ремонт автомобилей. remont auto КАРАГОДИН. В процессе эксплуатации автомобиля его рабочие свойства постепенно ухудшаются изза изнашивания деталей, а также коррозии и усталости материала, из которого они изготовлены
![]()
|
О и главная центральная ось инерции совпадает с осью изделия.6.3. Диагностирование составных частей двигателей'.Техническое состояние цилиндропоршневой группы также определяют по утечке воздуха, замеряемой прибором К-69М: ![]() Если значение утечки воздуха при положении поршня в в. м, т. больше предельного, следует проверить стетоскопом утечку воздуха через клапаны и убедиться в отсутствии утечки воздуха через прокладку головки цилиндров двигателя. Если при смачивании прокладки головки цилиндров мыльной водой на ней или в наливной горловине радиатора появляются пузырьки воздуха, это свидетельствует о слабой затяжке гаек головки цилиндров или о начале разрушения прокладки. Возможно наличие трещины в блоке цилиндров или камере сгорания. При отсутствии указанных дефектов и больших значениях утечки воздуха при положении поршня в в.м.т. следует продолжить! замеры при положении поршня в н.м. т. Результаты замеров следует сравнить с предельными значениями. Если показания прибора нестабильны, а утечки воздуха велики, это свидетельствует о неисправностях механизма газораспределения. Стуки двигателя прослушивают при помощи стержневого (рис. 6.18, а) или трубчатого (рис. 6.18, б) стетоскопов, прикасаясь концом стержня 2 или 4 к зонам прослушивания на двигателе. ![]() Состояние коренных подшипников коленчатого вала определяют, прослушивая нижнюю часть блока цилиндров при резком открытии и закрытии дроссельной заслонки. Изношенные коренные подшипники издают сильный глухой стук низкого тона, усиливающийся при резком увеличении частоты вращения коленчатого вала. Состояние шатунных подшипников коленчатого вала определяют аналогично. Изношенные шатунные подшипники издают стук среднего тона, по характеру схожий со стуком коренных подшипников, но менее сильный и более звонкий, исчезающий при выключении свечи зажигания или форсунки прослушиваемого цилиндра. Работу сопряжения поршень — гильза цилиндра прослушивают по всей высоте цилиндра при малой частоте вращения коленчатого вала с переходом на среднюю. Появление звука, напоминающего Дрожащий звук колокола, усиливающегося с увеличением нагрузки на двигатель и уменьшающегося по мере прогрева двигателя, Указывает на возможное увеличение зазора между поршнем и гильзой цилиндра, изгиб шатуна, перекос оси шатунной шейки или поршневого пальца, особенно, если у двигателя наблюдается повышенный расход топлива и масла. Скрипы и шорохи в сопряжении поршень — гильза цилиндра свидетельствуют о начинающемся заедании в этом сопряжении, вызванном малым зазором или Недостаточным смазыванием. Состояние сопряжения поршневой палец — втулка верхней головки шатуна проверяют, прослушивая верхнюю часть блока цилиндров при малой частоте вращения коленчатого вала с резким переходом на среднюю. Резкий металлический стук, напоминающий частые удары молотком по наковальне и пропадающий при отключении свечей зажигания или форсунок, указывает на увеличение зазора между поршневым пальцем и втулкой, недостаточное смазывание или чрезмерно большое опережение начала подачи топлива. Сопряжение поршневое кольцо — канавка поршня проверяют на уровне н. м. т. хода поршня при средней частоте вращения коленчатого вала. Слабый, щелкающий стук высокого тона, похожий на звук от ударов колец одно о другое, свидетельствует об увеличенном зазоре между кольцами и поршневой канавкой либо об изломе колец. Еще одним эффективным методом проверки состояния кривошипно-шатунного механизма является измерение суммарных зазоров в верхней головке шатуна и шатунном подшипнике. Проверку проводят при неработающем двигателе при помощи устройства КИ-11140 (рис. 6.19). Наконечник 5с трубкой '/устройства устанавливают на место снятой свечи зажигания или форсунки проверяемого цилиндра. К основанию 2 через штуцер присоединяют компрессорно-вакуумную установку. Поршень устанавливают за 0,5... 1,0 мм от в.м.т. на такте сжатия, стопорят коленчатый вал от проворачивания и с помощью компрессорно-вакуумной установки попеременно создают в цилиндре давление 200 кПа и разряжение 60 кПа. При этом поршень, поднимаясь и опускаясь, выбирает зазоры, сумма которых фиксируется индикатором 1. ![]() ГЛАВА 7. КОМПЛЕКТОВАНИЕ ДЕТАЛЕЙ И СБОРКА АГРЕГАТОВ 7.1. Комплектование деталей Комплектование — часть производственного процесса, которая выполняется перед сборкой и предназначена для обеспечения непрерывности и повышения производительности процесса сборки, для ритмичного выпуска изделий требуемого и стабильного уровня качества и снижения трудоемкости и стоимости сборочных работ. При комплектовании выполняют следующий комплекс работ: накопление, учет и хранение новых, восстановленных и годных без ремонта деталей, сборочных единиц и комплектующих изделий, подачу заявок на недостающие составные части; подбор составных частей сборочного комплекта (группы деталей, сборочных единиц и комплектующих изделий, составляющих то или иное изделие) по номенклатуре и количеству; подбор сопряженных деталей по ремонтным размерам, размерным и массовым группам; подбор и пригонку деталей в отдельных соединениях; доставку сборочных комплектов к постам сборки до начала выполнения сборочных работ. Различают три способа комплектования деталей: штучный, групповой и смешанный. При штучном комплектовании к базовой детали подбирают сопрягаемую деталь исходя из величины зазора или натяга, допускаемого техническими условиями. Например, к блоку цилиндров подбирают поршни. При штучном подборе