ремонт автомобилей. remont auto КАРАГОДИН. В процессе эксплуатации автомобиля его рабочие свойства постепенно ухудшаются изза изнашивания деталей, а также коррозии и усталости материала, из которого они изготовлены
![]()
|
ГЛАВА 10. КЛАССИФИКАЦИЯ СПОСОБОВ ВОССТАНОВЛЕНИЯ ДЕТАЛЕЙ Основная задача, которую преследуют ремонтные предприятия, это снижение себестоимости ремонта автомобилей и агрегатов при обеспечении гарантий потребителей, т. е. гарантии послеремонтного ресурса. Исследования ремонтного фонда (автомобилей и агрегатов, поступающих в ремонт) показали, что в среднем около 20 % деталей — утильных, 25...40% — годных, а остальные 40...55% — можно восстановить. Даже процент утильных деталей можно значительно снизить на АРП, если оно будет располагать эффективными способами дефектации и восстановления. Технологии восстановления деталей относятся к разряду наиболее ресурсосберегающих, так как по сравнению с изготовлением новых деталей сокращаются затраты (на 70 %). Основным источником экономии ресурсов являются затраты на материалы. Средние затраты на материалы при изготовлении деталей составляют 38%, а при восстановлении — 6,6 % от общей себестоимости. Для восстановления работоспособности изношенных деталей требуется в 5...8 раз меньше технологических операций по сравнению с изготовлением новых деталей. Несмотря на рентабельность, трудоемкость восстановления деталей еще неоправданно высока и даже на крупных ремонтных предприятиях в среднем до 1,7 раз больше трудоемкости изготовления одноименных деталей на автомобильных заводах. Мелкосерийный характер производства, использование универсального оборудования, частые его переналадки, малые партии восстанавливаемых деталей затрудняют возможность значительного снижения трудоемкости отдельных операций. Основное количество отказов деталей автомобилей вызвано износом рабочих поверхностей — до 50%, 17,1% связано с повреждениями и 7,8% вызвано трещинами. Основное место среди всех отказов автомобилей занимает двигатель — это до 43 % отказов. Примерно 85 % деталей восстанавливают при износе не более 0,3 мм, т.е. их работоспособность восстанавливается при нанесении покрытия незначительной толщины. Нанесение металла на несущие поверхности с последующей механической обработкой позволит многократно использовать деталь. Доля восстанавливаемых наружных и внутренних цилиндрических поверхностей составляет 53,3 %, резьбовых — 12,7%, шлицевых — 10,4%, зубчатых — 10,2%, плоских — 6,5%, все остальные — 6,9%. На рис. 10.1 приведена классификация способов восстановления деталей, которые нашли применение в ремонтном производстве и обеспечивают необходимые эксплуатационные характеристики деталей, а в табл. 10.1 приведены их оценочные показатели. Объемы восстановления деталей на АРП определяются наличием соответствующих по наименованию и цене запасных частей. ![]() Характеристики способов восстановления деталей Таблица 10.1 ![]() ГЛАВА 11. ВОССТАНОВЛЕНИЕ ДЕТАЛЕЙ СЛЕСАРНО-МЕХАНИЧЕСКОЙ ОБРАБОТКОЙ 11.1. Обработка деталей под ремонтный размер Обработка поверхностей детали под ремонтный размер эффективна в случае, если механическая обработка при изменении размера не приведет к ликвидации термически обработанного поверхностного слоя детали. Тогда у дорогостоящей детали соединения дефекты поверхности устраняются механической обработкой до заранее заданного ремонтного размера (например, шейки коленчатого вала), а другую (более простую и менее дорогостоящую деталь) заменяют новой соответствующего размера (вкладыши). В этом случае соединению будет возвращена первоначальная посадка (зазор или натяг), но поверхности детали, образующие посадку, будут иметь размеры, отличные от первоначальных. Применение вкладышей ремонтного размера (увеличенных на 0,5 мм) позволит снизить трудоемкость и стоимость ремонта при одновременном сохранении качества отремонтированных блоков цилиндров и шатунов. Ремонтные размеры и допуски на них устанавливает завод-изготовитель. Восстановление деталей под ремонтные размеры характеризуется простотой и доступностью, низкой трудоемкостью (в 1,5...2,0 раза меньше, чем при сварке и наплавке) и высокой экономической эффективностью, сохранением взаимозаменяемости деталей в пределах ремонтного размера. Недостатки способа — увеличение номенклатуры запасных частей и усложнение организации процессов хранения деталей на складе, комплектования и сборки. Очередной ремонтный размер (рис. 11.1) для вала (знак «—») и отверстия (знак «+») определяют по формуле ![]() где Di — i-й ремонтный размер, мм; Dн — номинальный размер, мм; i — номер ремонтного размера (/ = 1 ...п); β— коэффициент неравномерности износа; Имах — максимальный односторонний износ, мм; z — припуск на механическую обработку на сторону, мм. ![]() где Иmin — минимальный односторонний износ, мм. Число ремонтных размеров: для вала ![]() для отверстия ![]() где γ = 2(βИmax + z) — ремонтный интервал; Dmin, Dmax — соответственно минимально допустимый диаметр для вала и максимально допустимый диаметр для отверстия, определяемые из условия прочности или нарушения толщины термообработанного слоя. Ремонтный интервал зависит от величины износа поверхности детали за межремонтный пробег автомобиля, припуска на механическую обработку. Значения ремонтных интервалов должны быть регламентированы соответствующими техническими условиями или руководствами по ремонту. ![]() 11.2. Постановка дополнительной ремонтной детали Способ дополнительных ремонтных деталей (ДРД) применяют Для восстановления резьбовых и гладких отверстий в корпусных Деталях, шеек валов и осей, зубчатых зацеплений, изношенных плоскостей. При восстановлении детали изношенная поверхность обрабатывается под больший (отверстие) или меньший (вал) размер ц на нее устанавливается специально изготовленная ДРД: ввертыш, втулка, насадка, компенсирующая шайба или планка (рис. 11.2) Крепление ДРД на основной детали производится напрессовкой с гарантированным натягом, приваркой, стопорными винтами, клеевыми композициями, на резьбе. При выборе материала для дополнительных деталей следует учитывать условия их работы и обеспечивать срок службы до очередного ремонта. После установки рабочие поверхности дополнительных деталей обрабатываются под номинальный размер с соблюдением требуемой точности и шероховатости. Усилие запрессовки F подсчитывают по формуле ![]() где f = 0,08...0,10 — коэффициент трения; d — диаметр контактирующих поверхностей, мм; L — длина запрессовки, мм; р — удельное контактное давление сжатия, кгс/мм2. Диаметр контактирующей поверхности: для вала d = dно-2δ, (11.6) для втулки d = dво+2δ, (11.7) где dно, dво — соответственно нижнее и верхнее предельные отклонения вала и втулки, мм; δ — толщина втулки, мм. Значение минимально допустимой толщины втулки определяют из условия прочности δ = pnd/(2[σ]), (11.8) где n = σт/[σ] — запас прочности; [σ] — допускаемое напряжение, 50-с/см2; σт — предел текучести для материала втулки, кгс/см2. ![]() К расчетной толщине втулки 8 необходимо прибавить припуск на ее механическую обработку после запрессовки. Удельное контактное давление сжатия между деталями ![]() ![]() где Δ — максимальный расчетный натяг, мкм; С1 и С2 — коэффициенты охватываемой и охватывающей детали; Е1 и Е2 — модули упругости материала охватываемой и охватывающей детали, кгс/мм2. ![]() где d0 — диаметр отверстия охватываемой детали (для вала d0 = 0), мм; D — наружный диаметр охватывающей детали, мм; μ1 и μ2 — коэффициенты Пуассона для охватываемой и охватывающей детали (для стали — 0,3; для чугуна — 0,25). Если для постановки ДРД используются тепловые методы сборки, то температуру нагрева охватывающей детали или охлаждения охватываемой детали определяют по формуле Т= 10-3К(Δ + S)/(ad), (11.11) где К= 1,15...1,30 — коэффициент, учитывающий частичное охлаждение или нагрев при сборке; S — гарантированный зазор, мкм; а — коэффициент линейного расширения охватывающей детали при нагреве или охватываемой при охлаждении. 