ремонт автомобилей. remont auto КАРАГОДИН. В процессе эксплуатации автомобиля его рабочие свойства постепенно ухудшаются изза изнашивания деталей, а также коррозии и усталости материала, из которого они изготовлены
![]()
|
|
Порошок | Фракции | Скорость наплавки, см/мин | Микротвердость -1 03, МПа | Прочность сцепления с основой, МПа |
ПН73ХСЗРЗ | 200. ..300 | 38 | 7,5 | 250 |
28 | 6,5 | |||
21 | 5,5 | |||
13 | 4,5 | |||
100. ..200 | 38 | 6,5 | ||
28 | 6,0 | |||
21 | 5,5 | |||
13 | 3,5 | |||
60. ..100 | 38 | 3,2 | ||
28 | 2,9 | |||
21 | 2,5 | |||
13 | 2,4 | |||
ПГФБХ-6-2 | 100. ..200 | 15. ..38 | 8,0. ..10,0 | 350 |
200. ..400 | 15. ..35 | 8, 5. ..11,0 | ||
400... 600 | 15. ..30 | 9,0... 11,5 |
Электроконтактная приварка ленты (проволоки). Сущность процесса — точечная приварка стальной ленты (проволоки) к поверхности детали в результате воздействия мощного импульса тока. В точке сварки происходит расплавление металла ленты (проволоки) и детали. Схема приварки металлической ленты к поверхности вала показана на рис. 13.11. Деталь 2 устанавливают в центрах 1 или патроне, а сварочная головка с роликами 4. Лента (проволока) плотно прижимается роликами посредством пневмоцилиндров. Подвод тока к роликам производится от трансформатора 5. Требуемая Длительность цикла обеспечивается прерывателем тока.
Ленту приваривают ко всей изношенной поверхности или по винтовой линии в процессе вращения детали. Скорость вращения Детали пропорциональна частоте импульсов и продольному перемещению сварочной головки.
Преимущества способа: высокая производительность процесса (в 2,5 раза превосходит вибродуговую наплавку); малое тепловое воздействие на деталь (не более 0,3 мм); небольшая глубина плавления; незначительный расход материала (в 4...5 раз превосходит вибродуговую наплавку); возможность получения неплавленного металла с любыми свойствами; благоприятные санитарно-производственные условия работы сварщика, а недостаток — ограниченность толщины наплавленного слоя и сложность установки.
Способ электроконтактной приварки ленты используется для восстановлении поверхностей валов, а также отверстий в чугунных и стальных деталях, в том числе корпусных.
Твердость, износостойкость и прочность сцепления ленты с деталью зависят от марки стали ленты. Высокую твердость обеспечивают ленты из хромистых и марганцевых сталей. Рекомендации по выбору материала ленты представлены в табл. 13.12. Толщина ленты берется в пределах 0,3... 1,5 мм. Усилие прижатия роликов при приварки ленты 1,3... 1,6 кН.
Ролики (электроды) изготавливают из специальных медных сплавов, бронзы (БрНБТ, ХКд-0,5-0,3, БрХ, БрХЦр-0,6-0,05), сплава Мц-4, меди М-1.
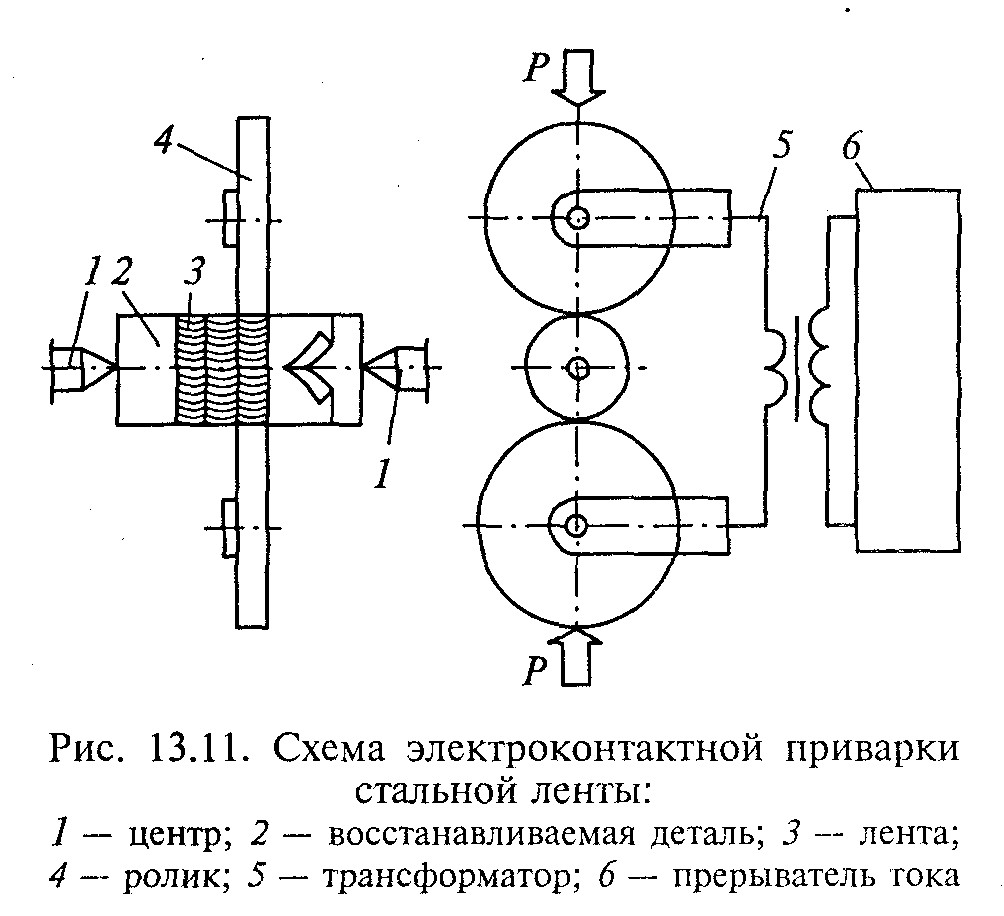
