|
1. Технологический процесс и его структура Технологическим процессом
Полирование Полирование- процесс чистовой обработки мягким кругом из войлока, фетра, парусины или кожи с нанесенным на него мелкозернистым абразивным порошком со смазкой. Иногда применяют полировальные круга с графитовым наполнителем. Это позволило: а) получать высококачественную гладкую поверхность шероховатостью RaO,05-0,025 б) устранить непроизводительные ручные способы и инструменты полирования; в) увеличить производительность в 6-8 раз. Также применяют полировальные абразивные ленты. Ленты иногда заменяются текстильными жгутами, покрытыми абразивными пастами. Полированием не исправляют погрешности геометрической формы, а также местные дефекты, от предыдущих операций (вмятины, раковины и др.). Полирование ведется при высокой скорости полировального круга или абразивной ленты (до 40 м/сек). В массовом и крупносерийном производстве применяют многошпиндельные полировальные автоматы
2.10. Материалы, термическая обработка зубчатых колес, методы получения заготовок, базирование, структура технологического процесса при обработке цилиндрических зубчатых колес. Служебное назначение и типовые конструкции зубчатых колес
Цилиндрические зубчатые колеса служат для передачи вращательного движения между валами с параллельными и перекрещивающимися осями. Различают силовые зубчатые передачи, служащие для передачи крутящего момента с изменением частоты вращения валов и кинематические передачи, служащие для точной передачи вращательного движения между валами при небольших значениях крутящего момента. Цилиндрические зубчатые колеса изготовляют с прямыми, косыми и шевронными зубьями. В зубчатой передаче с перекрещивающимися осями применяются колеса с криволинейными зубьями. Основными механизмами, в которых применяют цилиндрические зубчатые колеса являются коробки передач тракторов, автомобилей, станков пр.
По конструкции цилиндрические зубчатые колеса делятся на пять основных типов (рис. 2. 81): I - одновенцовые колеса с достаточно большой длиной посадочного отверстия; II - многовенцовые колёса, III одновенцовые колеса типа дисков; IV — венцы, которые изготавливаются отдельно соединяются затем со ступицей; V колеса - валы (вал-шестерни).
Требования к точности зубчатых колес
Основными показателями точности зубчатых колес являются: Кинематическая точность - характеризуется погрешностью угла поворота колеса за один оборот шестерни. Связана с накопленной ошибкой шага. Важна для механизмов, где требуется точность передаточного отношения. Плавность работы - характеризуется колебаниями скорости вращения колеса при равномерном вращении шестерни. Связана с ошибками шага и профиля зубьев. Влияет на динамические нагрузки и шум при работе передачи.
Пятно контакта зубьев - характеризуется концентрацией нагрузки на боковой поверхности зубьев, которые находятся в контакте. Влияет на долговечность работы передачи.
Боковой зазор между по нерабочими поверхностями зубьев при их контакте по рабочим поверхностям, характеризуется свободным вращением колес без заклинивания зубьев. Важен для реверсивных передач, а также для работающих при высокой температуре.
По ГОСТ 1643—81 установлено 12 степеней точности зубчатых колес (в порядке убывания точности): 1, 2, 3, 4, 5, 6, 7, 8, 9, 10, 11, 12. Для степеней точности 1 и 2 допуски в стандарте не указаны. Эти степени оставлены для дальнейшего развития, чтобы не вводить как в других стандартах обозначения с нулем (0 или 01). Наиболее широко в машиностроении применяются колеса 6 — 8 степени точности. В приборостроении и станкостроении используются колеса 5 степени точности. В открытых передачах используются колеса 9 степенью точности.
Независимо от степени точности стандартом установлены нормы точности на боковой зазор, который обозначен в порядке увеличения: Н, Е, Д, С, В, А. Зазор в сопряжении Н минимален и равен нулю. Обычно рекомендуется сопряжение В.
Точность зубчатых колес в силовых передачах выбирается в зависимости от скорости вращения, а точность зубчатых колес в кинематических передачах выбирается в зависимости от их назначения
Для точных зубчатых колес нормируется также торцевое и радиальное биение. Посадочное отверстие выполняется по 7 квалитету, а для прецизионных колес по 5 - 6 квалитету.
