совпадающему с направлением нормали к излучающей поверхности.
Направленность излучателей определяют относительными измерениями или экспериментально. Для некоторых простейших случаев характеристики направленности излучателей могут быть рассчитаны.
На (рис. 3.4) показана полярная диаграмма направленности излучения – приема для пьезоэлемента диаметром 12 мм на частоте 2,5 МГц (λ=2,34 мм). Боковые лепестки вследствие их малости не показаны.
По мере удаления от излучателя амплитуда колебаний уменьшается. Это обусловлено геометрическим расхождением лучей, что приводит к увеличению площади фронта волны, а также наличием потерь в среде, приводящих к постепенному затуханию колебаний при их распределении.
Затухание ультразвуковых колебаний с расстоянием опреляется коэффициентом затухания δ. Затухание ультразвуковых колебаний происходит по экспоненциальному закону
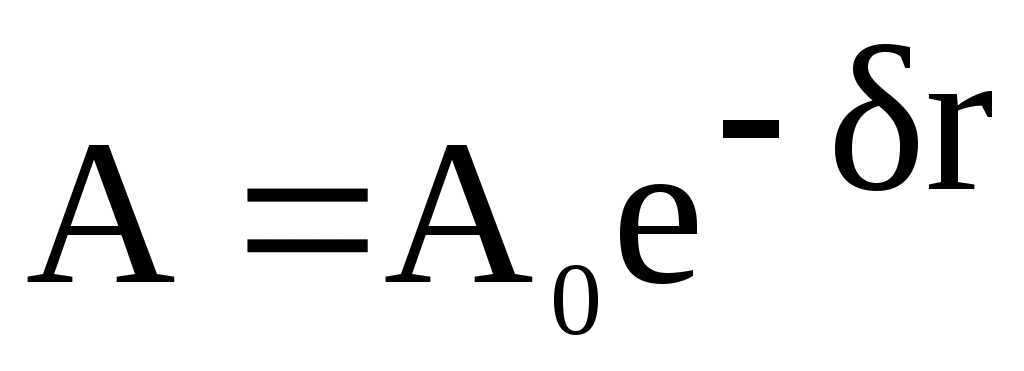
где А – амплитуда в точке измерения;
r – расстояние, пройденное волной, м;
А0 – амплитуда волны, прошедшей расстояние r без учёта затухания;
δ – коэффициент затухания, м-1.
Коэффициент затухания
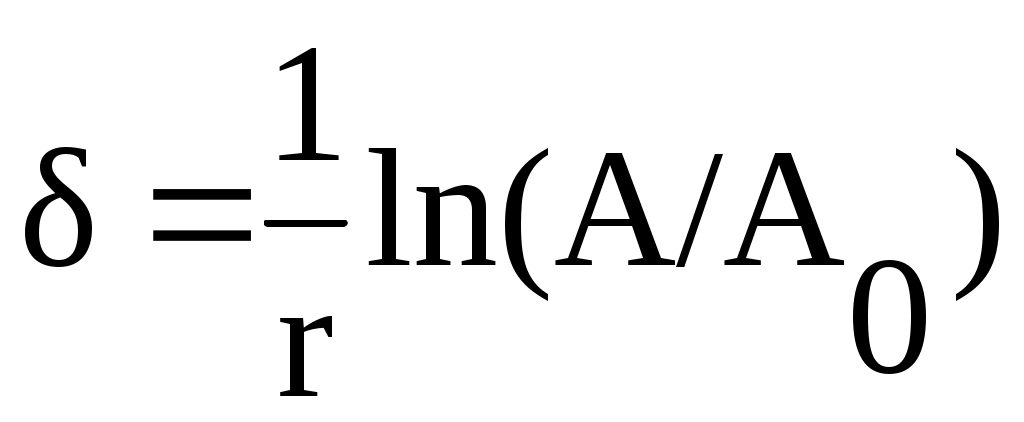
выражается в неперах/м (Нп/м) и имеет размерность м-1. Часто его представляют также в децибелах/м (дБ/м). При этом 1 Нп/м=8,686 дБ/м. 1 дБ/м=0,1151 Нп/м. Общее ослабление сигнала вследствие затухания в среде <А/А0>=<δ>r. Эту величину добавляют к ослаблению, вызываемому другими факторами.