11.3. Заделка трещин в корпусных деталях фигурными вставками Трещины в корпусных деталях (головках и блоках цилиндров двигателей, картерах коробок передач, задних мостах и других деталях) можно устранить следующими двумя видами фигурных вставок (рис. 11.3). Уплотняющие вставки (рис. 11.3, а) применяют для заделки трещин длиной более 50 мм с обеспечением герметичности как толстостенных, так и тонкостенных деталей. Для тонкостенных деталей используют вставки диаметром 4,8 мм, а для деталей с толщиной стенок 12... 18 мм — 6,8 мм. Для установки уплотняющей фигурной вставки сверлят отверстия диаметром 4,8 или 6,8 мм на глубину 3,5 или 6,5 мм за пределами конца трещины на расстояние 4...5 или 5...6 мм соответственно. Затем, используя специальный кондуктор (рис. 11.4), последовательно вдоль трещины сверлят такие же отверстия. Через каждые пять отверстий (рис. 11.5) сверлят отверстия поперек трещины — по два с каждой стороны. Отверстия продувают сжатым воздухом, обезжиривают ацетоном, смазывают эпоксидным составом, устанавливают и расклепывают фигурные вставки. Вставки диаметром 6,8 мм помещают в отверстие в два ряда. ![]() Стягивающие вставки (рис. 11.3, б) используют для стягивания боковых кромок трещины на толстостенных деталях. В деталях сверлят по кондуктору перпендикулярно трещине четыре или шесть отверстий (по два или три отверстия с каждой стороны) диаметром, соответствующим диаметру вставки, с шагом, большим на 0,1 ...0,3, и глубиной 15 мм. Перемычку между отверстиями удаляют специальным пробойником в виде пластины шириной 1,8 или 3,0 мм в зависимости от размеров вставки. В паз запрессовывают фигурную вставку, ее расклепывают и зачищают (опиливанием или переносным вращающимся абразивным кругом) этот участок заподлицо. ![]() Фигурные вставки устанавливаются в несколько слоев до полного закрытия паза с последующим расклепыванием каждого слоя. Фигурные вставки изготавливают способом волочения в виде фасонной ленты из ст. 20, ст. 3. ![]() Качество заделки трещины проверяют на герметичность на стенде в течение 3 мин при давлении 0,4 МПа. Для выполнения работ по заделки трещин с использованием фигурных вставок используют следующее оборудование: сверлильную машину или электрическую дрель; шлифовальную машину или станок обдирочно-шлифовальный; клепальный молоток; пистолет для обдува детали сжатым воздухом; емкости с ацетоном и с составом на основе эпоксидной смолы. 11.4. Восстановление резьбовых поверхностей спиральными вставками Один из способов восстановления изношенной или поврежденной резьбы — это установка резьбовой спиральной вставки. Эти вставки увеличивают надежность резьбовых соединений деталей, особенно изготовленных из алюминия и чугуна. Спиральные вставки изготавливают из коррозионно-стойкой проволоки ромбического сечения в виде пружинящей спирали (рис. 11.6). Технологический процесс восстановление резьбовой поверхности включает: рассверливание отверстия (см. табл. 21.3) с применением накладного кондуктора и снятие фаски (1x45°). Смещение осей отверстий не более 0,15 мм, перекос осей отверстий не более 0,15 мм на длине 100 мм; нарезание резьбы в рассверленном отверстии детали (см. табл. 21.3). Скорость резания 4... 5 м/мин, частота уплотняющей и стягивающей вставок в деталь: установить резьбовую вставку в монтажный инструмент (рис. 11.7, а); ввести стержень инструмента в резьбовую вставку так, чтобы ее технологический поводок вошел в паз нижнего конца стержня; завернуть вставку в отверстие наконечника инструмента, а затем с помощью инструмента в резьбовое отверстие детали (рис. 11.7, б); вынуть инструмент и удалить (посредством удара бородка) технологический поводок резьбовой вставки; контроль качества восстановления резьбы с помощью «проходного» и «непроходного» калибра или контрольного болта. При контроле резьбовая вставка не должна вывертываться вместе с калибром (контрольным болтом). ![]() Проходной калибр, завернутый на всю длину вставки, не должен отклоняться более чем на 0,5 мм в любую сторону. Непроходной резьбовой калибр соответствующего размера не должен ввертываться в установленную в деталь вставку. Резьбовая вставка должна утопать в резьбовом отверстии не менее чем на один виток резьбы. Выступание ее не допускается. ![]() 11.5. Восстановление посадочных отверстий свертными втулками Восстанавливают свертными втулками посадочные отверстия под подшипники качения. Технологический процесс включает в себя следующие операции: изготовление заготовки свертной втулки. Заготовки свертных втулок получают резкой стальной ленты на полосы шириной Н и длиной L = I + 3... 5 мм. Толщина ленты зависит от износа детали (табл. 11.1). Длина и ширина заготовки свертной втулки равны l = π(dmax-λ+δ) (11.12) Н= В(l + ψ/100), (11.13) где l — длина заготовки свертной втулки, мм; dmax — максимальный диаметр расточенного отверстия, мм; λ — номинальная толщина ленты (табл. 11.1), мм; δ — допуск на толщину ленты, мм; Н — ширина заготовки свертной втулки, мм; В — ширина восстанавливаемой поверхности, мм; ψ — величина относительной осевой деформации (числовые значения приведены в табл. 11.1); свертывание втулки из заготовки путем ее сгиба на специальных приспособлениях. После свертывания втулки с одного из ее торцов снимают фаску; подготовка ремонтируемого отверстия под свертную втулку: растачивание отверстия; нарезка на обработанной поверхности винтообразной канавки треугольного профиля; установка втулки в ремонтируемое отверстие с помощью специальной оправки, которая крепится в пиноли задней бабки токарного станка (рис. 11.8); раскатка втулки специальным раскатником (рис. 11.9) на режимах: окружная скорость 50...70 м/мин, подача 0,3...0,4 мм/об; обработка фаски в соответствии с чертежом на новую деталь. Таблица 11.1 Параметры стальной ленты в зависимости от износа восстанавливаемого отверстия |
Увеличение диаметра ремонтируемого отверстия, мм | Номинальная толщина ленты, мм | Относительная осевая деформация ленты при свертывании, % |
До 0,5 | 0,8 | 15,2 |
0,5. ..0,7 | 1,0 | 13,2 |
0,7. ..1,0 | 1,2 | 12,5 |
1,0 ...1,2 | 1,4 | 11,5 |
__ 1,2. ..1,4 | ' 1,6 | 10,2 |
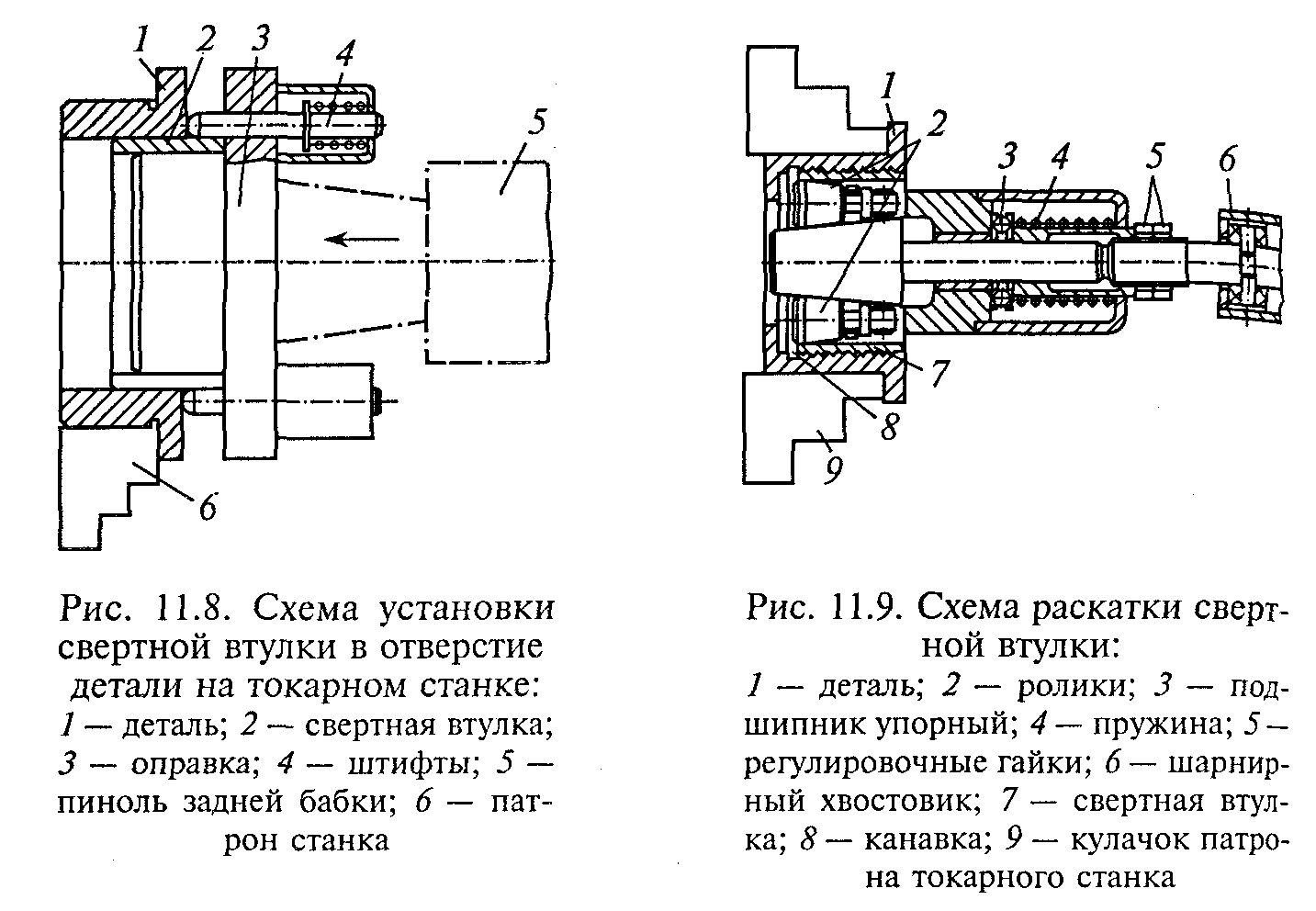
ГЛАВА 12. ВОССТАНОВЛЕНИЕ ДЕТАЛЕЙ СПОСОБОМ ПЛАСТИЧЕСКОГО ДЕФОРМИРОВАНИЯ
12.1. Сущность процесса
Способ пластического деформирования основан на способности деталей изменять форму и размеры без разрушения путем перераспределения металла под давлением, т. е. основан на использовании пластических свойств металла деталей. Особенность способа — это перемещение металла с нерабочих поверхностей детали на изношенные рабочие поверхности при постоянстве ее объема. Пластическому деформированию могут подвергаться детали в холодном или в нагретом состоянии в специальных приспособлениях на прессах.