затрачивается много времени. Этот способ применяют на небольших универсальных ремонтных предприятиях. При групповом комплектовании поле допусков размеров обеих сопрягаемых деталей разбивают на несколько интервалов, а детали по результатам измерений сортируют в соответствии с этими интервалами на размерные группы. Размерные группы сопрягаемых деталей маркируют цифрами, буквами или красками. Групповое комплектование применяют для подбора ответственных деталей (гильз, поршней, поршневых пальцев, коленчатых валов, плунжерных пар). При смешанном комплектовании деталей используют оба способа. Ответственные детали комплектуют групповым, а менее ответственные — штучным способом. Способ комплектования деталей находится в тесной связи со способом обеспечения точности при сборке. Наряду с тремя основными способами комплектования во избежание несбалансированности некоторые детали подбирают по массе (например, поршни двигателей внутреннего сгорания). Иногда комплектование сопровождается слесарно-подгоночными операциями. Крупногабаритные детали и сборочные единицы (блок и головка цилиндров, картеры, детали кабины, кузова, рамы и др.) целесообразно доставлять на посты сборки, минуя комплектовочный участок. При комплектовании на каждое собираемое изделие заполняется комплектовочная карта, в которой указываются: номера цеха, участка, рабочего места, где выполняются сборочные операции; обозначения деталей, сборочных единиц, материалов и комплектующих Изделий; номера цехов, участков, складов, откуда поступают комплектующие единицы; количество деталей, материалов и сборочных единиц, подаваемых на рабочие места сборки за смену; нормы расхода материалов и комплектующих изделий и др. Кодированная запись указанной информации позволяет применять вычислительную технику при ее обработке. На комплектовочном участке имеются столы для контроля деталей, стеллажи и шкафы для хранения инструмента и приспособлений, слесарные верстаки, прессы и т.д. Рабочие места рекомендуется специализировать по наименованиям агрегатов, узлов. На них должны быть соответствующие чертежи, таблицы посадок деталей, каталоги деталей, входящих в узлы, обязательно наличие местного освещения. 7.2. Методы обеспечения точности сборки Точность сборки — свойство технологического процесса сборки изделия обеспечивать соответствие действительных значений параметров изделия значениям, заданным в технической документации. Точность сборки зависит от точности размеров и формы, шероховатости сопрягаемых поверхностей деталей, их взаимного положения при сборке, технического состояния средств технологического оснащения, деформации системы «оборудование — приспособление — инструмент — изделие» в момент выполнения сборки и т. п. Точность сборки аналитически может быть определена с помощью сборочных размерных цепей. Размерная цепь представляет собой замкнутый контур взаимосвязанных размеров, обусловливающих их численные значения и допуски. Размерная цепь состоит из составляющих, исходного (замыкающего) и других видов звеньев. Составляющее звено — звено размерной цепи, изменение которого вызывает изменение исходного (замыкающего) звена. Составляющие звенья обозначаются прописными буквами русского алфавита с цифровыми индексами (например, А1, А2 или Б1, Б2). Исходное (замыкающее) звено — звено, получаемое в цепи последним в результате решения поставленной задачи при изготовлении или ремонте. Оно обозначается той же буквой алфавита с индексом Σ (например, АΣ или BΣ). Компенсирующее звено — звено, изменением размера которого достигается требуемая точность замыкающего звена. Компенсирующее звено обозначается той же буквой алфавита с соответствующим цифровым индексом и буквой к (например, А4к или Б7к)- По характеру воздействия на замыкающее звено составляющие звенья могут быть увеличивающими или уменьшающими, т. е. при их увеличении замыкающее звено увеличивается или уменьшается. Увеличивающие звенья могут обозначаться стрелками, направленными вправо — А , уменьшающие — стрелками влево — А . Требуемая точность сборки изделий достигается одним из пяти методов: полной, неполной и групповой взаимозаменяемости, регулирования и пригонки. Метод полной взаимозаменяемости — метод, при котором требуемая точность сборки достигается путем соединения деталей без йх выбора, подбора или изменения размеров. Применение метода полной взаимозаменяемости целесообразно при сборке соединений, состоящих из небольшого количества деталей, так как увеличение числа деталей требует обработки сопряженных поверхностей с меньшими допусками, что не всегда технически достижимо и экономически целесообразно. Метод неполной взаимозаменяемости — метод, при котором требуемая точность сборки достигается не у всех соединений при сопряжении деталей без их выбора, подбора или изменения размеров, а у заранее обусловленной их части, т. е. определенный процент (или доли процента) соединений не удовлетворяет требованиям точности сборки и требует разборки и повторной сборки. Метод неполной взаимозаменяемости целесообразен, если дополнительные затраты на выполнение разборочно-сборочных работ меньше затрат на изготовление сопрягаемых деталей с более узкими допусками, обеспечивающими получение требуемой точности сборки у всех соединений. Метод групповой взаимозаменяемости (так называемый селективный метод) — метод, при котором требуемая точность сборки достигается путем соединения деталей, принадлежащих к одной из размерных групп, на которые они предварительно рассортированы. В пределах каждой группы требуемая точность сборки достигается методом полной взаимозаменяемости. Данный метод обеспечивает высокую точность сборки, однако сопряжен с дополнительной