Материал и термическая обработка зубчатых колес
Основными материалами для зубчатых колес являются углеродистые и легированные стали, -которые термически; упрочняются до высокой твёрдости, марок 45, 20Х, 40Х, 40XH, 35XM и пр.
Основными видами термической обработки зубчатых колес являются: Объемная закалка является наиболее простым способом термообработки колес. Ее недостаткам следует отнести высокую прокаливаемость материала, что уменьшает сопротивление усталости материала при изгибе зубьев. Поверхностная закалка обеспечивает высокую твердость поверхности зубьев при вязкой сердцевине. Нагрев колес при поверхностной закалке производится в индукторах токами высокой частоты (ТВЧ).
Химико-термическая обработка (ХТО) заключается в насыщении поверхности металла различными химическими элементами. В настоящее время применяются следующие виды ХТО: Цементация - насыщение углеродом стали с последующей закалкой. При цементации обеспечивается высокую твердость поверхности зубьев при вязкой сердцевине. Для цементации применяются легированные стали с низким содержанием углерода: 20Х, 12ХН3А, 20ХНМ, 15ХФ и пр. Азотирование — насыщение стали азотом обеспечивает высокую твердость поверхности зубьев без последующей закалки. Сталями для азотирования являются 38Х2МЮА, 40ХФА, 40ХНА и пр. Зубья после азотирования не шлифуют. В этой связи азотирование применяют для упрочнения колес зубчатых передач с внутренним зацеплением. Недостатком азотирования является длительность процесса (до 60 час.) и малая толщина упрочняемого слоя до 0,5 мм. Нитроцементация - насыщение стали углеродом и азотом с последующей закалкой протекает при более высоких скоростях диффузии (до 0,1 мм/час). Сталями для данного вида ХТО являются 40Х, 18ХГТ и пр.
Стальное литье применяют для колес большого диаметра. Литейными марками сталей являются: 35 - 55Л, 40ХЛ, ЗОХГСЛ и пр. Литые колеса подвергают нормализации.
Чугуны применяют для изготовления зубчатых колес открытых тихоходных передач. Чугуны проявляют хорошую стойкость к заеданию. Поэтому чугунные зубчатые колеса могут работать без смазки. Для изготовления чугунных колес используют серые чугуны марок СЧ25 - СЧ45, а также высокопрочные чугуны с шаровидным графитом.
Методы получения заготовок
Заготовки для зубчатых колес в мелкосерийном производстве изготавливают из проката или свободной ковкой. В крупносерийном и массовом производстве - штамповкой на молотах, прессах и горизонтально-ковочных машинах (ГКМ). Металл перед ковкой и штамповкой нагревают до температуры 1200-1300 градусов.
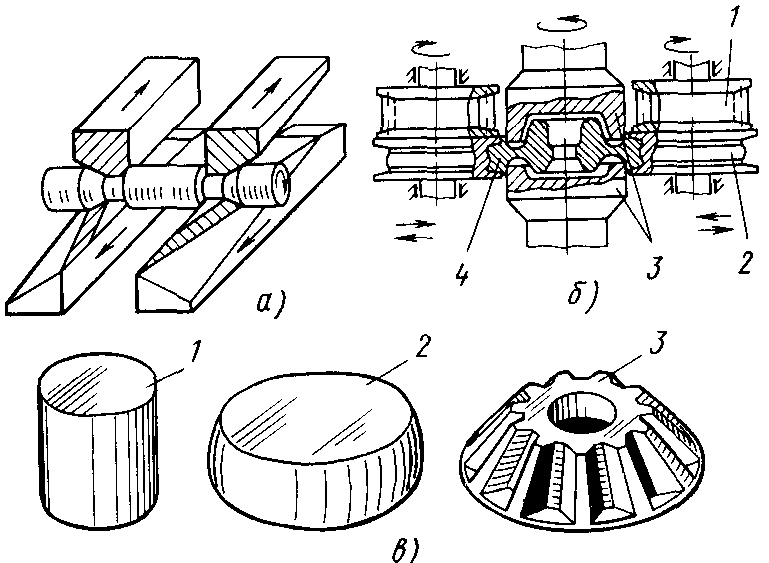
Рис. 198. Схемы получения заготовок: а — поперечно-клиновой прокаткой, б — горячим накатыванием зубьев цилиндрических колес, в — горячей штамповкой конических колес
Поперечно-клиновая прокатка круглыми валиками или плоскими плашками по сравнению с обьемной штамповкой обеспечивает экономию металла на 10-15%
Горячая объемная штамповка осуществляется на многопозиционных автоматах производительностью 70—180 шт/мин Заготовки не имеют облоя, припуск (на диаметр) под механическую обработку 1,0—1,5 мм На автоматах можно изготовлять заготовки зубчатых колес диаметром до 170 мм из штанги диаметром 90 мм Заготовки зубчатого колеса диаметром 67 мм и высотой 40 мм высаживаются за пять переходов из горячекатаного прутка с производительностью 70 шт/мин Отход металла в стружку — около 6 % Этот метод пригоден и для штамповки конических колес