Стальные детали твердостью до HRC 30 (низкоуглеродистые стали), а также детали из цветных металлов и сплавов обычно деформируют в холодном состоянии без предварительной термообработки. При холодном деформировании наблюдается упрочнение металла детали, т. е. происходит наклеп, который повышает предел прочности и твердости металла при одновременном понижении ее пластических свойств. Этот процесс требует приложения больших усилий. Поэтому при восстановлении деталей очень часто их нагревают.
В нагретом состоянии восстанавливают детали из средне- и высокоуглеродистых сталей. При восстановлении деталей необходимо учитывать верхний предел нагрева и температуру конца пластического деформирования металла. Относительно низкая температура конца деформирования металла может привести к наклепу и появлению трещин в металле. В табл. 12.1 приведены интервалы горячей обработки металлов давлением. В зависимости от конструкции детали, характера и места износа нагрев может быть общим или местным.
Таблица 12.1
Интервалы температур горячей обработки металлов давлением, °С
Материал детали | Обработка | |
Начало | Окончание | |
Сталь с содержанием углерода, %: < 0,3 0,3. ..0,5 0,5. ..0,9 | 1200. ..1150 1150. ..1100 1100.. .1050 | 800... 850 800... 850 800... 850 |
Сталь: низколегированная среднелегированная высоколегированная | 1100 1100. ..1150 1150 | 825. ..850 850. ..875 875... 900 |
Медные сплавы: бронза латуньЛС59 | 850 750 | 700 600 |
Процесс восстановления размеров деталей состоит из операций: подготовка — отжиг или отпуск обрабатываемой поверхности перед холодным или нагрев их перед горячим деформированием; деформирование — осадка, раздача, обжатие, вытяжка, правка, электромеханическая обработка и др.; обработка после Деформирования — механическая обработка восстановленных поверхностей до требуемых размеров и при необходимости термическая обработка; контроль качества.
12.2. Восстановление размеров изношенных поверхностей деталей методами пластического деформирования
Осадку (рис. 12.1, а) используют для увеличения наружного диаметра сплошных и полых деталей, а также для уменьшения внутреннего диаметра полых деталей за счет сокращения их высоты (бронзовые втулки и др.). Допускается уменьшение высоты втулок на 8...10%.
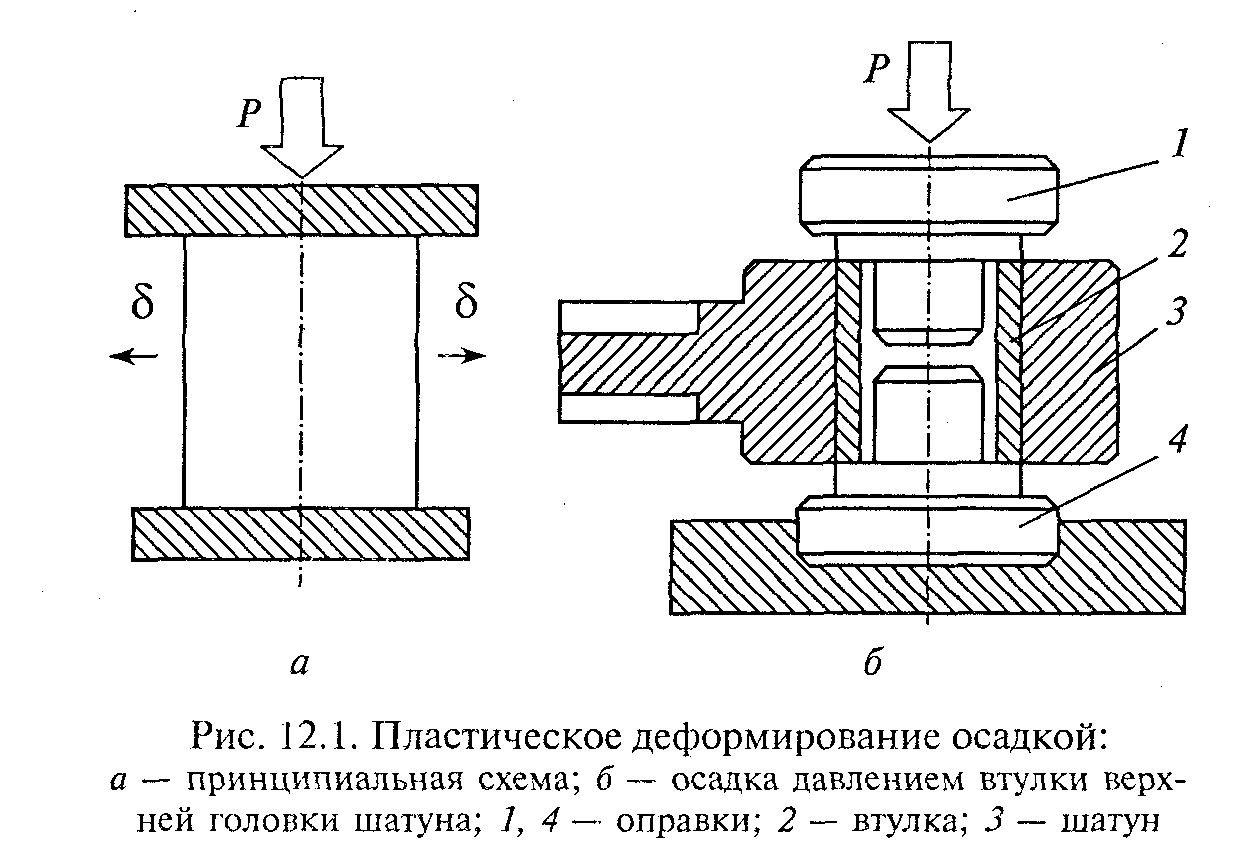
При осадке направление действия внешней силы Р перпендикулярно к направлению деформации 8. Для сохранения формы отверстий, канавок и прорезей пред осадкой в них вставляют стальные вставки. Осадку втулок из цветных металлов производят в специальных приспособлениях гидравлическими прессами (рис. 12.1, б). В специальных штампах при нагреве до температуры ковки осадкой восстанавливают шейки, расположенные на концах стальных валов.