Коэффициент затухания (δ) различен для различных материалов и складывается из коэффициентов поглощения (δ n) и рассеяния (δ r):
δ = δ n + δ r. (3.7)
В однородной изотропной упругой среде и в монокристаллах металлов затухание определяется поглощением ультразвука. При этом энергия упругих колебаний переходит в тепловую.
В поликристаллической среде и в металлах, обладающих упругой анизотропией, затухание определяется рассеянием энергии колебаний зернами металла. Это приводит к дополнительному уменьшению интенсивности колебаний в направлении распространения волн.
Для твердых тел коэффициент поглощения чаще всего пропорционален частоте δn/f для стали 0,1-1,5 Нп/МГц×м; для алюминия – 0,05-0,06; для магния – 0,1. Поглощение определяет затухание акустических волн в аморфных твёрдых телах, а также в монокристаллах.
Большинство твёрдых тел состоит из большого числа зёрен-кристаллов, на границах которых происходит рассеяние ультразвуковых волн. Вследствие этого роль рассеяния оказывается значительной и часто превалирующей. Особенно велико рассеяние в материалах, состоящих из разнородных частиц (чугун), и в материалах с большой упругой анизотропией – разной скоростью упругих волн для разных направлений в кристалле (медь, аустенитная сталь).
Для металлов δp увеличивается с ростом упругой анизотропии, среднего размера кристаллитов D и частоты: δpfn(n=2-4). В области λ/D= 4-10 δp Df2, а при λ>D δp D3f4. К примеру, в малоуглеродистой стали для продольных и поперечных волн при λ >10D:
δl≈0,12f+20D3f4,
δt≈0,1f+105D3f4.
Здесь D – в мм, f – в МГц, δ – в Нп/м.
Значения коэффициентов затухания в зависимости от частоты для некоторых материалов приведены на рис. 3.5.
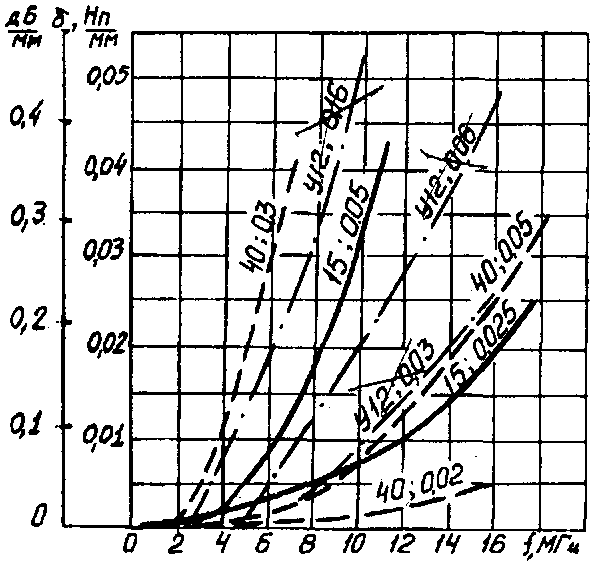
Рис. 3.5а. Коэффициент затухания продольных волн в сталях (даны марка стали и средний размер зерна в мм).