Для восстановления деталей применяют установки «Ремдеталь»: 011-1-02 и ОКС-12296-ГОСНИТИ - для шеек валов; 011-1-05 -для резьбовых участков валов малого диаметра и поверхностей деталей типа «вал»; 011-1-06 — для внутренних поверхностей гильз цилиндров; 011-1-11 — коренных опор блоков цилиндров.
Режим приварки определяется показателями:
электрическими — сила сварочного тока и длительность сварочного цикла. Малая сила тока не обеспечивает надежной приварки, а большая сила тока приводит к образованию на поверхности детали пор и трещин;
механическими — частота вращения, подача электродов, усилие сжатия электродов. Подачу электродов, частоту вращения детали, продолжительность сварочного цикла подбирают из условия получить 6... 7 сварочных точек на 1 см длины шва (подбирают на эталонных образцах при постоянной скорости вращения). Подача электрода обеспечивает перекрытие сварных точек: малое перекрытие ухудшает свариваемость ленты с основным металлом, а повышенное — увеличивает зону отпуска, что снижает твердость приваренного слоя. Недостаточное усилие сжатия электродов на поверхности ленты и детали приводит к эрозионному разрушению, сопровождающемуся сильным искрением в зоне контакта; большое усилие сжатия электродов приводит к деформации электродов и снижению их стойкости.
Таблица 13.12
Твердость приваренного слоя в зависимости от материала ленты
Марка стали привариваемой ленты | Твердость приваренного слоя, HRC | Марка стали привариваемой ленты | Твердость приваренного слоя, HRC |
Сталь 20 Сталь 40 Сталь 45 | 30. ..35 40. ..45 45. ..50 | Сталь 55 Сталь 40Х Сталь 65Х | 50. ..55 55. ..60 60 ...65 |
Ориентировочные режимы приварки стальной ленты приведены в табл. 13.13.
Таблица 13.13
Режимы приварки стальной ленты
Параметры | Детали | |
корпусные | типа «вал» | |
Сила сварочного тока, А | 7,8. ..8,0 | 16,1. ..18,1 |
Длительность сварочного цикла, с | 0,12. ..0,16 | 0,04. ..0,08 |
Длительность паузы, с | 0,08. ..0,10 | 0,10. ..0,12 |
Скорость сварки, м/мин | 0,5 | 0,7. ..1,2 |
Подача электродов, мм/об | Ручная | 3...4 |
Усилия сжатия электродов, кН | 1,70. ..2,25 | 1,90. ..1,60 |
Ширина рабочей части электродов, мм | 8 | 4 |
Диаметр рабочей части электродов, мм | 50 | 150. ..180 |
Материал ленты | Сталь 20 | Сталь 40. ..50 |
Материал детали | Чугун СЧ 18-36; СЧ 21-40 | Сталь любая |
Расход охлаждающей жидкости, л/мин | 0,5...1,0 | 1,5...2,0_ |
Для деталей типа «вал» диаметром 30...50 мм рекомендуются следующие режимы приварки ленты толщиной 0,44 мм: частота вращения — 5 мин'; подача сварочной головки — 3 мм/мин; усилие сжатия электродов — 1,5 кН; количество охлаждающей жидкости — 1,5 л/мин.
Роль охлаждающей жидкости — это охлаждение роликов сварочной головки и эффективный отбор теплоты из зоны приварки. Твердость восстанавливаемой поверхности достигает 55 HRC и более.