операцией сортировки деталей на размерные группы, необходимостью хранения запасов деталей всех размерных групп и невозможностью использования части деталей, когда сопрягаемые детали неравномерно распределяются по размерным группам. Метод регулирования — метод, при котором требуемая точность сборки достигается путем изменения размера одной из деталей (или группы деталей) соединения, называемой компенсатором, без снятия слоя материала. Например, требуемая точность осевого зазора (натяга) соединений с коническими подшипниками качения (дифференциал, главная передача, механизм рулевого управления и др.) обеспечивается изменением толщины неподвижного компенсатора, а точность зазора между торцом клапана и болтом толкателя или коромысла (клапаном-коромыслом) достигается путем изменения положения подвижного компенсатора — регулировочного болта — в осевом направлении. Метод пригонки — метод, при котором требуемая точность сборки достигается путем изменения размера компенсатора со снятием слоя материала. Например, требуемая точность посадки плунжера в гильзе или клапана в корпусе форсунки, а также герметичность в соединении клапан — гнездо головки цилиндров достигается путем притирки. Сборочные размерные цепи рассчитывают одним из двух методов: максимума — минимума или вероятностным. При расчете методом максимума— минимума номинальный размер замыкающего звена размерной цепи ![]() где ξi - — передаточное отношение (для цепей с параллельными звеньями ξi = 1 — для увеличивающих звеньев; ξi = — 1 — для уменьшающих звеньев); m — число звеньев размерной цепи; А — номинальный размер i-го составляющего звена. Допуск замыкающего звена δAΣ при расчете методом максимума—минимума определяют по формуле ![]() где δAi — допуск i-го составляющего звена. 7.3. Виды сборки Виды сборки изделий классифицируются по следующим основным признакам: объект сборки, последовательность сборки, точность сборки, уровень механизации и автоматизации процесса сборки, подвижность изделия при сборке, организация производства. По объекту сборки сборка подразделяется на узловую и общую. Примеры узловой сборки — сборка поршня с шатуном и кольцами, коленчатого вала с маховиком и сцеплением, головки цилиндров с клапанными механизмами, жидкостного и масляного насосов; примеры общей сборки — сборка агрегатов из узлов, сборка автомобиля из агрегатов и узлов. По последовательности сборки выделяют последовательную (сборочные операции выполняются одна за другой), параллельную (операции выполняются одновременно) и последовательно-параллельную (операции выполняются и одна за другой, и одновременно). Поуровню механизации и автоматизации процесса сборку разделяют на ручную, механизированную, автоматизированную, автоматическую. По состоянию объекта сборки выделяют стационарную (неподвижную) и подвижную сборку с непрерывным или периодическим перемещением собираемого изделия между рабочими местами сборки. По организации производства выделяют типовую поточную, групповую (поточную и непоточную) и единичную как наиболее распространенный вид организации сборки на существующих ремонтных предприятиях. 7.4. Виды соединений и технология их сборки При сборке выделяют следующие группы и виды соединений: по сохранению целостности при разборке — разъемные и неразъемные; по возможности относительного перемещения составных частей — подвижные и неподвижные; по методу образования — резьбовые, прессовые, шлицевые, шпоночные, сварные, клепаные, комбинированные и др.; по форме сопрягаемых поверхностей — цилиндрические, плоские, конические, винтовые, профильные и др. Соединения, содержащие в себе несколько признаков, обозначаются соответствующим сочетанием терминов, например неподвижные разъемные резьбовые соединения, подвижные неразъемные профильные соединения. Наиболее распространенными соединениями в конструкции автомобилей являются: разъемные подвижные (поршень — цилиндр, вал — подшипник скольжения, плунжер — гильза); зубчатые и шлицевые; разъемные неподвижные (резьбовые, прессовые и шпоночные); неразъемные неподвижные (сварные, паяные, клепаные, клееные); неразъемные подвижные — радиальные шариковые подшипники качения. Сборка резьбовых соединений. При сборке резьбовых соединений должны быть обеспечены: соосность осей болтов, шпилек, винтов с резьбовыми отверстиями и необходимая плотность посадки в резьбе; отсутствие перекосов торца гайки или головки болта относительно поверхности сопрягаемой детали, так как перекос является основной причиной обрыва винтов и шпилек; соблюдение очередности и постоянство усилий затяжки крепежных деталей в групповых резьбовых соединениях. Последнее означает, чта затяжка гаек (болтов) производится в определенной последовательности (рис. 7.1). Их затягивают крест-накрест в несколько приемов — сначала неполным моментом, а затем окончательным, указанным в нормативно-технической документации. Контроль момента затяжки резьбовых соединений осуществляют динамометрическими ключами по степени изгиба (рис. 7.2) или кручения стержня ключа либо с помощью предельных муфт, встраиваемых в резьбозавертывающие машины (установки). Сборка прессовых соединений. Качество сборки прессовых соединений формируется под воздействием следующих факторов: значения натяга, материала сопрягаемых деталей, геометрических размеров, формы и шероховатости поверхностей, соосности деталей и прилагаемого усилия запрессовывания, наличия смазки и др. Применение смазочного материала уменьшает требуемое усилие запрессовки и предохраняет сопрягаемые поверхности от задиров. Качество сборки прессовых соединений определяется также точностью центрирования сопрягаемых деталей (с помощью приспособлений и оправок). ![]() Повышение