Метод горячего накатывания зубьев цилиндрических зубчатых колес разработан ЗИЛом совместно с ВНИИМЕТМАШем взамен чернового нарезания зубьев колеса (z = 46, mn = = 6 мм, Ъ = 70 мм, р = 16°7) Поковку 4 (рис 198,6), полученную на ковочном прессе, устанавливают в зажимное приспособление, зажимают между стаканами 3 и включают индуктор для нагрева поковки Зубья накатывают за два последовательных этапа Сначала гладкими роликами 2 калибруют штампованную поковку по внешнему диаметру и ширине зубчатого венца, затем заготовка перемещается в верхнее положение После вторичного нагрева заготовки зубчатыми роликами 1 накатывают зубья Время цикла накатки составляет 2,4 мин Припуск на сторону зуба 1,5 мм Горячее накатывание позволяет снизить расход металла на заготовку ( 4 кг), высвободить рабочих, зуборезные станки, площадь и т д
…………………………………….
Заготовки из проката получают их отрезкой от прутка на заданный размер. Максимальный диаметр проката, который выпускает промышленность, составляет 250 ММ. Поэтому диаметр вершин зубьев не превышает этого размера.
Свободную ковку осуществляют на молотах или прессах между плоскопараллельными плитами. Этим методом можно получать заготовки диаметром свыше 250 мм. Однако форма заготовки при этом лишь приближенно соответствует профилю зубчатого колеса. Для снижения трудоемкости при механической обработке в крупных заготовках прошивают посадочное отверстие. При механической обработке заготовок полученным из проката и свободной ковкой расходный коэффициент металла является наиболее высоким по сравнению с штампованными заготовками.
Штамповку на прессах или молотах заготовок для зубчатых колес производят в подкладных или закрепленных штампах. Заготовку в подкладных штампах деформируют с торца (рис. 2.82, а). Закрепленные штампы могут быть закрытыми или открытыми (рис. 2.82, б; в). В открытых штампах в плоскости разъема образуется заусенец — облой, который удаляют затем в обрезных штампах в холодном или горячем состоянии. В закрытых штампах образуется торцовый заусенец, который удаляют точением. Штамповку в закрепленных штампах производят с торца, когда разъем штампа перпендикулярен оси заготовки, или с разъемом штампа вдоль оси заготовки (рис. 2.83, а; б).
Штамповкой (высадкой) на ГКМ получают заготовки из прутков для блоков зубчатых колес или валов - шестерен, когдазаготовки с большим перепадом по диаметру (рис. 2.84). Схема работы ГКМ показана на рис. 2.85. Матрица ГКМ имеет разъем. Одна часть матрицы подвижная другая неподвижная. Пуансон при высадке перемещается в горизонтальном направлении. Штамповка производится в следующей последовательности:
I — пруток закладывается в разъемную матрицу до упора; II — упор отводится, пруток зажимается в матрице и деформируется пуансоном; III - процесс деформации заканчивается, IV — подвижная часть матрицы пуансон отводятся в исходное положение, поковка извлекается из штампа.
Базирование зубчатых колес при механической обработке
Задачей базирования является обеспечение соосности делительной окружности колеса и посадочных поверхностей (центрального отверстия колеса или шеек вала-шестерни). От этого зависят такие параметры точности зубчатых колес и передачи, как колебание межосевого расстояния, боковой зазор и радиальное биение зубчатого венца.