Особенности сварки чугунных деталей. Многие корпусные детали изготавливаются из серого, высококачественного и ковкого чугуна, который является трудносвариваемым материалом. У деталей из чугуна сваркой заделывают трещины и отверстия, присоединяют отколотые части детали, наплавляют износостойкие покрытия.
Наличие в чугуне значительного содержания углерода и низкая его вязкость вызывают значительные трудности при восстановлении деталей из этого материала. Быстрое охлаждение чугуна приводит к образованию в околошовной зоне твердых закалочных структур. Местный переход графита в цементит, который может произойти при расплавлении чугуна, приводит к образованию структуры белого чугуна. В этих зонах металл тверд и хрупок. Разница в коэффициентах линейного расширения серого и белого чугуна является причиной образования внутренних напряжений, что приводит к появлению трещин. Выгорание углерода и кремния в процессе сварки приводит к тому, что сварочный шов получается пористым и загрязненным шлаковыми включениями. Они появляются в результате неполного выделения газов и шлаков из-за быстрого перехода чугуна из жидкого состояния в твердое.
Таким образом, трудность сварки чугунных деталей вызывается следующими основными причинами: отсутствие площадки текучести у чугуна, хрупкость и небольшой предел прочности на растяжение вызывает образования трещин в процессе сварки; отсутствие переходного пластического состояния при нагреве до плавления. Текучесть чугуна в процессе сварки затрудняет восстановление деталей даже с небольшим уклоном от горизонтального положения; получение отбеленных участков карбида железа Fe3C и высокоуглеродистых сталей, которые трудно поддаются механической обработке.
При восстановлении чугунных деталей можно применить горячий и холодный способы сварки.
Горячая сварка чугуна — процесс, который предусматривает нагрев детали (в печи или другими способами) до температуры 650...680°С. Температура детали во время сварки должна быть не ниже 500 °С. Такие температуры позволяют: задержать охлаждение сварочной ванны, что способствует выравниванию состава металла ванны; освободить свариваемую деталь от внутренних напряжений литейного и эксплуатационного характера; предупредить появление сварочных напряжений и трещин. Для деталей с большой жесткостью (блок цилиндров и другие корпусные детали) при сварке обязателен общий нагрев.
В процессе сварки происходят структурные преобразования с перераспределением внутренних напряжений (термическое воздействие). Металл, на который непосредственно действует сварочная Дуга, плавится, образуя жидкую ванну, а тот, который соприкасается со сварочной ванной, нагревается вследствие теплоотдачи. В результате скорости нагрева и охлаждения отдельных участков зоны термического влияния при сварке неодинаковы. Металл сварочной ванны при охлаждении кристаллизуется (с большой скороетью) в тонкий слой первого участка зоны термического влияния Происходит уменьшение объема за счет усадки на 1 %. Этот слой первого участка связан с основным металлом детали и твердым металлом шва, что мешает нормальной усадке и приводит к возникновению напряжений растяжения и образованию трещин.
Усадка во время охлаждения сокращает длину валика (валик соединен с основным металлом), а основной металл детали растягивает его. Этот процесс является следствием образования поперечных трещин. Для предотвращения этого процесса необходимо: обеспечить достаточную пластичность наплавленного шва (подобрать соответствующие присадочный материал, обмазку и режимы сварки); проковывать швы во время кристаллизации; равномерно нагревать и особенно охлаждать как шов, так и свариваемую деталь; сварку выполнять на постоянном токе обратной полярности («+» — электрод, «—» — деталь) и малой силы (25...30 А на 1 мм диаметра электрода); наплавлять валики длиной 30...40 мм; применять сварку отжигающими валиками и многослойным швом.
Если при сварке чугуна использовать электрод из низкоуглеродистой стали, то металл шва получится высокоуглеродистым (т.е. будет отличаться высокими хрупкостью и твердостью). Количество углерода в металле шва зависит от геометрии шва, в частности, отношения h\/hi, где h\ — глубина противления; Л2 — усиление шва (рис. 13.12). Чем меньше значение этого отношения, тем меньше в металл шва поступает расплавленного чугуна детали и тем ниже содержание в шве углерода. Например, если в чугуне около 3 % углерода-, то в металле шва в зависимости от h\ углерода будет 1,5...2,0% (в нижней части больше, чем в верхней). Снижают содержание углерода в наплавленном слое за счет уменьшения силы сварочного тока (глубины проплавления чугуна /г,), подбора компонентов покрытия электрода и многослойности сварного шва.
Изменяя состав и толщину обмазки сварочной проволоки, скорость сварки и силу тока, можно получить стальной шов с разным содержанием углерода и разной твердости — от закаленной высокоуглеродистой стали до мягкой отпущенной низкоуглеродистой. Лучшие результаты при горячей сварке чугуна дает ацетилено-кислородное пламя с присадочным материалом из чугуна.