прочности неподвижных соединений с натягом в 1,5...2,5 раза обеспечивается применением сборки с термовоздействием — нагревом охватывающей и (или) охлаждением охватываемой детали. При этом образуется необходимый сборочный зазор и не требуется приложение осевой силы. Нагрев деталей осуществляется в масляных ваннах, электропечах, индукционных установках и др. Для охлаждения деталей применяют жидкий азот, сухой лед (твердую углекислоту) в смеси с ацетоном, бензином или спиртом. Сборка соединений с подшипниками качения. При запрессовке подшипника качения размер его колец изменяется: внутреннее кольцо увеличивается, а наружное уменьшается. Эти изменения вызывают уменьшение диаметрального зазора между рабочими поверхностями колец и шариков. Внутреннее кольцо подшипника, сопряженное с цапфой вала, должно иметь посадку с натягом, а наружное — с небольшим зазором так, чтобы кольцо имело возможность во время работы незначительно провертываться. При установке в сборочной единице двух или нескольких подшипников необходимо уделять внимание соосности посадочных поверхностей в корпусных деталях. То же касается и шеек валов. Несоблюдение этого условия может привести к перекосам подшипников и заклиниванию шариков. При запрессовке подшипников качения с помощью оправок необходимо, чтобы усилие запрессовки передавалось непосредственно на торец соответствующего кольца: внутреннего — при напрес-совке на вал, наружного — при запрессовке в корпус и на оба торца колец, если подшипники одновременно напрессовываются на вал и входят в корпус. Нагрев подшипников в масляной ванне до 100 °С при установке на вал заметно уменьшает осевое усилие для запрессовки. Целесообразен также нагрев корпусной детали. ![]() ![]() Сплошной стрелкой показано направление смещения шестерен для исправления контакта. Если при этом боковой зазор получается чрезмерно большим или Малым, то необходимо сместить другую шестерню, как показано прерывистой стрелкой. Регулировка радиального зазора в коническом роликовом подшипнике производится смещением наружного или внутреннего кольца в осевом направлении регулировочным винтом или гайкой либо путем подбора соответствующего комплекса прокладок. Контроль заданного предварительного натяга после сборки узда осуществляют по моменту, необходимому для прокручивания одной из сопряженных деталей относительно неподвижной детали при отсутствии осевого люфта в подшипниковых соединениях. Срок службы подшипников качения зависит в значительной мере от степени предохранения их от грязи и пыли. Поэтому после сборки устанавливают прокладки, задерживающие смазку и предохраняющие подшипник от попадания в рабочую зону пыли и влаги. Сборка зубчатых передач. Сборка цилиндрических зубчатых передач осуществляется методами полной или неполной взаимозаменяемости. Перед сборкой зубчатой пары на специальном приспособлении определяют боковой зазор между зубьями для обеспечения плавности работы пары, а при необходимости подбирают пару. Для правильного зацепления зубчатых цилиндрических колес необходимо, чтобы оси валов лежали в одной плоскости и были параллельны. Их выверка производится регулированием положения гнезд под подшипники в корпусе. После установки зубчатые колеса проверяют по зазору, зацеплению и контакту. При сборке конической пары редуктора заключительной операцией является регулировка зацепления путем осевого перемещения ведущей шестерни (вперед-назад) и (или) ведомого колеса (вправо-влево). Это достигается перемещением части регулировочных прокладок с одной стороны на другую. Качество зацепления оценивается размерами, формой и положением пятна контакта на зубьях (рис. 7.3), значением бокового зазора между зубьями и уровнем шума на специальных стендах, оборудованных шумоизмерительной аппаратурой. 7.5. Контроль качества сборки В процессе узловой и общей сборки выполняют комплекс контрольных операций — проверок: комплектности деталей и сборочных единиц; точности посадок и взаимного расположения сопряженных деталей и сборочных единиц; использования одноименных размерных групп сопряженных деталей при сборке методом групповой взаимозаменяемости; выполнения технологических требований по сборке, регулировке, приработке и испытанию изделий; герметичности соединений, в том числе качества притирки клапанов; отсутствия прокладок и сальников, бывших в эксплуатации; смазки деталей сборочных единиц. Производится проверка технологических параметров и определение функциональных показателей собранных изделий (развиваемая мощность и удельный расход топлива, напор и подача масляного насоса, электрические параметры генератора и др.). Контроль сборки осуществляется с применением соответствующих средств измерений, которые выбирают с учетом конструктивных особенностей изделия, метрологических характеристик, а также себестоимости выполнения контрольной операции. В качестве средств измерения используют универсальные штангенинст-рументы, микрометрические и индикаторные инструменты, электрические и пневматические приборы и различные специальные контрольные приборы, приспособления, стенды и установки. Обеспечение требуемого уровня качества отремонтированных изделий невозможно без эффективного функционирования службы технического контроля как неотъемлемой составной части технологических процессов. В зависимости от стабильности соблюдения качества собранных изделий применяется выборочный или сплошной контроль. Операции технического контроля разрабатываются совместно с операциями технологического процесса сборки изделий, которые формируют и определяют заданное качество, а также обеспечивают получение информации для регулирования технологического процесса и предупреждения брака. Погрешности сборки по характеру и проявлению могут быть случайными и периодическими. Основные из них — это некачественные посадки, вызывающие появление других неисправностей. Распространенными дефектами являются отклонения от точности взаимного расположения деталей и узлов, неравномерная и беспорядочная затяжка групп резьбовых соединений, неплотность прилегания сопрягаемых поверхностей и др. Большинство погрешностей сборки возникает из-за низкого качества деталей и узлов, поступающих на сборку, и нарушения технологической дисциплины. 