Вдавливание (рис. 12.2, а) отличается от осадки тем, что высота детали не изменяется, а увеличение ее диаметра происходит за счет выдавливания металла из нерабочей части. Вдавливанием восстанавливают тарелки клапанов двигателей, зубчатые колеса (рис. 12.2, б), боковые поверхности шлицев на валах (рис. 12.2, в) и т.д. Шлицы прокатывают по направлению их продольной оси заостренным роликом, который внедряется в металл и разводит шлиц на 1,5...2,0 мм в сторону. Инструментом служат ролики диаметром 60 мм с радиусом заострения около 0,4 мм. Нагрузка на ролик составляет 2,0...2,5 кН.
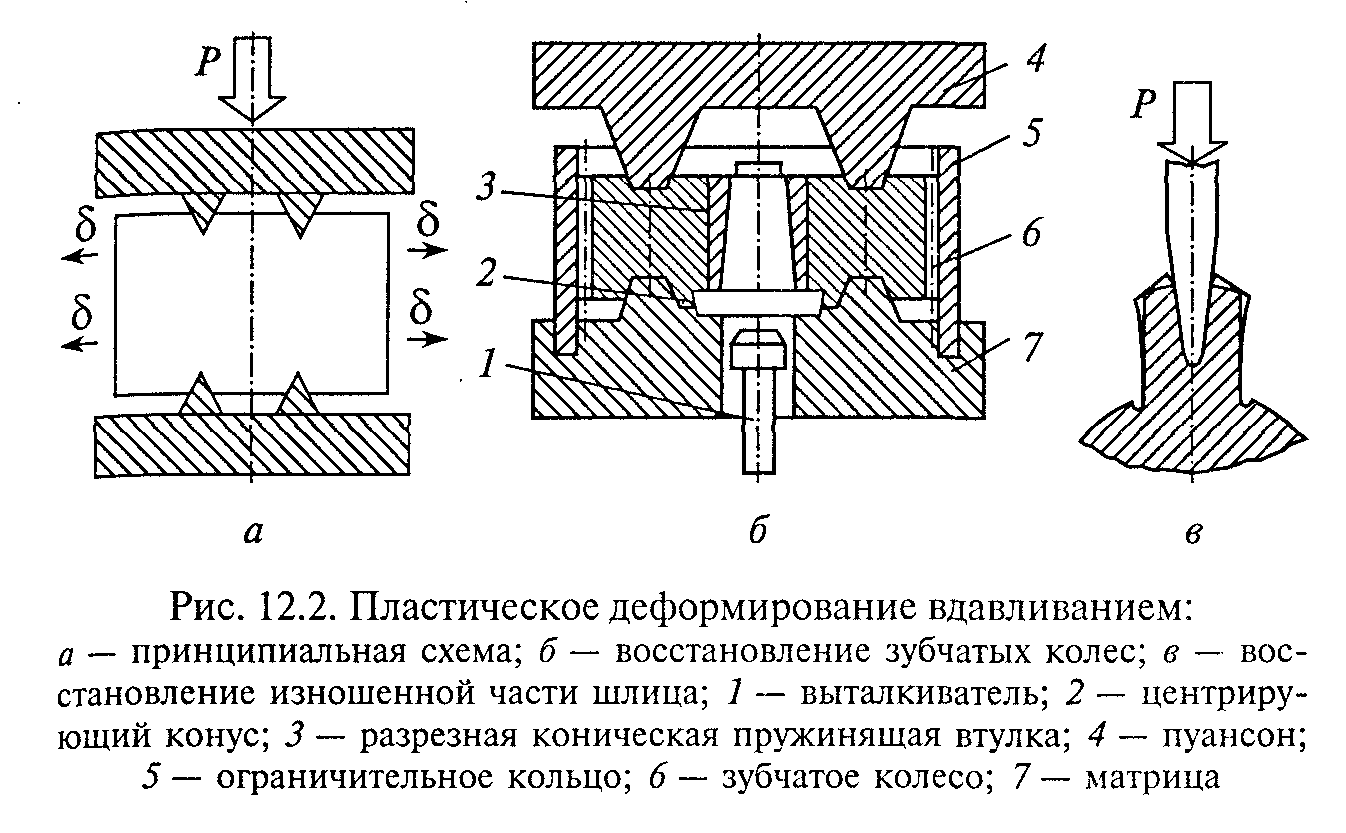
Раздачу (рис. 12.3, а) применяют для увеличения наружного диаметра пустотелых деталей (втулки, поршневые пальцы и др.) при практически неизменяемой ее высоте. Изменение наружного диаметра детали происходит за счет увеличения ее внутреннего диаметра. При раздаче через отверстие детали продавливают шарик (рис. 12.3, б) или специальную оправку (рис. 12.3, в). На увеличение диаметра влияет материал детали, температура раздачи, величина износа и размеры. При этом возможны укорочение детали и появление в ней трещин.
Обжатием (рис. 12.4, а) восстанавливают детали с изношенными внутренними поверхностями за счет уменьшения наружных размеров, которые не имеют для них значения (корпуса насосов гидросистем, проушины рычагов, вилок и др.). Обжатие осуществляют в холодном состоянии под прессом в специальном приспособлении (рис. 12.4, б). Втулку проталкивают через матрицу, которая имеет сужающее входное отверстие под углом 7...8°, калибрующую часть и выходное отверстие, расширяющееся под углом 18...20°. Калибрующая часть матрицы позволяет уменьшить внутренний диаметр детали на величину износа с учетом припуска на развертывание до требуемого размера. Наружный размер восстанавливают одним из способов наращивания. После восстановления детали должны быть проверены на отсутствие трещин.
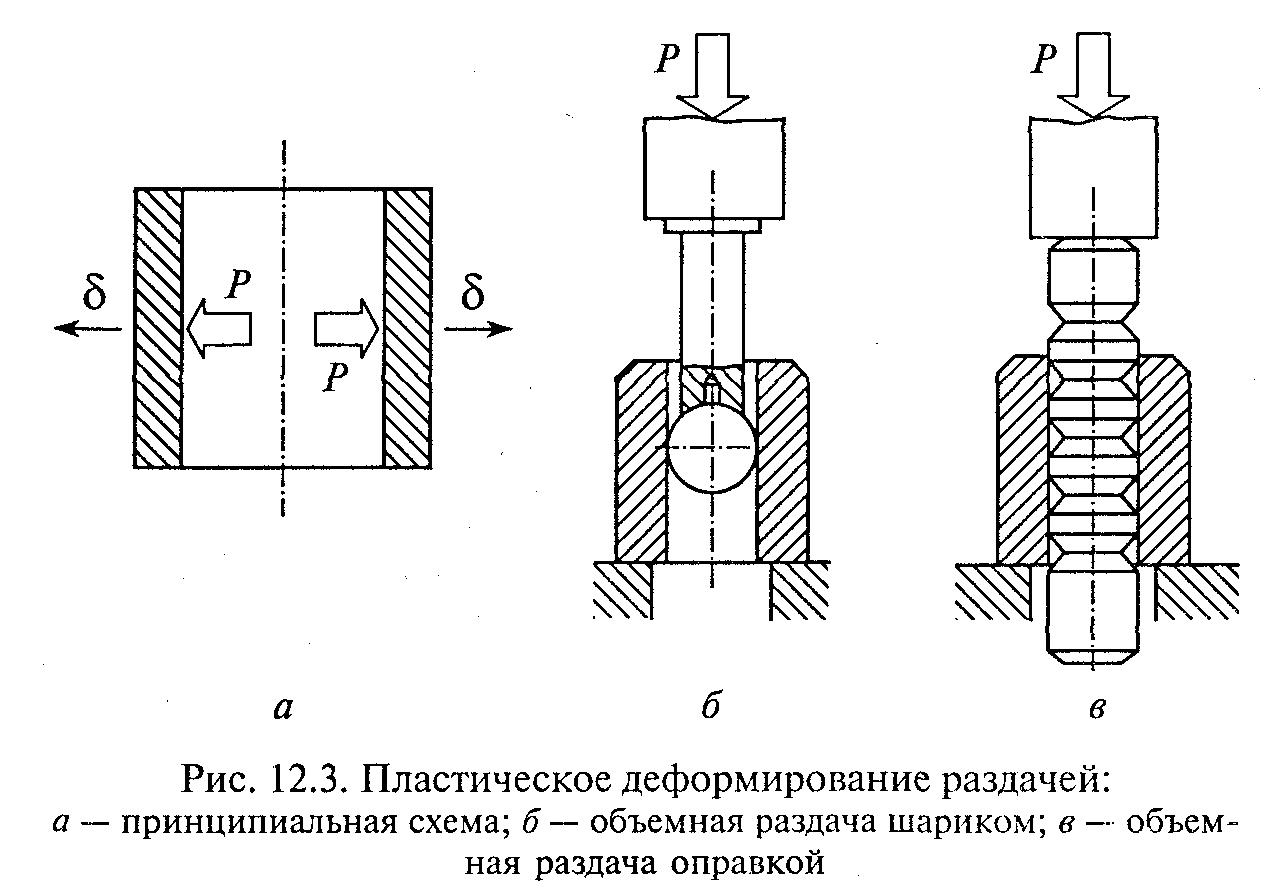
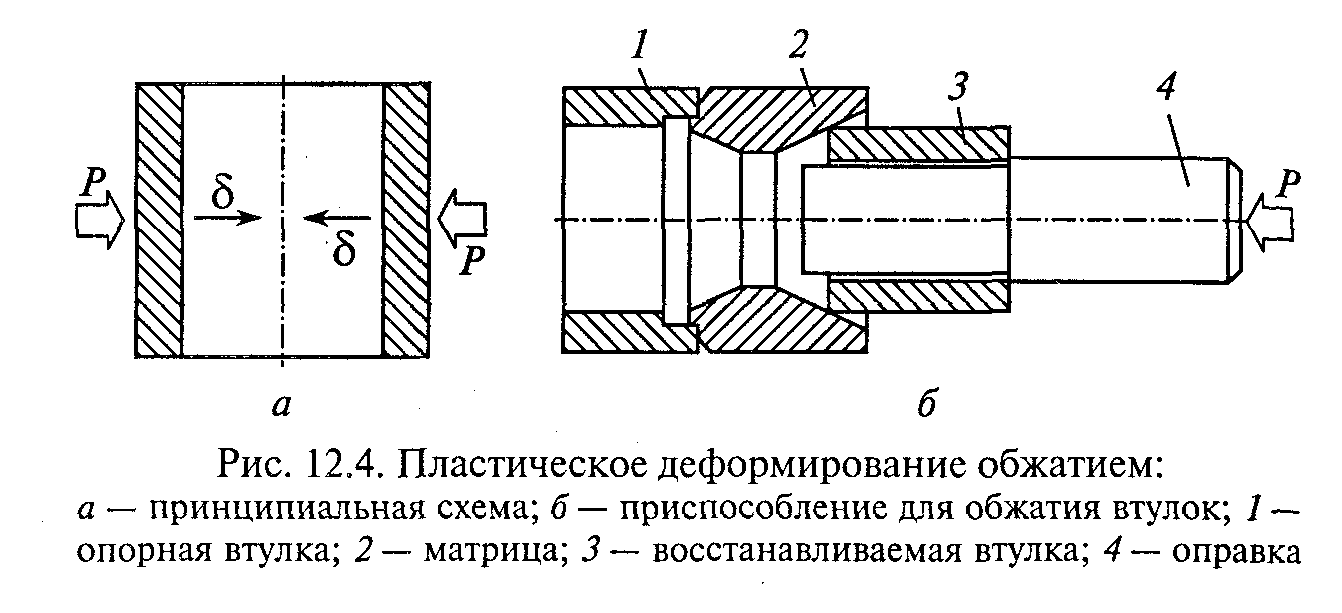
Накатка основана на вытеснении рабочим инструментом материала с отдельных участков изношенной поверхности детали (рис. 12.5). Способ позволяет увеличивать диаметр накатываемой поверхности детали на 0,3... 0,4 мм и применяется для восстановления изношенных посадочных мест под подшипники качения. К типовым деталям, подлежащим ремонту объемной накаткой, относятся чашка коробки дифференциала, валы коробки передач, поворотные цапфы и т. п. Накатке подвергаются детали без термической обработки, с обильной подачей индустриального масла. Рекомендуется применять для деталей, которые воспринимают контактную нагрузку не более 70 кгс/см2. Детали, имеющие твердость HRC < 32, можно восстанавливать в холодном состоянии. При накатке детали необходимо соблюдать условие