Горячая сварка чугуна предполагает необходимость применения специального нагревательного оборудования: термические и нагревательные печи, кожухи, термостаты и т. д. Поэтому этот способ сварки применяют только в тех случаях, когда необходимо получить наплавленный металл, близкий по структуре, прочности и износостойкости к основному металлу детали.
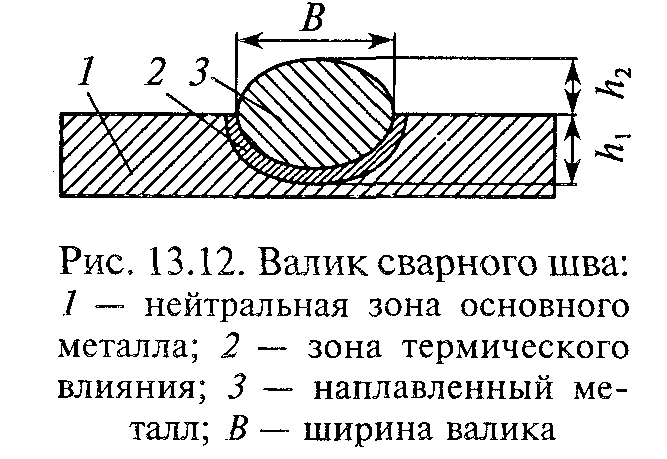
При сварке необходимо обязательно применять флюс, который выполняет следующие функции: растворяет образующиеся окси-дЬ1 кремния и марганца, переводя их в шлак; окисляет и частично растворяет графитные включения чугуна, находящиеся на свариваемых поверхностях; образует микроуглубления, которые повы-!0ают свариваемость чугуна; предохраняет от окисления расплавленную ванну; увеличивает текучесть сварочных шлаков. В качестве флюса применяют техническую безводную буру (Na2B4O7). Бура в чистом виде для сварки не пригодна, так как высокая температура ее плавления вызывает образование в сварочной ванне густых шлаков, которые плохо всплывают на поверхность металла, в результате чего образуются шлаковые раковины. Применение в качестве флюса смеси из 50 % переплавленной измельченной буры и 50 % кальцинированной соды увеличивает текучесть шлаков и расплавленного металла в ванне, улучшает качество сварки. Лучшие результаты дает флюс ФСЧ-1 следующего состава (% по массе): буры — 23, кальцинированной соды — 27, азотнокислого натрия — 50.
Кромки трещины для сваривания готовят механическим способом или оплавлением металла газовой горелкой с избытком кислорода. Перед сваркой подогретые кромки и конец стержня покрывают слоем флюса. Пламя горелки должно быть строго нейтральным. В ванну расплавленного металла вводят присадочную проволоку с флюсом, подогретые перед этим до температуры плавления. Затем сварщик концом чугунной проволоки воздействует на кромки ванны, делая круговые движения.
Горячей сваркой ацетиленокислородным пламенем с присадкой чугуна рекомендуется восстанавливать блоки цилиндров двигателей и других корпусных деталей при наличии трещин на ребрах жесткости.
Газовую сварку чугуна цветными сплавами без подогрева детали выполняют в сочетании с дуговой сваркой и широко применяют в ремонтном производстве для сварки трещин на обрабатываемых поверхностях корпусных деталей. Присадочный материал — латунь. Температура плавления латуни ниже температуры плавления чугуна (880...950°С), поэтому ее можно применить для сварки, не доводя чугун до плавления и не вызывая в нем особенных структурных изменений и внутренних напряжений. Использование этого процесса позволяет получить сварочные швы плотные, легко поддающиеся обработке.
При сварке трещин в чугунных деталях выполняют следующие операции: снятие с кромок трещин фасок с углом разделки 70... 80 °; Фубая обработка фасок (желательно с образованием насечки); °чистка места сварки от грязи, масла и ржавчины; подогрев подготовленных к сварке мест пламенем газовой горелки до температуры 900... 950 °С; нанесение на подогретую поверхность слоя флюса; Нагрев в пламени горелки конца латунной проволоки; натирание Латунной проволокой горячих кромок трещины (латунь должна Докрывать фаски тонким слоем); сварка трещины; медленный от-В°Д пламени горелки от детали; покрытие шва листовым асбестом.
При холодной сварке чугуна деталь не нагревают (возможен подогрев не выше 400 °С для снятия напряжения и предупреждения возникновения сварочных напряжений). Сварочная ванна имеет небольшой объем металла и быстро твердеет. Способ получил более широкое применение по сравнению с горячей сваркой из-за простоты выполнения.
В зоне сварного шва происходят отбеливание и закалка с одновременным ростом внутренних напряжений, которые могут привести к образованию трещин.