7.6. Балансировка деталей и сборочных единиц Неуравновешенность (дисбаланс) вращающихся частей является одним из факторов, лимитирующих надежность автомобилей в эксплуатации. Неуравновешенность — состояние, характеризующееся таким распределением масс, которое вызывает переменные нагрузки на опоры, повышенные износ и вибрацию, способствует быстрой утомляемости водителя. Дисбаланс изделия — векторная величина, равная произведению локальной неуравновешенной массы т На расстояние до оси изделия г или произведению веса изделия расстояние от оси изделия до центра масс е, т.е. D = mr = Ge. Дисбаланс возникает в процессе изготовления (восстановления) деталей, сборки узлов и агрегатов и изменяет свое количественное значение в процессе эксплуатации и текущего ремонта. В зависимости от взаимного расположения оси изделия и его главной центральной оси инерции различают три вида неуравновешенности: статическую, моментную и динамическую. При статической неуравновешенности ось 0В вращения детали смещена на эксцентриситет е и параллельна главной центральной оси инерции ОИ (рис. 7.4, а). Данная неуравновешенность присуща дискообразным деталям (маховики, диски сцепления, шкивы, крыльчатки, сцепления в сборе и др.) и проявляется как в статическом, так и в динамическом состоянии. Статическая неуравновешенность определяется главным вектором дисбалансов Д, (статический дисбаланс). ![]() При моментной неуравновешенности ось изделия и его главная центральная ось инерции пересекаются в центре масс. Данная неуравновешенность определяется главным моментом дисбалансов М или двумя равными по значению антипараллельными векторами дисбалансов в двух произвольных плоскостях (рис. 7.4, б). Моментная неуравновешенность является частным случаем более общей — динамической неуравновешенности, при которой ось изделия и его главная центральная ось пересекаются не в центре масс или перекрещиваются (рис. 7.4, в). Присуща она деталям и узлам типа валов, состоит из статической и моментной неуравно-вешенностей и определяется главным вектором дисбалансов Дт и главным моментом дисбалансов М или двумя приведенными векторами дисбалансов (в общем случае разных по значению и непараллельных), лежащих в двух выбранных плоскостях. Дисбаланс изделия характеризуется числовым значением (в г • мм, г.см, кг-см) и углом дисбаланса (в град.) в системе координат, связанных с осью изделия. Главный вектор дисбалансов Дт может быть разложен на два параллельных Дт1 и Дт2, приложенных в выбранных плоскостях, а главный момент дисбалансов М может быть заменен моментом пары равных антипараллельных дисбалансов Д^ и Д^в тех же плоскостях. Геометрические суммы Дт] + Д, -_Д и Дт2 + Дз = Д образуют два приведенных дисбаланса Д. и Д в выбранных плоскостях, которые полностью определяют динамическую неуравновешенность изделия. При вращении неуравновешенного изделия возникает переменная по величине и направлению центробежная сила инерции Р = mra2 = Geco2, где со — угловая скорость вращения. Приведение изделий, обладающих неуравновешенностью, в уравновешенное состояние осуществляется их балансировкой, т. е. определением дисбаланса изделия и устранением (уменьшением) его путем удаления или добавления корректирующих в определенных точках масс. В зависимости от вида неуравновешенности тела различают два вида балансировки: статическую и динамическую. Статическая балансировка. При такой балансировке определяется и уменьшается (до остаточного допустимого значения дисбаланса) главный вектор дисбалансов Дт путем удаления или добавления корректирующей массы тк (обычно в одной плоскости корректировки) так, чтобы »VK = тг (см. рис. 7.4, о). Статическая балансировка производится на стендах с призмами или роликами либо на специальных станках для статической балансировки в динамическом режиме (при вращении тела). Такая балансировка повышает точность балансировки и открывает возможность автоматизации процесса. Динамическая балансировка. При такой балансировке определяются и устраняются (уменьшаются) два приведенных дисбаланса Д и Д в выбранных плоскостях коррекции путем удаления или Добавления двух приведенных корректирующих масс, в общем случае разных по значению и расположенных под разными углами коррекции, в системе координат, связанной с осью детали. При Динамической балансировке устраняется (уменьшается) как статическая, так и моментная неуравновешенность, и изделие становится полностью сбалансированным, при этом Дт |
Сборочные единицы | Автомобили | |
легковые | грузовые | |
Коленчатый вал | 10. ..15 | 20.. .30 |
Коленчатый вал в сборе с маховиком и | 20. ..50 | 50... 70 |
сцеплением | | |
Маховик | 30. ..40 | 35... 60 |
Ведомый диск сцепления, кожух сцепления в сборе с нажимным диском | 10. ..25 | 30. ..50 |
Карданный вал | 15. ..25 | 50. ..70 |
Для балансировки коленчатых валов отдельно и в сборе с маховиком и сцеплением, карданных валов в числе прочих используют балансировочный станок ЦКБ-2468 (рис. 7.5). Принцип работы станка состоит в том, что неуравновешенная масса 6 вызывает колебание маятниковой рамы 1, имеющей пружинную подвеску 5, в горизонтальной плоскости.