nt=πd, (12.1)
где n — число зубьев инструмента;
t — шаг накатки, мм;
d — диаметр восстанавливаемой поверхности, мм.

В качестве инструмента для накатки используют рифленый цилиндрический ролик или обойму с шариками, устанавливаемые на суппорте токарного станка. Режимы накатки (м/мин): скорость для роликов из стали — 8...20, чугуна - 10... 15, латуни и бронзы 30...50, алюминия — до 90; подача для стали твердостью НВ 270... 300: продольная — 0,6, поперечная — 0,15 мм'. Число проходов зависит от материала детали, шага и толщины выдавливаемого слоя металла.
Электромеханическая обработка предназначена для восстановления поверхностей деталей неподвижных сопряжений и состоит в искусственном нагреве металла электрическим током в зоне деформации, что способствует повышению пластических свойств металла. Схема обработки приведена на рис. 12.6, а. Процесс состоит из двух операций (рис. 12.6, б): высадки металла и сглаживания выступов до необходимого размера.
Обработку ведут на токарном станке. В резцедержатель суппорта закрепляют специальную оправку с рабочим инструментом. Деталь и инструмент подключают к вторичной обмотке понижающего трансформатора. При вращении детали к ней прижимают инструмент, который имеет продольную подачу S, которая должна быть в 3 раза больше контактной поверхности/пластины. Через зону контакта детали и инструмента (площадь контакта мала) пропускаю ток 350... 700 А напряжением 1... 6 В. Деталь мгновенно нагревается до 800...900 °С и легко деформируется инструментом. Обработка осуществляется с охлаждением, что способствует закалке поверхностного слоя.
В качестве высаживающего и сглаживающего инструмента используют пластину или ролик из твердого сплава (для высаживания заостренная, а для сглаживания закругленная). При выдавливании образуются выступы, аналогичные резьбе. Диаметр детали увеличивается от da до du. Сглаживание поверхности осуществляют до dH. Ширина сглаживающей пластинки в 3... 5 раз больше подачи.
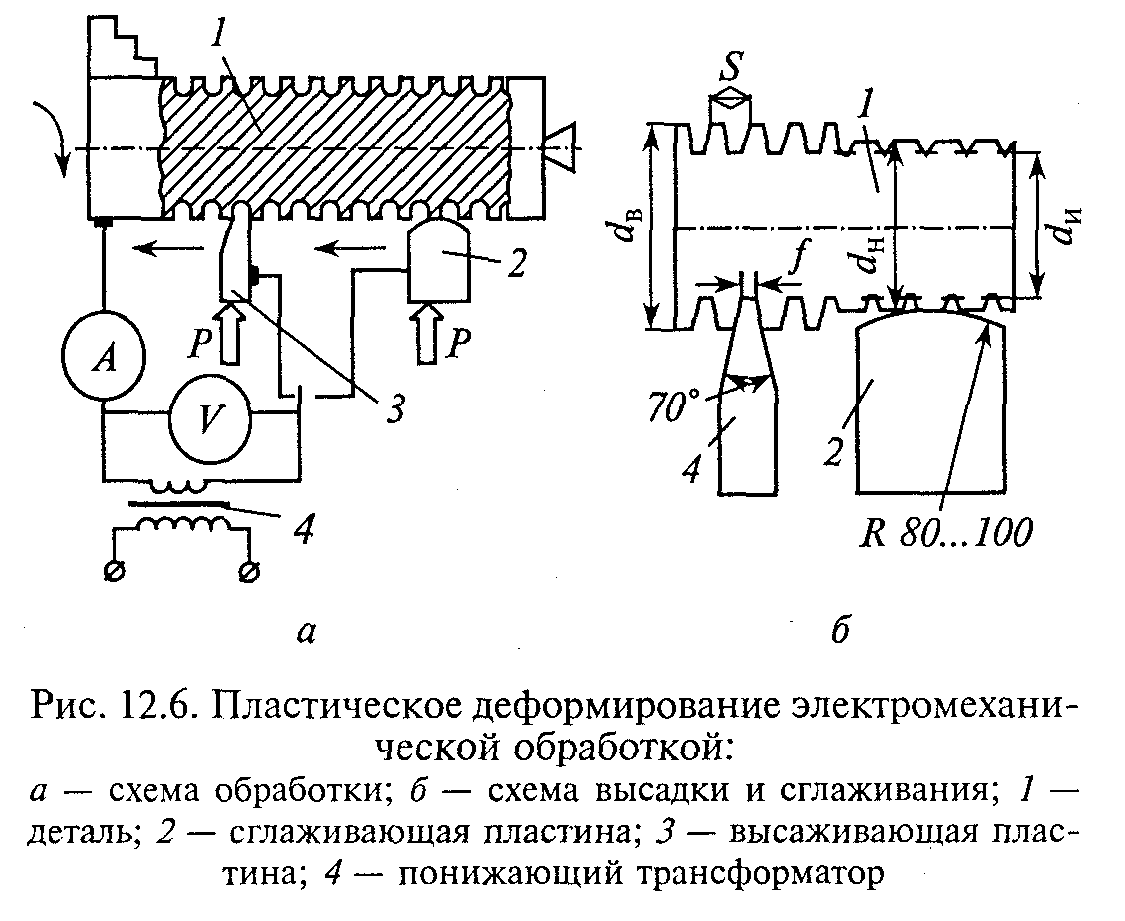
После обработки детали поверхность прерывистая, а гогощадь контакта с сопрягаемой деталью уменьшается. Предельное уменьшение площади контакта допускается 20%. Увеличение диаметра незакаленных деталей возможно на 0,4 мм, а закаленных — на 0,2 мм
12.3. Восстановление формы деталей
Во время эксплуатации у многих деталей появляются остаточные деформации: изгиб, скручивание, коробление и вмятины (валы, оси, рычаги, рамы, балки, и др.). Для устранения этих дефектов используют правку. В зависимости от степени деформации и размеров детали применяют механический, термомеханический и термический способы правки.