Высота сварочного шва определяется значением (h{ + /z2), не одинакова для электродов с разными покрытиями и находится в пределах 4...7 мм.
Холодная сварка применяется для устранения трещин и заварки пробоин в тонкостенных корпусных и крупногабаритных чугунных деталях, которые требуют последующей механической обработки и эксплуатируются под нагрузкой при тепловом воздействии.
Заварка трещин в тонких (до 10 мм) ненагруженных стенках осуществляется без разделки кромок. Процесс заварки в этом случае проводят в следующем порядке: поверхность детали очищают на расстоянии 25 мм от краев трещины; концы трещины обваривают за два прохода (рис. 13.13, а); дугу возбуждают на расстоянии 10... 12 мм от одного конца трещины и ведут сварку в направлении другого конца трещины (валик наваривают на расстоянии 10... 12 мм от конца трещины); не прерывая дуги, ведут сварку в обратном направлении, вторым слоем перекрывая первый; делят трещину на участки длиной 30...50 мм; отступив от конца трещины на выбранную длину участка, наплавляют с двух сторон трещины (отступая от ее краев на 1... 1,5 мм) подготовительные валики 1, 2 и 3, 4 (ширина валика равна толщине стенки детали), причем валики 2 и 4 не должны соприкасаться со стенками детали и перекрывать валики, которые лежат под ними; очистка наплавленных вдоль кромок трещины валиков от шлаков; наплавка валиков 5 и б (за два прохода, не прерывая дуги), образуя шов, закрывающий трещину; проковы-вание молотком участка шва (после окончания сварки), не зачищая шлака. В таком же порядке сваривают и другие участки трещины (//, ///, IV, V}.
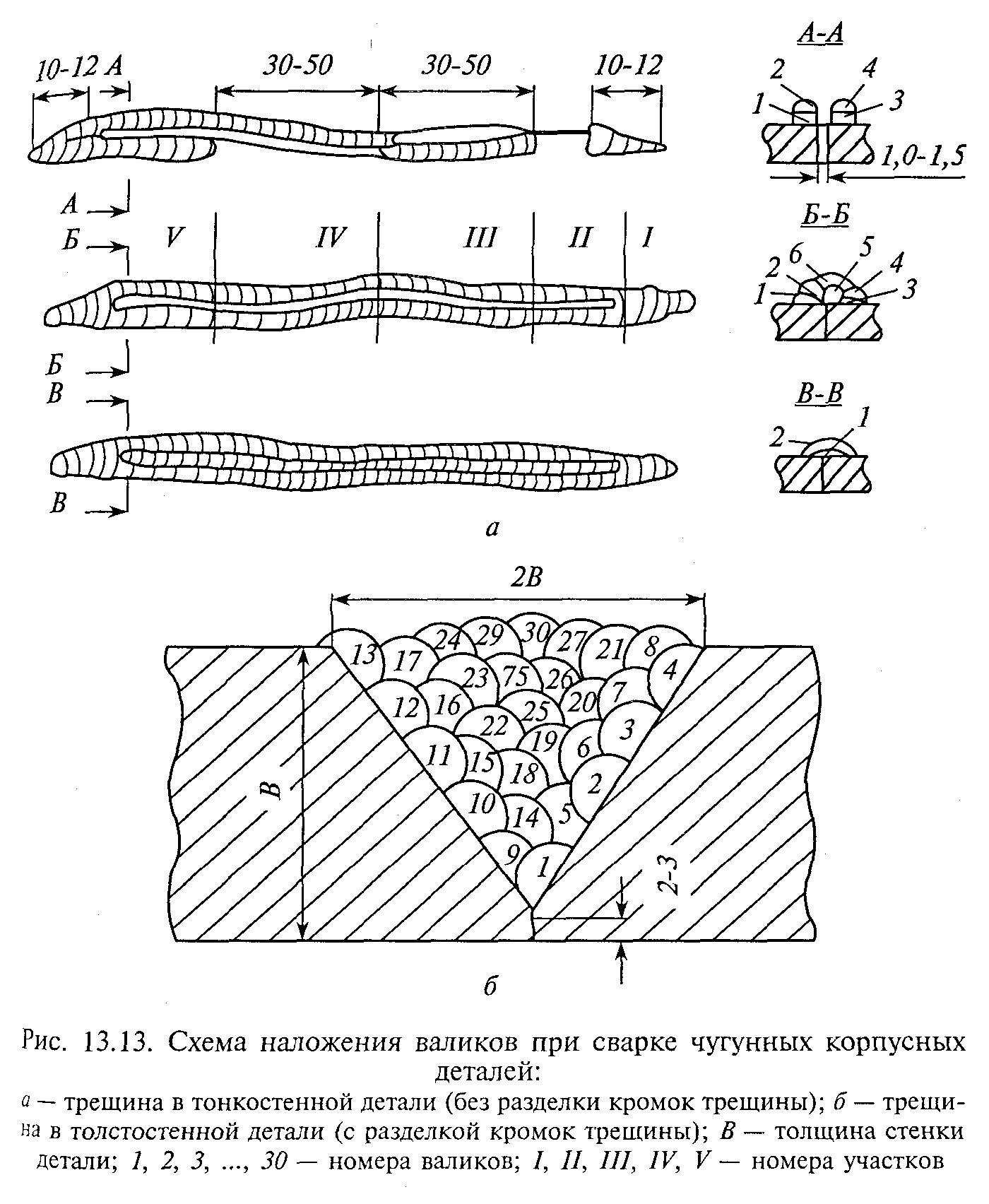
Сварку трещин в толстостенных деталях (рис. 13.13, б), которые в дальнейшем подвергаются механической обработке или работают под нагрузкой, проводят с разделкой кромок. Ширина разделки краев трещины под сварку на поверхности детали должна быть в 2 раза больше ее толщины, а глубина разделки на 2...3 мм меньше этой толщины. Кромки трещины разделывают фрезерованием или слесарным способом вручную. При такой технологии облегчается сварка деталей в вертикальной плоскости.