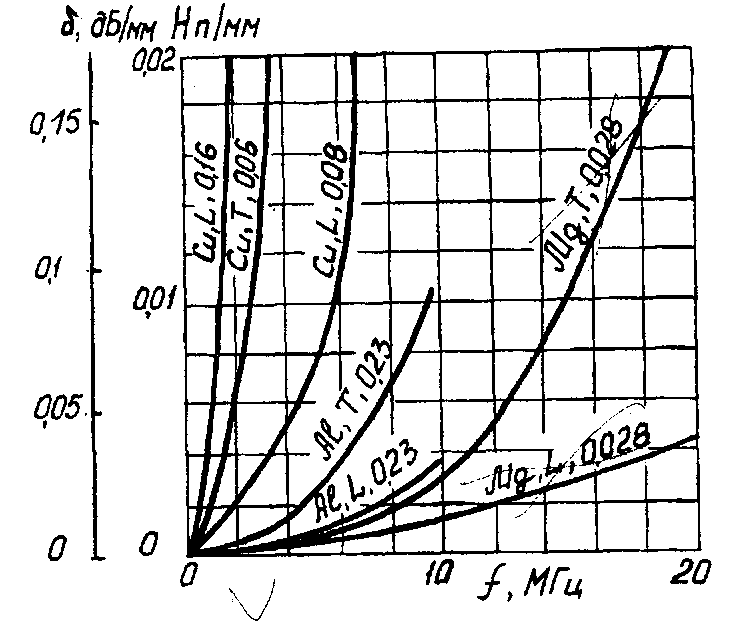
Рис. 3.5б. Коэффициент затухания в металлах (даны химический символ, тип волны, средний размер зерна в мм).
При распространении ультразвуковых волн в металлах возможна реверберация – постепенное затухание колебаний, обусловленное повторными отражениями.
Реверберация может быть объемной (из-за многократного отражения колебаний от граней контролируемого изделия) и структурной (из-за многократного отражения и рассеяния колебаний границами зерен металла). Возникновение структурной реверберации может быть объяснено анизотропией упругих свойств зерен металла, благодаря чему ультразвук при переходе из одного зерна в другое претерпевает отражение на их границах, преломление при переходе через границы и постепенное рассеяние во все стороны.
При распространении ультразвуковых волн в упругой среде могут наблюдаться интерференционные и дифракционные явления.
Интерференция – это результат сложения двух или нескольких когерентных колебаний, воздействующих на одну и ту же точку пространства. Она существенно влияет на характер акустического поля излучателя и определяет направленность распространения ультразвукового пучка.
Интерференция может привести к образованию стоячих волн, характеризующихся тем, что вдоль оси поля наблюдается чередование неподвижных точек и точек, колеблющихся с максимальной амплитудой.
Явление дифракции широко распространено в акустике. Оно связано с тем, что в случае наличия в среде препятствий, размеры которых соизмеримы с длиной звуковой волны или меньше ее, уже нельзя рассматривать распространение звука на основе лучевых представлений. В этом случае звук может огибать препятствия, образуя акустическое поле в таких местах, куда не проникает прямой луч от источника.
Если размеры препятствия равны длине волны или меньше, то лучи почти не отражаются от него, а огибают препятствие и рассеиваются в окружающей среде. Отражение лучей будет наблюдаться только в том случае, если размеры препятствий больше длины волны ультразвука.
Законы отражения и преломления ультразвуковых волн аналогичны законам геометрической оптики. Встречая на своем пути среду с другими акустическими свойствами, часть ультразвуковой энергии отражается от границы сред, а оставшаяся часть входит в новую среду. Рассмотрим явления, наблюдающиеся на плоской поверхности раздела двух сред.
Пусть плоская упругая продольная волна, распространяясь со скоростью С1 в однородной среде с плотностью ρ1, доходит до границы со второй средой с плотностью ρ2 и скоростью распространения волны в ней С2.
Условимся углом α падения ультразвукового луча называть угол, образованный лучом и нормалью к поверхности в точке падения луча.
При перпендикулярном падении ультразвукового луча на границу раздела сред отраженный луч будет также перпендикулярен к этой границе (рис. 3.6, а). При наклоном падении ультразвукового луча на границу раздела волна отразиться под углом β`, равным углу падения α (рис. 3.6, б). Если первая среда твердое тело, в котором могут распространяться как продольные, так и сдвиговые волны, то часть энергии падающей волны преобразуется в сдвиговую. Так как скорость распространения продольной волны примерно в два раза больше, чем сдвиговой, последняя отразится под углом γ`, меньшим угла β`.