При балансировке левого конца правый конец запирают фиксатором 4. Чем больше неуравновешенная масса, тем больше амплитуда колебаний рамы и тем больше индуктируется ток в катушке 3 индукционного датчика (имеющего линейную характеристику). Катушка, жестко связанная с рамой станка, колеблется в поле неподвижного постоянного магнита 2. Ток через полукольца о выпрямительного устройства и щетки 10 подается на милливольтметр 12. Для исключения влияния привода на балансируемое изделие применяют шарнирное соединение 7. Чем больше дисбаланс, тем больше показание милливольтметра. С помощью лимба П вала выпрямительного устройства и лимба 8 вала привода определяют положение неуравновешенной массы.
7.7. Технологические процессы сборки составных частей автомобилей
Сборка двигателя. На специально оборудованных рабочих местах собирают следующие составные части двигателя: поршень с шатуном, головку цилиндров, коленчатый вал с маховиком и сцеплением, масляный и жидкостной насосы и др. Общая сборка двигателя обычно производится на поточной линии.
На автозаводах некоторые сопряженные детали двигателя (блок цилиндров—крышки коренных подшипников, блок цилиндров— картер сцепления и др.) обработаны совместно, поэтому в процессе ремонта их нужно сохранять комплектно.
Для обеспечения качественной сборки двигателей рекомендуется все детали перед сборкой продуть сжатым воздухом, трущиеся поверхности тщательно протереть, промыть, смазать маслом.
Сопряжения кривошипно-шатунного механизма имеют весьма жесткие допуски посадок и должны обеспечивать необходимую герметичность.
Для обеспечения качественной сборки шатунно-поршневой группы целесообразно организовать на линии сборки двигателей два рабочих места: первый — для подбора поршней по цилиндрам, второй — для сборки группы. Цилиндры блока после механической обработки, мойки и тщательной очистки сортируют на размерные группы и маркируют. Поршни (одной массовой группы) подбирают по цилиндрам, согласовывая размерную группу поршня с размерной группой каждого цилиндра. На посту сборки группы по подобранному комплекту поршней подбирают комплект поршневых пальцев по размерным группам отверстий в бобышках и затем по поршневым пальцам подбирают комплект шатунов (одной массовой группы) соответствующих размерных групп отверстий в верхней головке. После сборки группы следует проверить правильность взаимного положения образующей поверхности юбки поршня и отверстия в верхней головке шатуна. Перед установкой Поршневых колец на поршень сначала проверяют их посадку в канавках, а затем подгоняют по цилиндрам, исходя из величины зазора в стыке (замке). Надевают и снимают поршневые кольца При помощи съемника. Разница в массе поршней в сборе с шатунами, устанавливаемых на один двигатель, для ЗИЛ-130 не должна превышать 16г.
Окончательную затяжку резьбовых соединений выполняют с требуемым моментом и в соответствующей последовательности После окончательной затяжки гаек коренных подшипников коленчатый вал должен свободно проворачиваться. Если вал туго проворачивается за маховик, то это свидетельствует о малых зазорах, несоосности постелей, изгибе вала или дефектах сборки. После сборки двигатель направляют на приработку и испытания.
Сборка коробки передач. Технологический процесс сборки коробки передач состоит из сборки отдельных узлов, выполняемой на специальных рабочих местах, и общей сборки, осуществляемой обычно на поточной линии.
На специально оборудованных рабочих местах вне линии общей сборки собирают следующие основные узлы: первичный вал, промежуточный вал, вторичный вал, крышку коробки передач, механизм управления. При установке узлов в картер обращают особое внимание на правильность монтажа подшипников, посадок в сопряжениях, служащих для переключения передач, а также на обеспечение требуемого бокового зазора между зубьями шестерен и осевые зазоры блока шестерен промежуточного вала, шестерен ведомого вала и блокирующих колец синхронизаторов. Шестерни ведомого вала и синхронизаторы должны перемещаться вдоль шлицев свободно, без заеданий. Собранные коробки передач направляют на испытания.
Сборка заднего моста. Процесс сборки заднего моста включает сборку узлов: картера заднего моста с трубами полуосей, сальниками и пробками; ведущей конической шестерни с картером подшипников; дифференциала с ведомой цилиндрической (конической) шестерней; ведомой конической шестерни с валом ведущей цилиндрической (конической) шестерни; редуктора; ступицы с тормозным барабаном; опорного диска заднего тормоза; регулировочного рычага и колесного цилиндра.
Особое внимание при сборке уделяется коническим шестерням гипоидной передачи. Качество их зацепления определяется величиной бокового зазора между зубьями, уровнем шума, величиной и расположением пятна контакта. Низкое качество сборки резко снижает работоспособность этой передачи вследствие появления задиров и усиливает шум.