Подготовительные валики на кромки трещины наплавляют раздельно: сначала два ряда валиков 1—8 на одну сторону среза вверх на участке протяженностью 30...50 мм, а затем — на другую сторону среза валики 9—17. Каждый предыдущий валик должен частично перекрываться последующим. После наплавки первого слоя очищают шлак и наплавляют второй. Подготовительные валики второго слоя не должны соприкасаться с основным металлом.
Так же наплавляют подготовительные валики и на других участках, дают им охладиться до температуры 30... 50°С, счищают с Них шлак и в такой же последовательности, как и при наплавке скосов, соединяют валики центральными (соединительными) вабиками. Заполнение шва на каждом участке проводят с перерывом для охлаждения.
Холодная сварка может осуществляться:
электродами МНЧ-1 (63 % Ni + 37 % Си) со специальным фтористо-кальциевым покрытием. Процесс сварки выполняется электродами диаметром 3...4 мм на постоянном токе 140... 150 А обратной полярности, короткой дугой, участками 20...30 мм, которые сразу же проковываются, Вместо медно-никелевых электродов можно также использовать железо-никелевые электроды типа ЖНБ;
электродами ЦЧ-4, представляющими собой сварочную проволоку Св-08 или Св-08А с фтористо-кальциевым покрытием, содержащим титан или ванадий, которого в наплавленный металл переходит до 9,5%. Процесс ведется электродами диаметром 3...4 мм на постоянном токе 120... 150 А обратной полярности при напряжении 20 В. Перед сваркой рекомендуется подогреть деталь до 150...200°С, а после наложения валиков сразу же их проковывать;
электродами ОЗЧ-1, представляющими собой медную электродную проволоку с фтористо-кальциевым покрытием, содержащим железный порошок. Процесс сварки рекомендуется вести на постоянном токе 150... 160 А обратной полярности и напряжении 20 В, короткой дугой, небольшими участками по 30...60 мм. После сварки каждый участок необходимо проковывать и продолжать ее после охлаждения шва до 50...60°С.
Особенности сварки деталей из алюминия и его сплавов. Особенности сварки этих деталей состоят в следующем:
очень плохая сплавляемость алюминия (температура плавления алюминия 658 °С) из-за образования на его поверхности тугоплавкой окисной пленки (А12О3), температура плавления которой 2050 °С. Окислы снижают механическую прочность деталей. Для их удаления применяют флюсы типа АФ-4А, в состав которых входят хлористый натрий (28%), хлористый калий (50%), хлористый литий (14%) и фтористый натрий (8%);
при нагреве до 400... 450 "С алюминий сильно теряет свою прочность, и деталь может разрушиться даже от легкого удара;
алюминий, как и чугун, не имеет пластического состояния и при нагреве сразу переходит из твердого состояния в жидкое. Алюминиевые сплавы в расплавленном состоянии активно растворяют водород, который при быстром охлаждении не успевает покинуть расплавленный металл и создает в нем поры и раковины. Источник появления водорода — это влага, для удаления которой рекомендуется прогреть детали;
коэффициент линейного расширения алюминия в 2, а теплопроводность в 3 раза больше, чем у стали, что способствует появлению значительных внутренних напряжений, которые приводят к деформациям в свариваемых деталях. Для уменьшения внутренних напряжений целесообразно подогревать перед сваркой детали до температуры 250... 300°С и медленно охлаждать после сварки.