При механической правке используют два способа: давлением и наклепом.
Механическая правка давлением может производиться в холодном состоянии или с нагревом. Правку в холодном состоянии осуществляют у валов диаметром до 200 мм в том случае, если величина (стрела) прогиба/не превышает 1 мм на 1 м длины вала (рис. 12.7). За размер стрелы прогиба принимают половину числового значения биения вала, показываемого индикатором. Для правки вал 4 ставят на призмы или опоры 5 винтового или гидравлического пресса выпуклой стороной вверх и перегибают нажимом штока 3 пресса через прокладку 2 из цветного сплава так, чтобы обратная величина прогиба/ была в 10... 15 раз больше того прогиба/ который имел вал до правки. Точность правки контролируют индикатором 1.
Пресс выбирают по усилию правки, которое рассчитывают по формуле
P=6,8σтd3/(103l), (11.2)
где Р — усилие правки, кН;
σт — предел текучести материала вала, МПа;
d — диаметр сечения вала, м;
l — расстояние между опорами, м.
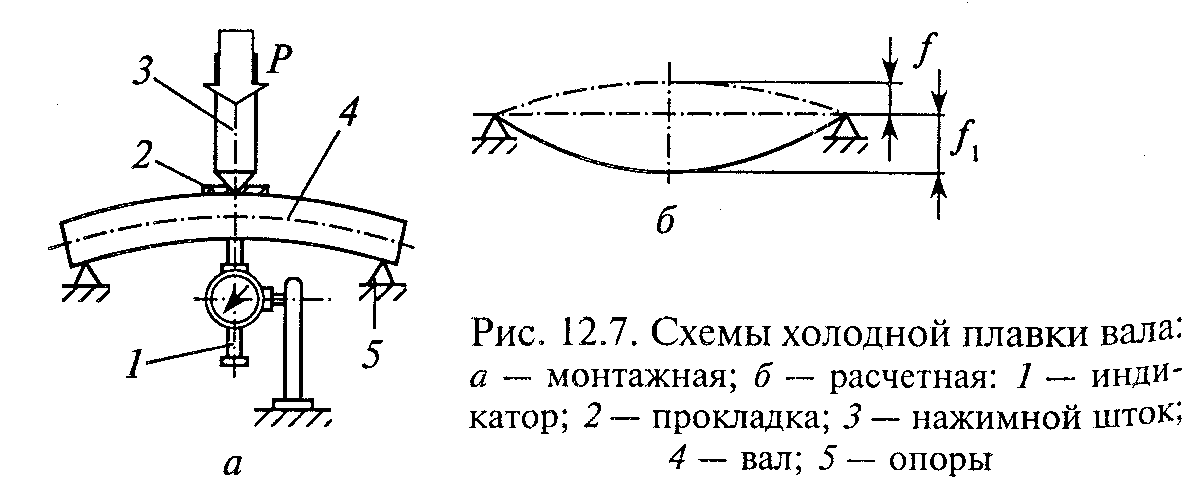
Недостатки механической холодной правки — это опасность обратного действия, снижения усталостной прочности и несущей способности детали. Опасность обратного действия вызвана возникновением неуравновешенных внутренних напряжения, которые с течением времени, уравновешиваясь, приводят к объемной деформации детали. Ухудшение усталостной прочности деталей Происходит за счет образования в ее поверхностных слоях мест с растягивающими напряжениями, причем снижение усталостной прочности достигает 15...40%.
Для повышения качества холодной правки применяют следующие способы: выдерживание детали под прессом в течение длительного времени; двойная правка детали, заключающаяся в первоначальном перегибе детали с последующей правкой в обратную сторону; стабилизация правки детали последующей термообработкой. Последний способ дает лучшие результаты, но при нагреве может возникнуть опасность нарушения термической обработки детали, кроме того, он дороже первых двух.
Механическая горячая правка производится при необходимости устранения больших деформаций детали и осуществляется при температуре 600...800°С. Нагревать можно как часть детали, так и всю деталь. Правка завершается термической обработкой детали.
Правка наклепом (чеканкой) не имеет недостатков, присущих правке давлением. Она обладает простотой и небольшой трудоемкостью. При правильной чеканке достигаются: высокое качество правки детали, которое определяется стабильностью ее во времени; высокая точность правки (до 0,02 мм); отсутствие снижения усталостной прочности детали; возможность правки за счет ненагруженных участков детали (рис. 12.8).
В качестве инструмента для чеканки применяются пневматические или ручные молотки. От наносимых ударов в поверхностном слое детали возникают местные напряжения сжатия, которые вызывают устойчивую деформацию детали.
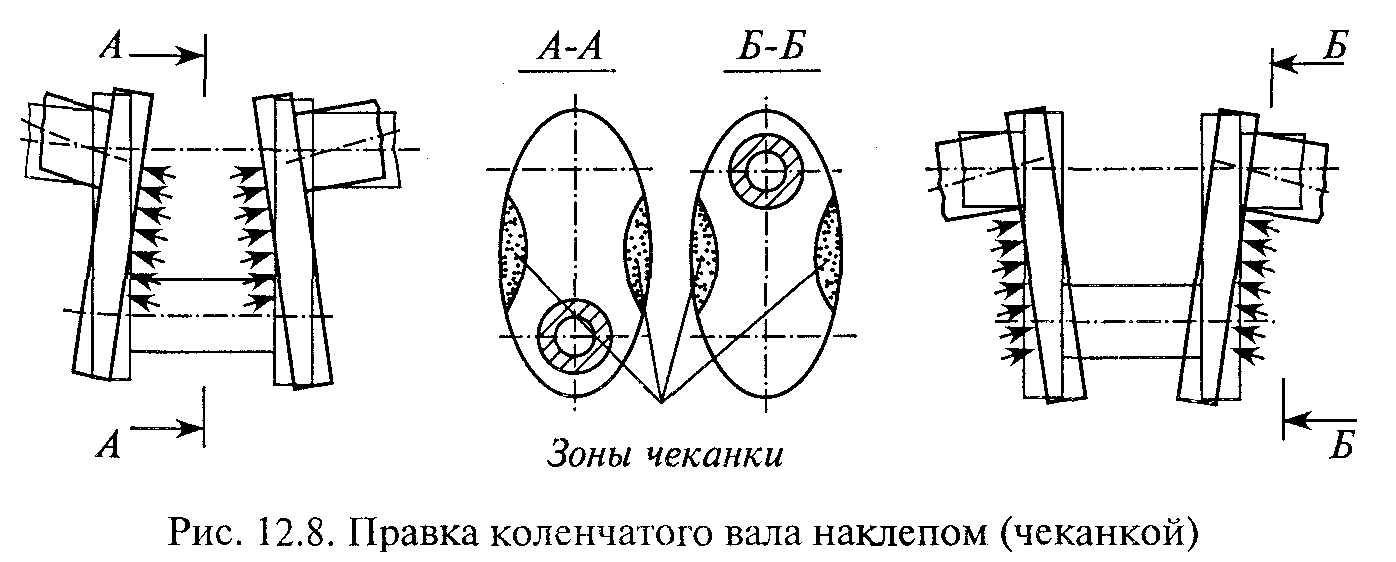
Продолжительность правки зависит от материала детали, энергии удара и конструкции ударного бойка.