Величина бокового зазора гипоидной пары должна находиться в пределах 0,12... 0,35 мм. Зазор между зубьями замеряют щупом у широкой части зуба не менее чем для трех зубьев ведомой шестерни.
Для нормальной установки зубьев по пятну контакта закрепляют стакан в сборе с ведущей конической шестерней на картере редуктора и наносят тонким слоем масляную краску на рабочие поверхности зубьев ведомой конической шестерни. После этого поворачивают вал ведущей конической шестерни в разные стороны, притормаживая ведомую шестерню. Если положение пятна контакта неправильное, необходимо произвести регулировку зацепления перемещением ведущей и ведомой шестерен в осевом направлении, используя соответствующие наборы прокладок. Перемещение ведущей конической шестерни осуществляется изменением) толщины прокладок, установленных между фланцами картера вала ведущей шестерни и картером редуктора. Ведомая шестерня перемещается за счет перекладывания прокладок из-под фланцев одной крышки картера редуктора под фланец другой крышки без изменения их общей толщины, чтобы не нарушить регулировку подшипников вала ведущей цилиндрической шестерни.
Уровень шума должен быть в пределах допустимых норм: для легковых автомобилей — не более 50, а для грузовых автомобилей — не более 80 дБ. Для создания предварительного натяга конических подшипников вала ведущей конической шестерни применяют набор регулировочных шайб, устанавливаемых между торцами внутреннего кольца подшипника и распорной втулки. При этом момент сопротивления вращению вала ведущей шестерни в подшипниках для автомобиля ЗИЛ- 130 должен находиться в пределах 1,0. ..3,5 Н-м, что соответствует усилию 16, 6. ..58,3 Н.
При сборке дифференциала коробки сателлитов ориентируют относительно друг друга, контролируют биение тыльной части ведомой конической шестерни, боковой зазор в зацеплении зубьев шестерен полуосей и сателлитов и плавность вращения шестерен полуосей.
Сборка карданной передачи. Процесс сборки осуществляется из предварительно собранных узлов — карданных валов, промежуточной опоры шарниров. Детали карданной передачи перед сборкой должны быть промыты и обдуты сжатым воздухом, а игольчатые подшипники смазаны жидкой смазкой. Смазочные каналы крестовин должны быть прочищены и в их отверстия ввернуты предохранительные клапаны. При сборке карданной передачи автомобиля ЗИЛ- 130 необходимо следить за тем, чтобы фланцы-вилки у коробки передач и заднего моста находились во взаимно перпендикулярных плоскостях.
При сборке карданных передач контролируют осевой люфт крестовин, легкость вращения подшипника опоры, перемещение скользящей вилки и суммарный окружной люфт карданных валов. Проверяют прогиб трубы вала. Собранные карданные валы подвергают балансировке. При наличии необходимого оборудования Рекомендуется проводить балансировку карданной передачи авто-Нобиля ЗИЛ- 130 в сборе. При этом карданная передача балансируется со стороны переднего и заднего шарниров, а также со стороны промежуточной опоры.
Сборка рулевого управления. Процесс сборки рулевого управле-Чия с гидроусилителем включает сборку следующих узлов: рулевого механизма с гидроусилителем, насоса гидроусилителя, карданного вала, колонки. Перед сборкой все детали необходимо тщательно промыть и просушить. При сборке необходимо смазывать детали маслом, применяемым для гидроусилителя. После рулевого механизма контролируют момент вращения рулевого винта (он должен быть не более 500 Н-м), эффективность и величину усилия реактивных пружин на всем пути перемещения поршня-рейки. Момент вращения вала рулевого управления должен быть равен 0,3...0,8 Н-м, что соответствует усилию 1,2...3,2 Н, приложенному на радиусе рулевого колеса 240 мм.
При сборке насоса гидроусилителя предварительно подбирают лопасти насоса по пазам ротора и золотник по отверстию в крышке, испытывают и регулируют клапаны.
7.8. Механизация и автоматизация процессов сборки
Для установки и закрепления собираемых изделий применяют различные захваты, стенды, универсальные и специализированные приспособления с ручными или механизированными зажимными устройствами. Наибольшее распространение при сборке получили электрические и пневматические сверлильные и шлифовальные машины, гайковерты. Для сборки прессовых соединений широкое применение получили прессы и приспособления с ручным или механизированным приводом.
На крупных ремонтных предприятиях организация поточной сборки изделий осуществляется с применением поточно-механизированных линий на основе эстакад с тележками (с ручным или механизированным перемещением изделия) и комплектом механизированных и автоматизированных средств технологического оснащения (рис. 7.6).