Базовыми поверхностями зубчатых колес на большинстве операций при механической обработке (токарных, зубонарезных, зубоотделочных) являются торцевые поверхности и посадочное (центральное) отверстие, которое может быть гладким с пазом под шпонку, шлицевым или профильным с равноосным контуром (РК) (рис. 2.86). Эти поверхности обрабатываются точно в первую очередь.
Усталостная прочность валов с профильным контуром в пять раз выше прочности шлицевых и шпоночных соединений за счет снижения концентрации напряжений, в то время как затраты на изготовление уменьшаются в два раза.
Базовыми поверхностями зубчатых колес типа валов являются центровые отверстия. Обработка этих деталей начинается с фрезерования торцов и сверления центровых отверстий.
Структура технологического процесса при обработке цилиндрических зубчатых колес
Технология изготовления зубчатых колес зависит от следующих факторов: программы выпуска, конструкции, размеров, метода получения заготовок, материала, точности и термической обработки. Основными факторами являются точность и конструкция зубчатых колес.
Типовой технологический процесс изготовления зубчатых колес включает изготовление штамповок или поковок, токарную обработку наружных поверхностей и торцов; обработку центрального отверстия, зубонарезание, термическую обработку, отделочные и доводочные операции базовых и зубчатых поверхностей. Особенностью технологического процесса изготовления зубчатых колес - валов является наличие операций по обработке зубьев, а в остальном он тот же, что и при изготовлении ступенчатых валов.
Токарная обработка
В мелкосерийном производстве зубчатые колеса до нарезания зубьев обрабатываются на универсальных токарно-винторезных и токарно-револьверных станках. Схема технологической наладки для обработки зубчатого колеса на токарно-револьверном станке представлена на рис. 2.87. При обработке деталь зажимают в трехкулачковом самоцентрирующем патроне. В позиции 1 револьверной головки двумя резцами обтачивают наружную поверхность заготовки. Одновременно одним резцом растачивают внутреннюю поверхность, другим резцом снимают внутреннюю фаску. После отвода револьверного суппорта, двумя резцами Б с поперечного суппорта подрезают торцы. В позиции 2 револьверной головки широкими пластинами подрезают внутреннюю торцовую поверхность. Резцом А поперечного суппорта снимают фаску на наружной поверхности. В позиции 3 револьверной головки растачивают начерно центральное отверстие. В позиции 4 с помощью специального приспособления прорезают внутреннюю канавку. В позициях 5 и 6 револьверной головки центральное отверстие развертывают начерно и начисто.
В крупносерийном производстве зубчатые колеса обрабатывают на токарных и токарно-револьверных станках с ЧПУ моделей 16К20ФЗ, 16КЗОФ305, 16К20Т1, 1В340ФЗ, 1Е365ПФЗ и пр. Общий вид токарного станка с ЧПУ показан на рис. 2.88. Станок имеет следующие основные узлы: 1 - привод; 2 - передняя шпиндельная бабка; 3 и 7 - верхний и нижний суппорт; 4 и 6 - револьверные головки; 5 - задняя бабка; 8 - станина с направляющими. Для повышения производительности применяются двухшпиндельные токарные станки с ЧПУ, у которых вместо задней бабки установлена шпиндельная бабка с приводом рис.2.89. Это дает возможность одновременно обрабатывать зубчатое колес с двух сторон.
Еще большая производительность обеспечивается применением токарных многорезцовых полуавтоматов (ТМП) моделей 1А720, 1А730 и пр. Схема наладки для обработки блока зубчатых колес на одношпиндельном ТМП представлена на рис.2.90. В данном случае обработка в центрах на оправке цилиндрических поверхностей производится с переднего продольного суппорта, а обработка торцев, канавок и большинства фасок с заднего поперечного суппорта.
В массовом производстве применяют многошпиндельные токарные полуавтоматы моделей 1К282, 1283, 1Б284, 1А286-6 и пр. Наибольший диаметр обрабатываемой заготовки на станке модели 1А286-6 составляет 630 мм. Схема наладки для обработки зубчатого колеса показана на рис. 2.91. Станок имеет поворотный стол, в центре которого расположена 6-ти или 8-мигранная колонна. На гранях колонны установлены суппорта трех типов: продольного, поперечного и продольно-поперечного точения. Последний суппорт имеет салазки для продольного и поперечного перемещения резцов. Напротив каждой грани колонны размещены вращающиеся шпиндели с патронами для закрепления заготовок. Согласно рис. 2.91 обработка на станке ведется по следующей схеме.