Т
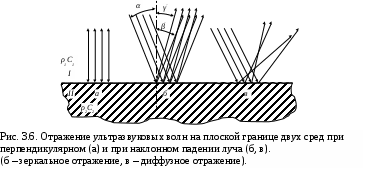
ак отражаются ультразвуковые волны от гладкой поверхности (зеркальное отражение). Если поверхность раздела имеет неровности, высота которых превышает 0,05 – 0,1 длины волны, то наблюдается диффузное отражение (рис. 3.6, в).
Если лучи падают на границу раздела двух сред под углом, отличным от прямого, то наряду с отражением наблюдается также и преломление, причем отношение синусов углов падения, отражения и преломления равно отношению скоростей распространения колебаний соответствующего вида в первой и второй средах. Если ρ1С1<ρ2C2, то при переходе продольных упругих волн из одной твердой среды в другую, кроме двух отраженных лучей, будут наблюдаться также и два преломленных (рис. 3.7).
Р
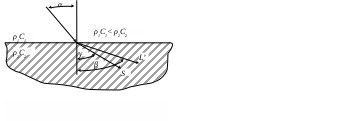
Углы падения, отражения и преломления связаны следующим соотношением:
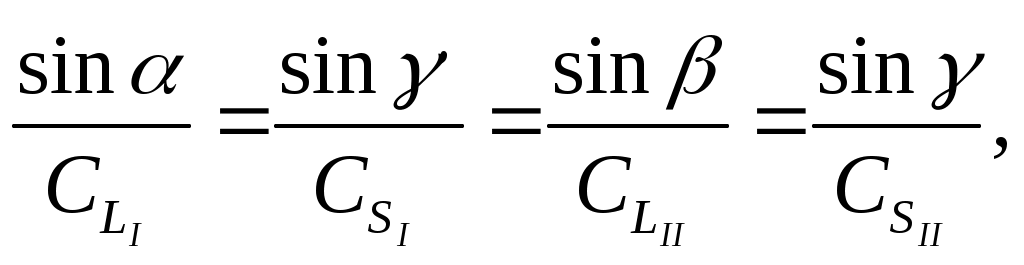
где СLI, CLII, CSI, CSII – скорости распространения продольных и сдвиговых волн в первой и второй средах соответственно.
При увеличении угла падения α продольной волны L углы β и γ будут также увеличиваться и при некотором значении α = αкрI (первый критический угол) преломленные продольные волны будут распространяться по поверхности, не проникая в глубь второй среды (рис. 3.8, а). При дальнейшем увеличении угла падения до значения αкрII (второй критический угол) по поверхности будут распространяться преломленные сдвиговые волны (рис. 3.8, б).
Для ультразвуковых лучей в полной мере справедлив закон обратимости или, как его еще называют в оптике, закон взаимности. Если луч падает из первой среды на границу со второй под углом α, преломляется и входит во вторую среду под углом β, то луч, падающий из второй среды на границу с первой под углом β, после преломления войдет в первую среду под углом α. Отсюда следует известное из оптики соотношение для относительных показателей преломления обеих сред:
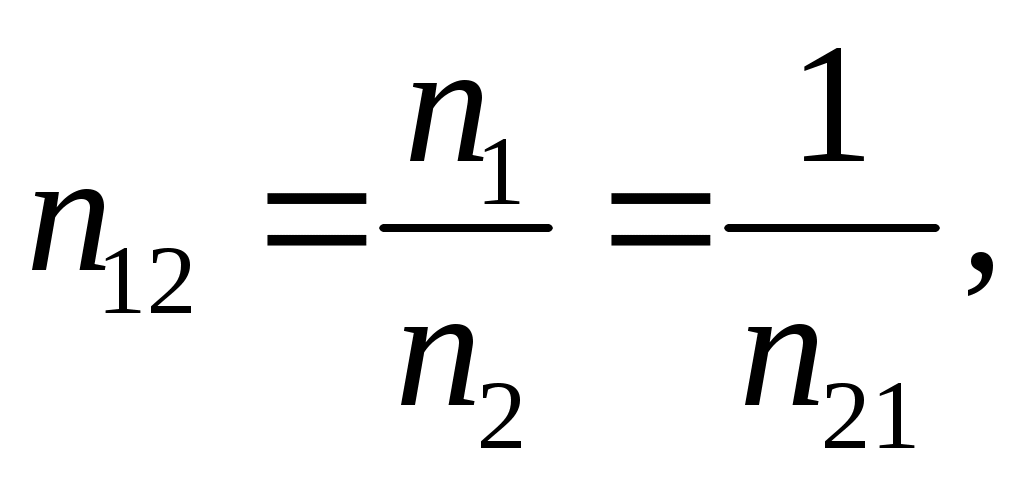
г
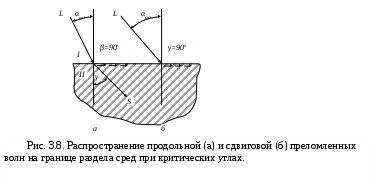
3.4. ОСНОВНЫЕ МЕТОДЫ УЛЬТРАЗВУКОВОГО КОНТРОЛЯ
Классификация акустических методов контроля показана на рис. 3.9.

Рис. 3.9. Классификация акустических методов контроля