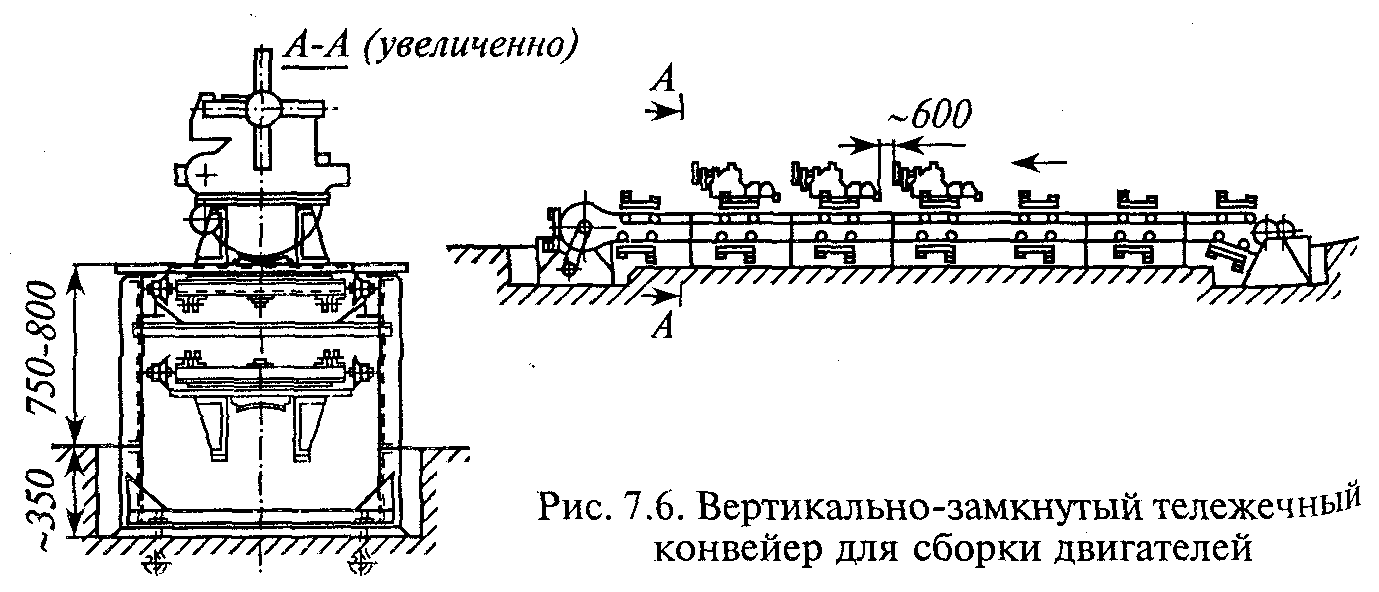

Дальнейшее эффективное развитие авторемонтного производства связано с использованием автоматов и роботизированных комплексов. На рис. 7.7 представлен автомат для сборки шатунно-поршневой группы, работающий следующим образом.
Шатун устанавливается в позиции I на палец отверстием в нижней головке и удерживается двумя штифтами. Поршни подаются автоматически на позицию II из нагревательной печи. Поршневые пальцы, подобранные по размерам вне автомата, поступают на позицию сборки с поршнем и шатуном по лотку.
Поршень приводится во вращение роликом 3. К последнему поршень прижимается роликами 2, действующими от гидропривода. Когда поршень занимает нужное угловое положение, он перемещается на позицию сборки. Одновременно поворачивается стол с шатунами. Один из них, оказавшийся на позиции II, поднимается, входя в поршень. Далее в отверстие поршня и шатуна входит центрирующий палец 1, а с противоположной стороны в поршень запрессовывается поршневой палец. Центрирующий шток отходит в обратную сторону. По окончании этих действий шатун с поршнем опускаются, а стол поворачивается. В позиции III устанавливаются два стопорных кольца, которые поступают к месту сборки из магазина 4 и вводятся штоком в отверстие поршня до попадания их в канавки.
В позициях IV, V надеваются поршневые кольца. Кольца находятся в магазинах и ориентированы замками по ножам. После подвода к месту сборки кольца разводятся в замках механизмами 5, 6, 1, имеющими вид клещей, расположенных на ползунках. После Разведения колец шатун с поршнем поднимается на определенную высоту до упора в соответствии с нужным расположением того или иного кольца на поршне. При переключении механизма Развода кольца оно оказывается в соответствующей канавке поршня. После сборки поршня с шатуном в его нижнюю головку устанавливаются вкладыши.
Автомат для установки коленчатых валов показан на рис. 7.8.

Блок цилиндров 1 шаговым конвейером подается на рабочую позицию. Конвейер 18, расположенный параллельно сборочной линии, с помощью гидр0. цилиндра 16 перемещает коленчатый вал П к механизму загрузки шайбы упорного подшипника. С помощыо гидроцилиндра 17, рейки и зубчатых колес коленчатый вал поднимается, и на него надевается шайба упорного подшипника.
Механизм загрузки, обеспечивающий поштучную выдачу шайб, состоит из магазина 7, толкателя 10 и гидроцилиндра 6. С помощью толкателя 9 и гидроцилиндра 8 шайба насаживается на коленчатый вал. Коленчатый вал устанавливается в блок подъемно-поворотным устройством. Поворотная стойка 12 с помощью гидроцилиндра 14, рейки 15 и колеса 13 поворачивается.
Вместе со стойкой поворачивается и рычаг 4 с клещами-захватами 2, удерживающими коленчатый вал. Подъем и опускание рычага осуществляются с помощью гидроцилиндра 5, а зажим и разжим клещей-захватов — гидроцилиндром 3.
Поршни с шатунами в сборе устанавливают в блок цилиндров со стороны головки цилиндров, но можно и со стороны коленчатого вала, если позволяет пространство между щеками вала и блоком. Первый способ требует специального приспособления для сжатия поршневых колец и ввода поршней в цилиндры, второй позволяет вводить поршни в цилиндры без приспособления (у цилиндров со стороны коленчатого вала имеется конический раструб).