Термический способ правки заключается в нагревании ограниченных участков детали (вала) с выпуклой стороны. В результате нагревания металл стремится расшириться. Противодействие соседних холодных участков приводит к появлению сжимающих усилий. Выправление вала происходит под действием стягивают усилий, которые являются результатом пластического упрочнения волокон. Эффективность правки зависит от степени закрепления концов детали — при жестком закреплении прогиб устраняется в 5... 10 раз быстрее, чем при незакрепленных концах балки. Оптимальная температура нагрева стальных деталей составляет 750... 850 °С.
При термомеханическом способе правки осуществляют равномерный прогрев детали по всему деформированному сечению с последующей правкой внешним усилием. Нагрев осуществляется газовыми горелками до температуры отжига (750...800°С).
Правка и рихтовка без нагрева вмятин капотов, крыльев применяется, если толщина их стенок не превышает 1 мм.
Процесс предварительного выравнивания вмятин происходит выбиванием вогнутой части детали до получения у нее правильной формы и его называют выколоткой. Процесс окончательного выглаживания поверхности после выколотки называют рихтовкой. При правке вмятины под нее устанавливают поддержку 3 (рис. 12.9, а); ударами выколоточного молотка по вмятине выбивают ее до уровня неповрежденной части поверхности. Подравнивают деревянной или резиновой киянкой оставшиеся после выколотки бугорки. При правке вмятин соблюдают следующие требования: глубокие вмятины без острых загибов и складок выравнивают, начиная с середины и постепенно перенося удары к краю; вмятины с острыми углами выбивают, начиная с острого угла или с выправки складки; пологие вмятины выправляют с краев, постепенно перенося удар к середине.
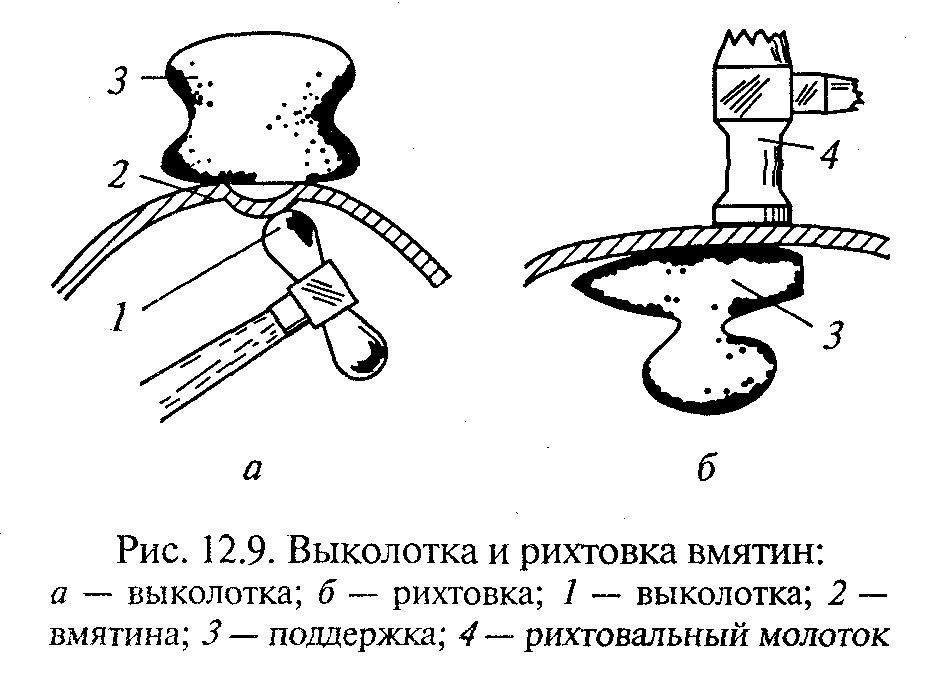
Рихтовка может быть ручная и механизированная. Ручную рихтовку выполняют рихтовальными молотками и поддержками, которые подбирают по профилю восстанавливаемых панелей. Под растянутую поверхность подставляют поддержку 3 (рис. 12.9, б), которую иной рукой прижимают к панели. По лицевой стороне восстанавливаемой поверхности наносят частые удары рихтовальным молотком 4 так, чтобы они попадали на поддержку. При этом удары постепенно переносят с одной точки на другую, осаживая бугорки поднимая вогнутые участки. Рихтовку продолжают до тех пор, пока ладонь руки не перестанет ощущать шероховатость. При работе необходимо ударять всей плоскостью головки молотка. Удары острым краем головки оставляют насечки (рубцы), которые трудно удалить.
12.4. Восстановление механических свойств деталей поверхностным пластическим деформированием
Обработка поверхностным пластическим деформированием (ППД) — это вид обработки давлением, при которой с помощью различных инструментов для рабочих тел пластически деформируется поверхностный слой материала обрабатываемой детали; применяется при восстановлении деталей из стали, чугуна, цветных металлов и сплавов, обладавших достаточной пластичностью.
В результате обработки ППД достигается: сглаживание шероховатости поверхности; упрочнение поверхности; калибрование; образование новой геометрической формы поверхности; стабилизация остаточных напряжений структурного состояния.
При обработке ППД с осевым перемещением деформирующих роликов пластическое деформирование начинается впереди роликов, на некотором расстоянии от поверхности.
В зоне контакта деформирующих роликов с обрабатываемой поверхностью образуется заторможенный (защемленный) клиновидный объем металла, способствующий направленному поверхностному пластическому деформированию. Металл, в основном, перемещается в окружном направлении. Внутри выступов микронеровностей наблюдается осевое течение металла. Вершины неровностей пластически деформируются, и происходит смыкание впадин. Уровень расположения впадин практически сохраняется постоянным.
Роликовые деформирующие инструменты и устройства различаются по виду обрабатываемой поверхности, кинематике процесса, форме, размерам, количеству деформирующих элементов, характеру контакта с обрабатываемой поверхностью, способу создания и стабильности усилий деформирования и др.
По способу создания усилий деформирования роликовые инструменты разделяются на регулируемые (жесткие) и самонастраивающиеся. В регулируемых деформирующих инструментах усилие деформирования создается за счет натяга — разницы между диаметром ^срабатываемой детали и настроечным диаметром инструмента. Обработка регулируемыми инструментами жестких деталей позволяет повысить точность размеров, а также исправить форму поверхности (овальность, конусность).
Самонастраивающиеся деформирующие инструменты рекомендуется применять при обработке маложестких деталей и материа. лов, подверженных перенаклепу. Они снабжены механизмом (пружинным, пневматическим, гидравлическим) для создания необходимого усилия деформирования и поддержания его в процессе обработки на определенном уровне; обеспечивают получение равномерного упрочнения поверхностного слоя и стабильной шероховатости поверхности.
В деформирующих инструментах и устройствах применяются стержневые и кольцевые ролики. Стержневые ролики применяют в многороликовом накатом инструменте сепараторного типа, служащем для накатывания деталей, имеющих форму цилиндра, конуса, а также для накатывания плоских кольцевых поверхностей, акольцевые ролики —в инструментах для упрочняющей и калибрующей обработки деталей, имеющих концентраторы напряжений в виде галтелей, канавок, а также наружных цилиндрических поверхностей.
По кинематике движения деформирующие инструменты и устройства разделяются на простые и дифференциальные. Простые инструменты работают по схеме простого накатывания, деформирующий ролик совершает движение вокруг своей оси (материальной или геометрической). Дифференциальные инструменты характеризуются наличием единой опорной поверхности для всех деформирующих роликов, благодаря чему, кроме вращательного движения, они совершают переносное движение относительно обрабатываемой детали.