Из большого многообразия методов акустического контроля (ГОСТ 23829—79), для контроля сварных швов применяют эхо-метод, теневой, зеркально-теневой, эхо-зеркальный метод, дельта-метод.
Эхо-метод (рис. 3.10) основан на регистрации эхо-сигнала, отраженного от дефекта. Кроме преимущества одностороннего доступа он также имеет наибольшую чувствительность к выявлению внутренних дефектов (Sminплоск≈ ≈0,5 мм2 и 2b=0,8 мм), высокую точность определения координат дефектов. К недостаткам метода следует отнести, прежде всего, низкую помехоустойчивость к наружным отражателям, резкую зависимость амплитуды сигнала от ориентации дефекта. Этим методом контролируют около 90% всех сварных соединений толщиной 4 мм и более.
Р
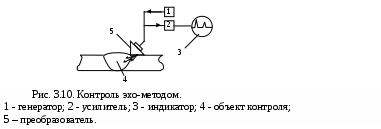
асчёт эхо-сигнала по АРД-диаграмме. Для плоскодонного отверстия, чаще других используемого в качестве искусственного отражателя, и полуплоскости разработаны удобные способы расчёта максимальных эхо-сигналов, применяемые для широкого диапазона диаметров.
Плоскодонное отверстие. Амплитуды максимальных сигналов от от плоскодонных отверстий определяют с помощью семейства кривых амплитуда-расстояние-диаметр (АРД-диаграмм). На рисунке 3.11 даны безразмерные АРД-диаграммы с линейным масштабом по оси абсцисс, на которой отложено приведённое расстояние (r/r6) преобразователь-отражатель (т.е. расстояние делённое на длину ближней зоны r6=N). Параметром семейства кривых является отношение диаметра диска к диаметру излучателя. Заштрихованные области в левой части диаграммы соответствуют изменению амплитуд, вызываемому различной длительностью ультразвуковых импульсов.
Пример использования АРД-диаграммы. Определим с помощью АРД-диаграммы амплитуду сигнала от плоского дефекта диаметром 6 мм, расположенного в стальном образце на глубине 100 мм перпендикулярно оси нормального искателя диаметром 12 мм, на частоту 2,5 МГц.
Длина волны λ=Сl/f=5,9∙106/2,5∙106=2,35 мм. Длина ближней зоны rб=а2/λ=62/2,35=15,3 мм. Приведённое расстояние r/rб=100/15,3=6,5. приведённый диаметр дефекта 2b/2a=6/12=0,5. на пересечении вертикали r/rб=6,5 и кривой 2b/2a=0,5 находим P´/P0=25,5 отр. дб.=0,053.