На позиции I производится установка заготовки. В этой же позиции со станка снимается готовая деталь. На позициях II - IV заготовка обрабатывается с одной стороны. На позиции V заготовка переустанавливается и обрабатывается с другой стороны. Для точной обработки отверстия на позиции VI применяют плавающую развертку. На позициях VII и VIII для сверления и зенкерования восьми отверстий используют специальные многошпиндельные головки.
Токарную обработку крупных цилиндрических колес диаметром свыше 500 мм для тяжелом машиностроения выполняют на токарно-карусельных станках (ТКС). Колеса 8 степени точности и менее точные обрабатываются на ТКС окончательно. Колеса 7 степени точности и более точные обрабатываются на ТКС с припуском для окончательной обработки после сборки с валом. Диаметр заготовок, обрабатываемых на ТКС, достигает 20 м. По своей компоновке ТКС делятся на одностоечные (моделей 1508, 1510, 1512 и пр.) и двухстоечные (моделей 1520, 1525, 1540 и пр.). Широко применяются ТКС с ЧПУ моделей 1512ФЗ, 1516ФЗ, 1525ФЗ и пр. При чистовой обработке на ТКС достигается точность по 7-8 квалитетам и шероховатостью поверхности 3,2-6,3 мкм.
Обработка посадочного (центрального) отверстия
Это отверстие является технологической базой при обработке зубчатого колеса. Для передачи крутящего момента применяется шпоночное или шлицевое соединение. Поэтому посадочное отверстие имеет шпоночный паз или шлицевую поверхность. Точность отверстия и перпендикулярность его оси торцу ступицы у незакаленных колес обеспечивается чистовым точением, развертыванием, шлифованием или протягиванием.
Отверстие протягивают после сверления или зенкерования круглыми протяжками. Точность отверстия после протягивания соответствует 7-9 квалитету. Шероховатость составляет 0,32 - 2,5 мкм. Производительность при протягивании значительно выше, чем при шлифовании. Схема протягивания гладкого отверстия зубчатого колеса на шаровой опоре представлена на рис. 2.94. Применение шаровой опоры обеспечивает перпендикулярность оси отверстия торцу ступицы колеса.
У колес, подвергаемых закалке, отверстие шлифуют на внутри шлифовальном станке (рис. 2.95), а торец ступицы - на плоскошлифовальном станке (рис. 2.14).
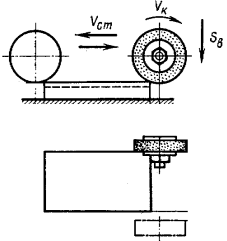 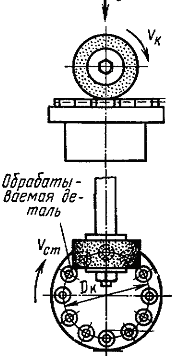
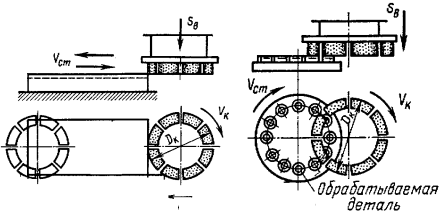
Рис. 2.14 Схемы шлифования плоских поверхностей на станках с прямоугольным и круглым столом а, б – переферией круга; в, г – сегментными кругами
Для повышения точности шлифование отверстия и торца рекомендуется выполнять с одного установа. При этом колесо закрепляют в специальном патроне (рис. 2.96). Шлифование отверстия производят кругом 1, а шлифование торца - кругом 2, установленным на шпинделе дополнительной шлифовальной бабки. Базирование колеса осуществляют роликами по боковой поверхности зубьев, что обеспечивает соосность центрального отверстия и делительной окружности.
Шпоночные канавки и шлицы в отверстиях зубчатых колес прорезают до закалки. В единичном и мелкосерийном производстве шпоночные канавки
|
|
|