Для деталей из алюминия и его сплавов рекомендуются слеДУ" ющие способы сварки:
неплавящимся вольфрамовым электродом в среде аргона (ар-гонодуговая сварка). В качестве присадочного материала используют сплавы алюминия. В зависимости от толщины деталей используют электроды диаметром 1...5 мм, силу сварочного тока — 45... 280 А, напряжением — 22... 24 В. Расход аргона колеблется в Пределах 4... 12 л/мин. Сварку ведут на переменном токе без применения флюса;
электродами ОЗА-2 (сплава алюминия) и ОЗА-1 (технического алюминия) на постоянном токе обратной полярности, короткой дугой (электродуговая сварка). Сила тока выбирается из расчета 35...45 А на 1 мм диаметра электрода. Стержень электрода изготавливают из алюминиевой проволоки. Электрод имеет покрытие АФ-4А;
ацетилено-кислородным нейтральным пламенем (газовая сварка) с использованием флюса АФ-4А. Присадочный материал должен быть того же состава, что и основной металл. В момент расплавления основного и присадочного материалов пленку окислов разрывают с помощью стального крючка.
13.3.Техника безопасности при выполнении сварочно-наплавочных работ
В зависимости от применяемого метода сварки и наплавки зависит организация рабочего места при выполнении работ по восстановлению деталей сваркой и наплавкой. Комплекс технически связанного между собой оборудования для выполнения сварочно-наплавочных работ называется постом, установкой (станком), линией. В комплексы в зависимости от оснащения входят: сварочное оборудование (источник питания, сварочный аппарат с приборами управления и регулирования процесса); технологические приспособления и инструмент; механическое и вспомогательное оборудование (транспортные, погрузочные и разгрузочные устройства); система управления.
Источники переменного тока — это сварочные трансформаторы (для ручной сварки и наплавки ТД-300, ТД-500, СТШ-500, механизированной — ТДФ-1001, ТДФ-1002 и др.) и специализированные установки на их основе, постоянного тока — сварочные выпрямители (для ручной сварки и наплавки ВД-201УЗ, ВД-306УЗ, ВД-401УЗ и др., механизированной — ВС-600, ВСЖ-303, ВДГ- 302 и др., универсальные — ВДУ-1201УЗ, ВДУ-1601 и др.; для многопостовой сварки — ВКСМ-100-1-1, ВДМ-1001 и др.), преобразователи (ПСО-300-2, ПСО-315М и др.) и агрегаты, специализированные источники на базе выпрямителей. Сварочные машины рекомендуется Устанавливать в отдельном помещении, а на рабочем месте в этом случае должен находиться щиток для дистанционного управления.
В состав установки (станка) для сварки или наплавки, кроме электросварочного оборудования, входят: технические средства Размещения и перемещения сварочных автоматов, головок, инструментов; технические средства размещения, закрепления и перемещения изделия (сварочные манипуляторы, позиционеры, кантователи, поворотные столы, вращатели); флюсовое оборудование (при сварке и наплавке под флюсом); вспомогательное оборудование и средства управления. Вращатели — это шпиндельные устройства, предназначенные для вращения детали вокруг оси.
Основной частью комплекса оборудования для механизированной сварки и наплавки является сварочная и наплавочная аппаратура — полуавтоматы и автоматы.
На рабочем месте газосварщика устанавливают сварочный стол с подставкой для газосварочной горелки. На расстоянии 3...4 м от сварочного стола монтируют рампу с кислородным и ацетиленовым редукторами и шкаф для хранения шлангов и горелок. Ацетиленовый генератор, а также баллоны с кислородом и ацетиленом хранятся в отдельных помещениях.
К электрогазосварочным и наплавочным работам допускаются рабочие не моложе 18 лет, прошедшие медицинское освидетельствование и специальное обучение, имеющие удостоверение на право выполнения указанных работ. Все сварщики, выполняющие дуговую и газовую сварку, должны ежегодно проходить проверку знаний.
Рабочий пост сварщика должен быть оборудован местной вытяжной вентиляцией для отсоса вредных паров, газов и аэрозолей, состоящих из окислов металлов и продуктов сгорания обмазок и флюсов.
Правильное и рациональное размещение рабочего места сварщика имеет большое значение в повышении безопасности сварочных работ, производительности труда и качества сварки. В целях защиты сварщиков, подсобных и вспомогательных рабочих от лучистой энергии, горящих поблизости сварочных дуг в постоянных местах сварки для каждого сварщика устраивают отдельные кабины площадью (2 х 2)...(2 х 3) м (не считая площади, занятой оборудованием) и высотой 1,8...2 м. Для улучшения вентиляции стены кабины не доводят до пола на 15...20 см. Материалом стен кабин может служить тонкое железо, фанера, брезент, покрытые огнестойким составом, или другие огнестойкие материалы. Дверной проем, как правило, закрывается брезентовым занавесом на кольцах. Стены окрашивают в светлые матовые тона. Полы должны иметь ровную нескользкую поверхность, без выбоин и порогов. В помещениях с холодными полами, например, цементными на рабочих местах под ноги укладывают деревянные решетки или настилы.