По характеру контакта с обрабатываемой поверхностью деформирующие инструменты разделяются на статические — непрерывного действия и ударные — импульсные. При обработке статическим инструментом контакт деформирующего ролика с обрабатываемой поверхностью осуществляется непрерывно под воздействием постоянного усилия деформирования. Инструменты ударного действия снабжены механизмами для прерывания контакта ролика с поверхностью детали.
Поверхностное пластическое деформирование цилиндрических отверстий роликовым инструментом осуществляется раскатками. Многороликовые регулируемые дифференцированные раскатки (рис. 12.10) применяются для обработки диаметров отверстий от 25 до 250 мм деталей, изготовленных из стали, чугуна, цветных металлов и сплавов (с твердостью до 40 HRC). В них деформирующие ролики 1 расположены равномерно по окружности в сепараторе 3. Опорой роликов является конус 2, установленный на оправке 4, Осевое смещение сепаратора ограничено с одной стороны буртиками оправки, с другой — гайкой 5 и контргайкой 6, преД" назначенными для регулирования размеров раскатки. Пружина " служит для автоматического возврата сепаратора с роликами в исходное положение после вывода раскатки из обрабатываемой детали. Для уменьшения трения сепаратора об оправку и исключения возможности задиров в сепараторе установлена втулка 8. Осевые усилия при обработке воспринимаются подшипником 7. От попадания ролики предохраняются крышкой. Смазочно-охлаждающая жидкость подается через отверстия, имеющиеся в оправке и гайке 10, которая предназначена для крепления опорного конуса.
Перед обработкой раскатка регулировочной гайкой настраивается на определенный размер, и сепаратор с роликами и пружиной отводится до упора в крайнее левое положение. Детали или инструменту сообщается вращение, и раскатка вводится в обрабатываемое отверстие. Осевая подача инструмента или детали происходит за счет самоподачи или принудительного перемещения.
После обработки при выводе инструмента или детали ролики, сжимая пружину, смещаются на меньший диаметр опорного конуса, и инструмент свободно выходит из обработанного отверстия.
Минутная подача (Sм) при раскатывании равна
Sm=Sonp, (12.3)
где Sa — подача на один оборот сепаратора с роликами относительно детали, мм;
nр — угловая скорость раскатывания, мин^1.
Подача на один оборот сепаратора с роликами относительно детали определяется по формуле
So=Spz, (12.4)
где Sp — подача на один ролик (расстояние между последовательными положениями двух соседних роликов на образующей детали), мм/рол;
z — число роликов на раскатке, ед.
Угловая скорость раскатывания равна
np=1000Vp/(πd), (12.5)
где Vp — окружная скорость раскатывания, м/мин.
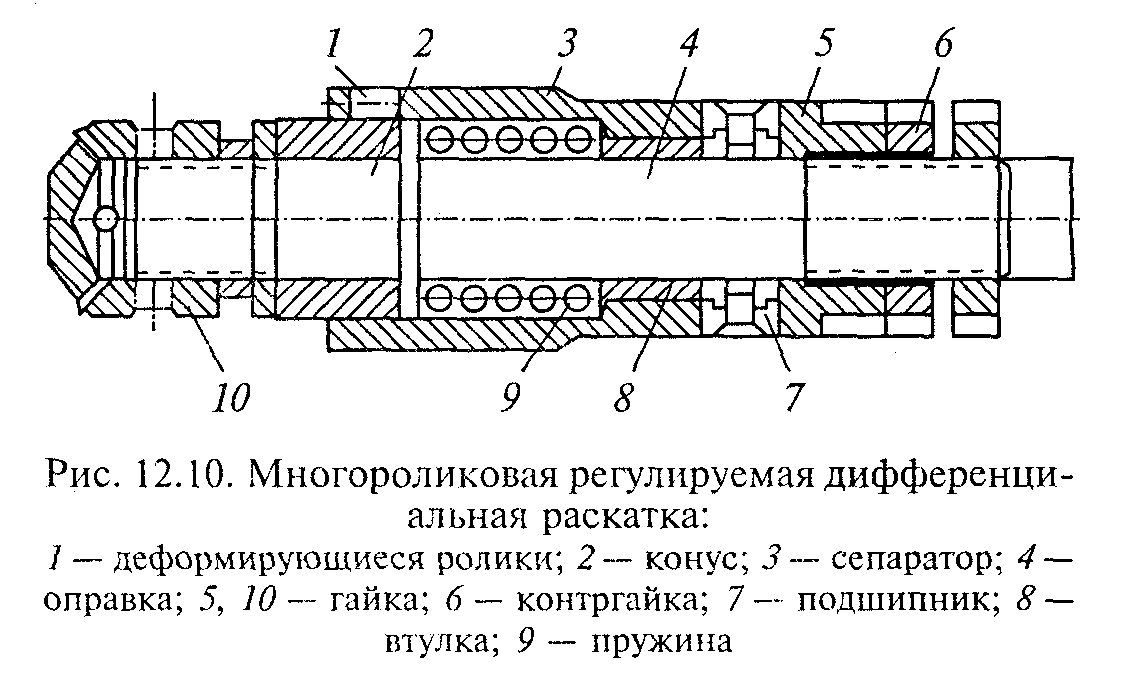
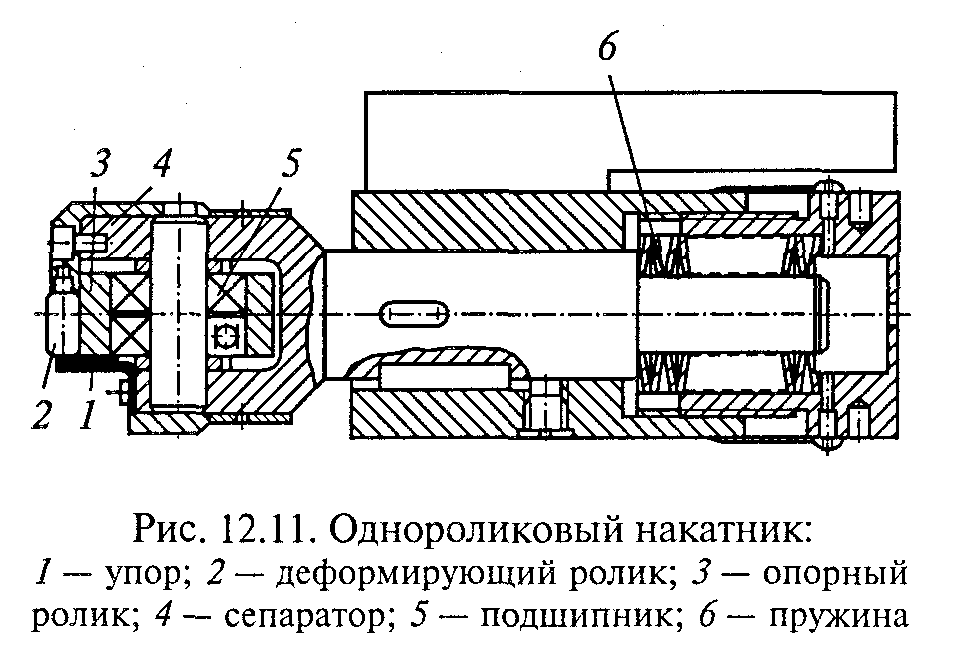
Поверхностное пластическое деформирование наружных цилиндрических поверхностей роликовым инструментом (рис. 12.11) применяется как для сглаживающей так и для упрочняющей обработки. Стержневой деформирующий ролик 2 устанавливается в сепараторе 4 и опирается на опорный ролик 3, смонтированный на подшипнике 5. От выпадания деформирующий ролик 2 удерживается упором 7. Усилие деформирования создается пружиной 6. Инструмент закрепляется на суппорте токарного станка.
Режимы обработки: скорость обкатывания — 60... 100 м/мин; осевая подача 0,1 ...0,4 мм/об; усилие деформирования 50...500 кгс. После обкатывания достигается шероховатость 0,63...0,08 мкм, снимаемый припуск 0,005...0,02 мм.
При обработке ППД могут возникать дефекты поверхности: отслаивание металла (шелушение) в результате перенаклепа из-за неправильного выбора режима обработки; вмятины, риски, сколы, раковины из-за нарушения целостности рабочей поверхности деформирующего ролика; волнистость из-за неодинаковых диаметров рабочих роликов) и формы (из-за наличия концентраторов напряжений и неравножесткости деталей).