При ручной дуговой сварке в кабине сварщика устанавливают сварочный стол или кондуктор, настенную полку для мелкого инструмента и приспособлений, стул со спинкой и другое оборудование. Кабина оборудуется местной вентиляцией.
Для предохранения глаз и лица сварщика от вредного воздействия дуги необходимо использовать щитки или маски со специальными светофильтрами в зависимости от силы сварочного тока: Э-1, при силе тока до 75 А, Э-2 — при 75...200 А, Э-3 — 200...400 А, а также ЭС-100, ЭС-300, ЭС-500.
В целях исключения попадания под напряжение при замене электродов сварщик обязан пользоваться сухими брезентовыми рукавицами, которые одновременно защищают его руки от расплавленного металла и лучистой энергии дуги.
Большое значение для безопасности сварщика имеет проверка правильности проведения проводов к сварочным постам и оборудованию. Прокладка проводов к сварочным машинам по полу или земле, а также другим способом, при котором изоляция проводов не защищена и провод доступен для прикосновения, не разрешается. Ток от сварочных агрегатов к месту сварки передается гибкими изолированными проводами. Для предупреждения поражения электрическим током все оборудование должно быть заземлено.
Электроустановки, электрооборудование и проводку разрешается ремонтировать только после отключения их от сети.
Перед началом работ электросварщик обязан надеть специальную одежду — брезентовый костюм, ботинки и головной убор.
При сварке и наплавке деталей под флюсом режим работы должен быть таким, чтобы сварочная дуга была полностью закрыта слоем флюса. Убирают флюс флюсоотсосами, совками и скребками.
Сварочную дугу при вибродуговой наплавке и сварке закрывают специальными устройствами, в которых должно быть предусмотрено смотровое окно со светофильтром нужной плотности.
При выполнении газовой сварки соблюдаются те же правила безопасности, что и при дуговой. Однако при газовой сварке необходимо следить, чтобы в радиусе 5 м от рабочего места отсутствовали горючие материалы.
В местах хранения и вскрытия барабанов с карбидом кальция запрещено курить и применять инструмент, дающий при ударе искры. Барабаны с карбидом хранят в сухих прохладных помещениях. Вскрытие барабана разрешается только латунным ножом. Ацетилен при соприкосновении с медью образует взрывчатые вещества, поэтому применять медные инструменты при вскрытии карбида и медные припои при ремонте ацетиленовой аппаратуры нельзя. Ацетиленовые генераторы располагают на расстояние не менее 10 м от открытого огня.
Баллоны с газами хранят и транспортируют только с навинченными на их горловины предохранительными колпаками и заглушками на боковых штуцерах вентилей. При транспортировании баллонов не допускаются толчки и удары. Переносить баллоны на руках запрещается. К месту сварочных работ их доставляют на специальных тележках или носилках.
Баллоны с газом устанавливают в помещении не ближе чем на 1 м от радиаторов отопления и не ближе чем на 10м — от горелок и других источников тепла с открытым огнем.
Запрещено хранить баллоны с кислородом в одном помещении с баллонами горючего газа, с барабанами карбида кальция, лаками, маслами и красками.
При обнаружении на баллоне или вентиле следов жира или масла баллон немедленно возвращают на склад. Соседство масла и кислорода может привести к взрыву.
В целях безопасности в обращении кислородные баллоны окрашивают в синий цвет, ацетиленовые — в белый, а баллоны с про-панбутановыми смесями — в красный.
Ацетилен с воздухом образует взрывоопасные смеси, поэтому нужно следить, чтобы не было утечки газа и перед началом работы тщательно проветривать рабочее помещение.
Подъемно-транспортное оборудование с механическим приводом обязательно регистрируется в инспекции Гостехнадзора, которая проводит его техническое освидетельствование.
Подъемные устройства с ручным приводом, цепи и канаты проходят освидетельствование комиссией под руководством главного инженера ремонтного предприятия. Техническая проверка содержит осмотр оборудования, поднятие груза, масса которого превышает на 10% грузоподъемность подъемного устройства по паспорту, на высоту 100 мм и выдержку в поднятом положении 10 мин. Цепи, канаты и чалочные устройства испытывают под двойным грузом. Результаты испытания заносятся в спецжурнал, а на кранах и других подъемных устройствах четко наносят краской предельную грузоподъемность и срок последующего освидетельствования.
К управлению кранами допускаются рабочие, имеющие специальные удостоверения на право работы на грузоподъемных средствах.